|
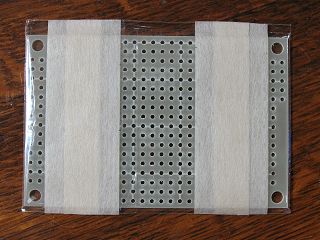 |
|
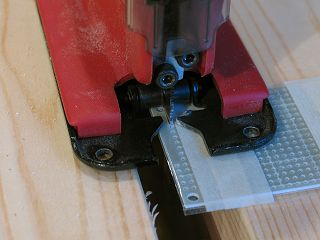 |
|
|
切り出す基板には銅箔面の傷・汚れ防止も兼ねて、マスキングテープを貼り付けその外側を切るようにしています。(切り幅は21-22mm)
|
|
切断にはおなじみの電動ジグソー(CJ-250)を使っていますが、ブレードは木工用では刃が持たないのと目が粗すぎるので、鉄工用に変更しています。(mini-ShopのN0.1ブレード)
|
|
|
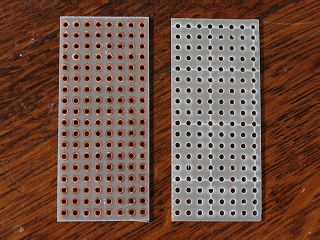 |
|
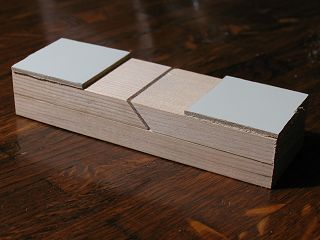 |
|
|
切断後切り口を替刃式ヤスリ(M-20GP)で研磨し直線性を極力出すと共に幅が21mmになるよう調整しておきます。
|
|
45度研磨ジグです。 斜めの溝は板を45度に切断後そこに基板を挟んで下の板に接着。 そして薄い下駄を両端に貼り付けました。 この下駄の存在でジグがヤスリで削られることはありません。
|
|
|
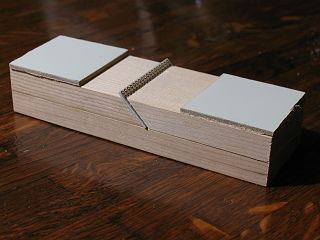 |
|
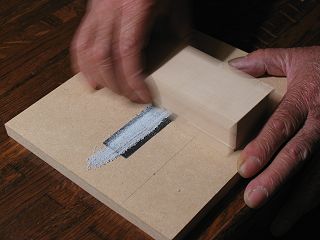 |
|
|
その下駄に研磨する基板を挿し込みました。 しっかり底当たりするように挿し込まないとなりません。
|
|
ジグを上下逆さにして台に貼った布ペーパー(#240)で研磨開始。 ペーパー幅が細いのでジグには当たりません。
|
|
|
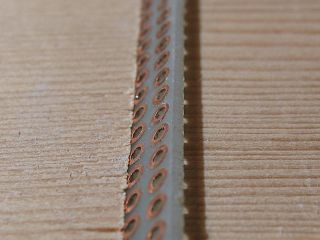 |
|
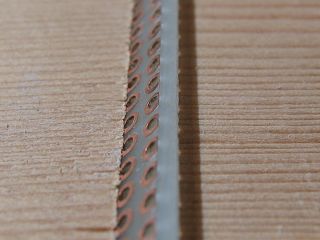 |
|
|
これは研磨前のクローズアップです。 この方向から見て基板の木口が平面になればよいわけです。
|
|
研磨開始では下駄の面と台の間に隙間が出来てがたつきますが、そのがたがなくなるまで終了したらこのように木口は平面になります。 そしてこれ以上は削れなくなります。
|
|
|
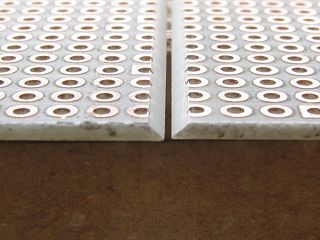 |
|
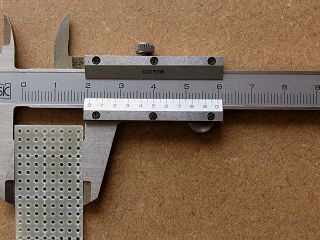 |
|
|
45度研磨が終了した2枚の基板の研磨断面クローズアップ。 この斜面にエポキシ接着剤を塗って直角に張り合わせることになります。
|
|
基板の幅がどうなったをノギスで確認しました。 実測20.65mmでほぼ計算どおりの値です。 4枚のばらつきは±0.05mm程度でした。
|
|
|
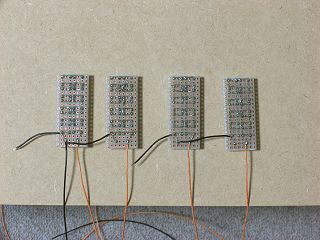 |
|
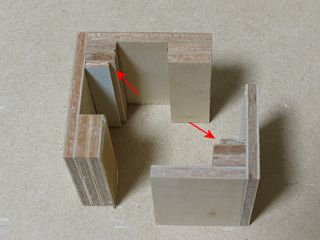 |
|
|
組み立て前の結線の様子です。 長さ50cmのオレンジ色の線は各基板のプラス側に結線し、黒い40mm程の線は各基板のマイナスに結線しますが、その反対側をもう1枚の基板のマイナスに結線した物を2組作ります。 そのうち1組のマイナスに1本の黒い50cmの線を接続してやります。
|
|
基板の直角接合ジグはこんな具合です。 矢印の先が基板と基板を突き合せ保持する部分です。 長さは45mmですので基板を当てると両端が僅かに飛び出し突き合せ状態がはっきりと確認できます。
|
|
|
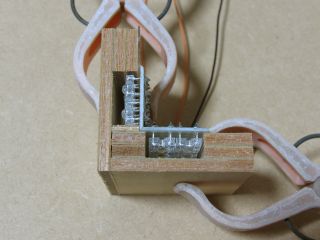 |
|
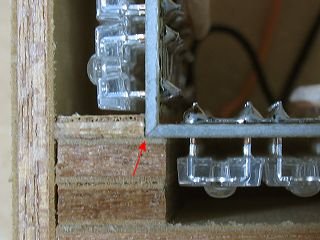 |
|
|
線で繋がった1組の基板の接合面(斜面)に楊枝でエポキシ接着剤を塗りつけてセットしますが、突合せ部分にポリエチレンの薄いフィルムを挟んでくっ付き防止をします。 そして突合せ部分の接触状態、位置関係を確認した上で洗濯バサミで固定します。
|
|
突合せ部分(赤矢印の先)のクローズアップ。 基板の45度に研磨した部分がきちんと接触しており斜面研磨がうまく出来ていることが判ります。
|
|
|
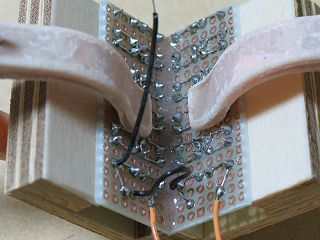 |
|
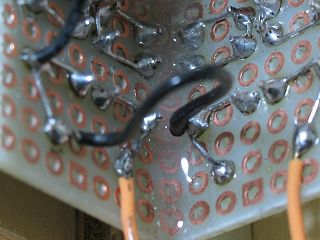 |
|
|
次にこのような角度に置いて突合せの隅の部分に楊枝でエポキシ接着剤を流し込みました。 傾けると流れ出すのでこの状態で硬化させます。
|
|
そのクローズアップです。 尚エポキシ接着剤は絶縁性能が良いので漏電などの問題を起こすことはありません。 但しエポキシが付いた部分は半田付けは出来なくなります。
|
|
|
 |
|
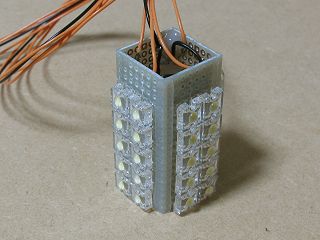 |
|
|
2組出来たL型を更に貼り合わせてジグで保持し輪ゴム2本でぐるぐる巻きにして若干圧着の力が掛かっています。(接着は矢印の先2箇所) 見た感じでは期待以上に上手く仕上がっていそうです。
|
|
完成したLEDランプブロック。 今回30分硬化開始型を使って1ヶ所の硬化時間を2時間とし次の接着をしましたが、この状態で12時間寝かして完全硬化後にはみ出た接着剤を削り落とし残る内部の結線を済ませます。
|
|
|
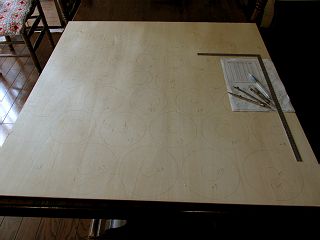 |
|
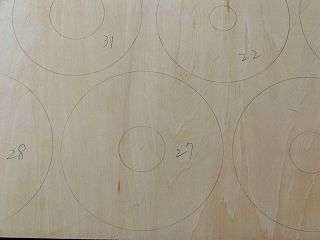 |
|
|
円盤の材料は4mm厚シナ合板ですが、サブロクの半裁で合計42枚を切り出せました。 購入に当たっては例外的な選別ですが表面が美しいかどうかより芯材の色味が白っぽいものを選別しています。
|
|
線引きに当たっては外側と内側の2つの円以外に円盤の番号(上から下への順序)を描き込んであります。 そうしないと切り離した時に訳がわからなくなります。
|
|
|
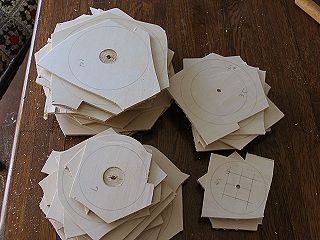 |
|
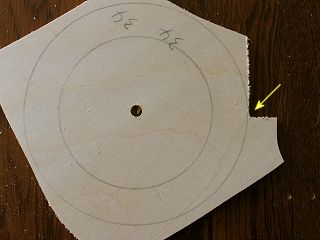 |
|
|
それらを適当に切り離しました。 回転させた時に切断ガイド/押さえ板に当たらなければ大きくても或いは変な形でも問題ありません。
|
|
全ての板には一箇所このような切込みを入れており、ここからジグで切り出します。 また中心に6φの穴をあけます。
|
|
|
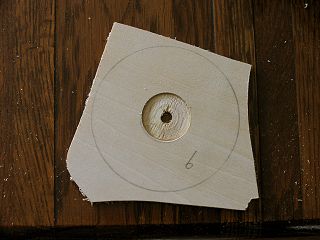 |
|
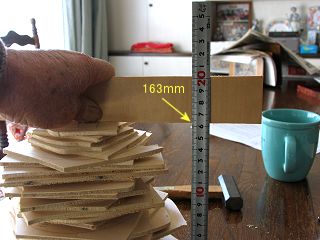 |
|
|
2.に属する25φの穴をあける板は25φのフォスナービットで深さ1mm程度の座繰り穴をあけてから中心に6φの穴をあけておきます。
|
|
ふっと思い付いて42枚を重ねて高さを測りました。 163mmで設計値162mmに対し1mm大きいだけ。 切り屑が多少挟まっておりますので、最終的には接着剤の厚みを含んでも圧着保持しますのでほぼ設計値になるでしょう。
|
|
|
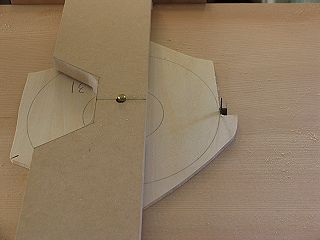 |
|
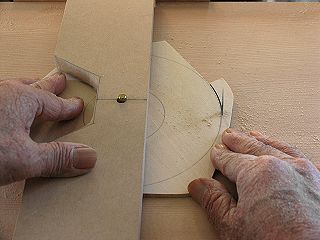 |
|
|
ジグそのものの詳細は別項をご覧頂くとして、先ほど説明した切り欠きをこのようにセットします。
|
|
そして切断開始。 殆ど単純作業に近く緊張を強いられることは殆どなく淡々と作業は進められます。
|
|
|
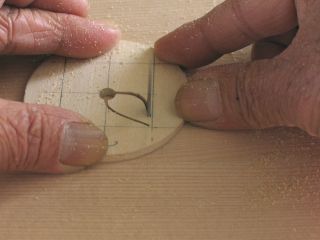 |
|
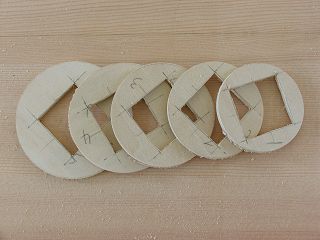 |
|
|
内側の切断に入ったところですが、切断ガイド/押さえ板を外して正方形を中心の6φの穴から切り出しています。
|
|
5枚の円盤はこのようにジグ無しで正方形を切り出しました。 この後成形研磨で寸法出しをします。
|
|
|
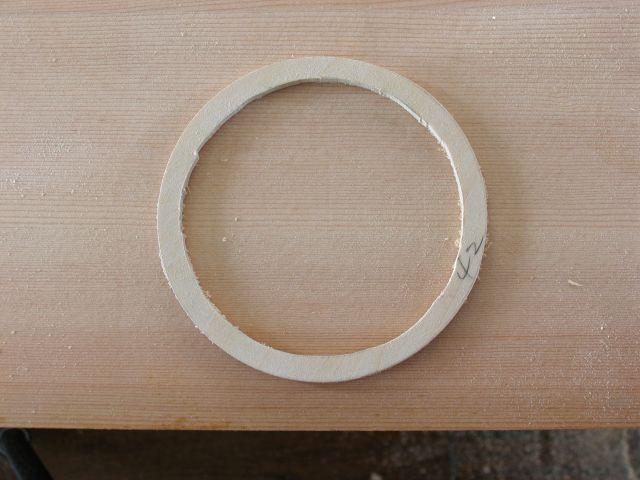 |
|
|
内側の丸穴をジグ無しで切ってみようと最も下のNo.42で試したのがこれです。 多大な緊張を強いられた割には結果が悪くかなりの成形研磨が必要になってしまいます。 そこでジグを使って内側の穴の切断を試すことにしました。
|
|
|
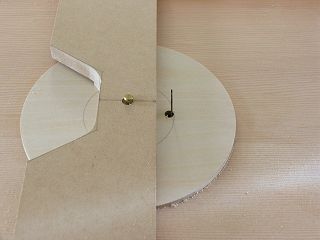 |
|
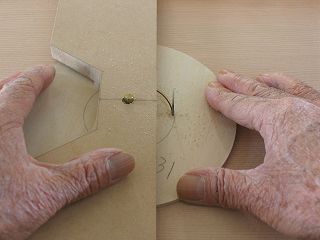 |
|
|
内側の円に接するように6φの穴をあけてここから切り出します。 切り出し位置は墨線より1mm前後内側になるので、ブレードが左に傾くよう少し押し付けて切断ガイド/押さえ板を固定します。
|
|
切断開始。 ブレードは左に僅か傾いたまま切断しているので墨線よりも内側を進みますが、そのまま続けるとブレードは少しずつ垂直になってくる(墨線に載ってくる)ようになります。
|
|
|
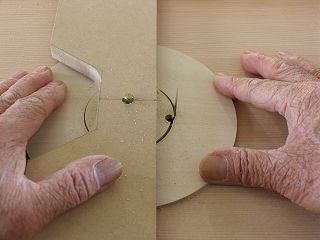 |
|
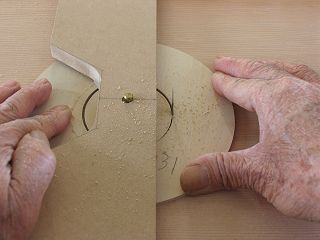 |
|
|
一周しましたが切断開始位置よりもブレードは右にずれて食い違っていますが、このまま切断を続けます。
|
|
そうすると既に切り落とされた内側の小さな円盤にブレードが当たり左に傾かないまま切断を続けるため、切り始めの部分の修正切断が自動的に出来てしまいます。
|
|
|
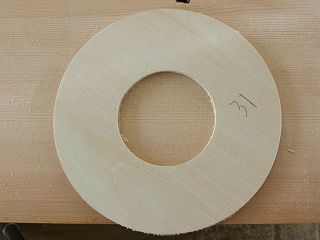 |
|
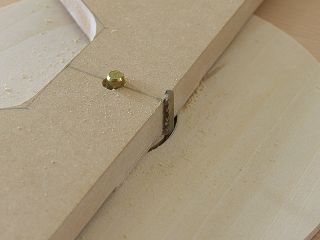 |
|
|
こうして切断が完了した物です。 切断後に修正の研磨は全く施していない切りっぱなしで、ほぼ完璧の状態。 これは感激でした。
|
|
内側の円のジグによる最少径切り出しは切断ガイド/押さえ板の幅(36mm)で決まりこのNo.25が切断可能な最も小さな直径(39mm)でした。
|
|
|
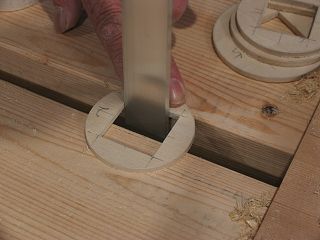 |
|
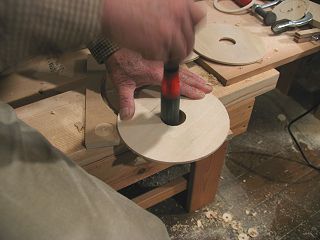 |
|
|
全ての切断が終了し寸法微調整の研磨に入りました。 正方形の穴には自作替刃式平ヤスリがドンピシャです。
|
|
ジグを使わず丸穴を切断した物はDR-1000Pの使用が最適でドンピシャに短時間で成形できます。
|
|
|
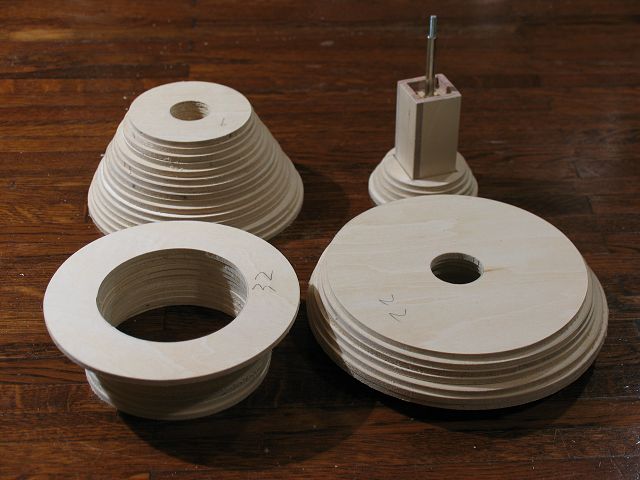 |
|
|
切断が完了した4種類のグループ。 右奥が一番上で次がその左、そして手前右、手前左と続き底の部分になります。 一番上にはランプホルダーを挿し込んでみました。
|
|
|
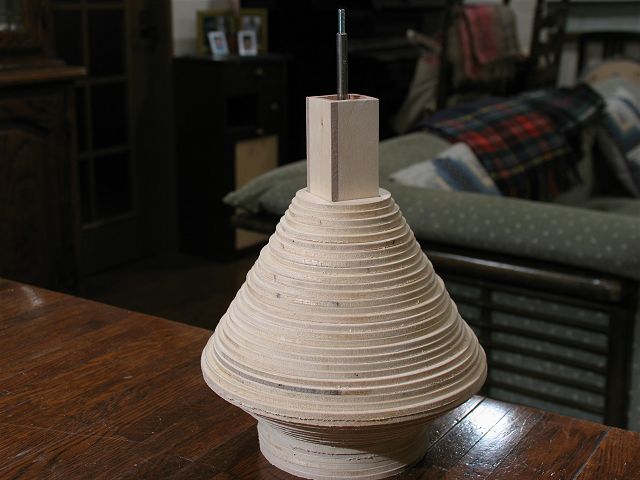 |
|
|
それらを積み上げてみました。 位置を正確に調整しているわけではないので多少凸凹していますが、最終的な形が見えつつあります。
|
|
切断ジグを実際に使ってみて円切り抜きにも有効なことが判り、その有効性が高まっていますが、汎用的なジグの製作ではジグ使用過程で発見した様々なことを考慮してより完成度の高いものにしたいと考えています。
|
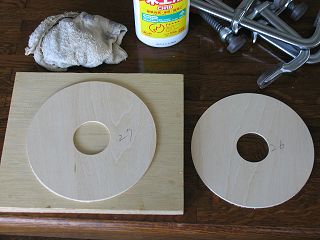 |
|
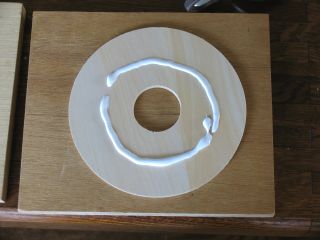 |
|
|
円盤接着開始。 これは27番の板の上に26番(右側)を貼り付けるところです。
|
|
26番の板をひっくり返して木工ボンドを塗り付けました。 この量は実際には多すぎます。
|
|
|
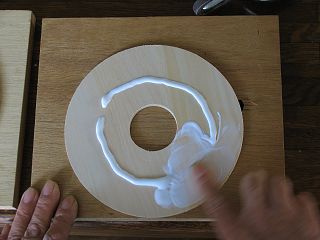 |
|
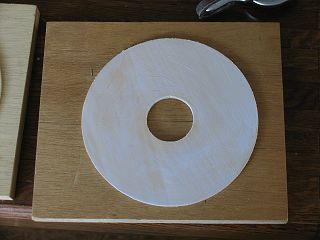 |
|
|
木工ボンドを指で広げてゆきます。 塗りつけたボンドの厚みが大きいと圧着保持の際にぬるっと横に滑るので、薄く薄く広げてやります。
|
|
薄く塗り広げると木目が結構透けて見えますが、ボンドの表面が乾燥しないよう更に均等に慣らします。
|
|
|
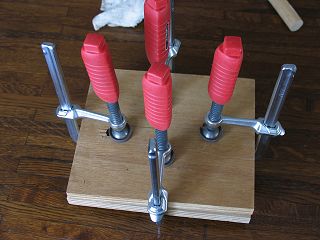 |
|
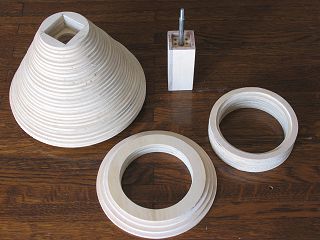 |
|
|
貼り合わせ後クランプで圧着保持。 この時締め付けた後に完全に緩め、ずれが生じていないか確認の上再度締め上げるのが重要。 3時間程寝かして次の接着に進みます。
|
|
ウィークデイに仕事の合間合間をぬいながら4日掛りで3つのブロックが完成しました。 一番手前と右は内径80mmの穴あき部分ですが、この後の工程後に接着します。
|
|
|
註) この接着作業は作業時間よりも寝かせる時間(3時間程度)が長いので、大変長く掛かります。 あせっての作業は
接着不良を招くので禁物。 また圧着保持は接着強度の確保と接着面の隙間防止にクランプ使用は不可欠ですが、やわ
なクランプ(安物のプラスチック製など)は圧着力が上がらないので不適当です。
|
|
|
 |
|
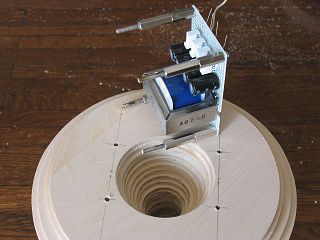 |
|
|
基板を保持する部分は真鍮製の六角パイプでM3の雌ネジが切られた15mmと20mmをM3のボルトで連結して使います。 また片側には20mm程M3のボルトが飛び出るようにしています。 これらは全て瞬間接着剤により固着しました。
|
|
固定金具取り付け面に3.2φの穴をあけ、取付金具は電源基板に仮固定しました。 そして穴の中に5分硬化開始型エポキシを楊枝で注入し、取付金具のネジ面にもエポキシを塗りつけます。
|
|
|
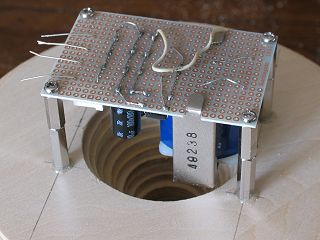 |
|
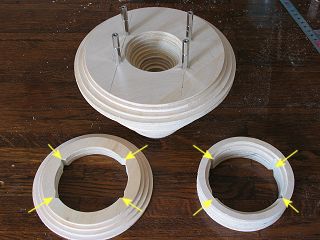 |
|
|
そうしたら穴の中にM3ボルト部分を挿し込みます。 圧着保持は不要で、このまま1時間放置すれば完全に固着します。 結構ぎりぎりですが、トランスは本体に接触しておりません。
|
|
仮止めした基板を外したのが上ですが、次に内寸80mmの穴をあけた2つのブロックに基板が引っ掛からないための切込みを(矢印部分)を電動ジグソーで入れました。
|
|
|
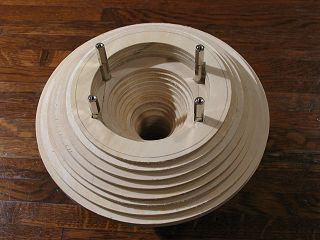 |
|
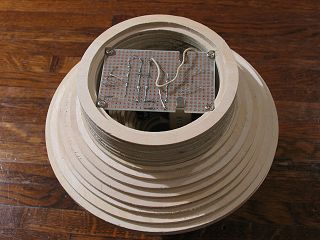 |
|
|
その上で右上の手前左側のブロック(32〜35番)を木工ボンドで接着しました。 一番底になるブロック(36〜42番)は外側の成形作業が終了後に接着します。
|
|
確認のため一番底のブロックを載せてみました。 底になる円盤は内径が少し大きいのですが、この部分に後ほど加工する蓋が納まります。
|
|
|
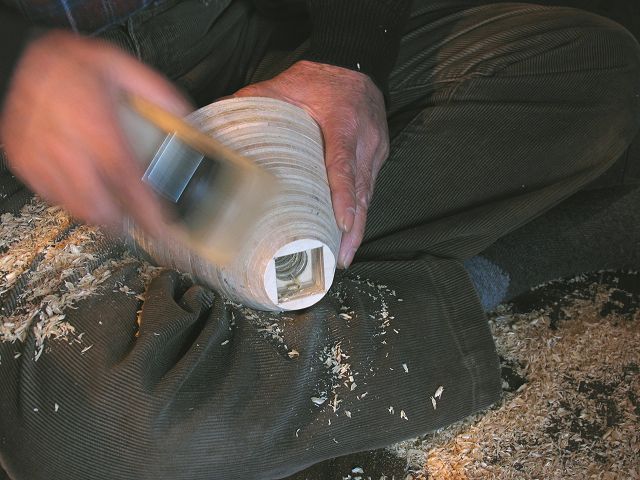 |
|
|
雨が降っていて外で作業できないため床にあぐらをかき、足の上で本体を支えカンナ(KK-50)にて段差を削り落としています。 先端の細い方から底部に向かって一様に削るのですが、効率良く作業は進みます。
|
|
|
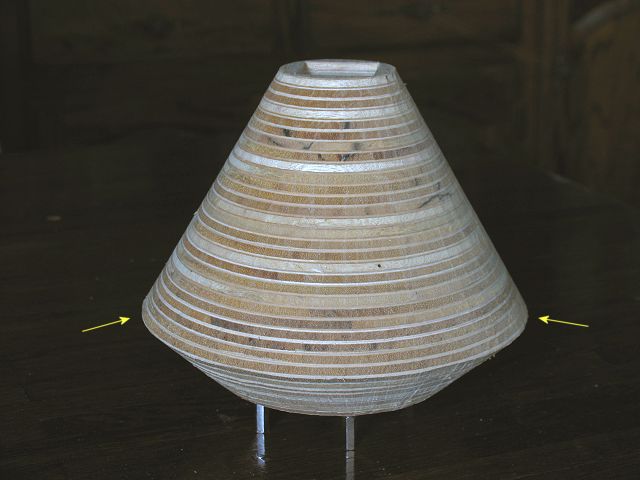 |
|
|
段差がほぼなくなるまで削り込んだ状態で、良く見ると上から下に掛けて削った跡が見えます。 この時点では下部の突出部分の丸みは全く手をつけずに進めています。
|
|
|
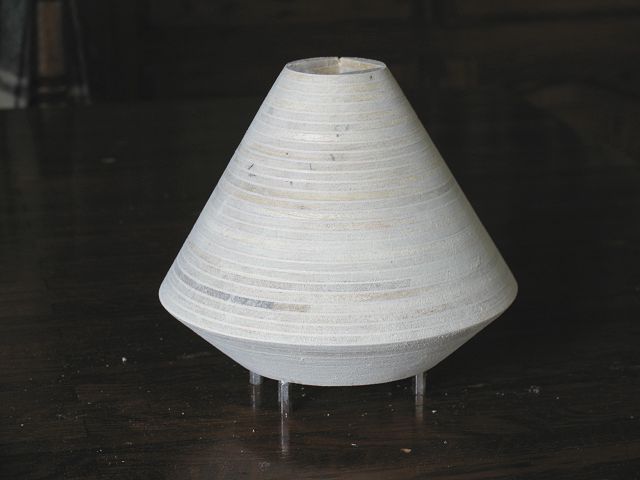 |
|
|
電動サンダー(S-5000)に#60布ペーパーを取り付けて外形を整え段差や凸凹を取り除きました。 作業は順調に進み30分程度の所要時間となっています。 但し研磨中は削り屑が舞い上がりますので、作業中の写真をお見せできません。
|
|
|
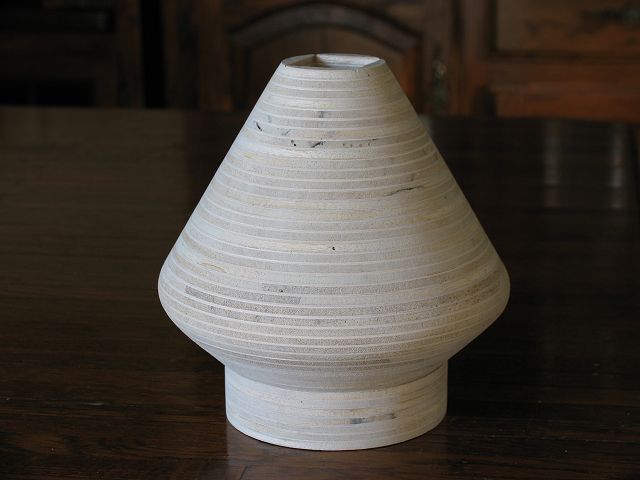 |
|
|
下部の突出部を粗目ヤスリにて手研磨で丸めて大雑把な形を出した上で、電動サンダーに#60のペーパーの組合せで研磨。 その後#120に変えて研磨し最後に#240のペーパーを付けたハンドサンダーで仕上げ研磨をしました。 底の円筒状のブロックの上に載せてあるだけですが、電源コード、スイッチ取り付けの加工後貼り合せます。 基本的な本体の組立作業は終了です。
|
|
|
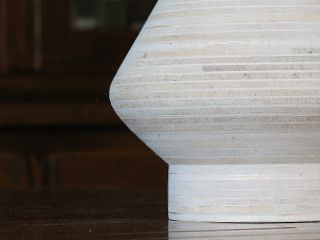 |
|
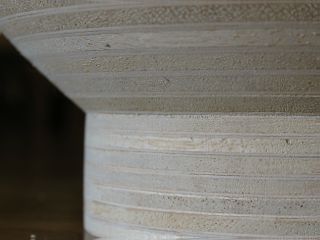 |
|
|
底に近い部分の丸みのある突出部分。底の円筒状ブロックはシャープに繋がっています。
|
|
底の円筒状の部分は別途研磨してから接着すればこのようにシャープな感じに仕上がります。
|
|
|
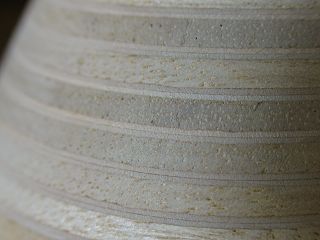 |
|
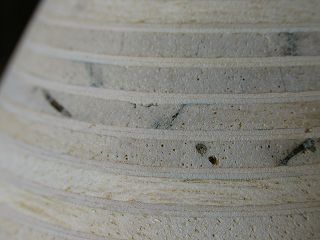 |
|
|
ドアップで表面を見たところ。 強力な圧着保持をしましたから板と板の継ぎ目はこのくらいアップして薄っすらと見えます。
|
|
こちらは少々汚らしい乱れのある所ですが、材料に起因するため濃い目に着色して目立たなくするしかありません。
|
|
|
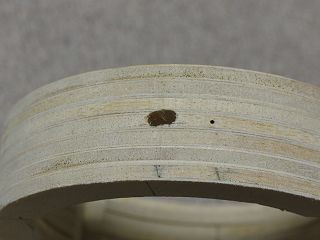 |
|
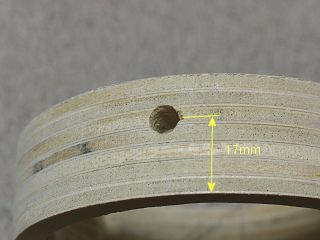 |
|
|
底のブロックに電源コードを通す穴をあけました。 方法は3φ木工ドリルで接近した穴を2個あけてヤスリで少し調整しただけです。 鉄工ドリルだと横滑りして上手く並んであけられないでしょう。
|
|
こちらは電源スイッチを固定する穴で設計時点よりも少し下にずらし、底面から17mmとしました。 これ以上下げると基板に当たる可能性があります。
|
|
|
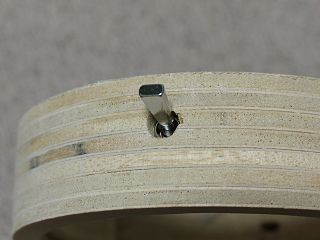 |
|
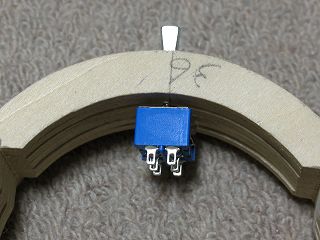 |
|
|
電源スイッチは緩からずきつからず入ります。 そして先端はこのように出て追加加工無しにON-OFF-ONの作動ができます。
|
|
内側から見た様子はこんな具合です。 最終的には塗装後エポキシ接着剤で固着してしまいます。
|
|
|
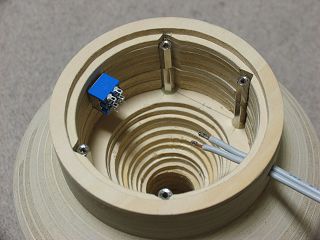 |
|
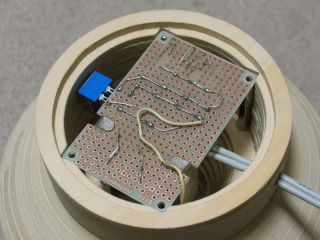 |
|
|
スイッチと電源コードを挿し込んだ底ブロックを本体に載せました。 基板がない状態での感じです。
|
|
そして電源基板を載せました。 この角度で見るとなにやらスイッチと至近距離にあるようですが?
|
|
|
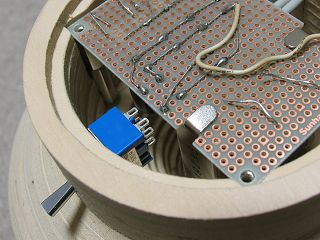 |
|
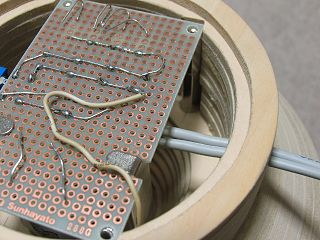 |
|
|
ご覧のとおり約5mm位の隙間があり、基板と接触する心配は全くありません。
|
|
電源コード側は余裕しゃくしゃくのようですが、この電源コードの下にヒューズホルダーが収まりますので、がらがらという感じにはならなくなるはずです。
|
|
|
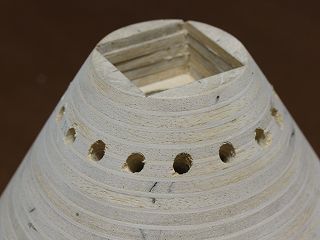 |
|
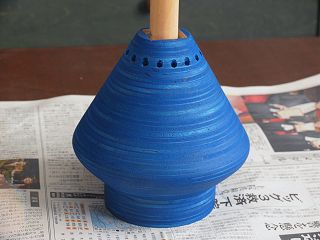 |
|
|
本体最後の加工は放熱口の穴あけ。 5φの木工ドリルであけたのだがかなり柔らかいためきりっとした切り口に仕上がらない。 少々残念ではある。
|
|
そして塗装に入ったのだが最初は着色。 ポアステインのブルー色を水で2倍に薄め、ラックニス刷毛で2回着色した所。 この後研磨するので完全乾燥させないとならない。
|
|
|
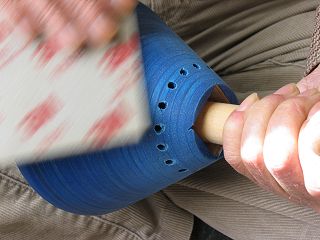 |
|
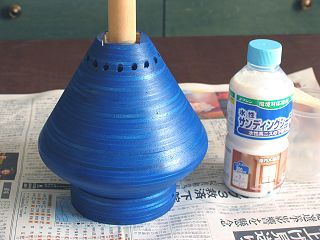 |
|
|
水性ポアステインの塗装面は水を含んだ木繊維が毛羽立ってきますので、スポンジ研磨剤で表面を軽く研磨しざらつきを取ります。 そして更に2回着色しました。
|
|
下地塗装は水性サンディングシーラーを4回塗り。 これは一度目の塗装後ですがスポンジ研磨剤で研磨後次の塗装に進みます。
|
|
|
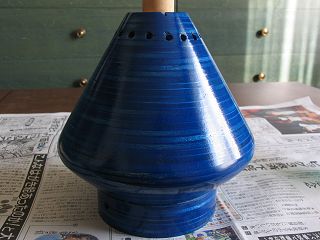 |
|
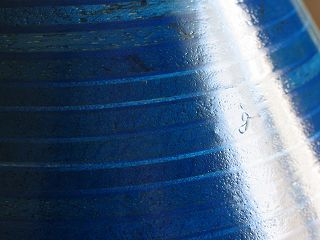 |
|
|
サンディングシーラーの塗装と研磨を4回繰り返した表面はかなりの艶が出て色味が濃くなって見えます。
|
|
その状態のクローズアップですが、光っている所の境界付近を見ると木繊維の穴がかなり埋まってきているのが判ります。
|
|
|
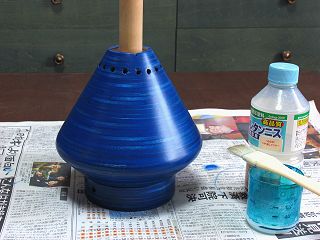 |
|
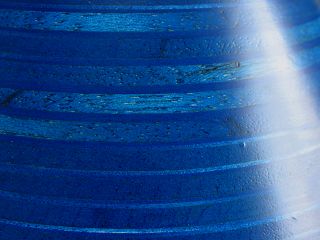 |
|
|
最後が水性ウレタンニス艶消しの塗装で、2回塗りして間にはスポンジ研磨剤で研磨しました。 面白いことに色味は少し明るくなりました。
|
|
そのクローズアップを見ると木繊維の穴はほぼ目立たなくなっており通常の目視距離では見えないと思います。
|
|
|
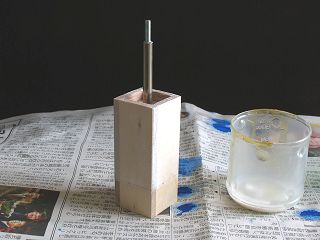 |
|
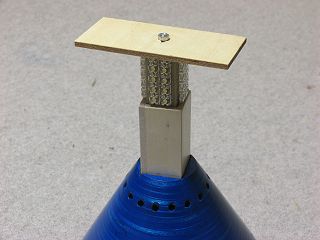 |
|
|
ランプホルダーはポアステインの白で着色し水性ウレタンニス艶消しクリヤー2回塗りで仕上げました。 これを本体トップにエポキシ接着剤で固定します。
|
|
そしてLEDランプブロックを仮固定し、LEDからの配線を底の方に通しました。
|
|
|
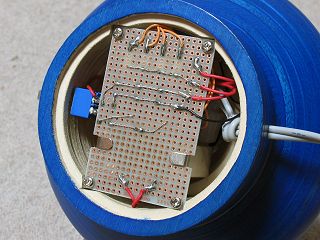 |
|
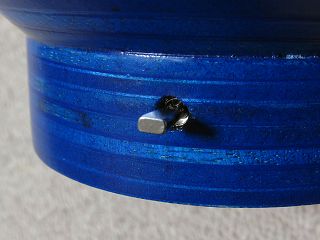 |
|
|
スイッチ電源コード周りと電源基板に配線を済まし電源基板を仮固定しました。
|
|
電源スイッチのクローズアップで、水平ポジションはOFFで、上に倒すとHigh(高輝度)、下に倒すとLow(低輝度)になります。
|
|
|
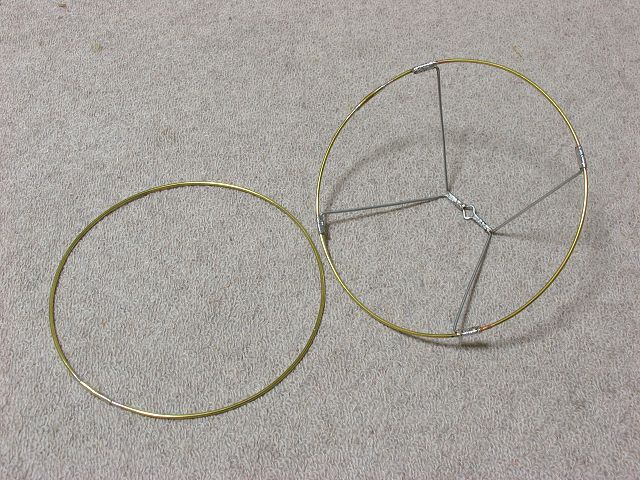 |
|
|
2mmの真鍮棒と1.5mmの亜鉛メッキ鉄線で作ったシェードのフレームです。 接続はハンダ付けとしています。
|
|
|
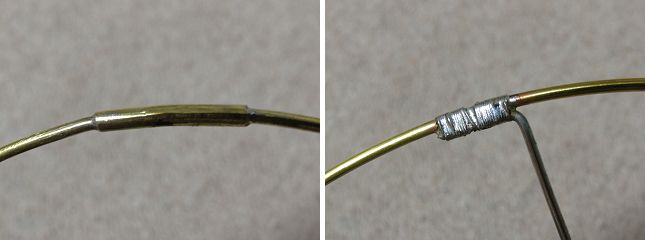 |
|
|
丸枠の接続には内径2mmの真鍮パイプを使い、ハンダ付けしています。(左) またアームと丸枠の接続は0.3mmの銅線を巻きつけて一旦固定してその後全体をハンダ付けという方法で、アームの中心部分も同じ方法としました。(右)
|
|
|
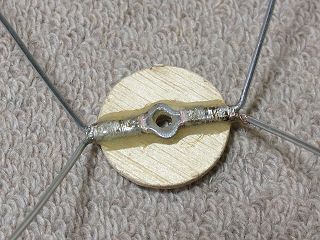 |
|
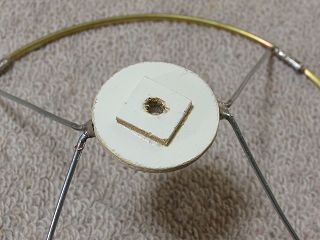 |
|
|
アームの中心部には直径30mmの円盤を2.7mm厚合板で作りエポキシ接着剤をどっぷりと使って接着(というか埋め込んだと言った方が適切?)しました。
|
|
裏面には四角く切断した板を貼り付けこの板はLEDブロックの内部に入り横方向のずれを防止します。
|
|
|
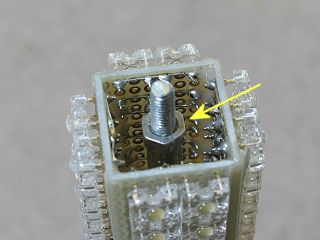 |
|
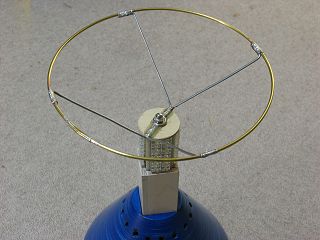 |
|
|
中央のネジにナットを捻じ込み、シェード枠を装填した時にネットの面に30φの円盤とLEDブロックの間に僅かな隙間が出るよう調整して瞬間接着剤でナットを固定します。
|
|
シェードの枠を固定しましたが、僅かな隙間を作ったお陰でシェード枠に横方向の力を加えても、LEDブロックには容易に及ばなくなります。 この後フレーム部分を白いペイントで塗装しました。
|
|
|
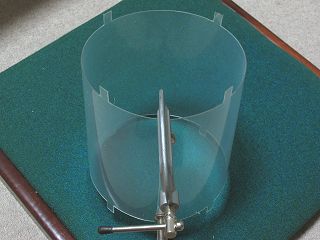 |
|
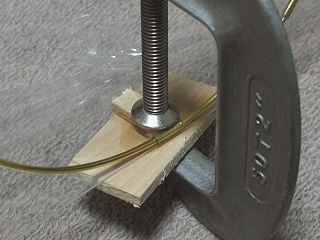 |
|
|
シェードの筒部分を切断して丸めた所です。 真鍮の枠に固定するための耳が上下4箇所に付いています。
|
|
真鍮枠にはこのように爪の部分を曲げて固定し、接着剤(塩ビ用液状)を少し流し込み1時間放置しました。
|
|
|
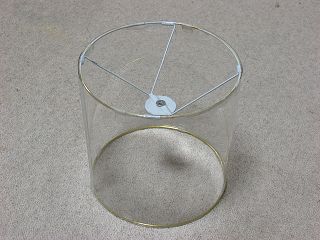 |
|
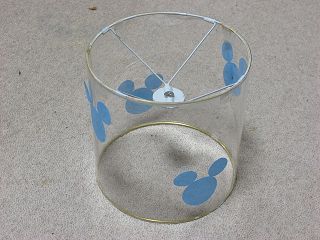 |
|
|
合計8箇所の爪を内側に曲げて接着後、PET板の始めと終わり部分をクランプで挟み接着剤を流し込んで組立ては一応完成です。 その後真鍮枠とPET板の接触部分に瞬間接着剤を流し込み、筒とフレームを一体化しました。
|
|
思いつきなのですが障子紙をステイン(水で6倍ほどに薄めた物)で着色し、ミッキーマウスの形に切って4箇所に軽く貼り付けました。 簡単な方法ですが雰囲気ががらりと変わり柔らかくなります。
|
|
|
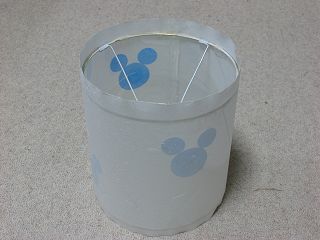 |
|
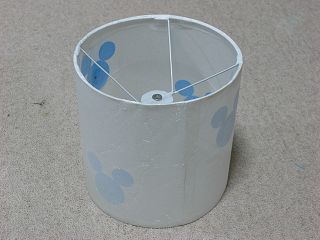 |
|
|
その上に障子紙を幅180mm程に切断したものを巻きつけて、障子紙の始めと終わりの部分を接着剤(ボンドGPクリヤー)で固定しています。
|
|
障子紙のはみ出た部分を内側に巻きつけ接着剤(ボンドGPクリヤー)で貼り付けました。
|
|
|
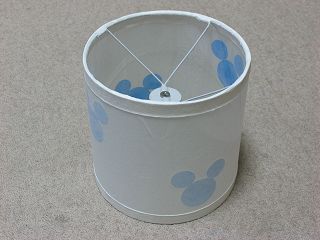 |
|
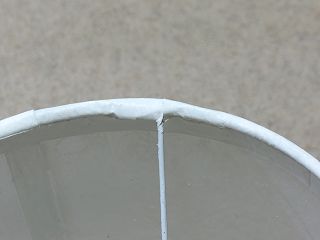 |
|
|
枠の部分には障子紙で作った帯(2枚折り)を巻いて、透けて見える内側に貼り付けた部分の粗が見えにくくなるようにしました。
|
|
そのクローズアップ。 ちょっと雑な仕上がりですが、現在の私の技量ではせいいっぱいです。
|
|
|
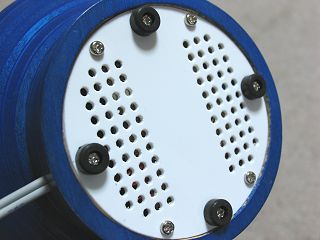 |
|
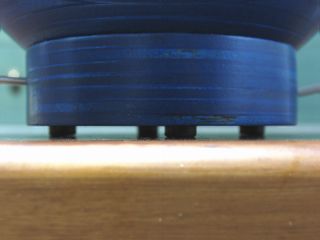 |
|
|
底蓋には2mm厚PET板を使いました。 放熱の空気流入口として3φの穴を84個あけました。 この穴に金属棒を挿し込んでも100V関連の危険な部分には触れません。
|
|
足は本体底面より4mm突出しており、その隙間から空気が入ります。 底板の穴は直径27mmの大きな穴と等価ですので放熱効果は十分だと思います。
|
|
|
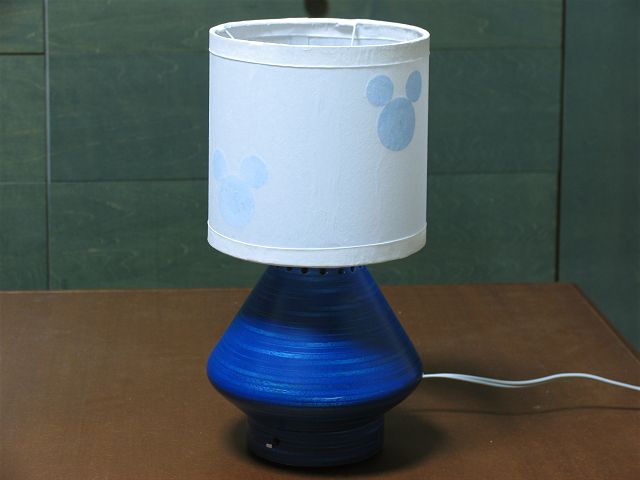 |
|
|
以上で完成です。 ミッキーマウスは構想段階では全く考えていなかった思いつきですが、簡単に出来てしかも喜ばれそうな感じがします。 本体のブルー色は大変美しく仕上がったと思います。 構想段階でのイメージにほぼ近いものに仕上がっています。
|
|
|
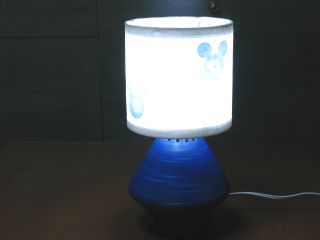 |
|
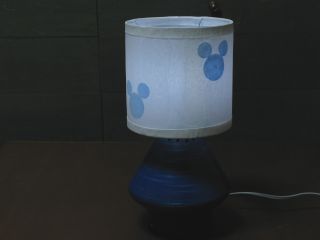 |
|
|
これは実際に点灯した写真で、左は高輝度モード、右は低輝度モードでの明るさの違いを表しています。 撮影はマニュアルとして同じ露出で撮っています。 スタンドの周りがかなり暗いですが、ミッキーマウスが潰れないよう露出を抑えたせいであり、実際に見た感じはもっと明るいです。
|
|
|
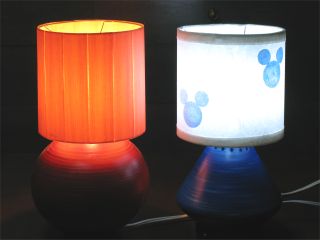 |
|
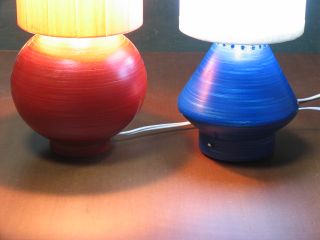 |
|
|
クリスマス用テーブルランプとの比較。 使用目的が違うので当たり前ですが、シェードを通過する光の量がこんなに違います。
|
|
またクリスマス用テーブルランプは本体が球状なので、下方向には光がブロックされて大きな影が出来てしまいます。
|
|
ぎりぎりでクリスマスに間に合いましたが、孫に見せるなり思いつきで入れたミッキーマウスのシルエットが大変気に入ったようで、早速自分で電源スイッチをパチンパチンといじって、点灯すると歓声を上げていました。 やれやれほっと一息!といったところです。Copyright (C) 2001-2019, Vic Ohashi All rights reserved.