|
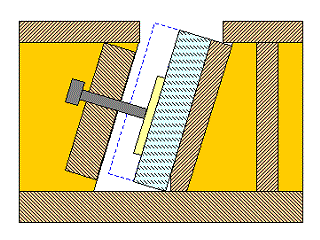 |
|
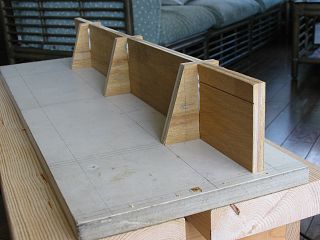 |
|
|
先にご覧頂いたジグの断面図から寸法線、寸法などを削除しました。 これ以降の写真と比較してください。
|
|
左の断面図の天板を除く右半分を組み立てた所です。 断面図との違いは台座で、幅を60mm伸ばしています。 これは作業台にクランプで固定する部分を確保するためです。
|
|
|
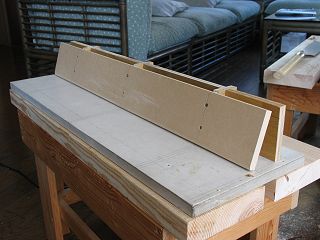 |
|
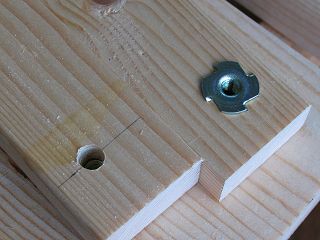 |
|
|
切削する材料を受ける板を固定しました。 この板の傾斜角度が材料の木口の傾斜角度を決定しますので、直線性共々正確に作らねばなりません。
|
|
材料は3本のM6ボルトで固定しますが、8φの穴をあけた上で断面図には描かれていない爪付きナットを玄翁で叩き込みました。 左が表側、右が裏側となります。
|
|
|
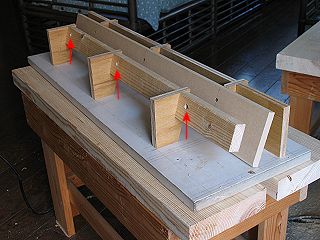 |
|
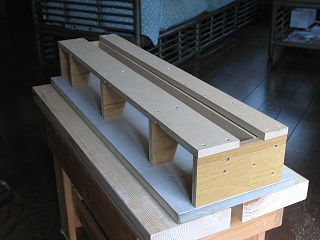 |
|
|
断面図左半分の天板を除き組み上げた所です。 矢印の先にM6ボルトを捻じ込む穴があります。
|
|
側板と天板を固定してジグの完成ですが、材料固定ネジが高すぎて天板角に当たるため天板を一部削りました。
|
|
|
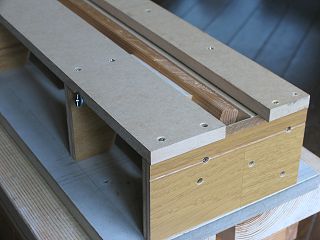 |
|
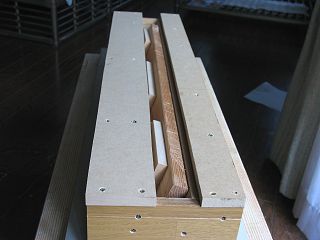 |
|
|
試みに切削予定の端材を所定の位置に落とし込み固定ネジを締め上げました。
|
|
それを真横から見た状態。 変ながたや撓みなどもなく上手く出来たようですので、別な板を装填して試験してみます。
|
|
|
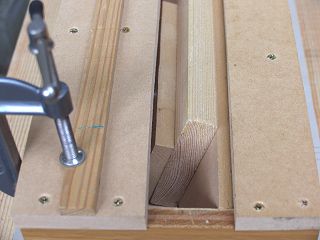 |
|
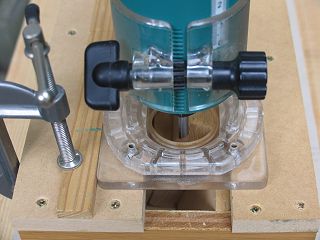 |
|
|
翌日出来具合のテストをしました。 長さ40cm程度のワンバイフォーの端材をセットしました。 左の上にクランプで固定しているのはトリマーのガイドです。
|
|
6mmのビットを若干浅めにセットして準備完了。 これでガイドに沿わせながら手前から向こうへ4回ほど切削すればOKです。
|
|
|
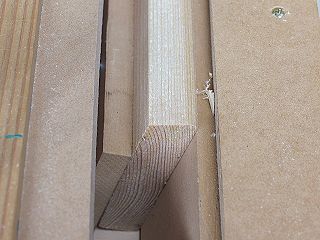 |
|
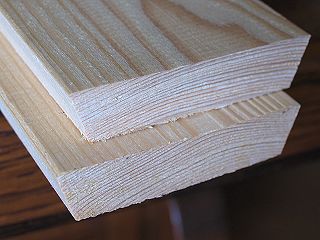 |
|
|
1回目の切削が完了しました。 ビットは浅めに取り付けたので右肩の丸い部分まで切削は及んでいません。 更にビットを出して切削します。
|
|
両面を切削し終えて取り敢えずはこんな物でよいかな?と加工を終了しました。 この時の板幅は87mmになっています。
|
|
|
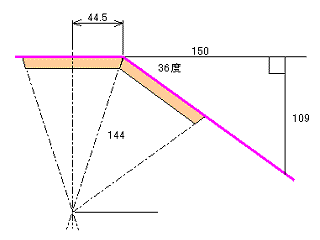 |
|
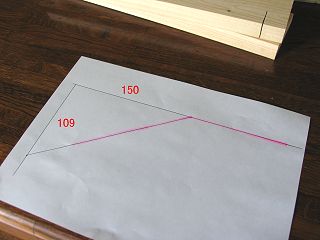 |
|
|
2枚の板の接合後の角度は144度になりますが、こんな考え方で接合角度の型紙を作ります。 勿論三角関数で算出しています。
|
|
A4サイズの紙に接合角度確認のテンプレートを描き上げました。 判りやすいようにピンクのマーカーで着色した線がそれです。
|
|
|
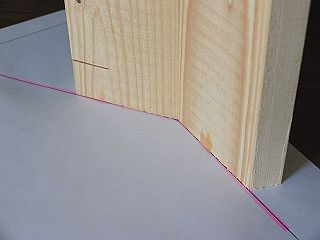 |
|
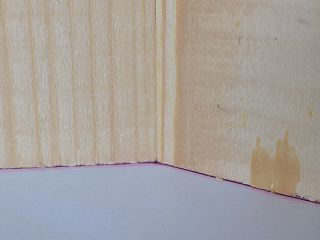 |
|
|
2枚の板をその線に沿わせて立てました。 自立させており一切保持はしておりません。
|
|
前面はこんな具合で接合部分に変な隙間はありません。
|
|
|
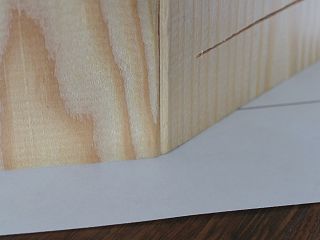 |
|
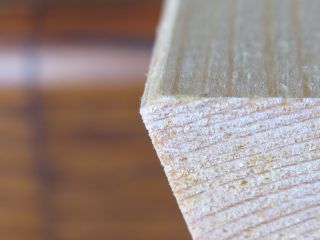 |
|
|
そっと裏へまわって撮影したのがこれで、やはりおかしな隙間は出ておらず切削角度が正確に出来ていることが判ります。
|
|
唯一の問題はこれ。 角の丸み部分がまだ残っています。 従って左の写真を良くみると判りますが、接合先端が尖ったような感じにはなりません。
|
|
|
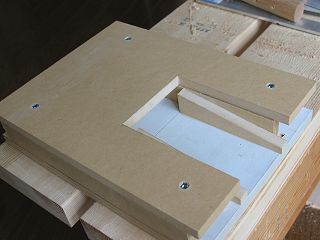 |
|
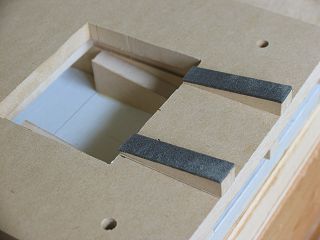 |
|
|
材料の斜めカットジグの材料を受ける部分で、ここに斜めになって見える2本で材料を受けて所定の傾斜にします。 4つ見える穴にはM6の鬼目ナットが捻じ込まれています。
|
|
これはその上に載せて材料が動かないよう押さえる板で、これを上下逆さに乗せて使います。 黒く見えるのは3mm厚のスポンジで密着度を高める目的で使っています。
|
|
|
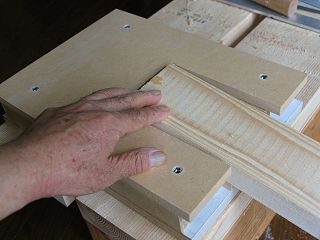 |
|
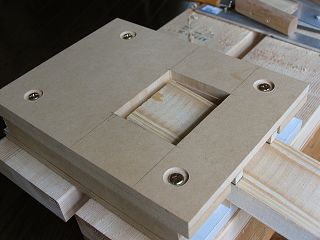 |
|
|
材料の固定手順で先ず切削する材料を斜めに受ける部分にしっかりと嵌め込みます。
|
|
その上に押さえ板を載せて4本のセットキャップボルトで固定しました。 ボルトの頭は予めフォスナービットでザグってあるので表面には出ません。
|
|
|
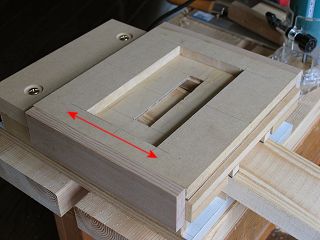 |
|
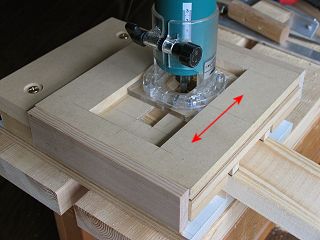 |
|
|
そしてコの字型のトリマーガイド板をその上に載せました。 このガイド板は矢印方向に移動可能です。
|
|
ガイド板に電動トリマーをセットしました。 電動トリマーは矢印方向に移動可能です。 これで電動トリマーは極めて安定した縦横の移動が可能になります。
|
|
|
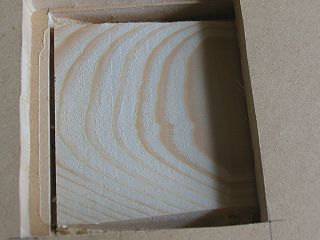 |
|
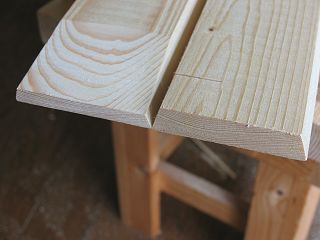 |
|
|
早速試し切削をしてみました。 切削量は材料先端で約9mmあります。 8mmのストレートビットを使っていますが、繋ぎ目の段差も殆ど見当たらず良好な結果です。
|
|
切削後(左)と未切削(右)を並べてみました。 全く問題が無いのでこのまま本番に入りました。
|
|
|
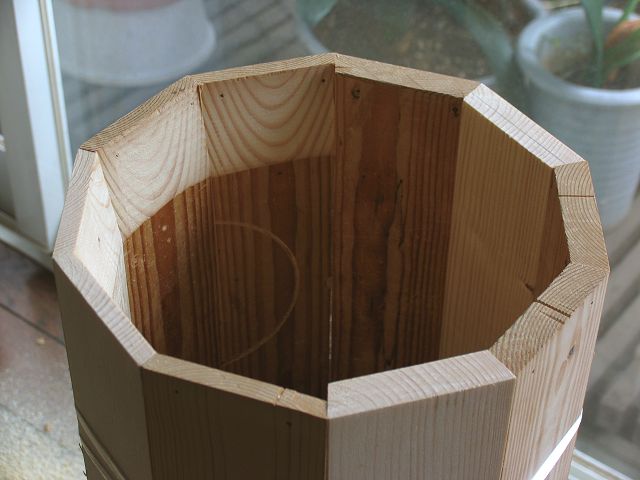 |
|
|
本番の切削も何ら支障なく順調に進みましたが、5枚を切削したところでくみ上げて外観を比較してみました。 左半分が切削後で上端の板厚は10mm、右半分は切削前で板厚は19mm。 ぼてっとした感じが薄れよりスマートな感じに変わっているのがお判りいただけるでしょうか?
|
|
|
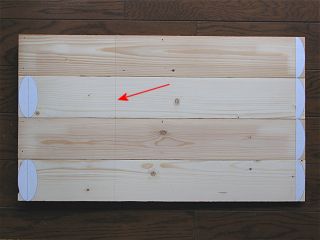 |
|
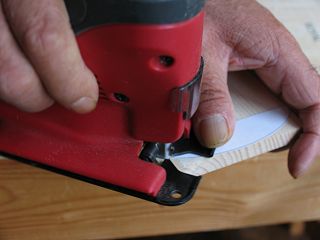 |
|
|
短径40mm、長径86mmの楕円をパソコンで描いて印刷し切り抜いた型紙を糊で貼り付けました。 切断後上下の位置合わせを容易にするため底から一定の距離に線を引いています。(矢印の先)
|
|
小さな曲率の切断は低重心設計のリョービ CJ-250と付属の曲線仕上切りブレードが最良の組み合わせ。 大型のジグソーよりも容易に高い切断精度が実現します。
|
|
|
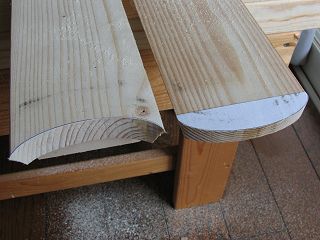 |
|
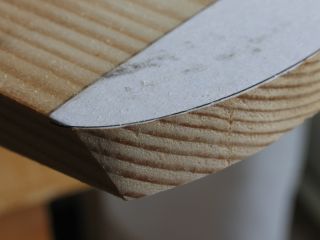 |
|
|
凹曲線と凸曲線の切断が終わりました。 型紙は水で濡らして剥がしますが、板を濡らすと反りが出てきますので、組み上げてから剥がします。
|
|
切断部分のクローズアップ。 切断線の極僅か外側を切っているのが判ると思います。 また切断面も非常に綺麗で仕上切りブレードの効果が判ります。
|
|
|
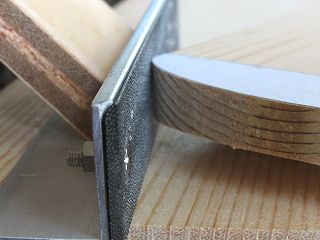 |
|
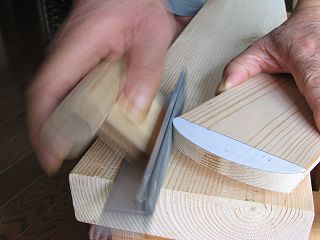 |
|
|
凸曲面の一次研磨には自作替刃式直角ヤスリを使いました。 こんな具合にヤスリ面を材料に当てます。
|
|
替刃式直角ヤスリで研磨中。 研磨面が直角になっているかどうかを気にしなくても良く作業効率は抜群。
|
|
|
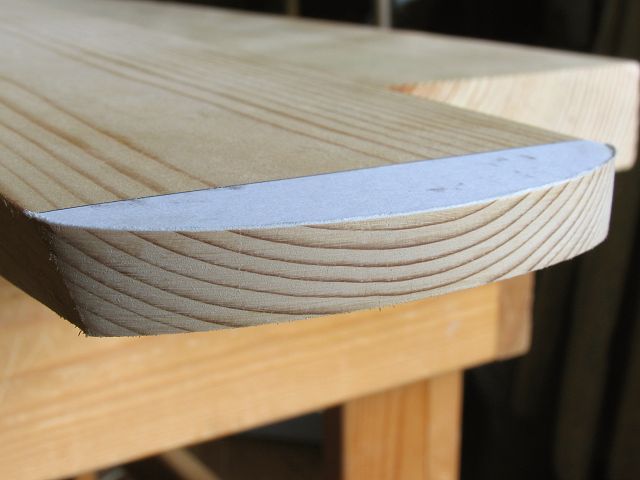 |
|
|
替刃式直角ヤスリで型紙の線ドンピシャになるまで(0.2-0.4mm位でしょうか?)削り上げて、その後#240サンドペーパーをハンドサンダーに取り付けて仕上げ研磨。 表面はつるつるに磨き上げられました。 尚型紙は板を濡らすと反るために組立てが完了するまでこのままです。
|
|
|
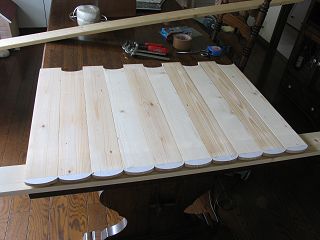 |
|
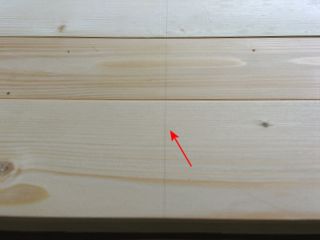 |
|
|
組立て作業の第一段階はテーブルの端に端材のワンバイフォー材を置き、その上に10枚の板の外側を上向きに板同士が隙間無く並ぶようにします。
|
|
その際既に引いてある線(底から一定の距離にある。)が真っ直ぐに並ぶようにします。(これがずれると垂直に立ちません。)
|
|
|
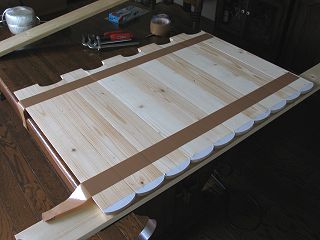 |
|
 |
|
|
上下の適当な2箇所に布テープを横に貼り付けて10枚の板を連結します。 この時テープの左端は板の幅程度長めに垂らしておきます。
|
|
そうしたら10枚の板をひっくり返すのですが、端材の板をもう一枚載せてバクマクランプで強く挟んでバラバラにならないようにしてからひっくり返します。
|
|
|
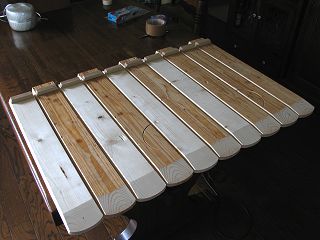 |
|
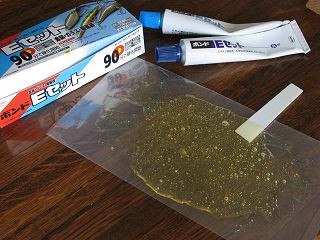 |
|
|
これがひっくり返した状態です。 これで接着剤を塗りつける準備が出来ました。
|
|
接着剤は90分硬化開始型エポキシで、ポリエチレンの袋の上にA液とB液を等量絞り出し、ヘラで混合します。 そしてヘラで接着面に塗りつけます。 硬化開始は90分後ですから慌てる必要はありません。
|
|
|
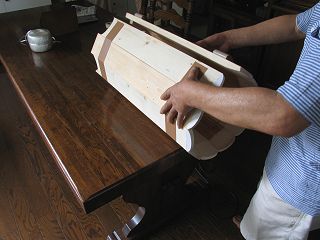 |
|
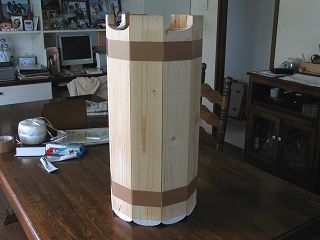 |
|
|
エポキシを塗り終わったら両端の板を持ち上げてゆっくりと円筒状にしてゆき端と端が合わさるようにして布テープを貼り付けます。
|
|
この時位置合わせの線がずれないよう注意します。 またむりやり曲げると布テープが破断する可能性があるので落ち着いてゆっくりやる必要があります。 そして上面を下にして立てます。
|
|
|
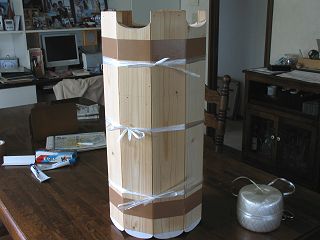 |
|
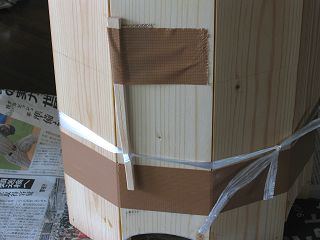 |
|
|
次に荷造り用のプラスチック紐を上、中、下の3箇所3-4回巻いて縛ります。(強く縛り上げる必要はありません。)
|
|
接合面の位置を再度確認・調整後に割り箸をプラスチック紐の下に通してから回転して数回捻り十分に締め上げます。 割り箸の端は戻らないようこのように布テープで固定します。 これで完全硬化(12時間)まで寝かせます。
|
|
|
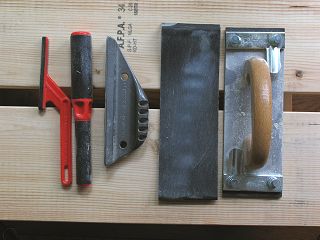 |
|
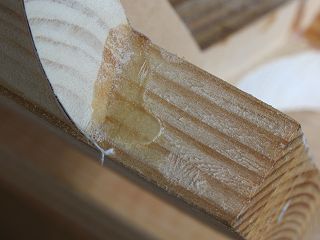 |
|
|
組み上がった本体各部を研磨するのに使った各種ヤスリ。 右端のハンドサンダーには#60と#240の布ペーパーを使います。
|
|
下部凹曲面を最初に研磨します。 エポキシがこのようにはみ出して固まっている箇所が幾つかありました。
|
|
|
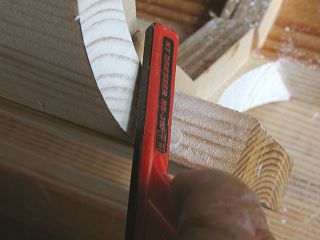 |
|
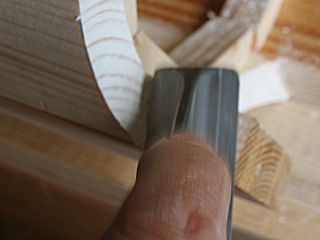 |
|
|
隅の所はRS-310Pがおあつらえ向き、エポキシを完全に削り取ります。
|
|
そして平らな部分はM-20GPで。 強研磨が得意ですから効率良く進みます。
|
|
|
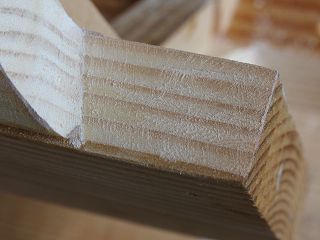 |
|
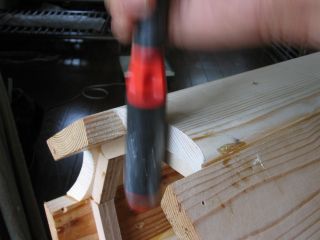 |
|
|
沁み込んだ部分も含め完全にエポキシは取り除けました。 この後#240ペーパーで仕上げます。
|
|
その他の凹曲面はDR-1000Pの出番。 私はグリップ部分にDR-800P用の替刃を取り付けているので、反対に握れば曲率が小さい所でもOKです。
|
|
|
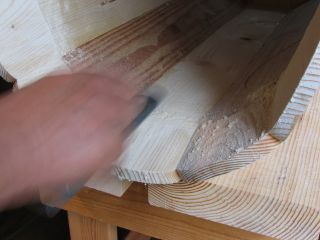 |
|
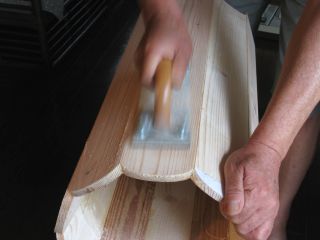 |
|
|
上部内側のテーパー部分でここにもエポキシが付着していましたので、M-20GPで強研磨し完全に削り落とします。 その後ハンドサンダーに#240ペーパーを付けて仕上げ研磨です。
|
|
最後が表側ですが、ここも付着したエポキシをM-20GPで削ってからハンドサンダーに替え#60ペーパーで型紙や墨線が消えるまで削り込みました。 そして#240ペーパーに替えてつるつるになるまで磨きこみます。
|
|
Copyright (C) 2001-2019, Vic Ohashi All rights reserved.