|
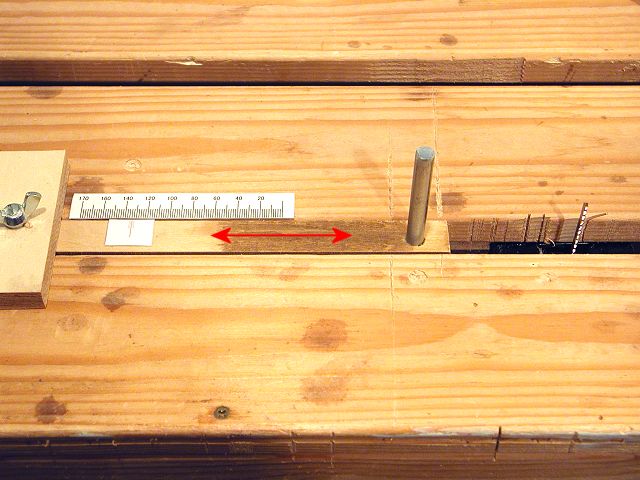 |
|
|
作業台に仕組んだジグの全景。 左からスライドする棒を固定する蝶ネジ、厚紙に印刷した目盛板、移動棒の左端には8φの鉄棒を埋め込んであり、その左側には作業台の裏に固定した電動ジグソーのブレードが突出しています。
|
|
|
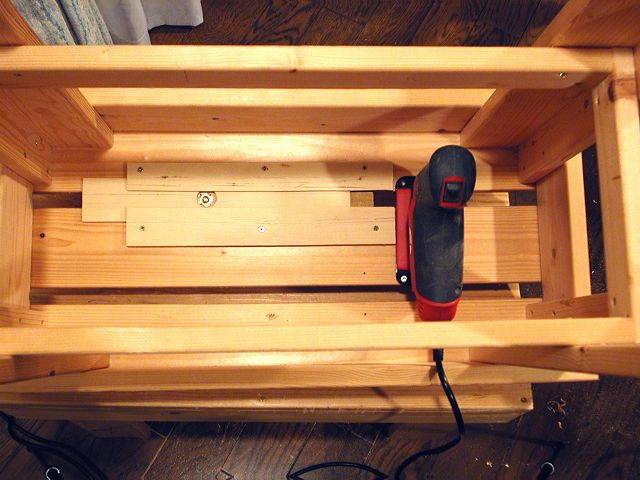 |
|
|
作業台の裏側。 真中が移動棒が上下には動かないよう薄い板を貼りあわせて作ったガイドに挟まれた状態です。 右には電動ジグソー(CJ-250)を台座の穴を利用してネジ止めしてあります。 こんな構造ですから使い終わったら元の作業台に簡単に戻せます。
|
|
|
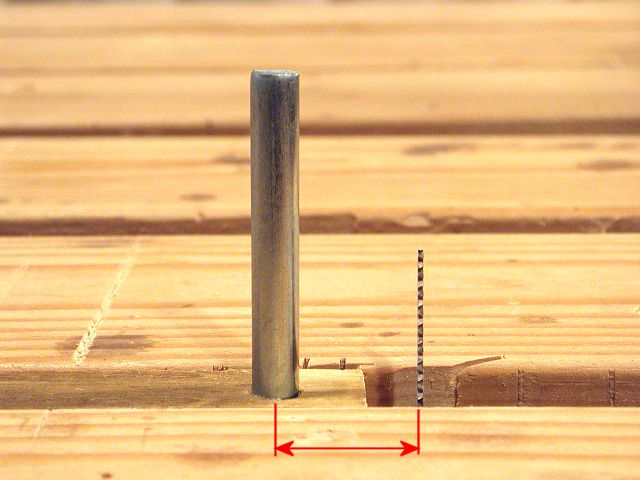 |
|
|
8φの鉄棒と突出したブレードのアップ。 この鉄棒は移動棒にエポキシ接着剤でがっちりと固定してあります。 そして矢印のスパンが切断する円板の半径になりますが、移動棒の可変によりこの半径も調整できるというわけです。
|
|
|
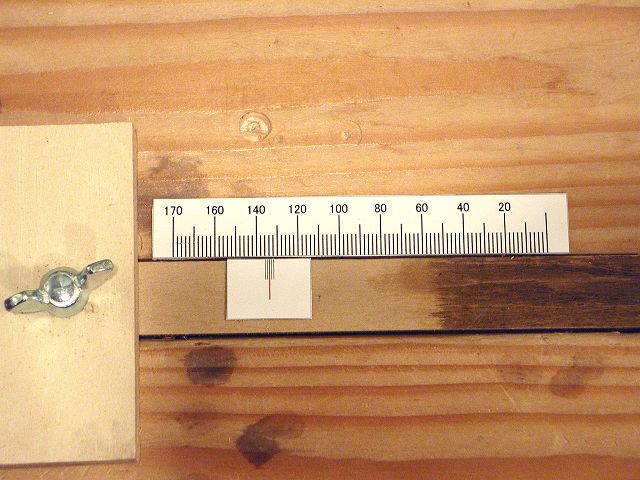 |
|
|
目盛板はExcelで作図して厚紙に印刷した物ですが、0.5mmまで読み取れるようになっています。 目盛板の数値は切り出す円板の直径を表します。 こんな簡単な目盛板でも切り出し誤差0.5mm以内を確保できます。
|
|
|
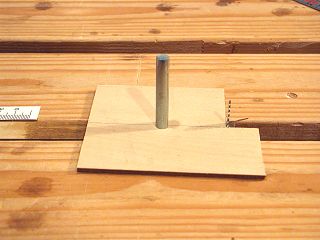 |
|
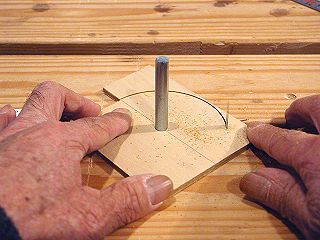 |
|
|
このジグの使い方です。 切り出す板に8φの穴をあけ切り出す直径(ここでは80mmとしています。)よりほんの少し大きくなるよう板の角を落とし、鉄棒にとおしました。 (ブレードはやや右に傾いています。)
|
|
ジグソーのスイッチを入れて切り出す板が浮き上がらないよう抑えながらゆっくりと反時計方向に回してゆきます。 切り進むにつれて右に傾いていたブレードが少しずつ垂直に立ってきています。
|
|
|
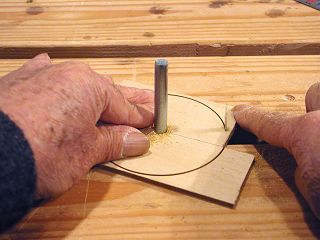 |
|
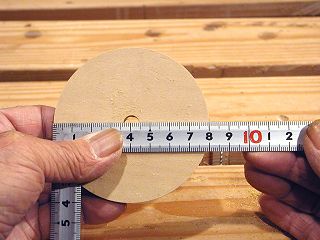 |
|
|
もう直ぐで一周しますが、ブレードはほぼ垂直になっています。 ということは切り出し半径は小さくなっていますので、更に一周回してやる事により所定の半径に成形(修正)出来ます。
|
|
こうして切り出した80mmの円板。 曲尺による実測では約79.7mm位でした。 勿論許容範囲です。 以上はブレードの傾きを強制的に修正しなかった場合です。
|
|
|
以上のようなブレードが左右に傾くことなく(つまり切断半径が小さくなったり大きくなったりする事無く。)切断できるのは
かなり稀です。(10枚切断して1枚くらいの頻度でしょうか?) 実際には左右に傾く事の方が多いので切断中にそれを
修正する方法について解説します。 特に小さく切れてしまうと修正不能になり材料の無駄になります。
この方法は高等戦術で上下するブレードの近くで操作することもあり怪我をしないよう慎重に作業する必要があります。
次の写真は周囲が暗すぎてピントが合わないため蛍光灯スタンドを使い撮影しましたので発色がかなり変わりました。
|
|
|
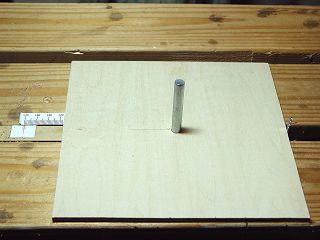 |
|
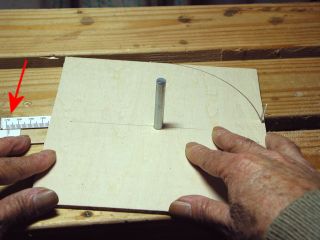 |
|
|
高等戦術の切り方は、切断半径を大きめに取り(ここでは直径175mmを切り出すのに180mm以上にセットしてある。)、更にブレードが若干右に傾くようにして切断開始します。 またスライドする棒は固定してありません。
|
|
切り進むと右に傾いていたブレードは垂直に立ってきますが、左手でスライド棒を少しずつ右に寄せて行きます。 目盛板を見ると僅かに移動しているのが判ります。
|
|
|
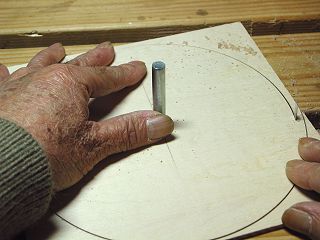 |
|
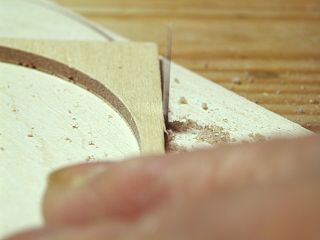 |
|
|
ほぼ一周しましたが切断半径を少しずつ小さくしている為に渦を描くように内側に切り込んでいます。 これを続けて所定の直径よりも1mm大きい所で一旦円として切り落とします。
|
|
その途中でもしもブレードが左に傾くような兆候を発見したら、ブレードの左側に板をこのように当てて垂直になるよう強制的に修正します。 さもないと所定の直径よりも小さくなりアウトとなります。
|
|
|
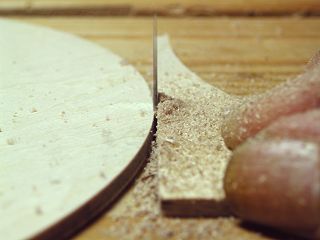 |
|
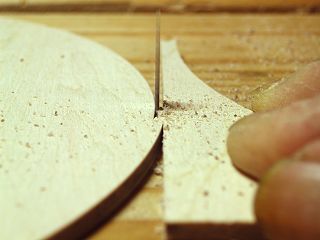 |
|
|
こうして出来た円の外径はかなりでこぼこになりますが、スケールを所定のドンピシャ寸法にセットして移動棒を固定し、板をブレードの左側にブレードが垂直になるよう押してやり修正の切断をします。 ここでは目分量ですが、0.3mm程度を削っています。
|
|
この修正切断はブレードの厚み(1mm前後)の切断が限度で、このような状態は修正のし過ぎであり下手をすると所定の半径よりも小さくなってしまいます。
|
|
|
なにかかなりややこしい事をやっているようですが、実際には端材などで練習すれば数時間でコツを掴めると思います。
そしてジグ無しで切断したのとは全く比較にならない高精度の切断が可能ですし、慣れれば作業もとんとん拍子に進む
でしょう。 実際の所私にとって初めての経験でしたので、最初の10枚を切り出すのに4時間近く掛りましたが、残る34
枚は7時間で切断できました。 ジグの製作と調整そして練習に5時間使っていますので2日費やしました。
|
|
|
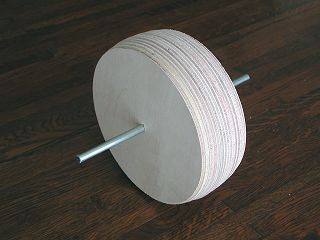 |
|
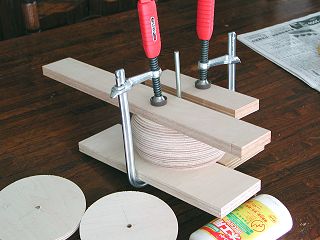 |
|
|
こんなに沢山貼り合わせてからでは遅いですが、最初の数枚を貼る時に鉄棒両端を持って回転させ円板が左右に揺れないよう調整して貼り合せます。
|
|
圧着保持の圧力は相当高める必要がありますので、ワンタッチバクマクランプを使いグリップエンドをスパナで回転させる事により強力に締め上げました。
|
|
|
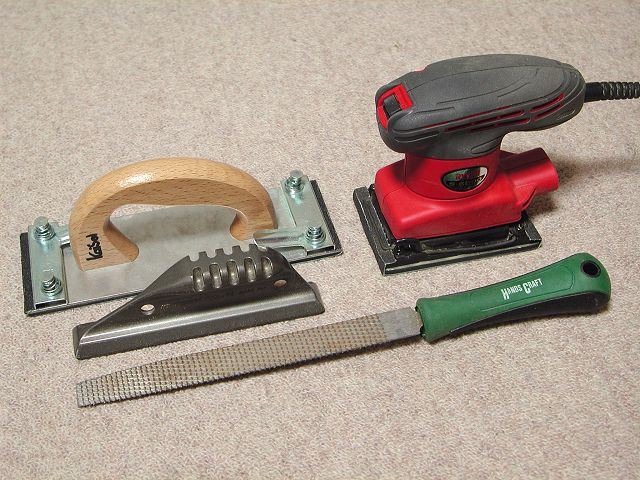 |
|
|
研磨道具はフルキャストの登場です。 最初に粗目木工ヤスリでざっくり落とし、次にミニ電動サンダーに#60を取り付けて研磨、入り隅の部分や僅かな出っ張りを落とす調整研磨は替刃式ヤスリで、その後#240を取り付けたハンドサンダーで全体を慣らし塗装前の仕上研磨としました。
|
|
|
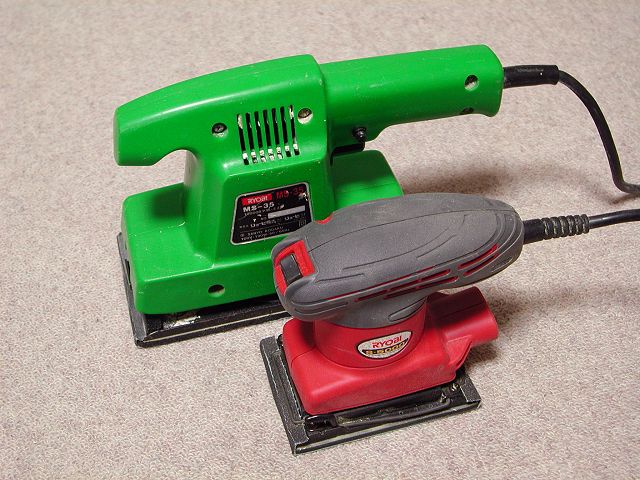 |
|
|
今回使ったミニ電動サンダーはリョービの新製品(S-5000)で、標準のサンダーに比べるとかなり小さくペーパーサイズは75 x 140mmと標準の93 x 228mmに対し半分の面積です。 実はこのサンダー、価格が安くなく研磨能力も低いのであまり評価していなかったのですが、今回考え方を改めました。 この件の詳しい解説はこちら(別ウィンドウ)をご覧下さい。
|
|
|
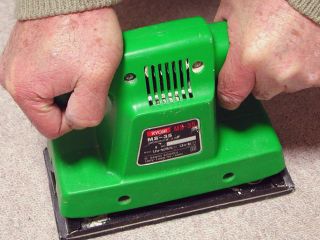 |
|
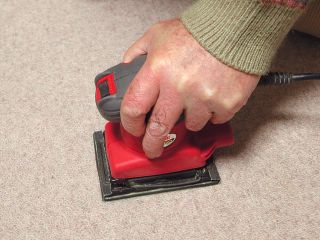 |
|
|
これが通常の電動サンダーの使い方。 片手で握っての使用は研磨圧を上げられないので必ず両手で使う必要があります。
|
|
ミニサンダーでは何と私の小さな手のひらでも収まってしまい片手でも研磨圧を上げられます。 サンダーとしての研磨能力は低いですが、片手使用したときには通常のサンダーより研磨圧が高く取れ作業性が良いのです。
|
|
|
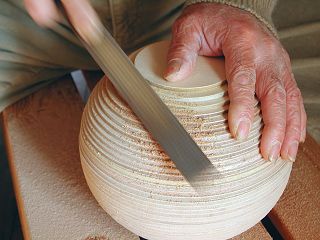 |
|
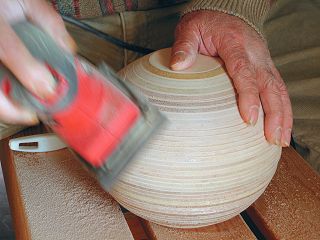 |
|
|
いよいよ研磨開始! まず粗目木工ヤスリで角をばさばさと半分くらいまで落とします。
|
|
その次は#60ペーパーを付けたミニ電動サンダーで各板の段差の隅の極近くまで削り落とします。 このミニ電動サンダーを最も長時間使用しましたが、普通のサンダーだったら比較にならないくらい手首の疲れが出たと思います。
|
|
|
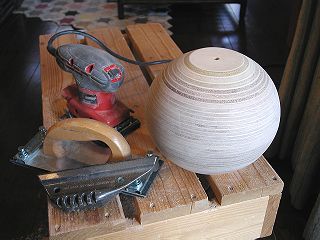 |
|
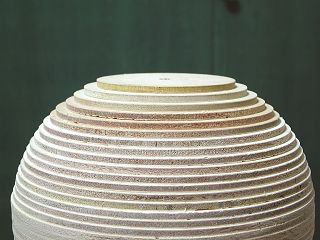 |
|
|
その後替刃式ヤスリで隅や若干の出っ張りの微調整を加え、#240ペーパーを付けたハンドサンダーで全体を仕上研磨して完了。
|
|
研磨による変化の様子。 これは研磨前で各円板による段々の隅まで削り落とさねばなりません
|
|
|
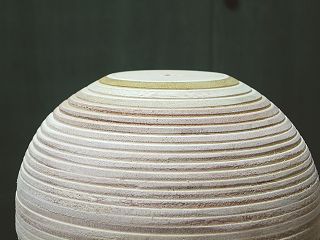 |
|
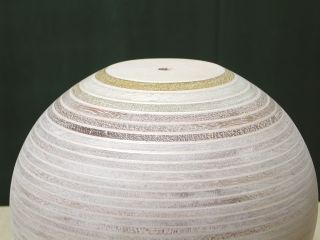 |
|
|
粗目ヤスリで角を大体落とした後電動サンダーによる研磨に入った状態で、まだ隅まではかなりあります。
|
|
電動サンダーで殆ど隅まで削り落としました。 このあとハンドサンダーで念入りに仕上研磨をします。
|
|
|
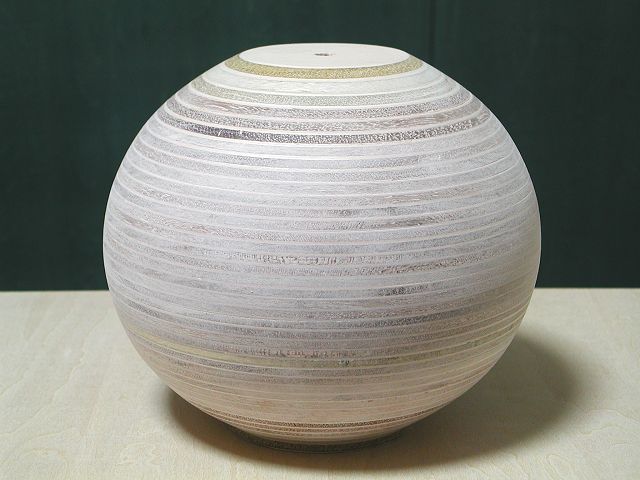 |
|
|
塗装前の仕上研磨が終りました。 上下方向に若干潰れているのが判ると思います。 表面の凸凹もほんの少しあるようですが、完璧さを要求したらきりがありませんがこれでも研磨に6時間使いました。
|
|
|
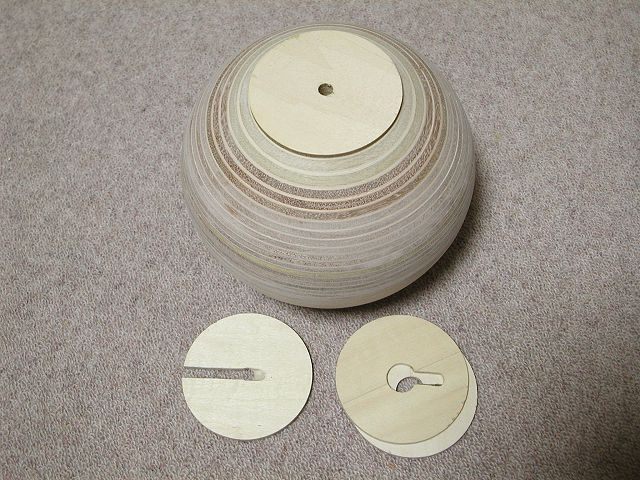 |
|
|
底のケーブル引出し部分の加工。 底板と同じ径の円板3枚を切り出しこのように穴をあけたり切込みを入れました。 左下の円板の切込みにケーブルを通します。
|
|
|
 |
|
|
組み立ての様子。 ケーブルの通る板を貼り(1番目)、次に鍵穴状の穴をあけた板2枚をはります。(2番目) ケーブルを一度このように通してから(3番目)、 ケーブル先端を折り曲げてランプの台の穴に通します。(4番目) 完成後この底面には傷防止を兼ねてフェルトを貼りこの穴を隠してしまいます。
|
|
|
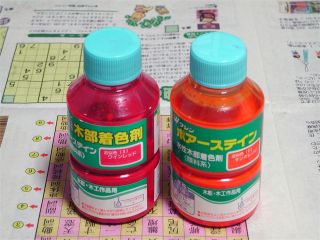 |
|
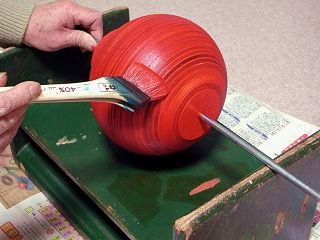 |
|
|
着色はポアステインのワインレッドとサンオレンジを3:2の比率で混合し真っ赤な色を出しました。 等量の水を加えています。
|
|
鉄棒がこんな風に作業を楽にします。 まるで肉の塊を金串に挿したれを塗りつけているバーベキューの風情?です。
|
|
|
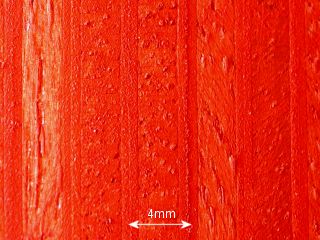 |
|
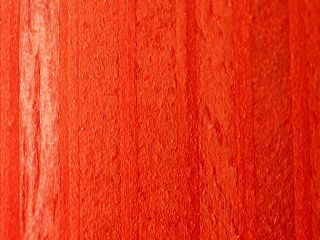 |
|
|
乾いたら塗りを参会繰り返し乾燥後ペーパーを掛けます。 これは研磨前でかなりざらつきがあります。 かなりアップして撮影しています。
|
|
ペーパーを掛けると最初はザアーザアーという音が出ますが、それがサアーサアー、スースーという音に変わるとこのように滑らかになります。(全く同じ部分です。)
|
|
|
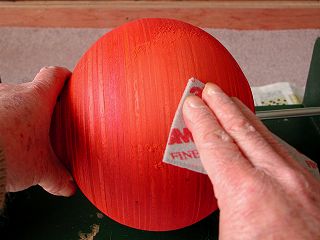 |
|
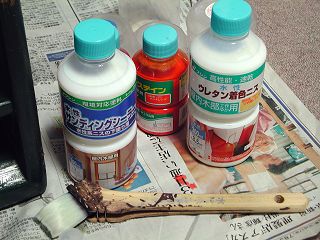 |
|
|
そのペーパーにはスポンジ研磨剤(細目: #240-#320)を使いました。 曲面研磨には大変具合が良いです。
|
|
その後更にステインを2回塗って乾燥後ニス塗りですが、水性サンディングシーラーと水性ウレタンニス艶無しを使用しました。
|
|
|
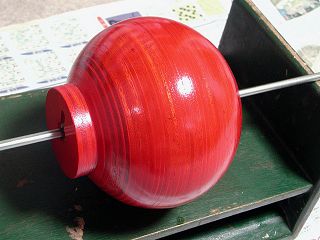 |
|
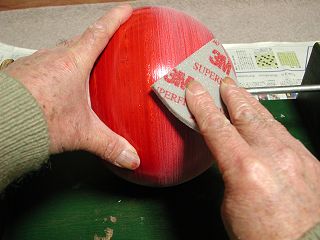 |
|
|
先ず目止めと肉乗り改善のためサンディングシーラーを2回塗りしました。 水性タイプは乾燥が速いので1回目と2回目の間は1時間しかおいていません。 艶がかなり出ます。
|
|
2時間後にスポンジ研磨剤(極細目: #320-#600)で表面を研磨しました。 完全に目を潰すのであればその後再びサンディングシーラーを塗って研磨!の工程を数回繰り返さないとなりませんが、今回はこの後仕上塗装に入りました。
|
|
|
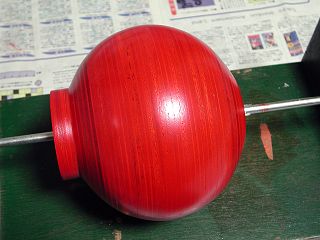 |
|
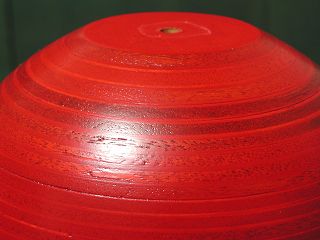 |
|
|
水性ウレタンニス艶ありを1回塗った状態です。 上の写真と比較すると艶の具合が全く異なり、こちらの方が上品?な艶になりました。 さあ肉は完全に焼きあがりました!!
|
|
一番あらが目立つ所を意地悪撮影! ラワンの木目は大きくて深いのと円板の接着境界部分の僅かな削りのこしが一部にあります。
|
|
|
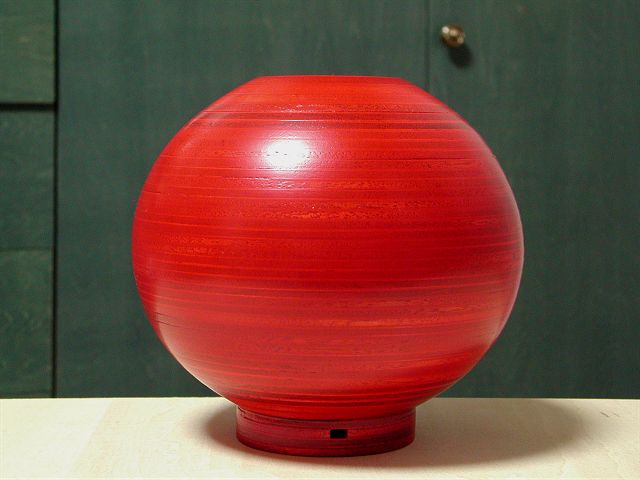 |
|
|
全体の雰囲気はこんな感じです。 油性ニスの場合もそうでしたが艶消しニスといっても上品なニブーイ艶があり、私はこの艶の出方が無類に好きです。 また多少の塗装斑を見えにくくしてくれる効果があり、「艶消しニスは7難隠す!!」です。
|
|
|
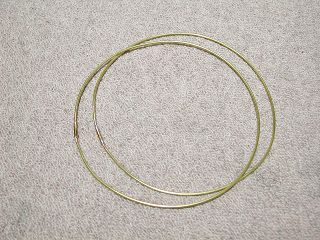 |
|
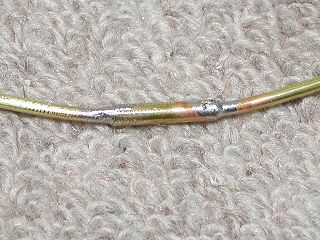 |
|
|
シェードの上下の枠には直径2mmの真鍮ワイヤーを使いました。 長さ470mmで切断するとほぼ直径15cmになります。
|
|
円状に繋ぐには内径2mmの真鍮パイプを長さ15mmに切断し曲げた真鍮棒を挿しこんで半田付けしていますが、瞬間接着剤でも問題ありません。
|
|
|
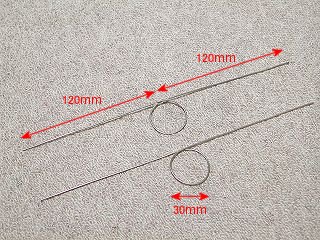 |
|
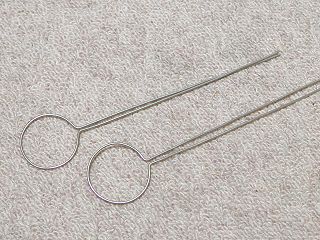 |
|
|
シェードを電球に固定する材料は直径1.2mm(サイズ#18)のステンレス線を使い、このように直径30mmの丸状に曲げます。 また両端は120mmの長さで切断します。
|
|
更にこのように折り曲げてやります。
|
|
|
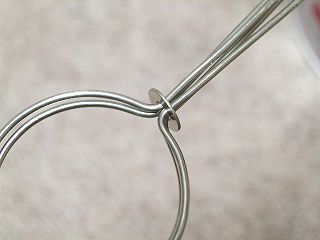 |
|
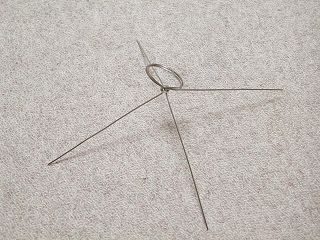 |
|
|
それを3mmの平ワッシャーに曲げた根元まで通します。 ワッシャーがなければステンレス線で小さな輪を作って代用しても構いません。
|
|
次に直線部分をこのように曲げて広げます。 隣どおしの直線部分は大体90度の角度をなすようにしておきます。
|
|
|
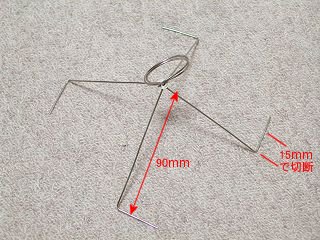 |
|
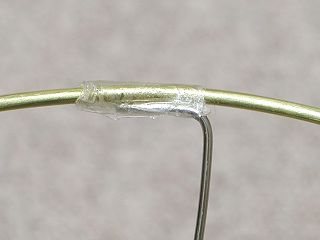 |
|
|
ワッシャーを挿入した首の部分から90mm離れたところを直角に曲げて4本が卍型となるようにします。 そして曲げた先は長さを15mm程度で切断します。
|
|
上の円状の枠にセロファンテープを巻きつけて仮固定します。
|
|
|
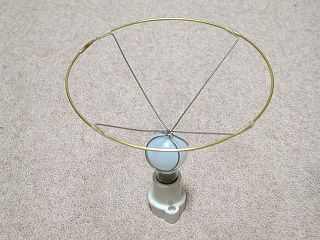 |
|
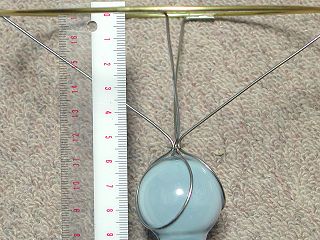 |
|
|
4箇所を仮固定した後全体の具合を見て修正し、良ければ瞬間接着剤を隙間に沁み込ませ表面にも塗りつけて完全固定します。 電球にはこのように取り付きます。
|
|
上の枠と電球の中心はほぼ75mmになりました。 これでシェードの中心に電球が位置することになります。
|
|
|
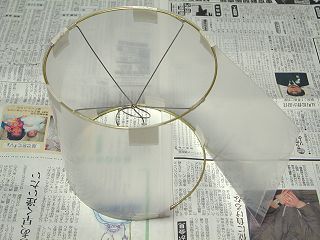 |
|
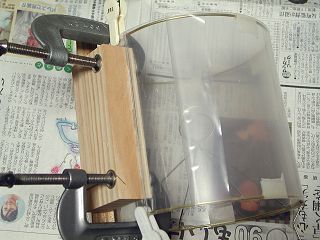 |
|
|
0.5mm厚PET板を 150 x 490mmに切断し上下の枠に巻きつけてマスキングテープで仮固定します。 表面の保護フィルムは剥がしません。
|
|
合わせ目は幅約10mmになりますが、接着面だけ幅15mm程度保護フィルムを切り取りクランプ2個でこのように固定します。
|
|
|
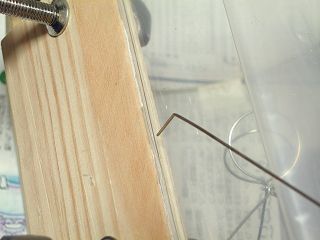 |
|
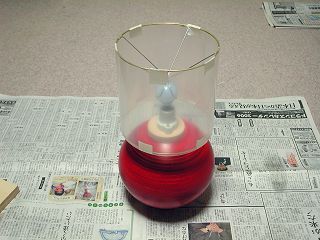 |
|
|
合せ部分にアプリケーターのノズルの先を当ててほんの少しの接着剤を流し込みます。 瞬間的に隙間に沁みとおります。
|
|
1時間ほど放置して筒状に仕上がりました。
|
|
|
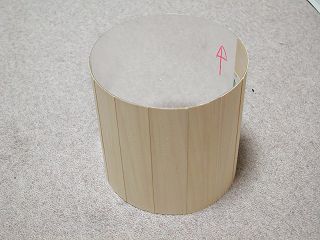 |
|
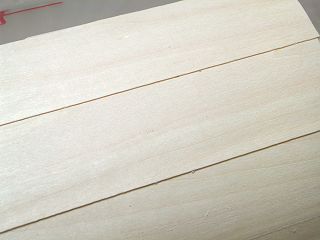 |
|
|
上下の枠を外し外側の保護フィルムを剥がして長さ150mmに切った35mm幅シナ木口テープを貼り付けます。 隣どおしは1mm程重ね合わせておきます。
|
|
重ね合わせる為このように段が付きます。 150mmに切った木口テープは15枚使いましたので2.3mあれば足ります。 mini-Shopの販売価格は\690.-で、突き板と比較すると無駄が出ないのがメリットです。
|
|
|
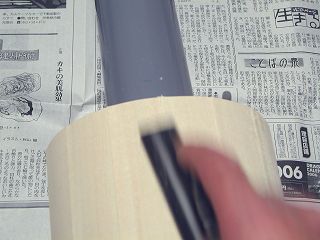 |
|
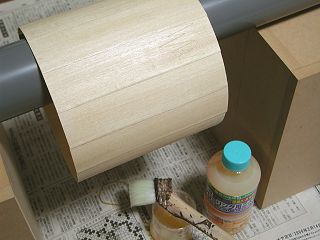 |
|
|
重ねて貼りあわせた部分は替刃式ヤスリで削りますが、削りすぎると白っぽく透き通ってしまうので完全に段差を落とさない方が良いようです。 最後に#400ペーパーを付けたハンドサンダーで全体を仕上研磨しました。
|
|
僅かに段差が残っているのが判ります。 水性フローリングニスを塗ると表面は丈夫になると共に汚れても落としやすくなります。
|
|
|
注意: 木口テープの粘着材は大変強力なので貼り直しはまず出来ません。 木口テープをうまく剥がすことは困難で、
十中八九途中で割れてしまうでしょう。 従って貼り直しをしないで済むよう慎重に作業する必要があります。
|
|
|
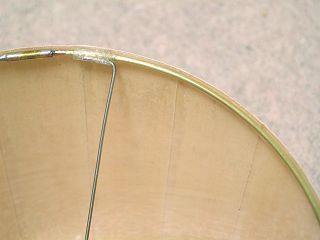 |
|
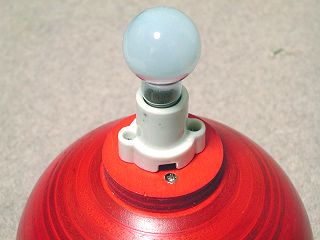 |
|
|
塗装が乾燥したら内部の保護フィルムを剥がしプラスチック用瞬間接着剤のプライマーをシェードの接着部分に塗り、上下の枠を嵌め込んで瞬間接着剤で固定します。
|
|
ランプソケットの固定と配線が終りました。 下駄は当初考えていたよりも5mm高い12mmとしましたが、ネジ止めですので後で変更も可能です。
|
|
|
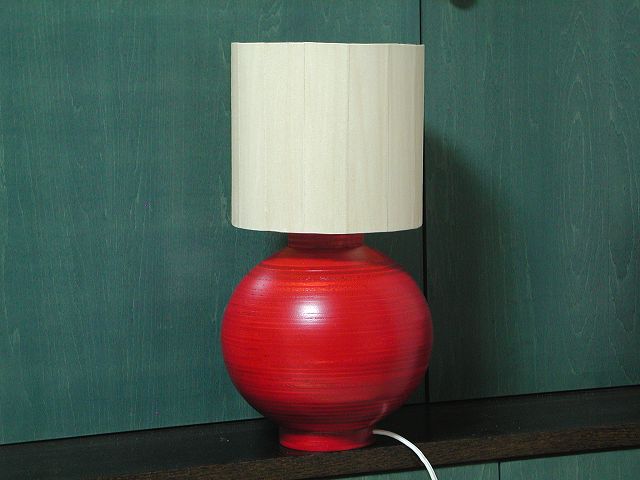 |
|
|
完成した小型のテーブルランプ。 球状の面にクリスマスオーナメントでも貼り付ければぐっと雰囲気が出てくると思います。
|
|
|
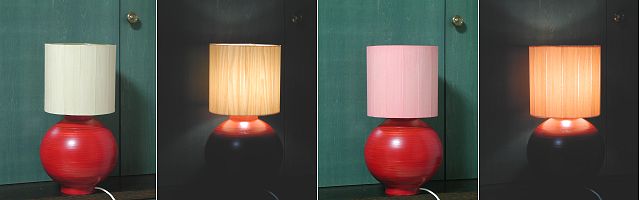 |
|
|
左2枚は着色無しのシェードで、右2枚はポアステインのワインレッドを10倍に水で薄めて着色したものです。 電球を通った光は黄味が減って赤味が増しますが、どちらが良いかは難しい判断です。
|
|
Copyright (C) 2001-2019, Vic Ohashi All rights reserved.