|
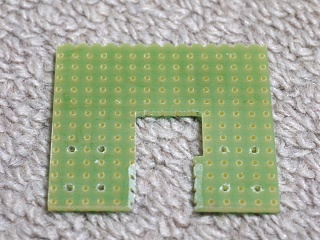 |
|
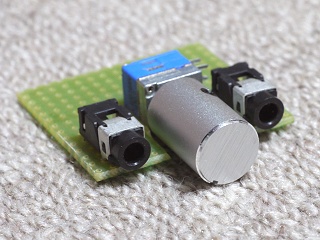 |
|
|
基板の切り出しと寸法出しが終わりました。 真ん中の欠き込みはVRを埋め込む部分で手前両側には8箇所の穴を1.2φに広げてあります。
|
|
3.5φヘッドフォーンジャックとVRを嵌め込んで、ツマミも固定してみました。 ツマミはパネル内に埋め込まれます。
|
|
|
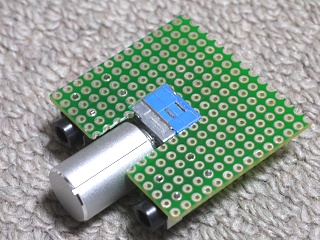 |
|
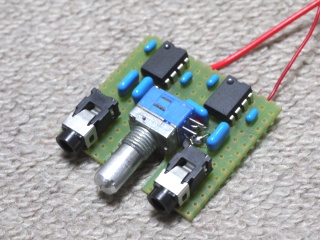 |
|
|
基板をひっくり返すとこんな具合です。 VRの面と基板裏面は面一になります。 この状態で基板とVRの接触部分に瞬間接着剤を流し込んで完全固定します。
|
|
配線途上ですが上面に取り付けられる部品は全て付いています。 小さな青い粒がゾーベルフィルター用コンデンサーです。 普通はこの中にあるべき抵抗が全く見当たりません。
|
|
|
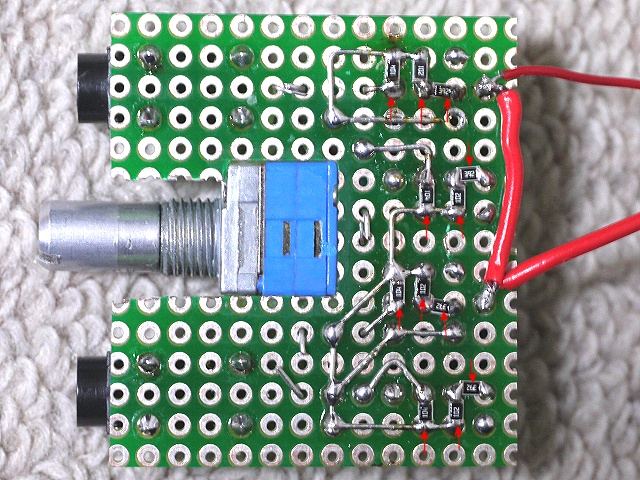 |
|
|
基板の裏側に12個のチップ型抵抗(100KΩ、1KΩ、3.9KΩ)が半田付けされています。 ゾーベルフィルター用の抵抗だけはまだ付いていません。 実装密度を高めるために今回始めてトライしましたが、非常に手間取るもののその効果は絶大だと思います。
|
|
|
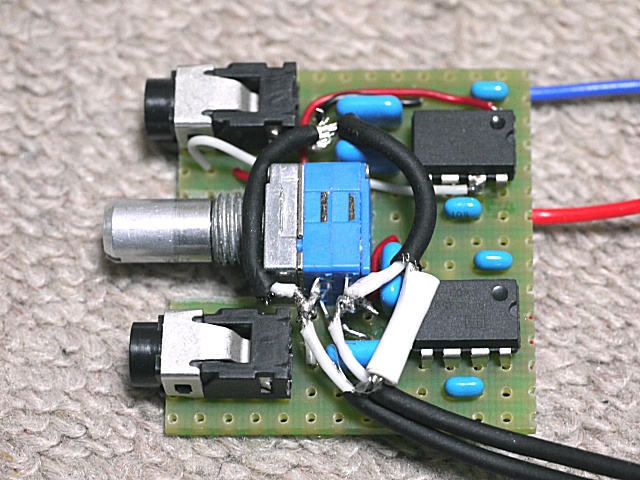 |
|
|
その後配線を進めて全てが終わった上面です。 通常は裏面に施すジャンパー線の一部は、裏面の突出量を抑えるため上面に施しています。 ミニヘッドフォーンジャック2個とその間のVR周りは最も詰めこんだ感じになります。
|
|
|
 |
|
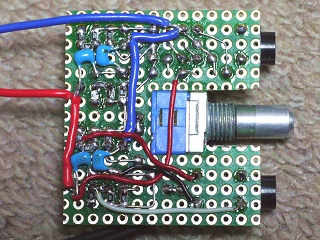 |
|
|
信号線となるシールド線は2芯シールドを使うと直径が2.5mm以上になり隙間にうまく収めにくくなります。 そこで直径1.6mmの単芯シールド線を2本並べて使います。 言うまでも無くこれで幅3.2mmで高さ1.6mmのスペースを喰う様になります。
|
|
基板の裏は最終的にこんな感じになりました。 前の写真に対してジャンパー線とバイパスコンデンサーが追加されていますが、電気的には問題なくてもかなりババッチクなってしまいました。
|
|
|
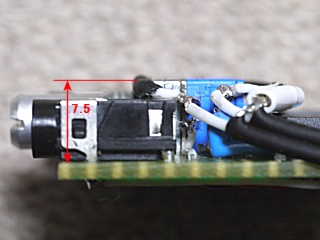 |
|
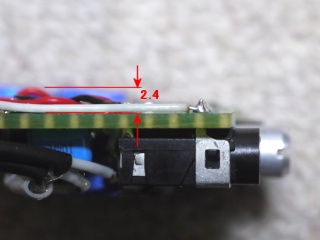 |
|
|
基板上面の出っ張りはVRの7.5mmを上限としています。 ケースのアルミ板はこの上2.6mmの位置に来るので、アルミ板に電気的に接触する心配はありません。
|
|
一方裏側の出っ張りは最大で2.4mmあります。 これは2本のビニール線が交差する部分なのですが、これを減らす名案がありません。
|
|
|
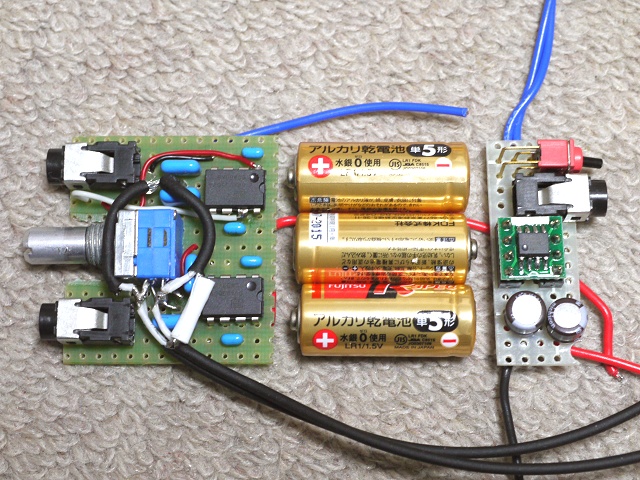 |
|
|
出来あがった2つの基板と電池3本を所定の位置関係に並べました。 この後アルミフレームの製作に進むのですが、基板上面と下面の隙間をどうするかをはっきりさせないとなりません。
|
|
基板裏側の突出部分はケースのアルミ板の面に最小0.1mmまで接近する計算です。 この突出部分は線材のビニール被覆部分なので電気的な接触がいきなり起こるわけではありませんが、薄いプラスチックシートを貼って電気的な接触はどんな状態でも起きないようにするか、基板上面には2.6mmの隙間がありその内0.6mm程度を裏面に回せばプラスチックシートを貼ることなく電気的な接触を回避できます。
|
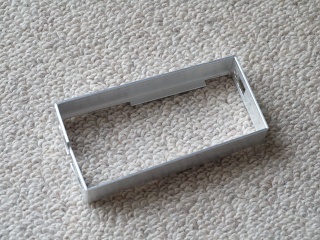 |
|
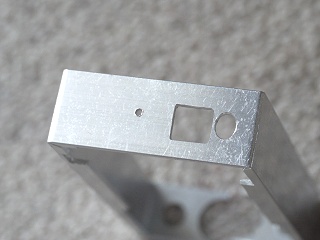 |
|
|
フレームを折り曲げた状態です。 こんな角度で見ている限り何も問題は無さそうですが?
|
|
背面の右端の電源スイッチの首の部分が出る穴は少々小さくて首が通りませんでした。 現物合わせで削ります。
|
|
|
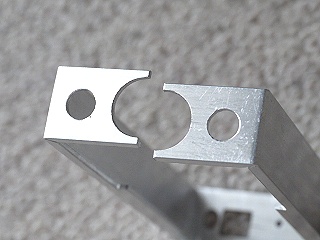 |
|
 |
|
|
前側はご覧の通り捩れがあり、うまく突合せが出来ませんので調整が必要です。
|
|
但しミニフォーンジャックの穴とツマミの穴は位置精度もよく問題ありません。 慎重に進めた甲斐がありました。
|
|
|
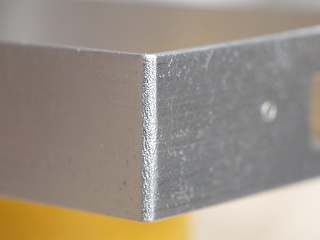 |
|
 |
|
|
問題は背面の折り曲げた部分です。 この写真では角が引き伸ばされたためにぶつぶつの凹みが出来ていますが、均等に出来ており正常です。
|
|
こちらは問題の角で上から下まで細い溝が出来ています。 これは極端に薄くなっている部分であり、更に折り曲げたり曲げ戻すような力が掛かるとポロリと折れてしまいます。
|
|
|
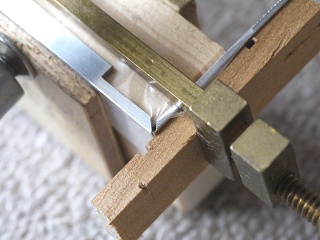 |
|
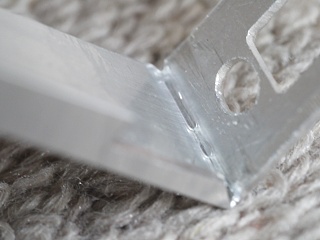 |
|
|
そこで問題の角の内側にエポキシ接着剤を塗り込み溝を接着剤で埋めて角を90度に保持し1晩寝かせました。
|
|
接着剤が硬化した後の内側の様子で、はっきりとは見えませんが一応エポキシで溝は埋め立てられています。
|
|
|
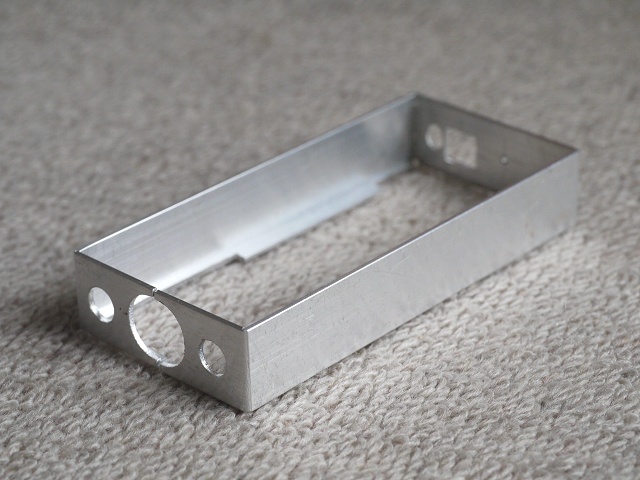 |
|
|
フレームの捩れも修正して曲げた後の調整作業が終わったフレームです。 捩れは完全に調整できましたが、本来の今週の目的であった雌ネジ切りは前面にパネルを貼りフレーム強度が更に上がった後に先送りします。
|
|
|
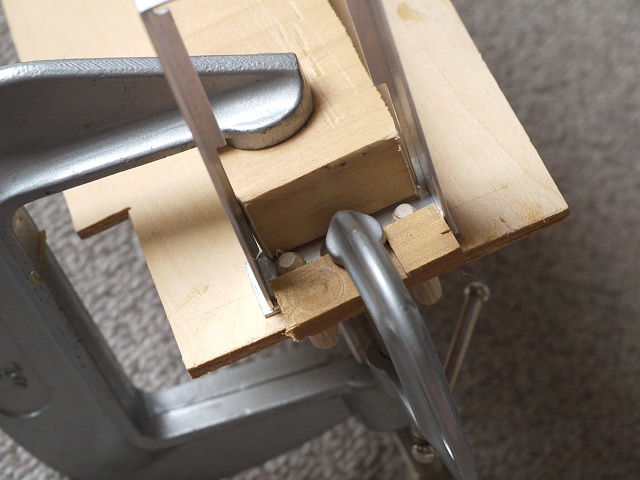 |
|
|
前面パネルをフレームにエポキシ接着剤(90分硬化開始型)で接着し圧着保持中。 お約束事で24時間保持時間を取ります。 小さなクランプの両側に見える小さな丸が位置合わせに使った6φの木ダボです。
|
|
|
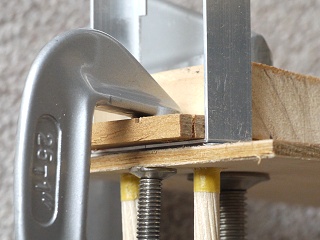 |
|
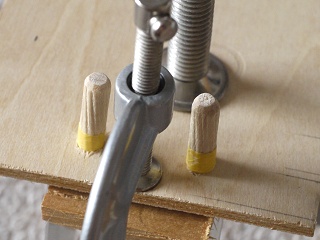 |
|
|
それを横から見るとこんな具合で木ダボを使っているのが良く判ります。 エポキシで木ダボがくっ付いてしまうのを防止するマスキングテープも黄色く見えます。
|
|
上の写真をひっくり返すとこんな具合です。 ここに見える5.5mm厚合板に6φの貫通穴を25.4mm間隔で2個あけておき、この面から木ダボを差込んでその先にフロントパネル、エポキシを塗ったフレームを通して圧着し位置出しをしたわけです。
|
|
|
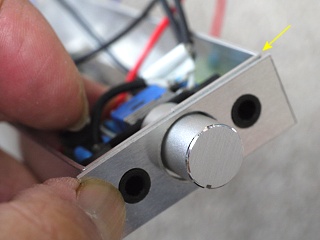 |
|
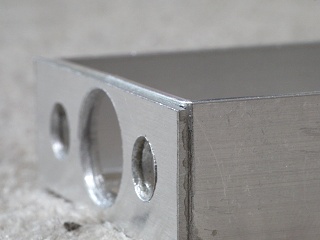 |
|
|
3つの穴の仕上げ研摩を致しました。 中央のツマミが出る穴は目視で等量の隙間が周りに出来るようにしています。 ただ1箇所貼り合せでずれが出来たようで、矢印の先のフレームが僅かに出ています。
|
|
その角部分のクローズアップです。 フレームの方が僅かに飛び出ているのが判ります。 ノギスで測ると0.4mmありました。 そこでフレームの右角から前面および後面までをテーパー状に削り落としました。 そしてこのために電池が出っ張ってこないよう電池位置を0.5mm沈めます。
|
|
|
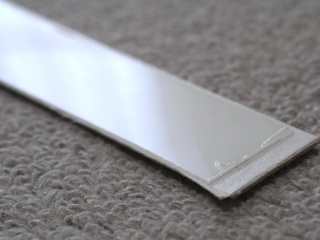 |
|
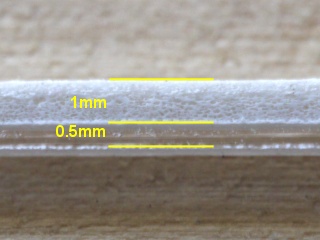 |
|
|
基板固定用の1.5mm厚スペーサーは1mm厚発泡塩ビ板に0.5mm厚透明塩ビ板を貼って作ります。 これはイレクター用接着剤で貼って乾燥中ですが、間に気泡が残らず厚み斑が少なく出来ました。
|
|
24時間後にカッターナイフで1mm幅に切断した物のクローズアップです。 非常に結果良好ですが強烈な有機溶剤臭が出ているので更に24時間寝かせてから使います。
|
|
|
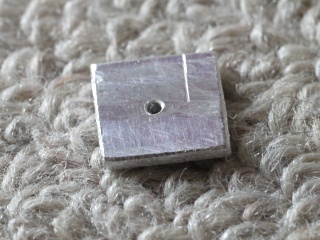 |
|
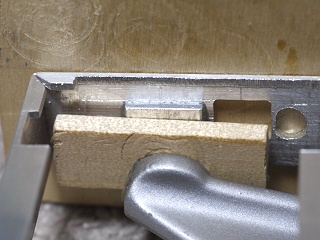 |
|
|
こちらはフレーム背面の内側に貼り付けるネジ切の補強板で、1.5mm厚のアルミ板から約10mm角に切り出し1.2φの穴をあけました。
|
|
それをフレームの所定の場所にエポキシで接着しました。 位置決めはフレームと補強板の穴に1.2φのドリルを差し込むことでしています。 こちらも24時間放置します。
|
|
|
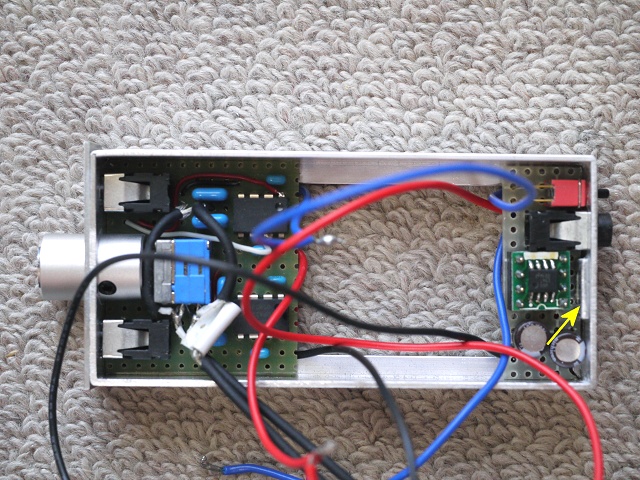 |
|
|
ここで確認のため2つの基板を所定の位置に収めてそれらとフレーム間の隙間を測定しました。 設計値は1.5mmの隙間ですが、実測値は1.5mm±0.05mmに収まっていました。 フレームと前面パネルの位置ずれと言う少々大きい問題はありましたが、なんとか無事に対処できほっとしています。
|
|
|
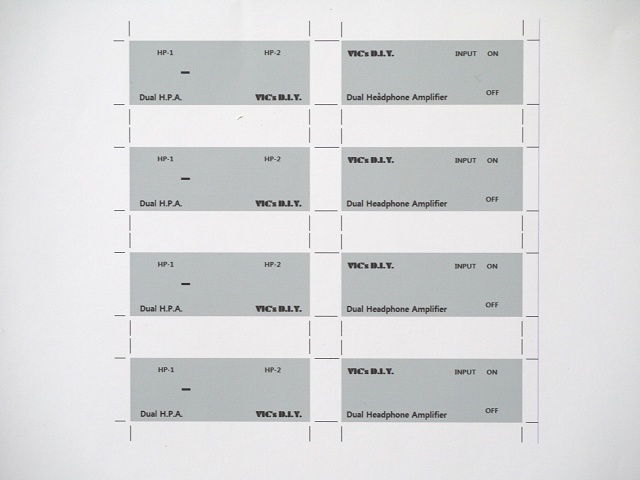 |
|
|
A4のマット紙に印刷し終わった状態。 一度に4組印刷しているので、貼り間違えても十分にスペアーがあり安心です。
|
|
|
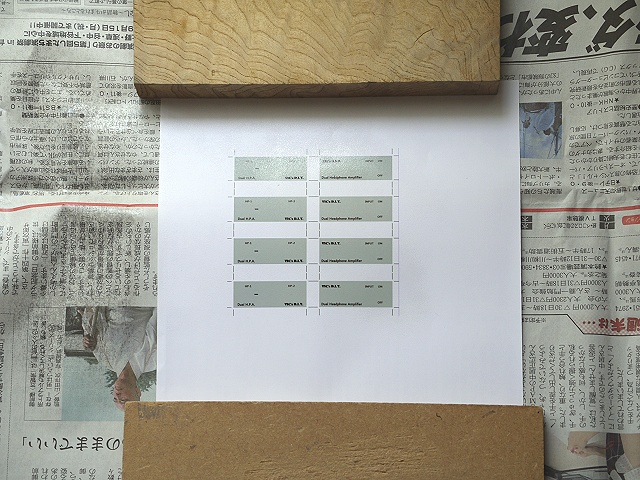 |
|
|
透明クリヤーのスプレー塗料を2回塗り後つや消しクリヤーを1回塗りしました。 塗装するたびに2時間乾燥させ最後は4時間乾燥させました。
|
|
|
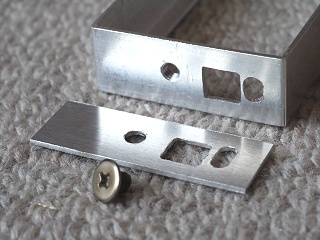 |
|
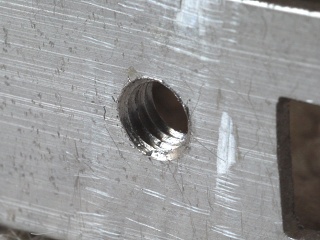 |
|
|
上の乾燥中に背面の雌ネジ切りをしました。 これは切り終わった後ですが、奥からフレーム、背面パネル、3.5mmの長さに切断したM4ステインレス薄頭ボルトです。
|
|
切った雌ネジのクローズアップです。 山が4つ見えているので4回近く雌ネジと雄ネジが噛み合うことになります。
|
|
|
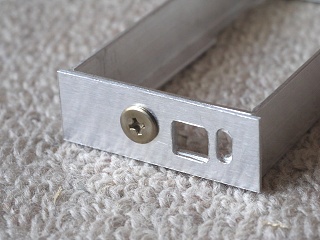 |
|
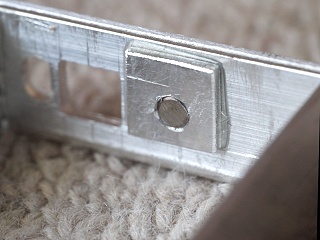 |
|
|
背面パネルとフレームをネジで共締めしました。 最終的には背面パネルはケース後部に埋め込まれますので、この状態でフレームは固定されることになります。
|
|
その時の内側。 ネジの先は3.5mmで切断しましたので出っ張りはありません。 従って電源基板の部品を痛めることもありません。
|
|
|
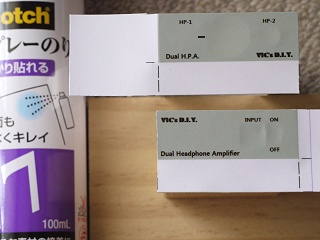 |
|
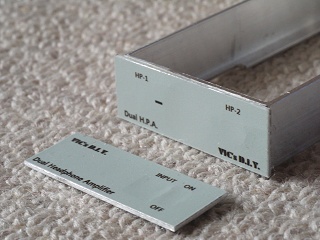 |
|
|
塗装が完全乾燥後2辺を正確に切り落とし裏にSCOTCHスプレーのり 77(左に一部が写っています。)を吹き付けて所定の位置に貼り付けました。
|
|
残りの2辺をカッターナイフでカットしました。 この後穴抜きをしますがそれは糊が完全乾燥後にします。(そうしないと切り口がだらけてしまう可能性が大です。)
|
|
|
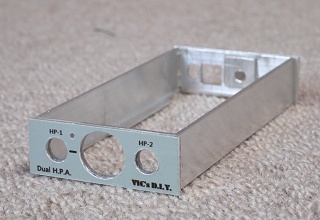 |
|
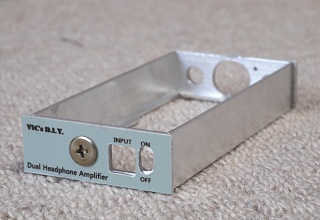 |
|
|
OLFAの刃先が30度の角度を持ったカッターナイフで少しずつ押し切りして穴部分を抜き取りました。 こちらは前面です。
|
|
そしてこちらは背面です。 この後切り口に毛羽立ちがありシャープさがないので、つや消しクリヤーをスプレーして生乾きの状態で角を押し慣らしてきりっとした感じにします。
|
|
|
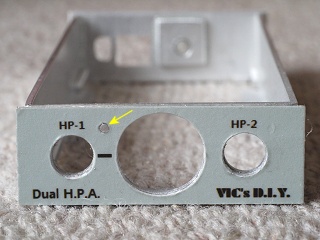 |
|
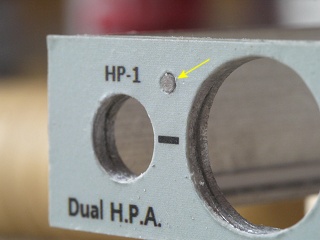 |
|
|
手回しピンバイスに取り付けた1.2φのドリルで穴をあけ2.4mmの長さに切った1.2φナイロンワイヤーを叩き込みました。
|
|
ナイロンワイヤーは0.1mm程前側に出っ張り背面は面一ですが、この為に見た目では丸い円がくっきりと浮かび上がる筈です。
|
|
|
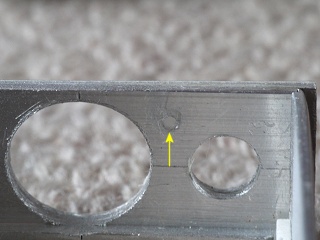 |
|
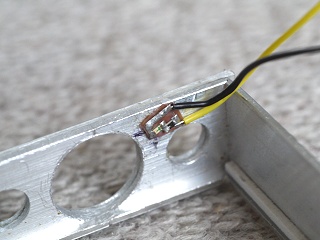 |
|
|
内側から見たLEDの光を導くナイロンワイヤー。 実は叩き込んだ位置を確認後、少量の瞬間接着剤をこちらから塗って抜け止めとしています。
|
|
そしてLED基板の位置を通る光を見て調整しながら瞬間接着剤で固定しました。 最終的にはワイヤーの一部もフレーム内面に瞬間接着剤で固定しています。
|
|
|
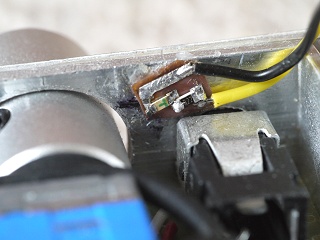 |
|
 |
|
|
本来のLED基板ではないのでご覧のようにかなり傾けて強引に貼り付けましたが、ヘッドフォーンジャックとも干渉せず固定できています。
|
|
本来の駆動電圧では写真に撮ると白っぽくなってしまうので、2.7Vまで下げて試験点灯しました。 期待通り丸みがくっきりと見えます。 そしてもっと斜めから見ても明るさが下がりません。
|
|
|
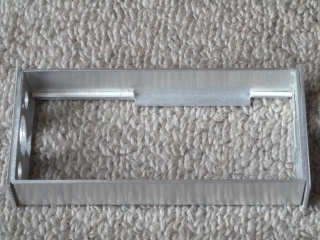 |
|
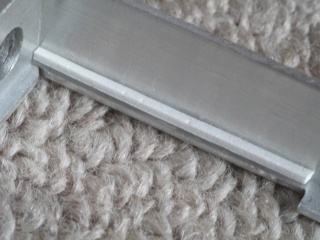 |
|
|
基板を1.5mm浮かして固定するためのスペーサーを貼り付けました。 瞬間接着剤を使っています。 この角度からは見えませんが手前側にもあります。
|
|
2枚貼り合わせた透明側を下にしていますので、若干浮き上がっているように見えます。
|
|
|
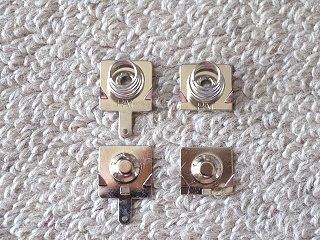 |
|
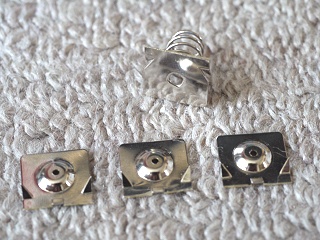 |
|
|
電池ホルダーに使うプラス/マイナス電極の加工。 左が加工前で右は下側を約1mm切り落とした物です。
|
|
プラス電極の中心に1.2mmの穴をあけました。 これで位置決めが楽になります。
|
|
|
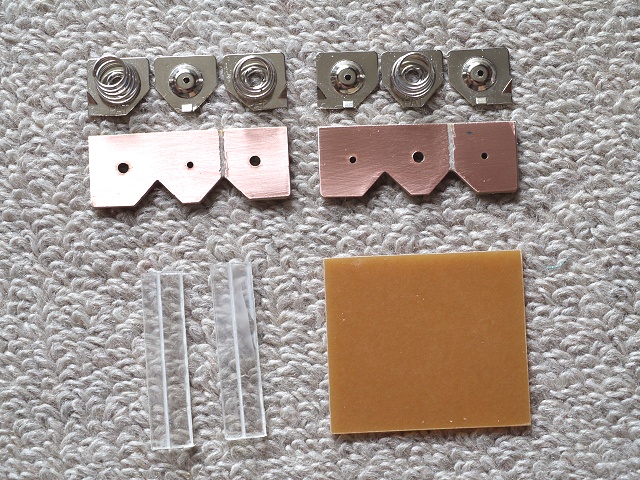 |
|
|
ホルダーの電極を貼り付ける面は1.5mm厚プリント基板生板を切り出して作ります。 そして位置決めの穴(2.0φと1.2φ)や断面三角の仕切り板の穴にワイヤーが出入りする穴を削っておきます。 また中央と右の電池の間に幅1mmの浅い溝をミニルーターで削り電気的に絶縁させます。 下左は断面三角の仕切り板で、0.5mm厚塩ビ板を幅5mmのL字状に加工したものです。 その右は底板で厚さ1mmのベーク板です。
|
|
|
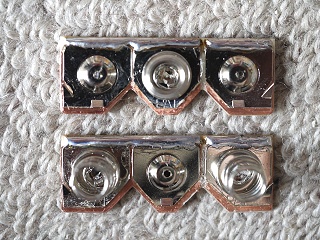 |
|
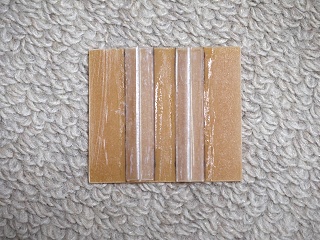 |
|
|
電池ホルダー側板に電極をエポキシ接着剤で貼り付け、硬化後に上側を半田で繋ぎ合わせるのと同時に電気的な接続をします。
|
|
L型に折り曲げた仕切り板を底板の所定の位置に瞬間接着剤で貼り付けます。
|
|
|
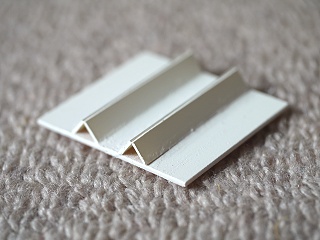 |
|
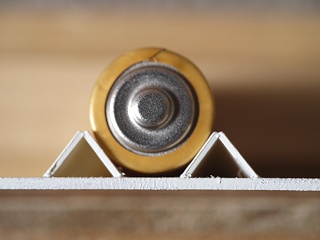 |
|
|
完全硬化後にラッカースプレー塗料で上面を塗装しました。
|
|
中央の電池はこのように収まります。
|
|
|
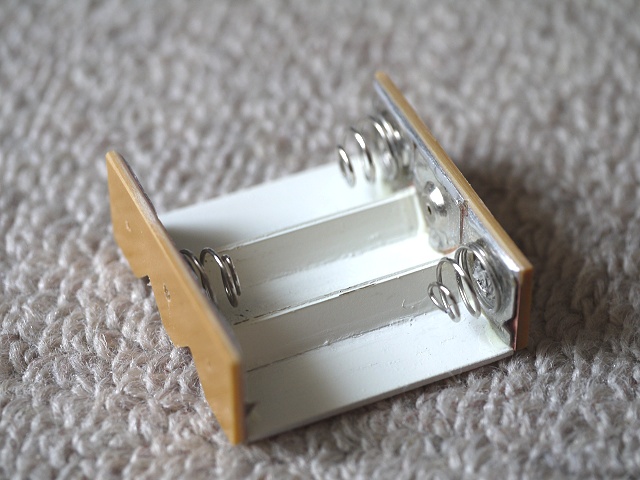 |
|
|
電極を貼り付けた側板を瞬間接着剤で底板に貼り付けました。 尚電極のスプリングが長すぎて電池がうまく収まりませんので伸びた長さにして2.5mm程短く詰めました。
|
|
|
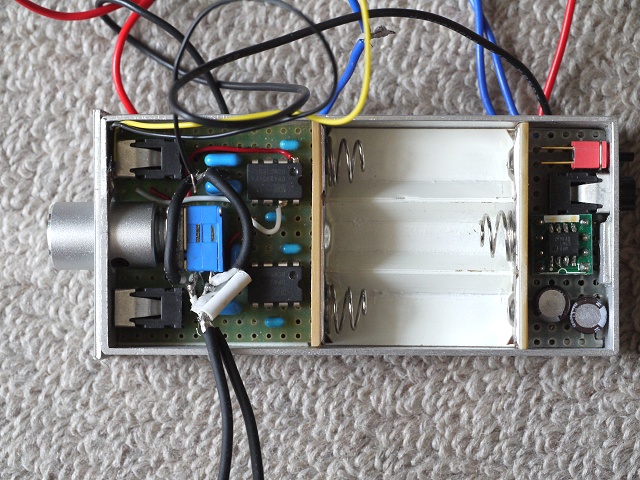 |
|
|
とりあえず2つの基板と共にフレームに嵌め込んで見ました。 底板の長さをノギスでドンピシャ寸法になるよう予め加工してありましたので問題なく(隙間なくきつくも無く)収まっています。 周りに見えるワイヤーは1〜2段細い物に変更して、2つの仕切り板を通るようにします。
|
|
|
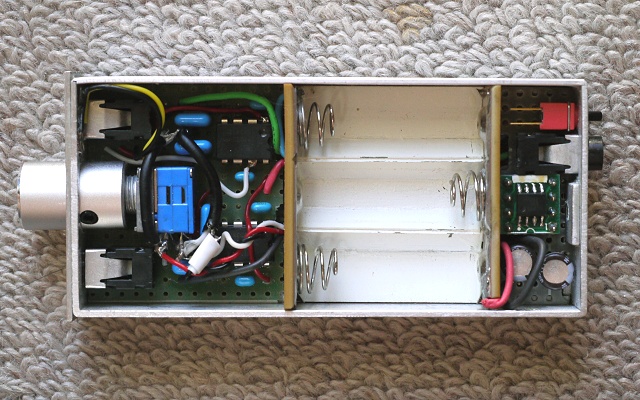 |
|
|
上の仕切り板に3本、下の仕切り板に4本のワイヤーの合計7本が旨く隠れました。
|
|
|
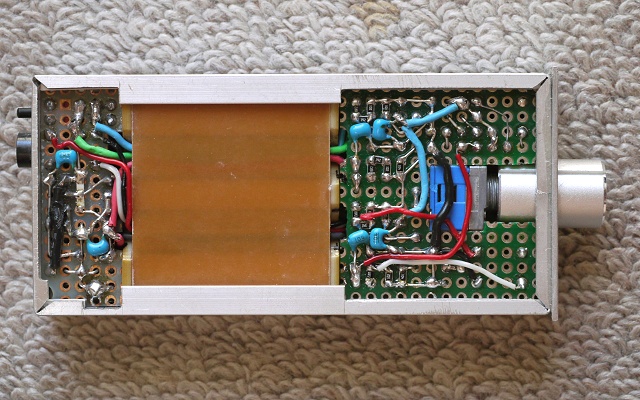 |
|
|
こちらは裏側です。 3角の仕切り板を考える前には裏面の隙間(1.2mm)に沿わせるつもりでしたが、遥かにすっきりとした外観になりました
|
|
Copyright (C) 2001-2019, Vic Ohashi All rights reserved.