|
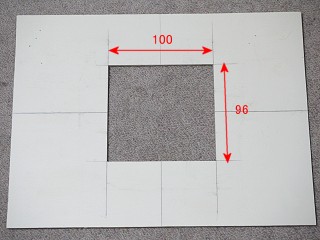 |
|
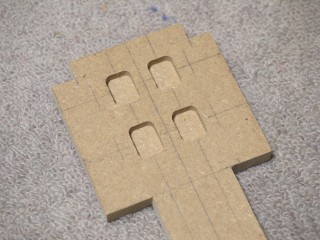 |
|
|
スピーカー端子盤の端子周りを落とし込む穴(12 x 16mm)はこのようなジグを作って6φのストレートビットを使いトリマーで加工します。
|
|
電動トリマー台座は90mm四方ですから左のジグの中で横に6mm、縦に10mmトリマーが動き、それにストレートビットの直径(6φ)が加算されるので、加工された穴は12 x 16mmになるという単純な仕掛けです。
|
|
|
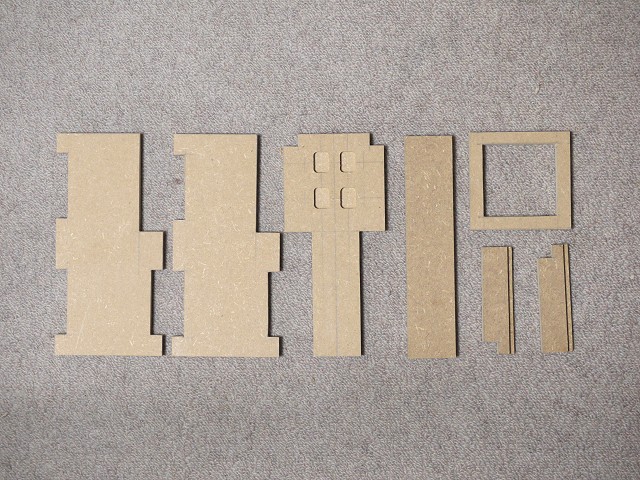 |
|
|
切り出してからカンナや替刃式ヤスリ(M-20GP)で成形、寸法出しが終わった7つの部材です。 これらの加工作業になんと1日半を費やしてしまいました。
|
|
|
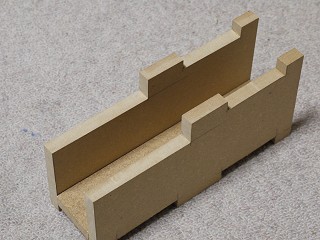 |
|
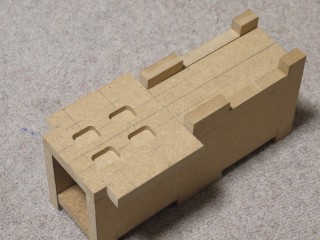 |
|
|
構造を理解願うために組立順序をお見せします。 先ず部材3を底に置いて2枚の部材1でそれを挟みます。
|
|
その上に部材2をこのように置きます。 部材2は左下では部材1の上に乗りますが、右上では部材1に挟まれる構造です。
|
|
|
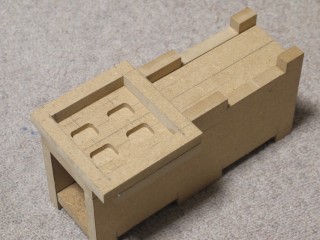 |
|
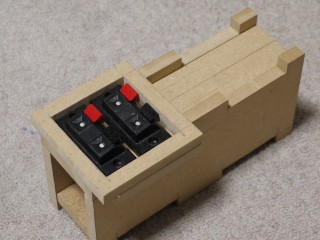 |
|
|
部材4が左下に載ります。 実際には接着する前にスピーカーケーブルを引き出す溝を追加加工しないとなりません。
|
|
スピーカー端子盤を所定の位置に固定します。 この上に12mm厚の本体部材が接着されます。
|
|
|
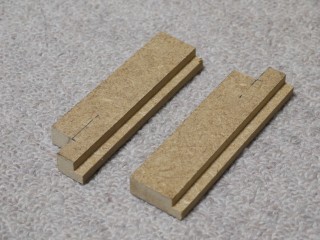 |
|
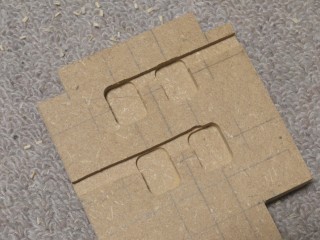 |
|
|
設計上はこの板をポートの一部として貼った時に73Hzの共振周波数になります。 更に調整板を追加する事で、70Hz、67Hzの設定が可能になります。 段差は調整板を繋ぐ時に出来る隙間防止です。
|
|
購入してきたケーブルに合わせ若干きつめの溝(幅5mm、深さ2.7mm)を彫りました。
|
|
|
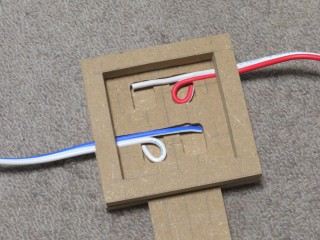 |
|
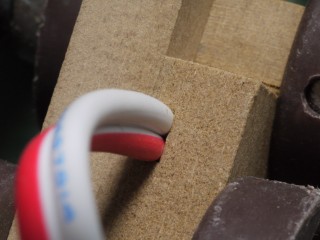 |
|
|
その溝にケーブルを潰し気味に押し込み部材4を載せます。 左右に出たケーブは左右のスピーカーに接続されます。
|
|
仮にクランプで圧着してみた様子ですが、ケーブルと溝の隙間は極小となっています。 この隙間は後ほど接着時にエポキシで完全に埋めます。
|
|
|
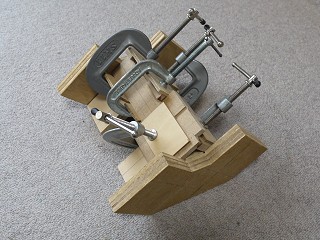 |
|
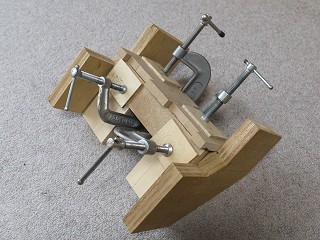 |
|
|
部材1と部材2をエポキシ接着剤で貼り合わせています。 直角精度を出すために自作のジグ(小型の物)を使っています。
|
|
部材1と部材3も同様に接着します。 部材の接着位置関係を間違えないよう充分確認しておかないとなりません。
|
|
|
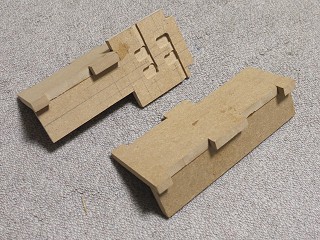 |
|
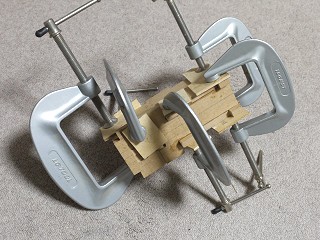 |
|
|
30分硬化開始型を使ったので、2時間放置した後にクランプを外し出来上がった2種類のL型に組んだ物。
|
|
その二つのL型を接着して断面がロの字となります。(ロの字の内寸は36mm x 45mmです。)
|
|
|
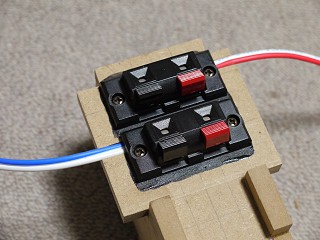 |
|
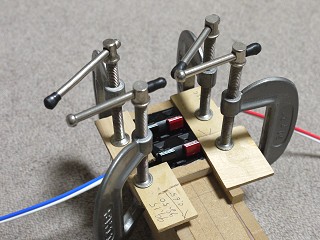 |
|
|
最終的に見える部分が僅かにありますので、黒のペイントで塗りつぶした後にスピーカーターミナルをネジ止めしました。
|
|
2本のワイヤーが嵌り込んだ溝にエポキシ接着剤を塗って隙間を埋め、その上から部材4を接着しています。
|
|
|
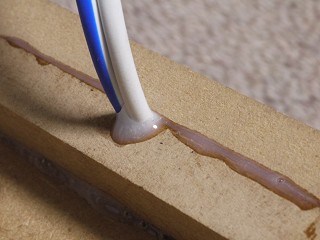 |
|
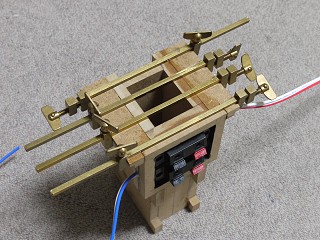 |
|
|
ワイヤーの出口部分。 僅かな隙間はエポキシで完全に埋まってしまいスピーカー端子周りで空気漏れを起こす部分は皆無になります。
|
|
9mm厚MDFを使う最後の作業。 部材5を接着します。 ここに見えている上が実際には背面方向になります。
|
|
|
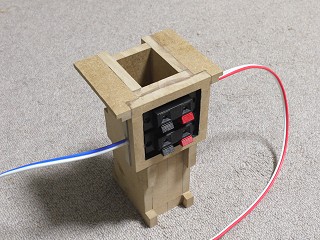 |
|
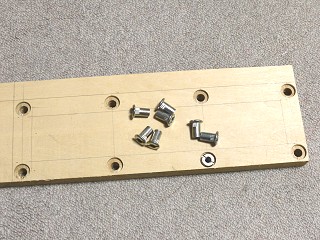 |
|
|
7枚のMDF部材は加工に若干怪しげな所がありながらも、許容できる寸法誤差内に納まったようです。
|
|
ポートアセンブリー製作の最後は18mm厚合板で背面板固定枠を作ります。 形はロの字ですが背面板を固定する4つのネジ穴をあけます。 ネジ穴は8φですが頭を沈めるために15φのフォスナービットで深さ3mmを先にあけます。
|
|
|
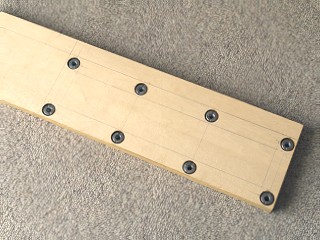 |
|
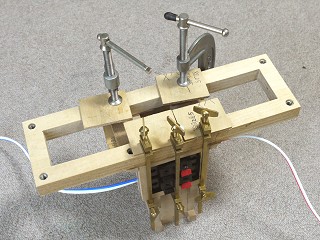 |
|
|
あけた穴の壁面や底面にエポキシ接着剤を塗りつけてセットキャップナット(14mm)を叩き込みます。 両端4ヶ所の穴には後ほど蓋をして空気漏れを無くします。
|
|
埋め込んだネジの頭側を下にしてMDFで組んだ上段部分にエポキシ接着剤で固定します。
|
|
|
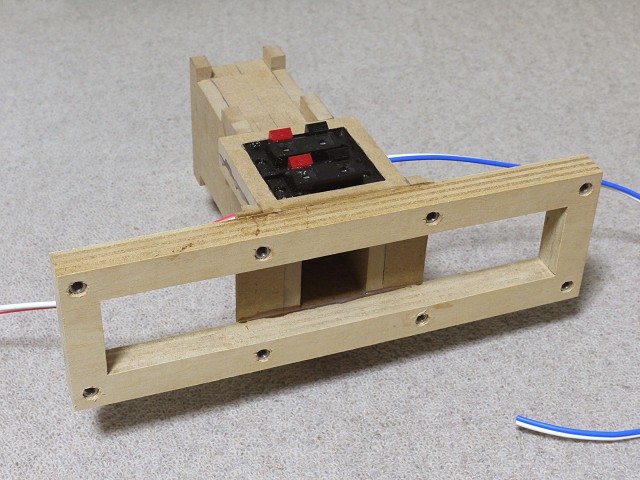 |
|
|
これでバスレフポートアセンブリーが完成しました。 この写真の手前が背面側で、スピーカー端子が見える面は底面か上面となり、向こう側が前面側です。 バスレフポートが手前左右から真中で一緒になり前面に向かって行く音道の道筋がお判りになるでしょうか?
|
|
|
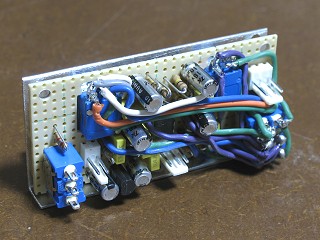 |
|
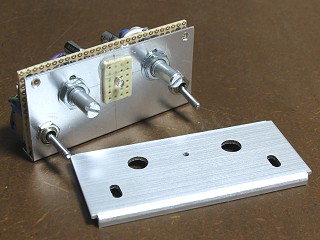 |
|
|
アルミのサブパネルを作ってそれに基板をトグルスイッチのナットで固定。 そして可変抵抗をアルミ板に固定後配線しコントロールアンプブロックとして完成しました。
|
|
手前は穴あけ加工が終わったフロントパネルで、奥がコントロールアンプブロックの前側です。 LEDは小さく切った基板に固定してサブパネルに貼り付けてあります。
|
|
|
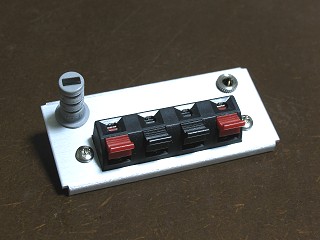 |
|
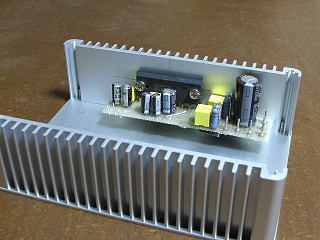 |
|
|
これはリヤーパネルで中央大きく占有しているのがスピーカーターミナル、左は電源コード用ブッシュ、右上は入力端子(ミニ・フォーンジャック)です。
|
|
パワーアンプ基板はパワーICをアルミ側板に固定する事にしました。 側板にはM3の雌ネジを切りました。 この結果ケース全体が放熱器になります。
|
|
|
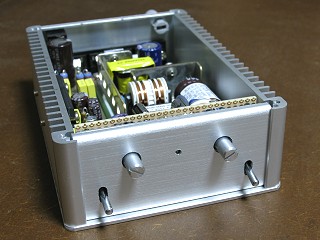 |
|
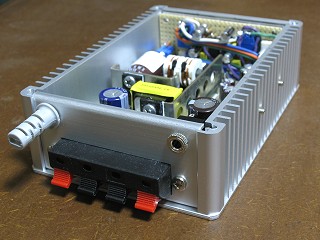 |
|
|
フロントパネル、リヤーパネルを固定しフロント側を見たところ。
|
|
同じくリヤー側を見たところ。 側面にネジが2本飛び出ていますが、後ほど長さは調整されます。
|
|
|
 |
|
|
さて問題はここから。 ごらんのとおりシールド板はまだ入れていませんが、入れたら左側の基板に付く3個のメスコネクターはシールド板に当たります。 また電源基板に付く2つのコネクターも随分とかさばるでしょう。
|
|
|
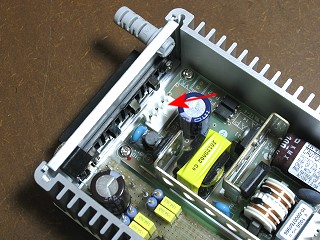 |
|
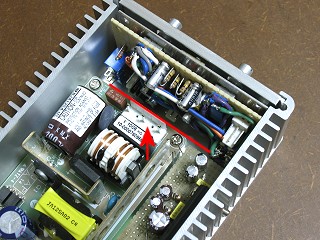 |
|
|
リヤー側では矢印のコネクターがスピーカー端子にこすれるようになります。
|
|
フロント側では矢印のコネクターはシールド板にこすれます。 また3個のコントロール基板のコネクタの先端は赤線の位置になり、シールド板に当たってしまいます。
|
|
この後に全体仕様に影響する大事なテストが残っています。 これまではスイッチング電源がパワーアンプ或いはコントロールアンプにかなり接近する所から
|
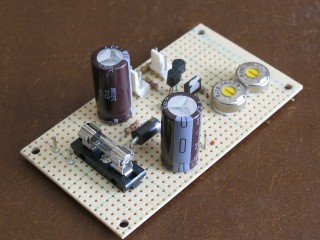 |
|
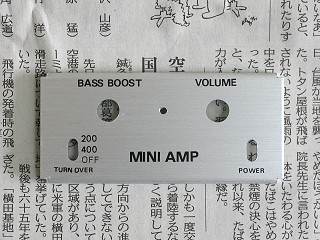 |
|
|
組み上がったスタンバイ制御基板。 スイッチング電源と同サイズにしたため充分ゆとりのあるレイアウトになっています。
|
|
最終アセンブリーの前にフロントパネルにインスタントレタリングで文字入れをしました。 その後水性ウレタンニスつや消しクリヤーを2回塗って剥がれ防止としています。
|
|
|
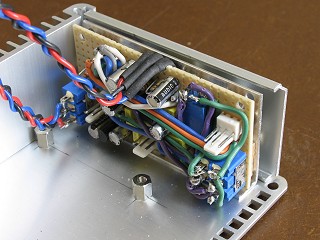 |
|
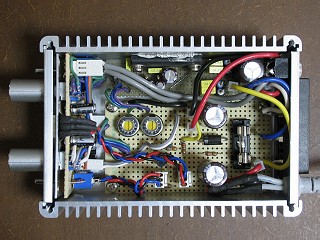 |
|
|
フロントパネル中央に見えるLEDを赤・青2色のLEDに交換し配線を中央上部より引き出しました。
|
|
全ての配線が完了しました。 結構いっぱい詰まった感じがあります。 この状態で通電し中央左の2つの丸い半固定抵抗を調節して全体のゲインを調節後に蓋を閉めます。
|
|
|
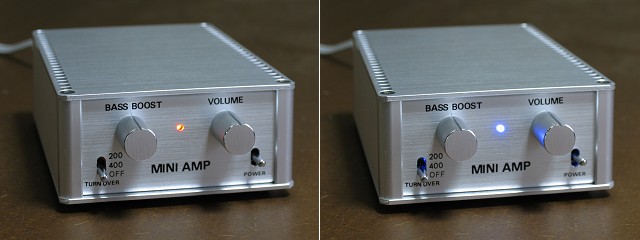 |
|
|
スイッチング電源を繋いだ状態で、アンプはスタンバイ状態にありスピーカーからは音が出ません。(左の写真) 右下に見えるスイッチのレバーを上に上げるとスタンバイ状態から解除され(ON)音が出る状態になります。 この間パイロットLEDは赤から青に変わります。 また電源スイッチはモメンタリースイッチなので、レバーは常に中央にあります。
|
|
|
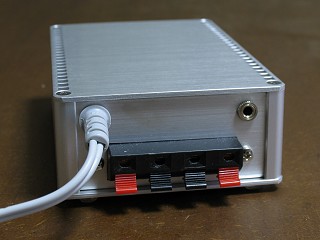 |
|
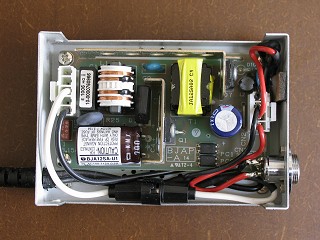 |
|
|
極めてシンプルな背面。 スペースが少ないので入力は3.5φのミニフォーンジャックを使っています。
|
|
市販の蓋付きアルミケースでは最も小さい物に何とか収めました。 また出力コネクターにはメタルコネクターを奢っています。
|
|
|
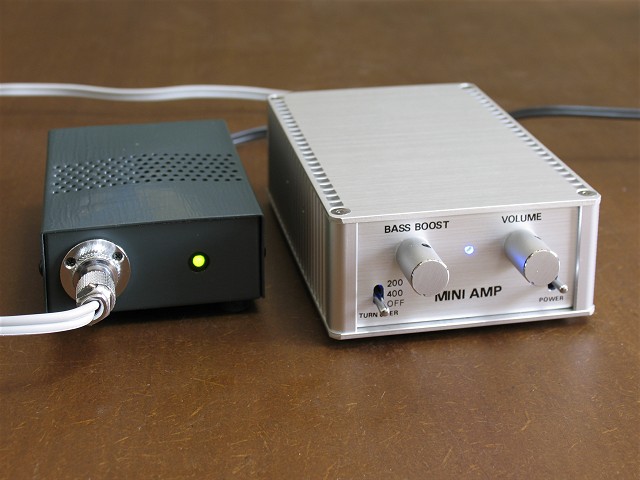 |
|
|
完成した外付けのミニアンプ。 小ささとは裏腹に大変馬力のあるサウンドを引き出してくれます。 小型スピーカーは低域補正を加えて、大きなスピーカーはフラットのままでドライブと使い分けが出来ます。
|
|
|
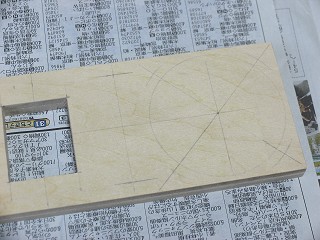 |
|
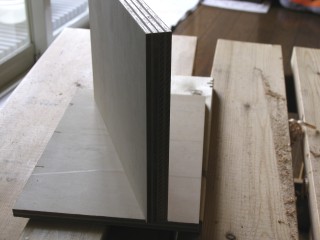 |
|
|
底板にスピーカーターミナルが飛び出る穴と前面のポート穴は予めジグソーで切断しましたが、スピーカー取り付け穴はその周辺が僅かしか残らずちょっとした事で破損しやすいので、組立後に切断します。
|
|
切断した天板と底板を合わせて立てたところです。 寸法はドンピシャになっているので高さは全く同じで、直角度が出ていますから恰も24mmの合板を立てたようで、隙間が出るようなことがありません。
|
|
|
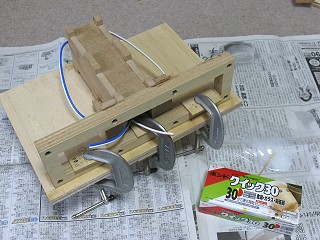 |
|
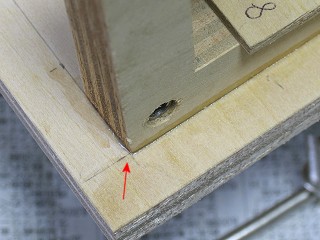 |
|
|
1回目は既に完成していたバスレフポートユニットを底板にエポキシ接着剤で貼り付け。 使ったエポキシは30分硬化開始型です。 小型C型クランプ4個で圧着保持しています。
|
|
底板には予め接着位置の墨線を引いてありますから正確に合わせないとなりません。
|
|
|
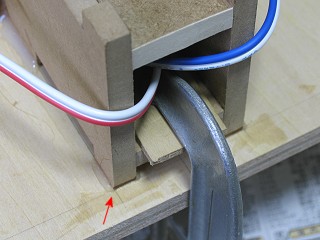 |
|
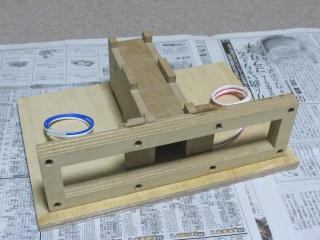 |
|
|
こちらは前面中央のバスレフポート開口部分でこちらも墨線に合わせます。
|
|
3時間寝かせてやりました。 ナイフで強い力を加えれば切断できる程度にエポキシは硬化しました。 これで次の接着作業に移ります。
|
|
|
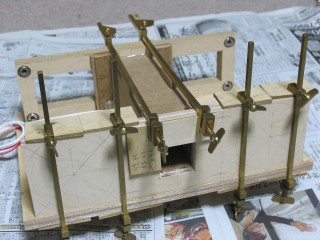 |
|
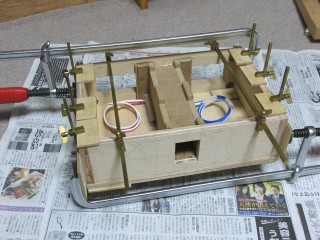 |
|
|
2回目はフロントパネルの接着です。 フロントパネルが垂直に立つよう念入りな調整が必要です。 圧着保持にはハタ金6本を使用しました。
|
|
3回目は左右の側板を貼り付けます。 一度に2枚貼るわけで調整箇所も多くなりますので素早くしかも慎重に! 圧着保持にはハタ金8本に400mmバクマクランプ2本を使いました。
|
|
|
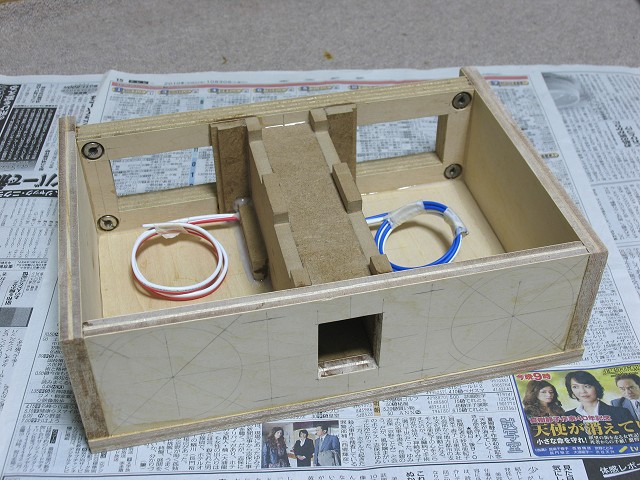 |
|
|
天板を接着すれば終わりですが、ここでスピーカー取り付け穴の切断と吸音材の貼り付けをしてからにします。
|
|
|
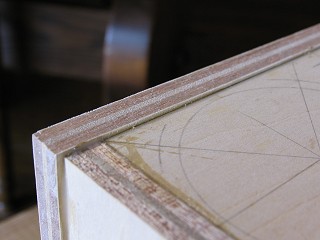 |
|
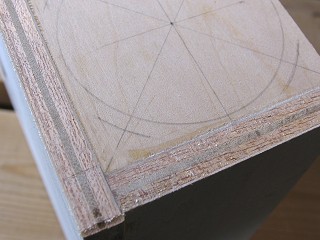 |
|
|
フロント部分を上に向けていますが、フロントパネルに貼り付けた側板の端は出っ張って接着されていますので、スピーカーの穴あけ前に出っ張りをコロ付き目地払いビットで削り落とします。 このトリマーによる切削は切削量が少ないので屋内で可能です。
|
|
切削後の写真ですが、左の写真の位置から約90度左に回転させた感じになっています。 出っ張りはご覧のように無くなり穴あけ作業がスムーズに出来ます。
|
|
|
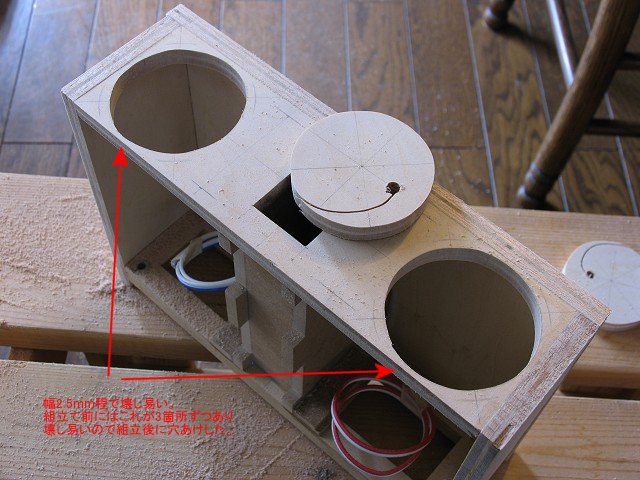 |
|
|
大きな箱でしたら箱として組立が終了してからスピーカーの穴あけをしても良いでしょうが、箱の内部が複雑で開口部面積が小さい今回のような場合箱として完成してから切断すると多量の内部に残ってしまう木屑が取り除けなくないます。 まただからと言って組み立て前にこの丸穴をあけるのは3方向に幅2.5mm程の部分があり、壊してしまう可能性があるので、この段階で穴あけをしています。
|
|
|
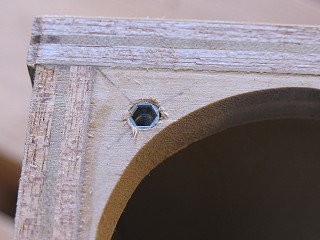 |
|
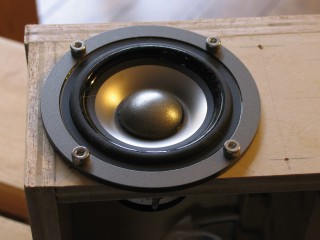 |
|
|
M4の鬼目ナットを捻じ込んだ。 スピーカーがこれにネジ止めできることを確認できてから一旦外して再度エポキシを塗り込んで完全固定する。
|
|
使ったネジはステンレスのM4 六角ボルトです。 指で摘んで締め付けられるくらいネジ位置は正確になっています。
|
|
|
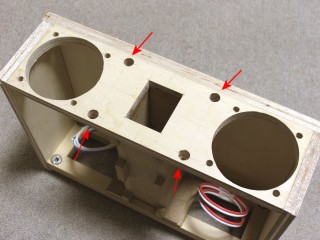 |
|
 |
|
|
フロント部分への最後の穴あけはフロントグリルホルダーメスの固定穴で10φ抜き穴ですが、この後裏側に3mm厚の板を貼って蓋をします。
|
|
実際のホルダーメス部分は最大で11φありますので、このように当てて玄翁で叩き込みますが、それは最後の塗装作業が済んでからになります。
|
|
|
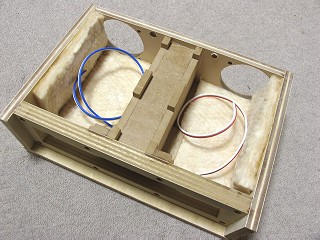 |
|
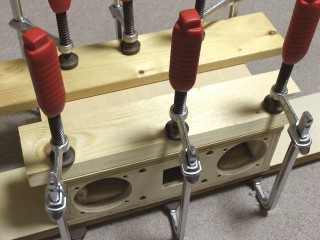 |
|
|
吸音材の私の使い方は対向面の片側だけというのが多く量は多くありませんが、今回も同様です。
|
|
そして天板をエポキシ接着剤で貼り合わせ。 バクマクランプを6本も使って何とも大げさな感じがしますが、隙間を作らないためには最低限の配慮でしょう。
|
|
|
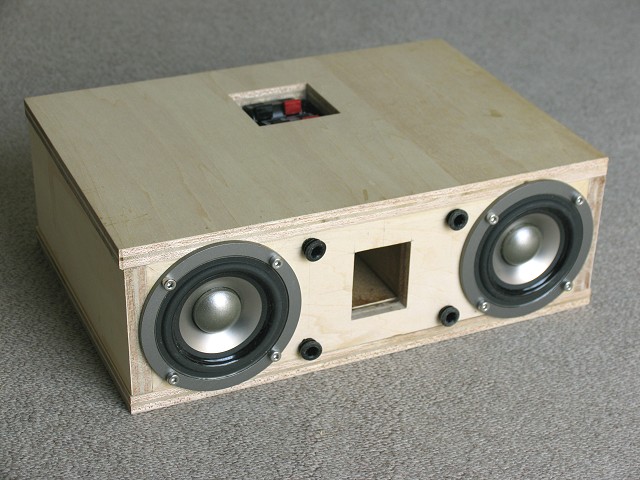 |
|
|
取り敢えずは前面接合部の段差のみを削り落とした程度です。 最終的な成形と仕上げ研磨は音のチューニングが終わった後塗装前に行います。 4箇所のフロントグリルホルダー受けを途中まで埋め込んで音漏れ防止しました。
|
|
|
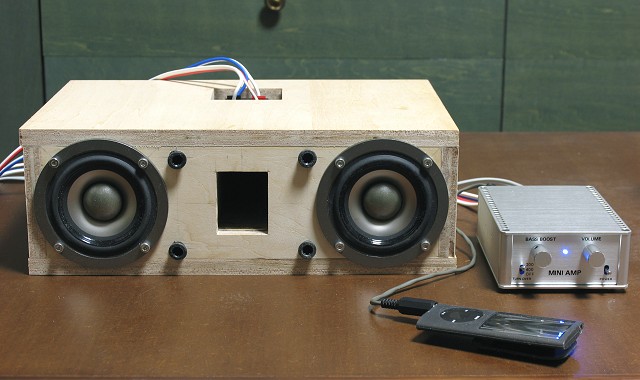 |
|
|
チューニング前の慣らし運転として1週間の間、毎日10時間位クリッピング歪を感じない程度の大音量で駆動を始めました。 アンプは既に完成したコンパクトアンプでiPod nanoが音源です。 低域補償はターンオーバー周波数を200Hz、ブーストレベルはMAXの設計値としています。
|
|
|
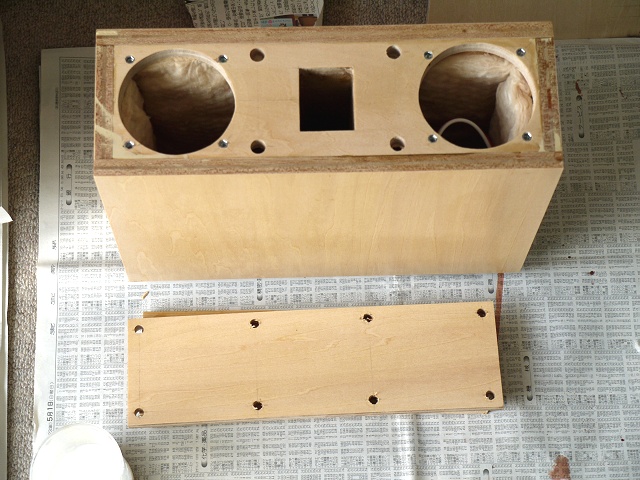 |
|
|
水性ウレタンニス透明クリヤーを3回塗りしました。 そして塗膜面を#240ペーパーで研摩してペイントの乗りが良くなるようにします。
|
|
|
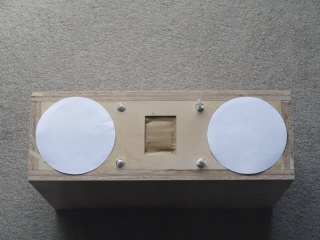 |
|
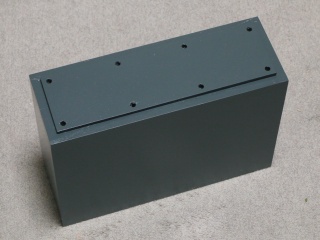 |
|
|
スピーカーユニットの外周より少し小さな円を紙に書いて切り抜きマスキングしました。 他の穴にはティッシュペーパーやダンボールを詰めています。
|
|
こうしておいて先ず前面を除く5面をディープグリーン色のスプレー塗料で2回塗りしました。
|
|
|
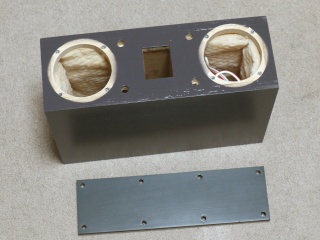 |
|
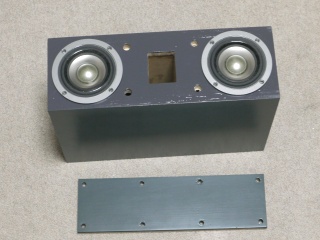 |
|
|
乾燥後にディープグリーン色で塗った部分をマスキングして前面をチャコールグレーで2回塗装しました。 このペイントは艶ありなのでピカピカ光ります。
|
|
色の組み合わせ確認のためスピーカーを乗せてみました。 ピカピカのチャコールグレーは気に入らないので艶消しをしますが、それ以外は落ち着いていて良い感じです。
|
|
|
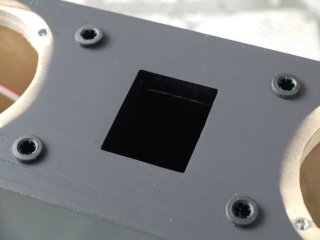 |
|
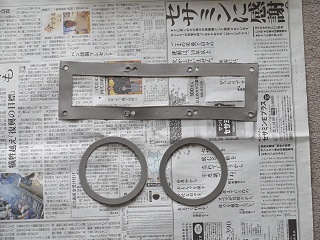 |
|
|
水性ウレタンニス艶消しクリヤーを塗りました。 安っぽいピカピカがうまく無くなりました。
|
|
スピーカーユニットと裏蓋を固定する部分に使うパッキンを作りました。 入手が容易な2mm厚発泡ポリエチレン製の物を使っています。
|
|
|
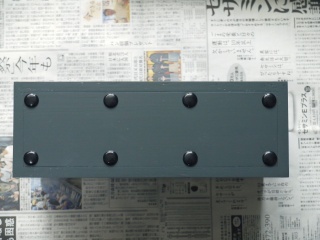 |
|
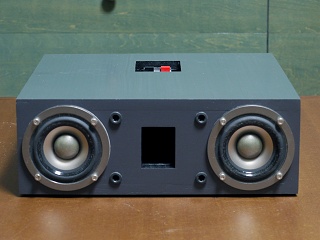 |
|
|
全体に水性ウレタンニス艶消しクリヤーを塗り物理特性を高めています。 裏板を固定した後はセットキャップボルトの頭に黒のカバーを被せました。
|
|
9.5φのクリヤーパンポンを底に貼って僅かに浮くようにしています。 これで低域の寝ぼけたような感じの音が薄れます。 そうそう私はSPターミナルのある面を上にしました。
|
|
さて残る作業は前面の保護カバーです。ボックス外形に対して内容積を目いっぱい稼ぎたかったため、私のスピーカーボックス製作では常識としているフロントグリルは全く製作することなど考えてはいませんでした。 上でも触れたようにパブリックなスペースで使う事は殆ど考えられませんから、ユニットを壊すチャンスも少ないのですが、ただひとつだけポータブルスピーカーとして運ぶ時にスピーカーを壊してしまう可能性が非常にあります。 そこで通常のフロントグリルではなくフロント保護カバーを作ろうというのが目的です。
|
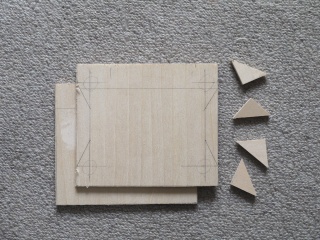 |
|
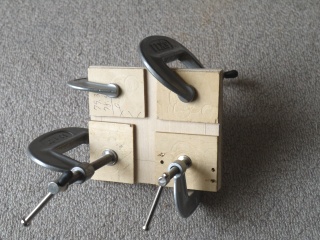 |
|
|
4mmシナ合板から切り出した部材。 シナの材料はこれ以外に5.5mm合板とシナ木口テープを使います。
|
|
正方形に近い2枚は貼り合わせて接着剤が硬化後に所定の形に成形します。
|
|
|
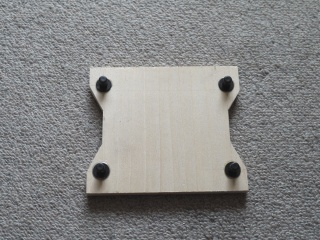 |
|
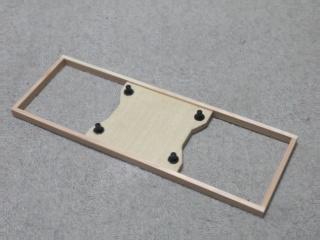 |
|
|
電動ジグソーで所定の形に成形切断し替刃式ヤスリで切断面を研摩しました。 その後固定するブッシュのオスをエポキシ接着剤で固定しますが、1箇所だけ0.5mmほど位置がずれていたので、ヤスリで穴を削って修正しました。
|
|
ヒノキ棒で周りを囲みました。 この枠のタテ・ヨコはスピーカーボックス断面の寸法より1mmずつ小さくなっていますが、これはこの後シナの木口テープを貼る事によりたて・ヨコそれぞれ1mm大きくなるのを補正するためです。
|
|
|
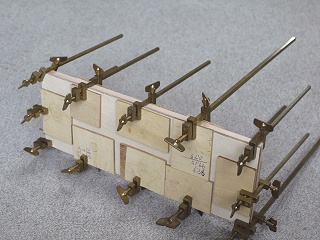 |
|
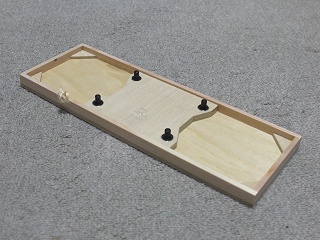 |
|
|
出来上がった枠に5.5mm厚シナ合板を貼り付けます。
|
|
接着剤が硬化したら内側4隅に3角形の補強板(4mm厚)を貼り付けます。 また外周の面(ヒノキ棒と5.5mmシナ合板)がツライチになるよう研摩します。
|
|
|
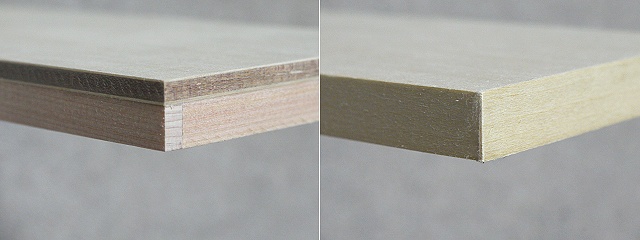 |
|
|
外周はこんな具合になりますが(左側)、決して綺麗とは言えないので、シナの木口テープを全周に貼り付けてやると前面シナの木目に変貌し、見違えるほど綺麗になります。(右側)
|
|
|
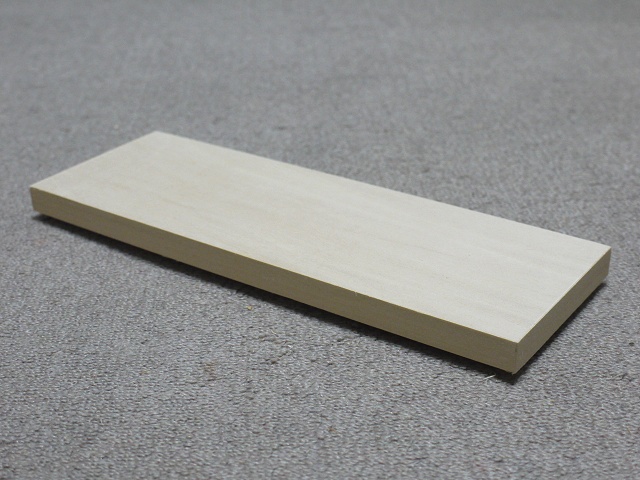 |
|
|
これで加工・組立は全て終了しました。 残る塗装前の仕上げ研摩を、#240、#400のサンドペーパーでやっておきます。
|
|
|
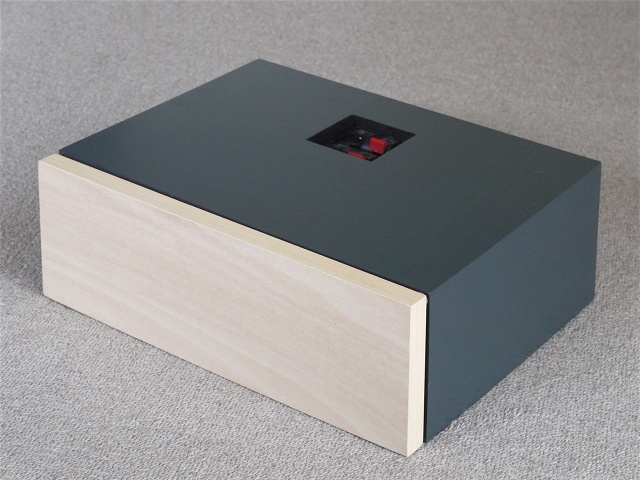 |
|
|
毎回同じ塗装作業をお見せするのは省きましたが、水性ウレタンニス透明クリヤー3回塗り、最後に水性ウレタン艶消しクリヤー1回塗りです。(無論間に#400-#600での研摩作業が入ります。) 濃い緑色の本体と明るい木目のカバーのコントラストが綺麗です。
|
|
|
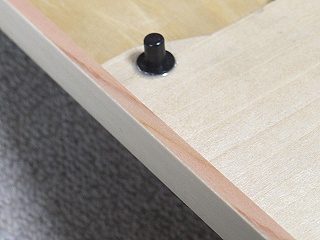 |
|
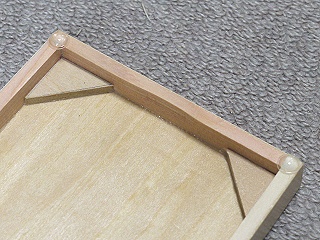 |
|
|
説明不要でしょうが、桧の棒の赤い部分と外側のシナの白っぽい木目が隣り合わせの奇妙な光景です。
|
|
カバーの内側4隅には本体に傷を付けないために8φのクリヤーパンポンを貼っています。
|
|
|
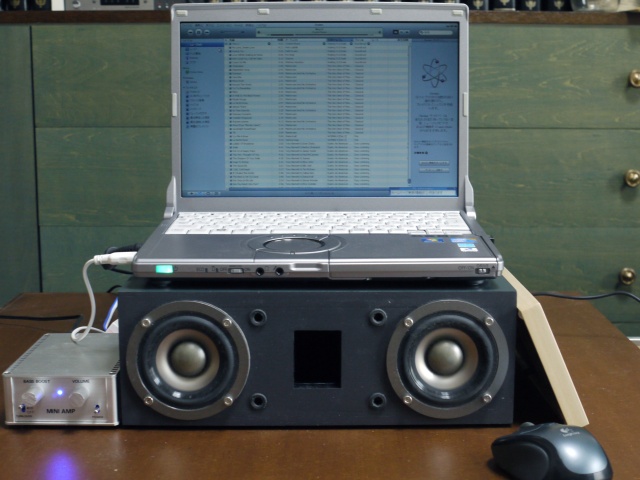 |
|
|
実際に使うスタイルにセットアップしました。 ノートブックPC用スピーカー2の方がコンパクトで豪華な感じに見えますが、音質は圧倒的な差でこちらの方が良いです。 従って上に載っているパソコンを外部に持ち出すときにはノートブックPC用スピーカー2と組み合わせ、普段はこの状態で机の上で使うことになります。
|
|
正直言って2つのノートブックPC用スピーカーを作っても2者択一になり、どちらかのスピーカーは使わなくなると想像していました。 しかし結果は両方が生きるという結果になり私は大変満足しています。 こうなった大きな要因は常識を超えた高性能の80mmユニットであるCopyright (C) 2001-2019, Vic Ohashi All rights reserved.