|
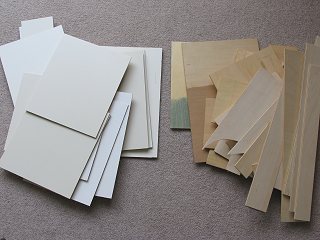 |
|
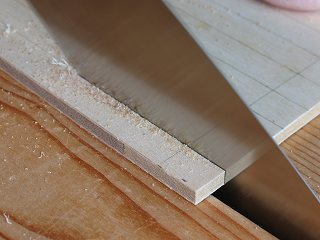 |
|
|
使用候補の端材、左が2.5mm厚カラー合板で額縁を作った時の残り。 右は4mm厚と5.5mm厚のシナ合板で着色されたり日焼けした物もありますがペイントで塗装するので使えます。
|
|
スペーサーとなる幅12mm厚さ5.5mmの板は13mm毎に線を引き翔250でいきなり連続して切断しました。 ちょっぴり高度なやり方ですが、こちらで詳しく解説しています。
|
|
|
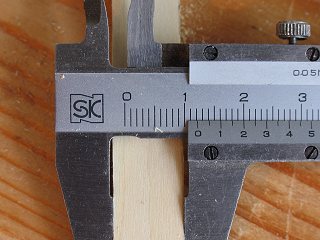 |
|
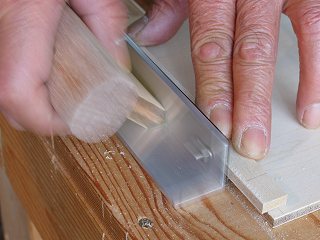 |
|
|
こうして切った板の幅は切断誤差を含めて12.2mm±0.2mm程度になります。 若干の幅広となるわけで、ノギスで実測したこの例では1.2mmでした。
|
|
それを先週ご紹介した直角研磨ヤスリでドンピシャ寸法(12.0mm)に調整します。 こんな作業にはもってこいの道具です。
|
|
|
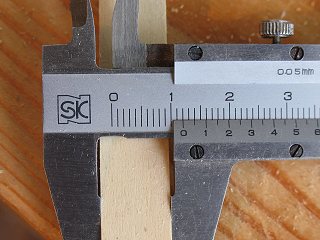 |
|
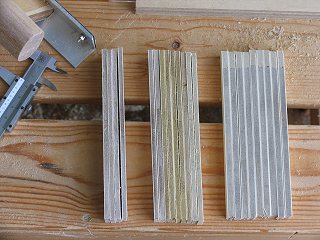 |
|
|
調整研磨を施した後の実測。 撮影時の視差があるのですが、12.0mmになっています。
|
|
その他の4mm厚合板で作るスペーサーを切り出しました。 これらが内箱の両側板に貼り合わせる2組と真中の仕切りを作る1組になります。
|
|
|
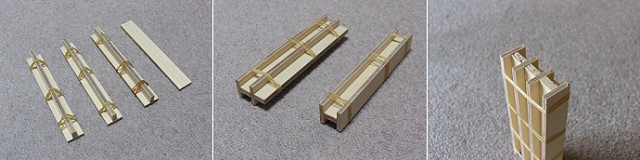 |
|
|
仕切り板の組立て開始。 これは中央に挿入するものですが、ボンド接着の圧着保持にはゴムバンドを使っています。 T字型3組を接着(左)、T字型2組を連結、残りのT字型をH型に接着(中)、それらを連結でそれぞれ乾燥時間1時間。
|
|
|
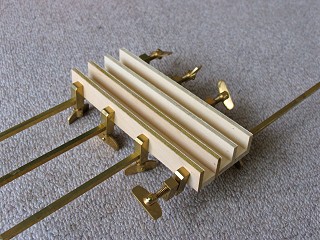 |
|
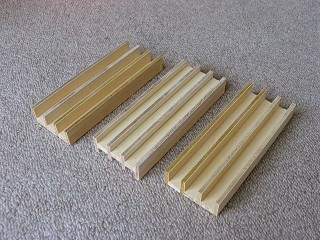 |
|
|
両端の仕切り板はゴムバンドで圧着保持できませんからハタ金を使い同様に組み立てました。
|
|
完成した3組の仕切り板。 それぞれの幅は設計値52mmに対し51mmと若干短くなりました。 原因は4mm厚の合板で実測すると3.75mmしかなく4枚使用のため1mm短くなったというわけです。 これに合わせて設計寸法の微調整をしています。
|
|
|
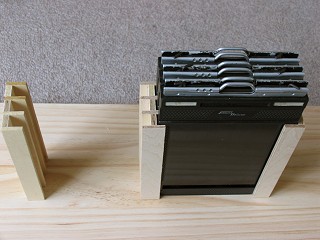 |
|
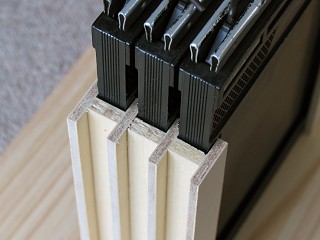 |
|
|
3つの仕切り板はこのような位置に内箱側版4枚に挟まれ、フィルムホルダーが挿入されます。
|
|
フィルムホルダーの上部は少し厚みが増しますが、隣どおしがぶつかりあうことはありません。
|
|
|
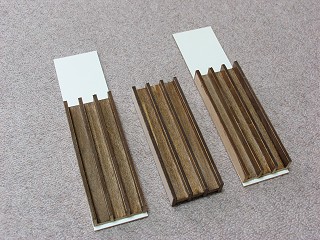 |
|
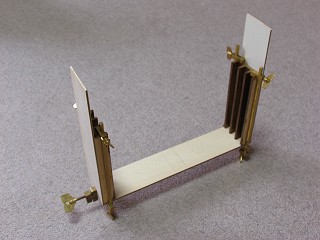 |
|
|
仕切り板の内側を着色ニス(エボニー色)で塗装後、エポキシ接着剤(5分硬化開始型)で側板に接着しました。
|
|
2枚の側板と底板をエポキシ接着剤(5分硬化開始型)で接着し、ハタ金5本を使って圧着保持しています。
|
|
|
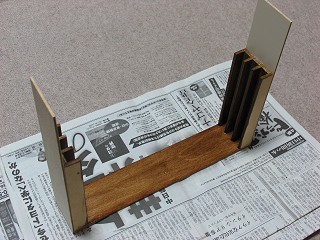 |
|
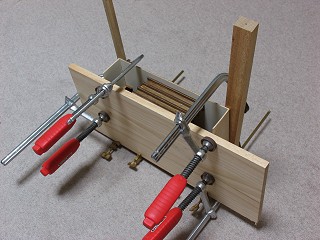 |
|
|
そして底板の内面を着色ニスで塗装。 塗装しては組み立てる!というやりかたは効率的ではありませんが、余計なところを塗装しないためにはこの方法が確実です。
|
|
塗料乾燥後長手方向の側板を接着。 圧着作業に時間が掛かるので60分硬化開始型エポキシを使用。 撓み防止のために全体を厚い板に当てたり、未接着の中央仕切り板を挿入しながら、ハタ金4本とバクマクランプ4本で圧着保持。 この状態で1晩寝かします。
|
|
|
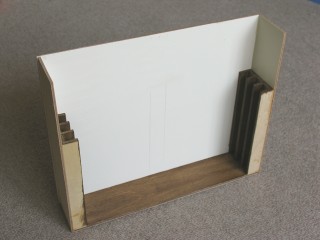 |
|
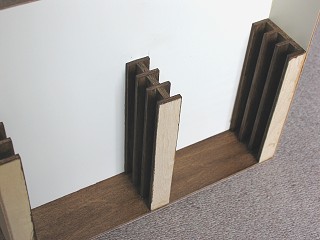 |
|
|
歪んだまま接着しやすい恐らく一番の難関部分が無事終わりました。 測ったところ寸法誤差は0.5mm以下。 歪み・ゆがみはほぼゼロです。
|
|
中央の仕切り板を5分硬化開始型エポキシで接着しました。 ここまでの切断開始以来の作業時間は丸2日掛かっています。
|
|
|
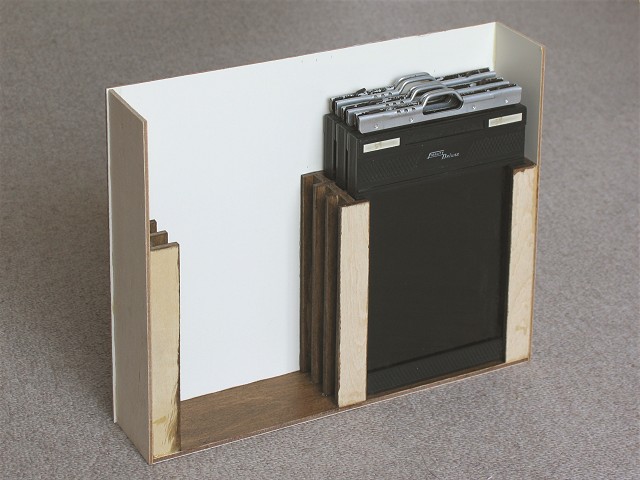 |
|
|
試しにフィルムホルダー3個を装填してみました。 勿論スムーズに入りますしかなりの強度が取れていて見た目よりも丈夫そうです。 まだ内箱として完成してませんが、一番の難関らしきところは無事通過し残る作業は淡々と進むと思われます。
|
|
小箱とは言え板厚が
|
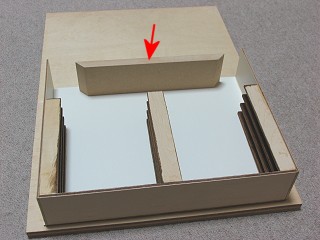 |
|
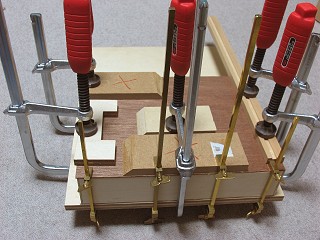 |
|
|
捩れ防止のため箱を全体が乗るような板に寝かせます。 矢印は内寸と同一幅に切断した板で、圧着保持の際箱が潰れないためのもので、接着終了後外します。
|
|
最後の内箱側板を60分硬化開始型エポキシで接着し圧着保持しています。 大袈裟なようですが全ての部分を密着させるにはこの位はごく普通と考えたほうが良いです。 そして6時間放置します。
|
|
|
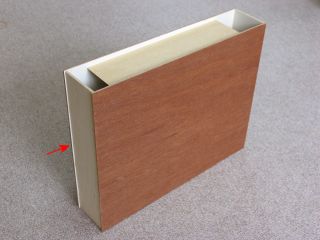 |
|
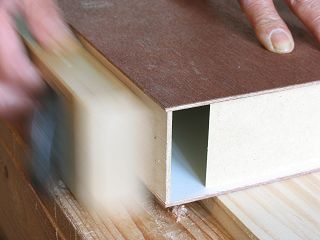 |
|
|
クランプを外しました。 矢印の先が若干飛び手いるのが判りますが、これは意識して側板を1mmずつ大きく切断したためです。
|
|
その僅かな出っ張りの大半ををカンナで削り落とします。
|
|
|
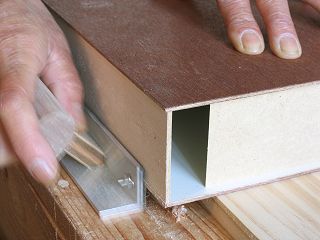 |
|
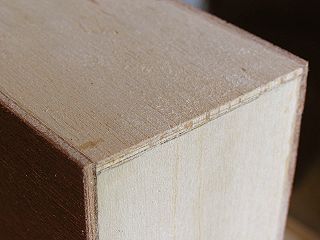 |
|
|
本の僅か(0.2mm前後?)残った出っ張りは直角ヤスリで削って段差を完全に無くします。
|
|
こうして接合面の段差を完全に落とし、各部寸法が設計どおりで捩れもないことを確認します。
|
|
|
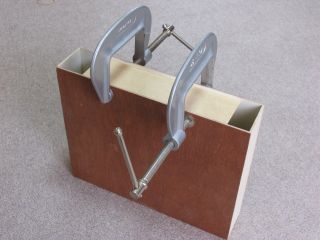 |
|
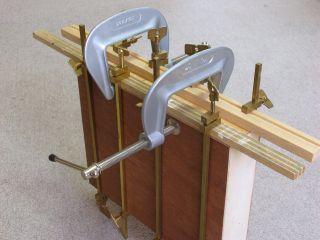 |
|
|
内箱最後の天板貼りの前に前の工程で使ったスペーサーを挿入しクランプで挟みました。 このクランプは箱の上下の切り離し作業が終わるまで緩めません。(中で移動してしまうと切り離しが厄介になります。)
|
|
そして天板を5分硬化開始型エポキシで接着しハタ金で圧着保持します。
|
|
|
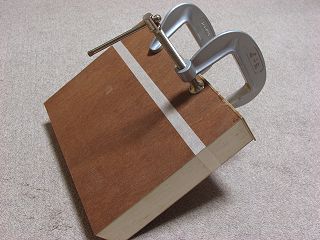 |
|
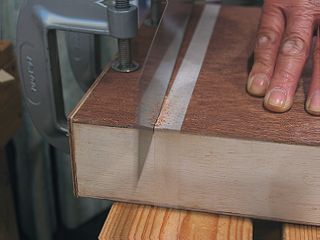 |
|
|
2時間後に上下の切り離し位置にマスキングテープを貼り付けいよいよ切断開始です。
|
|
角から切り込んでゆきますが、側板の短いほうは数センチ切り込んだらそこで止めてノコギリの先端だけで長い側版のほうだけを切り込んでゆきます。 ご覧のようにクランプは締め付けたまま。
|
|
|
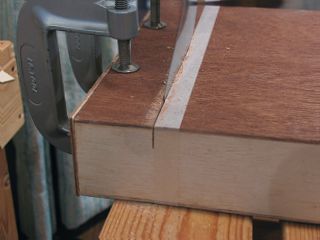 |
|
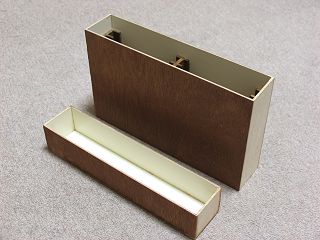 |
|
|
その様子はこんな具合。 薄い板ですから簡単に切断できますが、片手でノコギリを握るため直線性を保つのは意外に難しく注意が必要です。 端まで切り込んだら反対側の短い側板を切り落とさず上下を反対にして同じく長い側板を切断。 その後クランプを外して短い側板2枚を切り落とします。(こうしないとクランプの重みで切断終了寸前に割れてしまいます。)
|
|
切断した切り口を替刃式直角ヤスリで研磨し、直線性と切断面の直角出し、寸法出しをやって内箱が完成です。 ほっと一安心の一瞬と言えます。
|
|
|
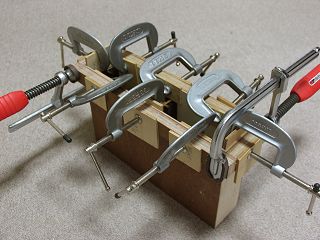 |
|
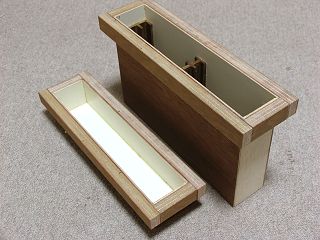 |
|
|
上下に分離した箱の口の周りに15mm厚合板を切った補強棒を貼り付けます。 ここから暫しは木工ボンドで接着です。
|
|
補強棒の貼り付けが完了した上下の内箱です。
|
|
|
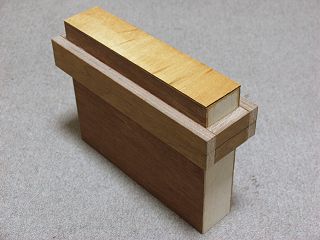 |
|
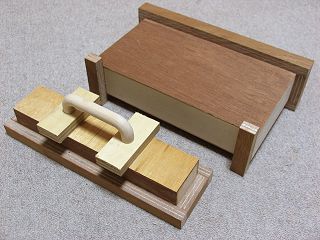 |
|
|
重ね合わせると殆ど隙間なく載りますし、寸法も設計値に対し±0.2mm程度に収まっています。 これは正確な切断と接着時のやりすぎ?とも思える圧着保持の賜物です。
|
|
上下の補強棒を木工ボンドで接着。 右上の本体下部の補強棒部分にはゴム脚が、左下の補強棒部分には木製取っ手(写真では載せているだけ。)を固定の予定です。
|
|
|
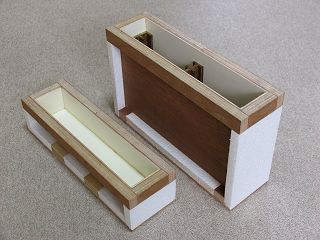 |
|
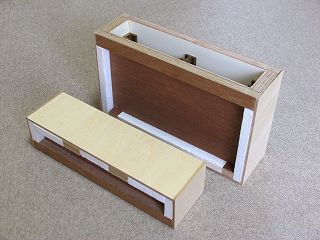 |
|
|
外箱は間に発泡スチロールを挿入して天板と底板の接着からスタート。 天板は設計時と異なり5.5mm厚に変更したので内側に接着に変更しています。 更に幅狭の側板側に発泡スチロールを挿入。
|
|
幅の狭い方の側板を接着。 前の写真も含め圧着保持にはハタ金やクランプ総動員は相変わらずです。
|
|
|
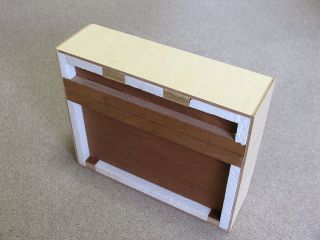 |
|
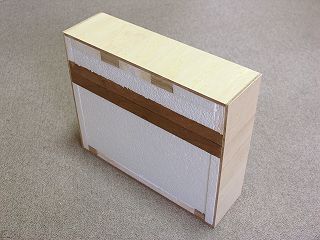 |
|
|
最後の側板を接着する前に念のために組立て誤差のチェック。 設計値に対し絶対誤差は最大で+0.5mmありますが相対誤差はほぼゼロになっています。
|
|
残る空間に発泡スチロール板を挿入して側板を貼る準備が整いました。 これで補強板部分を除き内箱と外箱の間は発泡スチロールで埋まったことになります。
|
|
|
 |
|
|
長手方向の側板を接着し接合部分の段差を削り落とし寸法の微調整が終わった箱。 発泡スチロールは完全に覆われてもう見えません。 大変時間が掛かっていますが大半は接着剤の乾燥硬化時間に費やされています。
|
|
|
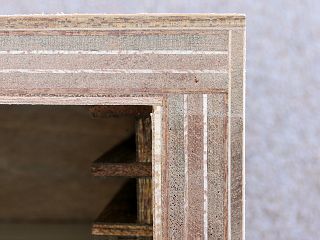 |
|
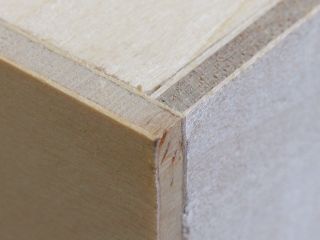 |
|
|
接合断面の拡大写真。 内側から2.5mm、15mm、4mmの板が交互に貼りあわされているのが良く判ると思います。 密着度が高いですから大変丈夫で22mmの厚板と同等です。
|
|
蓋の部分の角を上方からクローズアップ。 4mmの合板の突合せになっていますが、接着時の圧着保持が確実にやられているので隙間もなく剥がれる心配も先ずありません。
|
|
薄い板を貼り合わせて作る方法は私のよくやる手法で、一つ一つの作業(切断、切断面研磨・寸法出し、接着など)は難易度が低いのですが、それらを繰り返して行くうちに僅かな誤差が集積されて寸法が大きく狂ったり、捩れたりするので油断は禁物で慎重な作業の進め方が肝要です。 しかしひとつのやり方としてマスターしておくと色々なテーマに応用が出来ます。 次回には仕上げ研磨、金具などの取り付け、そして塗装と完成までの様子をお伝えいたします。
|
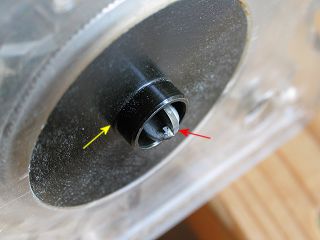 |
|
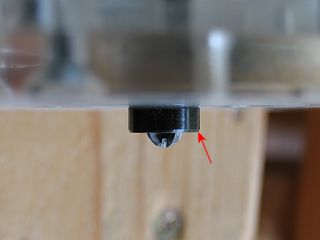 |
|
|
ダブテールガイド(黄色矢印の黒い部分)と6mm U溝ビット(赤矢印)を電動トリマーに取り付けて所定の位置にセットし準備OKの状態です。
|
|
ビット先端を真横から見るとこんな具合。 上記解説中のこの図面と見比べてください。
|
|
|
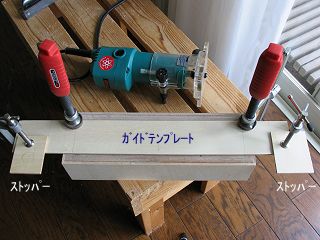 |
|
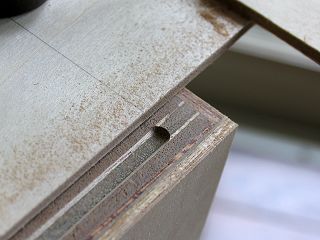 |
|
|
即席のテンプレート(ジグ)を固定した様子。 本来は長方形の所定の大きさに切断した1枚でOKなのですが、4mm合板は幅狭な物しかなかったので、直線切削4回、角丸切削4回に分けています。
|
|
直線切削の端にはストッパー(右上に見える板)を取り付けているので、正確に停止位置を決められます。
|
|
|
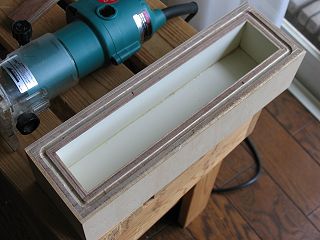 |
|
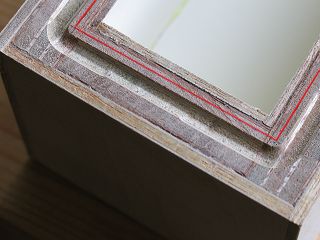 |
|
|
直線切削4回、角丸切削4回によりU溝は無事繋がりました。
|
|
そのアップでガイドテンプレートの端の位置を赤線で描き込んでみました。 ここにテンプレートの端があったわけです。
|
|
|
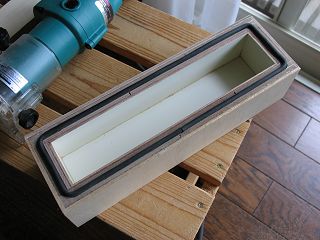 |
|
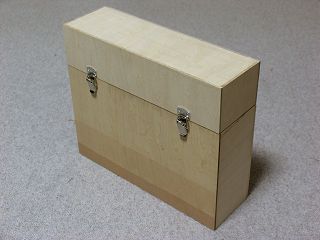 |
|
|
U溝の底に両面接着テープを貼り付けて、丸ゴム紐を貼り付けました。 これは塗装前に剥がして最終的には塗装後にボンドG-17で接着します。
|
|
蝶番とパチン錠をネジ止めしパチン錠で蓋をロックし確認しました。 蓋と本体の隙間は後ろ側で約1mm、前側は1mm弱になるようにしています。
|
|
|
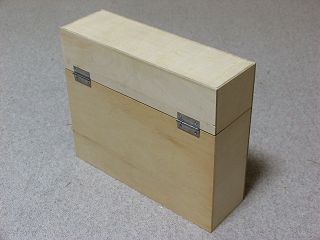 |
|
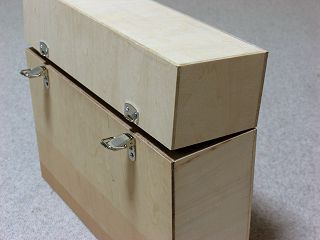 |
|
|
これは後ろ側の眺め。 本文にあるように見てくれよりも強度重視の蝶番取付けですが、ステンレスであり後で角を丸めて少しでも見え方が良くなるようにするつもりです。
|
|
パチン錠を緩めるとご覧のとおり蓋はかなり浮き上がります。 よってパチン錠ロックにより完全に密封され炎天下でも外気は中に入りません。
|
|
|
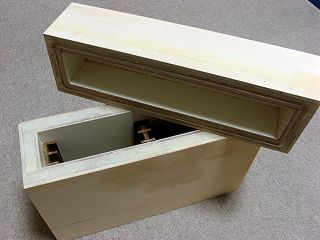 |
|
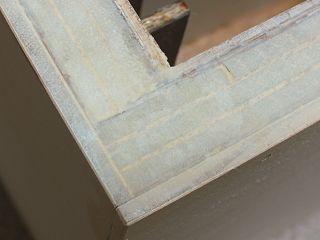 |
|
|
パテを継ぎ目の部分、木口で木繊維切り口が見える部分、凹み、傷に擦り込んで乾燥後ペーパーで研磨し、角部分も若干の面取りをした上で塗装の準備が整いました。
|
|
とは言ってもアップしないとその違いが判らないので、数枚撮りました。 これは合板の木口部分。 木繊維の穴は完全にパテで潰されています。
|
|
|
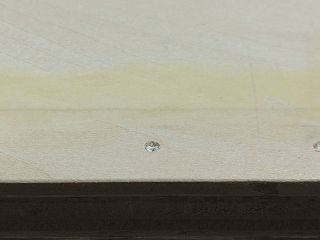 |
|
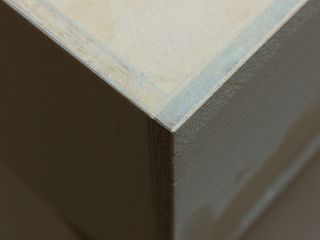 |
|
|
こちらは蓋の一部ですが、板幅が足らなくて継いだ部分で、その継ぎ目は中央横に走っている薄っすらとした黒い線。 勿論継ぎ目の溝、段差は残っていません。 下に見えるのは蝶番固定のネジ穴でこれはお構いなし。
|
|
そしてこちらは蓋の上面角。 これも継ぎ目が色が違うことで判りますが、段差、溝共に無くなっています。 ここまで潰しておけば後の作業は楽になります。
|
|
|
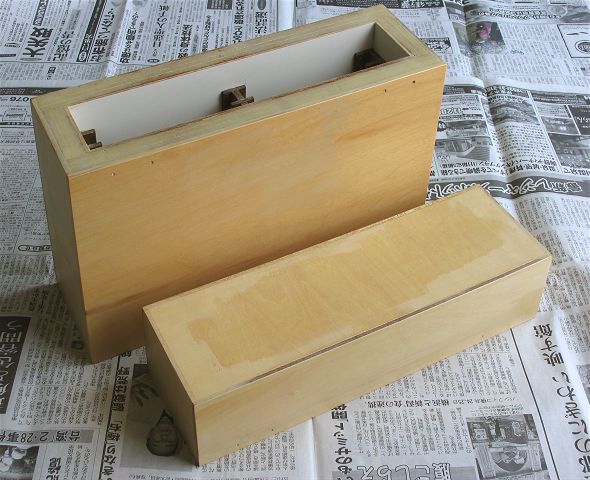 |
|
|
油性ウレタンニスを2回塗りし乾燥しているところです。 手持ちの都合でここではつや消しタイプを使っていますので、艶が殆ど見えていません。 またパテを塗ったところが明らかに判ります。 ニスで仕上げる場合にはパテは使えない所以ですが、ここでは下地作り(シーラー)として使っているので構いません。 通常より長い12時間寝かせ完全乾燥させてからスプレー塗料の載りを良くするため表面をサンドペーパーで均等に粗び目をつけます。
|
|
|
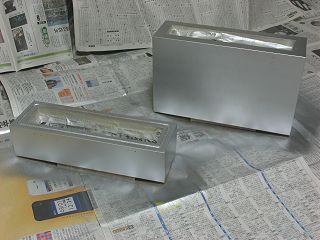 |
|
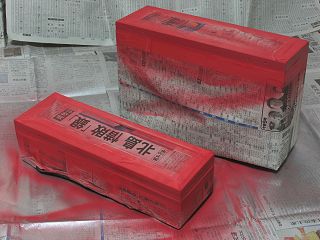 |
|
|
遮熱の第一歩は熱を反射する仕上げと言うことでシルバー色のスプレー塗装で塗りました。 白でも良いのですが、過去の経験では汚れが目立ちやすいのでシルバーにしています。
|
|
太陽からの輻射熱を反射するには全てが反射しやすい色で仕上げた方がよいのですが、単調で面白くないので赤い線をアクセントに入れました。
|
|
|
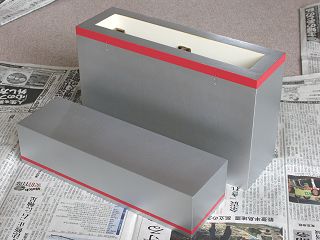 |
|
 |
|
|
赤い線部分が乾燥したところでペイント塗装は終わりでこの後、表面の軽い粗し研磨の後に最後の水性ウレタンニス(つや消しクリヤー)2回塗りによりコーティング。
|
|
水性ウレタンニスつや消しでコーティング後です。 油性ニスと違い黄変が殆どないので写真では左と変わらないように見えますが、ウレタン皮膜で覆われた表面はより丈夫になります。
|
|
|
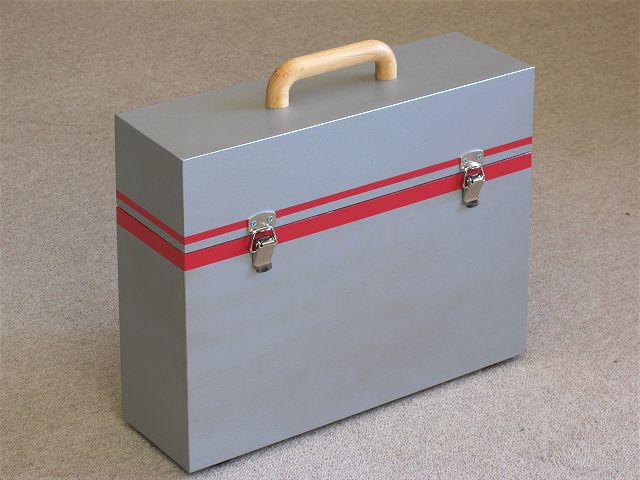 |
|
|
丸ゴム紐を接着、蝶番、パチン錠、ゴム脚、取っ手を取り付けて完成しました。 本体はペイント塗りつぶしですから木工という感じがしませんが、取っ手だけは生地に油性ウレタンニスで仕上げましたので、辛うじて木工作品らしさを残せたと思います。
|
|
|
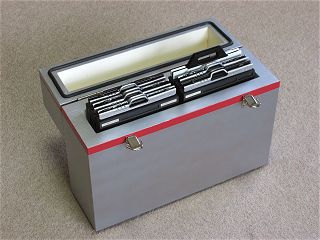 |
|
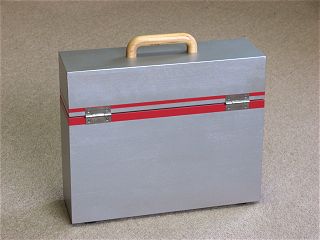 |
|
|
丸ゴム紐はボンドG-17クリヤーを使って接着しました。 本当はグレー色であると良かったのですが、残念ながら黒の物しかありませんでした。
|
|
裏側は赤のストライプを上下の端を丸見えになっている蝶番に合わせ、少しでも見栄え改善になればと塗装しています。
|
|
|
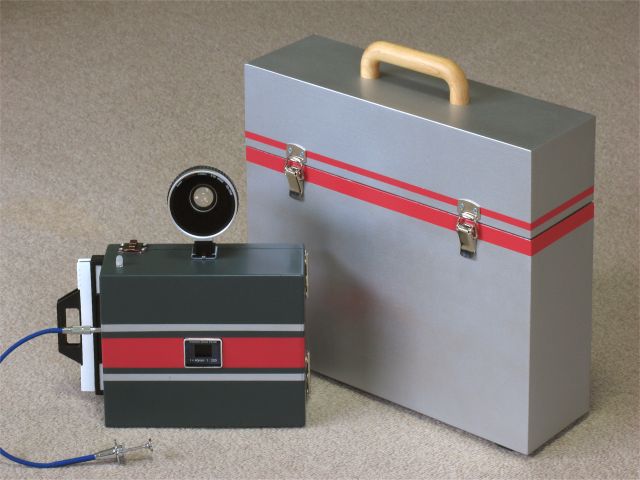 |
|
|
このキャリングケースと相棒となる 4 x 5判ピンホールカメラとのツーショット。 今後この組み合わせが私のピンホール写真撮影で活躍します。
|
|
|
翌日遮熱・断熱性能がどの程度かを確認するために内容積を同じにしたダンボールの箱を作りそれぞれに温度計を入れ
て、ベランダで2時間太陽光線に晒しました。
とはいってもこの手のテストには絶好とはいえない環境です。 曇ったり晴れたりの繰り返しで気温や湿度が低く、風もそ
よそよと適度にあり、直射日光下でも暑さを感じないすこぶる快適な日でしたので、箱の断熱効果があまりなくても箱の
内部の温度がそれ程上がることはないと予測しています。
気象庁の予報では今週はこんな天気との事ですので、傾向を掴めれば取り敢えずよかろうと始めています。
|
|
|
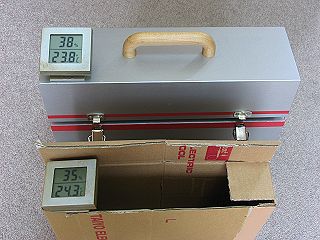 |
|
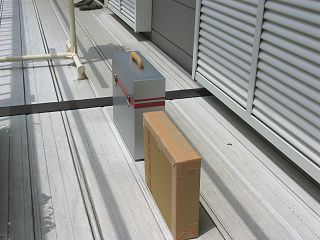 |
|
|
内容積が同じ箱をダンボールで作り出来上がったキャリングケースと遮熱・断熱のテスト開始。 それぞれに温・湿度計を入れますが、ダンボール側は24.3℃/35%、キャリングケース側が23.8℃/38%の表示になっており何れも室内です。
|
|
ダンボール、キャリングケース何れも密封しベランダで太陽の直射日光が指す場所に置きました。 テスト開始は5/29 10:45分です。 この写真では日が当たっていますが数分毎に日が陰る状態で理想的とは言えません。
|
|
|
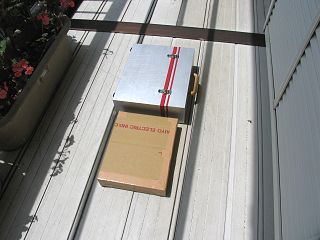 |
|
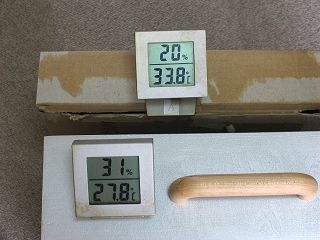 |
|
|
スタートして10数分も立たないうちに問題発見。 軽いダンボール箱は僅かな風で倒れます。 そこで両方とも寝かせてテストを続行。 実際の使用状態とはいえませんが、この方が太陽の輻射熱は強くなります。 また銀色塗装の反射は強烈です。
|
|
2時間後に室内に持ち込み開封して温・湿度計を取り出し素早く撮影しました。 尚写真を撮ってはいませんが、この時の室温(風通しがよい)は24.5℃、湿度が34%となっています。
|
|
|
考察: 自作キャリングケースの内部温度上昇は3.5℃、一方ダンボールの内部温度上昇は10℃ということで一応断熱効
果のあることは確認できました。 但しポータブルクーラーなどに比較すれば断熱・遮熱効果はかなり低いと言わざるを
得ないのかな? と思われます。 最もフィルムそのものを長期保存するのが目的ではなく、炎天下で数時間ケースを
晒しても中のフィルムが使用不能になるのを防止!ということですから、目的は十分果たせるでしょう。
|
|
Copyright (C) 2001-2019, Vic Ohashi All rights reserved.