|
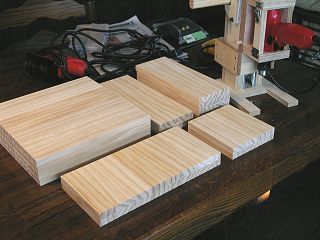 |
|
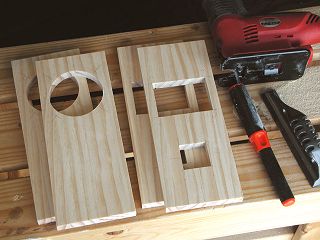 |
|
|
ホームセンターで切断してもらったラジアタパイン集成材。 手抜きではなく時間と費用を考えた合理的な方法だと思います。
|
|
前板と裏板の2次加工。 電動ジグソー(CJ-250)で切り抜き、替刃式ヤスリ2種類(平のM-20GPと丸DP-1000)で仕上げました。
|
|
|
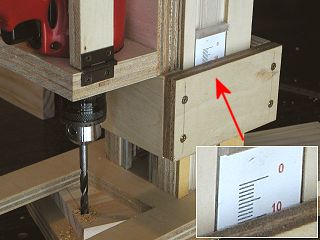 |
|
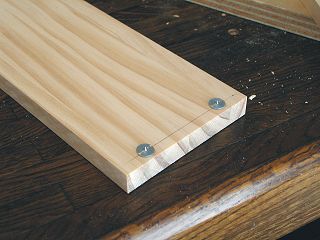 |
|
|
電動ドリルアタッチメントを使って底板と前板/背板接合部分に、深さ10mmの6φ木ダボ穴あけ。 穴の深さをプリセットできるので便利です。
|
|
その穴にマーキングポンチを嵌め込みます。
|
|
|
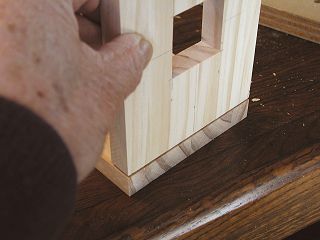 |
|
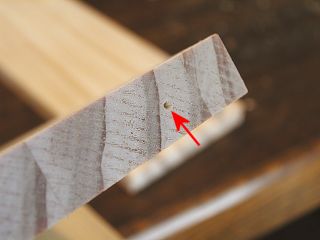 |
|
|
接合する相方(これは背板の下部)を上に軽く当てて位置をよく確認したらぐっと押し込みます。
|
|
木口面にマーキングポンチによる円錐状の凹みがつきました。
|
|
|
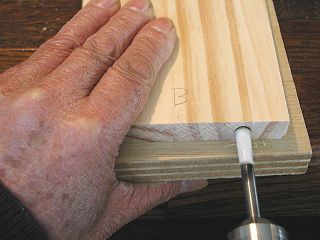 |
|
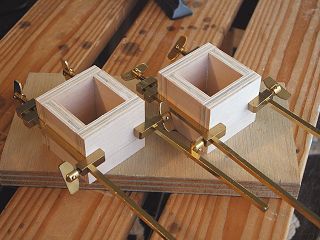 |
|
|
そこに深さ22mmの穴をあけます。 このスタイルで穴あけをすると実用上問題の少ない垂直出しがしやすいです。 こうして背板と前板の下部に同じ方法で穴をあけておきます。
|
|
次にバスレフポートの部分を9mm合板から作り木工ボンドで接着しますが、180mmハタ金を使って圧着保持しています。
|
|
|
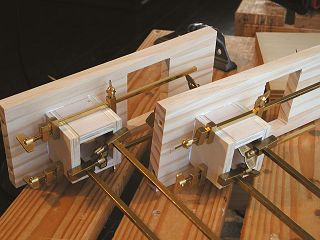 |
|
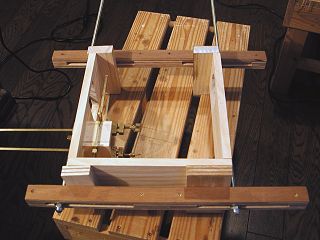 |
|
|
それを背板内側に貼り付けました。 こちらもハタ金を使って圧着保持しています。
|
|
ハタ金の圧着保持をしたまま底板と前板/背板を木ダボで接合。 自作中型クランプで強く締め上げ、接合部分を完全に密着させています。 接合分の直角度出しと捩れが発生しないよう注意。 (このまま5時間放置)
|
|
|
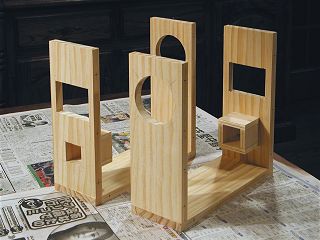 |
|
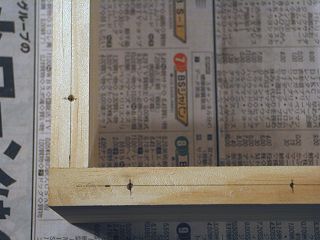 |
|
|
前板、背板と底板が接合されました。 側板が接合される部分の角に万が一段差がある場合には、完全に削り落として修正しないと先には進めません。 (その修正の為に寸法が若干変わるよりも重要です。)
|
|
側板を貼り付ける木口に木ダボ位置を印して深さ22mmの穴をあけます。 私は11本の木ダボを使いました。
|
|
|
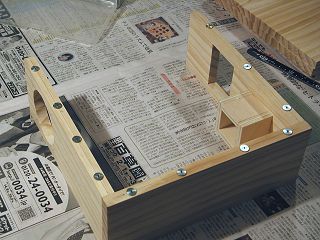 |
|
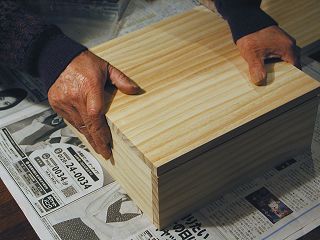 |
|
|
穴をあけ終わったらマーキングポンチをその穴に挿入します。
|
|
そしてそっと側板を載せて位置の調整をしてOKとなったら上から押さえ付けてマーキングポンチによる印しを付けます。
|
|
|
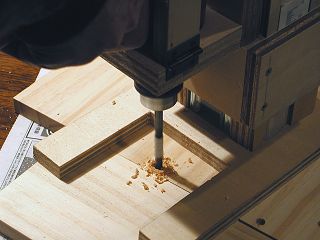 |
|
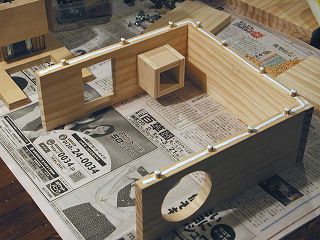 |
|
|
深さ10mm、6φの穴あけで、再び電動ドリルアタッチメントの活躍です。
|
|
木ダボを叩き込んで接着剤を塗りつけて接合の準備がOK。
|
|
|
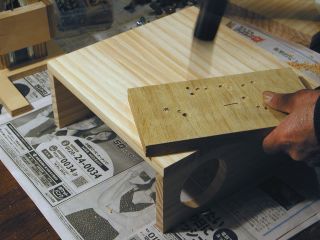 |
|
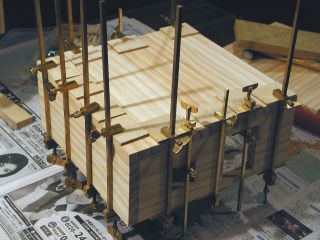 |
|
|
板を当ててその上から玄翁で叩きこんでやりますが、これだけでは密着させるのは不可能です。
|
|
ちょっとやりすぎとお思いかもしれませんが、11本のハタ金で圧着保持しました。 無論隙間の発生は全くありません。
|
|
|
ちょっぴり補足 スピーカーボックスの組み立てで最重要項目は十分な強度を保ちながら全く隙間無く接合することです。
その理由は音質に影響するからでこれを決して甘く見てはなりません。 この辺りはトリマー収納ボックスやA4サイズの
箱を作ったときの組み立て方と全く異なります。 正確に接合するのであれば木工ボンドに隠し釘併用による接合の方が
遥かに優れていますが、完全密着接合を求めるためここでやっているように木ダボ併用の木工ボンド接着で、クランプ・ハ
タ金などによる十分な圧着保持をするかネジによる締め付けの必要が出てきます。
外観に拘らない! 或いは作業に自信が無いのであれば、隠し釘を使って正確な接合をした上でネジで締め付ける方法
を取れば、木ダボ接合よりも簡単に作業できますし、音質的に好結果を得られます。
|
|
|
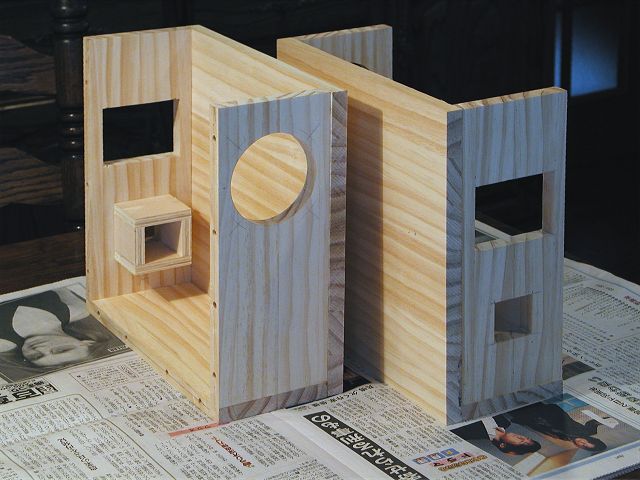 |
|
|
5時間以上放置して片側の側板貼り付けが終了です。
|
|
|
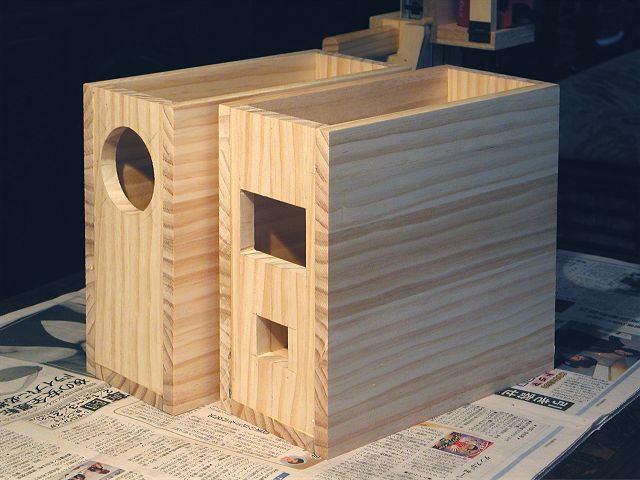 |
|
|
反対側の側板も貼り付けが終わりました。 実は設計時点では側板の木目方向は縦で考えていました。 しかし何となく横の方が収まりがよさそうで側板は正方形でしたので最終的に木目を横方向に貼り付けました。 こんな距離からでは一見完璧な精度の高い接合がされているように見えるのですが?
|
|
|
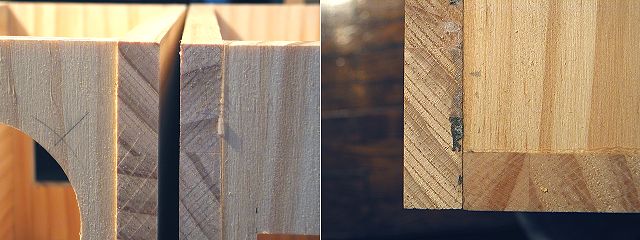 |
|
|
接合部分の僅かな段差、はみ出たまま固まってしまった木工ボンド、接着時の汚れなどこのままではまずい部分が結構あります。
|
|
|
完全にぴったりと隙間無く接着することを優先し位置精度は若干目をつぶっているため、接合部分の段差が若干発生して
いますし、木工ボンドの拭き取りも完全ではありません。(どだいハタ金の裏などは拭き取りようがありません。)
また接着時の汚れ(上の写真は新聞紙がくっついてしまったもの。)もあり、このままでは完成度が大変低いです。
そこでサンドペーパーで研磨してこれらの問題を取り去るのですが屋外での作業になり、今日は雨模様なので今週はこ
こで作業を止めます。 しかしサンドペーパーによる研磨は0.5-1.0mmも削り取ってしまうかなりの荒療治であり、
合板やランバーコアの場合には使えないテクニックです。(コンマ数ミリの表面材は無くなってしまう!)
|
|
|
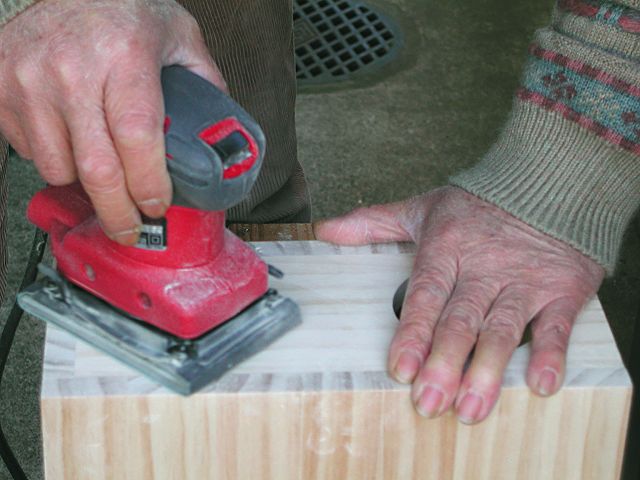 |
|
|
接合部の木口突出はコロ付かさ付目地払いビットを使えば簡単に落とせますが、修正研磨の主役はなんと言ってもこれ(S-5000 ミニサンダー)です。 片手操作が通常のサンダーより遥かに楽に出来るのでもう一方の手は作品を押さえることに専念します。
|
|
|
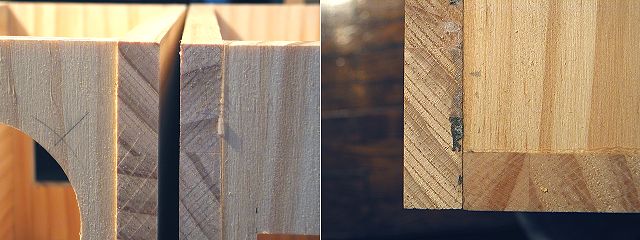 |
|
|
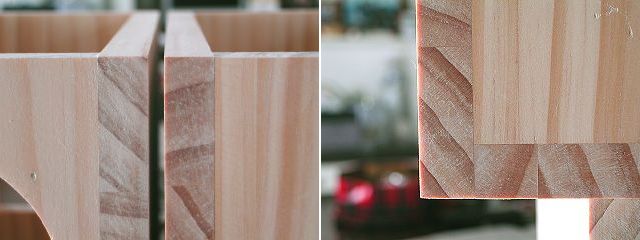 |
|
|
上は先週お見せした研磨前で、下が研磨後に同じ部分を撮影したものです。 電灯光下と自然光によるカラーバランスの 違いがありますが、綺麗に段差が無くなっている事がわかると思いますし、右の写真では接着時にくっついてしまった新聞 紙も削り取られています。
|
|
|
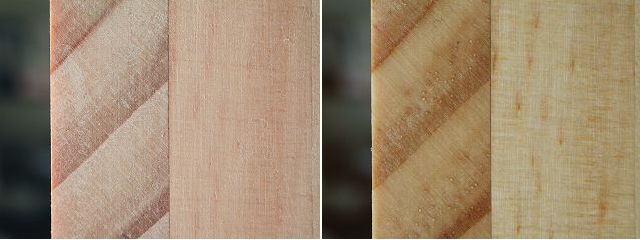 |
|
|
はみ出たり表面にくっついてしまった木工ボンドが完全に削り取られたかどうかのテストです。 左の写真はそのままです が、右は表面を水で濡らしたものです。 この例では木工ボンドは全く残っていません。
|
|
|
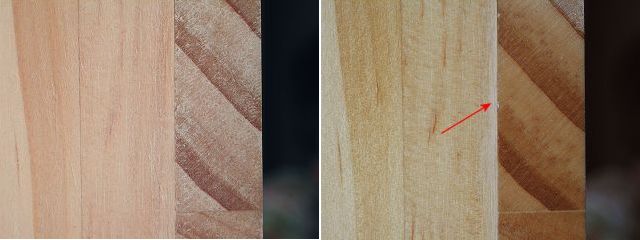 |
|
|
水で濡らしていない左の写真では一見全く問題ないように思えますが、水を濡らした右では矢印の先に縦にうっすらと白っ ぽいものが見えます。 この白っぽいものは木工ボンドの皮膜で、更に削りこむ必要があります。
|
|
|
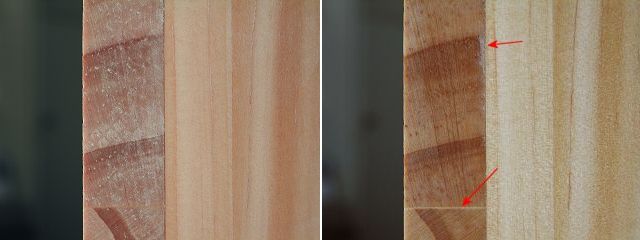 |
|
|
この木工ボンドの検出方法は大変簡単ですが大変鋭敏です。 左の写真はやはりなんともないように見えるのですが、 水で濡らした右では2箇所白っぽく浮き上がりました。 上の矢印は付着した木工ボンドの塊が取りきれなかったもので、 下の矢印は集成材を製造時の貼り合わせ部分の隙間にある接着剤です。 後者は落とす手立てがありませんが、前者 は更に削り込んで落とせます。
|
|
|
 |
|
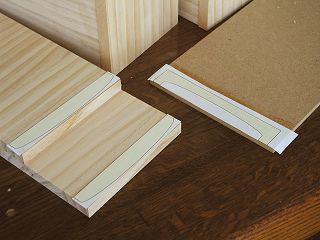 |
|
|
飾り前板を貼り付けましたが、この前に飾り前板の上の木口だけは替刃式ヤスリで磨き上げておきます。左右は1mmずつほど出っ張るようになっていますので、その出っ張りは完全接着後にコロ付目地払いビットで落とします。
|
|
曲面をできるだけ正確に切削・研磨するための2種類のテンプレートを印刷し、天板の前縁と端材の5mm厚MDFに貼り付けました。 テンプレートの実物大図面はこちらです。
|
|
|
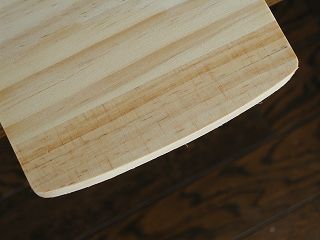 |
|
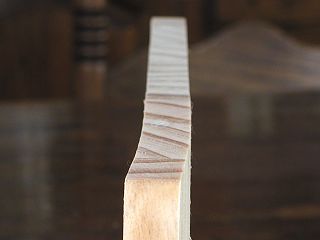 |
|
|
天板前縁はジグソーでテンプレートの線の少し外側をジグソー(CJ-250)で切断し、替刃式ヤスリ(M-20GP)で仕上げました。
|
|
余談ですが型紙を剥がすために水で濡らした天板前縁(右側手前)は水を吸って膨張しこんなに反ってしまいました。 完全乾燥すれば元に戻るもののこの性質は要注意です!
|
|
|
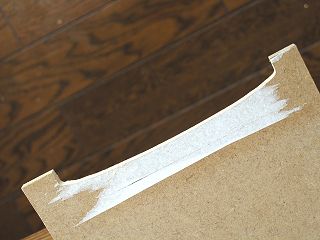 |
|
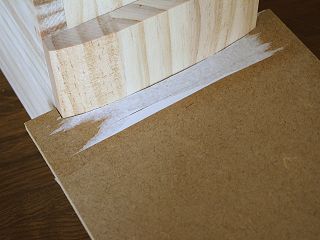 |
|
|
端材のMDFで作ったテンプレートはジグソーで切り抜き替刃式ヤスリ(DP-1000、RS-310P)で成形しました。
|
|
飾り前板はカンナで角を落としますが、テンプレートを当てて形状が近しくなるよう確認しながら進めます。
|
|
|
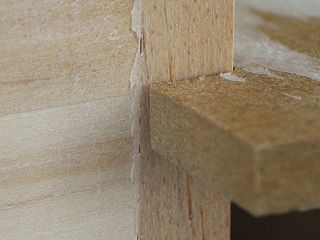 |
|
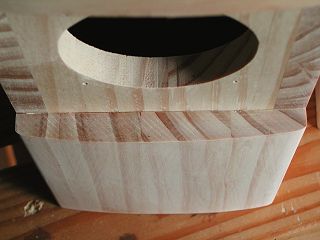 |
|
|
削りすぎは禁物。 このようにテンプレートを当ててあと0.5mm位かなー? のところで止めます。
|
|
その後で電動サンダー(S-5000)に#60のペーパーを付けてテンプレートの曲線どおりになるよう研磨してペーパーを#240に替えて仕上げます。 尚角はサンダーでは削り過ぎ易いので、替刃式ヤスリで成形します。
|
|
|
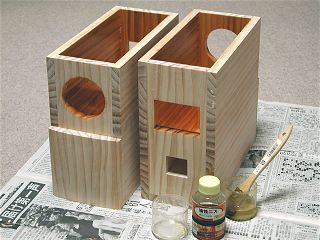 |
|
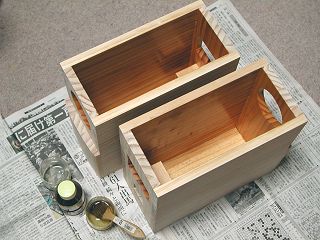 |
|
|
夕食後に15%の薄め液を加えた油性ウレタン透明ニスを箱の内部だけ2回塗りしました。 刷毛斑塗り斑等は一切気にする必要無しです。
|
|
スピーカーや端子盤取り付けの木口も忘れずに。 1回目は特にたっぷり沁みこませてやり、寝る前にもう一度塗っておけば翌朝には次の作業に入れます。
|
|
|
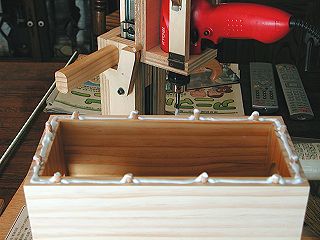 |
|
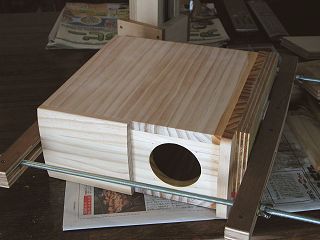 |
|
|
箱本体組立作業の最後の工程、天板貼り付けです。 ご覧のように6φ木ダボ12本を併用した木工ボンド接着です。
|
|
圧着保持には手持ちのハタ金やクランプは短くて使えませんので、自作中型クランプを使用。 これでもかというくらいネジを締め上げて密着度を確保しています。
|
|
|
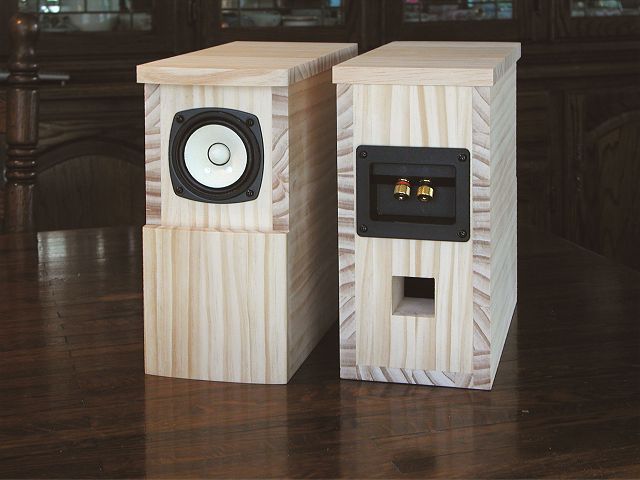 |
|
|
5時間後にスピーカーユニットと端子盤を固定し、取り敢えず試聴できる状態になりました。 とは言っても暫くはエージングをしないと本当の音にはなりませんので、比較試聴はまだ先です。
|
|
|
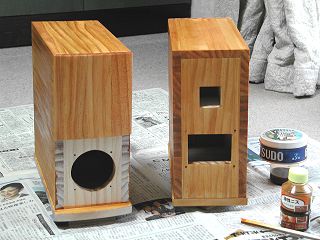 |
|
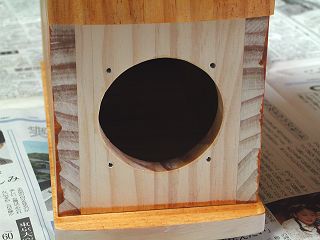 |
|
|
お昼時に塗装のスタート。 チーク色油性ウレタンニスに薄め液を20%加えかなり薄くしたものを塗りました。 これは薄い色を求められていることと着色斑の防止に大変効果があります。
|
|
スピーカー周りはこのように塗料が周りこんでしまいこのままでは着色斑になりますが、最後につや消し黒で塗りつぶすので問題ありません。
|
|
|
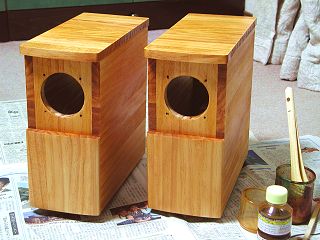 |
|
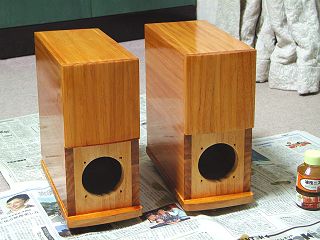 |
|
|
6時間後(日の沈む少し前)にひっくり返して天板とその縁、そしてスピーカー周りを塗装して1回目が終了です。
|
|
更に6時間後(寝る直前!)に2回目の塗装をしました。 塗膜が薄いのでこの間研磨はしていません。 色味が1回目よりほんの少し濃くなりました。 これで一晩寝かします。
|
|
|
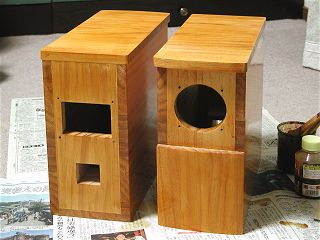 |
|
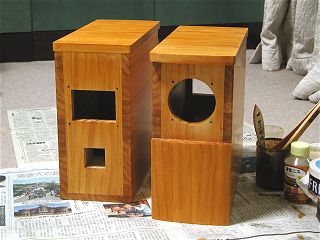 |
|
|
翌朝天板とその縁、そしてスピーカー周りの2回目の塗装をしています。 天板や前板などで1回目では白っぽさが残っていた部分も色載りしています。
|
|
昼食後、スポンジ研磨剤(極細目 #320-#600)で軽く研磨し、透明油性ウレタン艶ありニス(+10%の薄め液)で塗装、更に感想後つや消しニス(+10%の薄め液)と続け合計約50時間でニス塗りは完了しました。
|
|
|
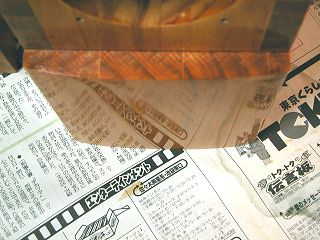 |
|
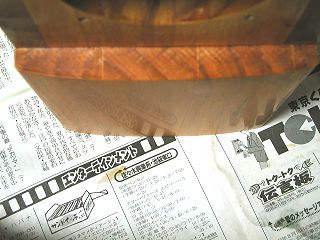 |
|
|
これはチーク色ニス2回そして透明ニスを1回塗った状態で、ご覧のように表面はぴかぴかで良く反射します。
|
|
同じ部分につや消しニスを更に塗ったあとで、にぶーい艶のため反射はかなり抑えこまれています。
|
|
|
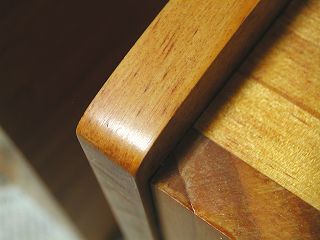 |
|
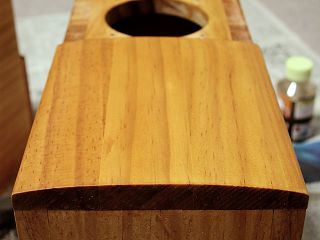 |
|
|
天板角部分のアップ。 つや消しニスによるこのなんとも言えないシックで格調高い質感が私は大変好ましく思っています。
|
|
殆ど艶がないということは実は塗装斑も目立ちません。 塗装技術が2段階特進したのでは?と良い意味の勘違いをするかもしれません。
|
|
|
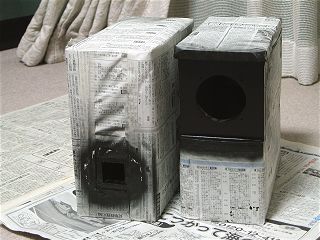 |
|
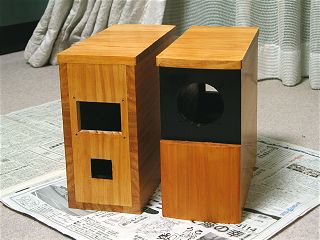 |
|
|
塗装作業最後はスピーカー周りとポート内部をつや消しの黒で塗ります。 このように塗装しない部分をマスキングテープと新聞紙で覆いスプレー塗料で2回塗りしました。
|
|
乾燥後新聞紙とマスキングテープを剥がしました。 これで塗装作業は無事終了です。
|
|
|
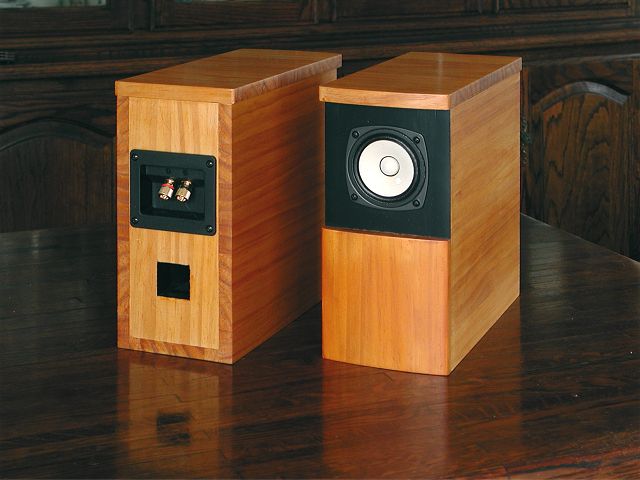 |
|
|
スピーカーユニットを取り付け吸音材を貼り、端子盤への接続も完了しました。 後は比較試聴とフロントグリル製作を待つのみです。
|
|
|
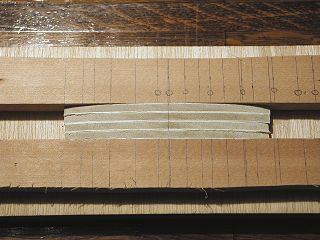 |
|
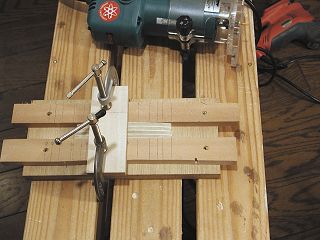 |
|
|
カマボコ状に少し大きめに切断した4枚の上下の側板を挟みトリマーで溝堀の準備をしました。 沢山見える線は切断位置やガイドの位置を表す線です。 両側に挟んだ板は厚みが14mmあります。
|
|
一番右端の溝を彫る為にガイドをセットしたところです。 後は3mmのストレートビットで10mm掘り込めば側板には4mm掘り込まない部分が残ります。
|
|
|
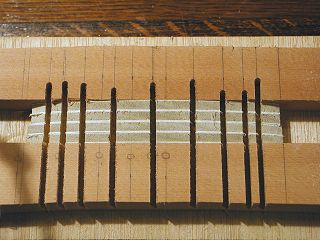 |
|
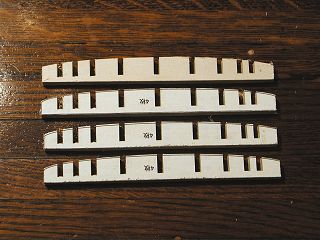 |
|
|
9本の溝を彫り終わったところです。 ご覧のように手前の押さえ板から掘り込み、終わりは上側の押さえ板の途中までになっています。
|
|
こうして溝を彫り終わった上下の側板。 トリマーを使ったこの方法は切削の正確さと作業時間の速さでベストだと思います。
|
|
|
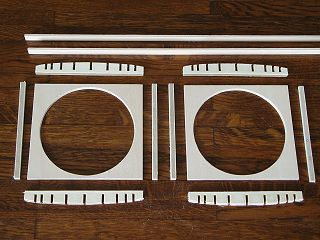 |
|
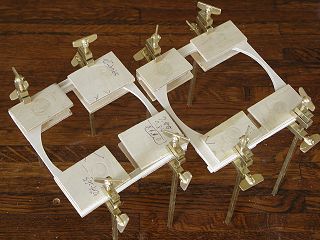 |
|
|
グリルを作るほかの部材も切り出しいよいよ組立ての開始です。
|
|
まず背板の端上面に左右の側板(5.5 x 5.5 x 113mm)を接着しハタ金で圧着保持します。
|
|
|
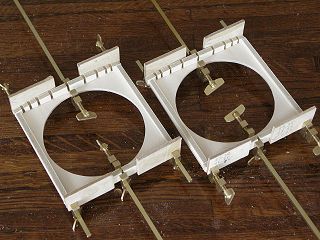 |
|
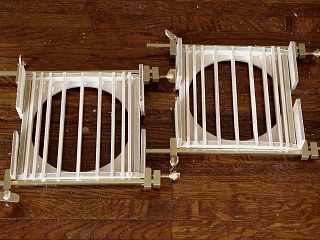 |
|
|
2時間後にに上下の側板を背板の上下断面に接着しハタ金で圧着保持します。
|
|
更に2時間後に9本の溝に桟を嵌め込み接着します。 これだけは圧着保持する必要はありませんが、背板が反ってきますので、それを強制的に補正するためハタ金で逆反りの力を加えています。
|
|
|
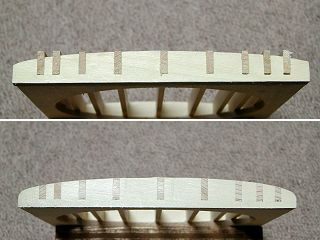 |
|
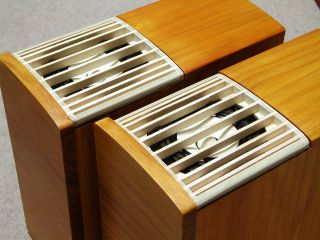 |
|
|
挿し込んで接着したヒノキ棒は全て幅10mmですから、このように端は突出します。(上) それをカンナで削って、替刃式ヤスリで所定の形に成形します。(下)
|
|
スピーカーのグリル固定部分内寸よりグリルの外寸は、1mm小さくなることを確認しておきます。
|
|
|
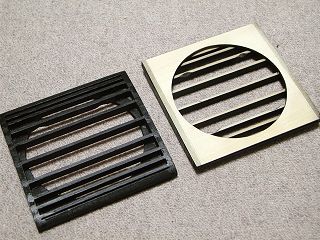 |
|
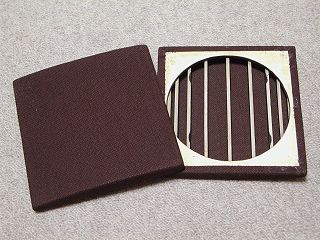 |
|
|
フロントグリルの前面側だけをつや消し黒のスプレー塗料で塗装します。
|
|
そしてジャージーをボンドG-17クリヤーで貼り付けました。
|
|
|
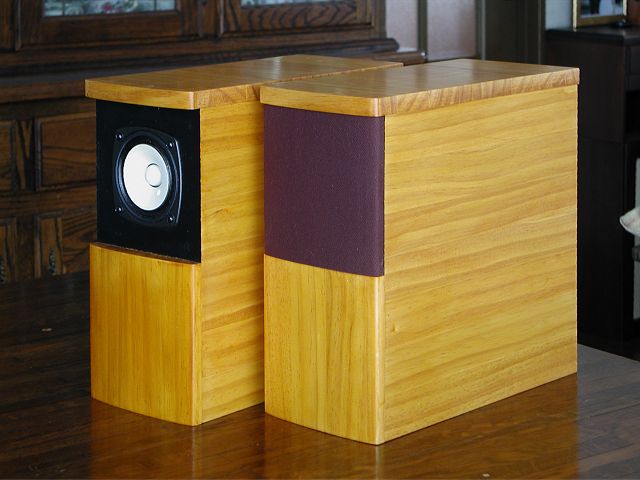 |
|
|
ジャージーを貼った接着剤が完全に乾燥後、フロントグリルを挿し込んで(圧入)8cmバスレフスピーカーシステムは完成しました。 いまどきムクに近い材料で作られたボックスを商品として生産しているメーカーはありませんから、自作のみで実現できて楽しめる領域です。
|
|
|
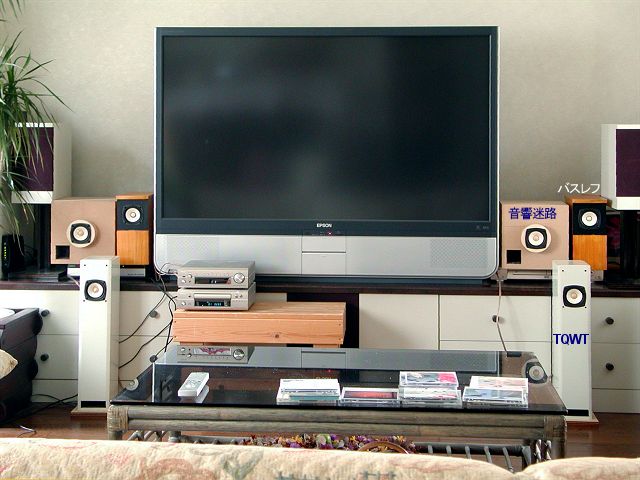 |
|
|
同じ系列のユニットを使った3種類のスピーカー(左から音響迷路型、TQWT、今回作ったバスレフ型)間の比較試聴の様子です。 その結果については下の解説をお読みください。
|
|
Copyright (C) 2001-2019, Vic Ohashi All rights reserved.