|
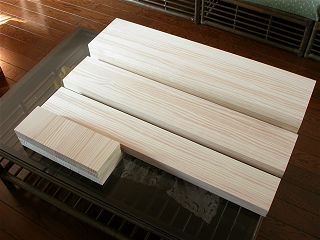 |
|
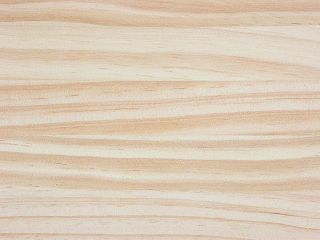 |
|
|
ホームセンターで切断してもらった21mm厚ラジアタパイン集成材。 手前の小さな板のみ更に手引きノコでで切断しました。
|
|
問題の好みが分かれる!と、お話した木目はこんな具合です。 節はないのですがなんとなく大柄、大雑把な感じがします。
|
|
|
 |
|
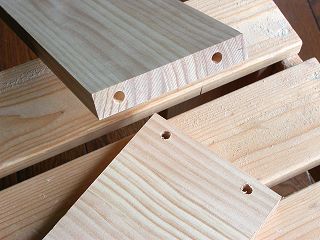 |
|
|
上の写真の小さな板から更に手引きノコで天板、底板、補強用の棒を切り出しました。 縦引きですがこの程度でしたら苦もなく横引きのノコギリで切断できます。
|
|
裏板と天板の接合開始。 8φの木ダボで接合するための穴あけを済ませたところです。
|
|
|
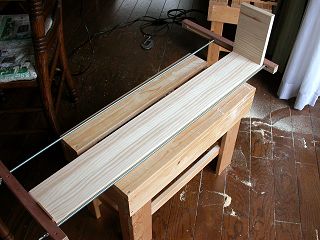 |
|
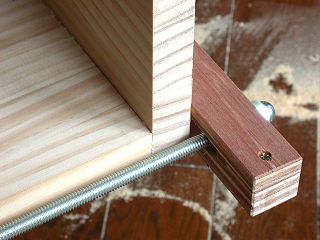 |
|
|
自作の中型クランプで裏板と天板を挟み締め上げて密着度を高めています。 L型部分の直角出しは十分な調整が必要です。
|
|
L型に接合している部分のクローズアップ。 クランプの位置を上下に移動すると、直角度の微調整が出来ます。
|
|
|
 |
|
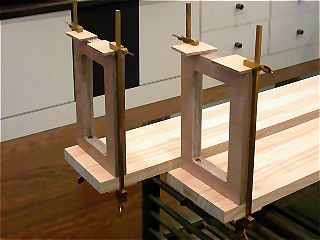 |
|
|
端材の18mmラワン合板から切り出した底板固定枠。 内部をジグソーで切断してます。 棒で組んだ枠よりも精度が高く強度も取れます。
|
|
その底板固定枠を裏板の反対側に木ダボ併用で木工ボンドにて接着。 この場合にはハタ金で密着度と直角度の調整をしています。
|
|
|
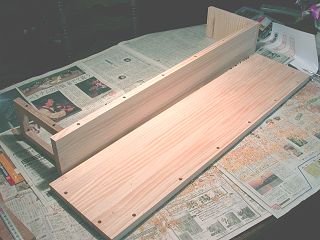 |
|
 |
|
|
側板を木ダボ併用で固定するため、ダボ穴を10箇所あけました。 コの字側は深さ20mm強、側板側は10mm強としています。 無論位置決めにはマーキングポンチを使っています。
|
|
左は片方の側板貼り付けが終わった物で右は接着剤硬化までの圧着中。 自作中型クランプ3組と300mmハタ金7本を一度に使うため、4面全てを貼り終わるにはゆうに1日掛かります。
|
|
|
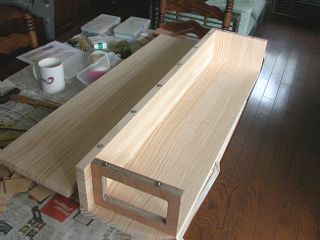 |
|
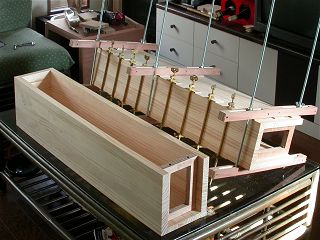 |
|
|
反対側の側板を接着するためダボ穴をあけます。 現在マーキングポンチでダボ穴位置を決めているところ。
|
|
再び自作中型クランプとハタ金は全員集合。 なんともはや気の抜く暇のない緊張が連続の作業です。
|
|
|
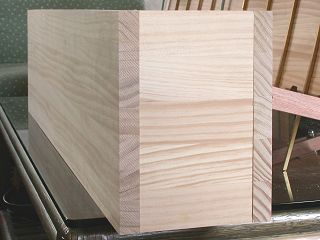 |
|
 |
|
|
箱の形に無事なりました。 側板のトップ部分は僅か(0.3-0.5mm)突出していますが、予定どおり。(後でペーパーで突出部分は削ります。)
|
|
こちらは底の部分。 台座に固定された底板が嵌まり込み、後で枠に取り付けられる鬼目ナットにボルトで固定します。
|
|
|
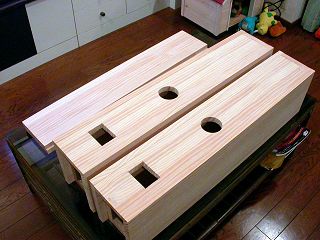 |
|
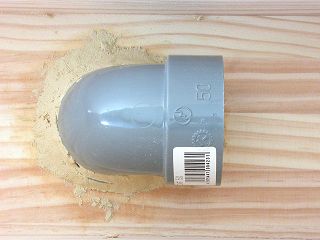 |
|
|
裏板にバスレフポートとスピーカー端子板の固定穴をあけました。
|
|
#50エルボをエポキシパテで固定。 これも実績の十分ある固定方法になりましたが、次の作業に支障のない程度に硬化するには1週間かかります。
|
|
|
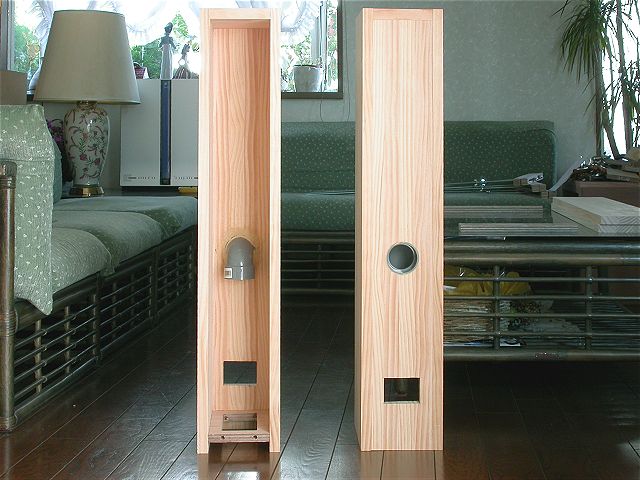 |
|
|
これに前板が付いて座板が固定されれば箱の組立ては終了ですが、補強や板割れ防止処理がその前に必要です。
ところで重量は座板なしで既に8kgあります。 スピーカーユニットは4.5kgありますから、座板、ネットワークを含むと15kg近くなってしまうでしょう。 口径12cmのシステムとしてはかなりの重量級です。
|
|
|
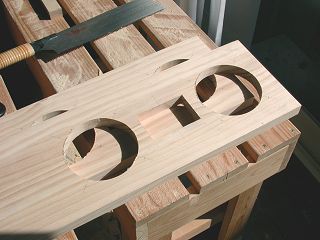 |
|
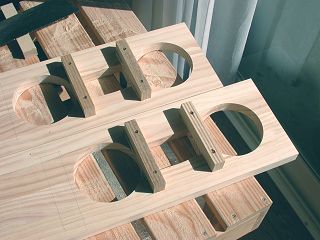 |
|
|
前板に3個のスピーカーユニットの穴をあけました。 板厚が21mmあり少々厳しいかなと思いましたが、小型のCJ-250を使って切り抜いています。
|
|
前板のF120AとFT7RPの間は18mmしかなくこの部分が割れやすいはずなので、18mm合板を切断した棒を貼って補強しています。
|
|
|
 |
|
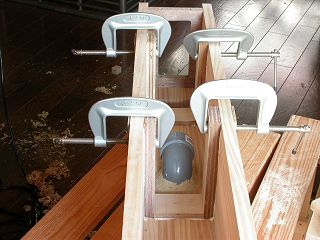 |
|
|
箱の上部の隅にラワンの角材を貼り補強しました。 他の補強もそうですが、木目と直角方向に補強棒を貼り付けるのが基本です。
|
|
箱の中間から下の方に2箇所コの字型となる補強を18mm合板を切断して貼り付けています。 これらは最終的にはコの字ではなくロの字の補強になります。
|
|
|
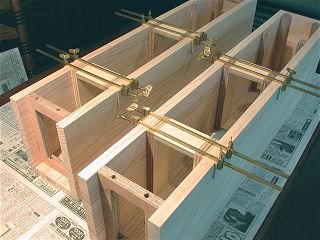 |
|
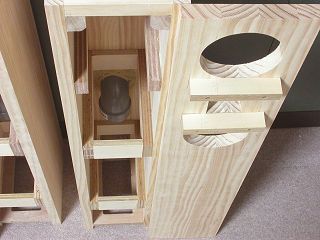 |
|
|
中段と下段の補強枠は前側を加えてロの字型になりました。
|
|
上から見下ろすとこんな按配です。 上の枠のみトウィーターが当るのでコの字の枠のままです。
|
|
|
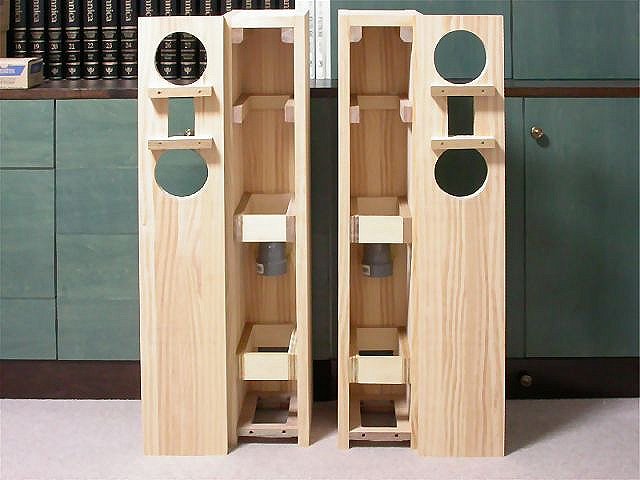 |
|
|
補強だけでたっぷりと1日掛かりましたが、ここまでやれば割れや剥がれは発生しないでしょうが、更に湿気を吸わないよう内部前面をニス塗りします。 大袈裟かもしれませんが、拘りの積み重ねのひとつとお考えください。
|
|
|
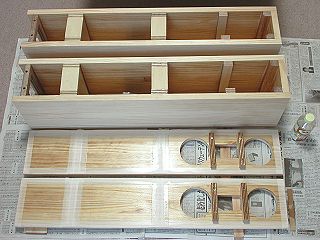 |
|
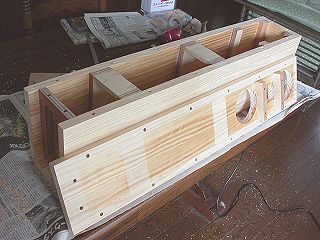 |
|
|
組み上げた箱の内部と前板裏側は接着部分をマスキングテープで覆い油性ウレタンニスを2回塗りして集成材の吸湿を抑えます。
|
|
1昼夜寝かした後いよいよ前板を接合。 8φの木ダボ14本を使って木工ボンドで接着します。
|
|
|
 |
|
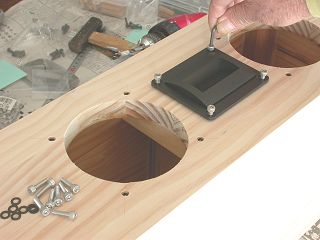 |
|
|
中型クランプで中央と両端を締め上げ、それらの間を8本のハタ金で密着度を上げています。 大型クランプが出るまでもありませんでした。
|
|
スピーカーは付属の木ネジではなく、ステンレスのM4六角ボルトと鬼目ナットの組み合わせで固定しました。 頻繁なネジ締めでも馬鹿になることはありません。
|
|
|
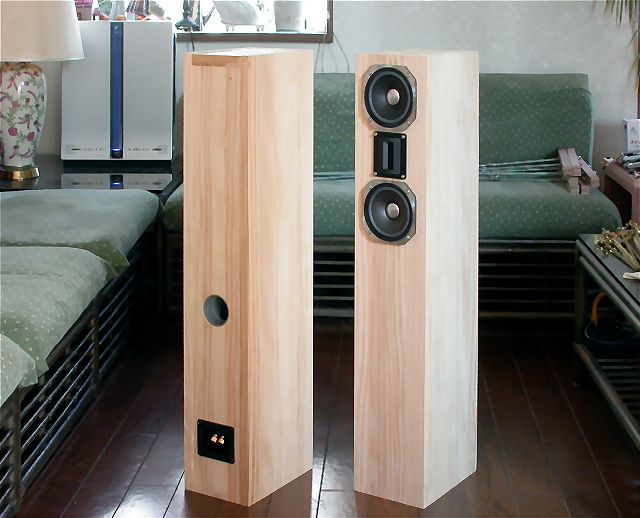 |
|
|
吸音材(FMミクロンウール)を仮に内部対向面に貼り付け、スピーカーユニットとスピーカー端子板を固定し結線して全域型として音が出る状態(トウィーターは未結線)となりました。 これで講習会に持ち込めます。
|
|
|
ここから4枚は#60 → #120 → #240 とサンドペーパーの粒度を替えて研磨した箱本体のクローズアップ写真です。 継ぎ目の段差がなくなっている様子や、場所によっては継ぎ目そのものが認識できない位になっていることが判ると思い ます。 カンナによる仕上げ削りは所詮集成材なので不可能なのですが、サンドペーパーと電動サンダーの組み合わせ で、カンナによる仕上げ削りにも劣らない処理が可能だという例です。
|
|
|
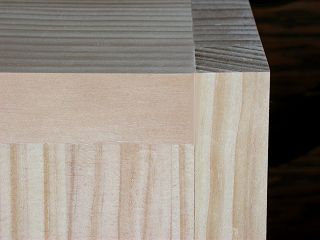 |
|
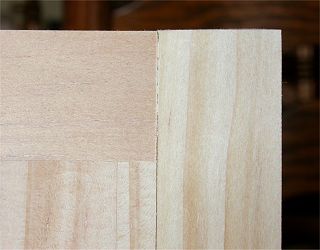 |
|
|
背面右上部分。
|
|
その部分の更なるクローズアップ。 継ぎ目に見える白いのは取りきれなかった研磨屑。
|
|
|
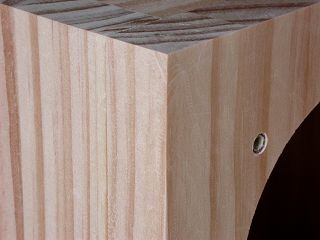 |
|
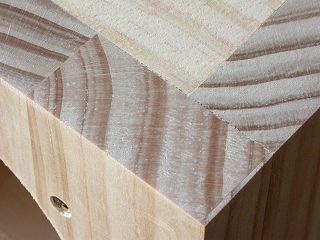 |
|
|
前面左上角。 ちょっと離れると継ぎ目は判らなくなる。
|
|
全面右角を上から。 隙間が殆どない接合とその段差が見事になくなっているのが判る。
|
|
|
ここからの4枚は上の4枚の写真と同じ部分を6回塗りのニス塗装が終わった後の写真です。 残念ながら撮影した日は 雨模様だったため発色が良くありませんが、それでもニスが沁みこんで透明感が増加した表面の感じや、着色無しで塗 装したため、ニスを塗ると黄色っぽくなったり赤みが増加したりする色の変化も良く判ります。
|
|
|
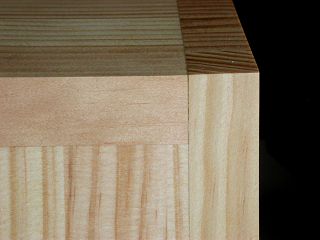 |
|
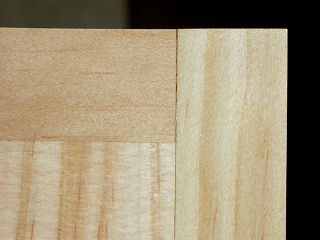 |
|
|
背面右上部分。 結構黄色味が増加している。
|
|
研磨屑の詰まっていた部分は、許容範囲内の隙間。
|
|
|
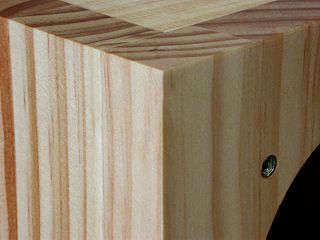 |
|
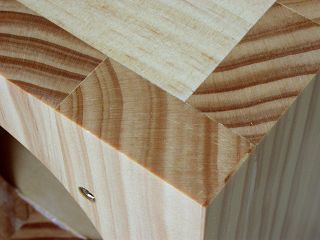 |
|
|
前板と左側板との継ぎ目がどこだか判りますか?
|
|
ニスが沁み込み透明感が増した状態は木口でよく判る。
|
|
|
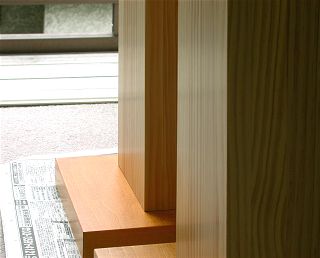 |
|
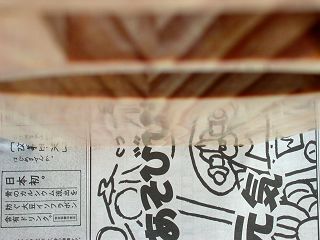 |
|
|
外は雨が降っているので外光も弱いのですが、半艶によるニブーイ反射の様子がわかると思います。
|
|
前面を真上から撮影。 下に敷いた新聞紙の文字が反射して見えます。 艶消しニスのみではここまでの反射はありません。
|
|
|
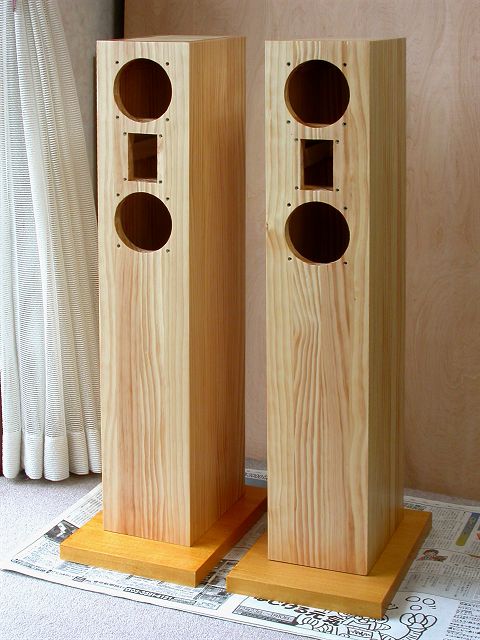 |
|
|
やっと塗装が終わった本体と台座。 台座はチーク色の着色ニスで色付けしましたが、電話台のときと同様、クリヤーを加えて色を薄くしてあります。
|
|
Copyright (C) 2001-2019, Vic Ohashi All rights reserved.