|
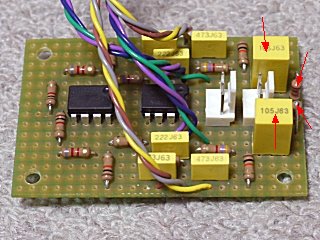 |
|
次にトーンコントロールの基板を組み上げました。 例によって簡単なテストをしましたが、Bass Treble共に機械的な中心位置にセットして1kHzの方形波を通してみた所、原波形に極めて近い出力波形が観測できました。
これはVRの中心位置でほぼフラット(うねりがあってもごく僅か)であることを意味しており、大変満足できる結果です。 但しBassブーストの場合オフセット電圧がかなり増加します。 これはこのトーンコントロール回路の低音側はDCアンプになっており、ブーストMaxではDCゲインが10倍以上あるため、入力のオフセット電圧が増幅されてしまうからです。 これを軽減する方法として出力にDCカットのフィルター(1μFのコンデンサーと22KΩの抵抗)を挿入しました。(左の矢印の4点の部材)
但し後ほどこのあとにデバイディングネットワークを繋いで総合的に動作させたときの状況により、22KΩの抵抗を外してしまう可能性があります。 |
|
|
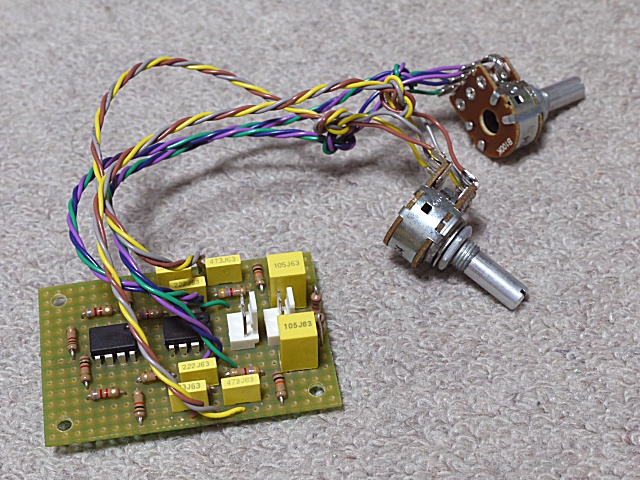 |
|
|
VRとの間は細いビニールコードで結線しているが、3本を軽くよじって煩雑な感じにならないようにしている。 最終的には長さは短くて済むので、シールド線も使っていない。
|
|
|
このトーンコントロールはオペアンプ(LME49720)のデータシートに掲載されたものの定数を私好みに変更したもので、変曲点は下記のとおり。 一般に見られるものより低域変曲点は下の方へ、高域変曲点は高い方にずれており、大袈裟な効きかたをしないようにしている。
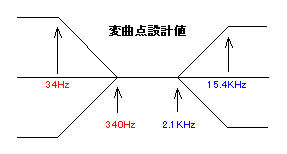 |
|
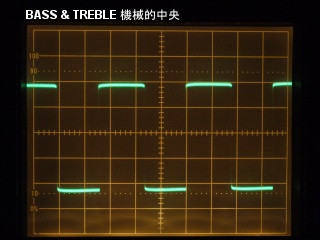 |
|
|
|
|
VRを機械的な中心にセットしたときだが、現波形に極めて近しく、周波数特性におけるうねりはごく僅かであることを示している。
|
|
|
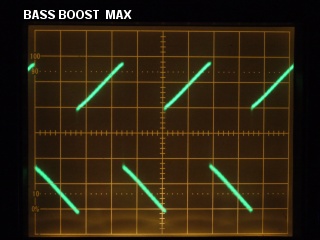 |
|
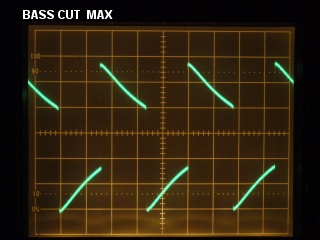 |
|
|
低音を最大ブーストしたときの波形で、右の最大カットしたときの波形を左右反転したようになっている。
|
|
ACアンプの低域方形波特性のに発生するサグが極端に発生したように見える。
|
|
|
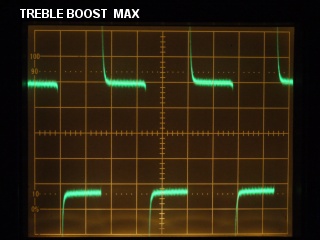 |
|
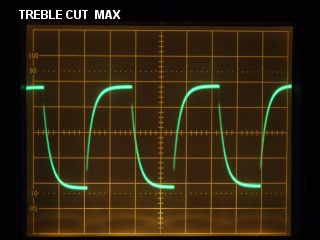 |
|
|
急峻で高いレベルのオーバーシュートの形となっているが、リンギングが全く見られない。 従って動作は安定していて発振の心配はない。
|
|
高域減衰が極端に起きたことを表す典型的な波形。 こちらもリンギングが全く見られない。
|
|
|
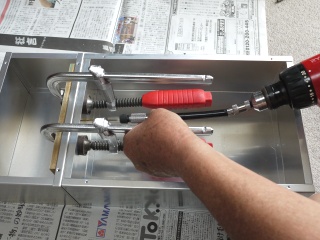 |
|
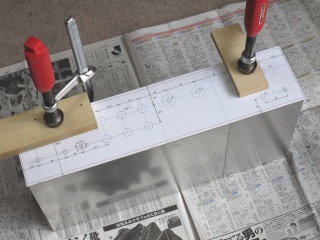 |
|
|
大きなシャーシと小さなシャーシをクランプで連結しておいて、ネジ穴をあけています。 狭い場所での作業なのでフレキシブルジョイントと低速のFDD-1000の組み合わせです。
|
|
6本のネジでシャーシを結合してからフロントパネルを所定の場所に当ててクランプで固定しました。 フロントパネルには穴あけのテンプレートが既に貼られ、センターポンチでマーキングもされています。
|
|
|
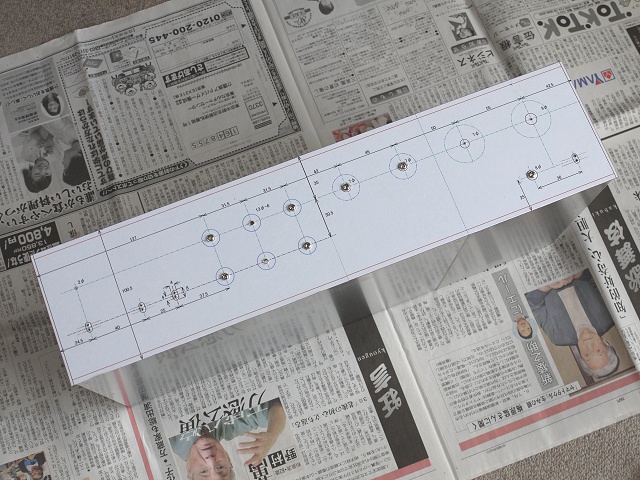 |
|
|
LEDの光が見える穴は2mmですが、その他は全て3mmの穴をあけておいてからクランプを外し、それらの穴の一部をM3のネジで固定しました。 クランプで固定するよりこの方が作業しやすいです。
|
|
|
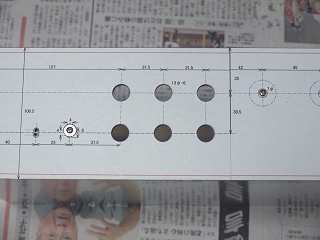 |
|
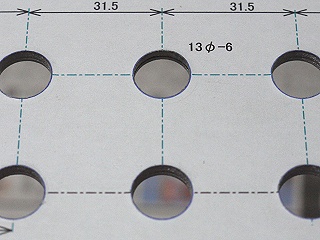 |
|
|
1.5→3.0→6.0→7.5とドリルで穴を広げ、リーマーで10φにしてから丸棒やすりで12φに広げ、最後に12φの回転ヤスリで12.6φまで削りました。(なんと6時間掛かりました。)
|
|
テンプレートに描かれた穴の線の一番外側の縁まで削りました。 真円度、揃った直径(12.6mm)、研削断面の綺麗さなど手研摩としてはかなり上等に仕上がったと思います。
|
|
|
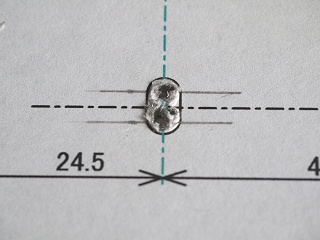 |
|
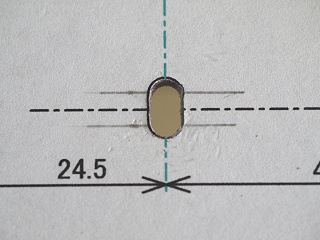 |
|
|
次がトグルスイッチ用小判型の穴です。 左が3mmの穴二つをあけた所ですが、最大径4mmの丸棒ヤスリで3.5mm位まで丸穴を広げ、最大4mmの正方形ヤスリで2つの穴の間を削り小判の幅を4mmにして丸穴を4mm径にします。(右写真)
|
|
|
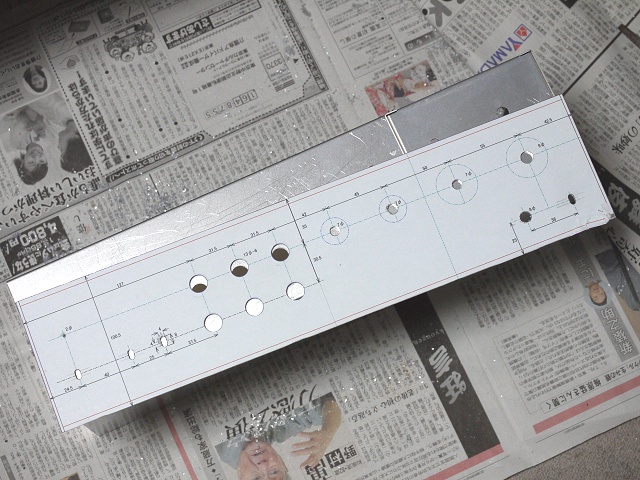 |
|
|
残る7〜9mmの穴あけは簡単。 フロントパネルの加工が無事済みました。 フロントパネルのテンプレートは剥がしアルミ板に付いている粘着剤も綺麗に落とします。
|
|
|
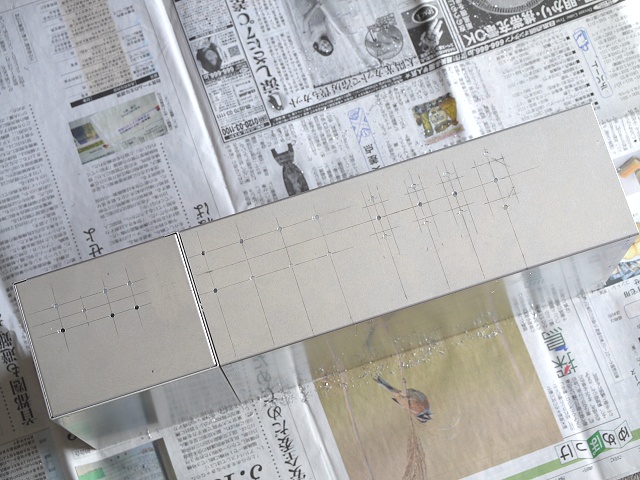 |
|
|
シャーシ背面の加工ですが、全ての穴は1.5φの穴をあけることからスタートします。 この写真はその後3.2φのドリルで拡大したところで、アース端子(左から2番目)とACコンセント、ACインレットの固定ネジ穴はここで終了です。
|
|
|
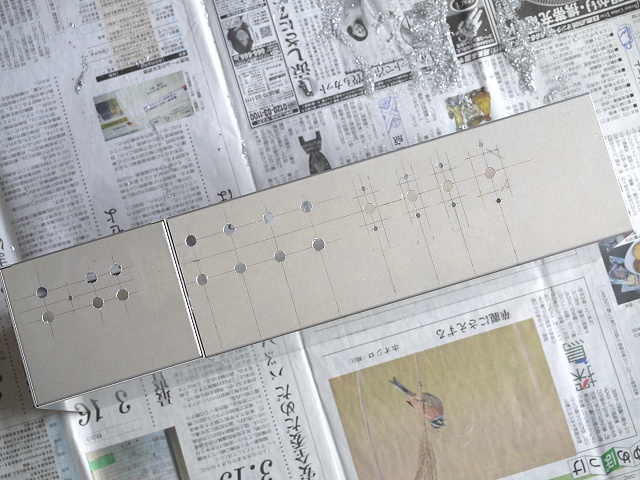 |
|
|
RCAピンジャック、スピーカー端子、ACコンセント/インレットの抜き穴部分は6.0φ、7.5φと広げました。 そしてRCAピンジャック穴は丸棒ヤスリで8.0φに広げて終了です。
|
|
|
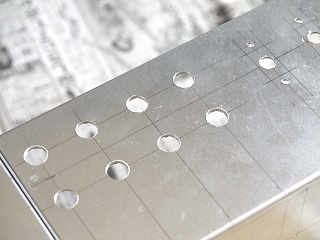 |
|
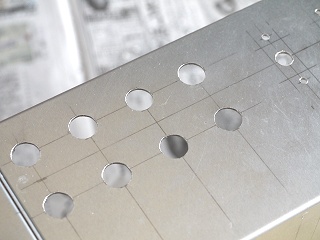 |
|
|
スピーカー端子穴は10φに拡大しました。 私の使っている10φのドリルは切れない代物で汚らしい穴になりますが?
|
|
その後太い丸棒ヤスリで12φとなるよう広げます。 この段階で丸穴の切り口も綺麗になります。
|
|
|
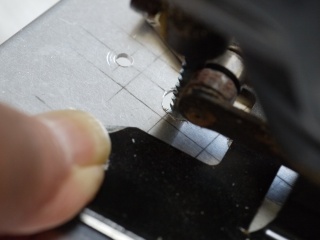 |
|
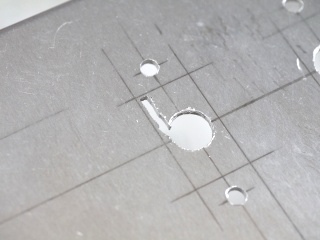 |
|
|
ACコンセント、ACインレットの穴は電動ジグソーに曲線切りのブレードを取り付けて切断します。
|
|
円の左端から四角の左の辺の内側に沿って切断します。
|
|
|
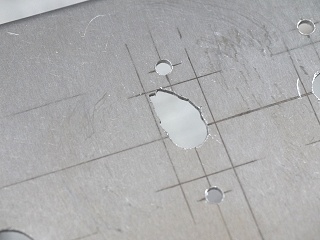 |
|
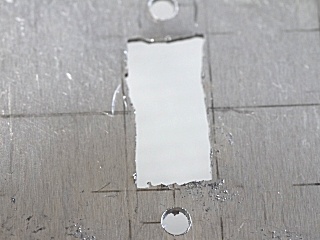 |
|
|
円の右端から左へ曲線を描きながら切断し穴を広げます。
|
|
そんなことを繰り返しながら内側を切り取りました。
|
|
|
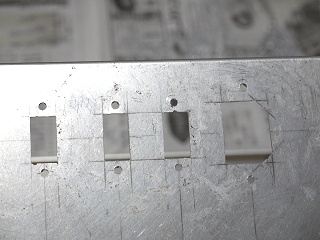 |
|
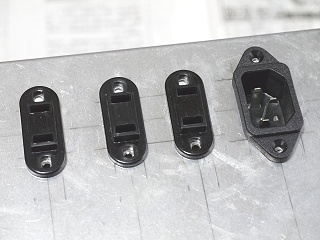 |
|
|
そして墨線のところまで平ヤスリで削って終了です。
|
|
それらの穴にはこんな風にACコンセント、ACインレットが入ります。
|
|
|
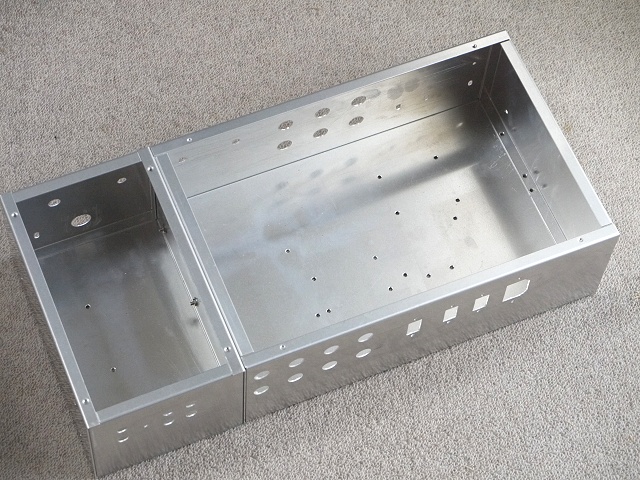 |
|
|
シャーシの底部には電源トランス、回路基板、リレー、整流器などを固定する3.2φの穴が40個近くあけます。 また左右の側面には木製側板を固定するネジ穴が4個ずつあけられます。
|
|
|
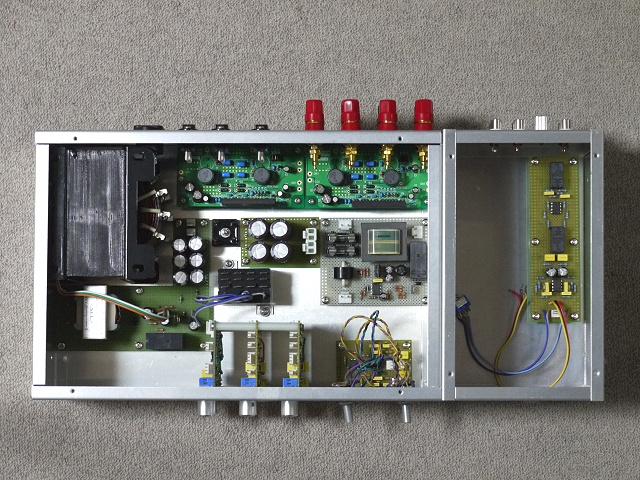 |
|
|
シャーシに固定される全部材を仮止めしてみました。 スピーカー端子穴が若干小さい、電源トランスの右側に1mm厚のスペーサーを挟む必要がある、などの若干の問題を発見しましたので後ほど修正します。
|
|
シャーシの加工はまだ全て終わったわけではなく、天板固定のネジ穴切り、2個のトグルスイッチ固定用金具製作・貼り付け、デバイディングネットワークブロックの固定金具製作・貼り付け、などが残っています。
|
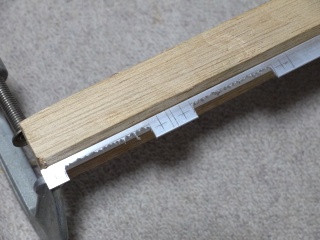 |
|
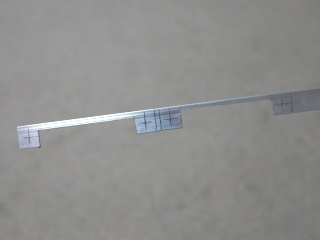 |
|
|
デバイディングネットワーク固定のブラケットの加工。 L字型アルミ棒に墨線を引いた上で、適当な棒に両端をクランプで固定します。 そして刃研ぎグラインダーで削り取りました。
|
|
平ヤスリで墨線まで削って直線になるよう仕上ました。(ヤスリで削る際は木の棒に固定したままの方が安全です。)
|
|
|
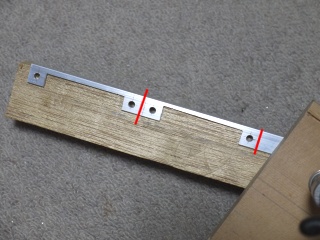 |
|
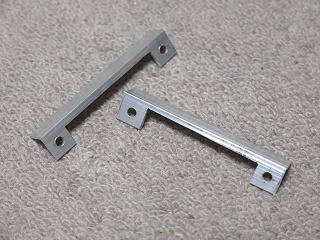 |
|
|
次に木の棒にまたがるように載せて両端をクランプで固定し3.2φの穴をあけました。(1.5φの次に) そして赤線の所をジグソーで切断します。
|
|
完成したブラケット。 以上の加工法はアルミ板が曲がったり撓んだりしないための工夫を凝らしています。
|
|
|
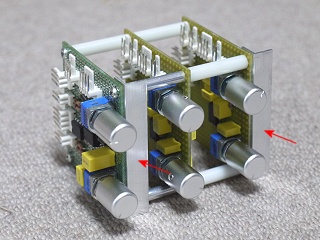 |
|
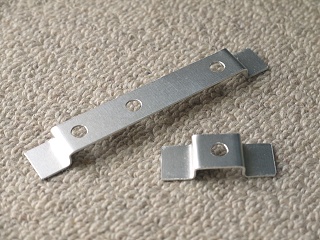 |
|
|
デバイディングネットワークブロックにブラケットを取り付けました。 後ほど矢印の面にエポキシ接着剤を塗りシャーシ前面の裏側に接着します。
|
|
こちらはトグルスイッチを固定するブラケットです。 曲げた部分のシャープさがありませんが、それによる問題はありません。
|
|
|
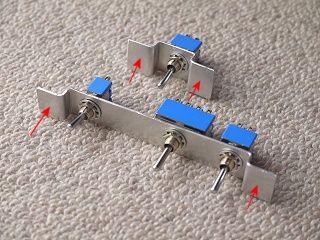 |
|
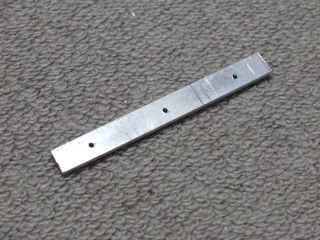 |
|
|
トグルスイッチを取り付けるとこんな具合で、こちらも矢印の先の面にエポキシ接着剤を塗ってシャーシ前面の裏側に接着します。
|
|
天板を固定するネジ穴は長さ25mm、幅9mmに切断した2mm厚アルミ板をシャーシ折り返し部分の裏に貼り付けます。
|
|
|
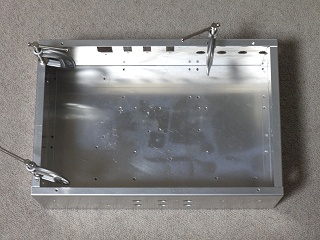 |
|
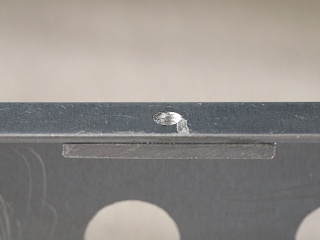 |
|
|
接着は無論エポキシ接着剤ですが、信頼性と強度が最も高い60分硬化開始型を使い20時間放置しました。
|
|
そしてM3のタップで雌ネジを切りました。
|
|
|
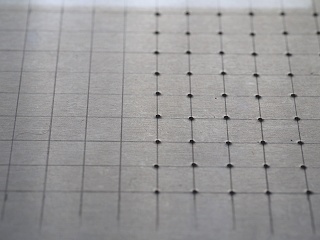 |
|
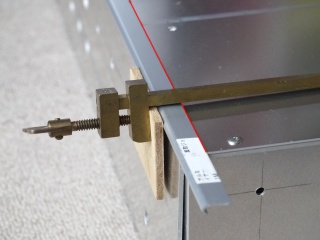 |
|
|
一方アルミ天板には放熱口をあけます。 穴径は3.5mm、穴の間隔は6mmとし、9列 x 47 = 423個となりますが、この右側はセンターポンチで浅いマーキングを施した所です。
|
|
一方アルミ天板の前側は断面J型のアルミ棒と突合せになるので、重なる部分をカットするため赤線のところをケガキます。
|
|
|
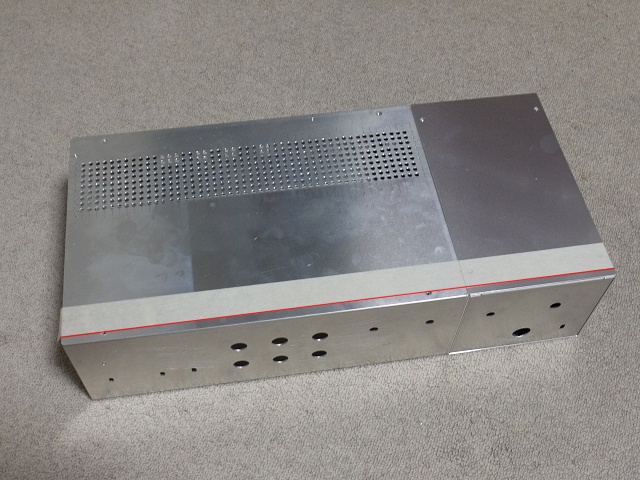 |
|
|
穴あけが無事終わりましたが、何と線引きから6時間掛かりました。 但し沢山あけた穴による突出問題は3.5φの穴あけ後には完全に解消しています。 アルミ天板の前側の切断線に沿ってマスキングテープを貼り付けて切断します。
|
|
|
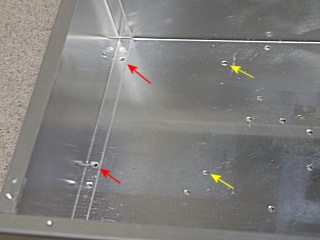 |
|
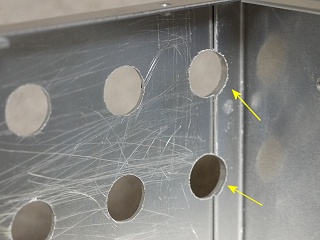 |
|
|
赤矢印と黄色矢印は電源トランスの固定ネジ穴ですが、赤矢印側はアルミの折り返しがあるため気入り側より1mm高いので、黄色側にダミーのアルミ板を貼りつけます。
|
|
スピーカーターミナルも右端の物は折り返し部分にまたがって穴があいているので、ターミナルの固定が不安定なため、下駄を履かせないとなりません。
|
|
|
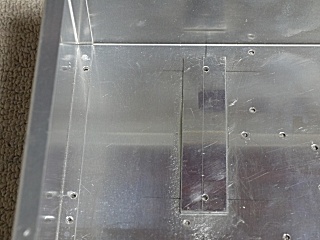 |
|
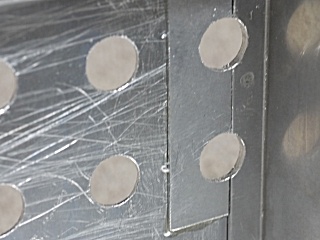 |
|
|
段差修正の結果はそれぞれこんな具合です。 これで固定・締め付け上の不安定さや傾いた固定状態が無くなります。
|
|
|
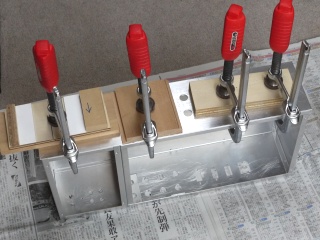 |
|
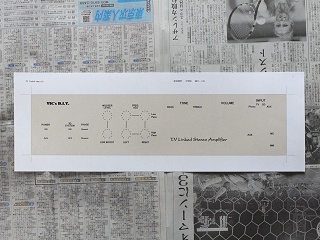 |
|
|
大袈裟な!と思われること必定ですが、アルミフロントパネルをエポキシ接着剤で貼り付けるのに密着度を上げたい為に4本のバクマクランプで締め上げました。
|
|
12時間以上圧着保持するのでその間にフロント用紙を塗装しました。 アクリル系スプレー塗料の透明クリヤーを2回、その後艶消しクリヤーを1回塗っています。
|
|
|
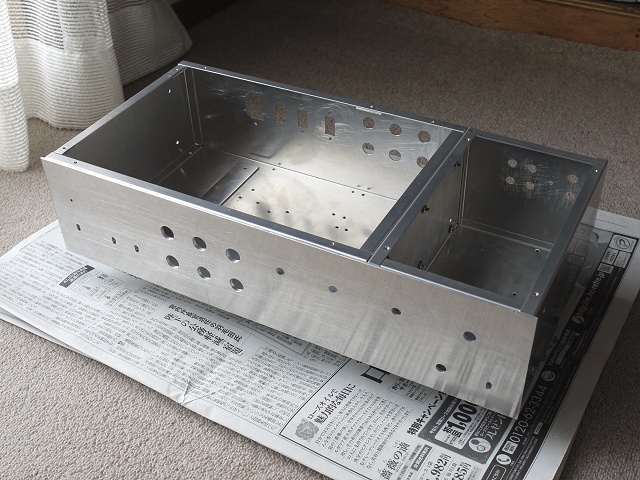 |
|
|
12時間以上寝かせてからクランプを外しました。 僅かな(0.2mm位?)接着位置ずれがありましたので、丸棒ヤスリで微調整をしています。 フロントパネルの上下方向はシャーシの高さに等しいですが、幅はシャーシよりも左右とも2mm出ています。
|
|
|
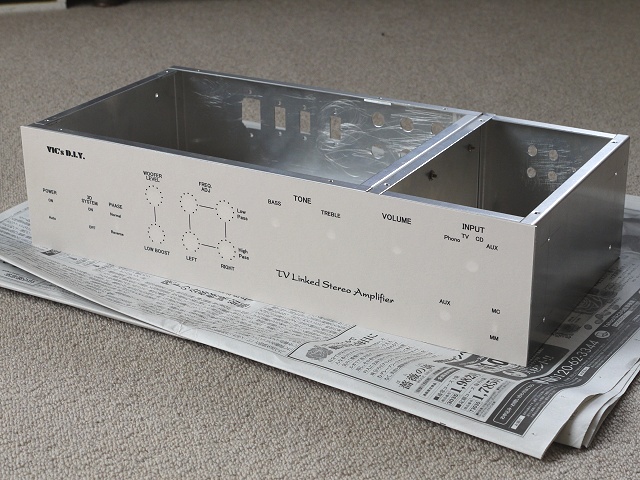 |
|
|
フロントパネル用紙を貼り付けました。 貼り付けには両面接着テープを使っていますが貼り方を工夫しないと気泡が残ってみっともないことになります。
|
|
|
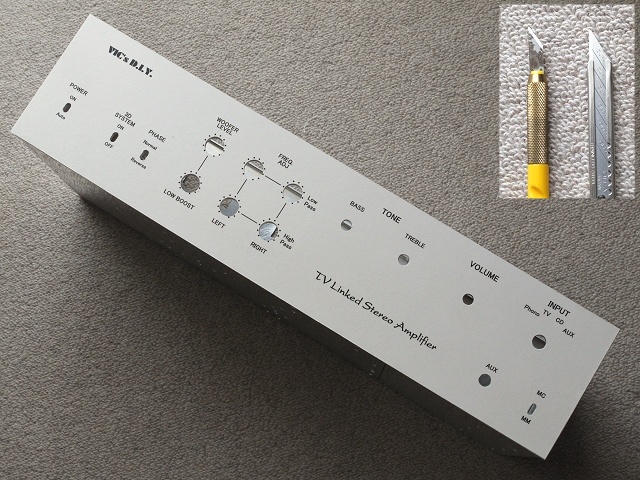 |
|
|
右上に見られるような刃先が狭角となっているカーッターナイフを使い押し切りの要領で少しずつ抜き穴を切り取ります。
|
|
|
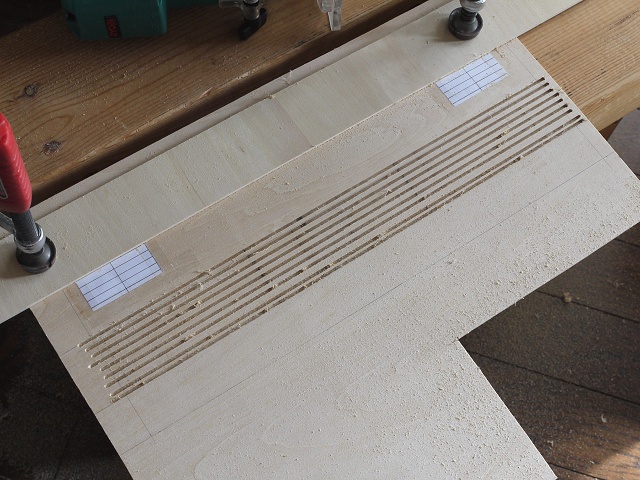 |
|
|
4mm厚シナ合板で天板を作りますが、切り出す前に放熱口のスリットを電動トリマーに3mmストレートビットを取り付けて彫ります。 ところがガイド板の固定位置を1個所間違えて間隔が違ってしまいました。 取り敢えずは作りなおしはせず作業を進めましたが、後ほど結局作りなおさないと駄目!という事態になります。
|
|
|
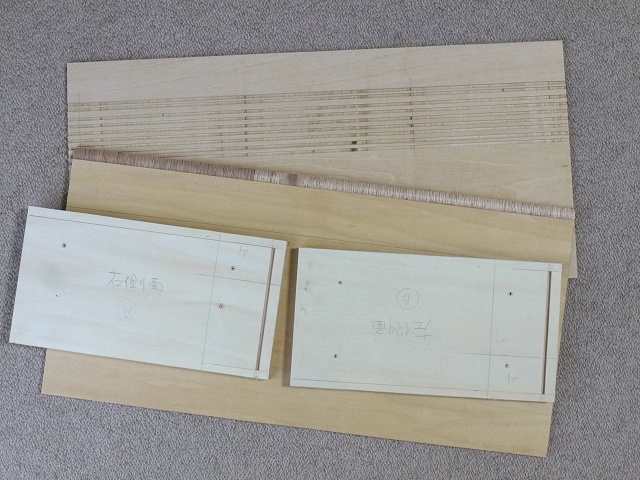 |
|
|
木工部分の材料はこれだけ。 天板、底板、側板2枚ですが、側板は4mmと9mmを貼り合せた13mmです。 また側板にはアルミパネルの両端を落とし込む3mm幅で深さ2.5mmの溝が彫ってあります。
|
|
|
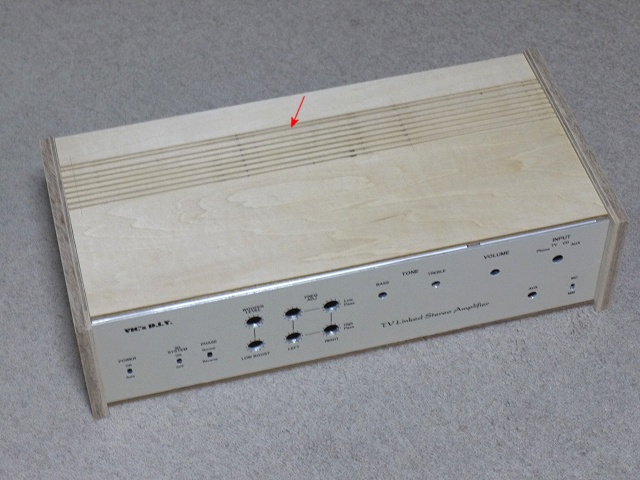 |
|
|
側板をシャーシの内側からネジ止めし天板の長さをカンナとヤスリで微調整しながら落とし込みます。 底板も同様です。 ここまでは天板の溝を彫り間違えた件は良かったのですが、このあと放熱の為の抜き穴加工をしている時に1本の細くなった(幅約1.3mmで赤矢印先)部分が折れてしまい結局作りなおしをしました。(次の写真)
|
|
|
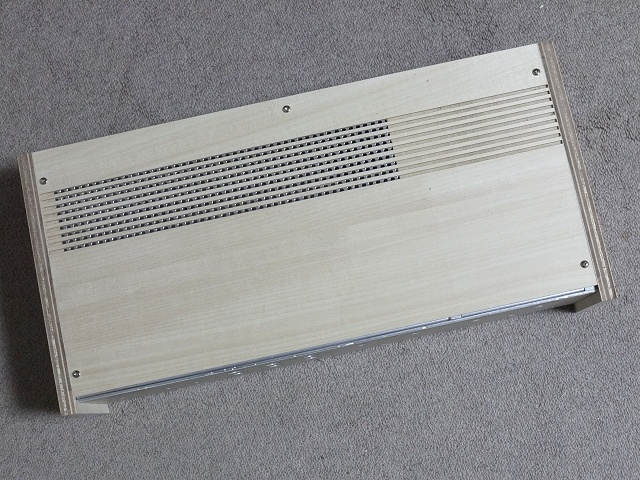 |
|
|
結局作りなおした天板。 この写真では放熱口の抜き穴加工、5本の止めネジ穴あけが終わり、アルミ板と共締めとしています。 負け惜しみみたいですが作りなおしたこちらの方が木目はぐんと美しいです。
|
|
|
 |
|
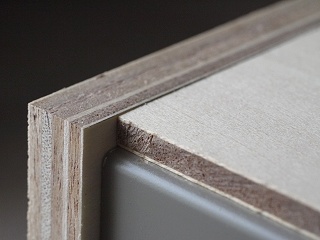 |
|
|
側板の高さは上下に1mm程度出っ張るように切断してありますが、天板と同じ高さから0.3mm高い状態になるようカンナとヤスリで削りました。 この後木口テープを貼るので最終的には側板は天板より0.5〜0.8mm程度高くなります。
|
|
側板下側も底板と同じ高さから0.3mm程出っ張る範囲となるよう削って調整しました。
|
|
|
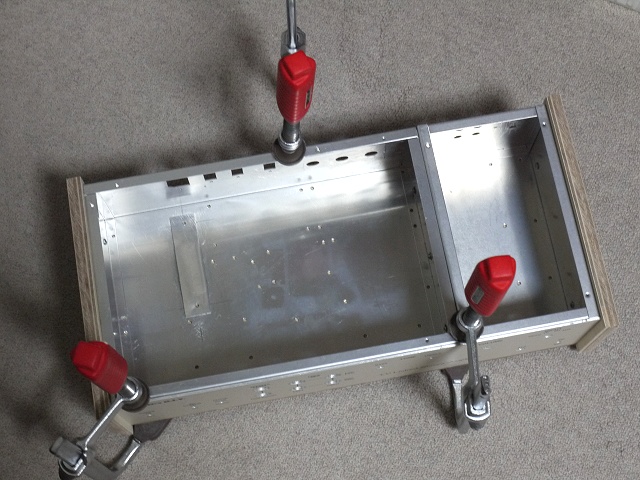 |
|
|
底板が外れないようクランプで抑えてシャーシの内側からネジ穴の位置をシャープペンでマーキングします。 ここに10φで深さ4mmの穴をあけネジの頭が納まります。
|
|
|
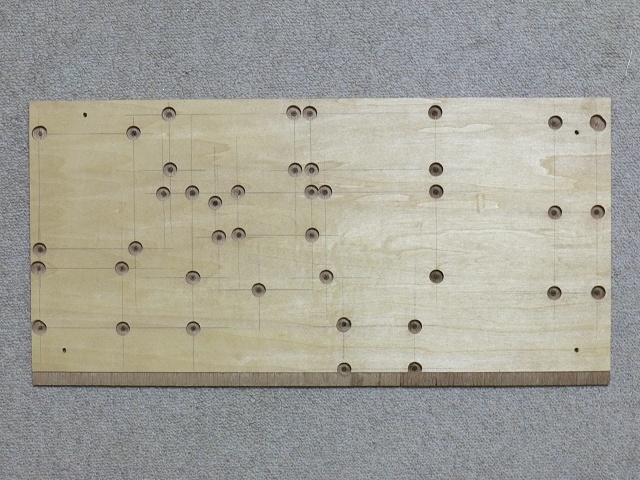 |
|
|
ネジの頭の実直径は6mm、頭の高さは2mmですから切削位置や深さがずれても問題は置きにくいです。 それよりもネジの数の多いこと。
|
|
|
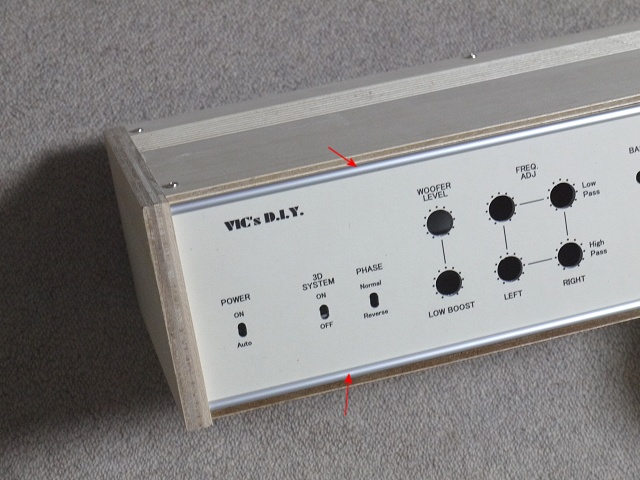 |
|
|
フロントパネルはアルミだぞ!!という自己主張?の飾り棒(断面がJ型)を上下に嵌め込んでみました。 私の目論見は上手く行きそうです。
|
|
|
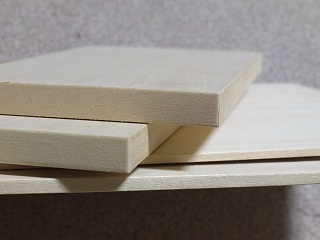 |
|
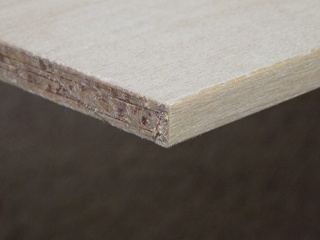 |
|
|
塗装前の最後の作業は木口テープ貼りです。 想像以上に簡単な作業でありながら外観に大きなご利益があります。 右の写真はそのご利益がはっきり判るよう、木口テープを貼った面(角の右側)と貼っていない面(左側)を見せています。
|
|
|
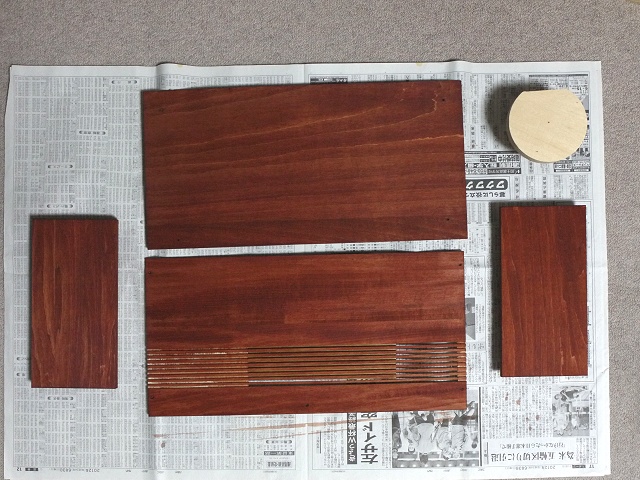 |
|
|
着色はポアステイン オーク色を水で2.5倍に薄めたものを3回塗りとしました。 前回のデスクトップスリムアンプに比べると濃度は薄くなっています。 この写真は2回塗ったところです。
|
|
|
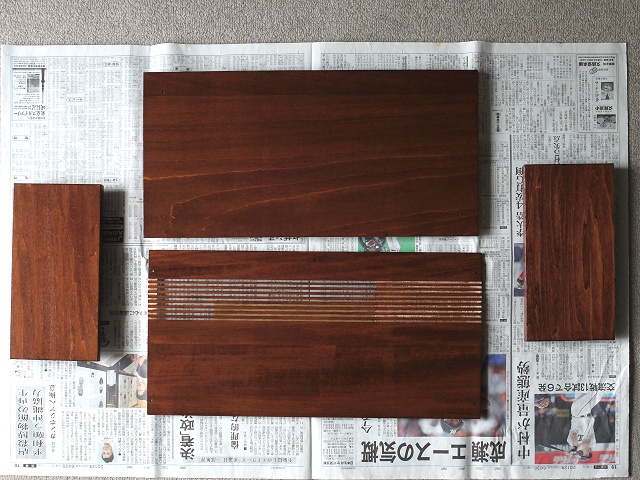 |
|
|
ニス塗りは水性ウレタンニス透明クリヤー3回塗り、水性ウレタンニスつや消しクリヤー1回塗りの私の定番処方です。
|
|
|
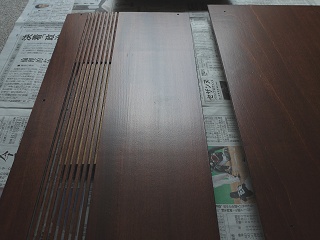 |
|
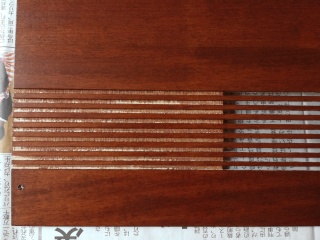 |
|
|
艶の具合が判るように露出を切り詰めて撮影しました。 上品で鈍い艶が大のお気に入りで、難点も隠してくれるというありがたい処方です。
|
|
放熱口の溝の中は黒く塗りつぶしますが、それはアルミ天板を貼った後です。
|
|
|
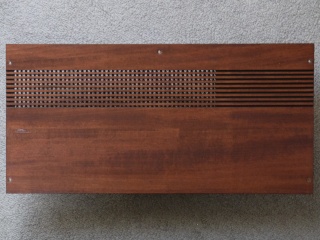 |
|
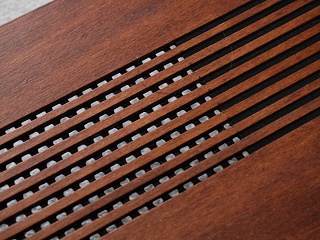 |
|
|
溝の中を水性ペイントつや消し黒で塗りつぶしました。 方法は簡単で細筆で強引に中に塗りつけます。 当然塗らなくて良いところが出てきますがそれは濡れ雑巾で拭き取ります。 水性塗料ならではの手法です。 ところで この過程で溝の下に密着しているアルミ板も塗っています。
|
|
|
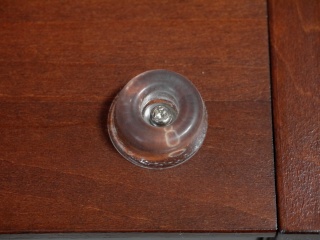 |
|
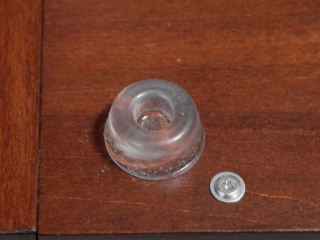 |
|
|
脚は底板をアルミケースに止めるためにもあります。 これは少し柔らかめのドアクッションを流用しています。 3箇所はクッションの中心に3φの穴をあけ両面接着テープとネジ止めとしていますが、1箇所のみ電源トランスに干渉するので、脚は両面接着テープのみとしその近くに独立したネジ止めとしています。(右側)
|
|
|
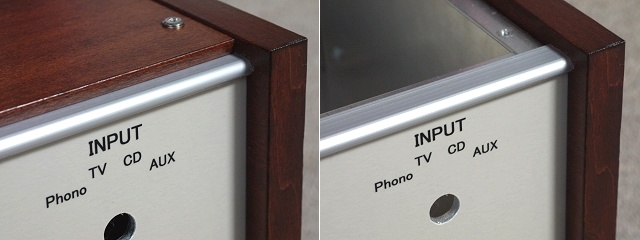 |
|
|
断面がJ型のアルミ押出し棒の固定状況です。 左は天板固定後で右は単板を外した状態です。 左右を比べて判りますが木製の天板は約2mmぴったりと被り押さえつけてくれます。 そのためこの飾り棒は両面接着テープでの固定としました。
|
|
|
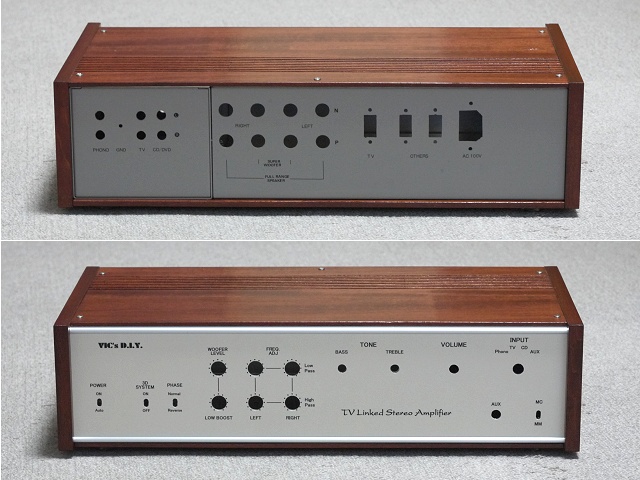 |
|
|
製作が終了したケースです。 いささか常識外れの写真ですが上が背面で下が前面です。 全面の上下に入れたアルミの棒は、フロントパネルが紙で覆われてしまい3mm厚のアルミであることが全く見えないのですが『ここはアルミのパネルだよーっ!!』と訴えているようです。 それはともかくとしても素晴らしいアクセントになっているのは間違いありません。
|
|
|
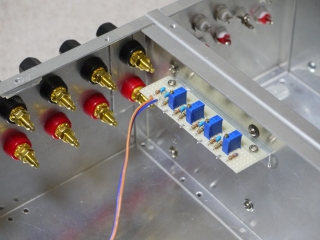 |
|
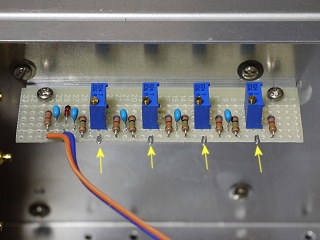 |
|
|
急遽追加したオフセット電圧調整基板は、2つのシャーシの結合面壁に接着しました。
|
|
矢印の先にパワーICの10番ピン或いは13番ピンから引き出したワイヤーを繋ぎその上の青いポテンショメータでオフセット電圧がゼロになるよう調整します。
|
|
|
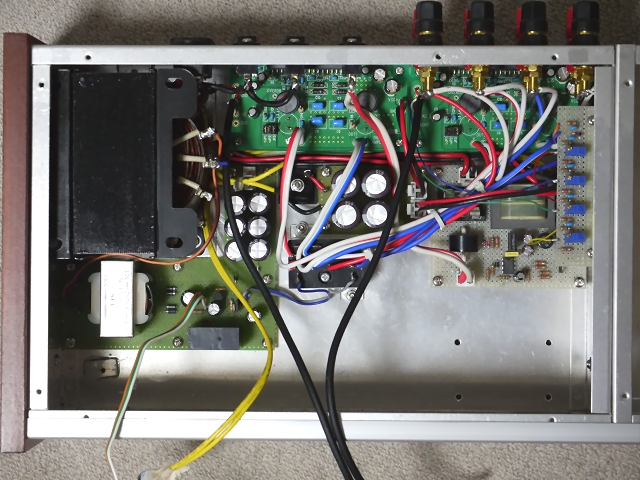 |
|
|
そして全ての電源回路、TV ON/OFF検出回路、デジタルパワーアンプ回路を組み込みました。 手前に伸びる黒いワイヤーはパワーアンプ入力から引き出した3芯シールド線、黄色が電源スイッチへのケーブル、左はLEDのワイヤーです。
|
|
|
 |
|
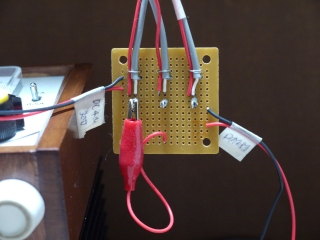 |
|
|
次に準備したのは電子温度計です。 温度センサーの右端はLM35DZでダンピング用の抵抗を繋ぎ熱収縮チューブで絶縁しました。 引出し線はシールド線に単線を加えた物。
|
|
温度センサー3本を小さな基板に固定し、ミノムシクリップで測定点を繋ぎ変える簡単な構造です。
|
|
|
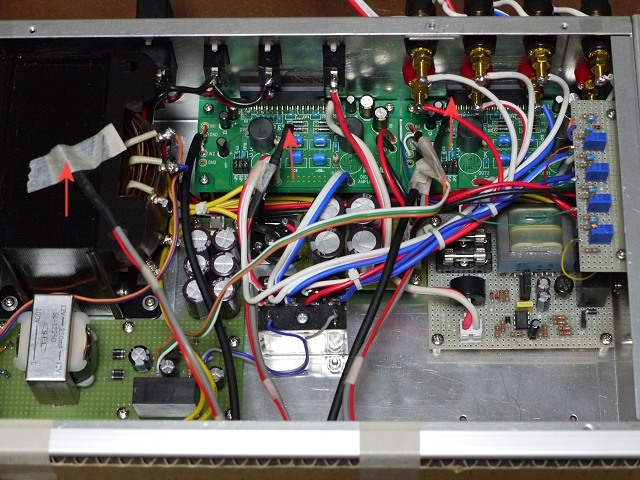 |
|
|
赤矢印は温度センサーを固定したところ、左は電源トランスに貼り付け、真ん中はパワーアンプICとブリッジ整流器の間に、そして右はパワーアンプICに近接させています。 これらのワイヤーはフロントパネルのまだ部品が固定されていない穴から手前に引出し、それらの穴から空気が出入りしないよう蓋をしました。
|
|
|
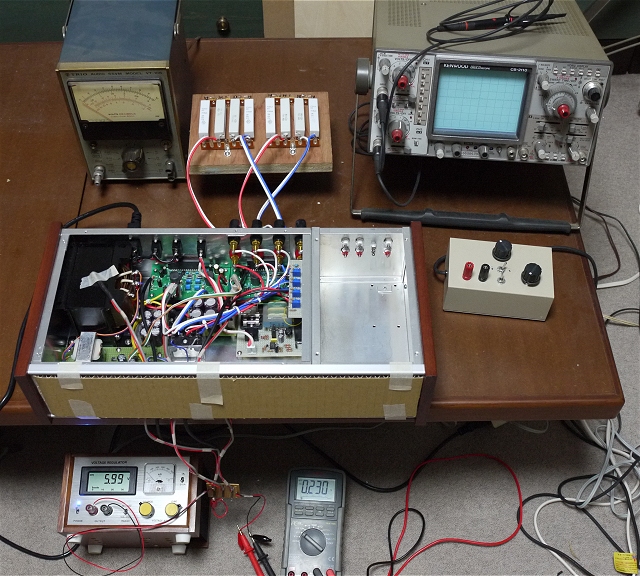 |
|
|
かなり大掛かりになってきましたが、これがアンプ内部温度上昇試験の全貌です。 左上は電子電圧計で出力電圧をチェック、その右側は即席で作ったダミーロード、出力波形を監視するオシロスコープ、その手前は簡易型の低周波発振器、テーブルの左下には電源が見えますが、温度計に6Vを供給します。 その右にぶら下がっているのが温度計基板で、DMMで温度を読み取ります。 フロントの穴を塞ぐために段ボールを被せています。 尚あたりまえですがテスト開始前に天板を被せて固定してしまいます。
|
|
|
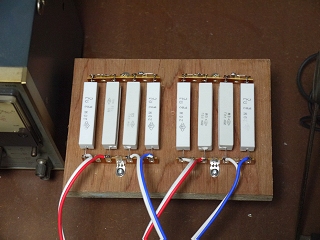 |
|
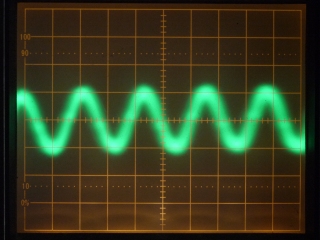 |
|
|
ダミーロードは2Ω 20Wのセメント抵抗2本を直列にしたものを1系統とし4系統を合板の上にラグ板を使って固定しました。
|
|
ノイズ波形を見てみました。 周期が1μsですので約1MHz、レベルは0.08〜0.1Vとかなり高いレベルでした。 しかし周波数が高いので耳には全くノイズを検知できませんでした。
|
|
|
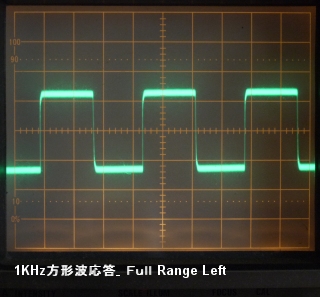 |
|
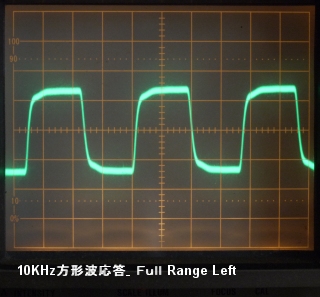 |
|
|
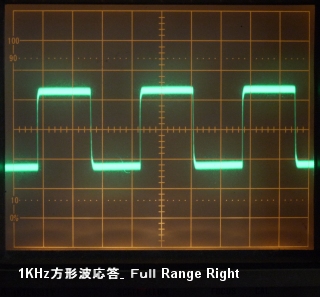 |
|
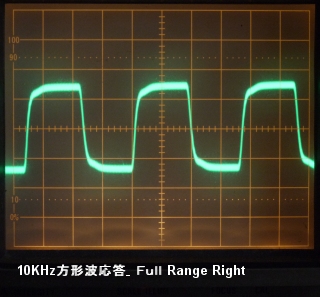 |
|
|
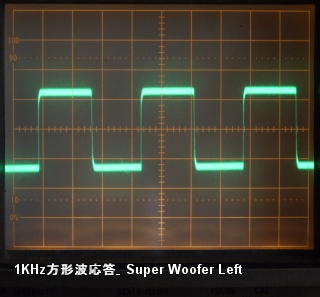 |
|
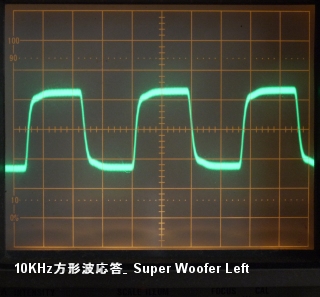 |
|
|
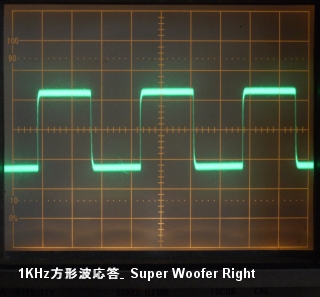 |
|
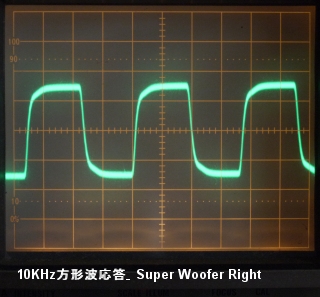 |
|
|
4チャンネルの方形波応答は1KHz、10KHz共にほとんど同じ波形になっています。 これは中域から高い周波数域がほぼ同じ周波数特性を持っていることを表しており見事なものです。 またいずれの波形にもオーバーシュートやリンギングが見られず、10KHzの左肩が丸みを帯びています。 これは40KHz辺りからなだらかに減衰していることを意味しており、動作が不安定になったり発振しやすいなどのクセがないことを表しています。
|
|
Copyright (C) 2001-2019, Vic Ohashi All rights reserved.