|
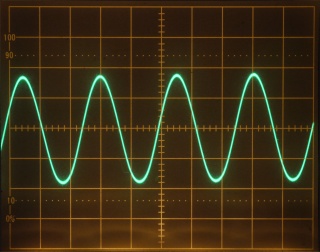 |
|
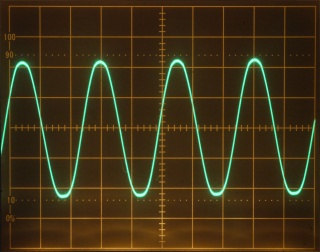 |
|
|
LMP7732の電源電圧1.8V、負荷抵抗15Ω時の補足です。 左は歪が少ない状態での最大値で113mV(0.9mW)ですが、更に入力電圧を増すと右のように出力電圧は上がります。 但し歪が増えて波形の頭が丸くなり奇数次高調波が増加していることを伺わせます。 そしてこの状態は使えないと判断しました。
|
|
|
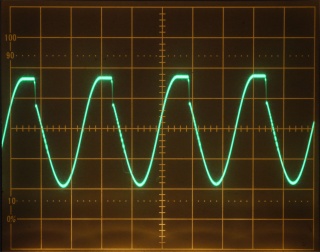 |
|
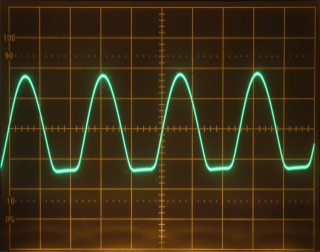 |
|
|
電源電圧1.8VでAD8656が示した挙動です。 低い出力電圧から正弦波とは似ても似つかない再生波形を示し使い物にならないと判断しました。
|
|
同じくLME49721が電源電圧1.8Vで示した挙動で、低い出力にも拘らず波形の片側がすっぱり切断されたような再生波形を示し、これも全く使い物にならないと判断しました。
|
|
|
次の一連の波形は電源電圧3.0Vの時の方形波応答ですが、2.7V〜4.5Vの電源電圧内で大きな変化はないと思われます。
|
|
|
 |
|
|
僅かなサグのため15Hz以下はレベルが低下します。(カットオフ8Hz) 3つのオペアンプ間での違いはありません。
|
|
|
 |
|
|
1KHzにおいても原波形と全く同じ形ですので、100Hzから10KHzまで完全にフラットでありオペアンプ間の違い無し。
|
|
|
 |
|
|
10KHzにおいても同様で、原波形と全く同じ形ですから、1KHzから100KHzまで完全にフラットであり全オペアンプで殆ど同じ傾向の周波数特性です。
|
|
|
 |
|
|
50KHzになっても傾向は同じで、10倍の500KHzまでフラットです。 以上を総合すると、10〜500KHzの間が全くフラットで、それより高い方にもピークやうねりが見当たりません。 極めて優秀な周波数特性を有しています。
|
|
|
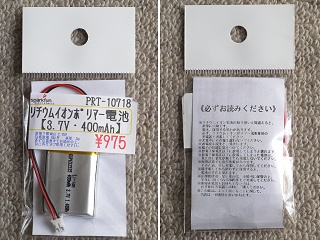
|
|
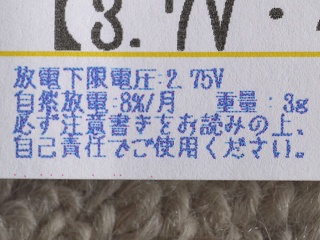
|
|
|
これがリチウムイオン充電池のパッケージで、左が表側で右が裏側です。 左上に小さくSparkfun Electronicsと入っていますが、メーカーのパッケージではなさそうです。
|
|
ラベル左下の青い文字のクローズアップ。 放電下限電圧が2.75Vは低すぎるのでは? スペックの一部と『使用者の自己責任』が強調された文書。 そして注意書きとは?
|
|
|
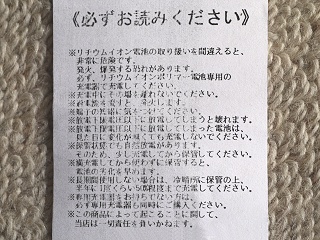
|
|
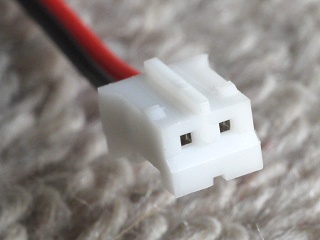
|
|
|
裏側の『必ずお読みください』と題した下の小さな文字の箇条書きがそれのようですが、リチウムイオン電池の一般的な取り扱い注意事項にしか過ぎません。
|
|
充電器に接続するコネクターですが、メーカーのホームページを調べたら JST(日本圧着端子)のPHシリーズであることが判りました。 些細なことですがこれは朗報です。
|
|
|
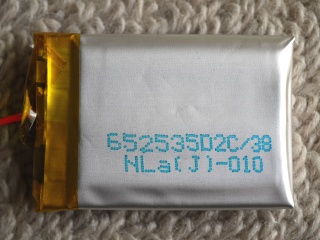
|
|
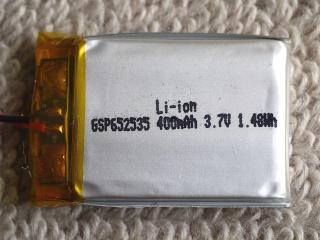
|
|
|
リチウムイオン電池はアルミ蒸着プラスチックに包まれています。 これを分解するのは避けたほうが良いでしょう。 気になるのは表、裏のどこにも生産メーカーが記載されていないことです。 パッケージを分解すれば判るのかもしれませんが、これでは何が起きても責任の所在がはっきりしません。
|
|
|
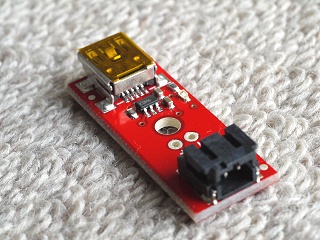
|
|
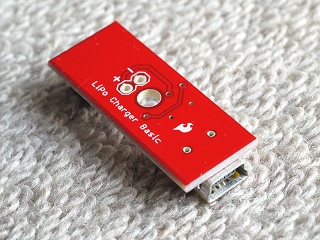
|
|
|
充電器のパッケージは電池以上で説明書はおろか注意書きも何も付属していませんでした。 ご覧の通りスッポンポンの裸基板で、手前が電池に繋がるJSTのオスのコネクターです。
|
|
充電器基板の背面。 LiPo Charger Basic の記載があるだけで、こちらも生産メーカーの記載が全くありません。 この後実際に動作させてみたら、充電中に赤のLEDが点灯する自動充電器であることが確認できました。
|
|
|
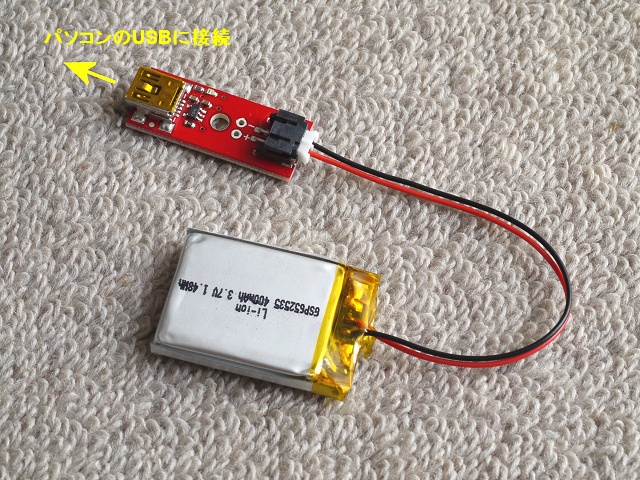 |
|
|
充電する場合にはこのように接続してUSBケーブル(mini-Bタイプ)でパソコンに繋いでやります。 一応充電動作らしきことははちゃんとしたようですが、全く説明書も無いので不安を感じます。
|
|
リチウムイオン充電池の扱いの気難しさや事故のリスク!を考えると、まともな説明書が電池、充電器共に付属していないこんな商品は、ズブの素人には全くお奨めできない物です。 とは言えこのようなことはおおよそ判った上で購入しているので、リチウムイオンまたはポリマー電池の一般的な技術知識を元に、実働試験などで致命的な問題が出なければ使う予定でおります。
|
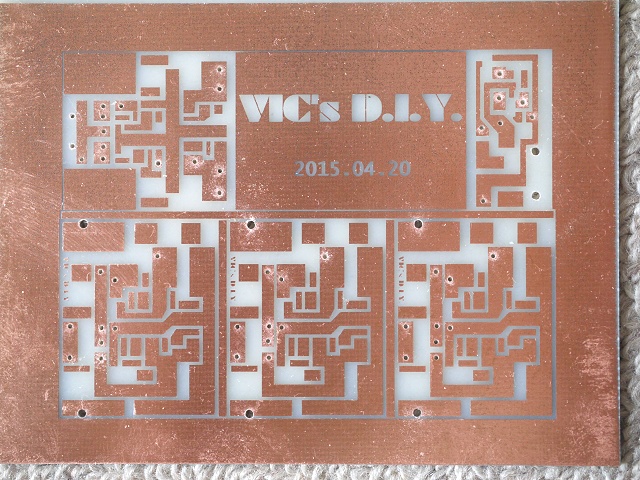
|
|
|
基板の所定の位置に穴をあけました。 大きい穴は1.2φですが、残りの小さな穴は全て0.6φとしています。
|
|
|
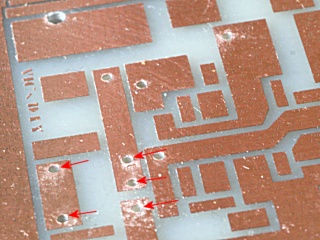
|
|
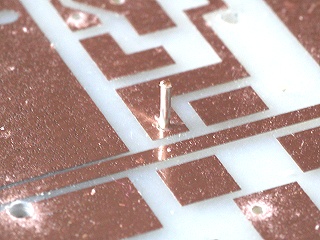
|
|
|
これら5個の穴は見ている角度が異なるものの、この下のスイッチの固定穴で、もっとも穴あけ位置の精度が重要です。
|
|
0.6φの小さな穴は全てジャンパー線を半田付けしますが、ジャンパー線は0.5φの錫メッキ線を使うのでこの口径としました。
|
|
|
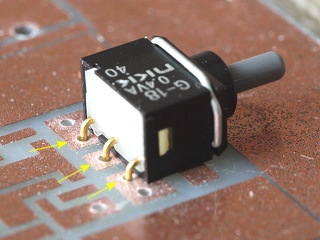
|
|
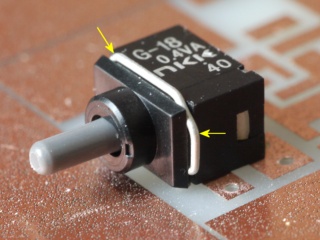
|
|
|
電源スイッチの取り付け穴中3個並んだ物は電気的な接点で半田付けされますが、残り2個は固定のみが目的です。
|
|
固定する2箇所はこの矢印のぐるりとスイッチを巻いたようなワイヤーで、基板に差し込んで曲げて先端はエポキシ接着剤で固定します。
|
|
|
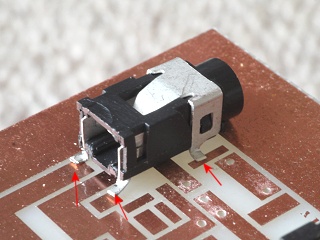
|
|
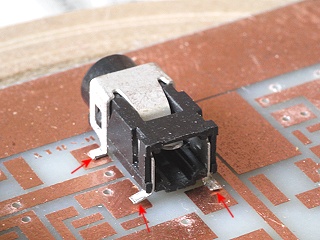
|
|
|
これは右側に付くヘッドフォーンジャックですが、矢印先の3本の電極は基板のパターンに半田付けし、見えない向こう側の1本は穴に差し込んで曲げ、エポキシ接着剤で固定します。
|
|
こちらは左側に付くヘッドフォーンジャックで左と同じですが、半田付けされる前側のピンは左右反対になります。
|
|
|
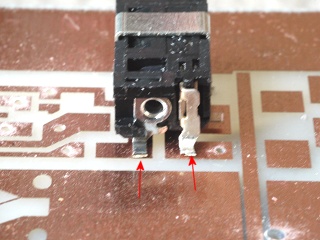
|
|
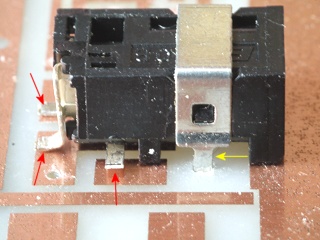
|
|
|
DCジャックの背面側で、2本の電極は後ろ側に半田付けして接続と固定を兼ねます。
|
|
真横からDCジャックを見ると3本目の電極がありますが、黄色のピンはジャック固定用のピンであり、基板に差し込んで裏側で折り曲げ固定されます。
|
|
|
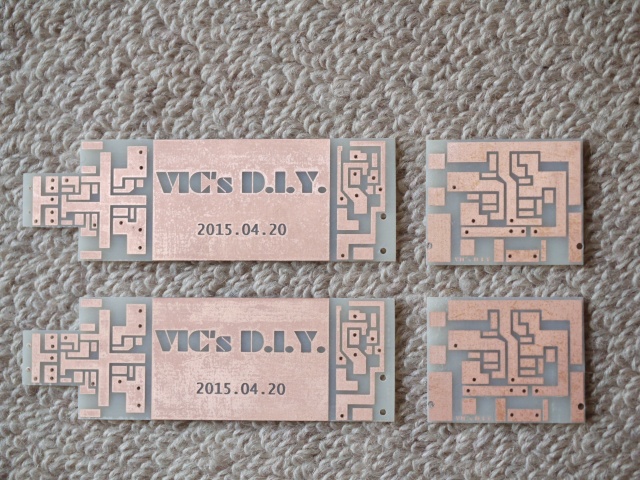
|
|
|
2次加工の穴あけ終了後電動ジグソーで切り離してヤスリで寸法出しをしました。 ノギスを使いながらゆっくりと作業しましたので、仕上がり寸法は設計値に対し±0.1mmの精度に収まっています。
|
|
|
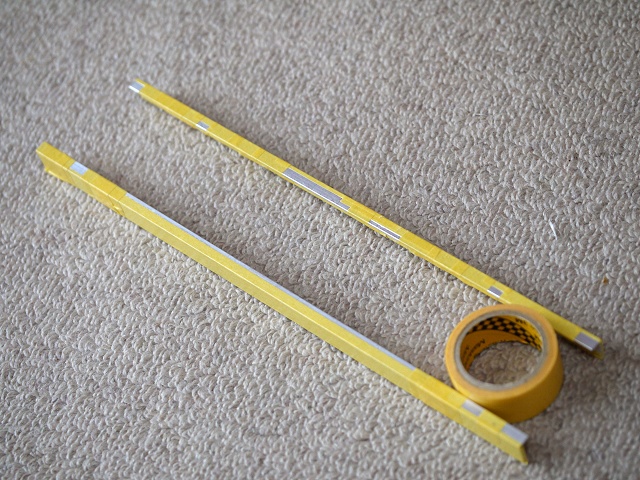
|
|
|
折り返された幅5mmの部分の加工の準備が終わりました。 マスキングテープで覆われていない銀色に見えるところだけをマスキングテープ領域には入らないよう刃研ぎグラインダーで削ってやります。
|
|
|
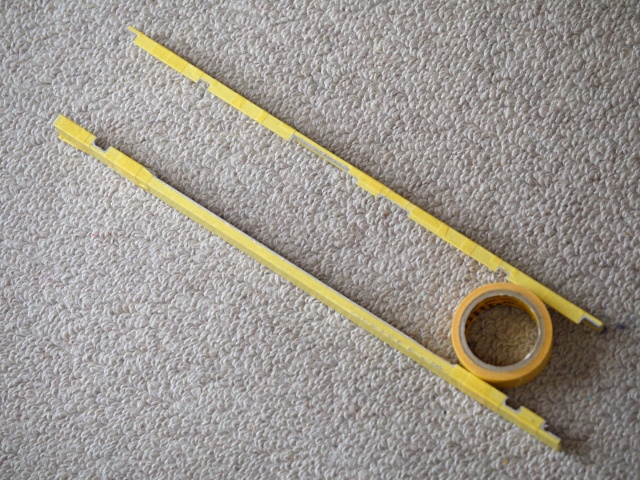
|
|
|
刃研ぎグラインダーで削り終わった状態です。 切削面はザクザクでお世辞にも切れだとは言えませんので、ヤスリでそれらザクザクを削りながら寸法出しをします。
|
|
|
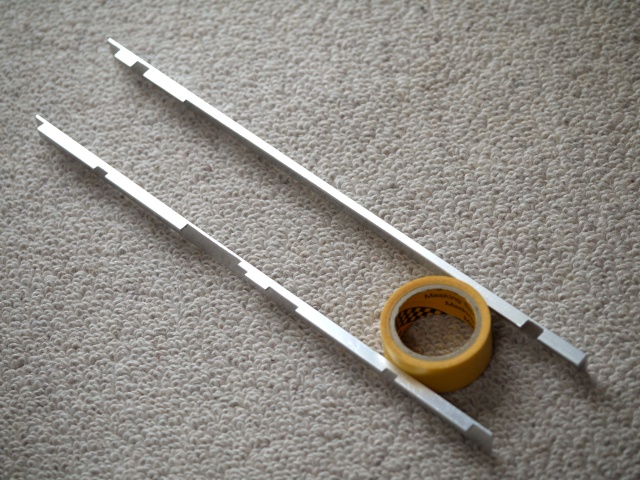
|
|
|
ヤスリによる寸法だしと仕上げ研摩が終わり、ザクザクだった切断面は滑らかになりました。
|
|
|
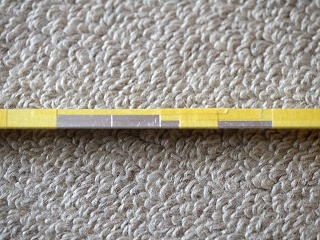
|
|
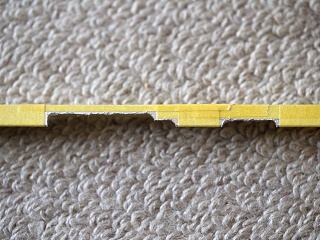
|
|
|
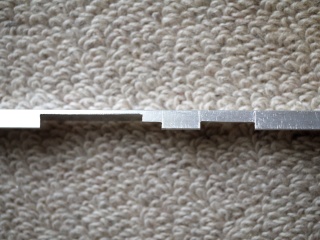
|
|
切削加工の詳細説明
左上の写真: ノギスで確認しながら罫引線を入れた後で、切削しない部分をマスキングテープで覆いました。
上の写真: 刃研ぎグラインダーで切削を終わった状態です。 マスキングテープで覆われた部分に侵入しないよう注意しながら作業しています。
左の写真: マスキングテープを剥がす前に平ヤスリでマスキングテープの部分迄削る込んでやりました。幅狭な部分もありますので、20、11、7mm幅の平ヤスリと3mm幅の角ヤスリを使っています。
これら切削作業の途中でノギスを使って正確な寸法出しが出来るよう何度も確認しています。
|
|
|
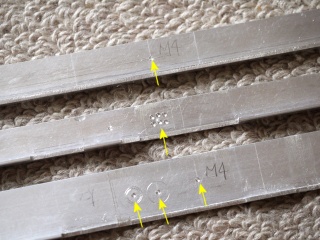
|
|
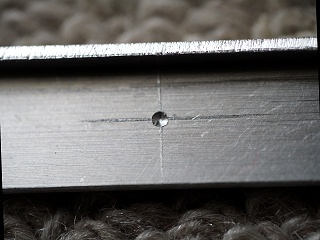
|
|
|
矢印の先は穴あけ位置を明確にするマーキングですが、位置を正確にするため0.8mmのドリルを手回しバイスに取り付け手回しにて深さ0.5〜0.7mm程の穴としました。 右はそのクローズアップです。
|
|
|
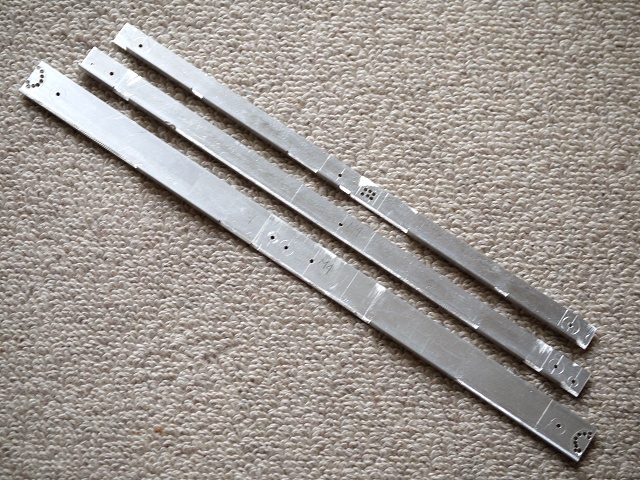
|
|
|
1個の穴を除き(後述)、全て1.5φのドリルで穴をあけました。 半円形、ちょっと大きめの長方形の穴は内部に沢山の穴を接近してあけています。
|
|
|
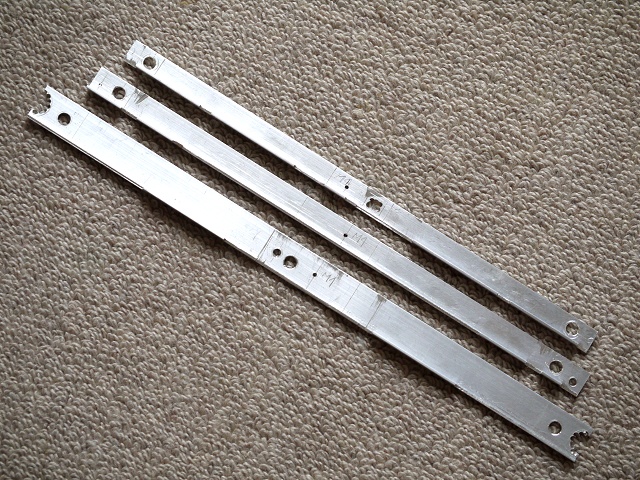
|
|
|
M4ネジ切り穴はそのままとし、4φの穴は更に3φのドリルで、6φの穴は3φ、4.8φとドリルを変えて広げています。
|
|
|
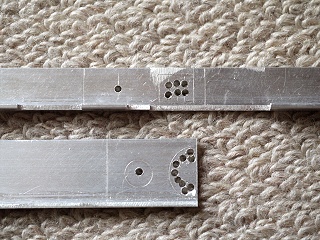
|
|
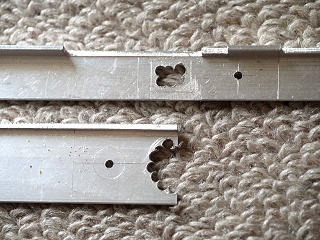
|
|
|
長方形の穴、半円形の穴は第一段階でその内側に1.5φの穴を接近して沢山あけてやります。
|
|
次にドリルを2φに変えて穴を広げると穴が繋がり中心部分は抜けてしまいます。 その後はヤスリで仕上げます。
|
|
|
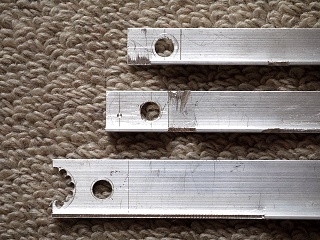
|
|
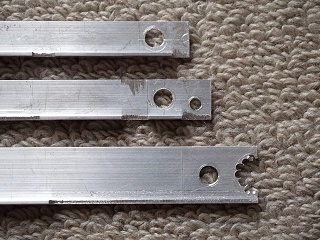
|
|
|
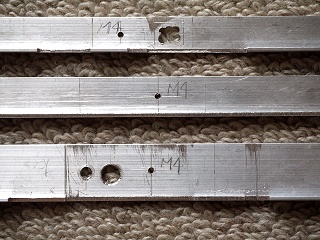
|
|
左上と上の写真:
6箇所の6φは敢えて4.8φの穴あけを最終としていますので、穴の外側に罫引き線が見えます。 これは所定の穴より大きい穴をあけないための対策です。 もしも6φのドリルを使うとどんなに注意しても穴位置がぶれるため、穴位置の修正研摩をすると穴が大きくなってしまいます。 4.8φのドリルであれば計算上は0.6mm穴位置がずれても穴位置の修正研摩をしても6φより大きくはなりません。
左と上の写真:
最終的に4φの穴が2個見えますが、6φの穴と同じ理由で3φでドリルによる穴あけを終了しています。 左の写真には1.5φで終了させた穴が3個見えますが、何れも1.5〜2.0mm厚のアルミ板を貼ってからM4のネジを切ります。
|
|
|
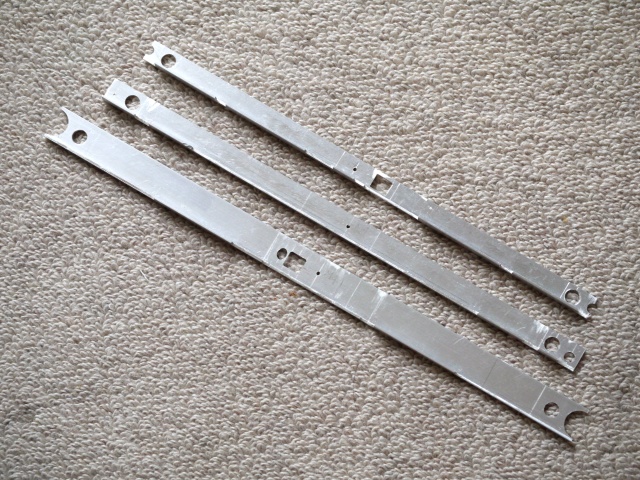
|
|
|
時々ノギスを当てて寸法を確認しながらヤスリで削ることで寸法出しが完了したフレーム材です。
|
|
|
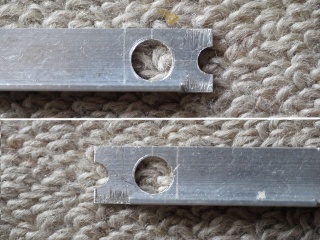
|
|
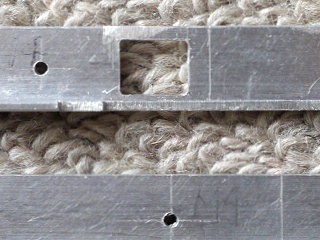
|
|
|
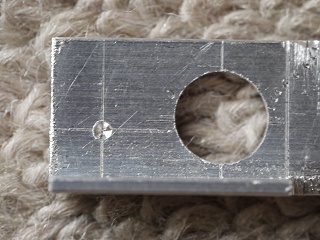
|
|
左上の写真: これはリチウムイオン充電池を使うモデルのフレームですが、両端に4φの半円が加工され、フレームを曲げて突きあわせた時に4φの円になり、電源スイッチの頭が納まりますが、フレームの突合せ前に基板の後部のコネクターを先に納めないとなりません。
上の写真:
1.5φの穴を沢山空けてそれらを繋ぐことで中を抜いた長方形ですが、平ヤスリと角棒ヤスリを使ってこのように仕上がりました。 ここに充電器接続のコネクターが通ります。
左の写真:
単四電池を使うモデルではLEDの位置がこのマーキングの位置になりますが、LED固定基板を貼った後で1.2φの穴としてナイロンワイヤーを通すことになります。
|
|
|
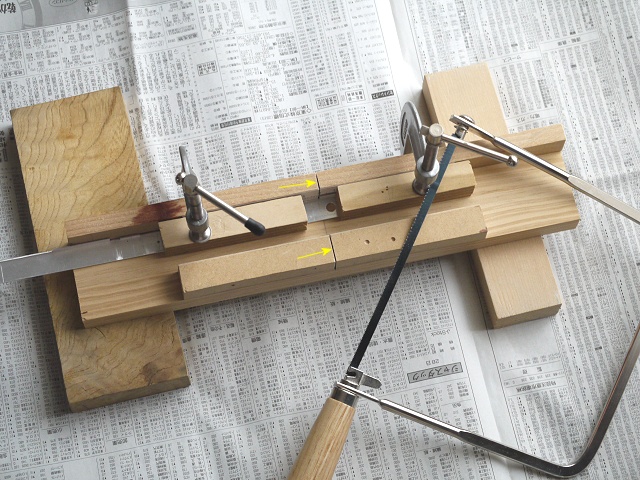
|
|
|
ジグの全景です。 2本の棒を直角に切断して隙間は糸鋸刃が通る幅として貼り付けます。 棒の間隔は4〜6cm程度という簡単な構造です。 その内側にアルミ押出材を押さえ棒を当ててクランプで固定します。 右手に写っているのはアルミ切断用の刃を付けた糸鋸です。 そうそうジグは左右に角棒を置いてその上に載せていますが、それはクランプがテーブルに当ってぐらつかないためです。
|
|
|
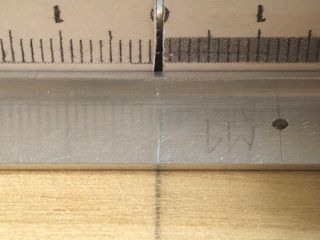
|
|
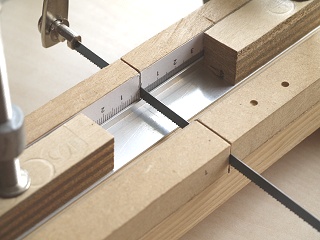
|
|
|
切断位置のアップです。 切断位置精度は楽に0.2mm以下を出すことが可能です。 スケールが見えますがこれは不要です。
|
|
糸鋸刃をジグの隙間に落とし込みました。 これで切り溝の幅のブレは0.2〜0.3mmが最大程度に収まります。 糸鋸刃の切り幅は0.7mmですので、ブレ込みで0.7〜0.9mmの溝が切れることになります。
|
|
|
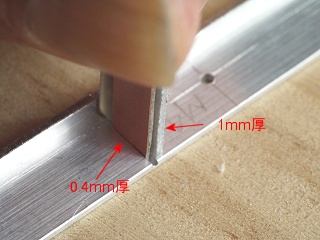
|
|
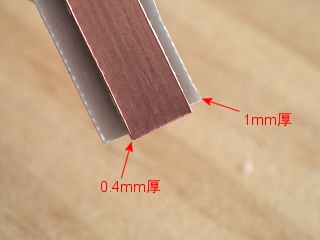
|
|
|
切る溝の深さは0.5〜0.6mmとしますが、深さの確認はこのような手順で。 先ず0.3〜0.5mm厚の板を切った溝に当てます。 その横に1mm以上の厚みの板を当ててやります。
|
|
その状態でそっと引き上げるとこんな感じになります。 薄い板が溝の深さ分だけ飛び出ます。
|
|
|
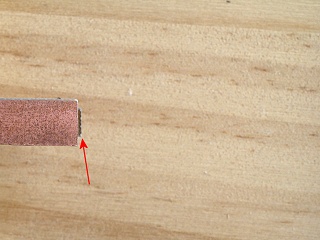
|
|
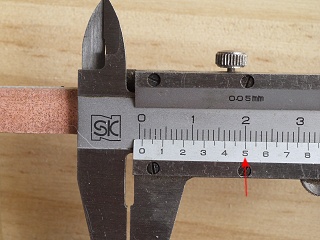
|
|
|
そのままひっくり返して指でこのように持ちます。 矢印の先が薄い板の出っ張りです。
|
|
ノギスをこのように当てて段差の測定をします。 バーニア目盛りは5のところで主目盛りと一致しているので、出っ張りは0.5mmであることが判ります。
|
|
|
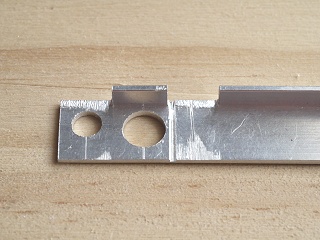
|
|
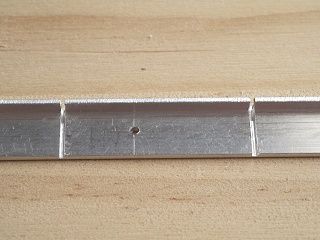
|
|
|
実際に溝の切込みが終わりました。 これは単四乾電池型の端(折り曲げ後前面中央になる。)の部分です。
|
|
2箇所の溝の間が背面になります。 大変シンプルな構造です。
|
|
|
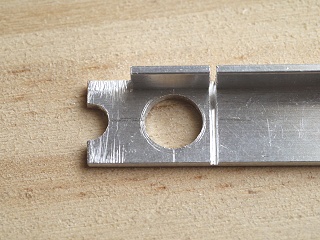
|
|
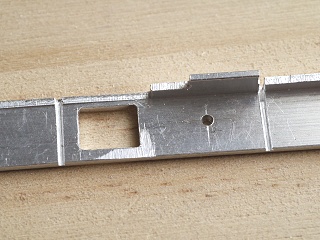
|
|
|
こちらはリチウムイオン充電池型の端部分です。 上の写真より近距離で撮影したので大きく写っていますが、実際はフレームの幅はこちらの方が狭いです。
|
|
背面部分には充電器接続のコネクターがあります。 折返し部分の加工も含め上よりも複雑な構造です。
|
|
|
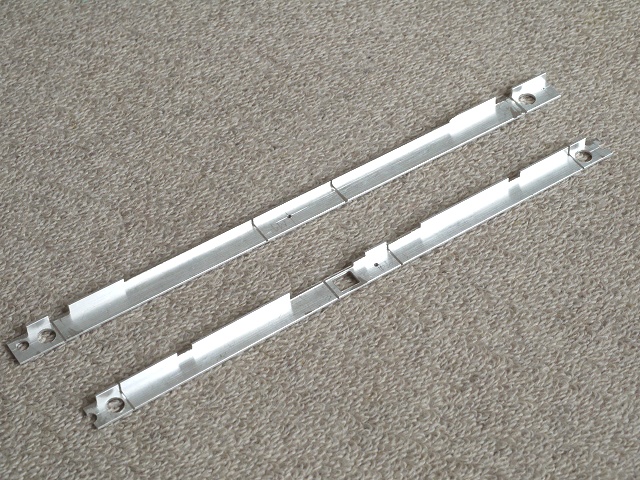
|
|
|
フレームの準備加工も最終段階に入りますが、ここまでで妙な間違いがないか確認しておきます。
|
|
|

|
|
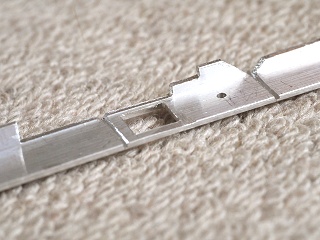
|
|
|
準備加工の最後は折り曲げ部分の45度切断処理ですが、フレームを曲げるような力が入らないようにヤスリで削ってゆきます。 これはリチウムイオン充電池型の端部分です。
|
|
背面部分はこの通りで、左の折り曲げ部分も45度に削っています。
|
|
|
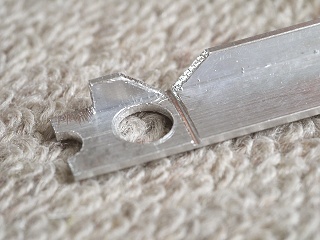
|
|
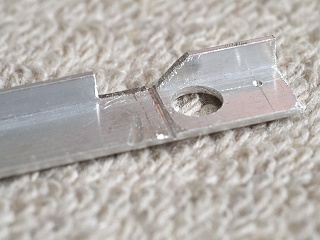
|
|
|
上の写真の反対側の様子です。
|
|
こちらは単四乾電池型です。 フォーンジャックの端子が干渉する部分があるので、大きく欠き取られています。
|
|
|
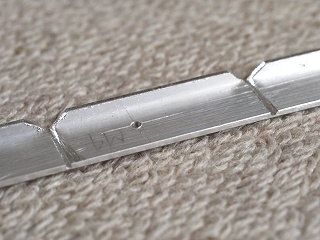
|
|
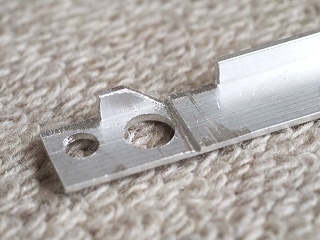
|
|
|
背面部分です。 このくらいの加工で済むのであれば楽に進むのですが?!
|
|
反対側の端の部分。電源スイッチが干渉するのでこれまた欠き取り量が多いです。
|
|
|
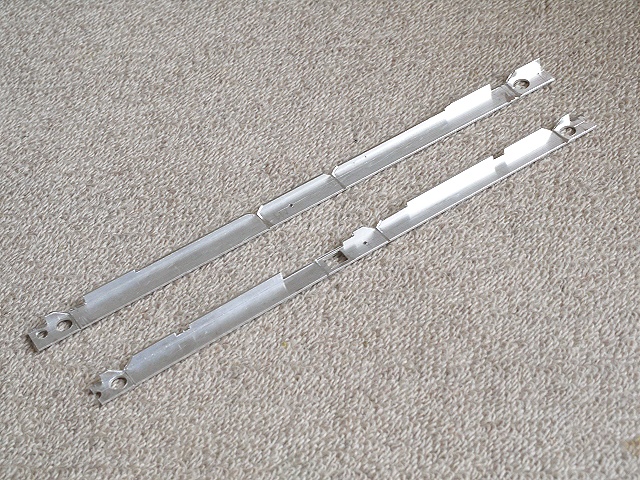
|
|
|
折り曲げ部分の加工が終わりました。 大きな山を無事越えました。 この後は背面にアルミ補強板を貼った上でM4の固定ネジを切ります。 そして電池ホルダー部分の加工を経てフレームの組み立て開始に進みます。
|
|
|
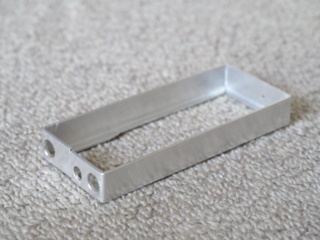
|
|
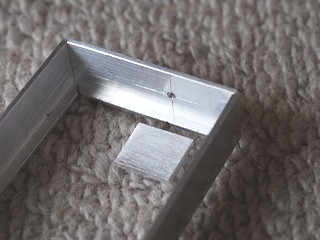
|
|
|
フレームの4箇所を折り曲げました。 若干の捩れがありますがこの程度であると後程簡単に修正できます。
|
|
背面の雌ねじを切る部分には板厚を増加するため1.5mm厚アルミ板を10 x 9mmに切断して貼り付けます。(これは貼り付ける前の様子です。)
|
|
|
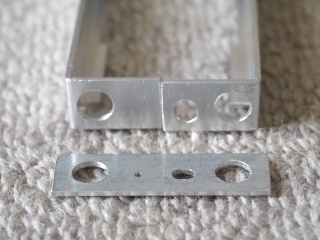
|
|
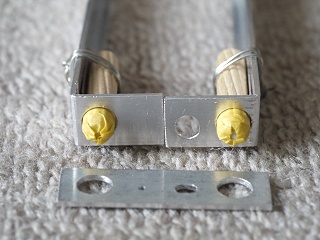
|
|
|
1mm厚アルミ板で前面パネルを切り出し、ヘッドフォーンジャックの穴2個、スイッチレバーとLEDの穴などを加工します。
|
|
アルミパネルをフレームに接着する準備です。接着位置はヘッドフォーンジャック穴が基準となるので、6φ木ダボを基準出しに使います。 木ダボの先にはマスキングテープを巻きエポキシで木ダボがフレームに接着されないようにしています。
|
|
|
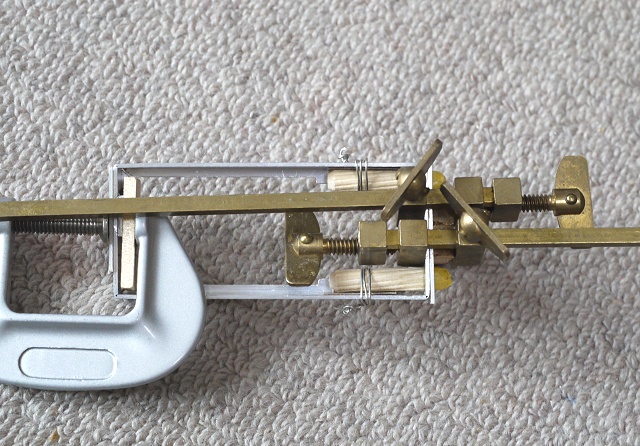
|
|
|
前面パネルの接着と背面のネジ板の接着を同時に致しました。 使用接着剤は90分硬化開始型エポキシですが、クランプやハタ金を使い12時間圧着保持しています。
|
|
|
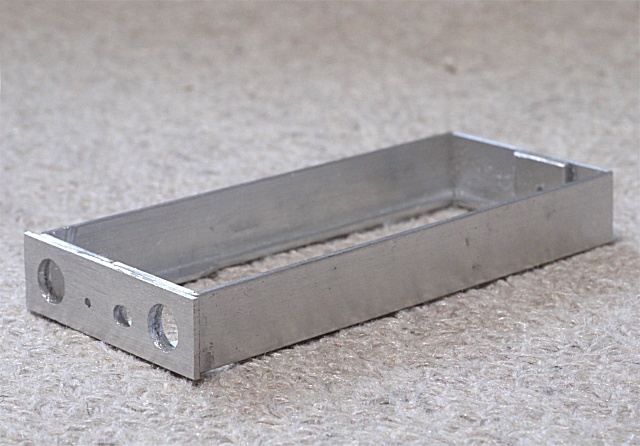
|
|
|
圧着保持を解いてからはみ出ているエポキシをカッターナイフで削り落としました。 エポキシは完全硬化してしまうと硬くてナイフで削り落としにくくなりますが、12時間後であればこのような作業が可能です。
|
|
|
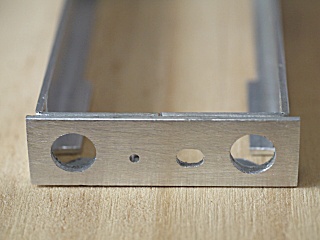
|
|
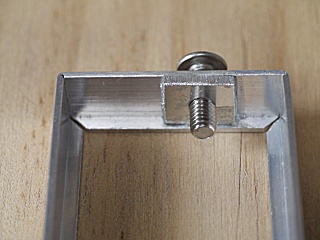
|
|
|
前面パネルに紙を貼る前にもう一度接着剤のはみ出し、傷などがないか確認しました。
|
|
背面の方は穴径を1.2φから2.0、2.5、3.2φとドリルを変えて大きくした後にM4のタップでネジ切りしました。 個々に見えるネジは長すぎますが、ケース背面の板厚に合わせて切断します。
|
|
|
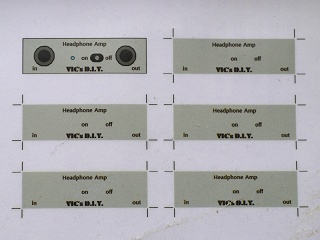
|
|
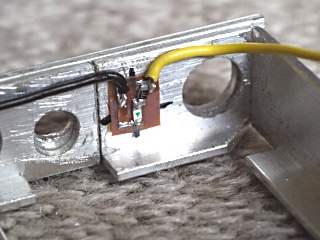
|
|
|
Excel上で描き上げた文字が入った紙パネルを複数印刷してその表面に透明スプレー塗料1回、つや消しスプレー塗料1回の塗装を施しました。 そしてスプレー糊によりアルミパネルに貼り付けます。
|
|
1.2φナイロンワイヤーを2.0mmの長さに切断し前面パネルに挿入後瞬間接着剤で固定し、LED基板を内側から当ててこれも瞬間接着剤で固定しました。
|
|
|
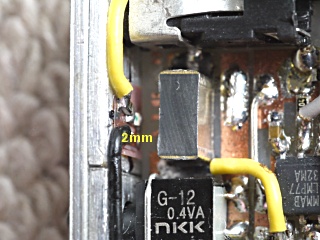
|
|
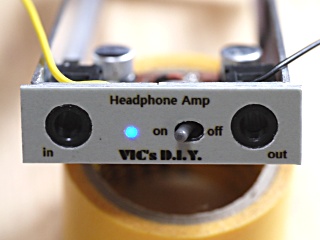
|
|
|
LED基板面と右側のコンデンサーの間は2mmしかありますんが、チップLEDのお陰でパイロットランプが実装できました。
|
|
試しに点灯したのがこちらです。 ナイロンワイヤーで光の拡散を図っていますのでシャープさはありませんが、視認性は抜群です。
|
|
|

|
|
|
フレームブロックがかなり完成に近づきました。 残るは電池ホルダーの製作と配線です。
|
|
|
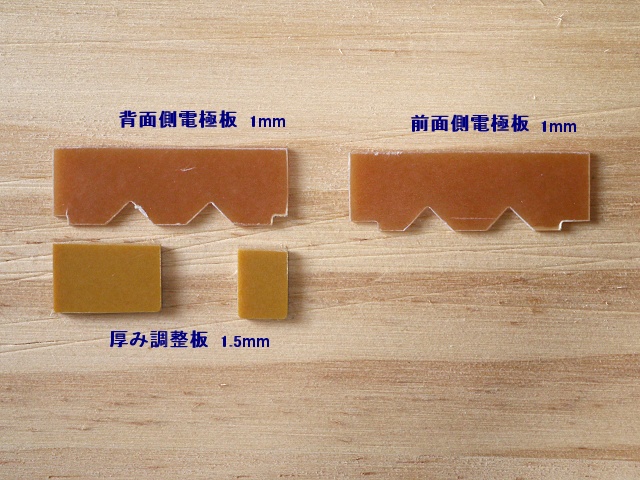
|
|
|
電極板は1mm、厚み調整板は1.5mmのベーク板から切り出します。 電極板の下側両端はフレームに乗っかって電極板の下がフレーム面と同じになるよう削り取ります。
|
|
|
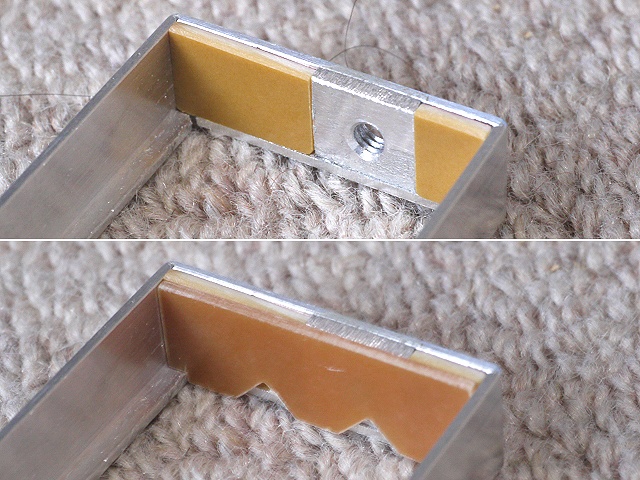
|
|
|
背面の様子はこうなります。 厚み調整板を雌ネジの両側に嵌め込み(上の写真)、その上に伝極板を載せて貼り付けます。(この写真ではまだ接着しておりません。)
|
|
|
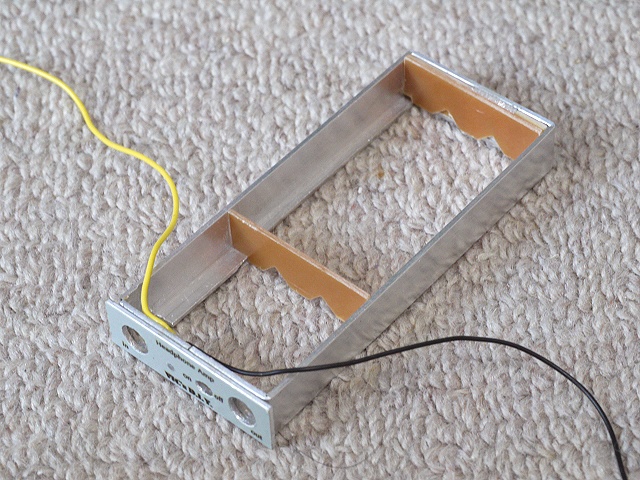
|
|
|
前側の電極板も挟み込んでみました。 電極板の上面或いは下面がフレームより飛び出ていなければOKです。
|
|
|
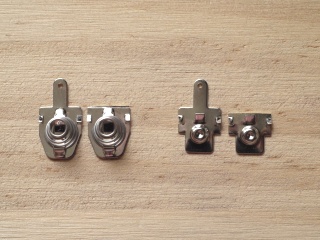
|
|
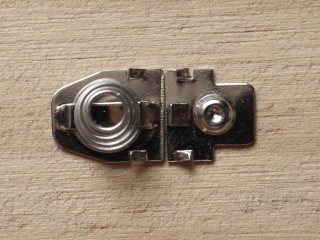
|
|
|
左側二つがマイナス電極でその左は加工前、その右は加工後です。 右側はプラス電極で左側が加工前、右が加工後です。
|
|
加工後の二つの電極を切断面で付き合わせるとこうなります。 子の時両電極の中心間の距離は10.5mmになります。
|
|
|
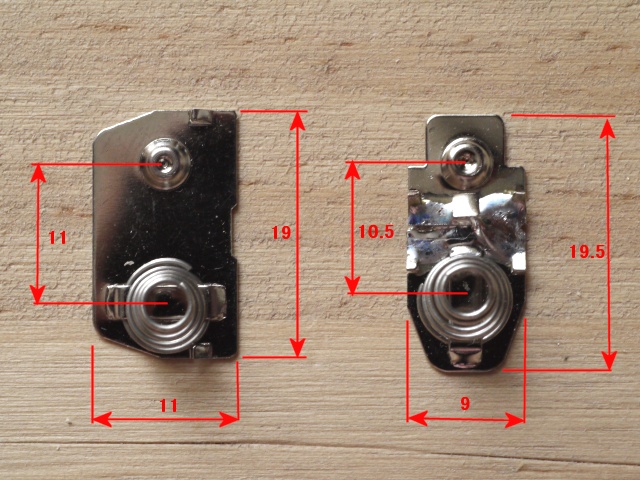
|
|
|
左がメーカー製のプラスとマイナスが接続された電極で、右がここで作った同目的の電極です。 長さが0.5mm長くなる以外全ての寸法が縮まり問題が解決されます。 長さが長くなる部分は問題になりません。
|
|
|
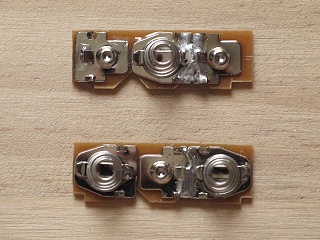
|
|
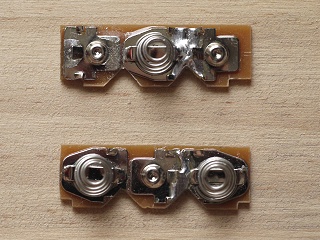
|
|
|
出来上がった電極と単電極を電極板にエポキシ接着剤で接着いたしました。 上が前側用で下が後ろ側用になります。
|
|
電極板の三角の切り欠きに被っている電極をヤスリで削り落としました。
|
|
|

|
|
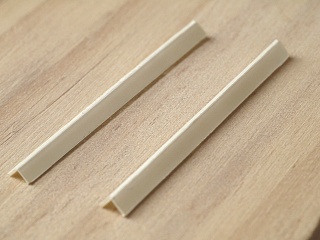
|
|
|
電池のプラスとマイナスからの引き出し線を半田付けいたします。 これらのうち下の青いワイヤーが背面から前面に配されます。
|
|
2つの電極板に裏からまたがる3角板。 0.5mm厚塩ビ板をへの字に曲げて内側をスプレー塗料で塗りました。(外側を塗ると接着面のため具合が悪いので。)
|
|
|
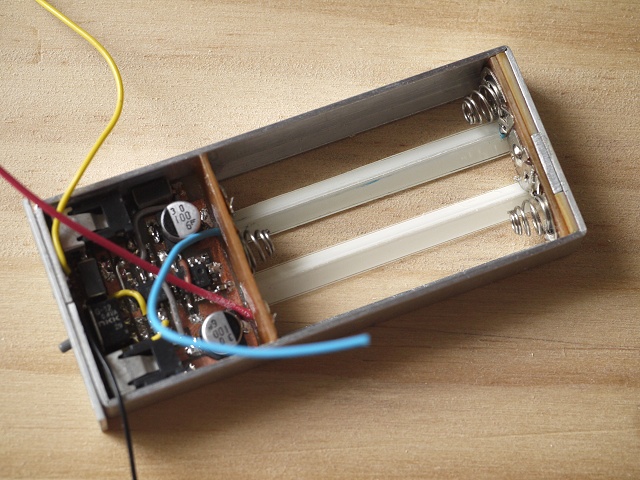
|
|
|
電極板を所定の位置に瞬間接着剤で貼り付け、その後背面から三角板を渡して接着しました。 そして青のワイヤーを三角板の裏に隠しながら前側に通します。
|
|
|
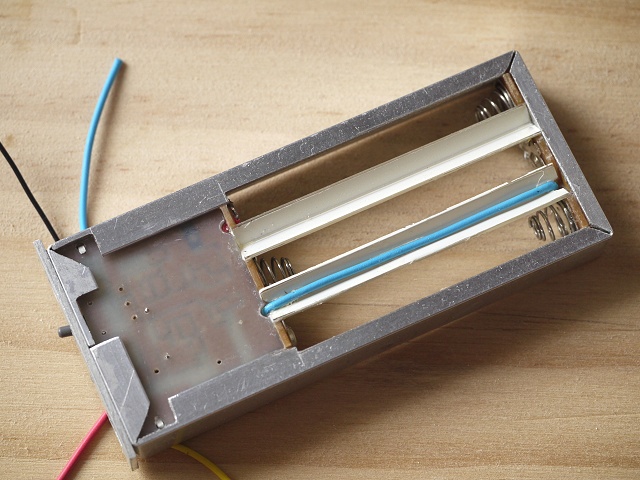
|
|
|
裏側はこんな具合です。 ワイヤーが上に飛び出ないように、三角板の底に瞬間接着剤で固定しています。
|
|
|
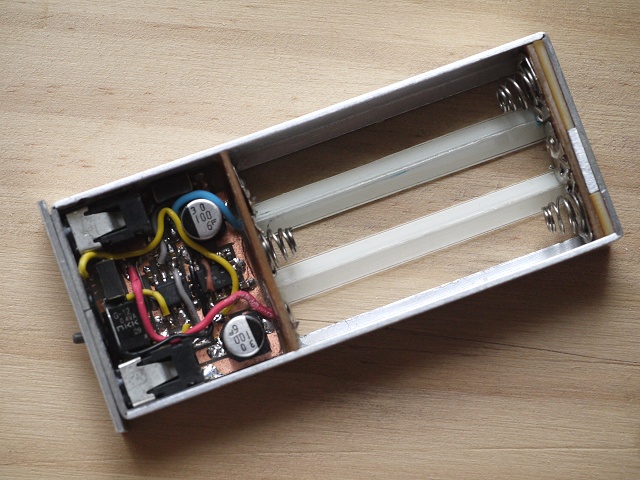
|
|
|
電池のプラとマイナスのワイヤー、そしてLEDからのワイヤー2本の配線を済ませ、組込みは完了いたしました。
|
|
|
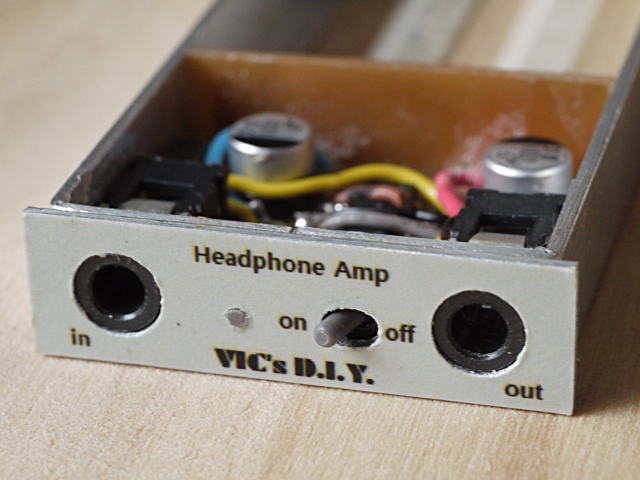
|
|
|
遅ればせながら前面パネル面への文字入れはこんな具合です。 on/off と描かれた左側のポチがLEDの光拡散のためのナイロンワイヤーです。 問題なく動作はしてますが、テストは次回です。
|
|
|
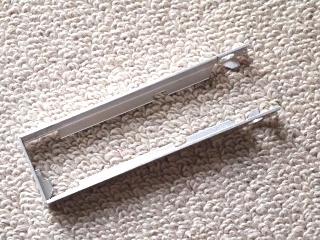
|
|
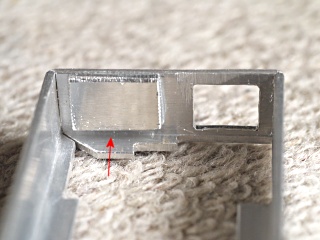
|
|
|
フレームをコの字型に折り曲げました。 更に両先端を内側に曲げないといけないのですが、曲げ加工後の予測寸法を確認してから実行します。(一度曲げたら元に戻せないので。)
|
|
固定ネジの補強板(10 x 7.2mm)をエポキシ接着剤で貼り付けました。 矢印の先に基板が挿し込まれるので、1.2mm程の隙間を残します。
|
|
|
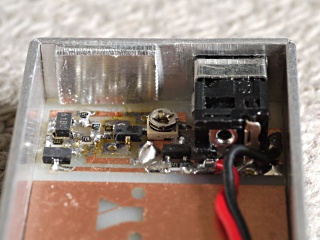
|
|
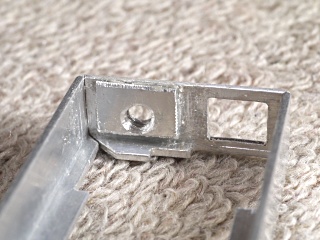
|
|
|
接着後12時間寝かせてから基板を差し込んで不具合がないかどうか確認しました。
|
|
そしてM4のハンドタップで雌ネジを切り込みました。 これらは3つのヘッドフォーンアンプに共通した加工作業です、
|
|
|
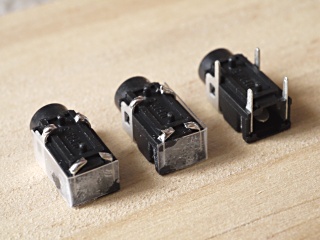
|
|
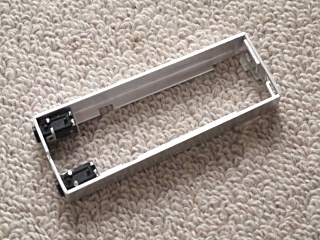
|
|
|
ヘッドフォーンジャックの予備加工です。 先ず端子を1〜1.5mm詰めて内側へ曲げて半田揚げします。 更に1個のジャックの左側面、背面、底面及びもう一個のジャックの右側面背面底面を0.2mm厚塩ビ板から切り出して瞬間接着剤で貼り付けます。(不要な電気的な接触、ショートの防止目的) 右端が加工前のジャックです。
|
|
それらのヘッドフォーンジャックをフレームの前内側に瞬間接着剤で固定しました。 子の時フレームとジャック横の間に0.2mmの塩ビ板が挟まれます。 ヘッドフォーン端子の上面が1.0mm位フレーム面から引っ込んでいることを確認します。
|
|
|
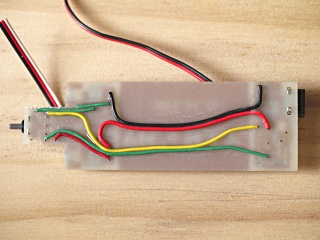
|
|
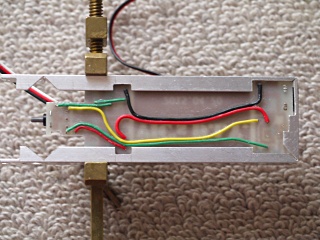
|
|
|
基板裏の最終処理です。 LED配線の3本を取り除き、残る4本のアンプと電源ブロックを結ぶワイヤーは、交差をさせない!、中央に寄せる!の2条件を守りながら基板面に密着させた状態で瞬間接着剤にて固定します。
|
|
裏側処理が終了した基板をフレームに挿入し電気的な不具合(フレームとのショート)が起きないかどうかの確認を致します。
|
|
|
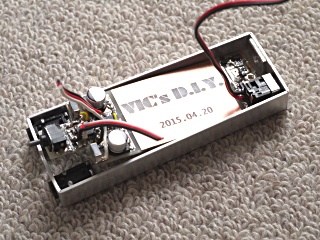
|
|
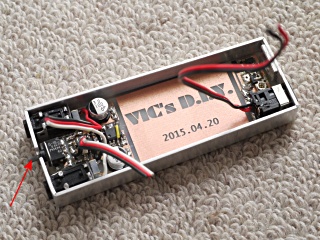
|
|
|
ここから4枚の写真は基板の装填方法です。 先ず基板の前側を上に上げた状態で後ろ側を差し込みます。
|
|
完全に差し込んだらフレームの前側を3mm程開いて、徐々に基板の前側を落とし込みます。(スイッチのレバーは赤矢印のフレームの突合せ部分の隙間を通ります。)
|
|
|
落とし込む途中でヘッドフォーンジャックの背面は0.1〜0.2mmの隙間を基板との間に保ちながら入るはずです。
そうでない時は一旦作業を停止して基板の当る部分を削ってやる必要があります。(加工精度で起きる問題です。)
|
|
|
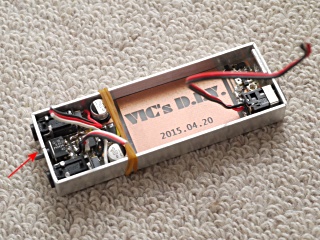
|
|
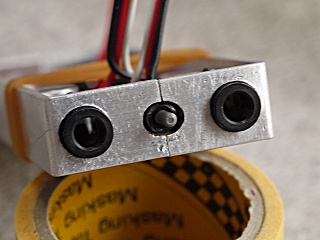
|
|
|
基板が完全に落とし込まれたらフレームの先を突き合わせることが可能になります。(赤矢印先)
|
|
突き合せた前面はこんな感じです。 突合せ部分で段差・食い違いが出来たり隙間が生じる場合には調整する必要があります。
|
|
|
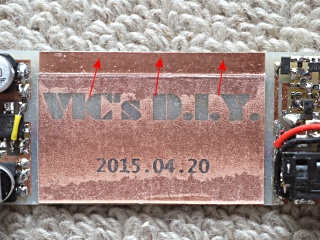
|
|
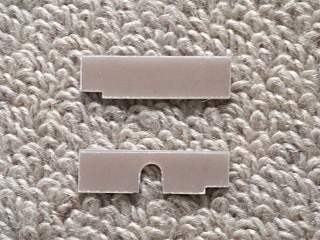
|
|
|
電池が入る部分の大半を1mm厚塩ビ板で覆うよう両面接着テープで貼り付けました。 よって矢印部分は1mmの深さの溝になり、ここを3本のワイヤーが後程通ります。
|
|
電池室の仕切り板は1mm厚グラスエポキシで作りました。 上が前側で下が電池からのケーブルパスの欠き込みがある後ろ側です。
|
|
|
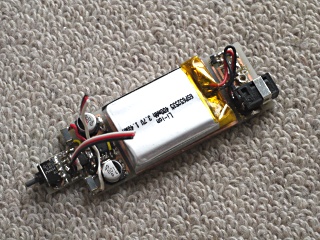
|
|
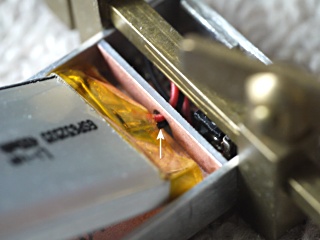
|
|
|
基板の電源ブロックに電池からのリード線を繋ぎました。(電池は予め充電しておきます。)
|
|
後ろ側の電池室仕切り板を挿入しハタ金で軽く圧着保持しています。 ケーブルパスを電池ワイヤーが通過しています。 この状態で仕切り板を瞬間接着剤で固定します。
|
|
|
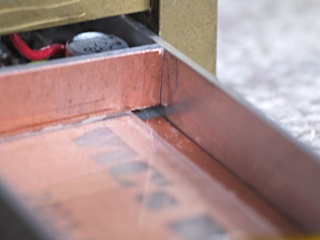
|
|
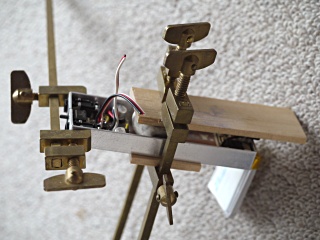
|
|
|
前側の仕切り板を同様に接着しました。 中央に隙間が見えますが、ここを3本のワイヤーが後程通ります。
|
|
これで全ての予備加工が終わりましたので最終的に基板を挿入し、ハタ金で保持した状態で瞬間接着剤にて基板をフレームに固定しました。
|
|
|
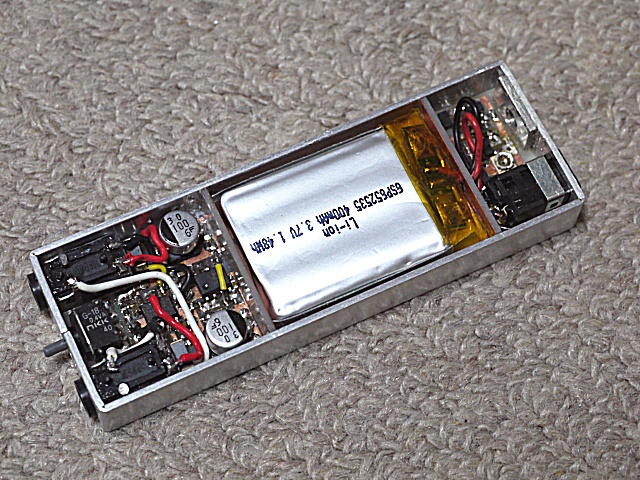
|
|
|
組み込みがほぼ完了した本体です。 イヤーフォーンとiPod Nanoを繋いで動作を確認いたしました。 残るhは前面/背面パネルの製作と取り付け、そして文字入れでその後実働テスト、電池の寿命テストとなります。
|
|
|
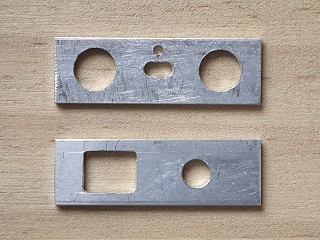
|
|
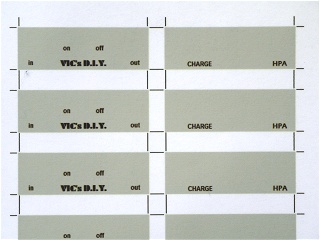
|
|
|
前面パネルと背面パネルを切り出し加工しました。 それぞれ1mm厚のアルミ板を使っています。
|
|
そして薄手のマット紙にExcelで描いた文字及び背景を印刷しました。 貼り直しが起きても問題ないよう4枚ずつ印刷しています。
|
|
|
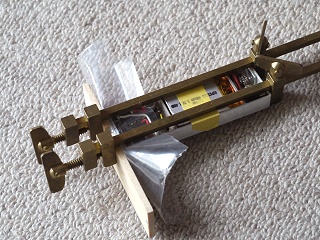
|
|
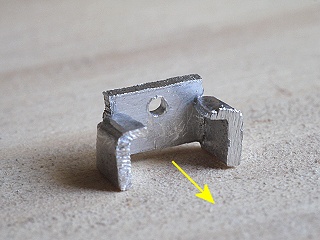
|
|
|
それにスプレー糊を吹き付けてアルミパネルに貼った後に穴あけをしてから、フレームにエポキシ接着剤(90分硬化開始型)で接着し圧着保持しました。
|
|
一方LED基板を後方に7mm、下に1mmずらして固定するためのゲタを1mmアルミ板で作りました。 矢印が前方ですが、電源スイッチにまたがるように載せて接着します。
|
|
|
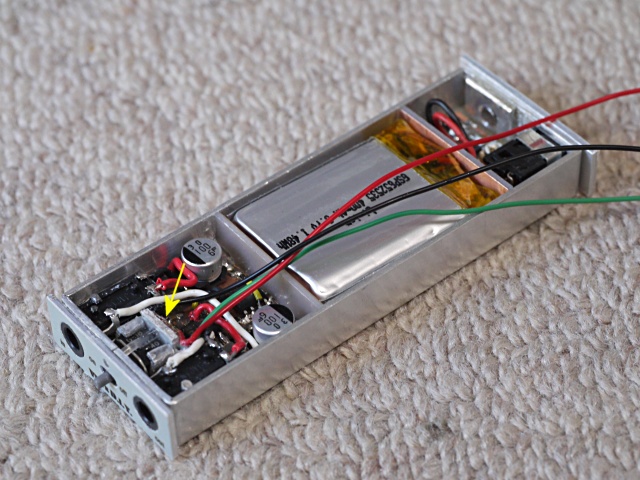
|
|
|
ゲタにあけた穴に2つのLED(赤と緑)の光が通る位置にLED基板を接着し、ゲタの丸穴にナイロンワイヤーを差込み、その反対側をパネル面の穴に通してからゲタを電源スイッチに載せます。 矢印の先が嵌め込んだゲタです。
|
|
|
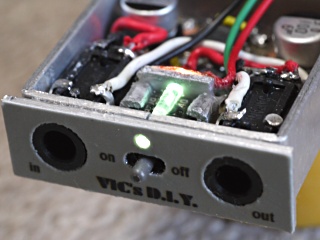
|
|
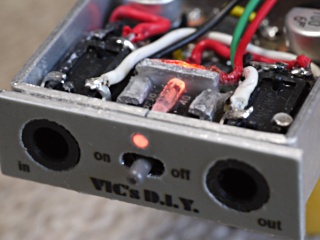
|
|
|
赤のリード線には2.7KΩ、緑のリード線には1.2KΩを接続して、2.7〜4.5Vの電圧を加え確認します。 これは4.5Vの時です。
|
|
こちらは3.0V以下に下がった時で緑は消灯して赤のみが点灯しています。 実際の点灯の仕方とちょっと違いますが、ナイロンワイヤーで旨く光を導けています。
|
|
|
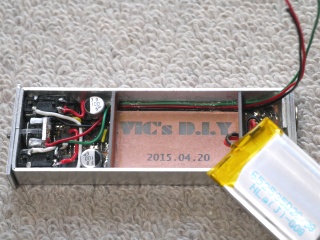
|
|
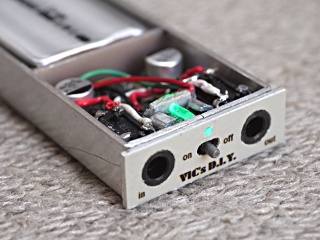
|
|
|
LEDからの3本のワイヤーを電池ホルダーに確保したケーブルパスを通し、背面の電源ブロックに導きました。
|
|
電源ブロックの所定の位置に3本のワイヤーを半田付けし、電源スイッチを入れました。 現在電池電圧は3.7Vくらいあり緑のみの点灯です。
|
|
|
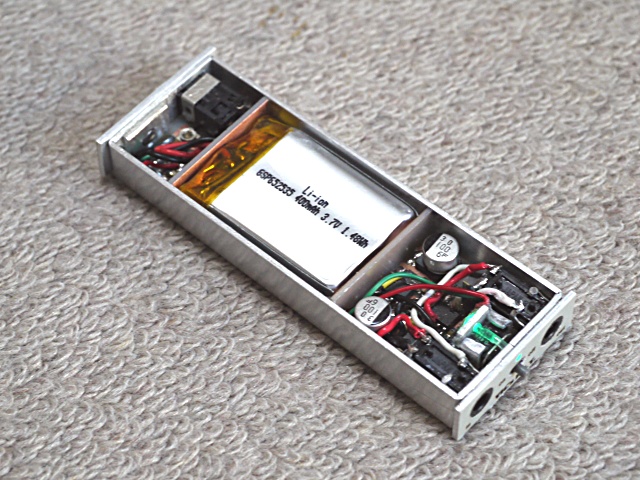
|
|
|
LEDびよる電圧表示はキャリブレーションは必要ですが、電池の配線を外せませんので後程魔法を使って実施します。 それを除けばヘッドフォーンアンプ本体はこれで完成となります。
|
|
|
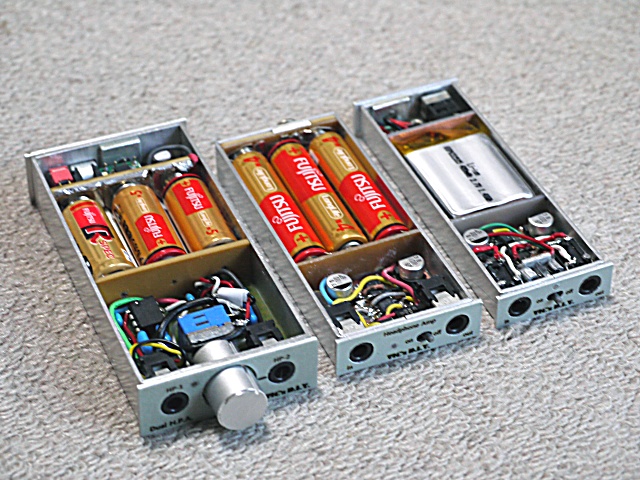
|
|
|
一挙に製作した左から、2ヘッドフォーン駆動型アンプ、単四電池型アンプ、そしてリチウムイオン充電池型アンプです。
|
|
|
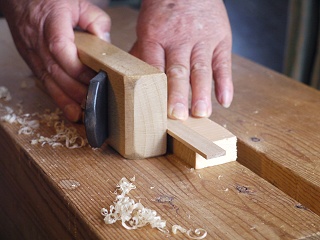
|
|
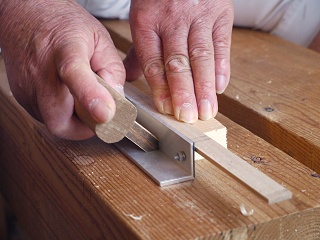
|
|
|
側板の幅は加工精度+0.1mm、-0.0mmで仕上げます。 いきなり切り出しでその精度を出すのは無理ですから先ずカンナで直角出し削りにて寸法を出して、直角出しヤスリで仕上げます。 それらの間に数回ノギスで確認しますので、精度出しに苦労することはありません。
|
|
|
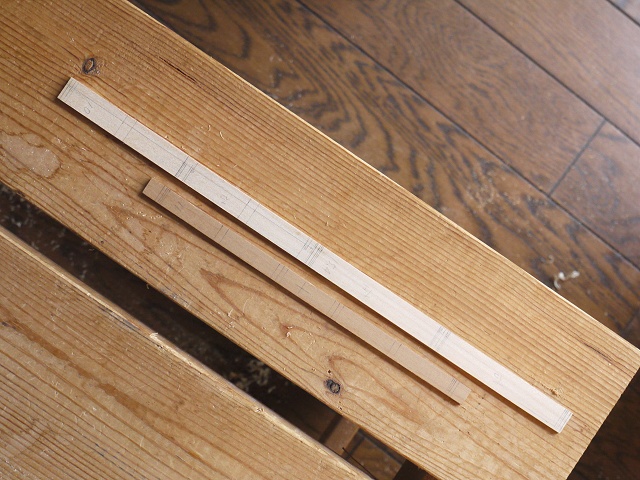
|
|
|
長くて白っぽい材料からは2出力型とリチウムイオン充電池型の側板を切り出し、短くて茶色い材料はコの字型の側板を1枚板から切り出します。 既に墨線を引き終わっており、トリマー加工を済ませてから最終的な長さで切断します。
|
|
|
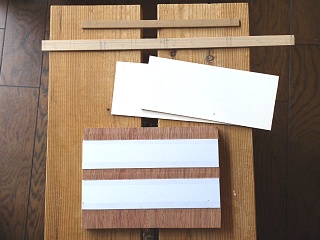
|
|
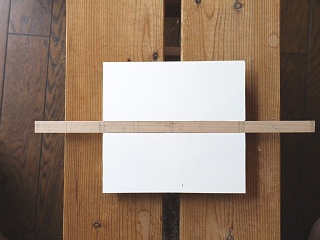
|
|
|
トリマー加工に使うジグの組立。 一番下の18mm合板に厚み調整の0.5mm厚ボール紙を2列に貼りました。 隙間の所に側板の材料を置きます。
|
|
左の白っぽい板は2.4mm厚化粧合板ですが、それで材料を挟むように置きます。 こうすると材料と白い板の表面はほぼ同じ高さになります。
|
|
|
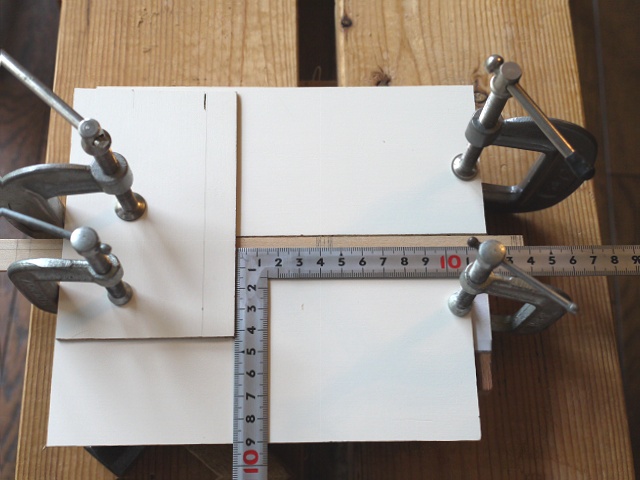
|
|
|
左手に新たに載った白い板はトリマーのガイド板になりますが、ガイド板の位置調整を慎重にした上で左右をクランプ2本ずつで固定します。 このガイド板の取り付け位置精度で加工精度が決まってしまいますので、充分に時間を掛けます。
|
|
|
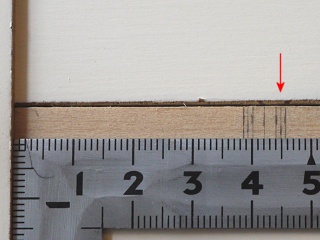
|
|
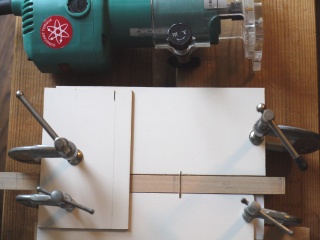
|
|
|
赤矢印先の線が切削の中心になるよう設定した状態です。 私の使っているリョービの電動トリマーの台座は1辺が45mmありますので、ガイドとの距離が正確に45mmであれば、トリマーの刃の中心はここを通ります。 右の写真は切削終了後で押さえ板も共切りしています。
|
|
|
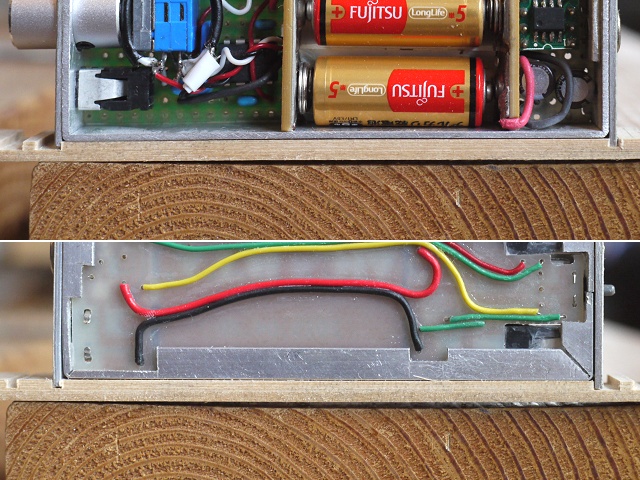
|
|
|
4mm幅(前側)と1.6mm幅(後側)が終わりましたので念のためにフレーム本体を当てて確認しています。 上の写真は左が前で、下の写真は右が前側になっていますが、何れも収まりに問題は無さそうです。
|
|
|
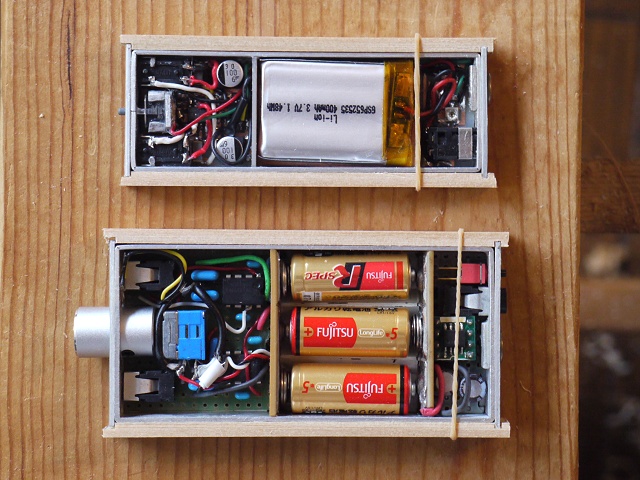
|
|
|
繋がっていた側板を切り離してフレーム本体に当ててみました。 ここではゴムバンドで挟んでいますが、次の工程で背面パネルと側板をエポキシを使って接着します。 以上が2出力ヘッドフォーン型とリチウムイオン充電地型の作業です。
|
|
|
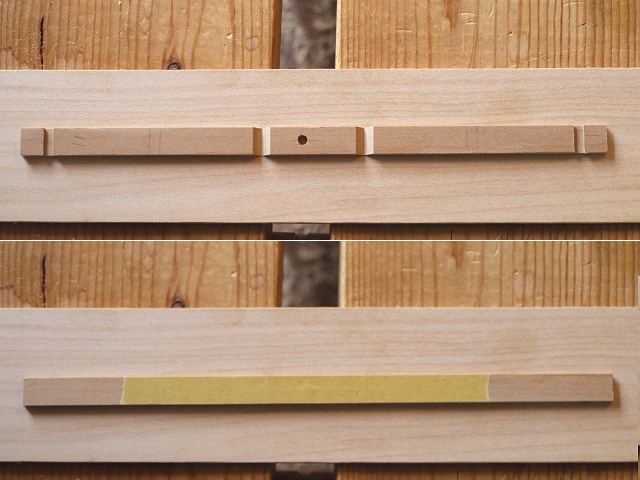
|
|
|
単四アルカリ乾電池型では一枚板に90度V溝ビットで深さ3mm(板厚と同じ!)の溝を角部分2ヶ所に彫ります。(上) 但し何もしないと3つにばらばらに切り離されてしまうので、切削位置の裏側にはマスキングテープを貼って皮一枚繋がっている状態にしてから切削します。(下)
|
|
|
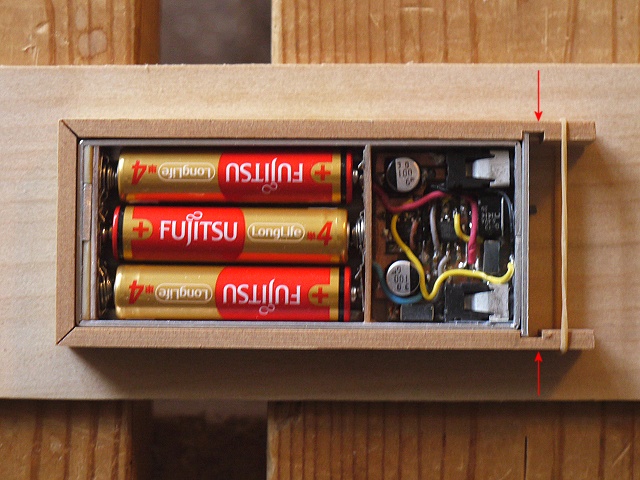
|
|
|
試しに加工の終わった材料を折り曲げてフレーム本体に当ててみました。 この後矢印のところを切断してやります。
|
|
|
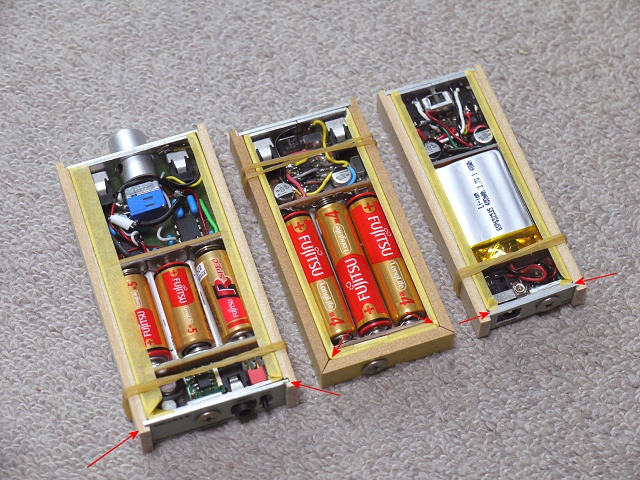
|
|
|
背面パネルを側板に固定、または側板を背面でコの字型に接合の準備です。 接着部分は矢印の先ですが、接着剤でフレームが側板に接着されないようマスキングテープでフレームを覆っています。
|
|
|
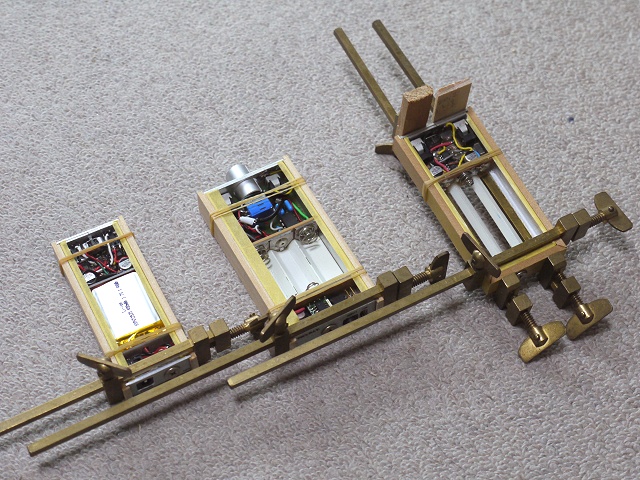
|
|
|
接合面にエポキシ接着剤を塗って接着しハタ金で圧着保持しています。 接着面積が小さくて弱いため、24時間放置して完全硬化させてから次の作業に進みます。 右端だけ前後方向にもハタ金を2本使っていますが?
|
|
|
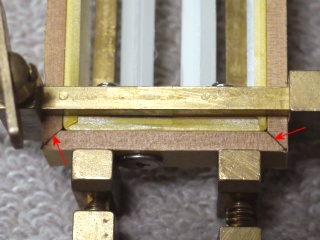
|
|
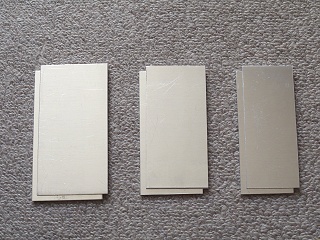
|
|
|
矢印部分の密着度を上げるためです。!
|
|
1.5mm厚アルミ板から上下の板を切り出しました。 最終寸法よりも縦・横0.5mm大きく切断してあります。
|
|
|
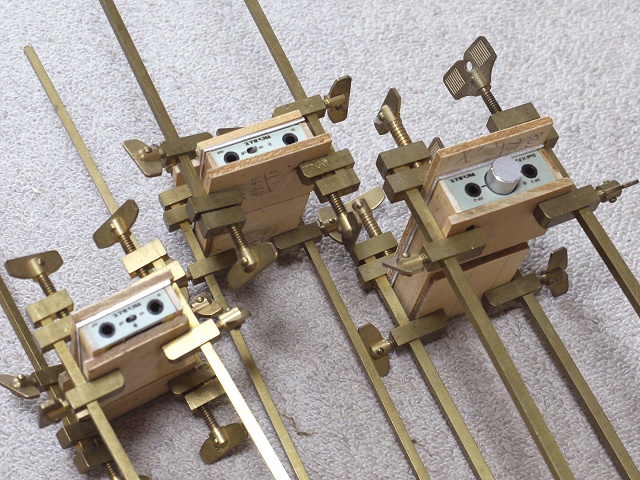
|
|
|
そして底側の1枚をエポキシ接着剤で貼り付けて圧着保持します。(上の状態) 2時間後(半硬化状態)に中身を抜き取って更に22時間寝かせ、完全硬化させました。
|
|
|
註) 2時間後の半硬化状態で中身を抜き取る理由は、若しも内部でエポキシが滲み出ているとしたら半硬化状態で本
体を抜き取らないと本体は内面に接着して抜けなくなってしまう可能性が極めて高くなります。
滲み出たエポキシは完全硬化後にナイフで削り落とします。 アルミや木材料を傷つけるような荒っぽい作業になり
ますが、完成後に見える部分ではなくなるので、気楽に実行出来ます。
|
|
|
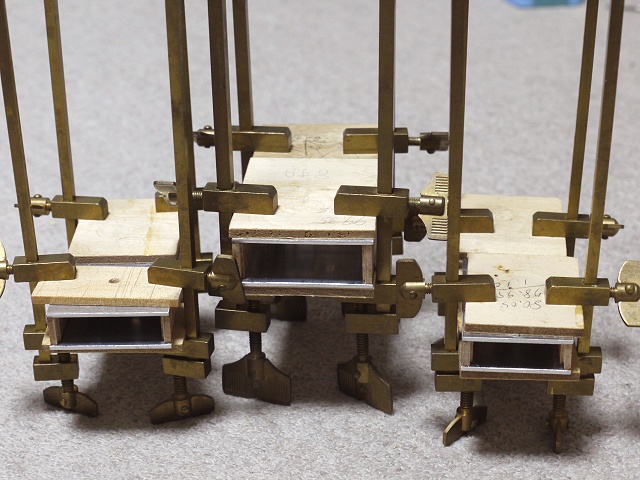
|
|
|
中側に滲み出ているエポキシをナイフで完全に削り落とし、本体がスムーズに出し入れできることを確認後に上側のアルミ板を接着しますが、ハタ金で圧着保持後に中身を抜いてしまいます。(上の状態) そしてティッシュペーパーを薄板に巻いてケースの中に突っ込み、上板との接着面に滲み出ている接着剤を拭き取ります。 そして24時間寝かせます。
|
|
|
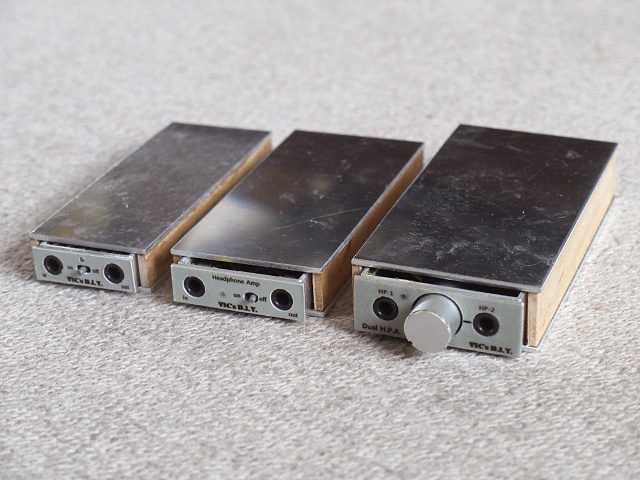
|
|
|
ケースの貼りあわせ後にアンプ本体を挿入できることを確認中です。 ご覧のようにアルミの天板・底板はアガチスで作った側板の面より僅かに突出しています。 この突出を金工ヤスリ中目でアガチス面まで削り落とします。 その後替刃式ヤスリでアルミ板の厚み面が均等に見えるまで削って(最初は厚みが1.5mm以上で不規則に見える。)、最後に#400サンドペーパーで仕上げ研摩します。
|
|
|
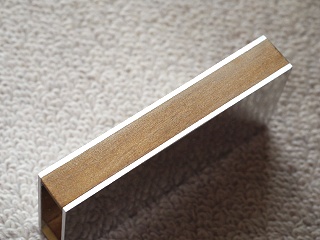
|
|
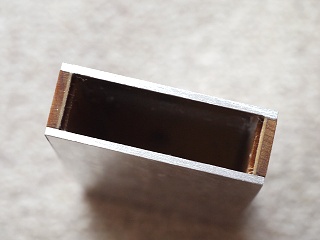
|
|
|
アルミ板の角の面取りをしました。 板厚1.5mmがきりっと見えます。 無論アルミ板とアガチスの板の間の段差はありません。
|
|
なんとなくアルミ板が1.5mmより厚く見えますがバリが残っているためで、適切な面取りを済ませるときりっとした見え方に変ります。
|
|
|
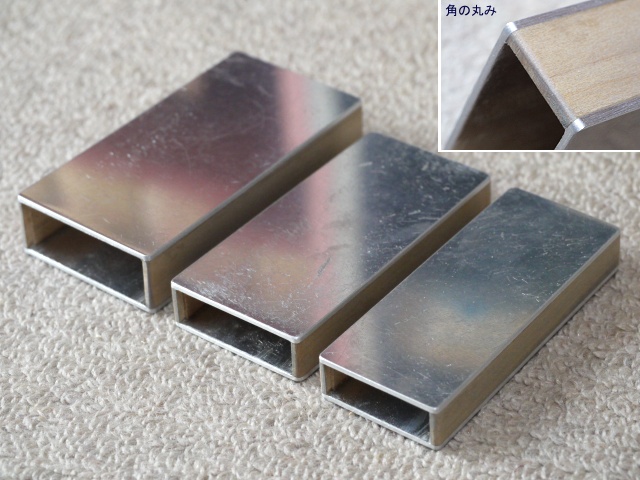
|
|
|
アルミ板のでっぱりの削り落としと替刃式ヤスリ及び#400サンドペーパーによる仕上げ研摩を経て、面取りと角のR成形(右上写真)が終わりました。 残るは上面と底面のヘヤーライン加工です。
|
|
|
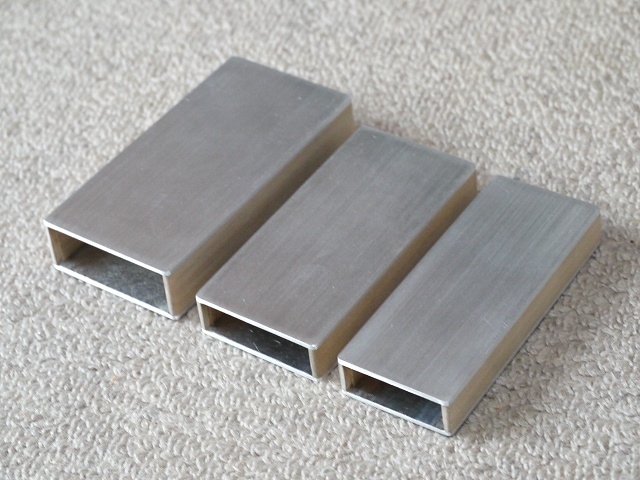
|
|
|
ヘヤーライン加工は#240サンドペーパーをハンドサンダーに取り付け沿わせて前後方向とヘヤーラインが完全に平行になるようにして研摩します。 アルミ板についた細かな傷が消えてしまうまで根気良く削り込み、終了したら水洗いしてアルミ滓を完全に洗い落とします。(特に内部に滓が残らないよう注意!)
|
|
|
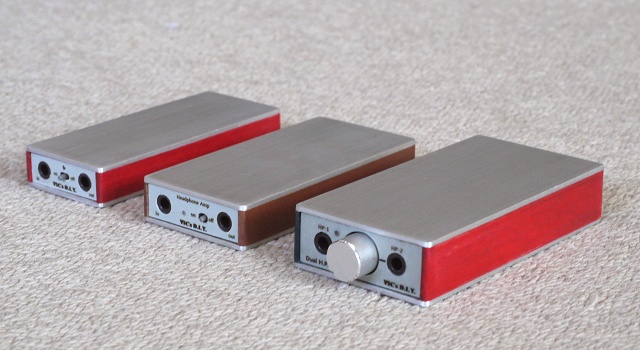
|
|
|
塗装工程は、水性ポアステインを2倍に希釈して3回塗りで仕上げた後に(各着色の間に#400で研摩)水性ウレタンニス透明クリヤー2回塗り、水性ウレタンニスつや消しクリヤー1回塗り(各塗装の間に#400で研摩)としています。
|
|
|
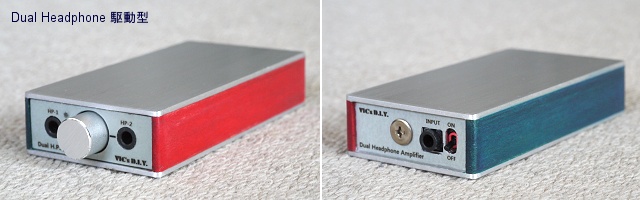
|
|
|
こちらはDual Headphone AMPとした物で、家内と一緒に使うのですが、家内が使う側をローズピンクで(ツマミで音量調整が可能)、私が使う側はマリーンブルーで(音量調整は外部)仕上げました。
|
|
|
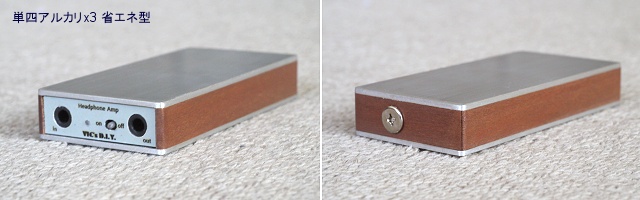
|
|
|
こちらは150時間以上も連続動作時間を有する省エネ型ですが、チーク色のポアステインで仕上げました。 この色にしたのはある購入しようかな?と考えているファッショナブルなヘッドフォーンの革貼りの色に合わせてやろうとしたものです。 歩きながら使う時はバッグの中にしまうのがベストでしょう。
|
|
|
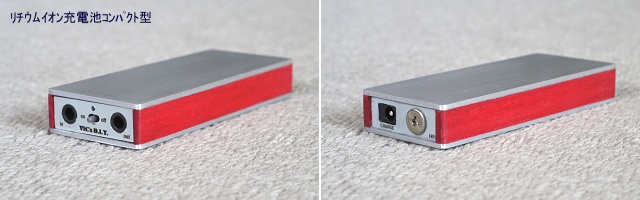
|
|
|
コンパクト型ですが重量も65gしかないので、iPod Nano共々シャツの胸ポケットに入れてもだれて下がるようなこともなく快適に使えます。 歩きながら使う本命になりそうで、最も使用頻度が多いと思われます。
|
|
|
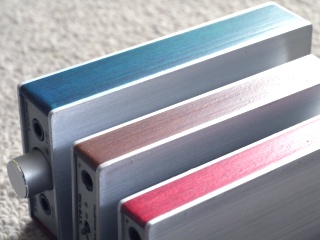
|
|
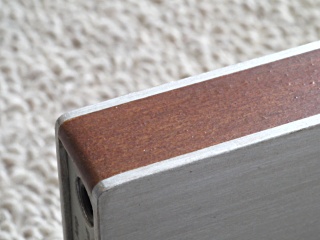
|
|
|
全てに言える共通点は表面の光り方で、半つや消しですからこのようににぶーい反射光を有しており、気品のある感じです。 アルミ面もぎらぎらした安っぽさがなく渋さを持っています。
|
|
その面をクローズアップしてみました。 しっとりした肌触りがあり高級感があります。
|
|
以上で3台のヘッドフォーンアンプが完成いたしました。 2ヘッドフォーン駆動型を製作開始したのが1/9で2月に入り2つを追加したので約9ヶ月も要したわけですが、初期の目論見、目標は充分に達成できたと考えています。Copyright (C) 2001-2019, Vic Ohashi All rights reserved.