|
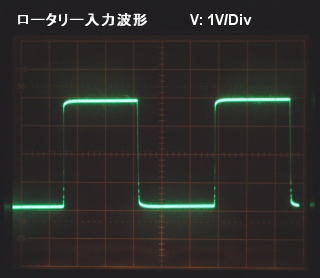 |
|
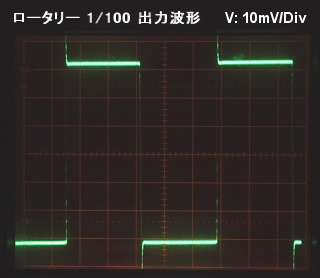 |
|
|
ロータリースイッチに信号が入る部分での10KHz波形です。 これに相似な波形が得られれば、100KHzまではフラットな周波数特性になります。
|
|
ロータリーSW出口の波形ですが1/100にてこのようなオーバーシュートが発生します。
|
|
|
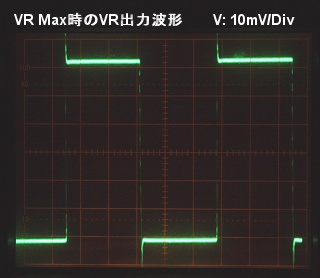 |
|
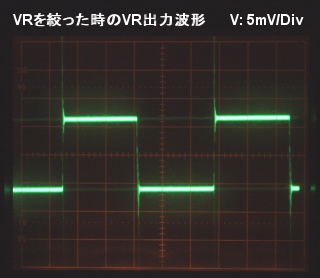 |
|
|
その時にVR MaxポジションでVRの出力波形はこんな風で、ロータリーSW出口に似ていますが、
|
|
VRを絞ってやるとこのようにオーバーシュートの高さは信号の大きさに対して大きい比率になります。
|
|
|
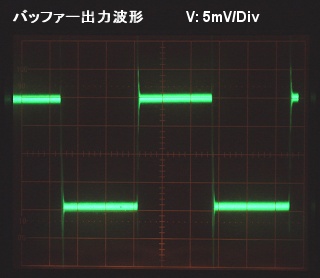
|
|
ここまでが補正する前の状態で、ロータリースイッチに入る信号にオーバーシュートが無くても、減衰後には発生していることが確認できます。 同様にボリュームでもMAXポジションではオーバーシュートの増加は見られませんが、ボリュームを絞るとオーバーシュートが増加してきます。 そして一度発生したオーバーシュートは左の写真のようにバッファーを通過した後でも同じレベルで残っており出力に出てゆきます。
ところでこのオーバーシュートは100KHz前後の周波数で極僅かなピークが回路系に存在することを暗示しています。 そしてオーバーシュートに留まっているのであれば簡単なローパスフィルター(ハイカットフィルター)でピークを抑えることにより取り除く事が可能です。 これがオーバーシュートに留まらずリンギングと呼ばれる状態になると補正はかなり難しくなってきます。 |
|
|
以下の写真はオーバーシュートを抑え込む実験の結果を表しています。 左側の写真は補正過剰状態で、右の方が適
切な補正が掛かっています。 但しロータリースイッチやVRが信号を減衰していないときには、100KHz近辺の信号レベル
が若干下がっている傾向があるので、もう少し全体を見ながら調整点を探す必要がありそうです。
|
|
|
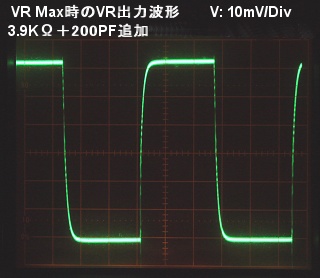 |
|
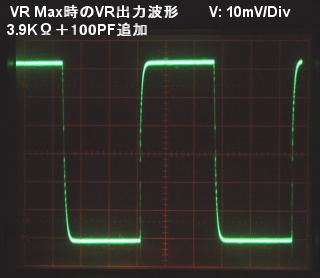 |
|
|
ローパスフィルターを追加していますが、減衰回路を通らない時には高い周波数のレベルが僅かに下がり出している傾向にあります。
|
|
100PFとしたこちらは左の200PFの場合よりも立ち上がり、立下りが共に良いようです。 減衰回路通過後の波形との比較になりますが、50-70PF辺りが最適となる可能性があります。
|
|
|
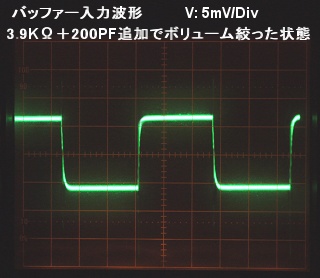 |
|
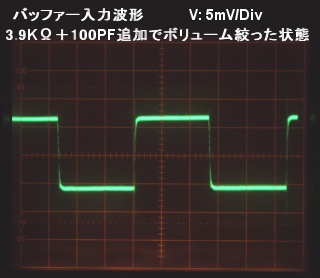 |
|
|
これはバッファーアンプの入力部での波形ですが、左肩が明らかに丸くなっており、補正過剰を表しています。
|
|
100PFの場合には肩が丸くなっている直前で綺麗にオーバーシュートを抑え込んだと言えます。
|
|
|
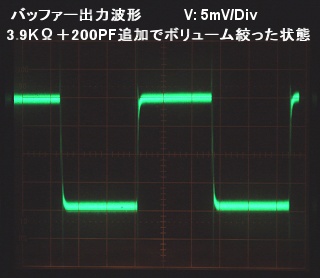 |
|
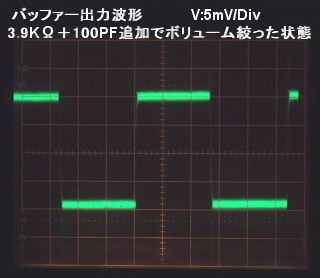 |
|
|
バッファーアンプの出力部では信号レベルがバッファーアンプのゲイン分だけ(1.545倍)上がっているだけで形は完全に相似です。
|
|
100PFの場合にはほぼ完璧な方形波の形です。 どちらの場合も波形のトップの部分の厚みが増していますが、これは外部のイズを拾っているようで、実際にはきちんとしたシールドが必要です。
|
|
|
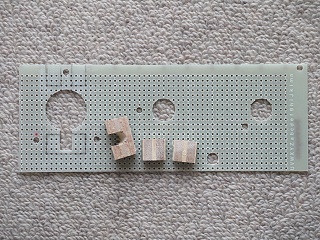 |
|
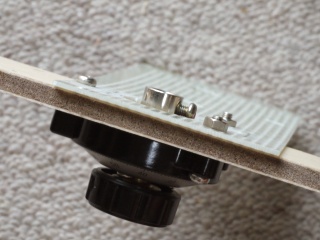 |
|
|
穴あけ加工が終わった発振回路基板。 中央と右の穴はロータリーSWが固定され、左に見える三つの穴はバーニアダイヤル固定の穴ですが、これらはフロントアルミパネル、スペーサーと共締めされます。 中央下に見えるのは12mm合板を切断したVR座受けでこれから基板に接着します。
|
|
フロントパネル(1.5mm)とスペーサー(4mm)の替わりに5.5mmのダミーの板をバーニアダイヤルとプリント基板の間に挟んで固定しました。 これでVR取り付けが頭の中で考えたとおり行くかどうかを確認します。
|
|
|
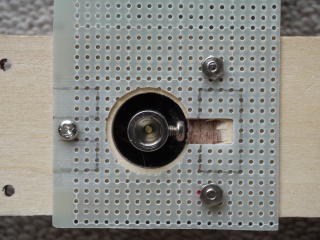 |
|
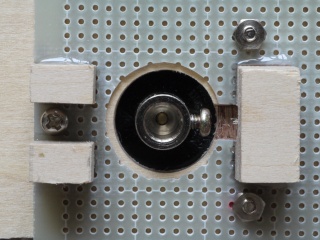 |
|
|
バーニアダイヤルを取り付けたプリント基板の部品取り付け面。 鉛筆で線を引いたところに12mm合板を切って作ったVR座受けを貼り付けます。 右の座受けは反対側中央が削られています。
|
|
座受けの接着が終了しました。 左側の座受けは2分割ですが、その間のスペースにバーニアダイヤル固定ネジが通ります。
|
|
|
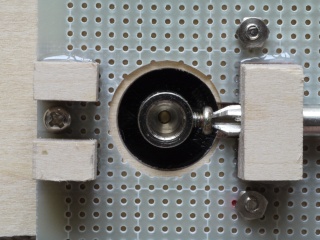 |
|
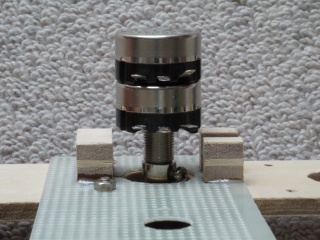 |
|
|
そして右側の座受けは反対側がえぐられトンネルが出来ているので、このようのドライバーを差込み、VRシャフトの固定ネジを締め付けることが出来ます。
|
|
座受けには2mm厚の座金が固定され、ここで見えているVRは実際には、この後加工する座金に固定されます。
|
|
|
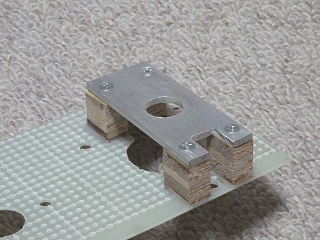 |
|
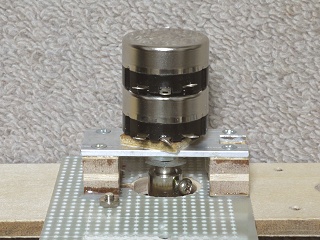 |
|
|
最終的に座金には2mm厚アルミ板を使いました。 そして加工終了後にエポキシ接着剤とネジを併用して固定しています。
|
|
上の写真との違いが良く判ると思います。 目論見どおり、バーニアダイヤルとVRの軸ずれは許容範囲に入っていると思われ、回転中に妙に渋くなるような事はありません。
|
|
|
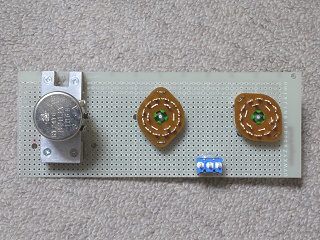 |
|
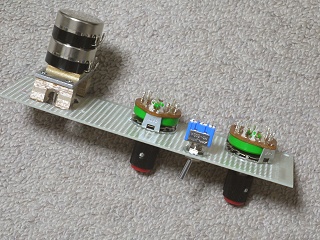 |
|
|
プリント基板に半田付け以外の方法で固定する部材がやっと取り付け完了しました。 これで配線に入れます。
|
|
その基板を下方から見たところ。 左端のバーニアダイヤルに取り付けるVRが如何に後方に突出するかが良く判ります。
|
|
|
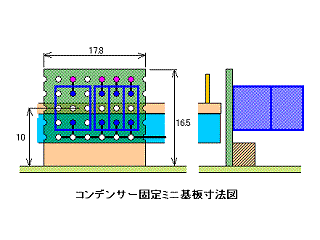 |
|
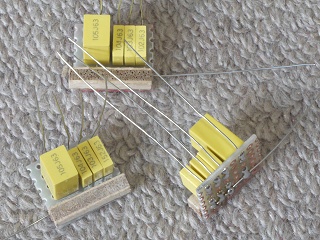 |
|
|
4個ずつ3ブロックのコンデンサーはそれぞれミニ基板に半田付けされ、その基板はロータリースイッチの脇に垂直に固定されます。
|
|
ミニ基板の下には4mm合板を4mm幅に切った棒を貼り付け、メイン基板への接着面積を稼ぎます。
|
|
|
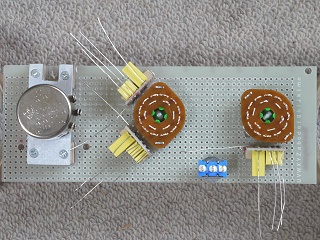 |
|
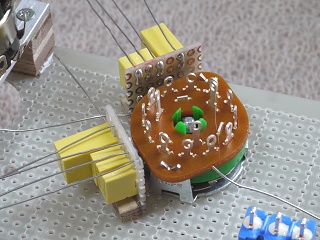 |
|
|
基板レイアウト図の所定の位置にミニ基板を接着します。
|
|
これで予め半田付けしておいたリード線を所定の接点や基板に半田付けすれば終わりで、プラプラ不安定な空中配線を回避できています。
|
|
|
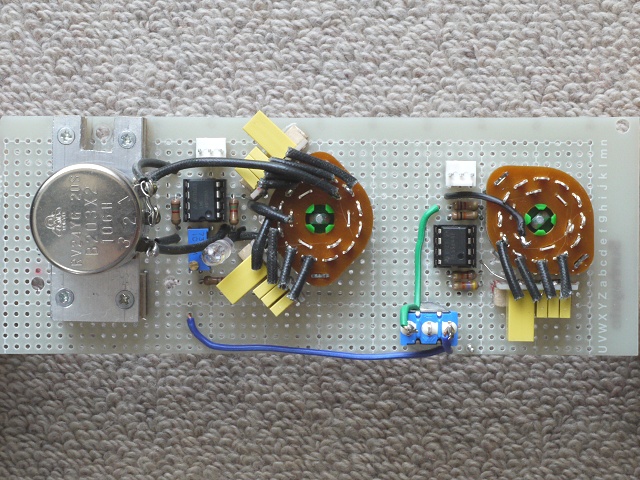 |
|
|
正弦波・方形波各発振回路部分の配線を済ましました。 誤配線がないか充分に確認をしておかないとなりません。
|
|
|
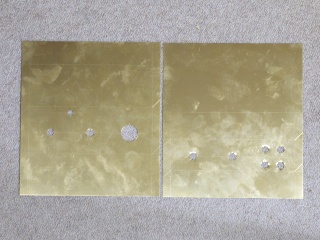 |
|
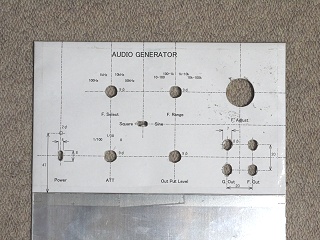 |
|
|
0.3mm厚真鍮板を切断する前に位置の判っている穴をあけました。 薄いから加工は楽!と思ったら大間違い。 切り口近辺が曲がりやすいので、ゆっくり慎重に進めるしかなく、くとんでもない時間が掛かります。
|
|
フロントパネルは柔らかいアルミ板とは言え、1.5mm厚ありますので、加工は真鍮板よりも楽なくらいでした。 しかし真鍮板2枚とアルミ板の予備加工で1日を費やしてしまっています。(切断はシールドボックス完成後に!)
|
|
|
 |
|
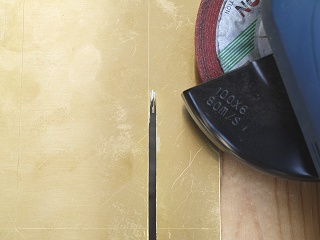 |
|
|
刃研ぎグラインダー使用時にはゴーグルが絶対必需品。 私はTSK セーフティーゴーグル #305を使っています。
安いだけの物では得られない安全性、安定性、長時間使用時の快適さが得られます。
|
|
刃研ぎグラインダー(CG-11)で切断中。 白っぽい縦の線が罫引きで引いた切断線で、それより0.2-0.3mm外側を切断できています。 また切断により平面がぺこぺこになることはありません。
|
|
|
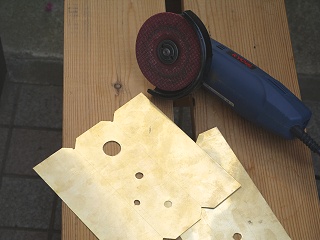 |
|
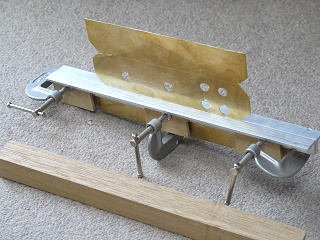 |
|
|
切断が完了した大小二つのシールドボックスを作る材料。 ここまでは目論見どおりに進むことが出来ました。
|
|
曲げ作業のスタート。 前にお見せした曲げる方法の写真と全く同じ方法で、手前に見える棒を当てて一気曲げします。
|
|
|
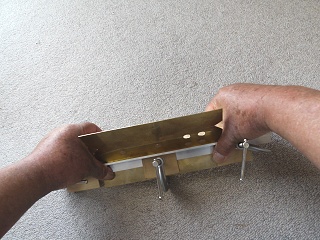 |
|
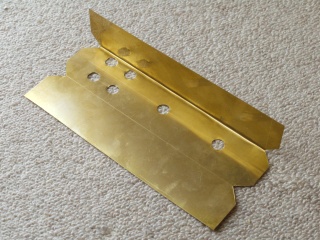 |
|
|
当てた棒は向こう側にあるので見えませんが、一気曲げに入った所です。 これにはかなり力が必要になります。
|
|
1回目の直角曲げが終わりました。 曲げた角の光の反射で曲げのシャープさが判りますが、私が期待していたシャープさの60-70%位しか得られていないようです。
|
|
|
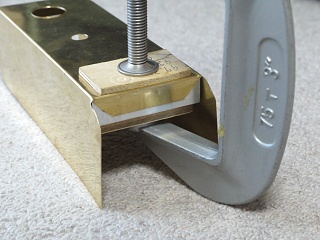 |
|
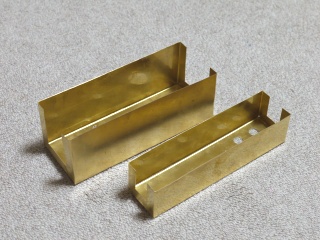 |
|
|
長い部分の曲げが終わった後に、端の耳の部分の曲げを施したところです。 その為にL型アルミ材を内寸幅に切断しています。
|
|
全ての耳の部分が曲げ終わりました。 曲げた後の最大寸法誤差(設計値に対して。)は1mm以内で、寸法誤差が余り影響しない物なので、辛うじて合格です。
|
|
|
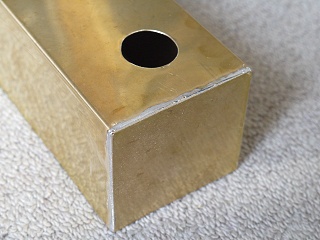 |
|
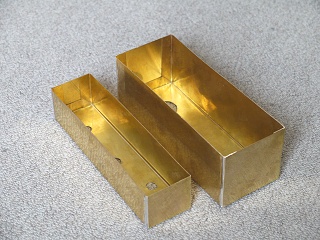 |
|
|
側板を耳の部分に当てて半田付けしました。 銀色っぽい筋になっているのがそれです。
|
|
そして蓋のない箱の状態になりましたが、予想以上にぺこぺこしていて強度的に弱いので補強をします。
|
|
|
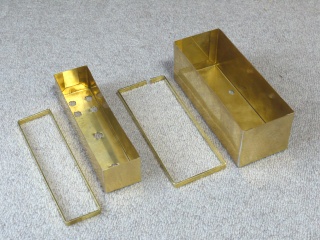 |
|
 |
|
|
厚さ1.5mm、幅6mmの真鍮棒を曲げてロの字の枠を作りました。これをボックスの内側に半田付けします。
|
|
補強が終わったシールドボックス。 みてくれがあまり良くないのが残念ですが、強度はぐんと上がりました。
|
|
|
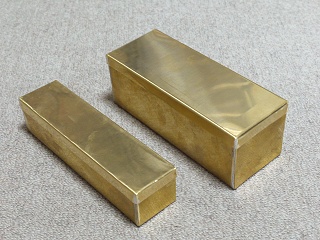 |
|
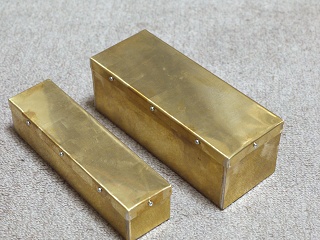 |
|
|
現物合わせで蓋を作りました。 被せ代は約9mmあります。
|
|
そして蓋はこのようにタッピングネジ(2.3φ)で固定されます。
|
|
|
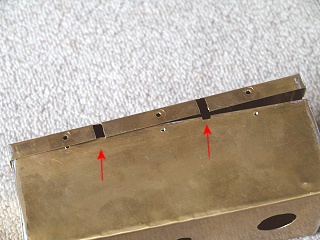 |
|
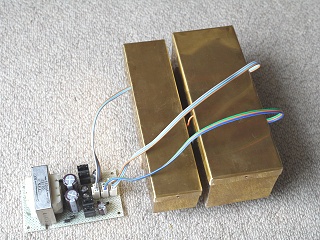 |
|
|
3本の電源ケーブル(平行3芯)と二つのBOXを連結する2本のワイヤーを引き出す穴をあけます。 蓋を外すだけでケーブルも外れる構造です。
|
|
電源ブロックとはこのように連結されます。 これでようやくシールドボックスの製作が終了です。 実動4日間を費やしました。
|
|
|
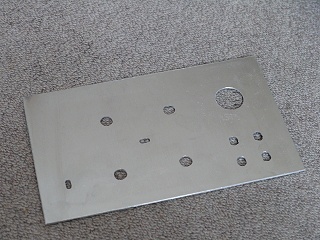 |
|
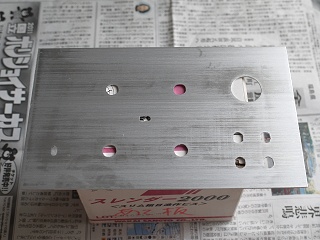 |
|
|
切断線に沿って電動ジグソーで切断しました。 (1.5mm厚もあるので電動ジグソーが使えたわけです。)
|
|
#120のサンドペーパーでヘヤーラインを入れました。 表面の細かな傷などはこれで消えてしまいます。
|
|
|
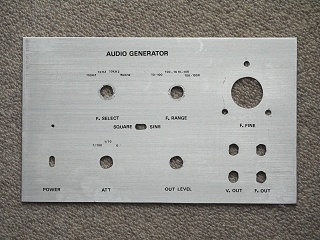 |
|
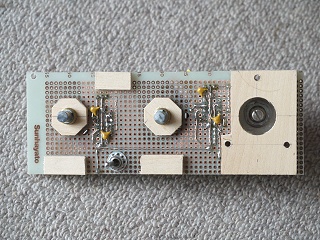 |
|
|
その後水性ウレタンニス透明クリヤーを2回塗り完全乾燥後にインスタントレタリングで文字入れ。 その後水性ウレタン艶消しクリヤーを2回塗りました。 更にバーニアダイヤル固定穴とLED窓穴をあけています。
|
|
4mm厚シナ合板を切ってスペーサーにしました。 基板の配線がない部分にこれを両面テープで接着しています。
|
|
|
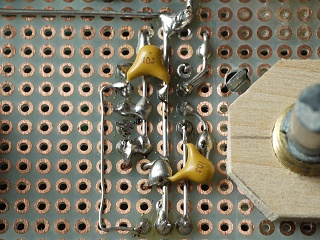 |
|
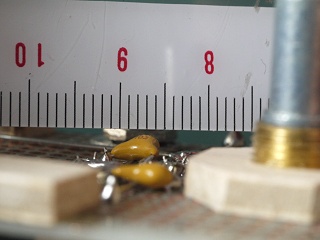 |
|
|
4mm厚のスペーサーは実はぎりぎりの厚さで、ここに見える黄土色の裏付け部品などは突出量が大きいので?
|
|
定規をスペーサーに当ててみましたが、先ほどの部品は隙間の残りが1mm以下です。 かと言ってスペーサーをこれ以上厚くするとVRやSWをナットで締められなくなります。
|
|
|
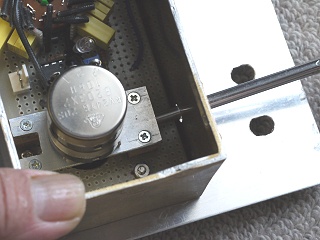 |
|
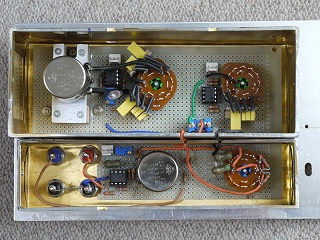 |
|
|
シールドボックスに収めてからバーニアダイヤルロックネジを締められるよう、追加の穴をあけてこのようにドライバーが挿せるようになりました。
|
|
2つのシールドボックスを共締めして蓋をする前です。 パネルにまだ固定していない部品は電源スイッチとLEDです。(右にその穴が見える。)
|
|
|
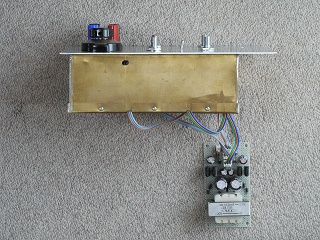 |
|
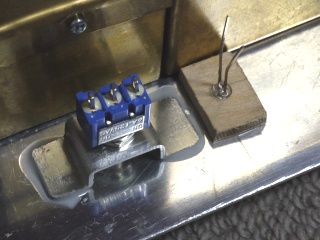 |
|
|
蓋を被せて電源基板と接続しました。 木製ケースにはこのような位置関係で固定されます。
|
|
電源スイッチ固定金具とLEDを固定する4mm厚の小さな板は何れもエポキシ接着剤で固定しました。
|
|
|
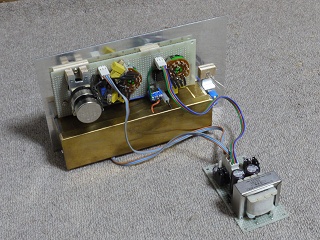 |
|
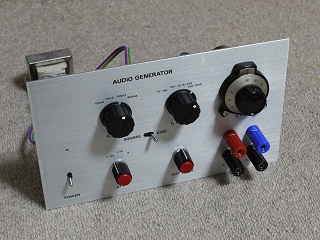 |
|
|
大きなシールドケースは無くても何ら問題は無い事が判ったので外してしまいました。 木製ケースの内部にこのように装填されます。
|
|
前面はこんな具合。 下二つの小さなツマミは動作確認用に取り敢えず付けているだけで、最終的には上と同じツマミに変更されます。
|
|
|
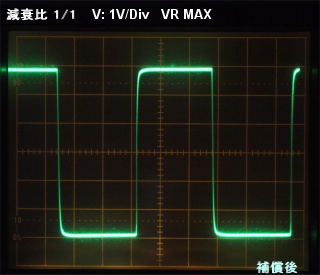 |
|
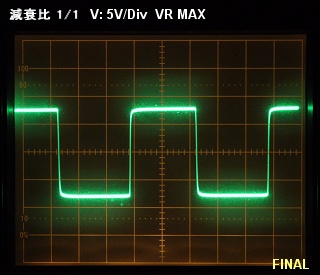 |
|
|
右側は目標スペックに合わせて最大出力を調整後(P-Pで約15V)。 1/10ではP-P 1.5V、1/100でP-P 0.15Vになる。
|
|
|
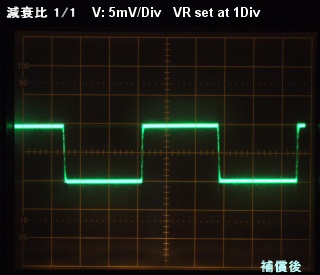 |
|
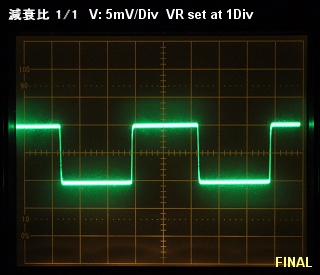 |
|
|
左の写真では波形の立ち上がり/立下り(垂直部分)に点線のような不連続部分があるが、右のシールドケース装填後にはこれが消えている。
|
|
|
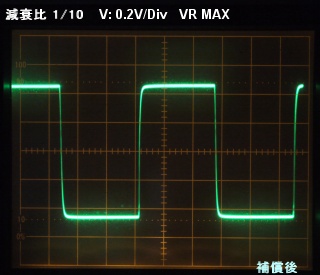 |
|
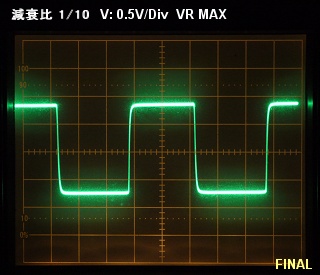 |
|
|
|
|
|
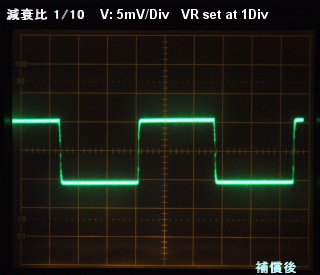 |
|
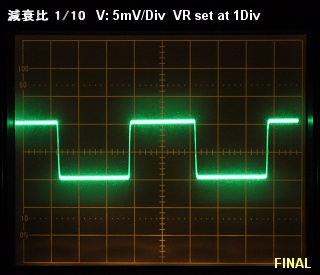 |
|
|
減衰比1/10でもアッテネーターを絞ると不連続のような現象が見えてくるが、シールドケース装填後にはこれが消える。
|
|
|
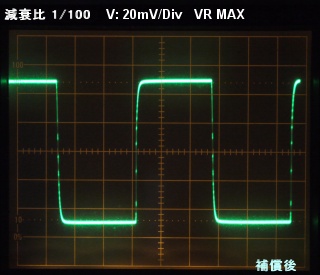 |
|
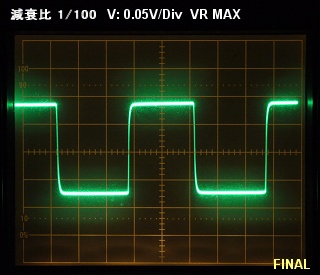 |
|
|
減衰比が1/100になるとVRがMAXの状態でも不連続のような波形が認められるが、これもシールドケース装填後は問題ない。
|
|
|
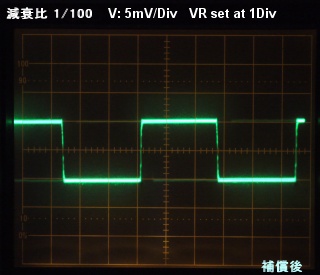 |
|
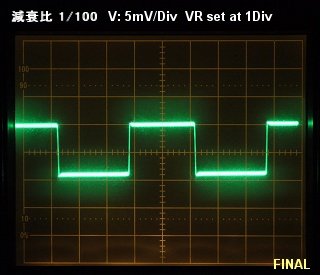 |
|
|
ピーク電圧が5mVという微弱な信号でもオーバーシュートは見られない。 2段階のフィルターによる補正が実にうまく出来ていると思う。
|
|
|
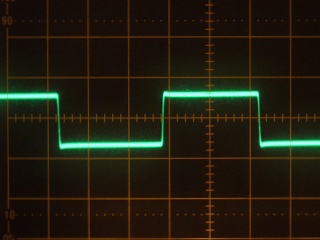 |
|
ところが出力信号電圧を更にVRで絞ったところピーク電圧3mVになるとご覧のように極々僅かだがオーバーシュートが出てくる。
これをどう扱うか暫し悩んだが、これを抑えると高い信号電圧で肩が丸くなることと、方形波のピーク電圧3mVという微弱な信号を必要とする可能性が無いと考えこのまま行くことにした。
(5mv/Div) |
|
|
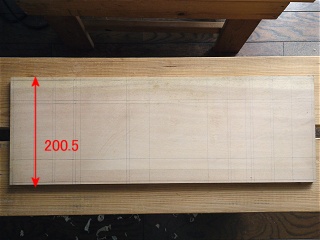 |
|
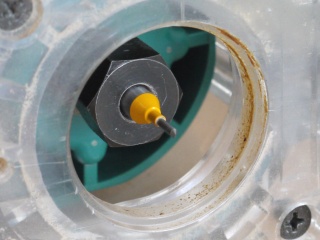 |
|
|
この横に木目が通っている板の上下は200.5mmあり、ケースの奥行 + 0.5mmです。 そしてトリマーで前と後のエッジを加工後、左側板、台板、右側板に切り離します。 加工寸法精度を上げる方法のひとつです。
|
|
先ずアルミパネルを落とし込む溝を1.6mmのストレートビットで彫ります。 深さは2.3mmとしました。 私のトリマー加工ではこの1.6mmストレートビットは高価ですが大活躍しています。
|
|
|
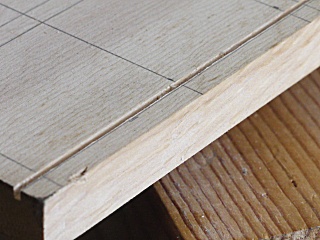 |
|
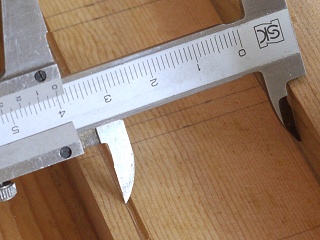 |
|
|
前側の縁から5mm離して1.6mm幅の溝が彫り終わりました。
|
|
次に45度傾斜切削ですが、V溝ビット(VB-90G)を使うのでビットの軸中心は板の前の縁になります。 従って溝の前川の縁から40mmの位置にガイド板を固定します。 ご覧のようにノギスを使って万全を期しています。
|
|
|
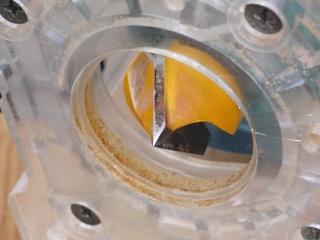 |
|
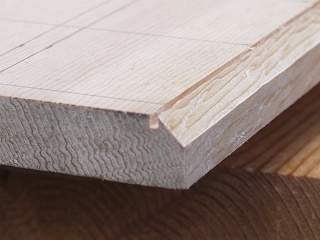 |
|
|
VB-90Gを取り付けてビットの突出量を5mmにセットしました。 この調整・確認にもノギスを使っています。
|
|
そして切削。 この上の写真の作業を開始する時からここまでに1時間近くも掛けました。 何度も確認してボンミスを避けるためと、加工精度を0.2mm程度まで高めようとした結果です。
|
|
|
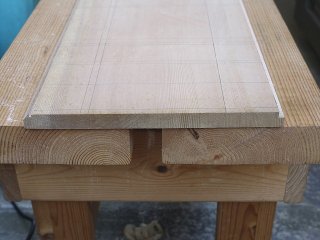 |
|
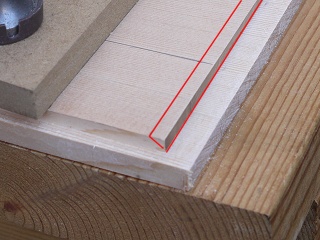 |
|
|
後ろ側は10mmのストレートビットを使い、4.5mm幅、深さ5mmで欠き取り、今週の最初の写真の板(幅200.5mm)の前後はこのようにトリマーで加工されてから側板2枚と底板の合計3枚に切り離します。
|
|
右側板の底板が接着される部分の加工は2段階で。 第一は10mmストレートビットで幅9.5mm、深さ5mmで先ず削り落とします。 赤線を引いた部分は後程斜めに切削します。
|
|
|
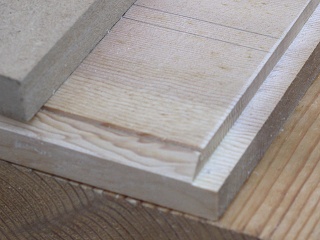 |
|
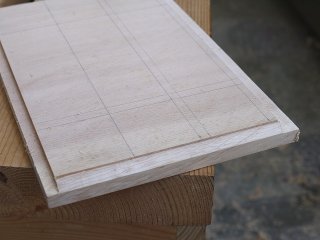 |
|
|
天板が落とし込まれる部分は深さ5mm、幅6mmで欠き取ります。 左側板も同じように加工します。
|
|
これは加工が終わった左側板で、手前が前側の縁、左が天板嵌め込み側で右が側板接着側です。(右側の斜め切削加工はこの下の写真にて。)
|
|
|
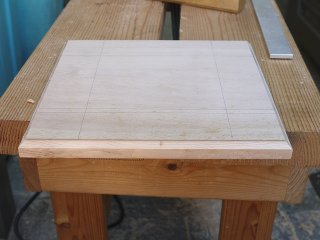 |
|
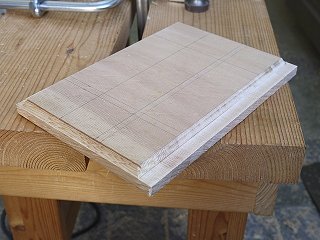 |
|
|
台座は左右の角を45度の切削します。(切削幅、切削深さ共に5mm。)
|
|
側板の台座を接着する部分も45度に斜め切削します。 一部にバリが残りますので、それらを全てヤスリで削り取ります。
|
|
|
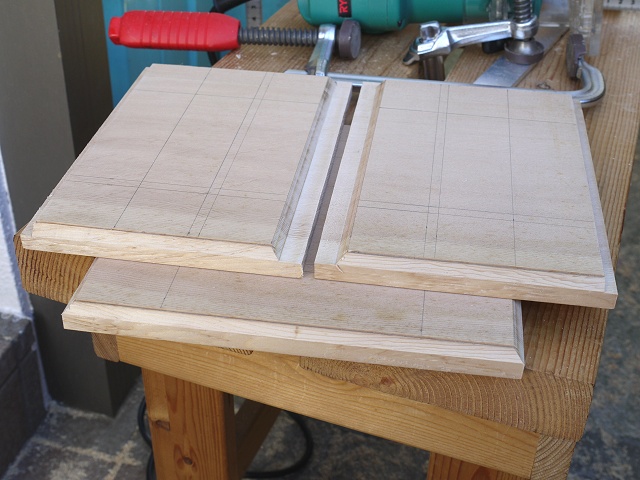 |
|
|
トリマー加工作業が終了しました。 上の左は左側板で、右は右側板。 そしてそれらが載っているのが底板です。
|
|
|
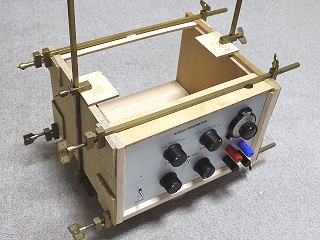 |
|
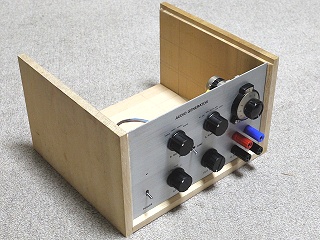 |
|
|
3枚の板の組み上げは接着で。 30分硬化開始型エポキシ接着剤を使っています。 フロントパネルを落とし込んで接着位置が狂わないようにして、ハタ金で4時間保持しました。
|
|
ケースのコの字部分が完成しました。 アルミフロントパネルは落とし込んだだけで接着していません。 従って抜き差しが出来ます。
|
|
|
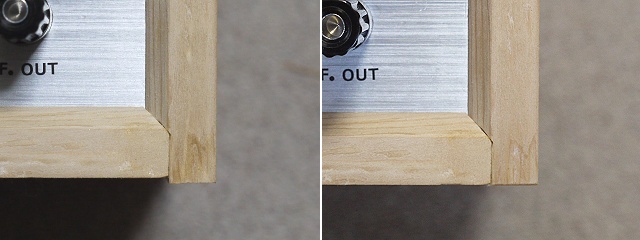 |
|
|
左の写真に見られるように、底板の面よりも側板は突出しています。 これは意識してそうしたのですが、接着後に笠付き目地払いビット(MB-12.7G)で突出部分だけを削る事が出来ます。(右の写真)
|
|
|
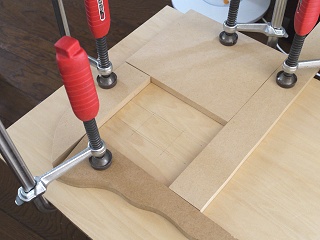 |
|
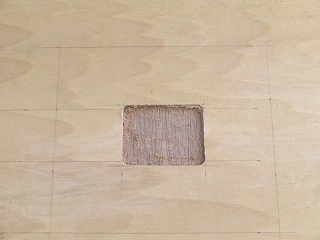 |
|
|
天板には空気流通のためのスリット状の穴をあけますが、裏側に36 x 50の大きさで深さ2.75mmの座繰り穴をトリマービットで削ります。
|
|
6mmのストレートビットで削り終わりました。
|
|
|
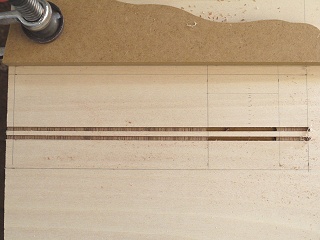 |
|
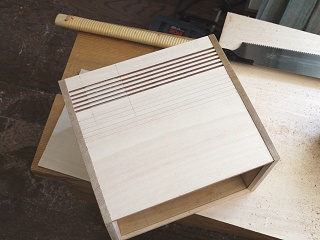 |
|
|
次に表面側に3mmのストレートビットで深さ2.75mmの溝を等間隔で6本切削します。 すると裏側の浅く削った部分は細長い穴となって残ります。
|
|
溝の切削が終わった天板を現物合わせでサイズを調整し嵌め込みました。
|
|
|
 |
|
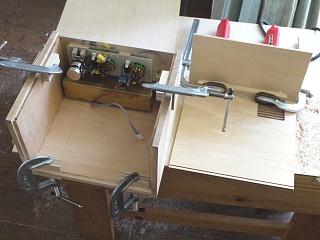 |
|
|
裏板も現物合わせで切断し天板と接着します。
|
|
その後天板と裏板をネジ止めする桟を4箇所接着しました。(左) また天板と裏板の接着を補強する棒を接着しています。(右)
|
|
|
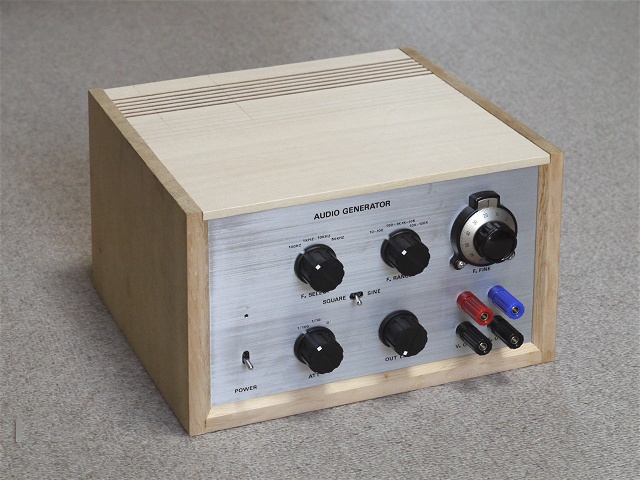 |
|
|
天板の前縁にシナの木口テープを貼り、合板であることを隠すお化粧をしました。 これでやっとケースの製作が終了しました。 シナ合板とムク材の色違い、明るさ違いが大きいですが、着色過程で調整して合わせます。
|
|
|
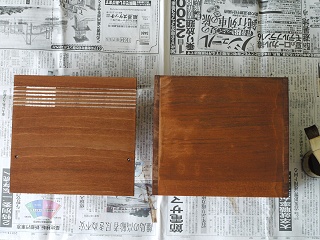 |
|
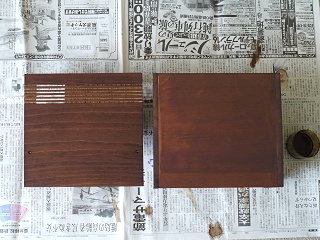 |
|
|
オーク色ポアステインを水で2倍に薄めて1回目の着色。 左の蓋はシナ合板なので色身が右より薄いです。 右の白っぽい斑は取りきれずに残っている接着剤ですが、底面なので無視しています。
|
|
右は3回目の着色で左は1回多い4回目としました。 色味・濃度がほぼ同じに仕上がっていると思います。 こうなれば木目の違いは気が付かれなくなります。
|
|
|
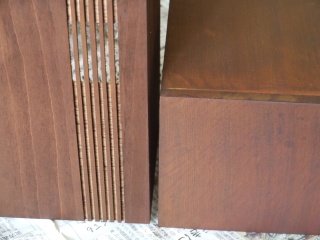 |
|
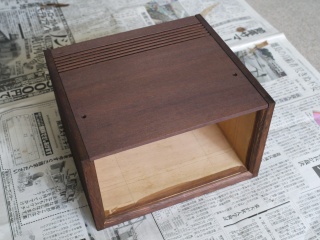 |
|
|
乾燥した状態での左は天面、右は側面になります。 少し違う感じがしないではありませんが、濡れた状態(ニス塗り後もそれに近い。)ではぐっと接近します。
|
|
同じく乾燥後に組み上げました。 なんら違和感はありません。
|
|
|
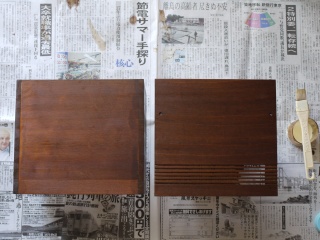 |
|
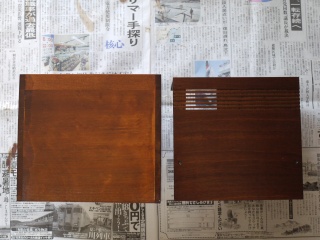 |
|
|
水性ウレタンニス透明クリヤーを1回塗った状態です。 艶はごく僅かしか出ず色身の深みがありません。
|
|
透明クリヤーを2回塗った後空研ぎペーパーで研摩し、更に透明クリヤーを1回塗った状態です。 色身がぐっと落ち着いてきました。
|
|
|
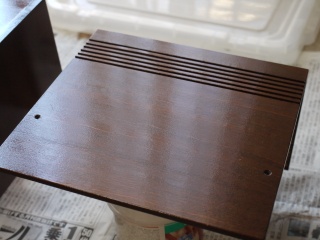 |
|
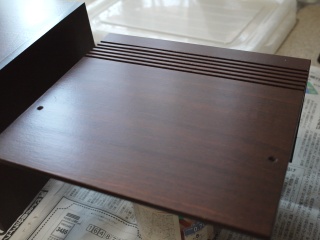 |
|
|
最後は艶消しクリヤーニスを塗りますが、艶の出方の違いをよくご覧ください。 左は透明クリヤー3階塗りの後で、綺麗な艶を出すと言う意味ではまだまだ不十分ですが、艶消しニスを塗った後の右は、非常にしっとりとした上品な5分艶に変わりました。 この艶が正に私の求めるものです。
|
|
|
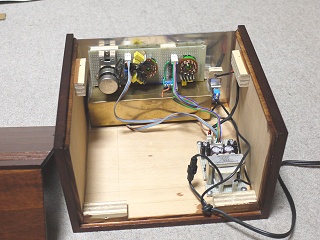 |
|
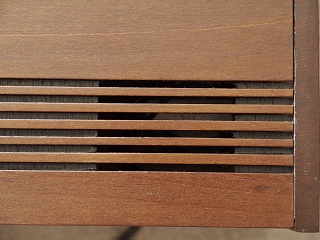 |
|
|
電源基板を固定し、内部の残る配線を済ませれば完成です。 やけにがらんとしていますが、、電源のノイズが飛び込まないよう離しているためです。
|
|
天板のスリット内部を水性ペイント艶消し黒で塗りつぶしました。 一本の溝に細い筆で塗るというよりも『落とす』ような感じで素早くペイントを塗りつけます。 当然ニス塗り下部分にはみ出ますが、それは濡れ雑巾で直ぐに拭き取ります。
|
|
|
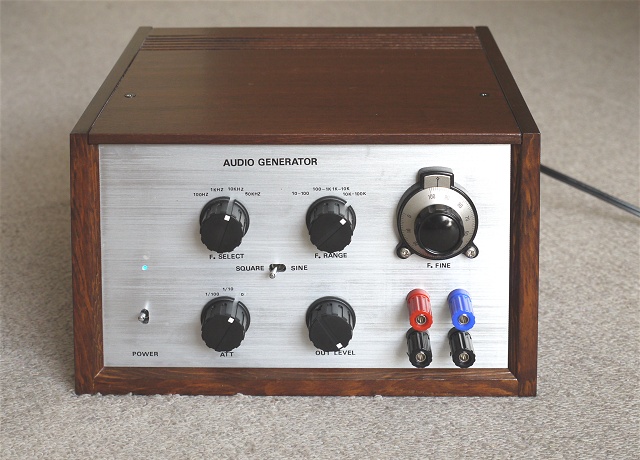 |
|
|
ようやく完成しました。 定電圧電源で2種類、そして今回の低周波発振器と本物木目ケースは3作目になります。 これでアンプの製作などで、周波数特性、増幅度、最大出力の測定などが可能です。 また後ほど歪率の発生具合を確認すれば(私の期待は中域から高域では0.01%以下、低域で0.1%以下です。)、歪率測定にも使えるはずです。
|
|
Copyright (C) 2001-2019, Vic Ohashi All rights reserved.