|
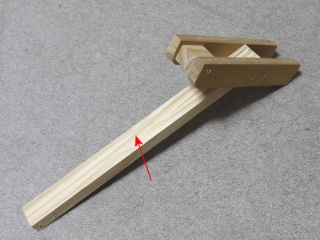 |
|
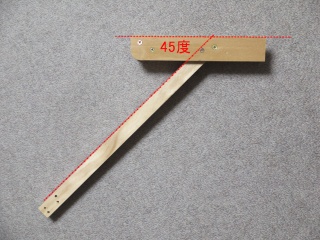 |
|
|
これが45度研摩をする一過性のジグです。 端材の木材から4つの部材を切り出しネジで組み上げています。 矢印の先の面に研摩される材料を固定します。
|
|
真横から見るとこんな具合です。 写真中に示した角度が正確に45度であることが重要です。
|
|
|
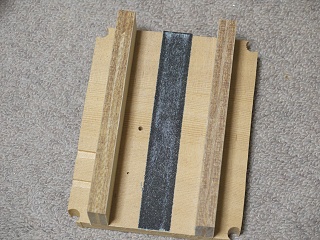 |
|
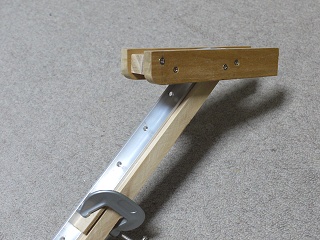 |
|
|
逆さにしてお見せしていますが、これを上に被せて前後に動かして研摩します。 真中縦に黒っぽく見えるのが両面接着テープで貼った布サンドペーパー#60です。
|
|
さて実際の研摩の様子ですが、このように研摩する材料をしっかりとクランプで固定します。
|
|
|
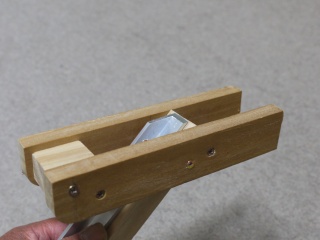 |
|
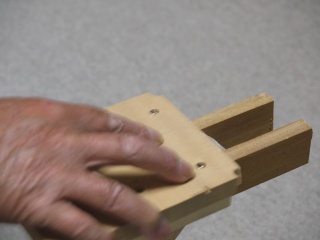 |
|
|
材料の先端はほんの少しジグから飛出るくらいがよろしい。 そしてこのように左手で握って保持します。
|
|
右手は左上の道具を被せて前後にゴリゴリと動かし研摩します。 材料の先端が鋭くナイフのようになれば終了ですが、研摩速度は大変遅いので時間が掛かります。(削りすぎは起しにくい!)
|
|
|
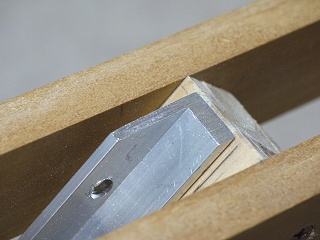 |
|
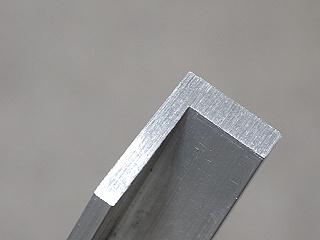 |
|
|
終了間近となっている材料先端の様子です。
|
|
これが研摩終了の材料先端。 研摩ジグ無しではこんなに綺麗で正確な角度の面には絶対になりません。
|
|
|
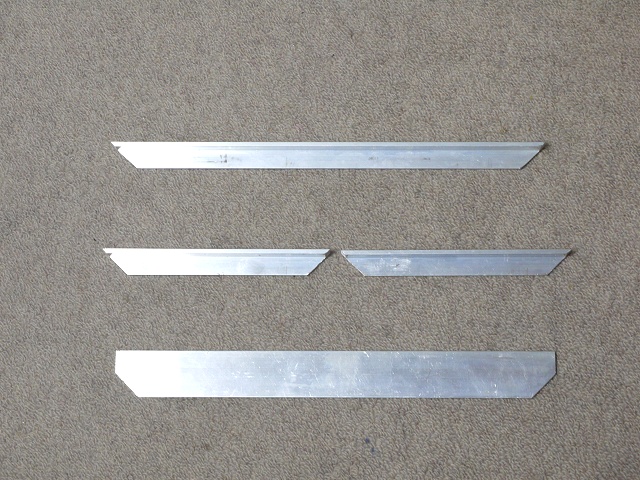 |
|
|
切断と先端の角度出しが終わった4本の部材。 ここまでで丸一日掛かってしまいましたが、この製作作業で一番忍耐と根気を要求する作業でしょう。
|
|
|
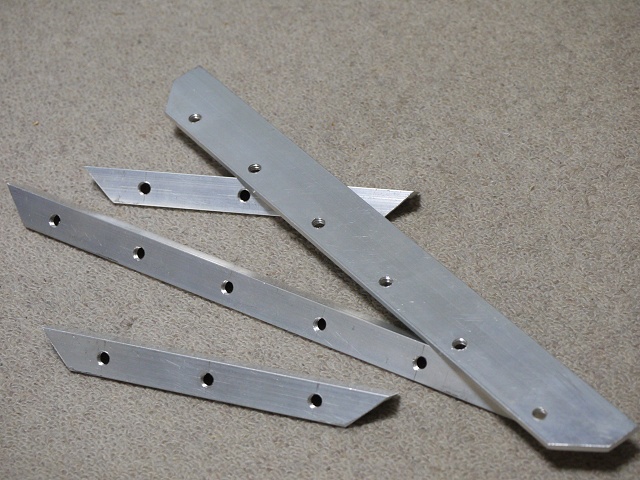 |
|
|
5φの下穴をあけてタップでM6の雌ネジを切りました。 穴あけの位置精度とネジ切り時の直角度の精度が重要です。
|
|
|
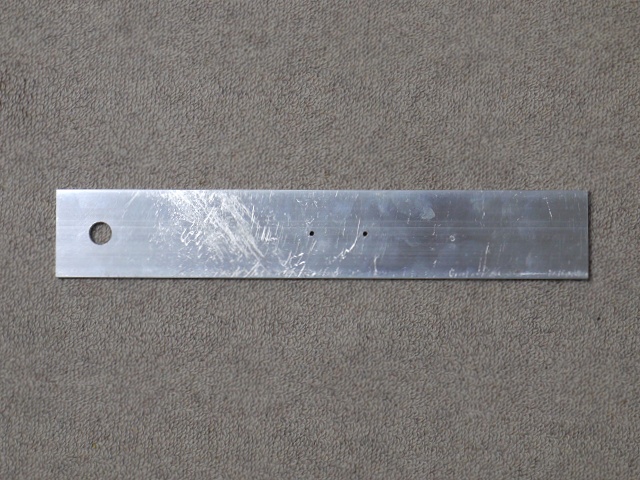 |
|
|
放熱板となるアルミ板(300 x 50 x 5mm)にパワーIC固定のネジ(M3 x 2)とDCジャックを固定する穴(13φ)をあけます。 たった3個の穴ですが板厚が5mmですので加工には時間が掛かりますし、ご覧のように細かい傷が沢山付いてしまいます。
|
|
|
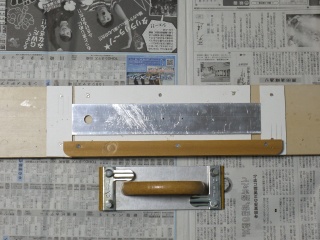 |
|
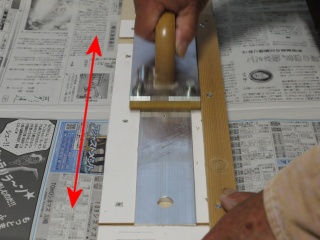 |
|
|
そこでこのようにアルミ板が動かないように固定して研摩します。 茶色の棒はハンドサンダーを直線に動かすためのガイドです。
|
|
ハンドサンダーをガイドに沿わせてアルミ板を研摩します。 #120のペーパーを使っていますが、空研ぎペーパーが目詰まりを起さず都合が良いです。
|
|
|
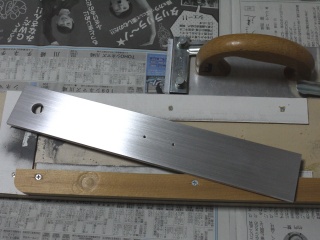 |
|
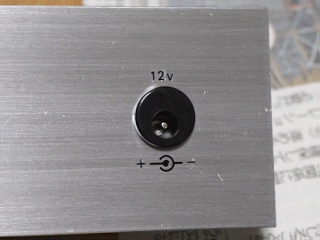 |
|
|
傷が全て取れてしまいウソのように綺麗な表面になりました。 この面をウレタンニスで保護します。
|
|
水性ウレタンニス透明クリヤー2回塗り後完全乾燥させてからインスタントレタリングで文字入れし、その後透明クリヤー1回塗り、艶消しクリヤー1回塗りとしました。
|
|
これで金属加工は暫しお休みとなり、木工作業となります。 最初に5.5mm厚シナ合板から背面板を切り出し、上で加工したアルミ板と接着します。 接着にはエポキシ接着剤を使います。 次に底板を切り出し底板固定ネジが通る穴
|
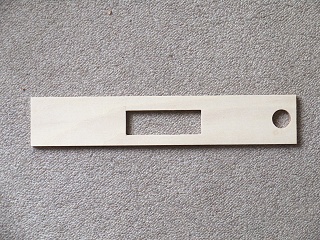 |
|
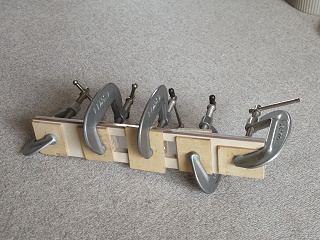 |
|
|
5.5mm厚シナ合板から切り出した背面板。 これと5mm厚アルミの背面板と貼り合わせます。 この板は52mm幅でアルミ板は50mm幅ですから、貼り合わせ時にこの板が上下に1mmずつ飛出るようにします。
|
|
エポキシ接着剤を使っていますが、密着度が上がるようクランプでかなり締め上げて4時間ほど寝かします。
|
|
|
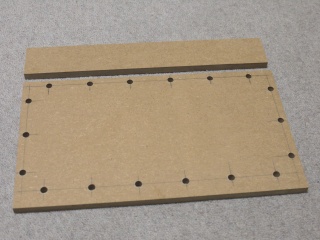 |
|
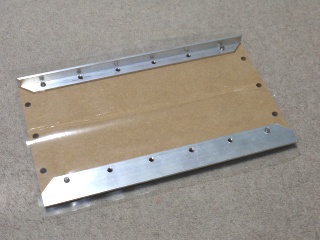 |
|
|
底板は2枚構成で、上が手前側になりますが接着剤で固定され、下は18本のM6 のボルトが通る穴があいたネジで固定する底板です。
|
|
アルミのチャンネル材を固定しますが、底板との間にポリエチレンシートを挟みこの後の接着作業で接着剤が底板に付着しないようにします。
|
|
|
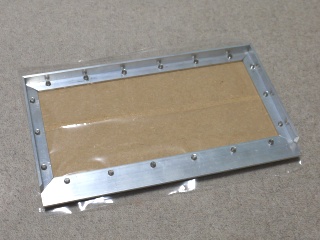 |
|
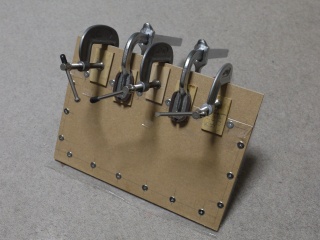 |
|
|
4本のチャンネル材の突合せ部分に問題がないか、組立後に4本のチャンネル材で出来る長方形が設計寸法どおりになっているかを確認します。
|
|
問題なくば次の工程で、底板前部分を平板アルミ板に接着します。平板の幅は30mmありますが、半分の15mmが接着される部分です。
|
|
|
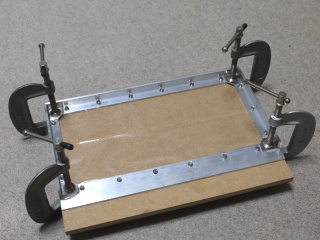 |
|
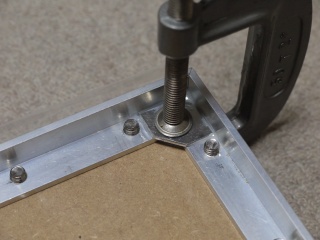 |
|
|
次にチャンネル材の突合せ部分4ヶ所の内側に20 x 20mm厚さ1.5mmのアルミ板をエポキシ接着剤で貼り付けました。
|
|
これが拡大写真ですが、この工程で4本のチャンネル材は強度不十分ながら連結され、位置関係が確定します。
|
|
|
 |
|
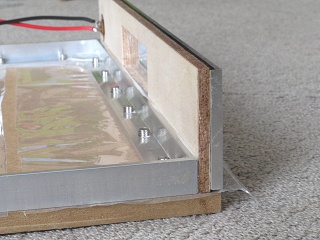 |
|
|
背面板の接着。 垂直に立つようにするのが重要ですが、L字型チャンネル材の直角度に依存しています。
|
|
完全硬化後クランプを外した右横です。 底板はポリエチレンシートが被さっているので、接着されません。
|
|
|
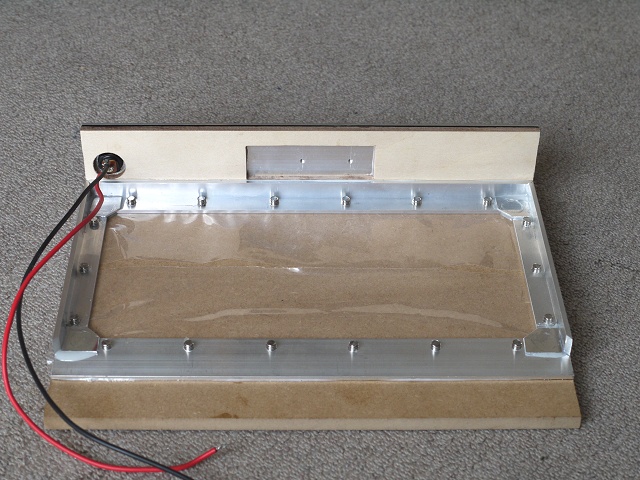 |
|
|
箱構造の底板と背面板の2面が組み上がった事になります。 次が前板を貼り合わせてから天板を貼る事になり、最後が左右の側板です。
|
|
|
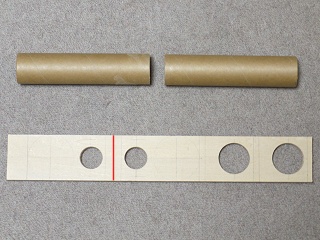 |
|
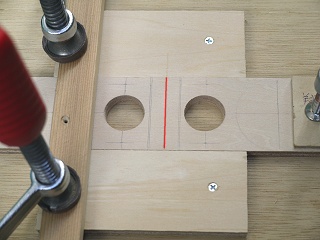 |
|
|
52mm幅に切断した9mmシナ合板から手前の4枚の板を切り出します。 赤線はV溝ビットでの切断位置。 また厚紙円筒を所定の長さに切断しました。
|
|
52mm幅を別な板で挟み動かないよう押さえました。 この写真でも赤線はV溝ビットの先端が通る位置になります。
|
|
|
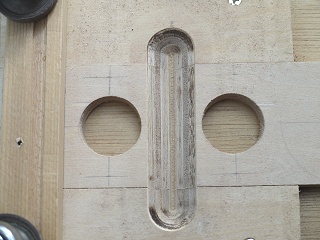 |
|
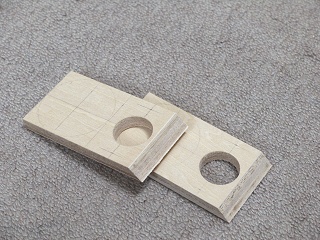 |
|
|
切削深さが9.7mmになるようノギスで数回確認した後に一気に切削しました。
|
|
2つに切り離されました。 こんな小さな写真でも切断面は美しくない事が判りますが?
|
|
|
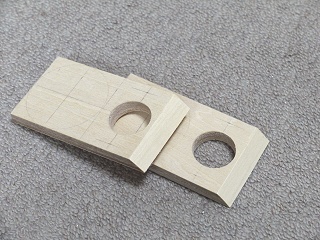 |
|
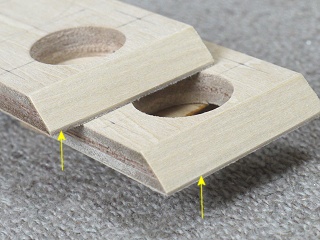 |
|
|
替刃式ヤスリで表面をならした後にシナの木口テープを貼り、ヤスリで段差を取り除きました。
|
|
そして45度斜面の先端を削って1.5mm幅となるようにしました。 この段差と後ほど加工するアルミ板の厚みは一致するので、ぴたっと収まります。
|
|
|
 |
|
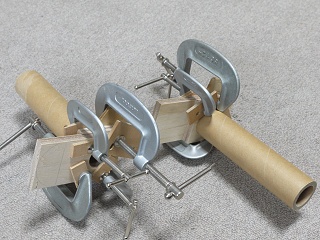 |
|
|
2番目の板に円筒を接着します。 直角度が出るように曲尺で念入りに確認する必要があります。
|
|
1番目の板と2番目の板を貼り合わせました。 位置関係の正確さは極めて重要です。 適当にやると後でとんでもない事になります。
|
|
|
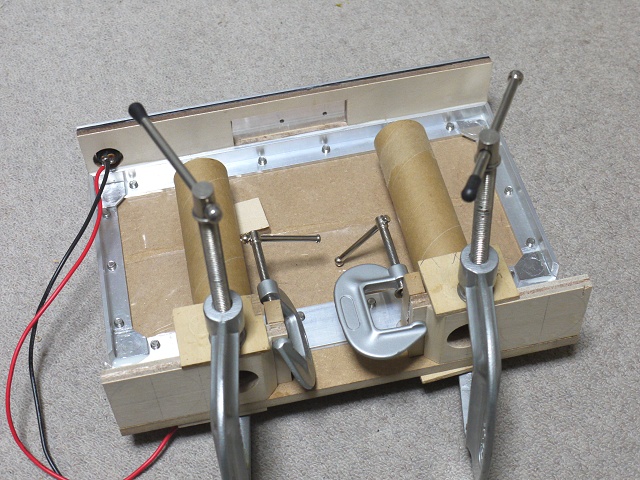 |
|
|
出来上がった物を所定の位置にエポキシ接着剤で接着しました。 更にその後に取り付けられるMDFの部材2個を接着しています。 そしてこの後に接着されるべきMDFにはコントロール基板が固定されるので、その辺りの加工をしている最中に待てよ?!と気になる事を見つけ作業を止めました。
|
|
何を見つけたのかというと、コントロール基板は部品が付いた面が奥の方になるように固定するのですが、その奥行を15mmとして設計を進めてきました。 そしてこの距離でぎりぎりになる上背の高い部品はトグルスイッチで14mmという認識でいました。 ところがそれよりも奥行きが長くなる部品の存在に気が付いたのです。
|
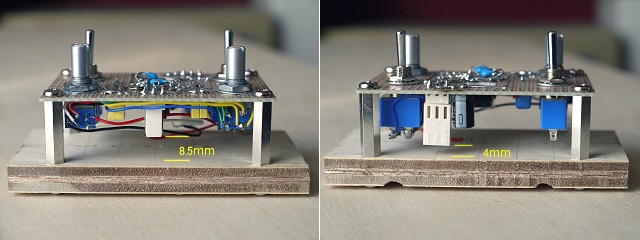 |
|
|
スペーサーを20mmに変更後の板と部品の間隔。 左の写真はオスのコネクターだけの場合で8.5mmあるが、以前の15mmスペーサーでも3.5mmあったので問題なしと勘違いしていました。 実際には右の写真のように4mmの隙間で、ここにワイヤーが入るからぎりぎりOKというところです。
|
|
|
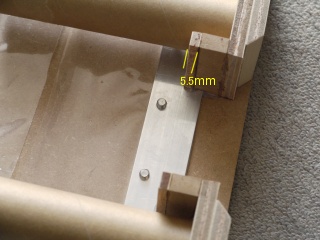 |
|
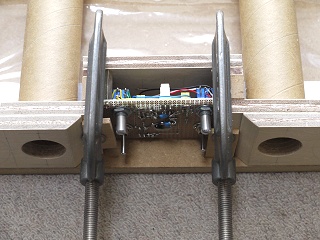 |
|
|
結局5.5mmの下駄を履かせることになりましたので、端材の5.5mm合板を切断して貼りつけました。
|
|
そしてその上にコントロール基板を固定する板を接着しました。 基板の位置も気になったので、基板を仮取り付けした状態で圧着保持しています。
|
|
|
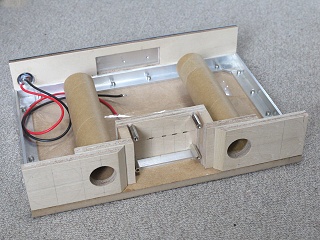 |
|
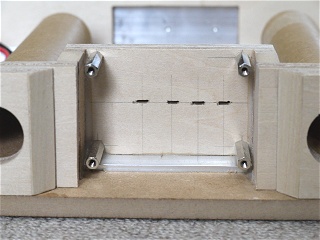 |
|
|
やれやれやっと問題が完全解決しました。 幸いな事に全体的な工作・組立精度には全く影響がありません。
|
|
コントロール基板及びアルミパネルへの配線は3芯ワイヤーが4組あります。 そこで3芯平ワイヤーが通る穴(1.6 x 5mm)を4つトリマービットであけてあります。
|
|
|
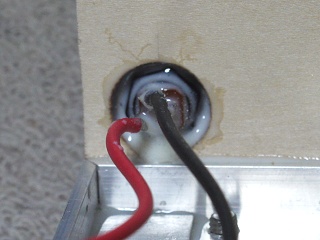 |
|
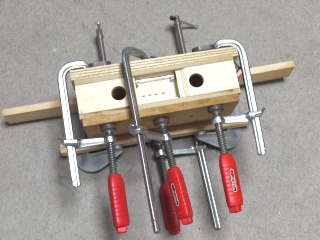 |
|
|
上板を接着する前にDCジャックの固定ネジ、及び端子の隙間にエポキシ接着剤を塗りつけて隙間を完全に塞ぎました。
|
|
上板をエポキシ接着剤で接着。 中型のクランプ6本を使って圧着保持4時間。
|
|
|
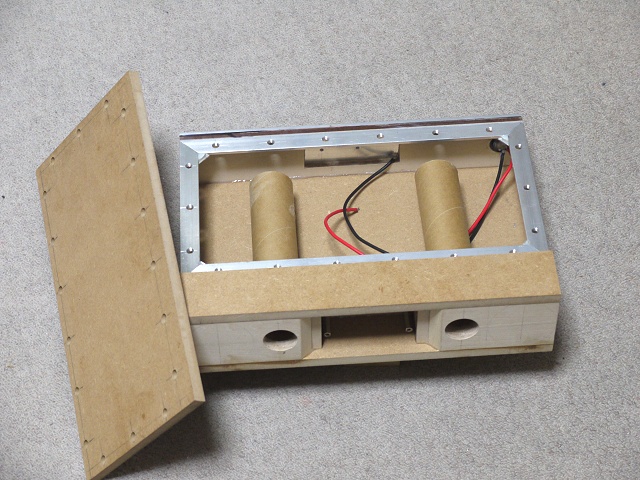 |
|
|
ポリエチレンシートを挟んで仮固定していた裏蓋をやっと外せます。 曲尺で調べましたが、箱のねじれは全く無く、外形の寸法誤差は±0.2mm以下となっており、高精度を保てていると思います。
|
|
|
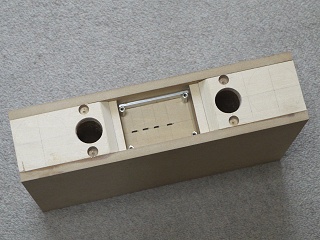 |
|
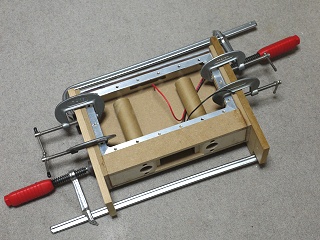 |
|
|
グリルを固定するゴムブッシュを嵌め込む4個の穴(10φ x 9mm)をあけました。 深さを正確にしないと突き抜けて空気漏れに繋がるので、電動ドリルアタッチメントで彫る深さにリミットを掛けています。
|
|
そうして左右の側板をエポキシ接着剤で固定しました。 圧着保持にはフレーム部分に50mm C型クランプ4個全体を400mmバクマクランプを使い、めいっぱい締め上げています。
|
|
|
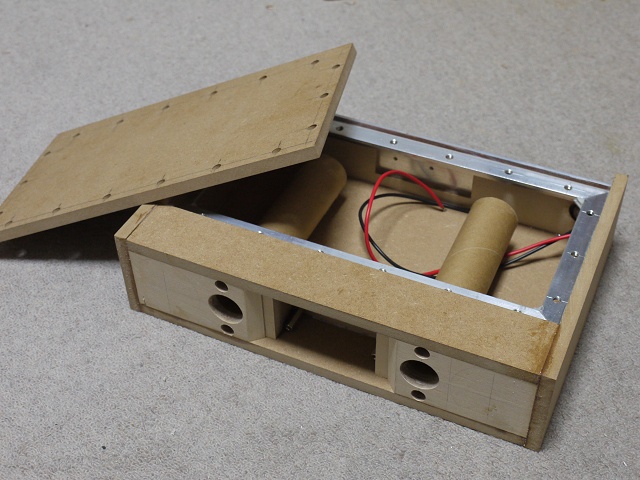 |
|
|
組立作業はこれで終了です。 左に立てかけている底蓋も調整することなくすっと嵌め込めます。 かなりへんてこな順序で組み立ててきましたが、精度を狂わせない!という大条件は完全に守れたようで、捻れや反りは全くありません。
|
|
|
 |
|
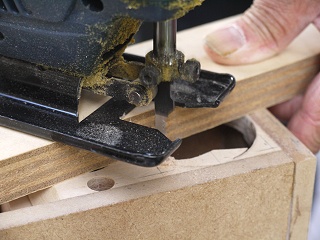 |
|
|
側板の接着が完全硬化後やっとスピーカーユニット取り付け穴の切断に入れます。
|
|
箱の内部のアルミフレームにブレードが当るので、底に近い所を切断する時はこのように18mmの合板を下駄として電動ジグソーと箱の間に挟みました。
|
|
|
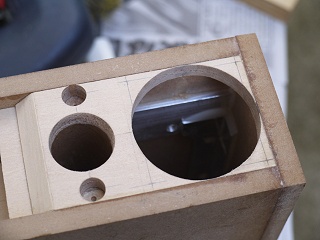 |
|
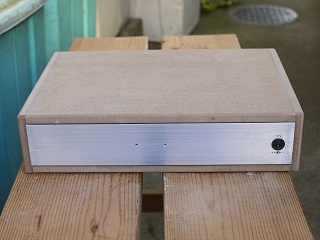 |
|
|
スピーカー取り付け穴をあけ終わりました。 この写真をご覧になれば穴をあけてから組み立てる方法は駄目である事が判るでしょう。
|
|
段差取り、突合せ調整の研摩とボース面ビットによる面取りが終わり、組立作業は終了で、これは背面です。
|
|
|
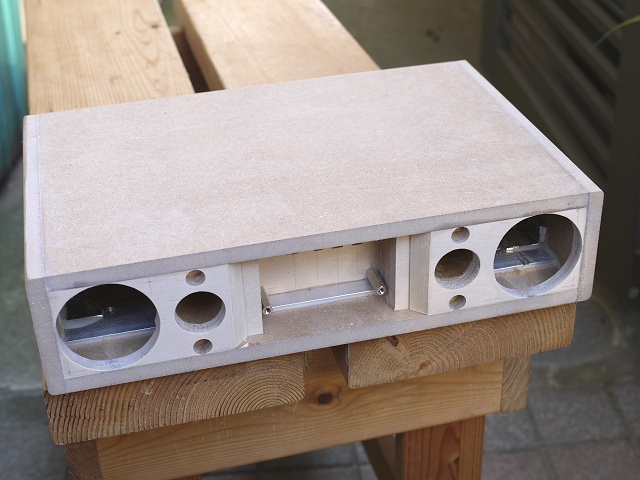 |
|
|
『アルミフレームを構成する部材を底板に仮固定して!』からスタートした、かなり変則的な手順の箱作りでしたが、箱の捻じれや反りを絶対に出さないという絶対条件をきっちり守れたと思います。 右手の穴の奥には最初にブレードが当って傷つけたアルミフレームが見えます。
|
|
ここで電気回路を組み込んで音出しが出来るようにして暫し電気回路上の問題がないか、異常な発熱がないかのランニングテストを数時間やっています。 この時には裏蓋固定部分にパッキンは入れておりませんし、吸音材も入れてません。 コントールアンプの背面板を通過する4本のワイヤーが通る穴も隙間があり音的には完成には程遠いのですが、これでとんでもない音になるのであれば、先に進めません。 幸いそのような問題も無く一応パスといったところです。
|
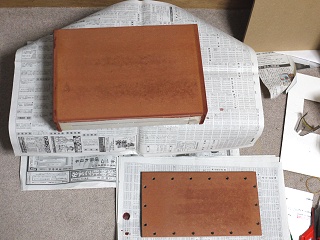 |
|
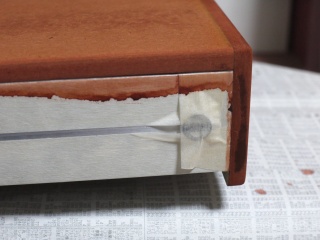 |
|
|
ポアステイン マホガニーブラウン色で着色開始。 色斑防止のため水で2倍に薄めています。 これは一度目が乾燥したところですが、5回着色としかなり濃度を上げました。
|
|
言い忘れましたが、背面のアルミ板は塗装作業が終わるまでマスキングテープで完全に覆ってやります。
|
|
|
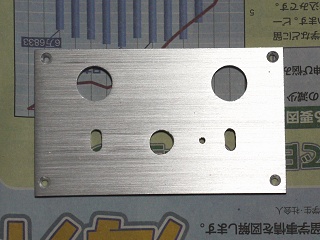 |
|
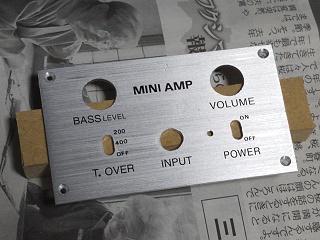 |
|
|
合間にフロントパネルのヘヤーライン加工をしました。 #120ペーパーでスタート、終わりは#240ペーパーとしていますが、空研ぎペーパーが最も具合がよろしい。
|
|
そしてインスタントレタリングで文字入れをしました。 この後水性ウレタンニス透明クリヤーを2回塗りその後艶消しクリヤーを1回塗って仕上ます。
|
|
|
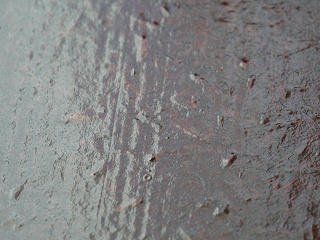 |
|
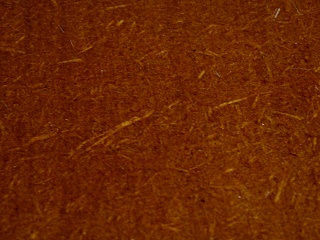 |
|
|
これは水性ウレタンニス透明クリヤーを2回塗った後のクローズアップ写真ですが、大き目の木片が起き上がって出来るぶつぶつがあちこちにあります。
|
|
こちらはスライドトップテーブルを作った時のMDF表面写真で、大き目の木片の出っ張りを強引に削り取ってその上を塗装したため、色味の薄い木片が目立ちます。
|
|
|
この問題解決のため実際には着色作業の段階から、飛出た木片を削り取る研摩をやっています。 着色作業では削り取
って木の地肌が見えた部分をスポット的に着色しました。 またニス塗りに入ってからは研摩し過ぎで木片まで削りこまな
いよう要注意です。 従って1回辺りの研摩はそれ程深く出来ませんから塗り回数が増えてきます。
|
|
|
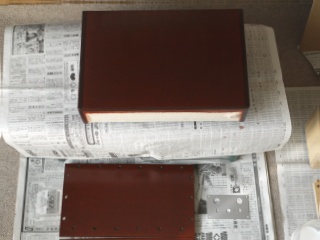 |
|
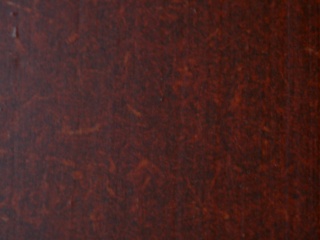 |
|
|
着色5回、透明クリヤーニス6回塗りが終わった状態です。 色の濃度はヘッドフォーンアンプケースと同等になったと思います。
|
|
大き目の木片はスライドトップテーブルの時(上の写真)のようには目立ちません。 そして、これは一体何の木の木目??と思わせるような重厚感があります。
|
|
|
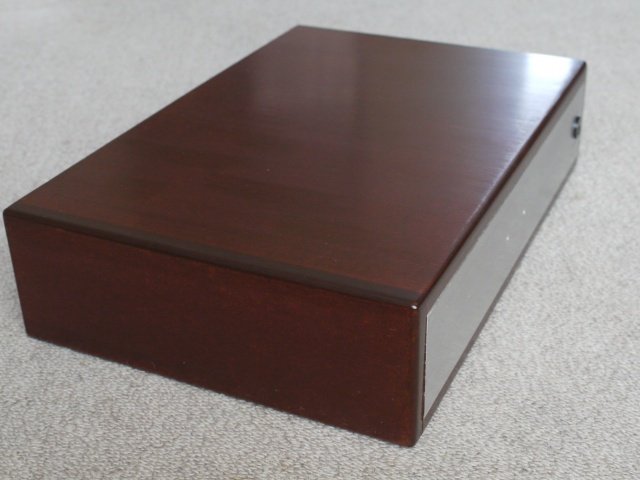 |
|
|
これを見て材料がMDFそのものだと気が付く人は殆どいないでしょう。 スライドトップテーブル以来の宿題が片付いたように思います。 チープなMDFをチープに見せない魔法です。
|
|
|
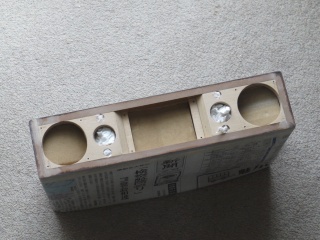 |
|
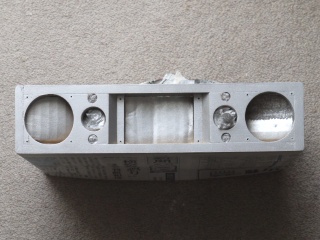 |
|
|
さて前面の塗装開始です。 スピーカー穴、バスレフポート穴、グリル固定ブッシュ穴にダンボールを被せたりティッシュペーパーを詰めてマスキングします。
|
|
そしてシルバー色のスプレーペイントで1回塗りしました。 そこで塗り斑を確認します。
|
|
|
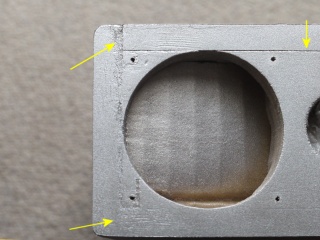 |
|
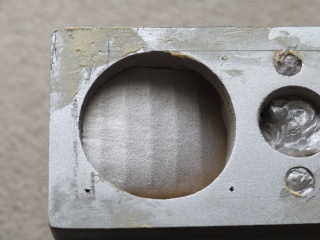 |
|
|
何箇所か問題があります。 矢印の先はそれらで、窪み、段差、傷などが目立ちます。
|
|
油性のパテ(mini-Shopで販売しています。)でそれらを埋めました。 完全乾燥後に#400ペーパーで削って均します。
|
|
|
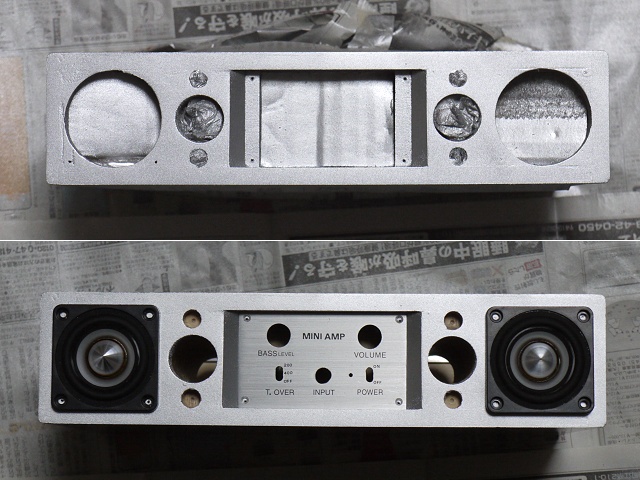 |
|
|
そしてシルバー色スプレーペイントを2回塗りしました。 上は塗った直後でまだ難のある個所がありますが、それらは下の写真を見て判るように、スピーカーユニットの下に隠れます。 なかなか精悍な感じの面構えです。
|
|
|
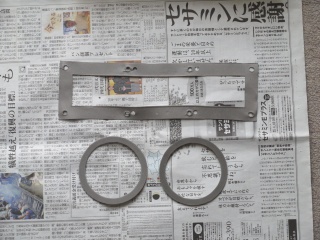 |
|
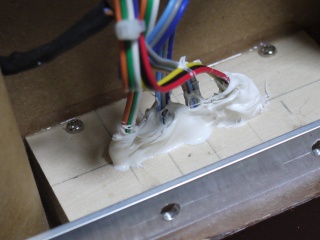 |
|
|
裏蓋固定部分とスピーカーユニット用のパッキンを作りました。 本当はウレタンフォームの2mm厚ぐらいのものが欲しかったのですが入手不能で、発泡ポリエチレンを使っています。
|
|
前面のコントールパネルに行くワイヤーが仕切り板を通る部分の隙間をコーキング材(変性シリコーン)で埋めました。 機密を保てますが必要とあらばナイフで切って簡単に取り除けます。
|
|
|
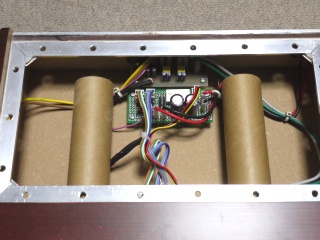 |
|
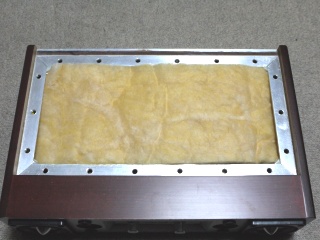 |
|
|
そしてコントロールパネルから後方に出ているワイヤーを束ねて固定しました。
|
|
最後に吸音材ですが、底面と左右の側面にコの字型に入れています。 そして裏蓋を固定し本体は完成です。
|
|
|
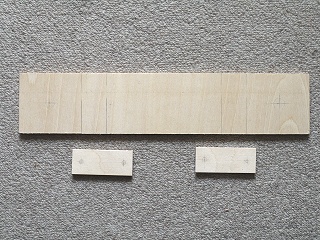 |
|
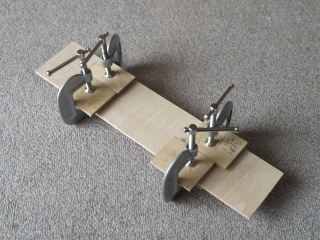 |
|
|
4mm厚シナ合板から3枚の部材を切り出します。 大きな物は補強の裏板で、小さな2枚はブッシュのオス部分を埋め込む板です。
|
|
小さな板を大きな板の所定の場所に木工ボンドで接着します。
|
|
|
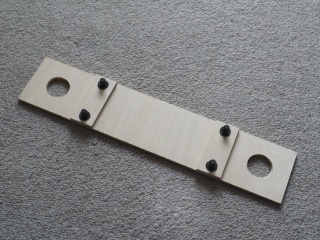 |
|
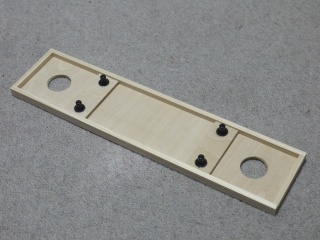 |
|
|
接着剤硬化後に8φの貫通穴をブッシュの位置にあけてオスのブッシュを叩き込みます。 またスピーカーのフェイズプラグが当らないよう25φフォスナービットで穴をあけておきます。
|
|
14mm厚の大きな板を5 x 10のヒノキ棒で挟むように木工ボンドで接着します。(木工ボンド硬化後の写真で圧着保持は無論必要です。)
|
|
|
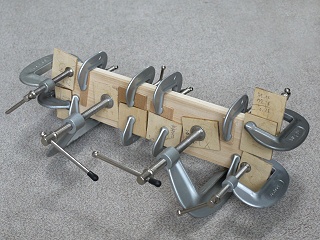 |
|
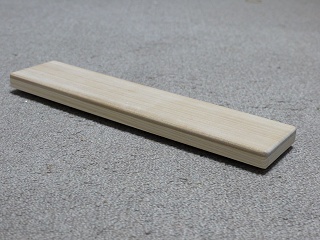 |
|
|
5mm厚アガチス材を切断して表面に貼り付けました。 接着部分に浮きがでないようご覧のように沢山のクランプで圧着保持しています。
|
|
接着剤硬化後コロ付き傘つき目地払いビット(MB-12.7G)で飛出た5mm厚の板を削り落とし、その上を#240ペーパーで研磨後にボーズ面ビット(BZ-10G)で角を丸く削ってやりました。 更に仕上げ研摩を#400ペーパーでやっています。
|
|
|
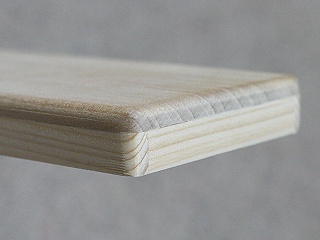 |
|
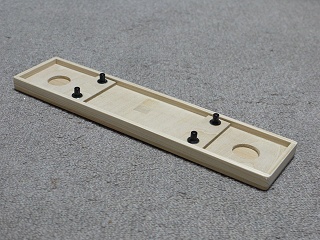 |
|
|
丸く面取りした角はこんな具合です。 色々な木目が交錯していますが、合板の木口のような見苦しさはありません。
|
|
これで塗装前の作業は全て終了しました。
|
|
|
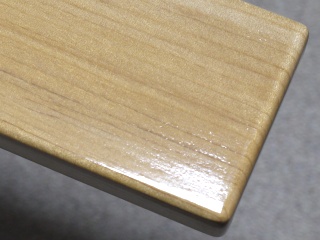 |
|
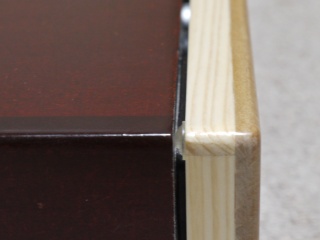 |
|
|
水性ウレタンニス透明クリヤーを3回塗りました。 それらの間には#400空研ぎペーパーによる研摩がされています。
|
|
アガチス(右)と桧(中央)そして本体(左)の色味の組み合わせが素適です。 尚カバーと本体が接触して傷にならないよう8φのクリヤーパンポンが間に貼ってあります。
|
|
|
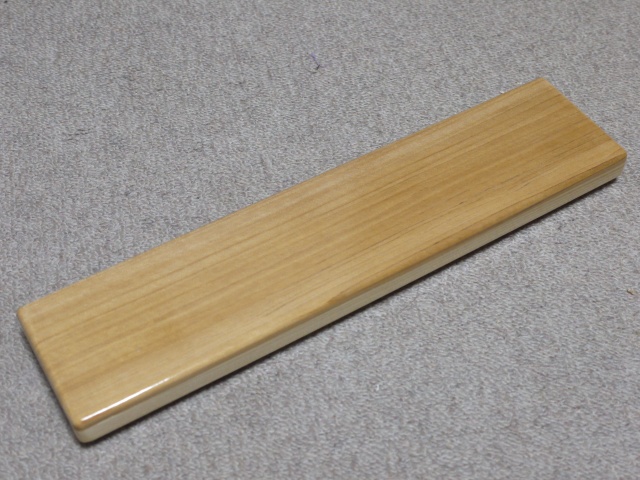 |
|
|
かなりの艶が出て大変綺麗なのですが私の好みはその艶を抑えた(5分艶)にしたいのので、この上に艶消しクリヤーを一回だけ塗ります。
|
|
|
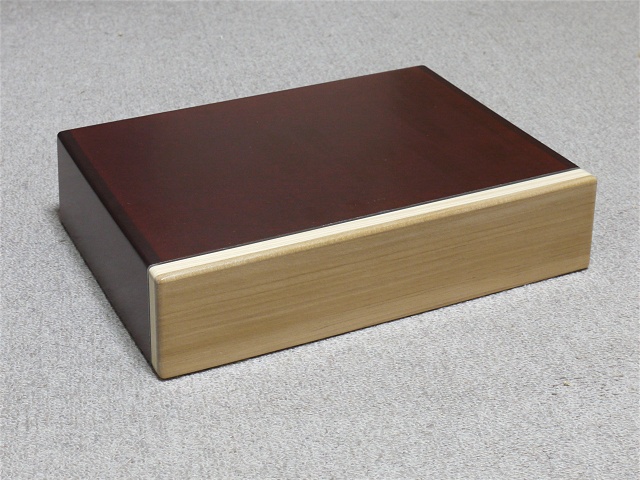 |
|
|
艶消しクリヤーが乾燥したので本体に取り付けました。 何か宝石箱のような美しさがあると思いませんか?
|
|
|
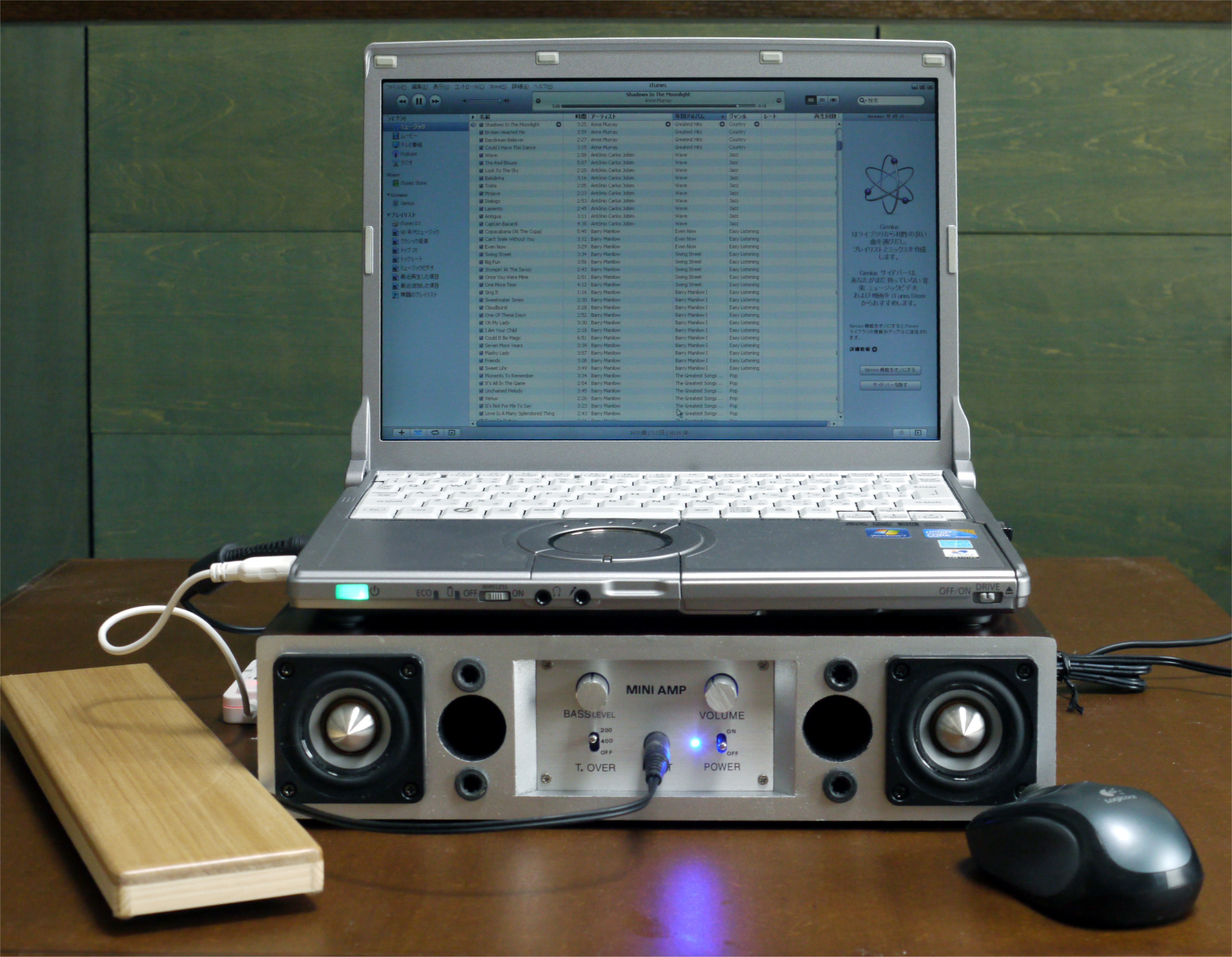 |
|
|
実際に使う際のセットアップをしました。 まだ十分にエージングが出来ていませんが、このスピーカーの音、そしてノートブックPC用スピーカー1との比較については、この後のコメントを参照ください。
|
|
|
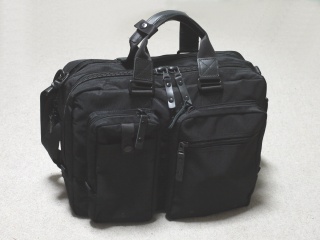 |
|
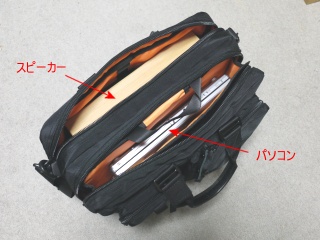 |
|
|
外寸が380 x 280 x 230mmの中型パソコンバックを運搬時には使います。 私のノートブックPCはレッツノートS8でコンパクトですがWindows XPが標準のお気に入り。 これとポータブルPCスピーカー2、ACアダプター2種類、無線マウス、カードリーダー、DVD/CDのディスク10枚程度が楽に入ります。(因みにポータブルPCスピーカー1はどうやっても納められません。)
|
|
Copyright (C) 2001-2019, Vic Ohashi All rights reserved.