|
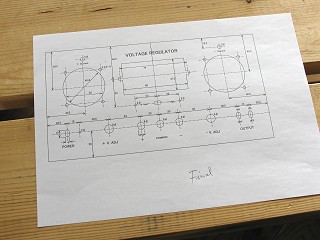 |
|
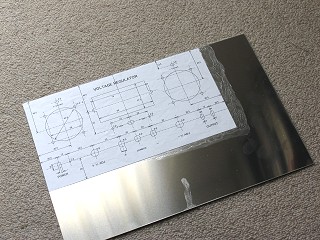 |
|
|
既に描き上げているパネル面加工図の実物大プリントを取ります。 私は同じ物を2枚印刷し1枚はアルミ板に貼り付け、もう一枚はパネルの加工が終わるまで参照用に使います。
|
|
2mm厚アルミ板に糊で貼り付けます。 これは紙工作用のでんぷん糊です。 従って最後に温湯で簡単に落とせます。
|
|
|
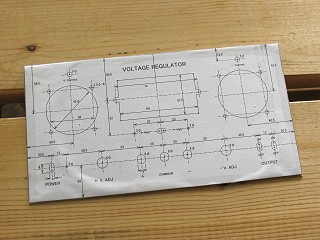 |
|
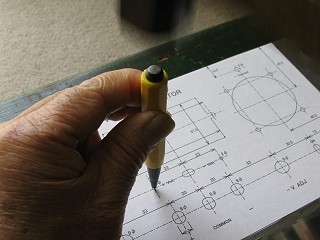 |
|
|
2辺を電動ジグソーで切断しました。 ここで使うブレードは軽金属用です。 ご覧のように一部ははがれかかっていますので、周りはセロファンテープで剥がれないよう貼り付けています。
|
|
全ての穴あけ位置にセンターポンチでマーキングしています。 マーキングは2φのドリル用にしますので、深くはありません。 このためアルミ板の反りが起きません。
|
|
|
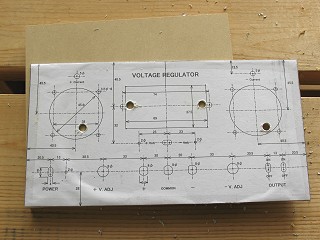 |
|
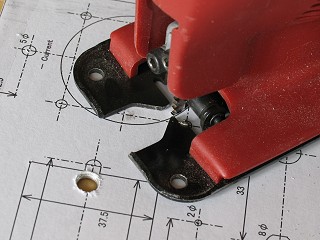 |
|
|
切り抜く穴を最初に加工してしまいます。 最初に適当な場所に6φの穴をあけました。
|
|
電動ジグソーには木工円切り用のブレード(mini-Shopで販売しているNo.5)に変更。 円切り用ですから曲線切りはお手のものです。
|
|
|
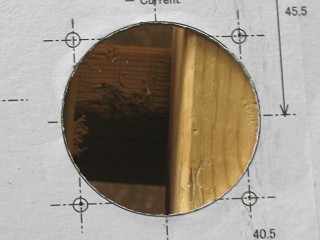 |
|
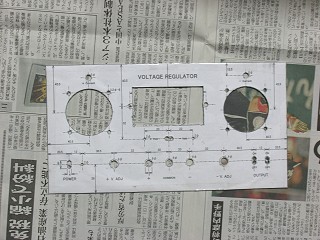 |
|
|
切り抜いた後はこんな具合です。 直径が45mmなので円切りブレードでないと具合が悪いです。 切断精度が高いのでこの後の研磨も楽です。
|
|
もうひとつの丸穴をあけて四角い穴をあけ、小さな穴を全てあけて部品の挿入具合を確認し始めたら あれっ!
|
|
|
中央に取り付けるデジタルパネルメーターの下に横向きにトグルスイッチが入るのですが、パネルの裏側に来るメーター
基板の下端は前面のベーゼル下面より12mmも飛び出ます。 これがトグルスイッチに当りこのままではどちらかが取り
付けられません。 暫しの間頭の中は真っ白でしたが、気を取り直してデジタルパネルメーターを5mm上方にずらす事に
しました。 デジタルパネルメーターの下部に穴があいてしまいますが、デザイン処理を考えます。
|
|
|
 |
|
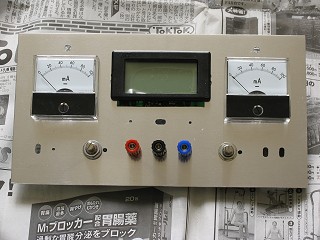 |
|
|
修正の穴をあけ終わりました。 デジタルパネルメーター固定のネジ穴が5mm上に追加であいています。
|
|
トグルスイッチを除く部品を仮に取り付けました。 これでトグルスイッチとの干渉は無くなるのですが、ご覧のようにメーターベーゼル下に穴が見えてしまいます。
|
|
|
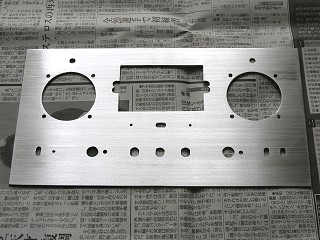 |
|
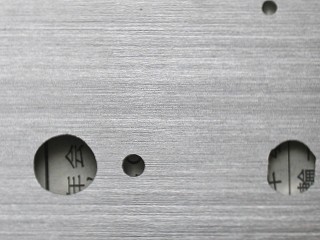 |
|
|
切断部分のバリを落としてヘヤーライン加工を施しパネル面に付いた小さな傷を消してしまいます。 細かな手法は上の方をお読みください。
|
|
左下の部分のアップです。 手加工ですのでまあまあの仕上がりだと考えています。 梨地仕上げが出来ると更に良いのですが、あり合せの工具・材料ではちと無理でしょうか?
|
|
|
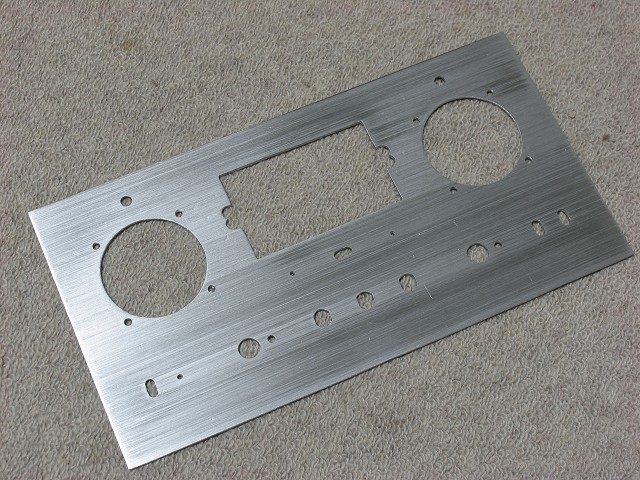 |
|
|
水洗いを済ませてから水性ウレタン透明クリヤーニスを1回塗りました。 この後インスタントレタリングで文字入れしますが、塗膜が充分に硬膜化して欲しいので、数日乾燥させます。
|
|
|
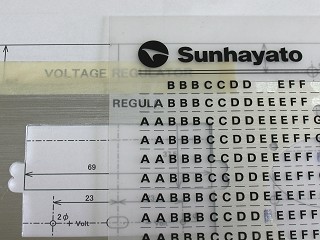 |
|
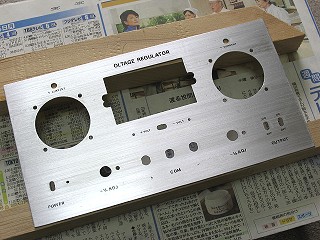 |
|
|
便利に使っていたインスタントレタリングもメーカーは既に製造中止とのことです。 私が使う分くらいは買い置きしておかないとなりません。
|
|
文字入れを完了後水性ウレタンニスを塗りましたがこの写真を見て文字抜けを発見しました。
|
|
|
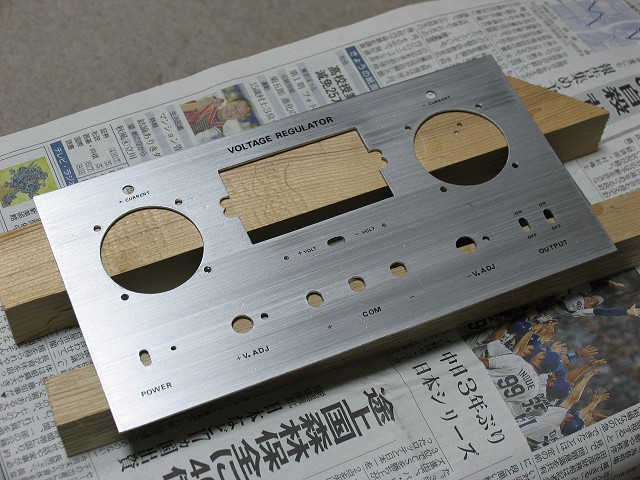 |
|
|
抜けていた一文字を追加して再度水性ウレタンニス透明クリヤーを塗り更に艶消しクリヤーを塗って完成です。 抜けていた文字とは? 何と以前は OLTAGE REGULATOR となっていました。
|
|
|
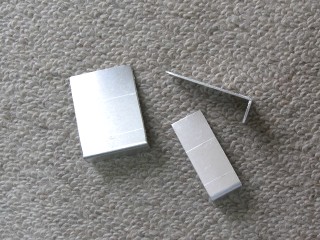 |
|
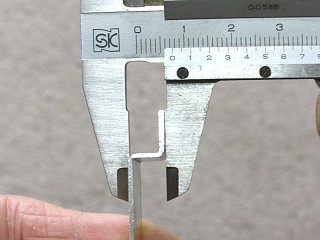 |
|
|
トグルスイッチ固定金具の切り出し。 既製品ですが高さ35mmの仕切り板のようなものから3枚切り出しています。
|
|
1回目の折り曲げが終わったところ。 設計値の7.5mmぴったしになっています。
|
|
|
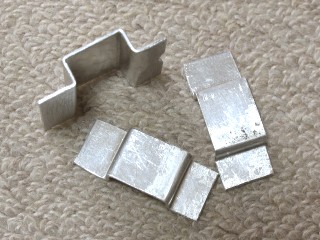 |
|
 |
|
|
3つの金具の折り曲げが終わりました。 手加工ですからこの辺りが見栄えの限度でしょう。
|
|
それらに穴をあけてトグルスイッチを固定します。 これでトグルスイッチのレバーは表面に2/3程度しか出なくなります。
|
|
|
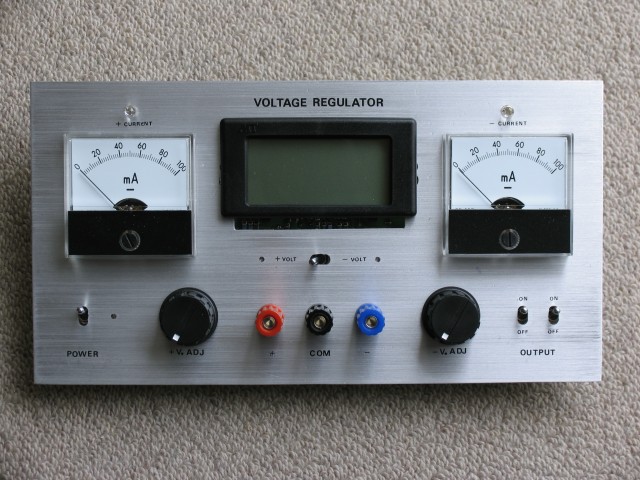 |
|
|
フロントパネルに固定する全ての部材の取り付けが終わりました。 中央のデジタルパネルメーターだけは設計時点の位置から上に5mm移動したためその下に穴があいてしまいました。 これは後ほど塞ぎます。
|
|
|
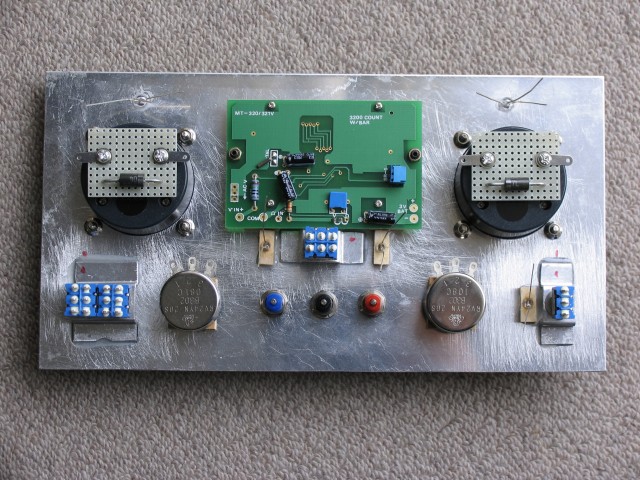 |
|
|
裏の部品取り付け面はこんな様子です。 アルミ板の表面があちこちで汚らしく見えますが、これはエポキシ接着剤の載りを良くするために#60のペーパーでざらつきを増加させたためです。
|
|
|
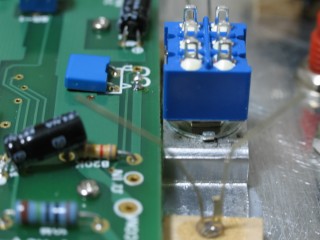 |
|
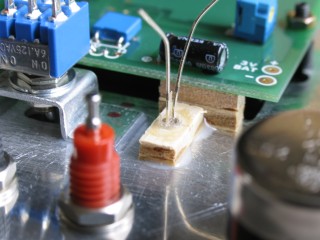 |
|
|
左半分は上方へ5mm移動したデジタルパネルメーターの基板そのすぐ右に干渉していたトグルスイッチがあります。
|
|
それを下方向から見たところ。 パネルメーターベーゼルの浮き上がり防止に7mm厚の板がアルミパネルとパネルメーター基板の間に挟んであります。
|
|
|
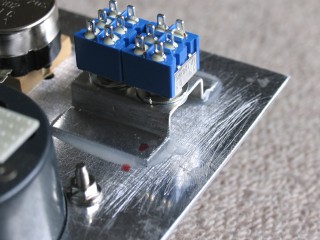 |
|
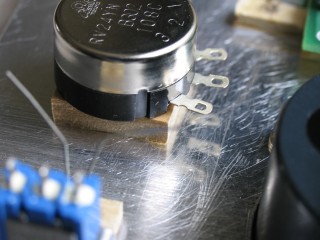 |
|
|
接着強度を上げるためパネル面を#60で粗びた面が良く判ります。
|
|
こちらは可変抵抗取り付けの様子。 5mm厚の板を挟んでいます。
|
|
|
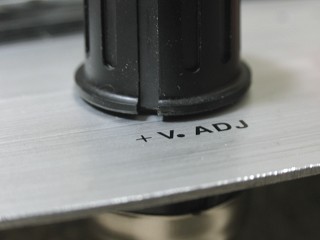 |
|
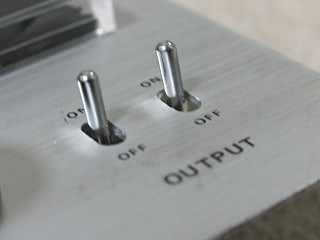 |
|
|
その効果はこんな具合でツマミとパネル面の隙間は0.5mm程度しかない絶妙な仕上がりです。
|
|
トグルスイッチのレバーの出具合はこんな感じで、 パネルに直付けした場合の無粋な外観とは比較になりません。
|
|
|
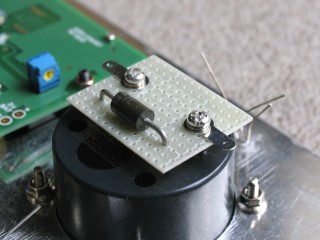 |
|
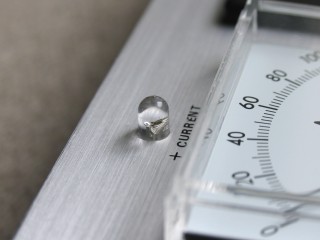 |
|
|
逆流防止のショットキーバリヤーダイオードは小さな基板に固定しメーターにネジ止めしました。
|
|
電源出力のインジケーターLEDはパネル面から突出していますが、後ほど光拡散キャップを被せて視認性を改善します。
|
|
|
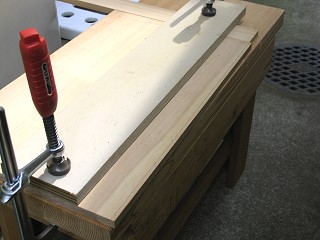 |
|
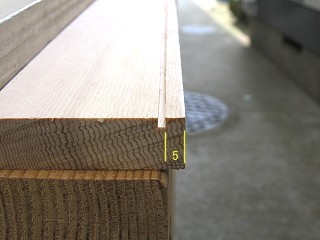 |
|
|
1.6mmストレートビットで深さ2.2mmの溝を彫ります。 電動トリマーの軸が中心からごく僅かずれている事を利用してガイド板に接触させる面を変更して1.7mm幅としました。
|
|
板の端から5mmの位置に溝はあけられています。
|
|
|
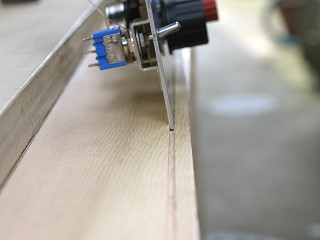 |
|
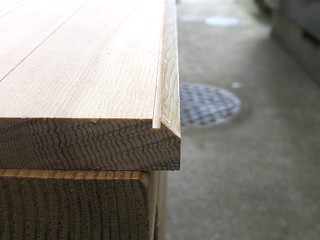 |
|
|
幅1.7mmですから1.5mm幅のフロントパネルを落とし込むと隙間がありますからこのように傾きます。
|
|
コロ付き角面ビットを使って幅5mmの部分を45度に削りました。
|
|
|
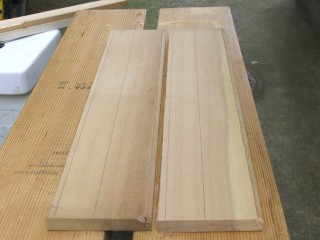 |
|
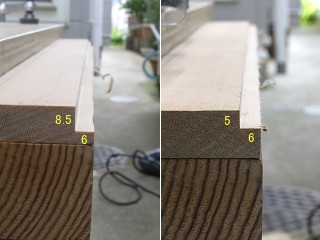 |
|
|
長手方向反対側も同じ加工を施してから幅91.5mmで切断し2枚の板が取れました。
|
|
溝を彫った反対側は、1枚は幅6mm、深さ5mmに切削(左の写真)、もう一枚は幅6mm、深さ8.5mmに切削します。(右の写真)
|
|
|
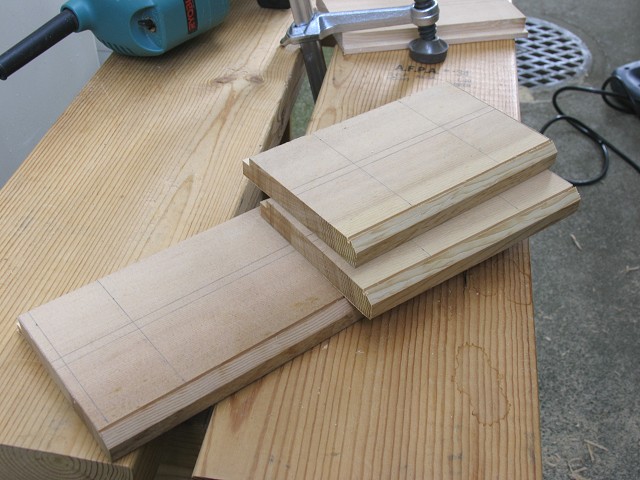 |
|
|
深さ8.5mmに削った板は長さ240mmで切断して底板に(一番下の板)、深さ5mmに削った板は140mmの長さで2枚切り出し側板になります。 尚切断は1mm程度長めに翔265を使って、その後ストレートビットでドンピシャ寸法にトリミングしました。
|
|
|
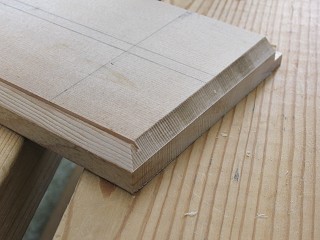 |
|
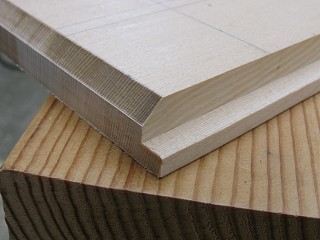 |
|
|
底板の側面は幅5mmを45度に切削します。 これは右前側から見たところです。
|
|
右側の角を後ろ側から見たところですが、このような変わった段差が発生します。
|
|
|
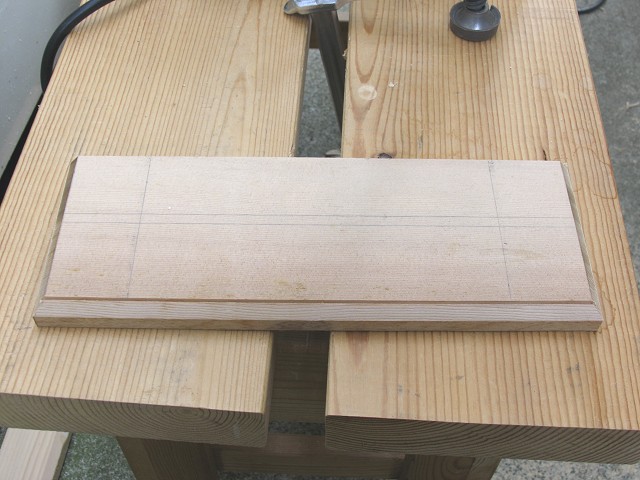 |
|
|
左右の側面角を45度に切削した底板。 この後空気取り入れ口を切断すれば出来上がりとなります。
|
|
|
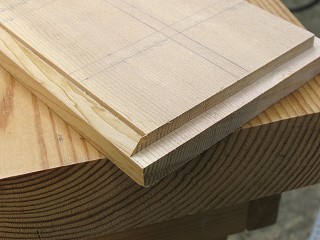 |
|
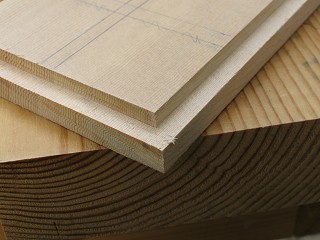 |
|
|
これは左側板の上の前側の角を見ているところですが、幅6mm、深さ5mmに削りました。
|
|
同じ左側板の上の後ろ側の角はこんな具合で、同じ深さで切削した角になっています。(段差無し)
|
|
|
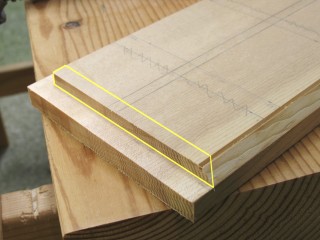 |
|
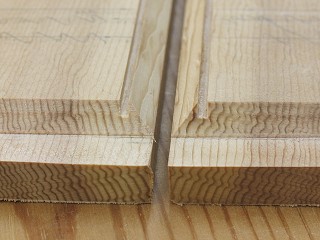 |
|
|
これは右側板下の前側の角を見ていますが、黄色線で囲った部分を45度に削り落とします。 これにはV溝ビット(VB-90G)を使いました。
|
|
切削が終わった左右の側板(左が右側板で右が左側板の下の部分。)です。 これで神経を集中しないとならないトリマー加工が終わりです。
|
|
|
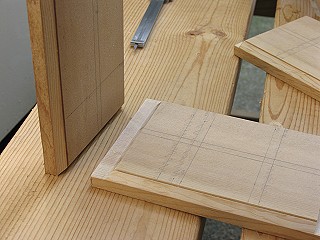 |
|
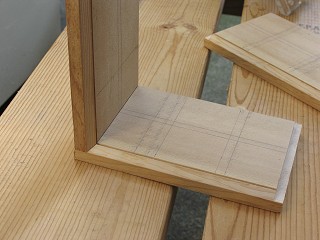 |
|
|
組立時の収まり具合をお見せします。 左に立っている板が底板で右に寝かしてあるのは右側板です。
|
|
右側板の下に底板を載せて45度傾斜切削部分がぴったりと合うように接合すればOKです。
|
|
|
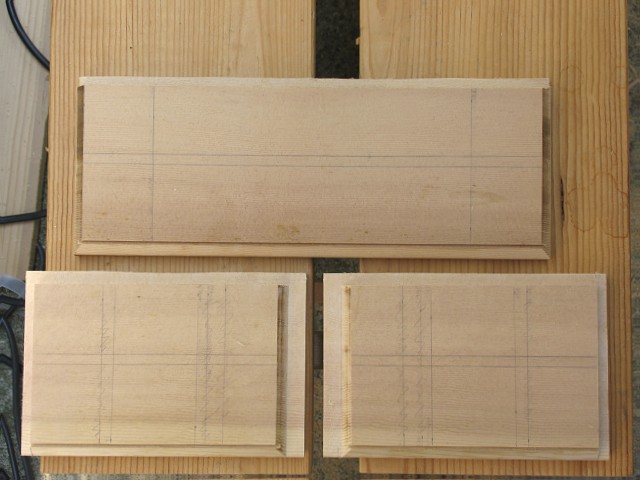 |
|
|
切り出しとトリマーによる成形加工が終わった3枚の部材(側板2枚と底板)。 緊張を強いられる作業は無事終わりました。
ここに沢山見える線はトリマー加工時のガイド板の固定位置を示すもので全部で18本ありますが、ガイド板を必要としないコロ付きのビットを4回使っており、合計で22ヶ所トリマーで切削加工した事になります。
|
|
|
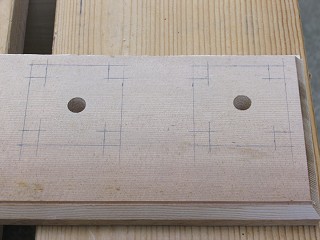 |
|
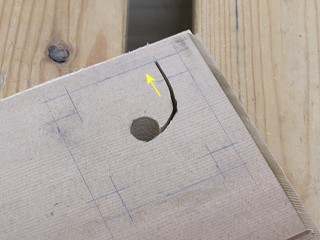 |
|
|
底板に太っちょ十字を2つあけますが私の典型的な手順をご紹介します。 最初に8-10φの穴を切り抜く部分の中にあけます。 ここから切り始めです。
|
|
電動ジグソー(CJ-250)に円仕上切りブレードを付けてこのように『曲線を描きながら最後は墨線に沿うように切断。』します。
|
|
|
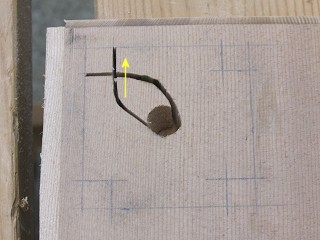 |
|
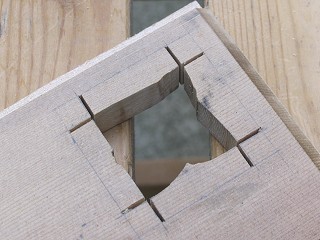 |
|
|
反対のカーブを描きながらもうひとつの墨線に沿うよう切り進みます。
|
|
全く同じ手法で残りの3箇所の隅に向けて切り込みを入れました。
|
|
|
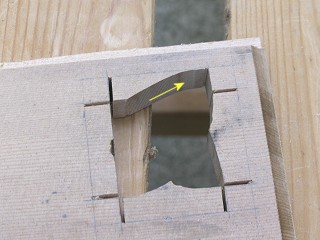 |
|
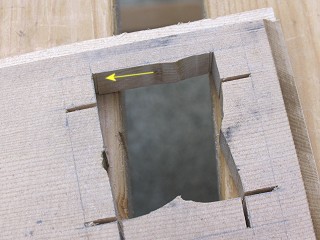 |
|
|
そうしたらこの方向にジグソーを動かして切断します。
|
|
左側の角に向けて切り落とします。 まだ直線にはなっていません。
|
|
|
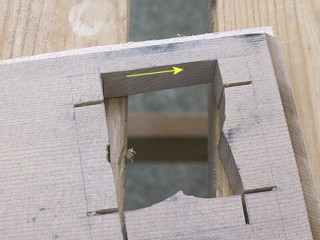 |
|
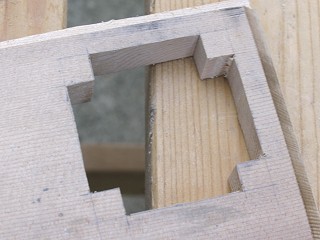 |
|
|
反対側から僅かに飛び出た部分を切り落とします。 これで墨線より0.2〜0.3mm内側を切り落とした事になります。
|
|
残り3箇所も全く同じ方法で切り落としてやります。
|
|
|
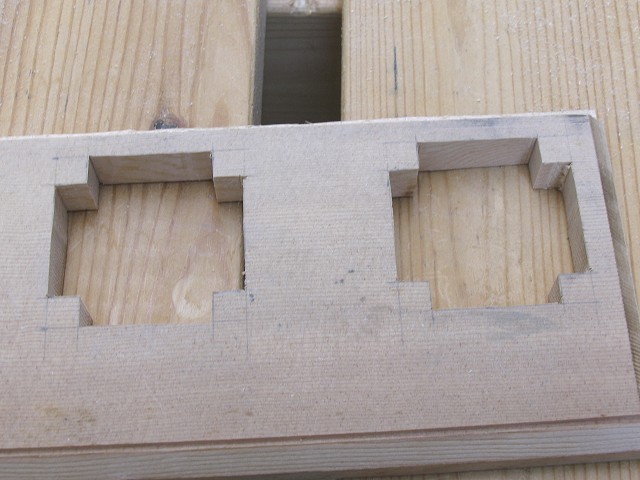 |
|
|
もうひとつの太っちょ十字も切り抜きました。 まだ研摩による寸法調整はしていませんが、先ほど説明したように0.2〜0.3mmの削り落としなので、作業に時間が掛かるわけではありませんし、このままでも余り問題なく見られる程度にはなっています。
|
|
|
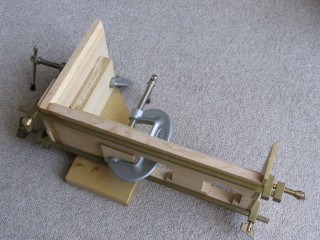 |
|
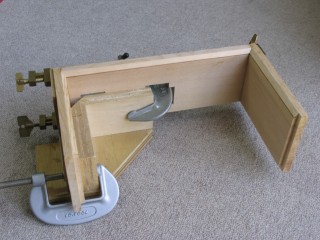 |
|
|
エポキシ接着剤で組み上げます。 L字型に接着している所ですが、自作『直角接合ジグ』を使って完璧な直角を出し、50mmクランプで部材の固定、ハタ金で圧着力の増加と完璧を期しています。
|
|
反対側の側板を貼り付けてコの字になります。 これが終了後この字の開いた部分を測ったところ、設計値は内寸が240mmですが、根元で240mm丁度、開いた先端で0.3mm程度すぼまっている状態で無論OKでした。
|
|
|
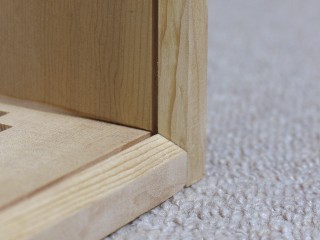 |
|
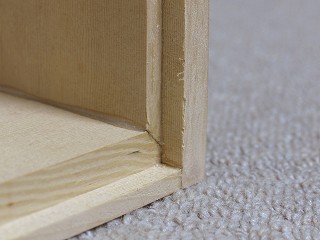 |
|
|
右前下の角部分です。 ここで見える細い溝にアルミパネルが落としこまれます。
|
|
左後下の角です。 底板は8.5mmも深く彫り下げましたが、この面に木ネジで裏板を固定します。
|
|
|
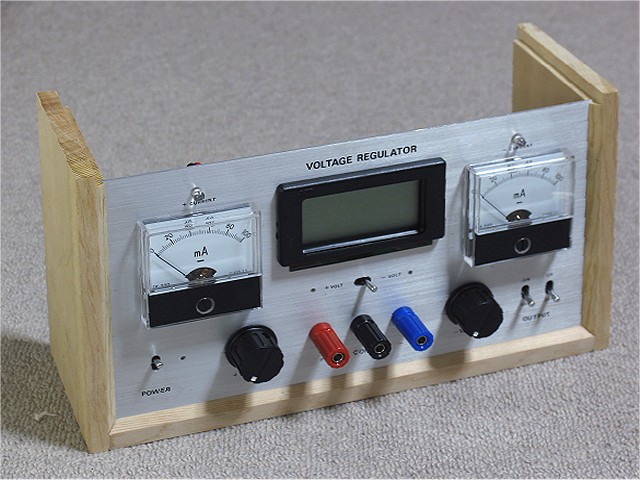 |
|
|
試しにアルミフロントパネルを落とし込んでみました。 全く問題なく収まっています。
|
|
|
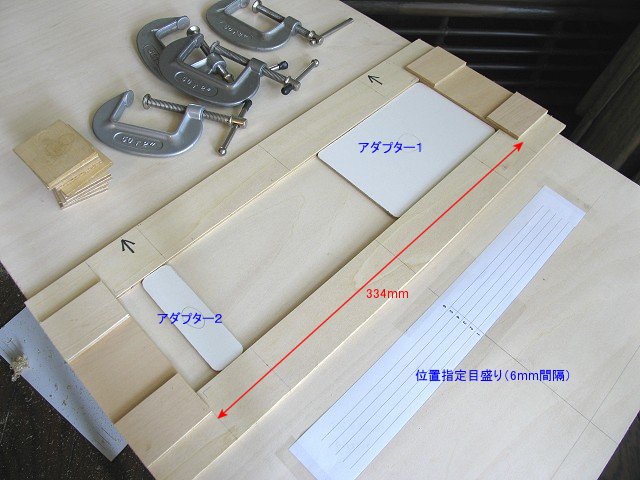 |
|
|
こちらは準備が終わった天板にスリットを掘り込む仕掛けです。 細長い枠の中だけを電動トリマーは移動(最長334mm - 90mm = 244mm)が可能で、その移動量は2枚のアダプター(角の丸い2つのクリーム色の板)の挿入で更に制限されます。 また目盛り板は6つの溝の間隔が正しく6mmにするためのもので、ジグの黒い矢印の先をこの目盛りに合わせます。 一番下は切り出す前の5.5mmシナ合板で、溝加工が終わったら所定の寸法で切り出します。
|
|
|
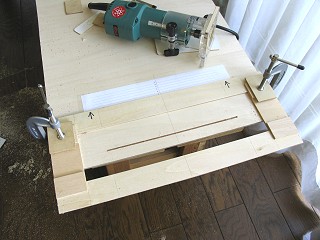 |
|
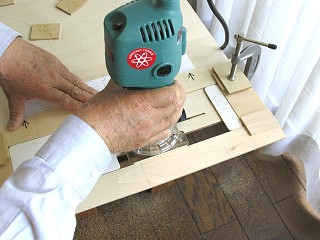 |
|
|
ジグを所定の位置に固定したら3mmストレートビットを取り付けて深さが2mm程度になるようセットしてフルに切削します。
|
|
次にジグは緩めずにアダプターを落とし込んで(左にアダプター1、右にアダプター2を落としてある。)ビットの飛び出る量を6mm以上にセットし、慎重にトリマーを落としこんで貫通穴をあけます。
|
|
|
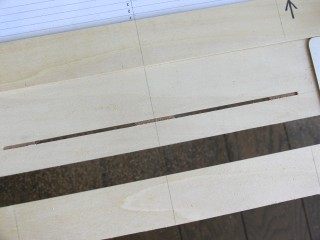 |
|
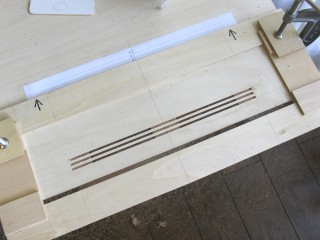 |
|
|
今度はアダプターを入れ替えて同じく貫通穴を彫ります。 貫通穴の長さはそれぞれ約80mmになります。
|
|
目盛り板に従ってジグの固定位置をワンステップ(6mm)ずらし、同じ作業を繰り返します。 こうしてこの写真では3本の全溝と貫通穴が彫れました。
|
|
|
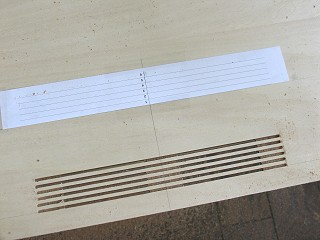 |
|
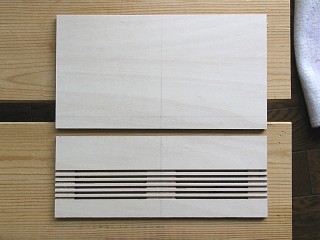 |
|
|
6本の溝、及び貫通穴が彫り終わりました。 この後所定の寸法で切り出します。
|
|
現物合わせで背面板も切り出しました。
|
|
|
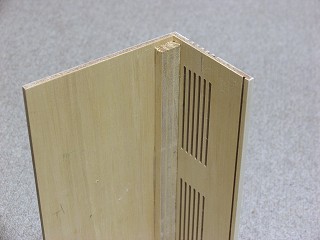 |
|
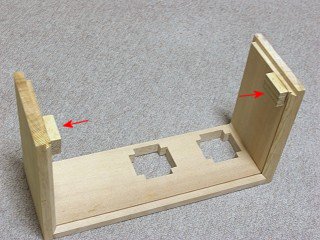 |
|
|
天板に背面板の角を当てるような形でエポキシ接着剤で貼り付けた後に補強材を切って同じくエポキシ接着剤で貼りました。
|
|
本体の2箇所に天板固定用の木片を貼り付けます。
|
|
|
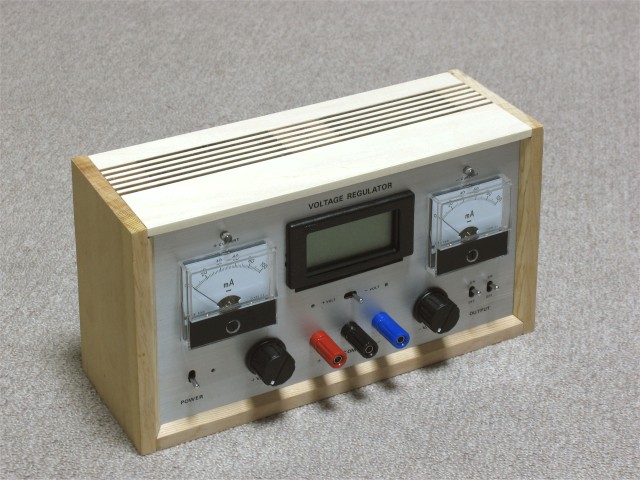 |
|
|
シナ合板の白っぽさが異様な感じを与えますが、塗装工程の着色で安定します。 頭の中でイメージしたとおりの物になりました。
|
|
|
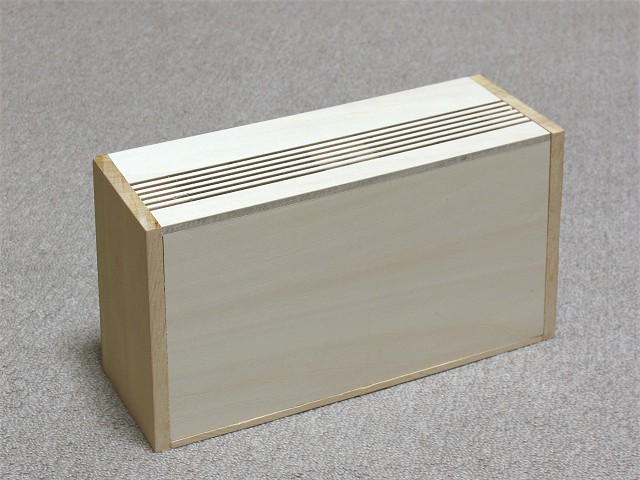 |
|
|
前後を反対にした眺めで、最終的には電源コードが1本ここに出てきます。
|
|
|
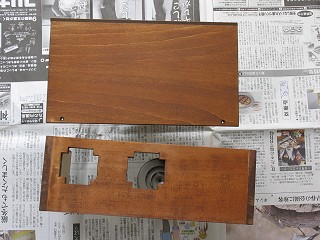 |
|
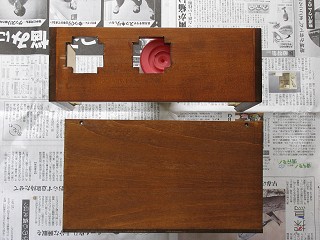 |
|
|
塗装工程における劇的な変化の一回目。 上はシナ合板で下の本体より白っぽかったですが、2回のステイン塗装で1回塗りの本体とほぼ同色になりました。 明度を下げるためにそれぞれもう一回ステインを塗って良しとしました。
|
|
透明クリヤーニス2回目が終わりました。 1時間半後に#400ペーパーで軽く表面を研摩してもう一度透明クリヤーニスを塗ります。
|
|
|
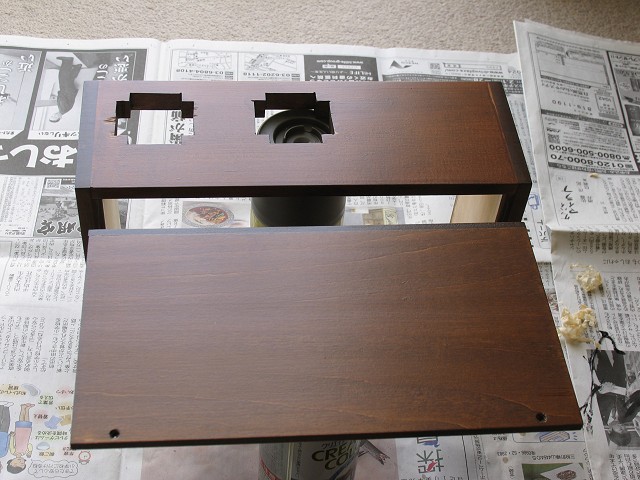 |
|
|
最後に艶消しクリヤーニスを塗ってほぼ乾燥しました。 それまで塗るたびに艶が増加してきましたが、一気にしっとりとした鈍い艶の重厚な感じに劇的な変化をしています。
|
|
|
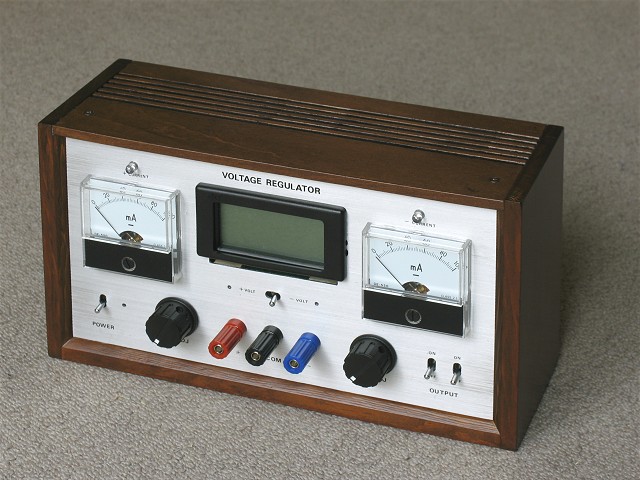 |
|
|
塗装前の物とは似ても似つかないくらい劇的な変化を見せ、重厚で落ち着いた感じに仕上がりました。 このくらいの変化が出る塗装作業にも力が入ります。
|
|
|
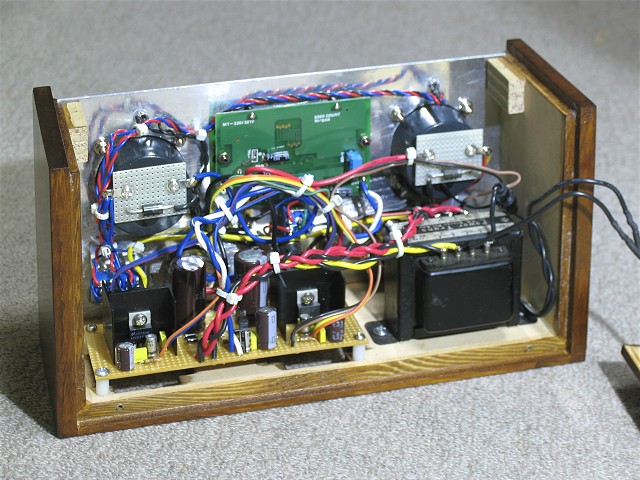 |
|
|
丸一日塗料が完全に硬化乾燥となるのを待って、基板と電源トランスの組み込み、そしてフロントパネルとの結線を済ませ完成しました。 ワイヤーは切断することなくフロントパネルを引き抜けるよう長めになっているので、結束バンドを使って空気の流通を阻害しないよう束ねています。
|
|
|
 |
|
|
通電テスト中。 現在は+電圧を表示中ですが、真中のスイッチを右に倒せばー電圧の表示に変わります。
|
|
|
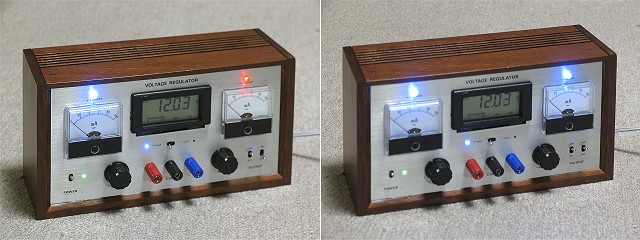 |
|
|
左の写真は+電圧は出力されているがー電圧は遮断中であることを表しており、右の写真は±両電圧が出力されている事を表しています。
|
|
回路が組み上がった後に一通り実働特性を測りましたが、電圧調整の抵抗を可変抵抗に置き換えたことによる出力電圧の変化が若干あった程度で、予定していた±4V〜±23Vのスペックには変わりありません。 まだ底板にゴム脚を付ける、底板にあけた空気取り入れ口にメッシュの蓋をする、デジタルメーター下の穴を塞ぐ、という作業が残ってはいますが、製作記としては完了と致します。Copyright (C) 2001-2019, Vic Ohashi All rights reserved.