|
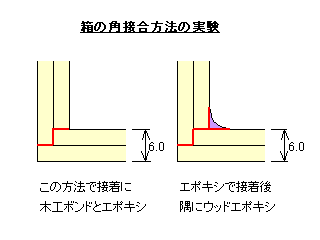 |
|
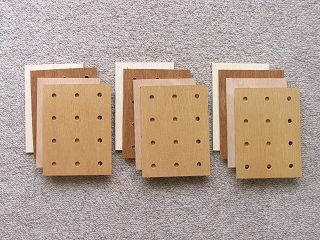 |
|
|
接着強度試験のために作った被試験試料の断面。 左が1番目と2番目で右が3番目ということになります。
|
|
手持ちの端材の関係で穴あき合板、カラー合板、普通の合板が混在していますが、それぞれの組が同じになるようにしています。
|
|
|
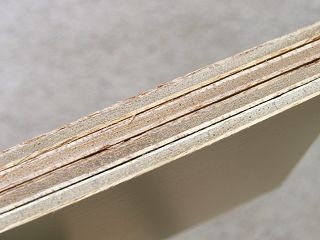 |
|
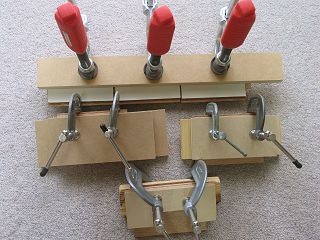 |
|
|
切断面中接着する部分だけはM-20GP(替刃式ヤスリ)でツルツルに研磨し直線性も確認しておきます。
|
|
最初に木工ボンドで2枚ずつを貼り合わせてクランプで3時間圧着保持しました。
|
|
|
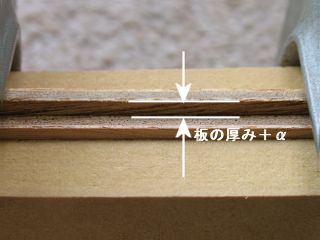 |
|
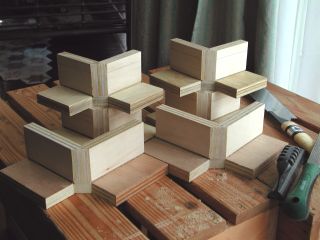 |
|
|
この時に2枚の最終接着面となる部分は予め研磨したものとし、段差が板厚+αとなるようにしておきます。
|
|
L字型に接着するには今年始めに製作した直角接合ジグを使います。 これは本番でも必要になるはずです。
|
|
|
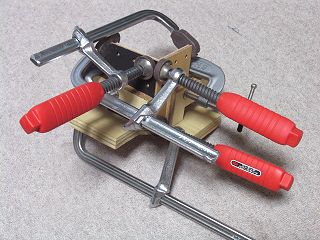 |
|
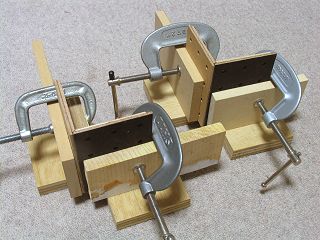 |
|
|
3時間後に接着面を突き合わせてM-20GPで僅かな段差(+α部分)を削って板厚と削り接着しました。 これは木工ボンドタイプですが、圧着保持にこんなに大袈裟なことになりました。
|
|
こちらはエポキシ接着の2組で接着面の隙間の発生が木工ボンドほどシビアではないため圧着保持も楽です。
|
|
|
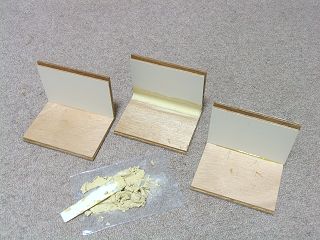 |
|
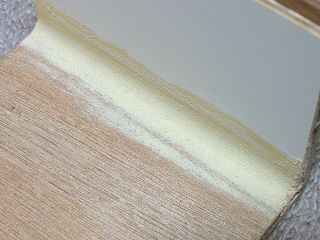 |
|
|
更に3時間後エポキシで接着した1組の隅にウッドエポキシを擦りこみました。(中央) 左は木工ボンド接着、右はもうひとつのエポキシ接着タイプです。
|
|
ウッドエポキシを隅に擦りこんだ試料のアップ。 指先で5-6回強く擦りこんだ後で水を付けて表面を馴らしています。
|
|
接着剤が実用強度にならないと次の作業に進めないため1日がかりの作業になりましたが、問題は完全硬化までに掛かる時間で、木工ボンドとここで使った5分硬化型エポキシは12時間おけば充分ですが、ウッドエポキシは1週間というのがメーカーの説明になっています。 そこまでは待てそうにないので、余ったウッドエポキシの硬化状態を確認しながら強度試験に入ることにします。
|
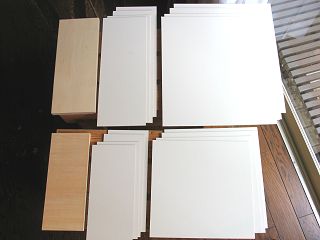 |
|
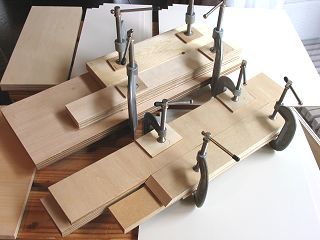 |
|
|
2.5mmカラー合板から切りだした16枚の側板と2枚の底板(左側)です。 切断は板が薄いだけに極めて簡単ですが切断精度は大変重要で、0.3mm以内の誤差に収めています。
|
|
側板外側の板と内側の板を木工ボンドで貼り合わせ圧着保持中、クランプとの間に端材を挟んで全体に圧着力が行き渡るよう配慮しています。
|
|
|
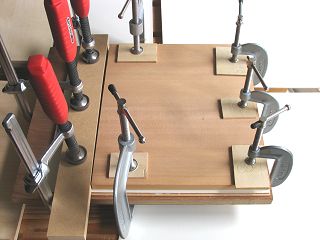 |
|
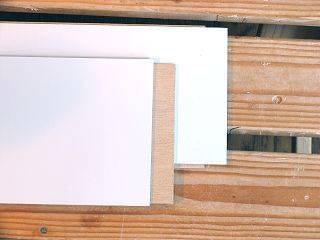 |
|
|
こちらは大きな側板の貼り合わせ中。 充分な圧着保持のためにクランプを多用しますので、手持ちクランプを全て使っても4回に分けないとならず、大変時間が掛かります。
|
|
貼り合わせた側板。 手前の板の白い部分はその下よりも2.5mmずつ上下にはみ出ており、これで段違いの接着を可能にします。
|
|
|
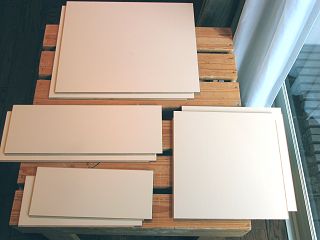 |
|
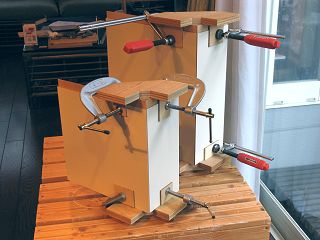 |
|
|
2枚貼り合わせが終わった側板8組。 ここまでで既に接着剤硬化時間だけで24時間を使いました。
|
|
大きな側板と小さな側板をL字型に接着。 ここでは60分後硬化開始のエポキシ接着剤を使い上下は90度接合ジグとクランプで保持しています。
|
|
|
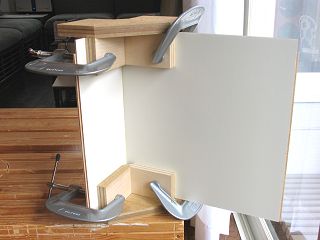 |
|
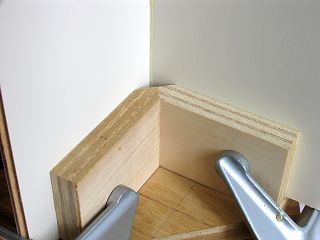 |
|
|
保持中に内側から見た所。 中間部分は全く保持していませんが、貼り合わせた板は反りがなく撓みも出にくくエポキシの充填効果があるため問題ありません。
|
|
ジグと側板との間に全く隙間がありませんから、正確な直角のL字型になります。 60分後硬化開始のエポキシを使ったので落ち着いて接着部分の調整が可能です。
|
|
|
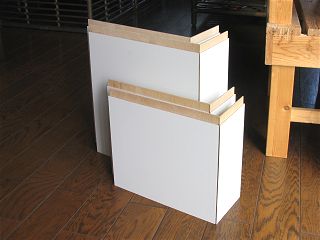 |
|
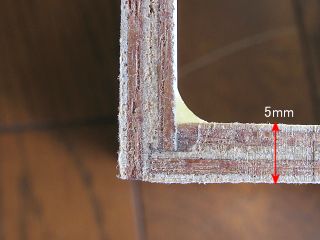 |
|
|
12時間経ってエポキシ接着剤が完全硬化したL字型ブロック4個です。 この状態でもかなりの曲げ強度がありますが箱型になれば更に頑丈になるはずです。
|
|
接着断面のアップでジグザグ接着面が判ります。 また3プライ 2.5mmのカラー合板裏面同士を貼った6プライ5mm厚になってますが、クランプで充分に圧着したため接着面は殆ど判らず、5プライの5mm合板のように見えます。 入り隅にはみ出たエポキシも強度アップに繋がるでしょう。
|
|
|
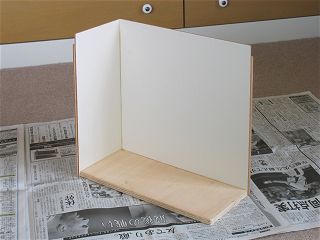 |
|
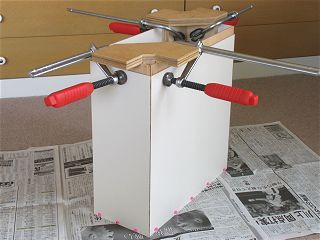 |
|
|
L字型側板ブロック1つを底板にエポキシ接着剤で固定しました。 この角度では見えませんが圧着保持には隠し釘(22mm)を使っています。
|
|
更にもう1つのL字型側板ブロックをエポキシ接着剤で貼り合わせ。 底板へは隠し釘で圧着保持、上部は90度接合ジグを使い保持しています。
|
|
|
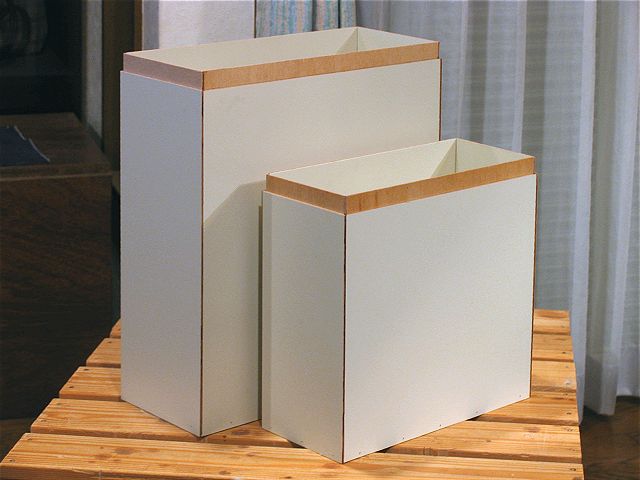 |
|
|
完成した2種類のごみ箱本体。 板の切断からここまで3日間という時間の掛かる(大半は接着剤の硬化時間。)作業でしたが狙いどおりの出来栄えです。 因みに仕上がり重量は大きな方が1.8kg、小さな方が1.2kgでした。 これを重いと考えるかそれとも軽いと考えるかは微妙な所ですが?
|
|
未経験の構造を採用し事前の実験を踏まえた上で肉厚5mmの箱を製作しましたが、最終的な強度は確認できないものの感触としては極めて強固な物になっており、今後薄く作る箱の標準構造・製作方法としたいと考えています。 特にピンホールカメラ作りではその真価を発揮しそうです。
|
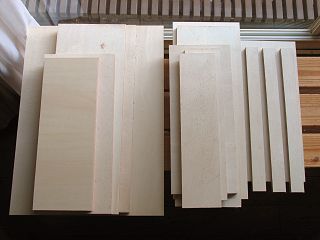 |
|
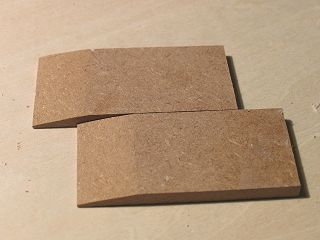 |
|
|
ごく僅かな端材しか出ず大変ハッピーになった12mmシナ合板の主要部材。 これらだけで\3,000で済んでいる計算で、塗装を含む全トータルで\6,000-\7,000の材料代で収まりそうです。
|
|
スチールピンを埋め込む部分に貼るスペーサー。 斜めに削った面が滑らかになることを考え5.5mm MDFを使いました。 木工粗目ヤスリでざっと削り替刃式ヤスリ(M-20GP)で仕上げてあります。
|
|
|
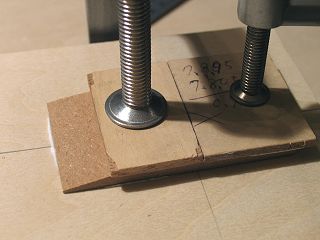 |
|
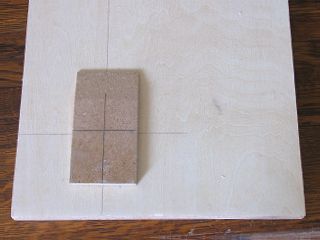 |
|
|
そのスペーサーを側板内側手前下に貼り付け圧着しています。 側板には正確な穴の位置を既に描いてあります。
|
|
貼り付けが終わったスペーサーに穴あけ位置の線を引きます。 位置誤差が極少になるよう慎重に。
|
|
|
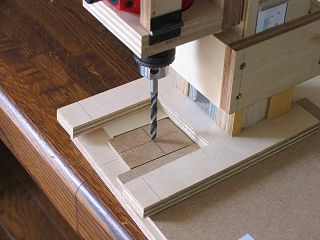 |
|
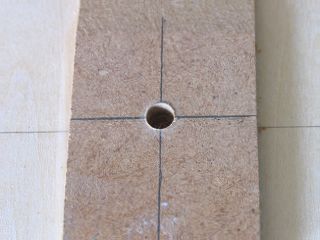 |
|
|
電動ドリルアタッチメントを使い直径6mm、深さ9mm強の穴を垂直に且つ位置を正確に保ってあけます。 このようなジグ無しでは精度を保つのは困難でしょう!
|
|
穴をあけ終わった状態です。 この程度ですと穴あけの位置誤差は0.3mm以下に入っていると思います。
|
|
|
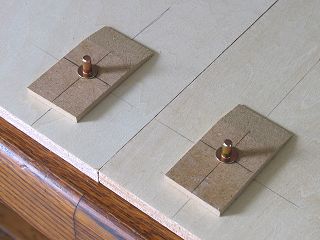 |
|
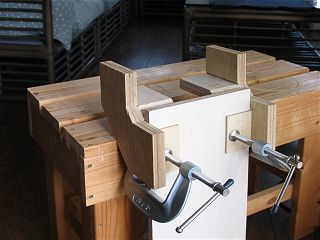 |
|
|
両側板に穴あけをしてスチールピンを挿しこんでみました。 後で最終的にはエポキシ接着剤で固定してしまいます。
|
|
側板の予備加工が終わったので天板を固定しますが、今回は直角接合ジグを使いアマチュア的な最上級の接合をします。 まず側板に直角接合ジグをこのように固定します。
|
|
|
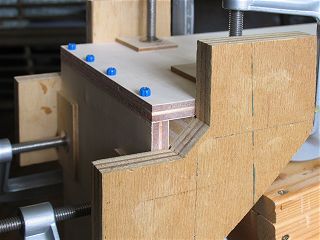 |
|
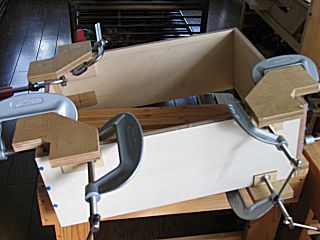 |
|
|
側板木口に木工ボンドを塗り天板を当ててクランプで固定後隠し釘36mmで4箇所固定します。 これで完璧な直角が約束されます。
|
|
3時間後に残る3ヶ所の接着を同様な方法で行いロに字型の枠にします。 底の板(左側)は奥行が130mmと幅狭なので、2箇所の角のみ直角接合ジグを使っています。
|
|
|
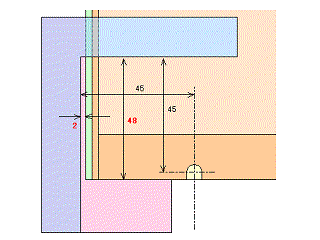 |
|
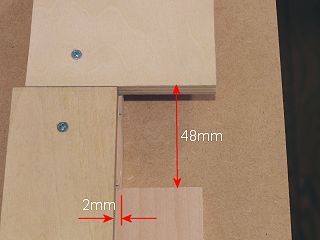 |
|
|
電動トリマーと6mmストレートビットで正確な位置に溝を彫るためのジグ。 これだけでは判らないと思いますので右と下の写真もご覧の上ご理解ください。
|
|
ジグは簡単な構造で、L型に切断した下の板にLを上下逆さにした形の上の板をネジ止めしたものです。 写真中の48mmと2mmの間隔が重要。
|
|
|
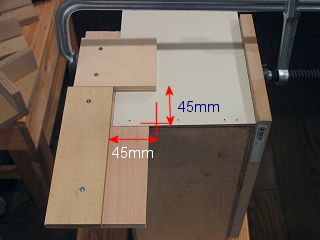 |
|
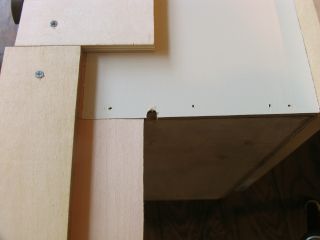 |
|
|
ごみ箱の右側下にジグをクランプで固定しました。 交差した赤線はジグの上板縁から45mmの位置にあります。 トリマーをジグに沿わせて切削するとごみ箱左端から43mmの距離で下から3mm、まで彫りこむことになります。
|
|
電動トリマーに6mmストレートビットを取り付けて深さ13mm彫りますが、一度に13mm彫るのはかなり負荷が掛かるので2回に分けています。
|
|
|
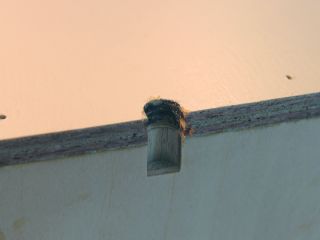 |
|
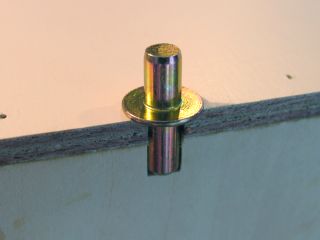 |
|
|
彫り込んだ部分のクローズアップです。
|
|
スチールピンはこのように嵌り込む予定です。
|
|
|
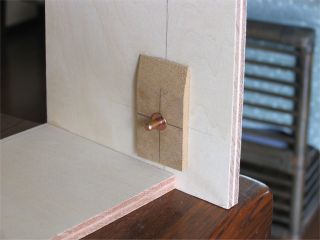 |
|
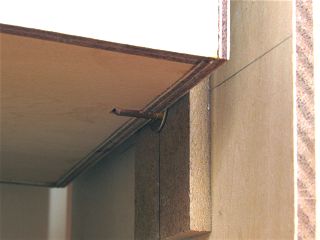 |
|
|
可動部分の確認をするため本体枠にスチールピンを挿しこみました。
|
|
スチールピンにごみ箱底にトリマーで彫った溝を上から落とし込みました。 これは右下の部分を下から見た所。
|
|
|
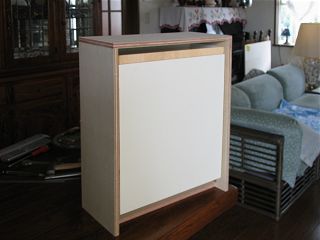 |
|
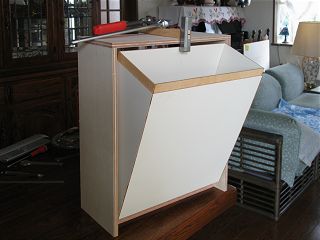 |
|
|
後へ倒れないよう底の後ろ側を支えていますが、これがごみ箱の通常の位置になります。 前板はまだ取り付けていません。
|
|
手前側に倒しごみ箱使用時の位置。 重心移動により手前に倒れるので玄翁などで支えています。 後ほどストッパーなど追加の加工をします。
|
|
まだ前板も取り付けておりませんが、ごみ箱本体を容易に取り外し且つ装填できる構造がお判りいただけると思います。 回転軸に対して重心が奥にあるのが普段の時、重心が手前に移動するのが使用時という目論見も上手くいってます。
|
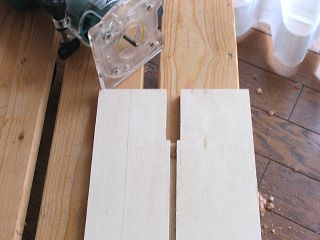 |
|
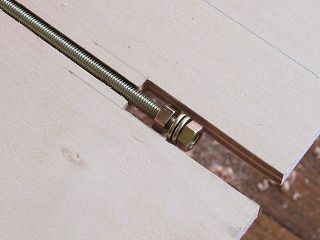 |
|
|
全ネジリンク棒を落とし込む溝をハイストリマービット1/4インチストレートで6.3mmの深さで彫りました。 1/4インチは6.35mmですので、直径6mmの棒に対し適切なゆとりの溝幅になります。
|
|
全ネジを落としこんでみた様子。 メートル規格のビットで削るとしたら作業の手間は倍以上。 インチ規格のハイストリマービットだからこそ可能な、安物だ!とバカに出来ない痛快テクニックと言えます。
|
|
|
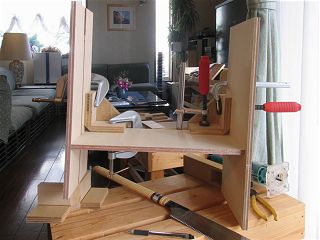 |
|
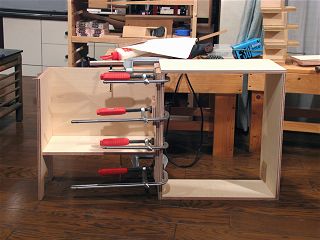 |
|
|
予備加工した板(左側)に底板と右端の側板を木工ボンドと隠し釘で固定。 直角接合ジグで保持しています。
|
|
この写真では前側が向こうを向いていますが、右側の前板を接着して更にプラスチックごみ箱部と連結しました。
|
|
|
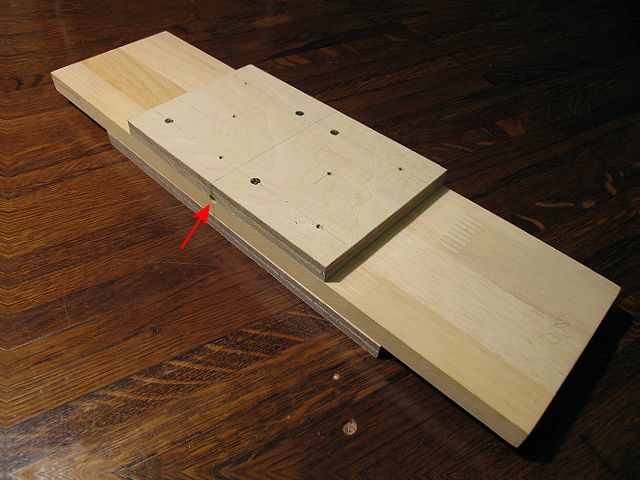 |
|
|
ペダルは2枚の12mmシナ合板で14mm集成材を挟む構造で作りましたが、接着剤は使わずネジのみで組立てた後に下の板と真中の板の合わせ目を中心にして直径6mm深さ13mmの穴(矢印の先)をあけました。(接着剤を使わない理由は後で判ります。)
|
|
|
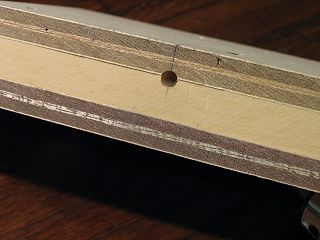 |
|
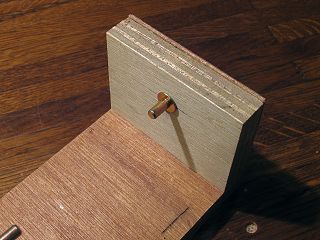 |
|
|
下の板(写真では上になっている。)と真中の板の合わせ目にあけた6φの穴ですが位置精度は誤差0.5mm以下が必要です。
|
|
こちらはペダルを受けるホルダーでスチールピンが埋め込まれています。(このスチールピンの位置精度も誤差0.5mm以下にします。)
|
|
|
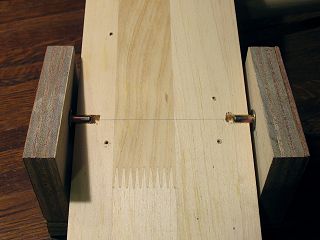 |
|
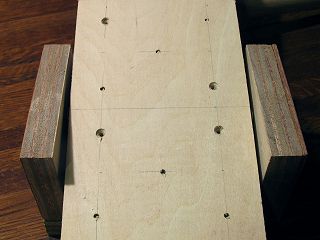 |
|
|
コの字のホルダーにペダルを装填する方法。 先ずペダルの下の板の固定ネジを緩めてペダルをこのように挿し込み溝にスチールピンを落とし込みます。
|
|
そうしたら底板を載せてやれば底板にもあいた6φの穴のかたわれにピンが嵌りますので、ネジ止めすればよいわけです。
|
|
|
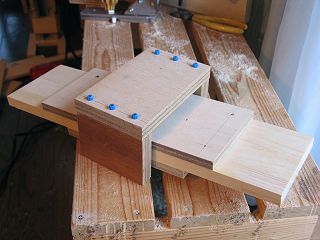 |
|
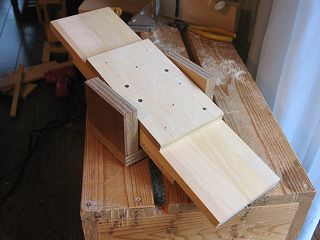 |
|
|
そしてひっくり返せばこんな風になります。 一見面倒な組み立て方をしているようですが、もし調整の必要性や分解しての作業が必要になれば再度ひっくり返して?
|
|
底板を止めているネジを緩めれば完全にばらすことが可能ですから、例えば完成後であろうと本体全体をひっくり返せば手入れ、調整が出来るという細かな配慮です。(やりすぎかな?!)
|
|
|
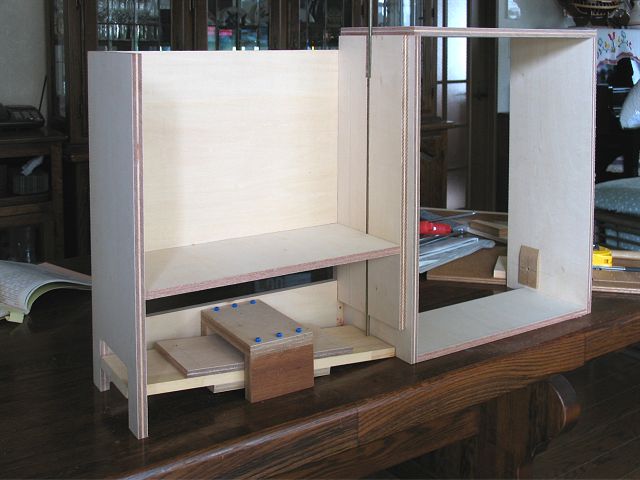 |
|
|
ペダルを所定の位置に置いてみました。 ペダルブロックの向こうに見えるのは前部の幕板でそこにペダルブロックを固定します。 手前側にも同様な板が入ります。 まだ切断していない全ネジも挿し込んでみました。
|
|
|
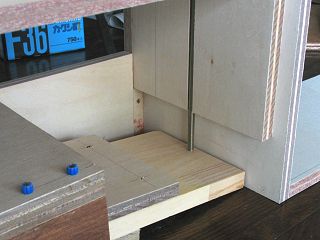 |
|
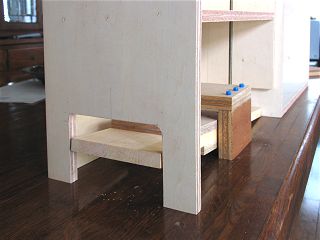 |
|
|
ペダルの奥の先端に全ネジが載っていますが、ペダルを踏めばネジは上に押しあがります。 このネジが触れる面は摩擦で板が削れますから何か対策をしないとなりません。
|
|
ペダルの前面側。 後で化粧加工してもうちょっと恰好よくしますが、この部分をつま先で踏みます。 現在ペダルの上下ストロークは設計値の40-45mmより10mm程大きいので最終的なペダルの定常位置は下がってつま先が入りやすくなるはずです。
|
|
|
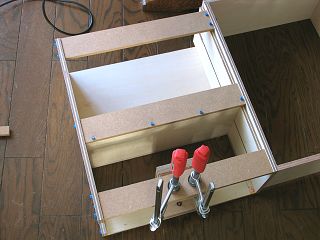 |
|
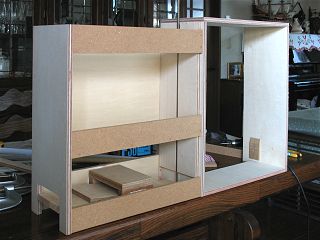 |
|
|
裏側には3mm厚のカバーを落とし込む予定ですがそれを固定する厚さ9mmMDFの桟を3本固定し、一番下はペダルブロックに接着しました。
|
|
これでペダルブロックは完全に所定の位置に納まりました。
|
|
|
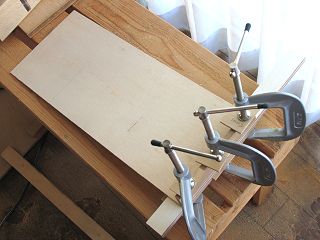 |
|
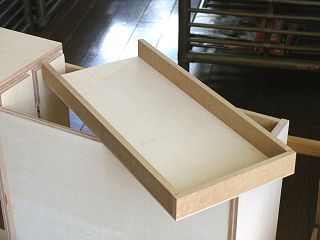 |
|
|
次に蓋の組立て。 3mm厚カラー合板に9mm厚MDFから切り出した枠を接着剤だけで貼り付けましたが、ご覧のように大袈裟にも思える圧着力の確保をクランプでしています。
|
|
MDFはひびが入りやすく隠し釘を使えないので、1箇所毎に接着硬化時間3時間を掛け1日がかりで組み上げました。
|
|
|
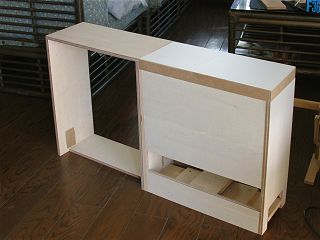 |
|
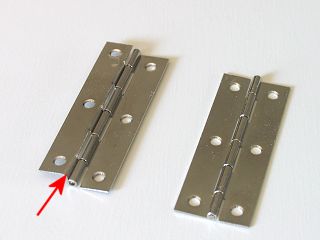 |
|
|
蓋を所定の位置に載せました。 本体との寸法誤差が最大で0.5mm弱ありましたので、替刃式ヤスリで蓋の周囲を削って修正しています。
|
|
蝶番の蓋に固定する側は左のように羽を曲げました。 このテクニックはトイレットペーパーホルダーの製作でやった方法と同じです。
|
|
|
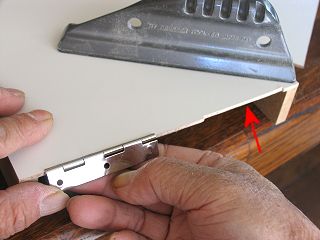 |
|
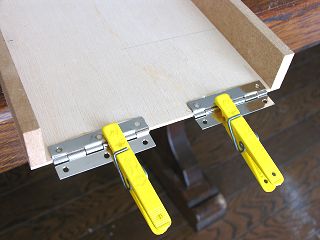 |
|
|
蓋の蝶番取り付け位置を1.5mm削りこみました。(矢印の先) この結果削り込まない蓋の端は蝶番回転軸の中心に一致します。
|
|
そして板が薄すぎてネジ止めできないので、蝶番をエポキシ接着剤で蓋に固定しました。
|
|
|
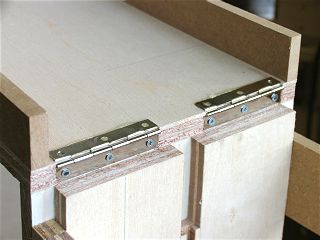 |
|
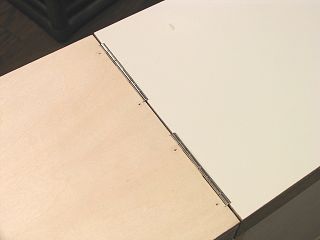 |
|
|
同様に本体側も蝶番取り付け位置を1.5mmノミで削り落とし、蓋を反対側に完全に倒した上体で蝶番を本体にネジ止めしました。
|
|
これらの削りこみで蝶番以外の部分の本体と蓋の隙間は蝶番自身の厚み(約3.5mm)よりぐっと小さくなります。
|
|
|
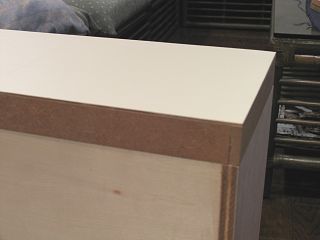 |
|
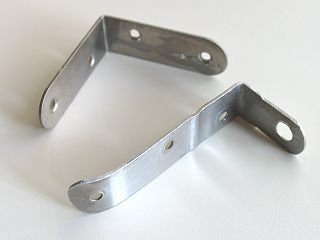 |
|
|
蓋の前側(蝶番を取り付けた反対側)です。 スライド蝶番のように取り付け後に位置調整が出来ないので不安だったのですが、ご覧のようにまずまず合格といってよいと思われます。
|
|
蓋を押し上げるL金具は手元にあったステンレス製のL金具(左上)を一旦伸ばしてから6φの穴を端にあけた後その中心から18mmの位置で再度曲げました。 また長い先端部分は取り敢えずですが、蓋の裏側と擦れるため適当に曲げて摩擦を減らしてあります。
|
|
|
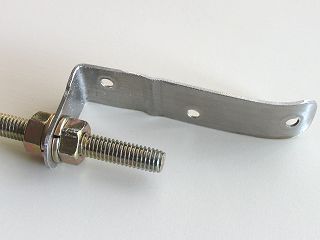 |
|
 |
|
|
それを所定の長さに切断した全ネジにナット2個にスプリングワッシャー2個で挟んで固定します。(スプリングワッシャーの使用はナットの緩み防止です。)
|
|
組み上がった禅ネジを蓋を開けて上から挿し込みました。 これでカラクリ機構は一応完成です。
|
|
|
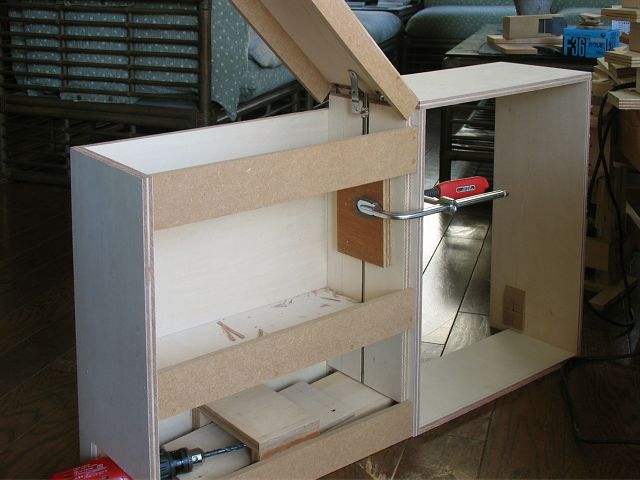 |
|
|
ペダルを踏んだ状態。(ペダルの上に電動ドリルを載せて抑えています。) 開き角度は期待していた角度にほぼなっていますが、この写真を見た限りでは判らないものの蓋の上下の動きはあまりスムーズではありません。 L金具が蓋の裏側の面を押し上げながらスムーズに滑らないためのようです。
|
|
|
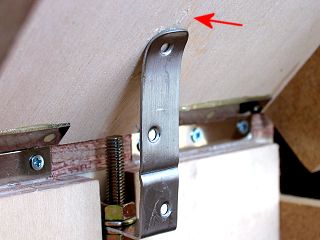 |
|
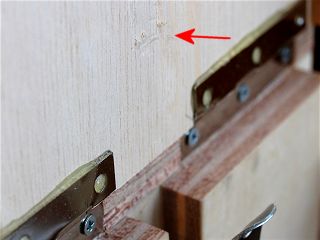 |
|
|
L金具が蓋に擦れる部分のクローズアップ。 5-6回上下させただけで矢印の先に傷が付いています。
|
|
全ネジを引き抜いてその部分を見るとご覧のとおり。 想像以上に大きな力で付いた擦り傷です。 滑りを良くするだけでは根本的な改善は期待できそうにありません。
|
|
|
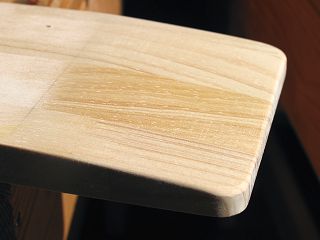 |
|
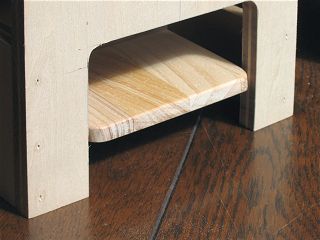 |
|
|
ペダルの前側上面を長さ75mmにわたりカンナで斜めに削ったのち木工ヤスリで仕上げ、前面の厚みを半分の7mmまで薄くし、角も丸く削りました。
|
|
ペダルのストロークの減少とペダル前側の厚みの減少でつま先を入れる上下のスペースは当初35mmしかなかったのが50mm強と改善されました。
|
|
|
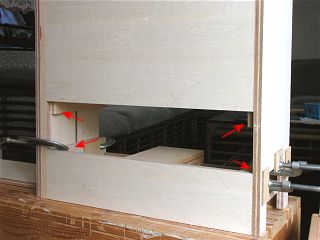 |
|
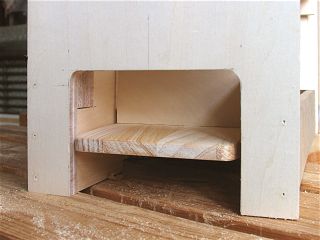 |
|
|
引出し左右を上下で支えるレールを接着しています。 木製レール仕様の最も簡単なやり方です。
|
|
ペダル前面周りの奥がごちゃごちゃ見える部分を隠す覆い加工をしました。
|
|
|
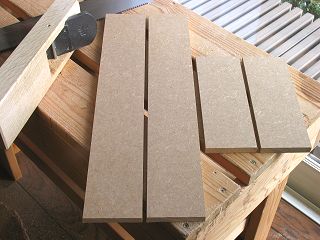 |
|
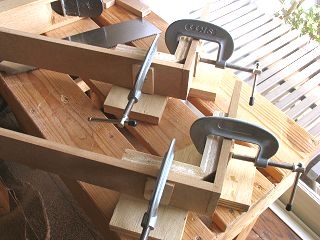 |
|
|
引出しの枠はその後発見した手持ち端材の9mm厚MDFを使いました。(設計時は12mm厚。)
|
|
MDFは隠し釘のように細い釘でも割れやすいので木工ボンドだけで組み立てましたが、直角接合ジグは直角度確保と圧着保持の点で必需品の道具です。
|
|
|
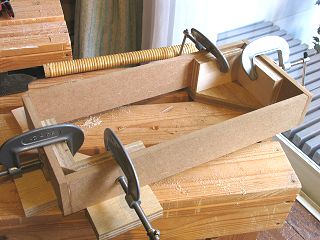 |
|
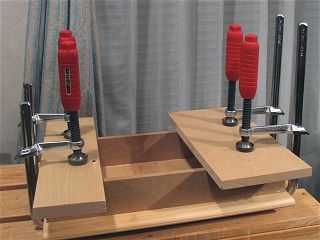 |
|
|
L字型に組み上がった枠同士をもう一度直角接合ジグを使ってロの字型に接着します。 小型の直角接合ジグでも大き過ぎて一度に4箇所を接着できないためです。
|
|
出来上がった引出しの枠に底板をこれまた木工ボンドで貼り付けですが、ご覧のようにバクマクランプでやりすぎ?とも思える圧着保持をしていますが、木工ボンドだけで組み立てる場合には絶対的な圧着保持は不可欠です。
|
|
|
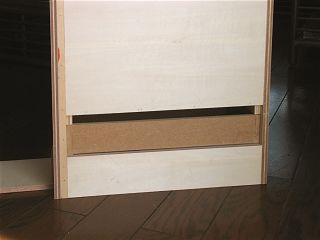 |
|
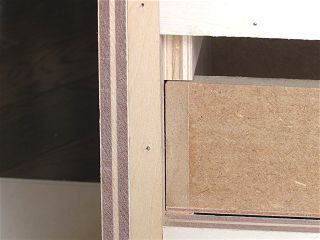 |
|
|
組み上がった引出しの箱の接合部分の僅かな段差をカンナで削り替刃式ヤスリで研磨した後に挿入しました。
|
|
本体の内寸に対し引き出しの外寸幅は1mm小さいので左右に0.5mmずつの隙間が出来ますが、見た感じはこんなものです。
|
|
|
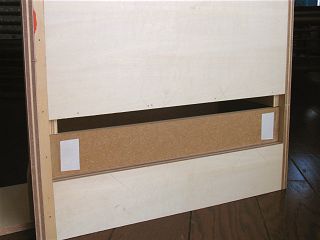 |
|
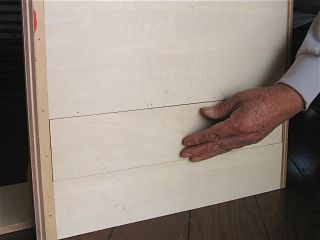 |
|
|
引き出し前板貼り作業。 まず箱の前面両端に両面接着テープを貼り付けてやります。 両面テープはこんな程度の大きさで充分です。
|
|
そうしたら予めサイズ調整をしておいた前板をそっと嵌め込み隙間の出具合を調整した後に引き出し箱に押し付けます。 写真では見えませんが右手は引き出し背面を押しています。
|
|
|
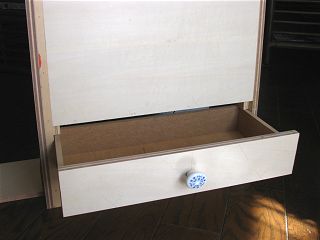 |
|
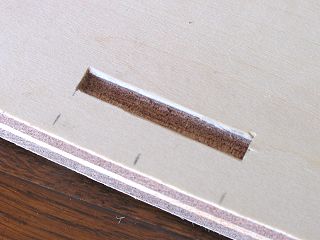 |
|
|
そして引出しを抜き前板と箱をクランプで挟み両面接着テープが充分貼り付くようにしてツマミ取り付けの穴をあけてツマミを固定して終了。 これだけで前板はずれたり剥がれたりしなくなります。
|
|
小さなカラクリの製作! プラスチックごみ箱が入る本体上板の中央裏側にこんな溝をノミで彫りこみます。
|
|
|
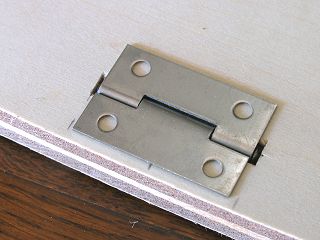 |
|
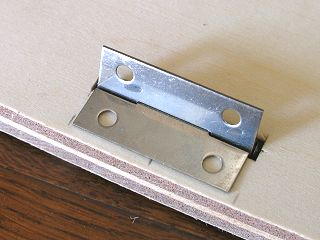 |
|
|
その溝には蝶番の回転軸の飛び出ている部分をこのように落とし込みます。
|
|
彫り込んだ理由はこのように何にも触れることなく片方の羽が動くようにするためです。 このあと手前のネジ穴2箇所にネジを締め込み片方の羽のみ固定します。
|
|
|
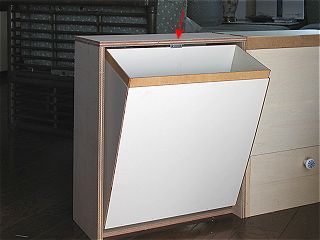 |
|
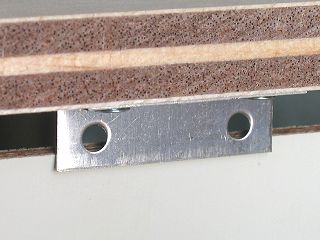 |
|
|
その結果プラスチックごみ箱は手前に倒れることなく蝶番がストッパーになってくれます。 判りにくいでしょうか??
|
|
矢印の先を拡大するとこのとおり。 自重で垂れ下がった蝶番の羽にごみ箱の側壁が引っ掛かっています。
|
|
|
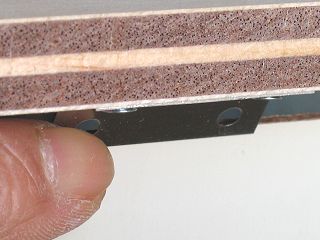 |
|
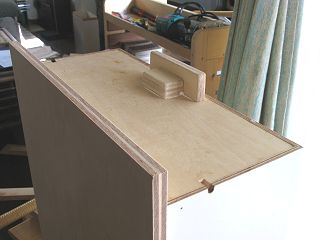 |
|
|
解除するには羽を指で奥のほうに押してやればよいだけ。 普通の蝶番は270度以上開かない性質を使ったアイデアの 超簡単カラクリです。
|
|
その後プラスチックごみ箱の前板を仮固定して前板の下への出っ張りと同じ高さの脚を貼り付けました。
|
|
|
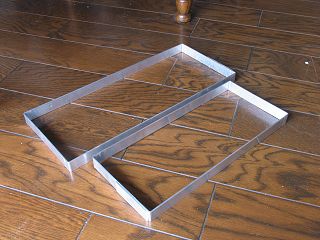 |
|
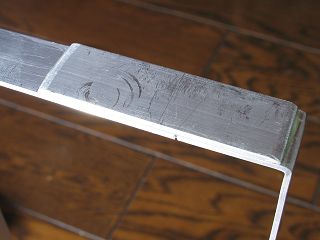 |
|
|
厚さ2mm、幅20mmのアルミ押し出し材を曲げて作ったごみ袋押さえ枠。 残念ながらあまり綺麗に加工できておりません。
|
|
繋ぐのには短く切断した同じアルミ板を繋ぎ目の外側に貼り付けました。 理想は溶接でしょうがそんな加工をするのはちと敷居が高すぎます。
|
|
|
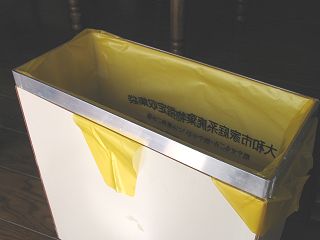 |
|
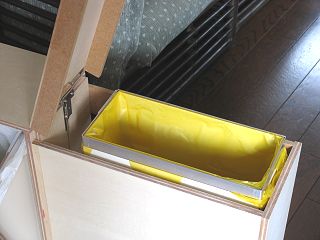 |
|
|
とはいえ折り曲げの位置精度はかなり高く出来たので、きつからず緩からずに出来上がり、ご覧のようにごみ袋を固定できています。
|
|
そして燃えるごみ用ごみ箱を所定の位置に収めました。 アルミ枠は箱上端の強度不足(3mm厚合板は割れ易い!)を補う役目を果たしてもくれます。
|
|
|
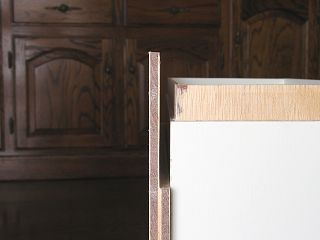 |
|
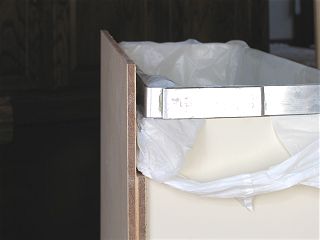 |
|
|
こちらはプラスチックごみ箱部の前板上部を横から見たところですが、板厚が半分の6mmになるよう裏をトリマーで削りサンドペーパーで仕上げました。
|
|
この欠き込み部分にごみ袋を外側に折った部分を収められごみを入れやすくなります。 そうしてアルミ枠で押さえます。
|
|
|
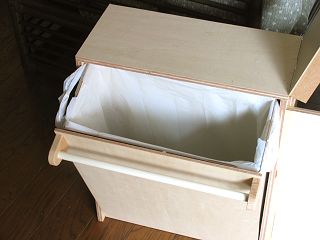 |
|
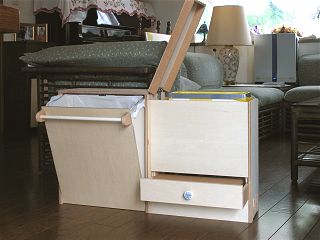 |
|
|
前面上部にはこれまで使ってきた直径13.5mm、長さ900mmのタオルハンガーを切断し布巾ハンガーとしましたが、これはごみ箱を引く取っ手にもなります。
|
|
以上で全加工作業がやっと終了し残るは塗装のみとなりました。 完成度はかなり高いと自認しています。
|
|
|
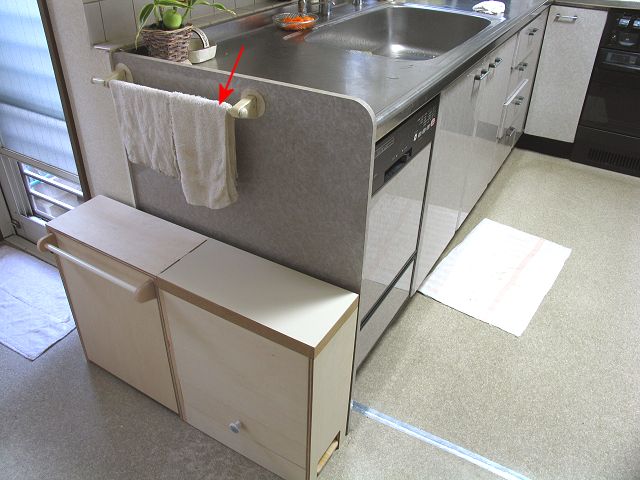 |
|
|
早速実際の設置場所に運び込み使用方法などを家内に説明しました。 矢印の先が切断した残りを再び元の位置に取り付けたタオルハンガーで、これが布巾掛けのみならず次にお見せする重要な役目を果たします。
|
|
|
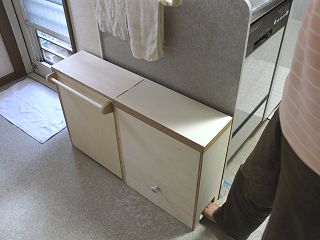 |
|
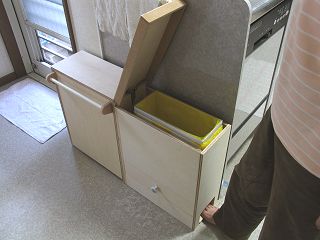 |
|
|
ペダルを踏み込もうとしているところ。 これをいきおいよく踏み込むと蓋が90度以上開いて付け根の蝶番固定部分が壊れやすいのですが?
|
|
ご覧のとおりあいた蓋の手前側はタオルハンガーに当って約80度以上は開きません。 しかも吸盤で固定されたタオルハンガーは衝撃吸収効果があり、実用性高いストッパーとしての役目を果たします。
|
|
Copyright (C) 2001-2019, Vic Ohashi All rights reserved.