|
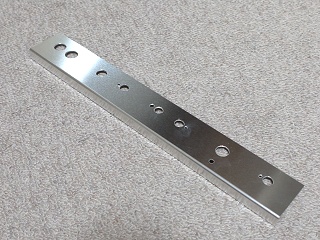 |
|
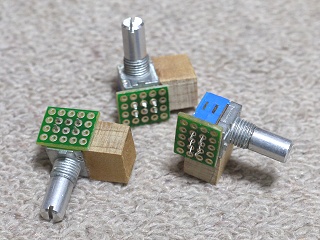 |
|
|
高さ35mmの既製のサブパネルを所定の幅に切断し穴をあけました。 丸ツマミは全て埋め込み式にしますので、ロータリースイッチや可変抵抗は全てサブパネルに固定します。
|
|
下駄となる厚さ10mmの板をサイコロ状に切断し可変抵抗をエポキシ接着剤で貼り付けました。
|
|
|
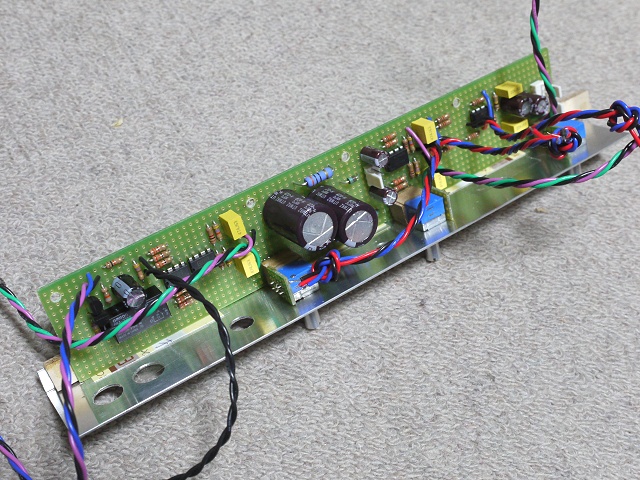 |
|
|
サブパネルに3個の可変抵抗を固定した上で下駄の下側の面にエポキシ接着剤を塗り、位置関係を慎重に調節の上で基板を接着しました。 この角度では圧着保持の様子が全く見えませんが?!
|
|
|
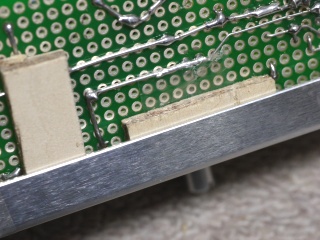 |
|
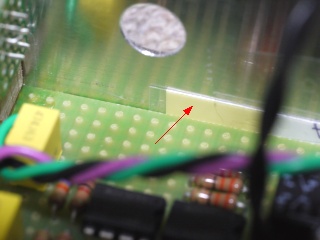 |
|
|
サブパネルと基板の間には4mmの隙間が出来ますので、4mm厚シナ合板を挿し込んで圧着保持をしています。
|
|
サブパネルと基板の間には僅かな隙間があったほうが良いので、0.5mm厚のプラスチック板を切って挟みました。
|
|
|
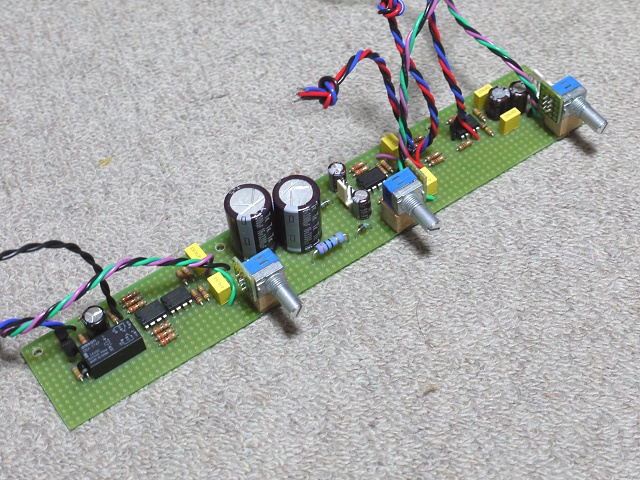 |
|
|
2時間放置してから可変抵抗を締めていたナットを緩めてサブパネルを外しました。 可変抵抗接着の相対的位置関係はこれ以上ない正確さを得ています。
|
|
|
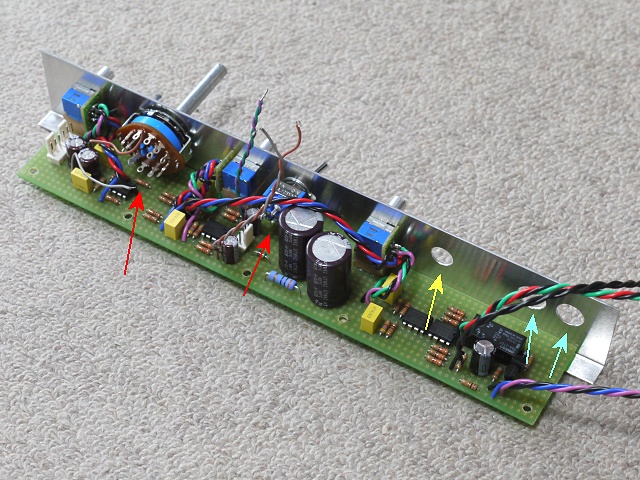 |
|
|
他のサブパネルに固定する部材(赤矢印先のロータリースイッチとトグルスイッチ)と、サブパネルに首を突っ込むヘッドフォーンジャック(黄色矢印)とRCAピンジャック(空色矢印先)が干渉しないかの確認のため仮組立をしました。 こうなるとスカスカだったこの基板が結構実装密度が高くなるのが判ります。
|
|
|
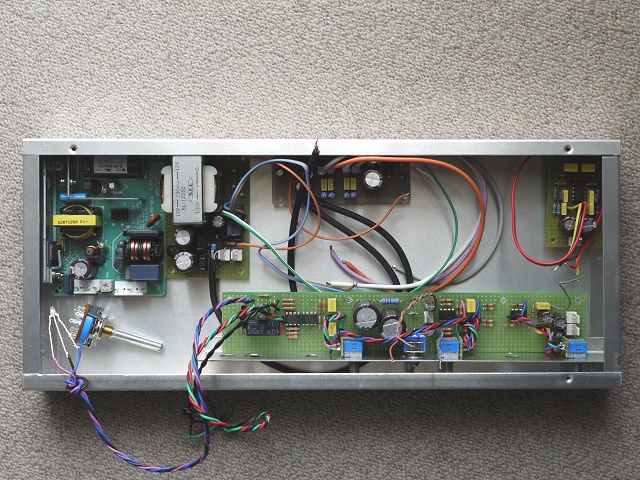 |
|
|
このテーマの基板製作はこれで一応完了しました。 おおまかにシャーシ内のレイアウトはこのようになります。 そして次には2つの電源基板以外を所定の位置に固定し、入力、出力端子も取り付けてベストな電源基板の位置を動作確認で探し出します。
|
|
|
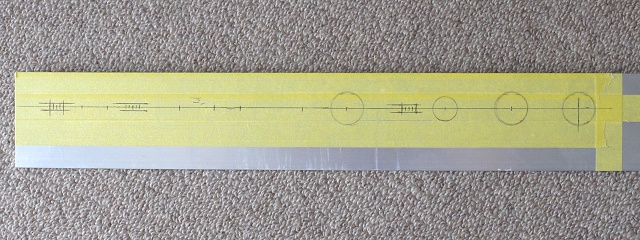 |
|
|
墨線はマスキングテープを貼った上に引いています。 こうすれば穴あけ作業時に表面に付く傷はかなり少なくなります。 下のほうにマスキングテープを貼っていない部分がありますが、ここは切り落とします。
|
|
|
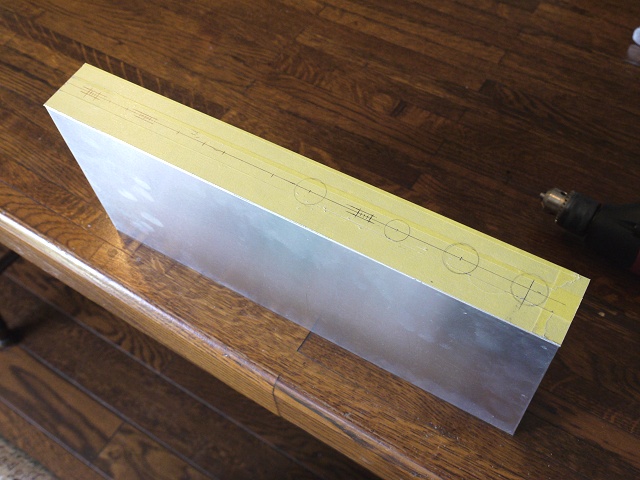 |
|
|
切断が終わったのでシャーシの上に載せました。 押し出し材の幅はシャーシの幅ドンピシャになるよう慎重に研摩で調整しています。
|
|
|
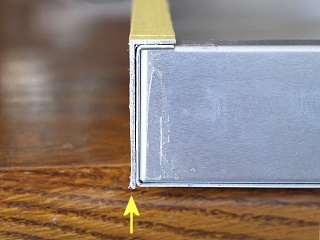 |
|
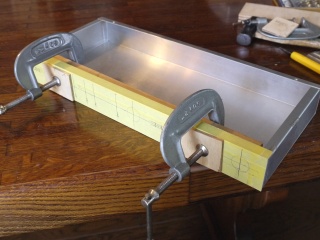 |
|
|
それを右横から見下ろした所です。 押し出し材は引っ掛けた状態です。 また矢印の先は1mmほど出っ張っていますが、底板に彫られる溝にはまり込みます。
|
|
押し出し材パネルを所定の位置に当ててクランプで締め込みました。 この押し出し材が絶対にずれては困るので、穴あけ作業が終わるまでクランプは3個使い最低でも2個は締め上げた状態にして進めます。
|
|
|
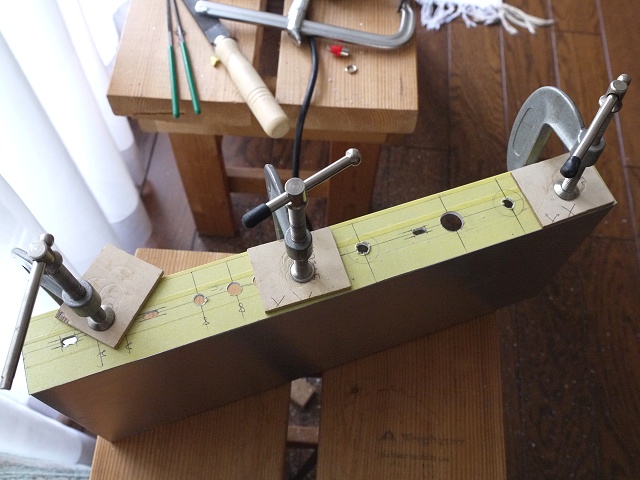 |
|
|
3個のトグルスイッチの穴、2個のRCAピンジャックの穴、2個のヘッドフォーンジャックの穴、小さなツマミ用の穴(直径13mm)がフルに1日掛かってあけ終わりました。 ここまでは1mm、2mm、3mm、5mm、6.5mm、8mmのドリルを使って2mm径、3.5mm径の穴2個(トグルスイッチ用)、6mm径(フォーンジャック1)、8mm径(RCAピンジャックとフォーンジャック2)をあけています。 多くのドリルを使っていますが、いきなり大きな穴をあけるとハンドドリルであける場合には穴位置がずれやすいので、1mmステップでドリルを交換して大きくしています。
|
|
|
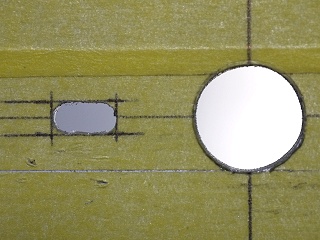 |
|
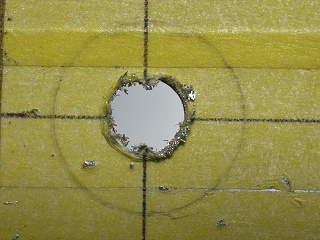 |
|
|
取り敢えず良しとした左のトグルスイッチの穴と右の小さなツマミ用貫通穴。 貫通穴はツマミ現物を使って更なる調整研摩を後ほどやります。
|
|
3個の18mm貫通穴は6.5mm径まであけています。 この後はユニークな方法で穴を広げます。
|
|
|
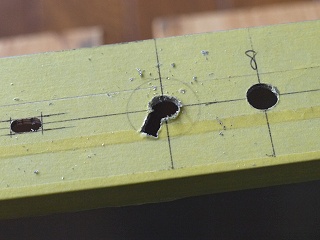 |
|
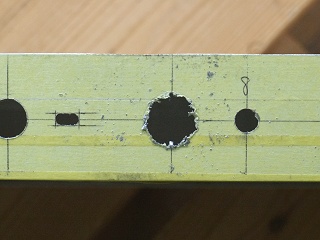 |
|
|
ユニークな方法とはこれです。 mini-Shopで販売している木工円切り用ジグソーブレード(No. 5)を使って墨線の0.5mm手前くらいまで沢山の切り込みを入れて穴を広げます。 慎重に作業をしないとなりませんが、ヤスリで削りこんで行くよりも作業効率が良くて楽です。
|
|
ジグソーで切り終わった状態です。 切り口はランダムにぎざぎざでお世辞にも綺麗ではありませんが、ここから曲面ヤスリで仕上げて行きます。(曲面ヤスリにはmini-Shpで販売している替刃式のRS-310Pを使いました。)
|
|
|
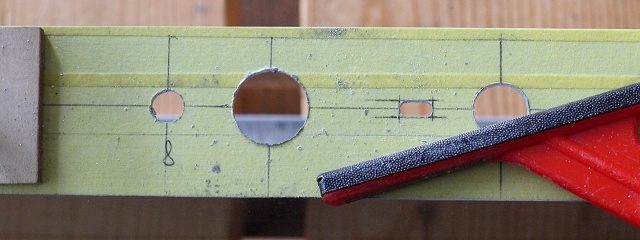 |
|
|
まだ現物合わせでの調整研摩が必要ですが墨線のところまで削り込みました。 右手に見える赤い道具がこの研摩に使ったRS-310Pです。
|
|
|
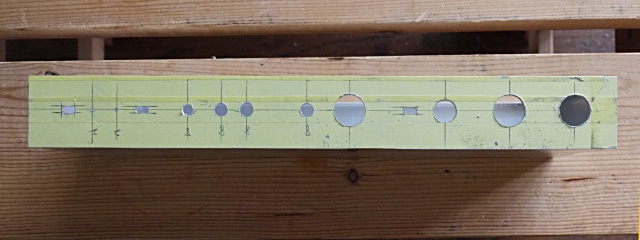 |
|
|
2日半をようしてやっと穴あけが終わったフロント部分。 山場は通過しましたが、この後基板固定のネジ穴あけ、蓋を固定するM3のネジ切り、背面に放熱板を固定などが済めば、シャーシの加工は一応終わります。
|
|
|
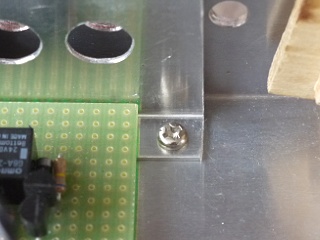 |
|
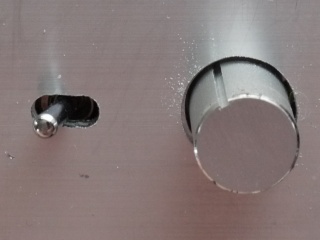 |
|
|
サブパネルのシャーシへの固定は2本のM3ネジで。 こちらは前面から見ると左側のネジを内側から見ています。
|
|
フロントパネルを当ててみたトグルスイッチと録音出力レベル調整ツマミ。 位置関係はまずまずのように思えます。
|
|
|
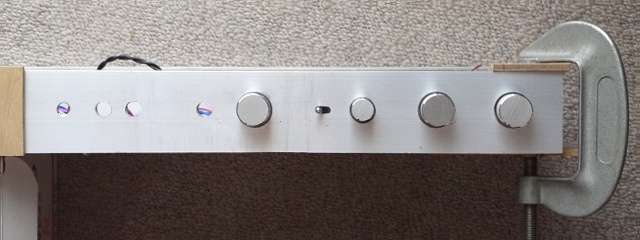 |
|
|
この写真では判り難いですが他の大きなツマミ3個の位置は微妙にずれているので、隙間調整のための研摩が必要です。 但し削りすぎると台無しになるので、微調整研摩とフロントパネルを取り付けての確認を4回繰り返してOKとしました。
|
|
|
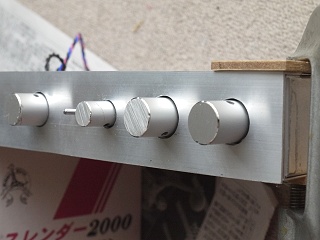 |
|
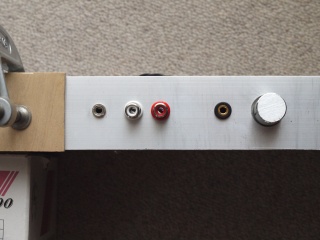 |
|
|
隙間の均等具合がまずまずである様子はこの写真の方が判りやすいでしょうか?
|
|
そうそうRCAピンジャック、2種類のミニヘッドフォーンジャックも取り付け後の問題がないか確認しています。
|
|
|
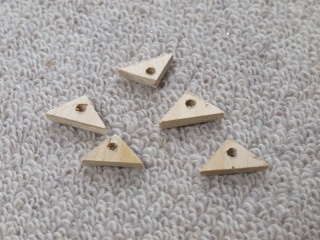 |
|
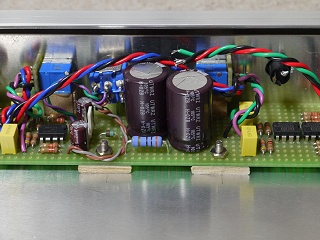 |
|
|
基板の後ろ側の固定には4mmのスペーサーが市販品には無いのでシナ合板をこのように切断し穴をあけました。
|
|
その4mm厚スペーサーを挟み込んでネジ止めしたところです。 これで基板やツマミのぐらつきがほぼ無くなりました。
|
|
|
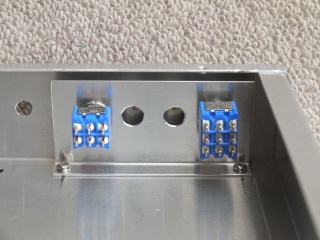 |
|
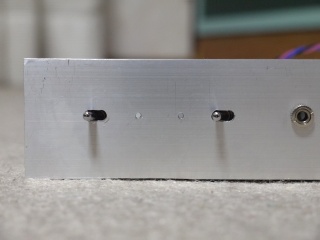 |
|
|
2つ目のサブパネルを切り出して加工し2つのトグルスイッチを取り付けて所定の位置に固定しました。 間の大きな穴にはLEDを通します。
|
|
それを前面から見たところ。 このアンプでは3個のトグルスイッチは横方向に操作します。
|
|
|
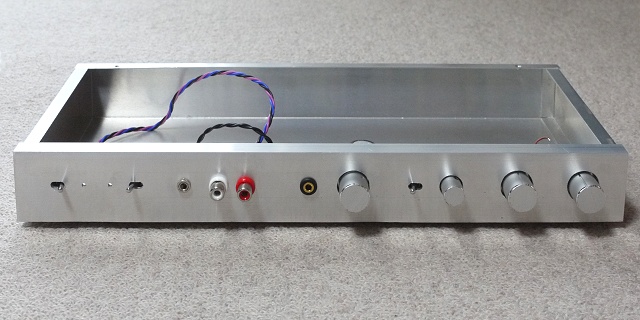 |
|
|
残る作業はヘヤーライン加工、文字入れ、ニス塗装となったフロント部分。 一番操作頻度が高いと思われるヘッドフォーンジャックとそのレベル調整が真中にあります。 その左側のRCAピンジャックとミニフォーンジャックは排他使用の入力端子です。
|
|
|
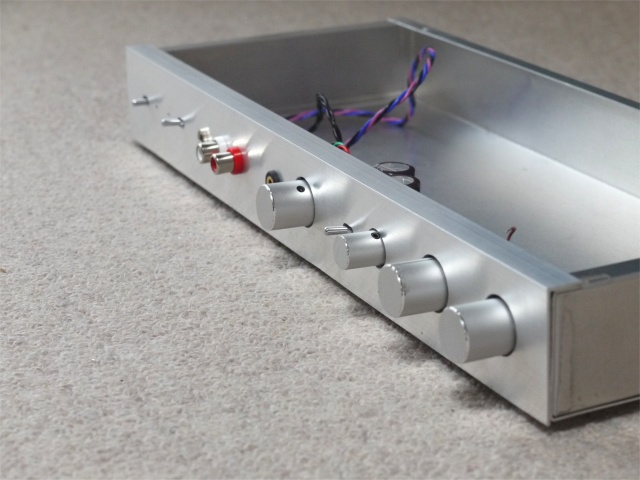 |
|
|
斜め右からみた所ですが、フロントパネルの右端は固定されていないので若干浮いています。 最終的には数箇所に両面接着テープを貼って固定します。
|
|
作業中に緊張を強いられることはこの後の作業では殆どありませんので、作業速度も上がって来るでしょう。 ケース加工の残るは、4つの基板の固定、放熱板の固定、側板固定穴あけ、天板の加工、底面と天板に放熱の穴あけです。
|
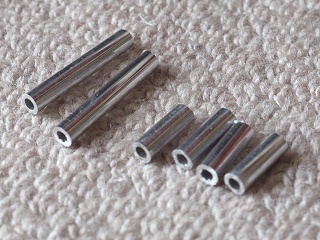 |
|
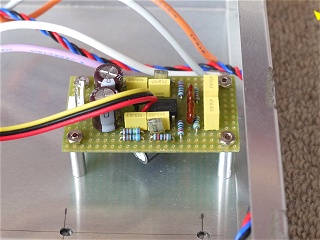 |
|
|
手元には15mm、30mmのスペーサーが無かったので、ホームセンターで売っていたアルミのパイプ(外径5mm、内径3mm)を切断して自作しました。
|
|
大きな裏付け部品のあるイコライザー基板は15mmのスペーサーで少し浮かしています。
|
|
|
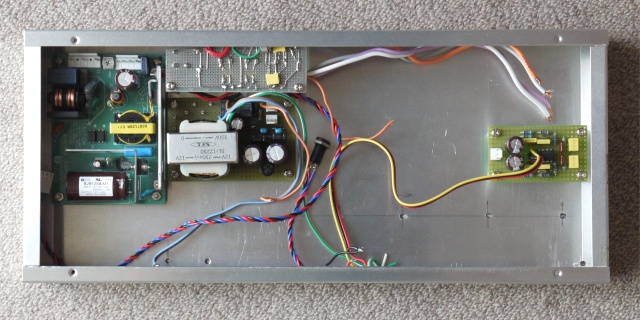 |
|
|
残りの30mmスペーサーはパワーアンプ基板を逆さに固定するのに使いました。 これが前面の細長い基板を除く全ての基板を固定した状態です。
|
|
|
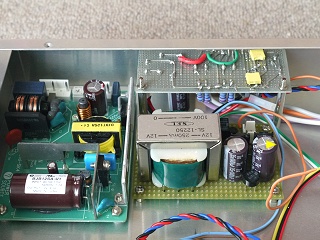 |
|
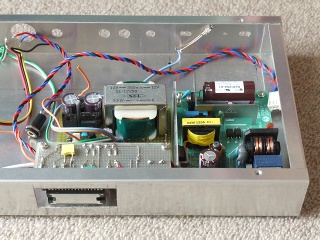 |
|
|
一番混みあっているのはこの部分で、最も熱が発生する部分でもあります。
|
|
それを前後反対にして見たところです。 手前左にシャーシの切り欠きがありますがこれはパワーICを放熱板に直接固定するための窓です。
|
|
|
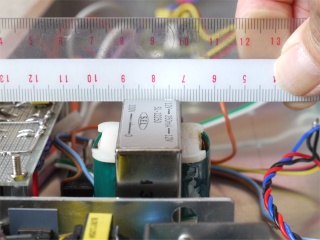 |
|
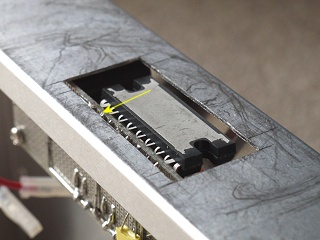 |
|
|
確認した問題点1。 電源トランスがシャーシより1.5mmほど出っ張ります。 現在スペーサーは5mmを使っていますが、薄いスペーサーには変えたくありません。
|
|
確認した問題点2。 パワーアンプ基板の配線がシャーシの切り欠き窓に接触しそうです。(黄色矢印先) ヤスリで削って窓を大きくする必要有り。
|
|
|
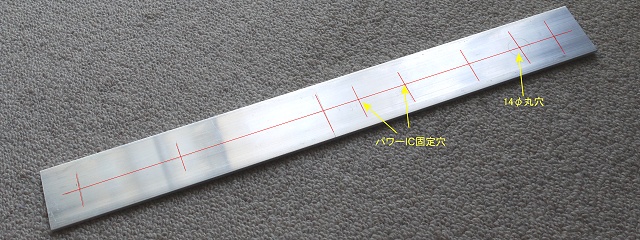 |
|
|
幅40mm、厚さ3mmのアルミ板を所定の寸法(350.5mm)に切断しました。 これに8個の穴をあけますが、シャーシと一緒に全ての穴を2.5φであけます。 そして14φと記した穴をのぞき放熱板側の穴は全てM3のネジを切ります。 一方シャーシ側はネジ穴の位置にある穴は3.2φに拡大、シャーシの放熱板の14φに相当する穴は9φに拡大します。
|
|
|
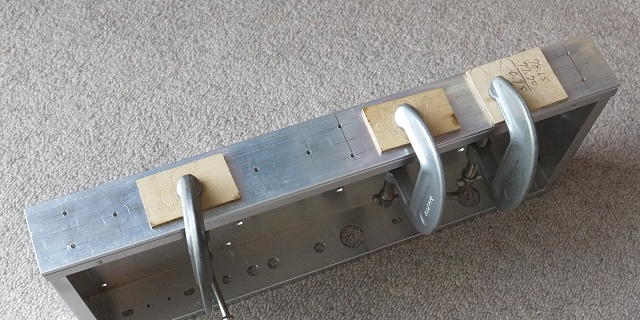 |
|
|
放熱板をシャーシ背面にクランプでしっかりと固定した上で穴あけ開始。 全ての穴を2.5φ貫通穴とします。 その後ばらしてそれぞれの穴を最終的な大きさ、或いは雌ネジ切りなどをします。
|
|
|
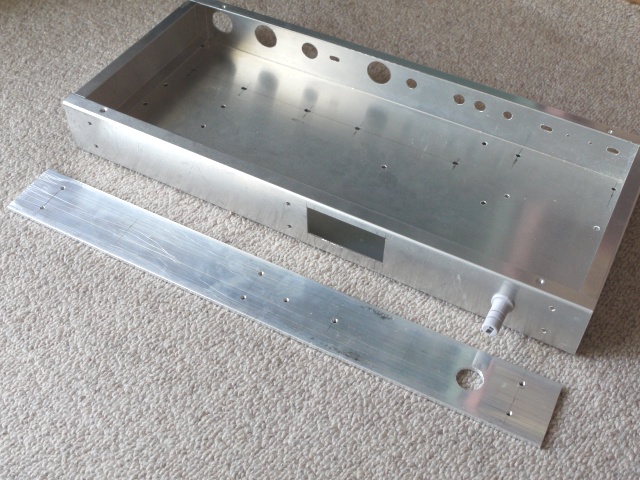 |
|
|
穴あけ、タップ立てが終わったシャーシと放熱板。 シャーシにコードブッシュを取り付けてあります。
|
|
|
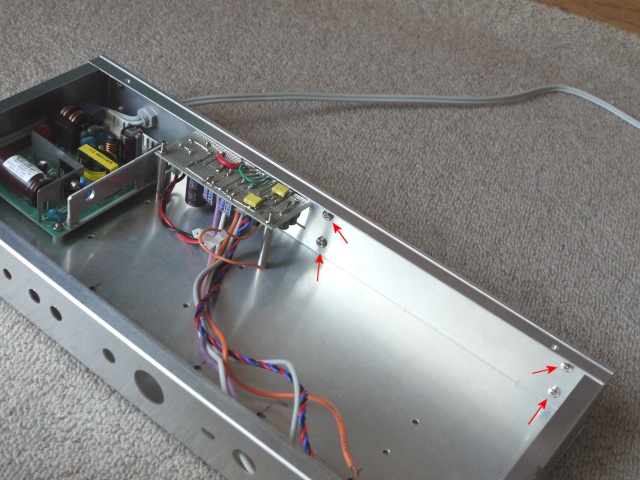 |
|
|
シャーシに放熱板を当てて内側から6個のM3ボルトで固定。 その後パワーアンプICを固定しアンプ基板を固定しました。 またACコードの干渉具合を見るためスイッチング電源基板も取り付けました。
|
|
|
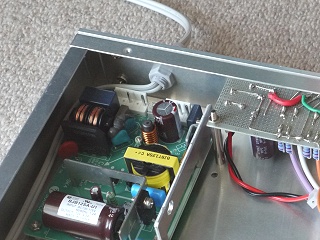 |
|
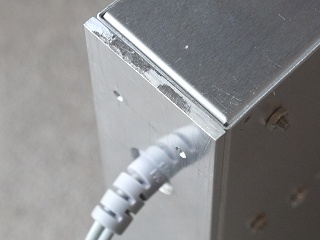 |
|
|
電源コードは90度折り曲げてスイッチの方に引き回しますが、スイッチング電源に干渉して問題を起すような事はなさそうです。
|
|
放熱板のシャーシへの固定の様子。 電源コードブッシュはシャーシに固定され放熱板には接触していません。
|
|
|
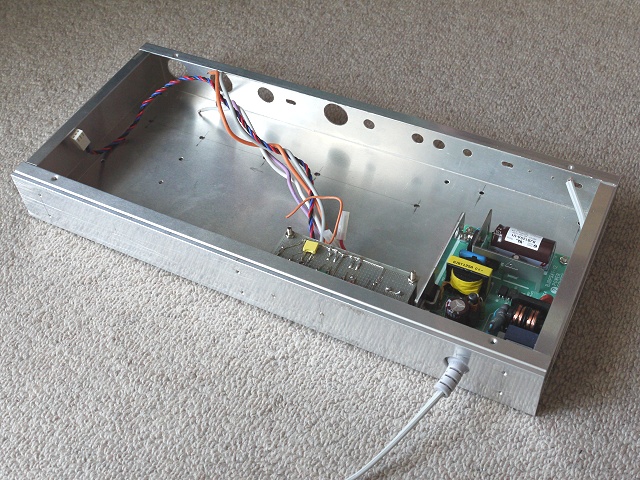 |
|
|
背面には放熱板をシャーシに固定するネジ穴とパワーICを固定するネジ穴が合計で8個見えます。 外観を尊重してこれらを埋めて隠すてもありますが、そこまではやらないことにします。
|
|
|
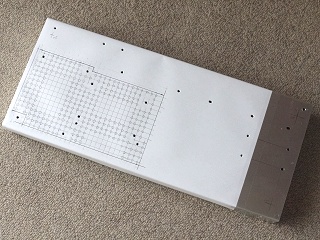 |
|
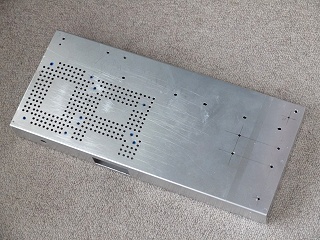 |
|
|
コピー用紙をセロファンテープで貼り付けて284個の放熱口穴位置を書き込みました。
|
|
最初に2φ、次に3.5φのドリルで穴あけをしました。 おおむね良好なのですが、284個中7個は1mm程度すべった状態であいてしまいました。
|
|
|
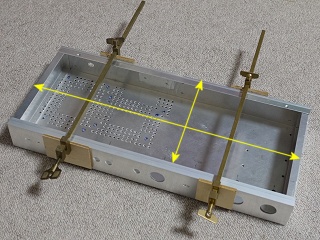 |
|
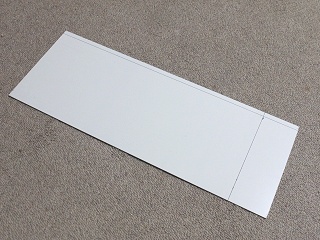 |
|
|
アルミ天板の寸法を現物合わせで決定します。 この目的でフロントパネルと放熱板を2本のハタ金で仮固定しました。 そして矢印の寸法を測ります。
|
|
1mm厚のアルミ板に測った寸法どおりの墨線を引きます。 秋葉で売っているアルミ板には片面に薄いビニールを貼った物がありボールペンで描けるので、大変便利です。
|
|
|
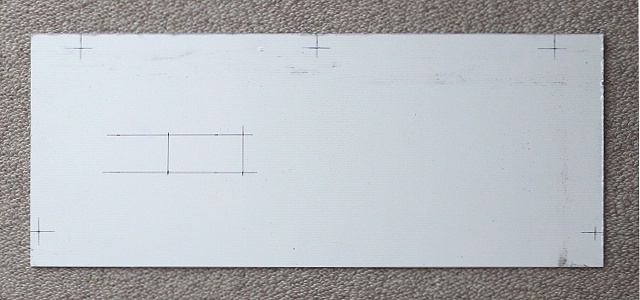 |
|
|
ジグソーで切断後に替刃式ヤスリ(M-20GP)で切り口の仕上げ研摩をしました。
|
|
|
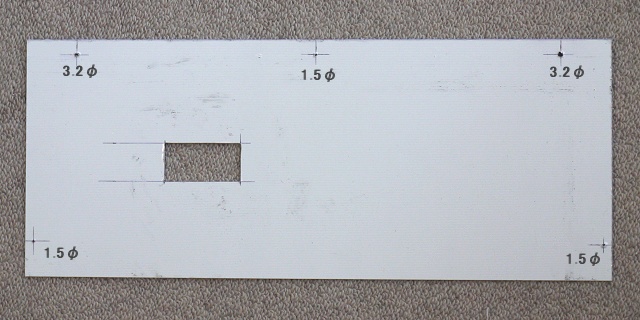 |
|
|
3.2φの穴は位置の微調整をしながら3.5φ程度にヤスリで拡大します。 1.5φの穴はこの後シャーシに固定した後に1.5φ貫通穴をあけます。
|
|
|
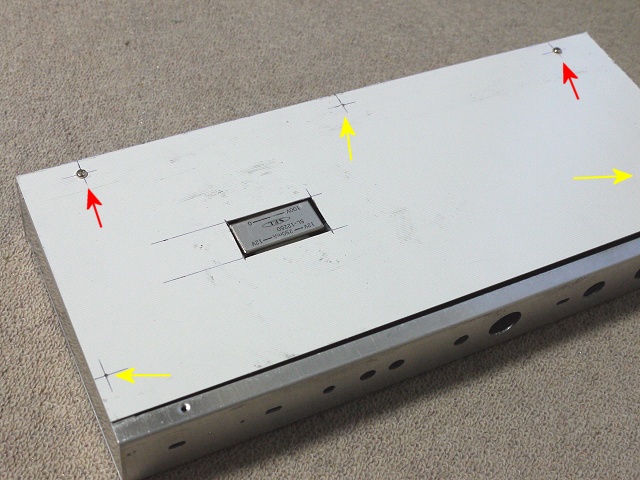 |
|
|
2本のネジでシャーシに固定しました。(赤矢印) そして1.5φの貫通穴(黄色矢印)をあけてアルミ板を外し、アルミ板の1.5φの穴を3.5φに拡大、シャーシにあけた3個の1.5φの穴は2.5φに拡大します。
|
|
|
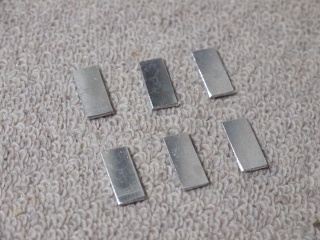 |
|
 |
|
|
1.5mm厚アルミ板から 9 x 20mmの板を6枚切り出します。 これは雌ネジを切る部分を厚くしてやるためで、接着後に2.5mm厚となります。
|
|
底の4隅中3隅にエポキシ接着剤で貼り付けています。(赤矢印はその内の2つ)
|
|
|
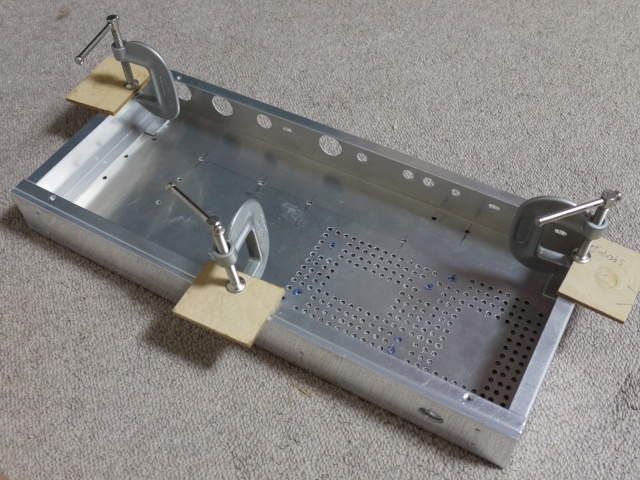 |
|
|
小さなC型クランプで固定してるのはシャーシ上部の折り返し部分にあけたネジ穴で3箇所あります。 これで接着剤が完全硬化するまで待ちますので一晩寝かしました。 その後1.5φのドリルで貫通穴をあけ、更に2.5φのドリルで穴を拡大した後にM3のタップでネジを切りました。
|
|
|
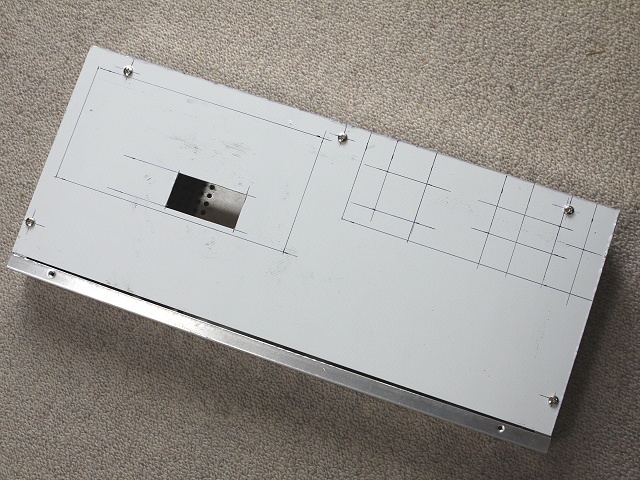 |
|
|
確認のためアルミの天板をシャーシに載せて5本のネジで仮止めしました。 天板が固定される位置も正確になっており問題はありません。 天板に新たな線が沢山描かれていますが、スピーカーターミナルとRCAピンジャック等の穴位置です。
|
|
|
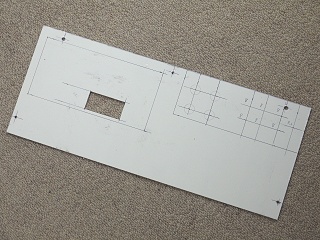 |
|
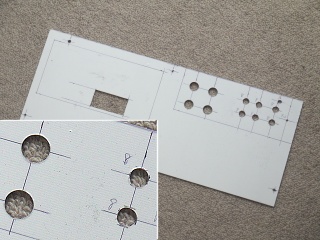 |
|
|
穴の中心線だけでは心許ないので、スピーカーターミナルは直径12mmの円を、RCAピンジャック用は8φと直径を書き加えました。 そして最初は1.5φ、次に2.5φ、最後に6.5φのドリルで穴を広げます。
|
|
スピーカーターミナル用の穴は12φ、RCAピンジャックの穴は8φになるよう丸棒ヤスリで広げますが、大きい12φは替刃式ヤスリのRS-310P(mini-Shopで販売中)が使え、かなり細かな研摩面になります。 こんな日曜大工用の道具が金工にも役立つのは大変便利です。
|
|
|
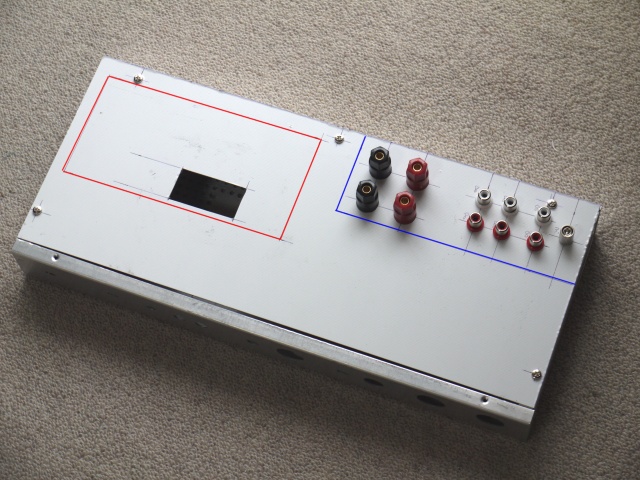 |
|
|
スピーカーターミナル、RCAピンジャック、アースターミナルを念のため仮止めしました。 赤線を引いてある内側は天板の放熱口があけられるエリアで、後ほど300個程の3.5φの穴があきます。 また青の線は木製天板の切り欠き部分で、このエリアのアルミ天板が露出します。 尚これを見ると想像が付くと思いますが、最終的なワイヤー接続はスピーカーケーブル、アースケーブルの接続部分にバナナプラグを使うと、上又は下から差し込むだけで接続が終わります。 何れにせよ背面を覗き込むことなく接続できます。
|
|
|
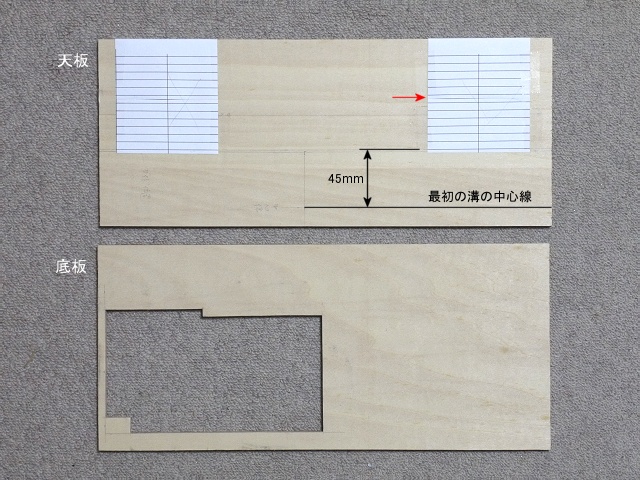 |
|
|
上の寸法図に従い作業開始。 先ず天板と底板を切り出しました。 そして天板にはトリマーのガイド板を当てるスケールを髪に印刷して貼り、底板は空気取り入れの穴をあけました。 スケールは6mm間隔で13本の線を引き、一番後ろ側(写真では下側)の溝の中心線とスケールの最初の線の間が45mm(電動トリマーの台座の幅の半分)にしてあります。 またスケールは赤矢印のところで上下に分割され、7本の溝を彫ったら下側のスケールは剥がします。(スケール下半分を研削するようになるので。)
|
|
|
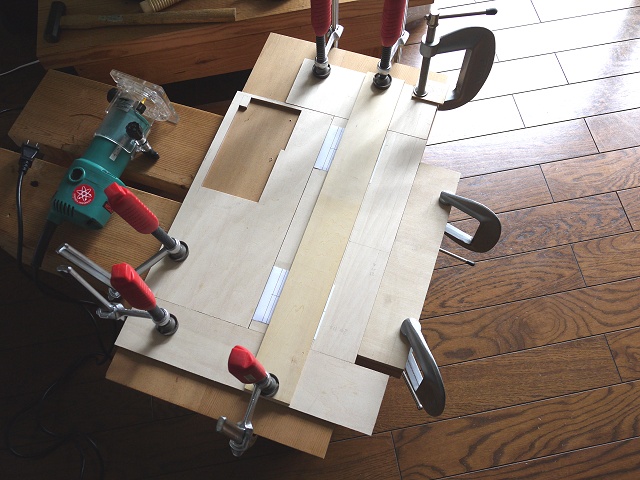 |
|
|
加工する基板の全周を同じ厚さの板で囲み動かないようクランプを合計8個も使って固定しています。 大袈裟なようですが電動トリマーを移動したときにクランプに干渉しないようにした結果です。 ガイド板はスケールの一番右の線に合わせています。
|
|
|
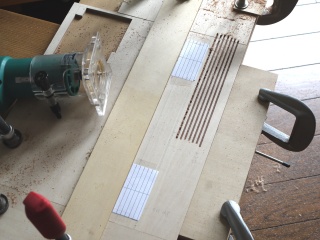 |
|
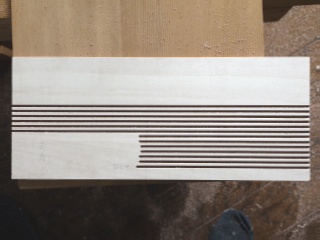 |
|
|
3mmのストレートビットを深さ2.5mmにセットして7本の溝を切削しました。 ここでスケールのほぼ右半分は取り除きます。
|
|
残り6本の溝は天板の横幅いっぱいに切削します。 このあと左下の部分を切断します。
|
|
|
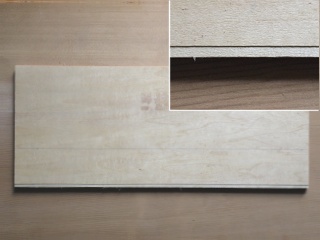 |
|
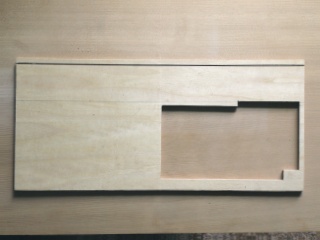 |
|
|
天板をひっくり返して前側の3mm幅を0.2mm座繰りました。 これはアルミフロントパネルが1.2mm厚、アルミ天板が1mm厚の差を被せ面で補正するためです。(右上はその部分のクローズアップ)
|
|
底板の内面の全面にはフロントパネルが落とし込まれる溝を彫りました。 1.6mmのストレートビットを使って深さ1.5mmで彫っていますが、前後の位置はフロントパネルの全面が溝の壁面に当るようにします。
|
|
|
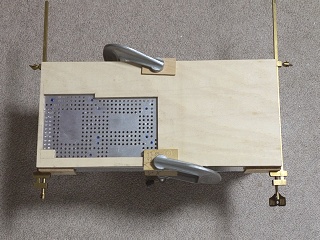 |
|
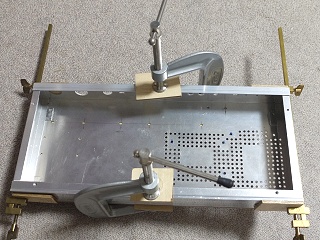 |
|
|
底板の次の加工は底板固定の4つの穴あけと固定ネジの頭を隠す座繰り穴の位置決めです。 先ず底板を所定の位置になるよう十分確認の上でハタ金とC型クランプ各2で固定しました。
|
|
そしてシャーシの内側からシャープペンでネジ穴にマーキングを施します。 穴はゴム脚固定用4個と基板・サブパネル固定ネジ穴12個の合計16個あります。
|
|
|
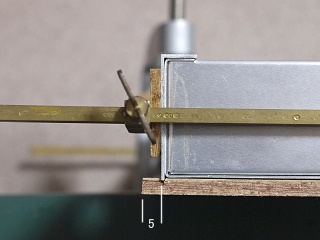 |
|
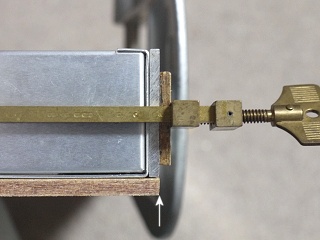 |
|
|
底板取り付け位置決めの大事な所。 フロントパネルの下部は底板に彫られた溝に落としこまれ、フロントパネルと底板全面とは5mmの差があります。
|
|
もうひとつは底板背面先端で、放熱板の面と一致するはずです。
|
|
|
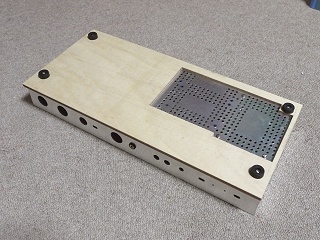 |
|
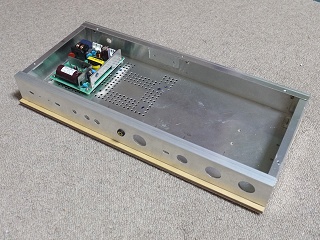 |
|
|
ネジ頭隠しの座繰りはU字型ビットで後ほどしますので、取り敢えず底板取り付けの問題が無いか確認しました。 ゴム脚4個の止めネジでゴム脚・木製底板・シャーシが共締めされます。
|
|
ひっくり返したところ。 ゴム脚固定ネジの1本はスイッチング電源基板固定ネジの1本にもなりますので、確認のため仮締めしました。
|
|
|
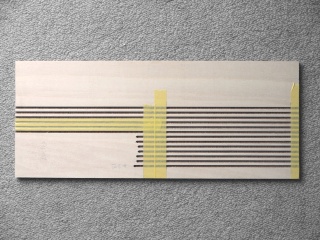 |
|
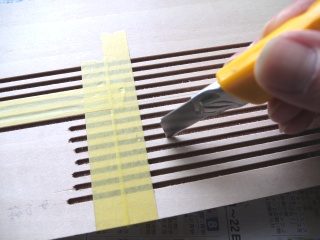 |
|
|
次が天板の加工です。 マスキングテープで溝貫通部分とその後の切断位置を明確にしておきます。
|
|
溝の貫通切断は大きいカッターナイフのみでやりました。(刃の切れ味を維持するため2回刃をおりましたが。)
|
|
|
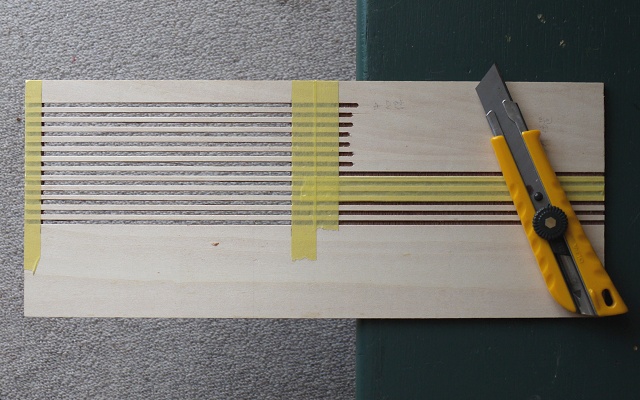 |
|
|
貫通穴あけが終わりました。 このあと工作用の3mm厚の金工ヤスリで切断面を研摩しました。(研摩しておかないと後の塗装がしにくい。)
|
|
|
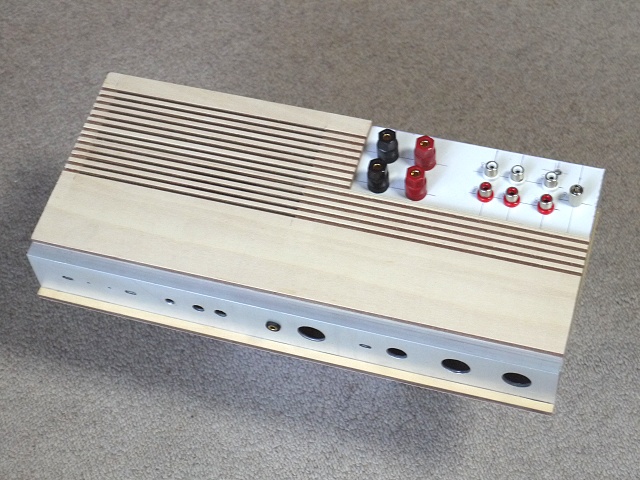 |
|
|
そして替刃式ノコギリ(翔220)でL字型の切断をし、その切断面を替刃式ヤスリで仕上ました。 アンプ本体の所定の位置に重ねています。
|
|
|
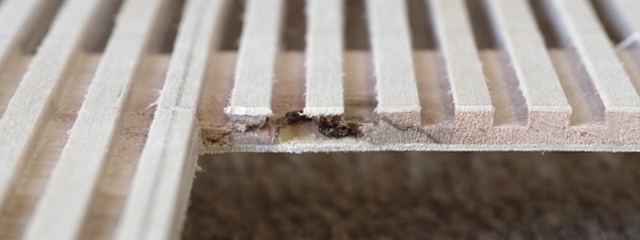 |
|
|
無事溝の切削は終了!と言いたいのですが、私の加工ミスではなく材料の芯材に荒れた部分があったため、溝彫り時に芯材の欠けが発生しました。 この面は艶消し黒で塗りつぶす為後ほどウッドエポキシで埋め込み修正します。 どうも運にも見放されたかな?という心境です。
|
|
|
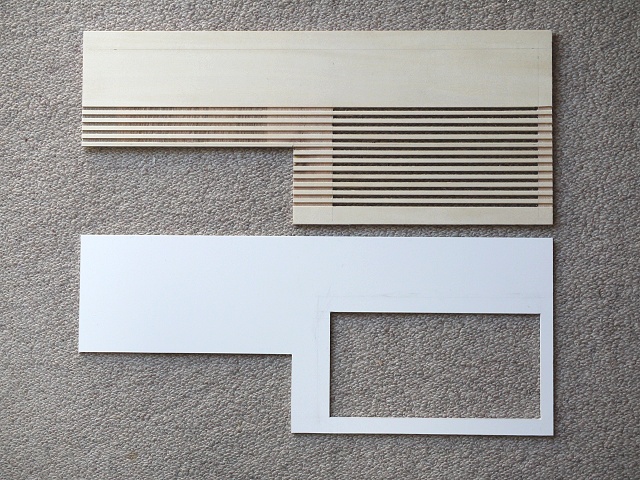 |
|
|
超スローペースで作りなおした木製天板と低発泡塩ビ板。 塩ビ板にあけた大きな穴は木製天板のスリット状抜き穴を覆いません。 これらを60分硬化開始型エポキシ接着剤にて貼り合わせ完全硬化をねらって一晩寝かせました。
|
|
|
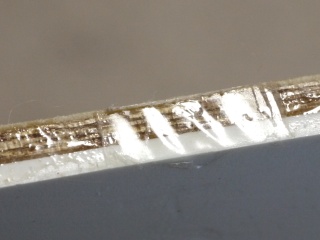 |
|
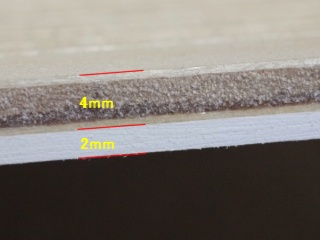 |
|
|
接着後完全硬化するまで寝かせた後の側面。 光っているのははみ出て固まったエポキシ接着剤です。 後ほど側板を当てて現物合わせで研摩します。
|
|
前と後の貼り合わせ面と欠き取り部分はこのように平らになるよう、且つ所定の寸法になるよう研摩しました。 少しずつ確認しながら進めたので4時間ほど掛かっています。
|
|
|
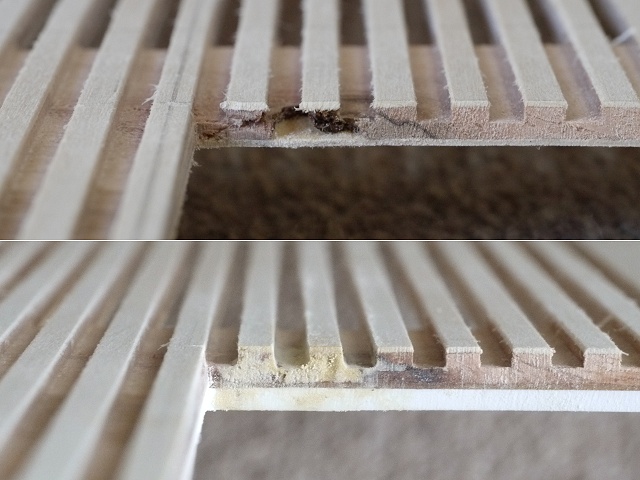 |
|
|
芯材がぼろぼろに欠けてしまった部分の修復を致しました。 上が修復作業前、下が修復作業後ですが、材料はウッドエポキシで2種類の粘土のような材料を等量混合し充填部分に若干溢れるくらいに埋め込みます。 その後12時間後くらいに溢れた部分をカッターナイフで削り取り、更に12時間後にヤスリで研摩して仕上ます。 ウッドエポキシは1週間で完全硬化となりますが、そうなると切削・研摩は極めて難しくなります。
|
|
|
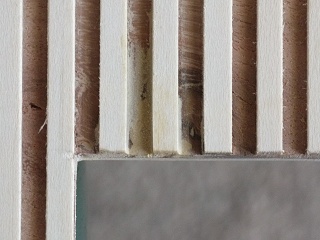 |
|
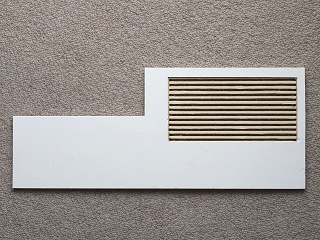 |
|
|
修復部分を真上から見たところ。 ウッドエポキシは木工パテ同様木目を潰しますので使う部所は良く考える必要があります。 このようにニスを塗る表層部分には付着していません。
|
|
貼り合わせと修復作業が終わった木製天板をひっくり返しました。板の部分は2mm引っ込んだ状態になります。
|
|
|
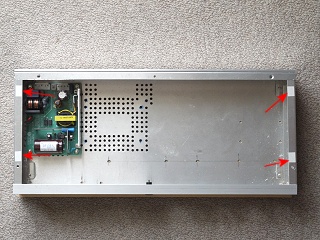 |
|
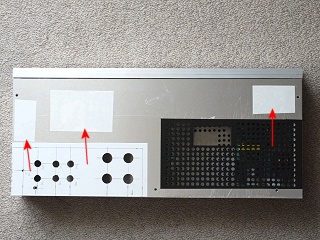 |
|
|
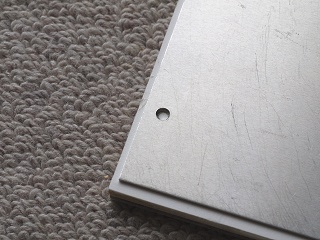 |
|
左上はアルミ天板の位置が横滑りでずれるのを防ぐ為小さく切った両面接着テープをシャーシの折り曲げ部分に貼った所です。
上の写真は180度回転していますが、アルミの天板を所定の位置に載せた所です。 軽くシャーシに押し込んでやれば横方向にずれなくなります。 そして木製天板を仮止めするために大き目の両面接着テープを数箇所貼っています。
その後そっとアルミ天板と木製天板を貼ったまま持ち上げてひっくり返し、4箇所の穴の位置に貫通穴をあけてやれば、ドンピシャの位置に固定ネジ穴があくという次第です。
|
|
|
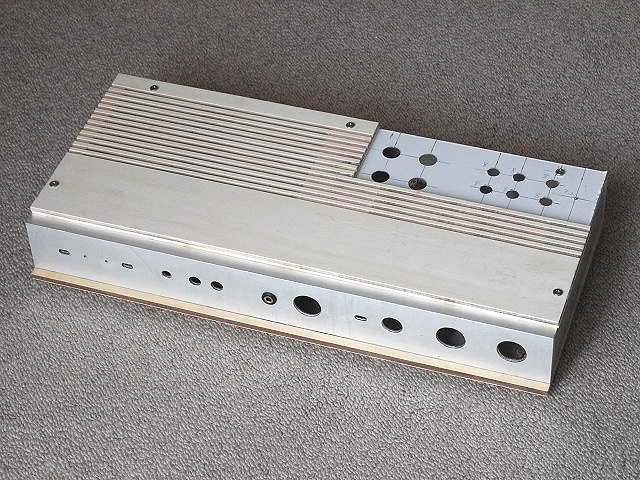 |
|
|
あけた穴に例の薄い頭の飾りネジを使い天板をシャーシに固定しました。 ターミナル部分の保護シートはインスタントレタリングで文字入れするまで傷防止の為剥がしていません。 この両サイドに側板を当てて天板と底板の幅を微調整カットすれば、箱作りは終了します。
|
|
|
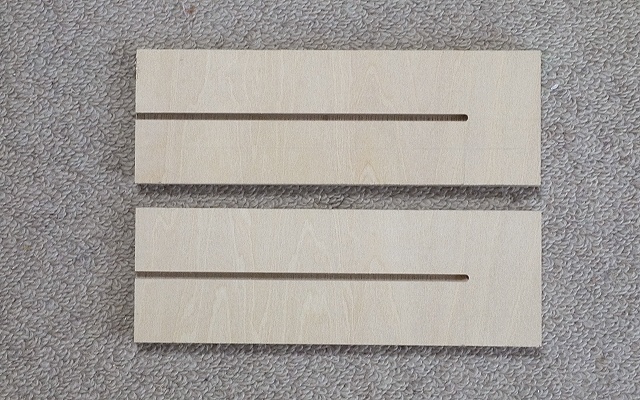 |
|
|
溝彫りをしてから所定の寸法で切り出した側板。 左側が後側になります。
|
|
|
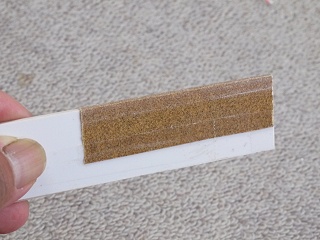 |
|
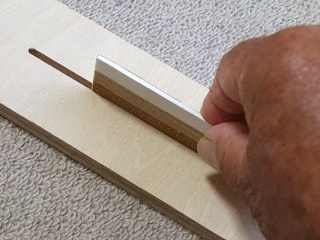 |
|
|
彫った溝の内面を研摩するヤスリ。 2mm厚の塩ビ板に#240のペーパーを巻きつけてセロファンテープで止めた物です。
|
|
こんな具合に側面と側面を研摩できます。 次に#400ペーパーに変えて研摩すれば完璧です。
|
|
|
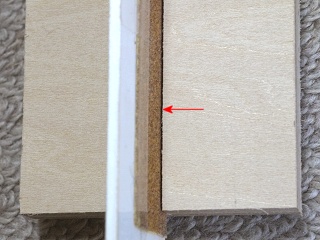 |
|
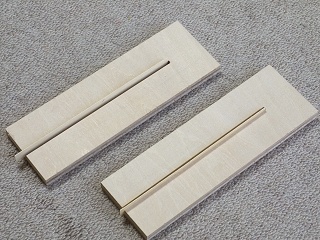 |
|
|
研磨中に発見したことですが、ペーパーを巻きつけると厚みは2.5mmになります。 そうするとここに見える隙間は0.5mm。 具合の良さそうな隙間です。
|
|
研摩終了後に木口テープを貼り付けました。 この写真の左側が左の側板、右が右側の側板になります。 そしてはみ出た部分をカッターナイフで切断してペーパーで軽く研摩します。
|
|
|
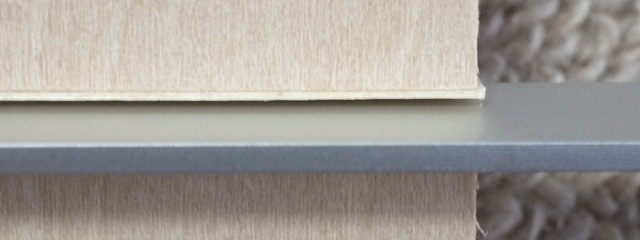 |
|
|
一応確認の為にレールとなるアルミ棒(2mm厚)を入れてみました。 反射のために隙間部分が実際より黒ずんで隙間幅が広いように見えますが、0.4-0.5mm厚の紙を挿し込むときついので実隙間が判ります。
|
|
|
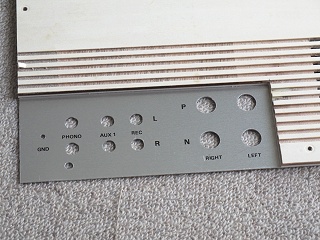 |
|
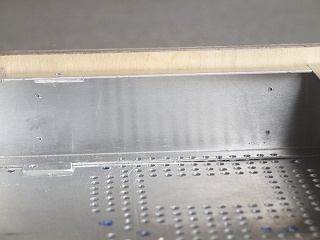 |
|
|
ターミナルが固定される面の保護シートを剥がし文字入れをした上で水性ウレタンニス透明クリヤー2回塗りで仕上げました。(こうしないとアルミ面の綺麗さが維持できません。)
|
|
シャーシ側面4箇所に1.5φの穴をあけました。 穴位置はそれほど正確でなくてもOK。
|
|
|
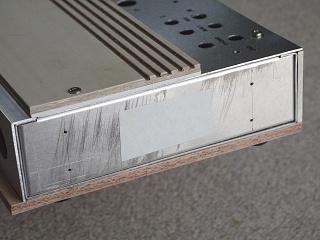 |
|
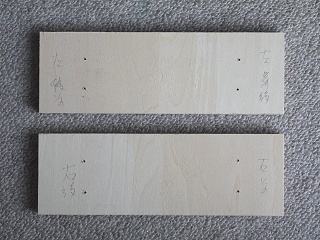 |
|
|
シャーシ側面に両面接着テープを貼り付けました。 これは後ほど剥がすので前面貼り付けでなくてよいです。
|
|
その上から側板を当てて位置を十分調整の上貼り付けます。 そして1.5φのドリルで内側から側板にマーキングをします。 この写真はマーキングが終わった所です。
|
|
|
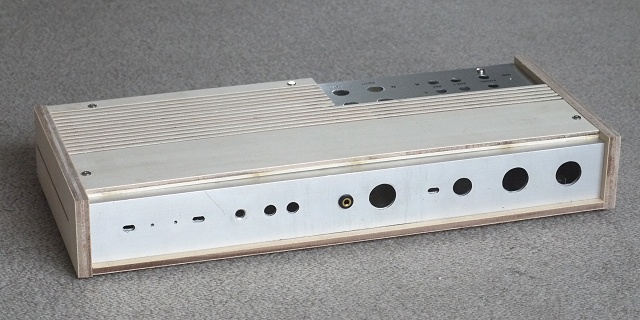 |
|
|
シャーシ側面の穴は1.5φから3.2φに拡大し側板を当てて内側からネジ止めします。 側板の1.5φの穴がネジ止めの下穴となるので、正確な固定が出来ます。
|
|
|
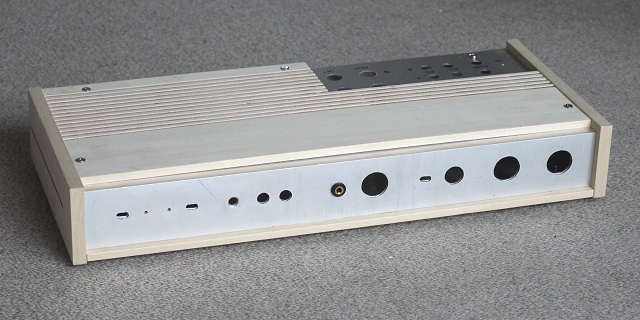 |
|
|
全ての切断面にシナの木口テープを貼りお化粧をしました。 これによってムク板で作ったかのような外観に変貌します。
|
|
|
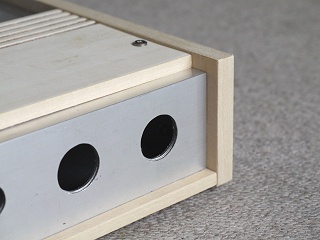 |
|
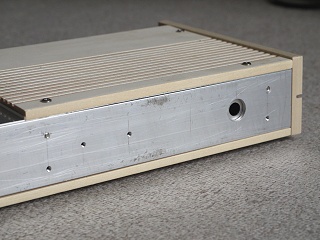 |
|
|
前面右側のクローズアップですが。妙な隙間がなくぴったりと収まっています。
|
|
背面の様子ですが放熱板には細かな傷が沢山ありますので、研摩してそれらを消した上でペイントで塗りつぶそうと考えています。
|
|
|
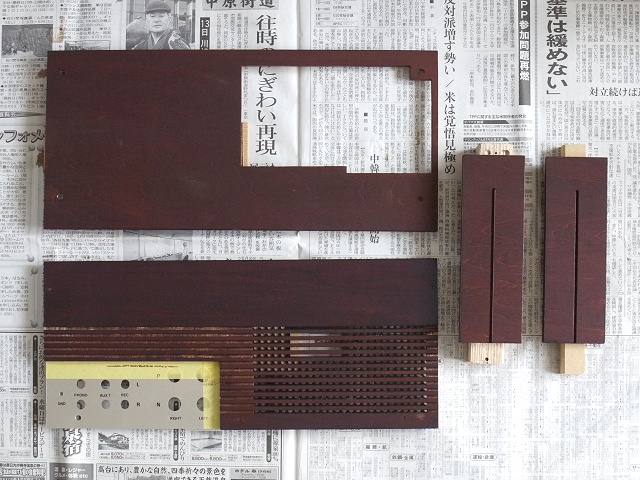 |
|
|
塗装作業の1番目はオーク色のポアステインを水で2倍に薄めたもので5回着色しています。 木目はほんの僅かしか見えなくなりますので、樹種が何かは判り難いです。 そして重厚な感じになります。
|
|
|
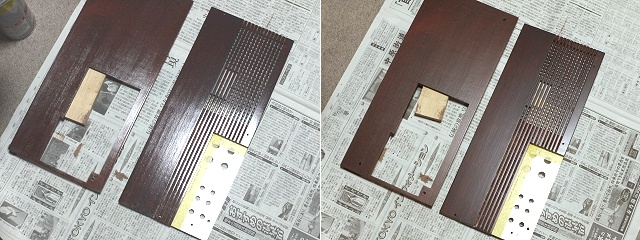 |
|
|
左は水性ウレタン透明クリヤーを3回塗りした状態。 かなり艶が出ていますが表面が平らでないので、あまり上品な艶ではありません。 そして右は水性ウレタン艶消しクリヤーを2回塗った所です。 艶が抑えられて表面が平らでない難点が隠され上品で深みのある感じになりました。 これが正に狙っていたものです。
|
|
|
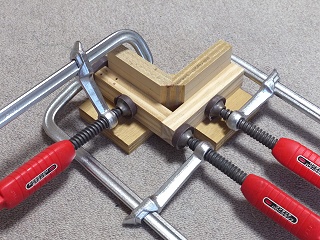 |
|
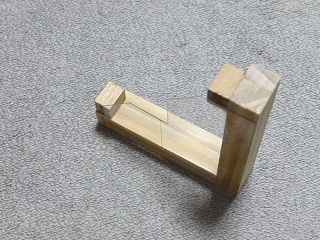 |
|
|
自作90度接合ジグを使って2本の棒をL字型に接着中。 何とも大袈裟なクランプによる保持ですが、正確に90度を得て密着度の高い接着には不可欠のやりかたです。
|
|
L字型先端に爪を接着しました。 そして2等辺三角形の形をしたプラスチック板をエポキシで貼り付けました。 そして設定線を十字状に入れましたが、ここでは見えないので次の写真をご覧下さい。
|
|
|
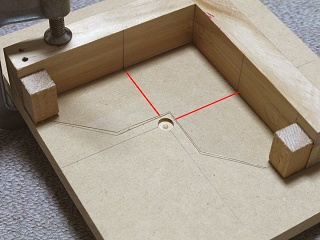 |
|
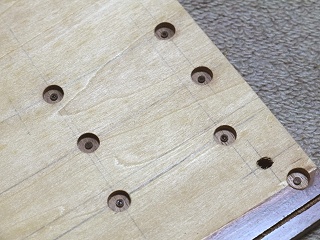 |
|
|
赤い線を引いて判りやすくしましたが、これがジグ状の設定線です。 その線を板に引かれた墨線に一致するようジグを当ててクランプで固定します。 あとはトリマーを挿入すればご覧のとおり座繰り穴があきます。
|
|
実際に底板に穴をあけ終わった状態です。 8φのストレートビットを使っていますが、中心の直径2mm位は完全に切削されないので、3mmのノミを使ってこの後削り取りました。
|
|
|
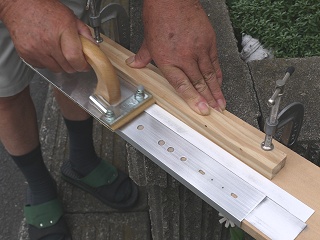 |
|
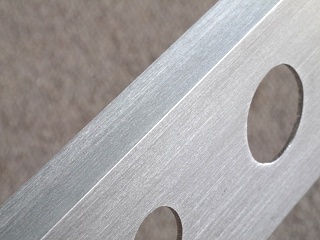 |
|
|
ヘヤーライン加工をしている所。 サンドペーパーは#400を使っています。 これが終わったら研摩かすを水で洗い落とした方が良いです。
|
|
ヘヤーラインのクローズアップ。 大変細かな目になっています。 また折り曲げ角はシャープになっております。
|
|
|
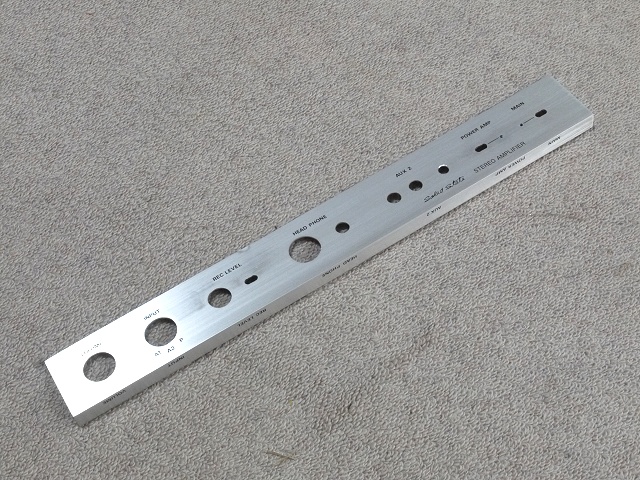 |
|
|
そしてインスタントレタリングで文字入れをしましたが、普通に較べ文字の量は2倍あります。
|
|
|
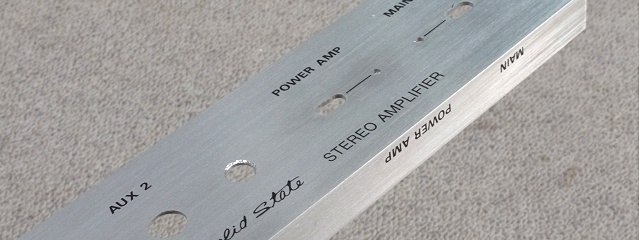 |
|
|
テーブルトップで使う時の為の表示がフロントパネルの折り曲げ部分に入る為です。 この後水性ウレタンニス透明クリヤーを2回塗ってインスタントレタリングの剥がれ防止としました。
|
|
|
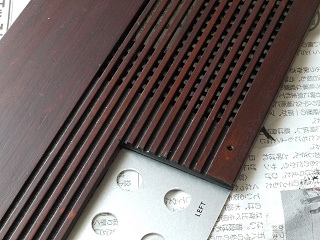 |
|
天板の溝の中は水性ペイント艶消し黒で塗りつぶしました。 方法としては少々固めの工作用筆で大目に含ませたペイントをつぎ込むような格好で短時間の内に塗りつけます。
デリカシーのないやり方ですから表面に沢山付着しますがそれらが乾燥しない内に濡れ雑巾で拭き取ってしまいます。 乾燥しないうちに拭き取らないとならないので、一回辺りの塗りこみは溝1本が限度です。 濡れ雑巾は真っ黒に汚れ他に付着すると厄介ですから溝3本位を塗りこんだら水道で一度洗った方が安全です。
こうして塗り終わったら1時間ほど乾燥させてから塗りこみ状況をよく確認します。 多分完全に塗られていない部分が見つかるでしょうからその部分をもう一度塗って完了です。
この方法は水性ペイントの特性を利用した塗りこみ方で、間違っても油性ペイントを使わない事。 ペイントシンナーで拭き取ると水性ニスで塗装した部分が溶ける心配がある。
|
|
|
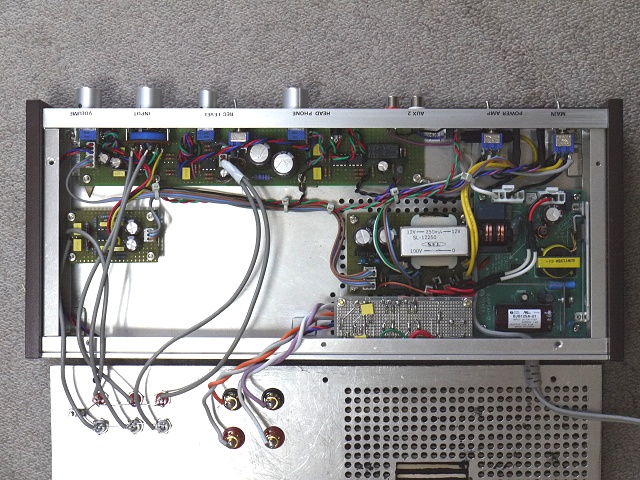 |
|
|
ケースの製作は完了しましたので早速内部に基板を組み込み配線をしました。 既にバラック状態で配線して動作確認をしていたので短時間に済んでいます。
|
|
|
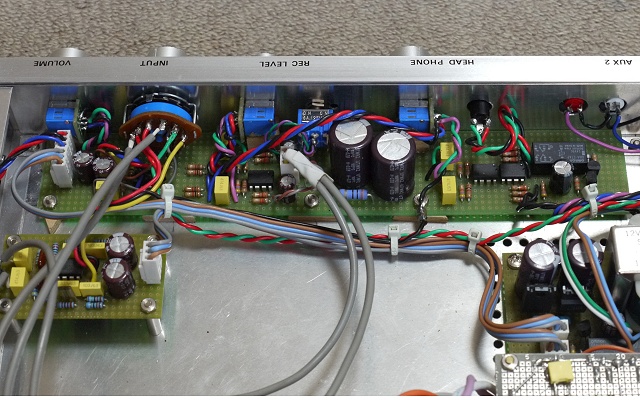 |
|
|
フロントパネル裏に配置した長い基板と電源部から離したイコライザー基板(左端)の配線の様子。 上下方向に配置される太い導線は入・出力端子から来るシールドケーブルです。
|
|
|
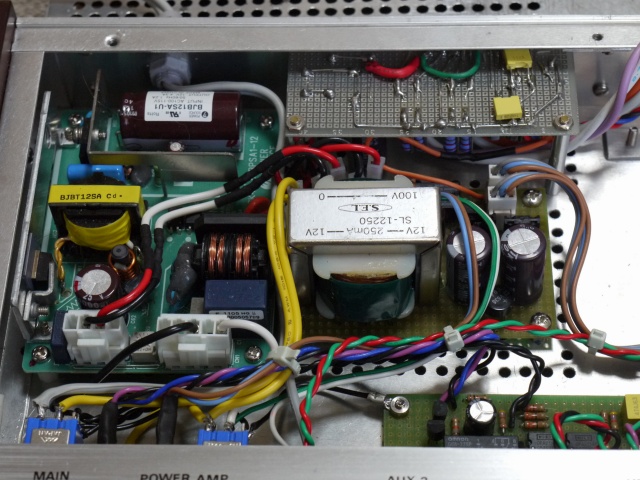 |
|
|
一番混雑しているのが電源部で、左端がスイッチング電源、中央のトランスの見える部分がリニヤー電源、その上の基板が逆さになっているのがメインアンプ基板です。
|
|
|
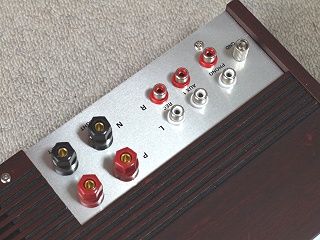 |
|
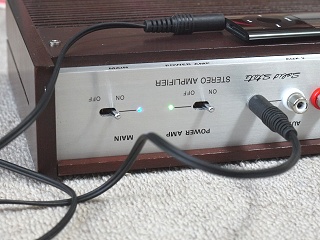 |
|
|
上面の入・出力端子群。 右上端のGND端子を除き全て挿しこむ作業で接続が完了します。
|
|
左のLEDはメインスイッチ ONで赤く点灯。 数秒後青に変化しその時点でヘッドフォーンが接続されます。 右のLEDはパワーアンプ ON後数秒経ってデジタルアンプの動作が安定したらスピーカーが接続され、緑に点灯します。(何れもショックノイズ削除機構です。)
|
|
|
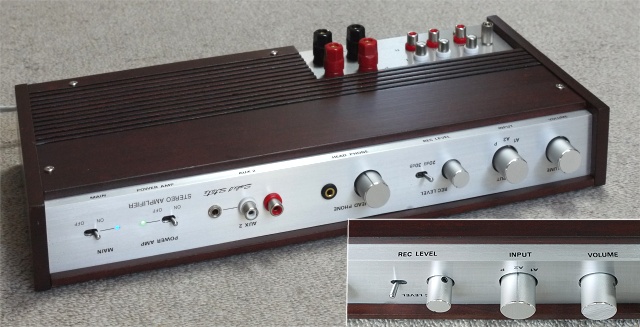 |
|
|
完成したアンプの前面の様子です。 勿論これはテーブルトップモードですから、前面に入った文字は逆さまになっています。 フロントパネル上面に入れた文字で各ツマミの機能が判ります。(右下の写真)
|
|
|
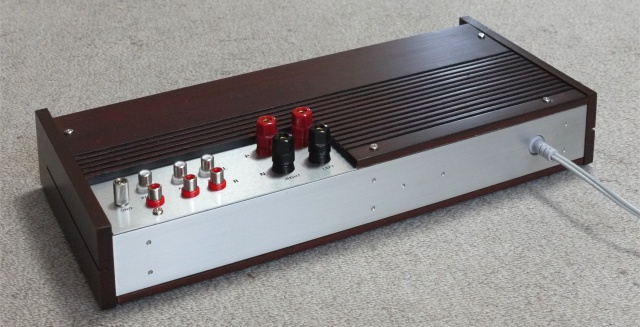 |
|
|
背面は電源コードが引き出されているだけで極めてすっきりしています。 接続は全て上面の端子でなされます。
|
|
|
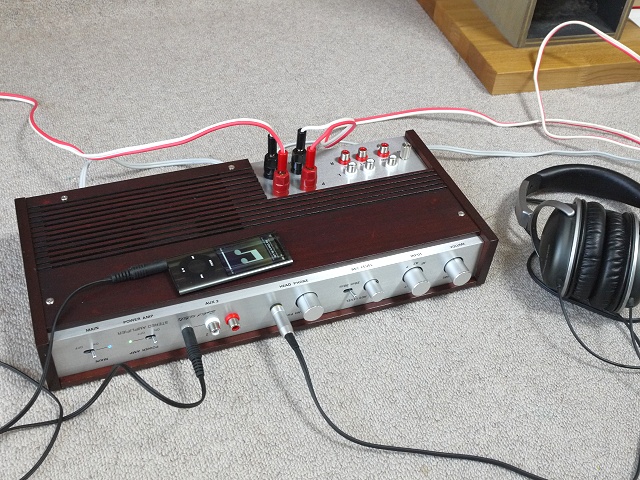 |
|
|
一通りの動作テストをしました。 スピーカーはバナナプラグを使って接続。 入力はiPod Nanoで、前面のAUX 2端子に繋ぎました。 澄み切ったパンチのある音色は爽快でした。 特筆すべきはノイズが非常に少ないことで、特にヘッドフォーンで聴くとそれが確認できます。
|
|
|
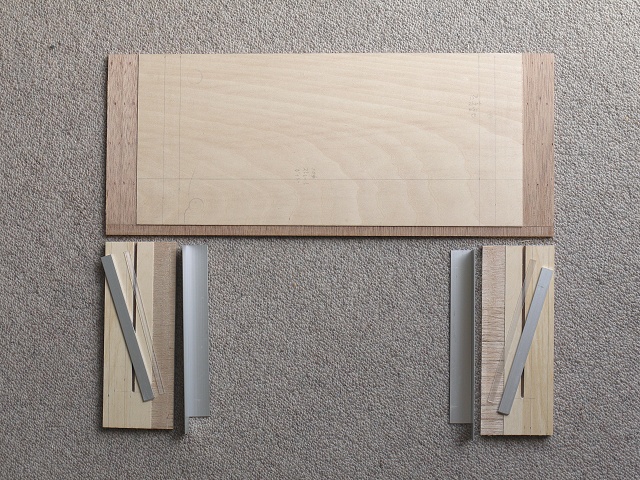 |
|
|
ブラケットを作る材料で断面がJ型の棒と1mm厚アルミの平板を除く物を所定の寸法に加工しています。 板のL字型アルミ板と断面Jの棒を接着する面は段差が出来ないようトリマーで座ぐってあります。(深さ0.8〜1.0mm) 斜めに置いてあるのは溝とレールの間に詰める0.5mm厚のプラスチック板です。
|
|
|
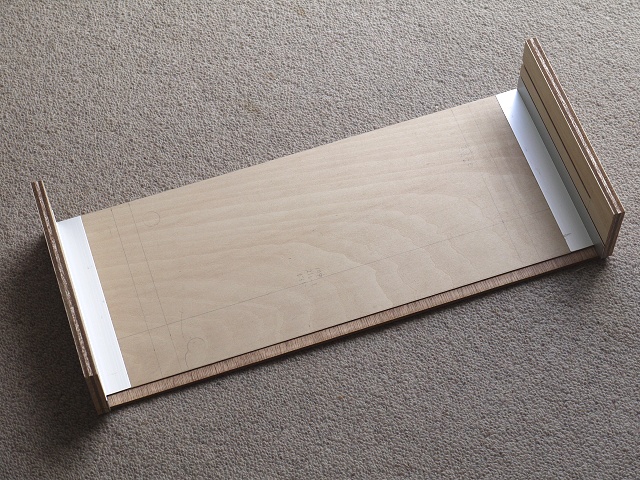 |
|
|
因みにL型アルミアングルはこのように天板と側板の接合を補強する格好で接着されます。 この写真の手前の方に座繰りが見えますが、これは後ほど断面J型のアルミ棒を貼り付ける面です。
|
|
|
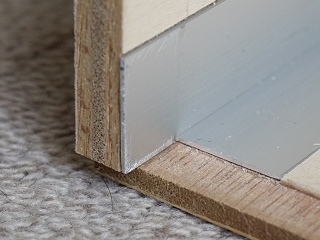 |
|
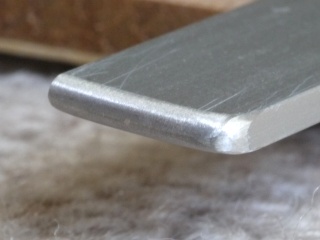 |
|
|
上の写真の左下の角のアップです。 ここにJ型アルミ棒を貼り付けると変な事になるのですが、後ほど補修致します。
|
|
これはレールに使うアルミ棒(10 x 2mm)ですが、前面の露出する部分の角はアンプ側板の溝を傷つけることなく受け入れる為、中目のヤスリで角を落とした後に#600のサンドペーパーで磨きつるつるにしました。
|
|
|
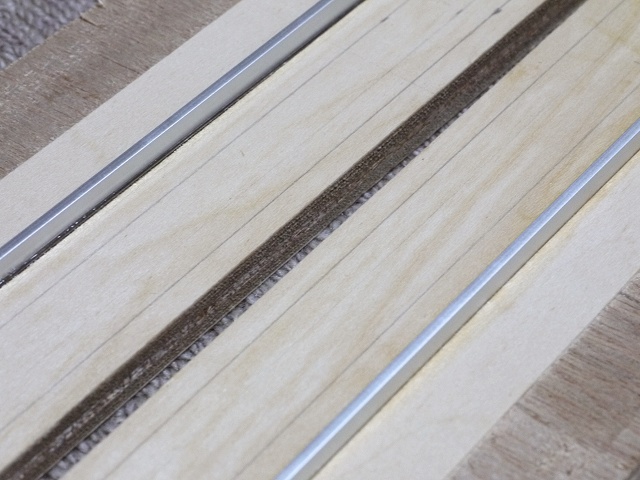 |
|
|
溝は2.4φのストレートビットで深さ5.2mmとしましたが、#120ペーパーで0.1mm強内壁を研摩し、60分硬化開始型のエポキシ接着剤を溝に流し込み楊子の先で内壁に伸ばした上でレールを落とし込み、更に0.5mm厚プラスチック板を厚入しました。 写真の左側のレールの右側は黒っぽい帯が見えますが、これは0.5mm厚のプラスチック板で、こちらが下側になります。 右のレールはプラスチック板が差し込まれていない上側ですので、黒い帯は見えません。
|
|
|
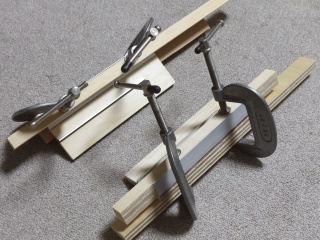 |
|
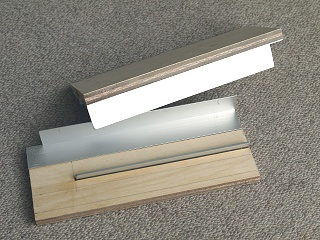 |
|
|
接着の第二ステップはL字型アルミ板の接着です。 アルミ板の表面を#120のペーパーで荒らした上で接着しクランプで15時間圧着保持しました。
|
|
こうして完成した側板ユニットです。 たった0.8mm厚のアルミLアングル材は想像していたよりも曲げ強度が高く、背面の補強板は不要になりそうです。
|
|
|
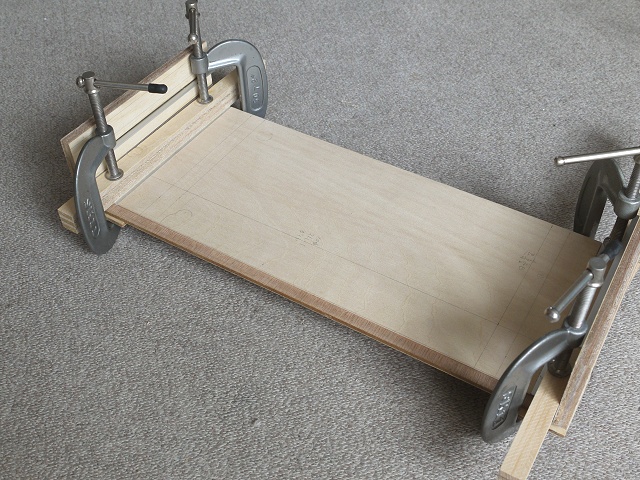 |
|
|
側板ユニットを天板の両端に接着しました。 予め正確な座繰り切削をしていますからそれに合わせてぴったりと接着しています。
|
|
|
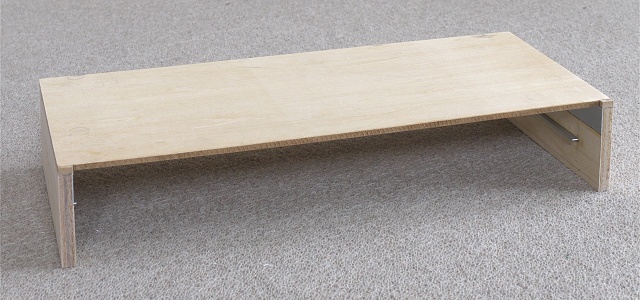 |
|
|
15時間後にクランプを外しコの字型の内側の寸法を測りましたが、手前奥行とも369.5mmでした。 アンプの幅は369mmですから、それよりも0.5mm長いという設計どおりの寸法です。
|
|
|
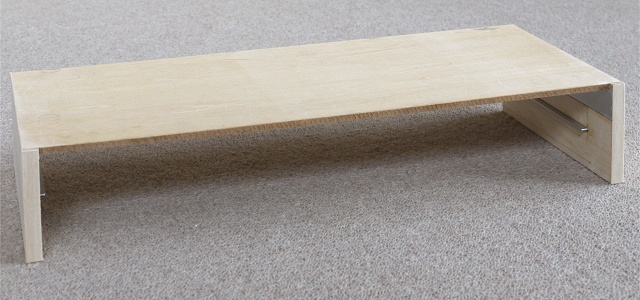 |
|
|
全ての木口と側板表面に木口テープを貼りお化粧をしました。 側板は35mm幅を2枚貼っていますので?ぎ目の線が見えますが、高濃度の着色をしますので見えなくなると思われます。(右下の写真)
|
|
|
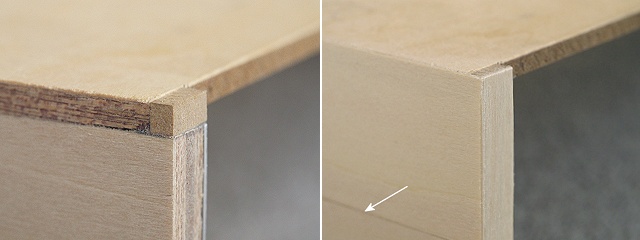 |
|
|
前の方で触れた前側の上の角の欠けた部分はMDF材を切断して貼り付け(左側)、その後木口テープで覆って修復が判らなくなるようにしています。 尚側板の木口テープの?ぎ目がうっすらと見えます。(右側)
|
|
|
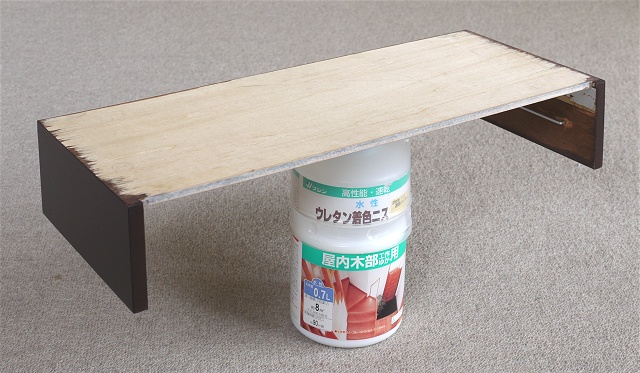 |
|
|
そしてニス塗装を済ませました。 天板トップとブラケットの内部は後ほど艶消し黒のペイントで塗りつぶします。 ニス塗装の仕様はアンプ本体木部の仕様と全く同一です。
|
|
|
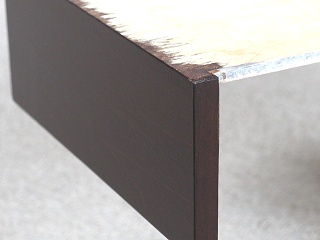 |
|
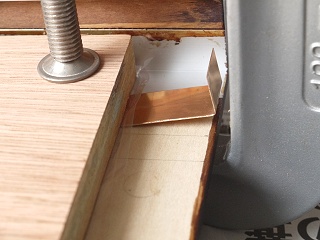 |
|
|
ブラケット左側板のアップですが、木口テープの継ぎ目は見えません。
|
|
0.4mm厚燐青銅板を切断して折り曲げた簡単なブレーキ・ストッパーをエポキシ接着剤で貼り付けました。
|
|
|
 |
|
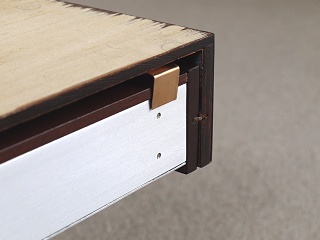 |
|
|
ブレーキ・ストッパーの全貌はこんな具合です。 矢印の先はテーパーになっているためアンプをブラケットに装填すると最後の方でアンプのゴム脚が矢印の面に擦れて重くなってきます。
|
|
ブラケットの上面と内部を艶消し黒のスプレーペイントで塗装しましたが、この光景ではアンプの後部がブレーキ・ストッパーの先端の90度に曲げた部分に当って止まる!をご覧ください。
|
|
|
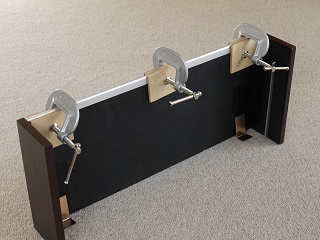 |
|
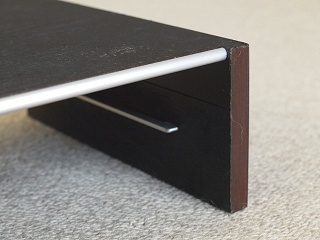 |
|
|
最後の作業は断面がJ型のアルミ棒を飾りとして接着しました。 この接着には30分硬化開始型のエポキシ接着剤を使っています。
|
|
J型のアルミ棒の接着が終わりました。 あるホームセンターを何気なく物色している時に見つけて求めた物ですが、素晴らしいアクセントになってくれました。
|
|
|
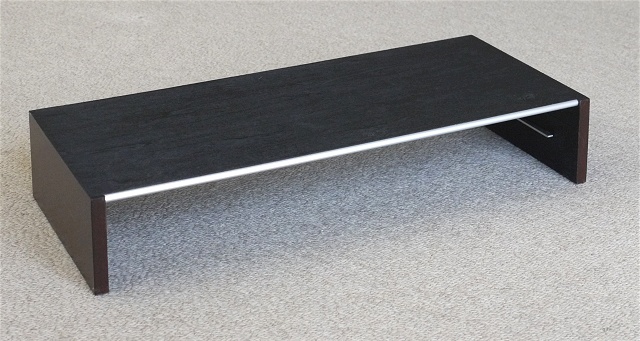 |
|
|
完成したブラケット。 3種類のアルミ押し出し材のそれぞれの特徴をうまく使って出来上がりました。
|
|
|
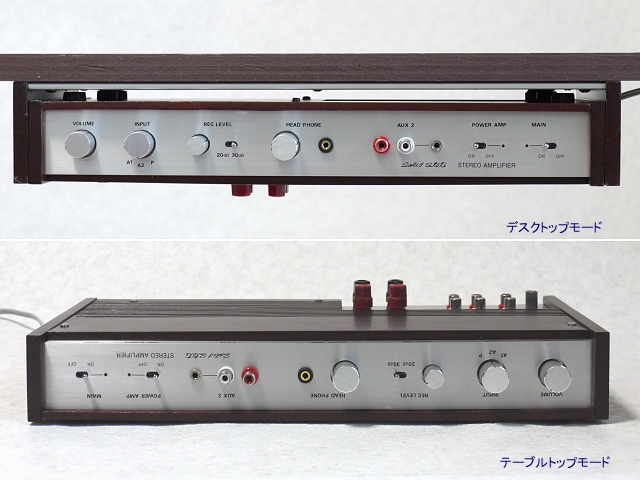 |
|
|
2モードが良く判るよう18mm厚合板にブラケットを取り付けて写真を撮りました。 デスクトップモードは書斎の吊り戸棚の下に取り付ける前提で、殆どがこの状態で使用されます。 テーブルトップモードはLPレコードをCD化する際に、書斎では狭くて作業できないので、別室でする際の使用を想定しています。 デスクトップモードではフロントパネルの全ての文字が正常に読めますが、テーブルトップモードでは逆さになって読み難いです。
|
|
|
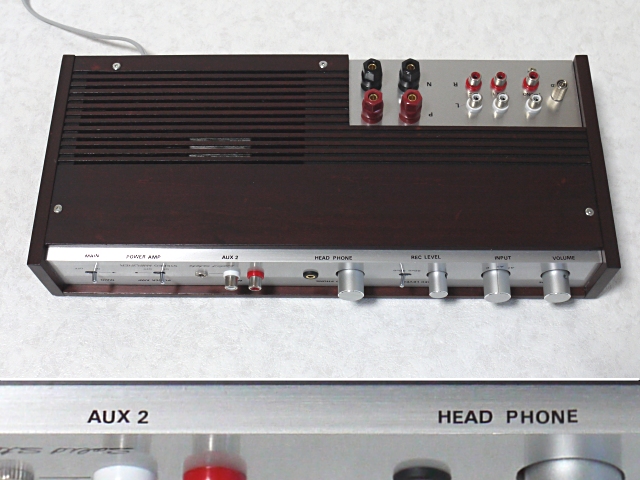 |
|
|
しかしテーブルトップモードでは上から見下ろす使い方が普通になるので、フロントパネルの手前側上部に入れた文字が真っ先に目に入るので(下の拡大写真参照)、操作上の支障はありません。 また同様にスピーカーやレコードプレーヤーの配線もアンプの使用位置に座ったまま、姿勢を変更することなく出来ます。
|
|
|
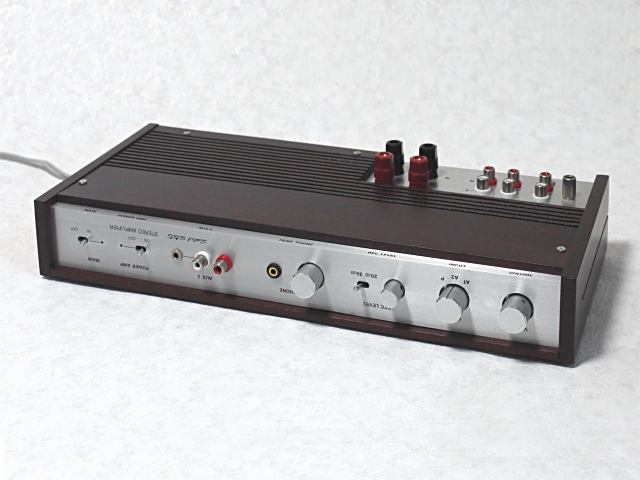 |
|
|
前の方に記載してあるように、このアンプはスピーカーからの出力、録音出力、ヘッドフォーン出力の3出力のレベルを独立してコントロールできます。 そして変わった2モードの使い方と市販の製品には全く無い機能を有しており、自作して始めて実現できた例です。 そして音質レベルもかなりの質が伴っていると思います。 大変時間が掛かりましたが、やっと一呼吸できます
|
|
Copyright (C) 2001-2019, Vic Ohashi All rights reserved.