|
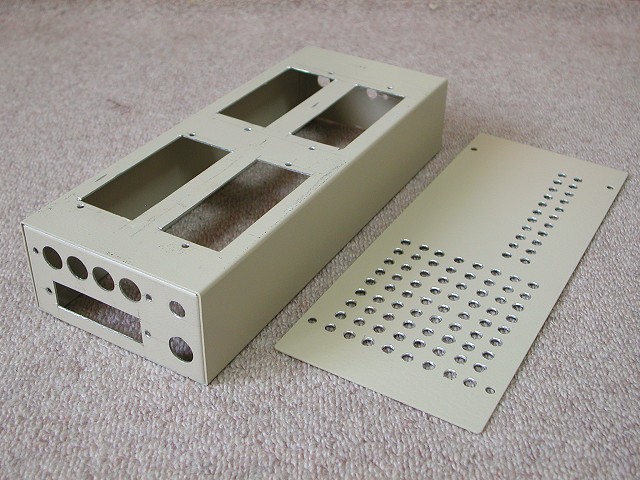 |
|
|
先週あけた四角い穴に続き丸穴をあけ終わりましたが、右に見える底板の沢山の穴を始め量が多いのと加工精度をシビヤーに抑えたい部分もあり、結局1日がかりになってしまいました。
|
|
|
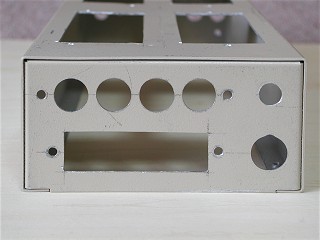 |
|
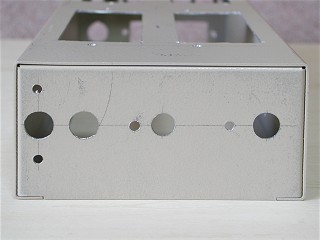 |
|
|
背面パネルは完成後唯一目に触れる面なので最も慎重に加工しました。 大きな丸穴5個は8φの穴をあけてから丸棒ヤスリで削り最後は替刃式ヤスリ(RS-310P)で仕上げています。
|
|
前面の丸穴中、中央と右端の穴はボリュームとスイッチが付きますが、飾り前板にあける穴との位置関係が狂うと芯ずれで見苦しくなるので位置関係を正確に加工しています。
|
|
|
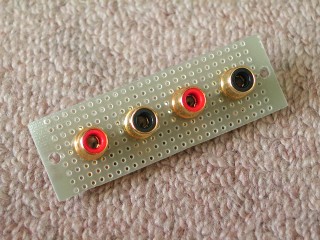 |
|
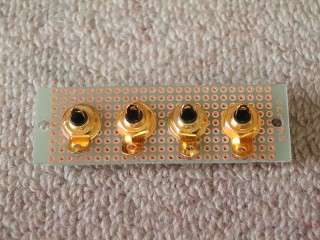 |
|
|
市販の入力端子盤が使えないので、ピン4個を1.5mm厚グラスエポキシ板を加工して取り付けました。 このグラスエポキシ板は穴あきプリント基板の流用です。
|
|
その裏面。 丸い銅箔部分を剥がさずに使っていますがピン同士は電気的に絶縁された状態になっています。
|
|
|
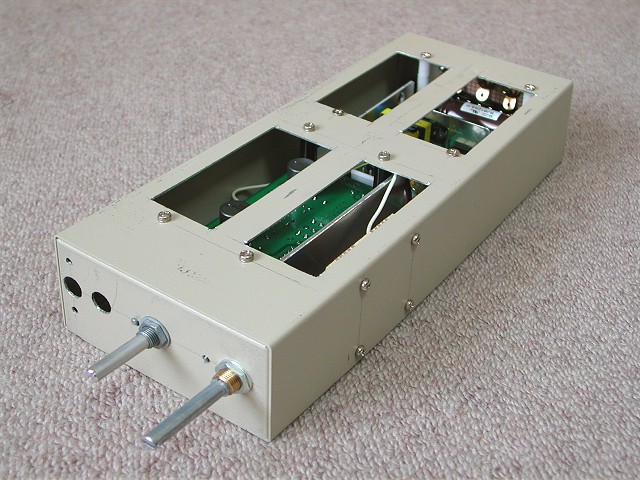 |
|
|
穴あけが終了したアルミケースに加工上の問題がないか主要部材を取り付けて確認しました。 ボリュームとスイッチのシャフトは所定の長さに切断せねばなりません。 また左側の穴はLED配線がとおる穴と電源スイッチアセンブリーを固定する穴です。
|
|
|
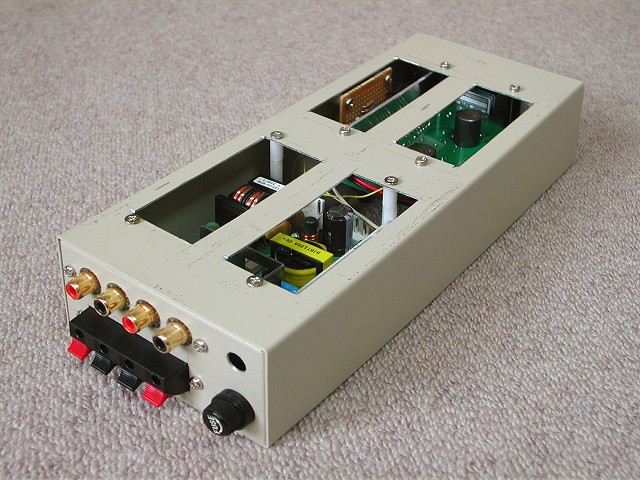 |
|
|
背面はご覧のとおりぎりぎりいっぱいにスペースを使った感じです。 右下は追加したフューズホルダーでその上の穴にコードブッシュがとおります。 上面の穴を通して見えるのは手前が電源基板で、奥がアンプ基板です。
|
|
|
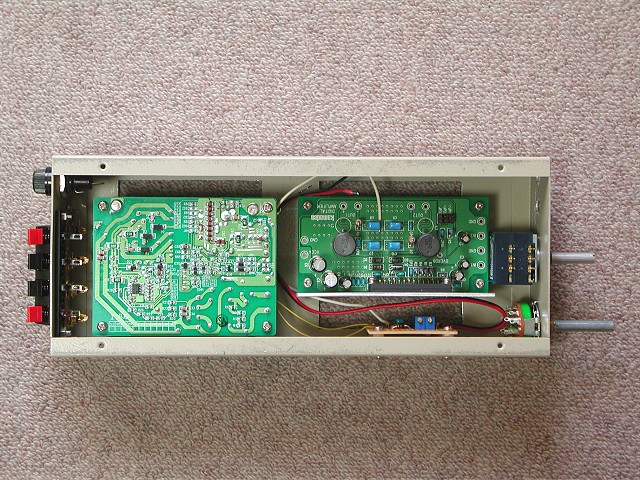 |
|
|
底面から見るとこんな具合で左が電源基板、右がアンプ基板。 右下がオフセット電圧調整回路です。 これで配線をすると隙間なく埋まってしまう感じになるでしょう。
|
|
|
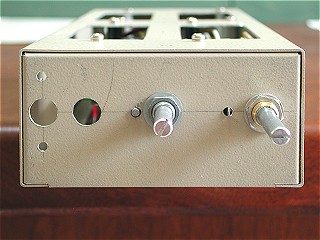 |
|
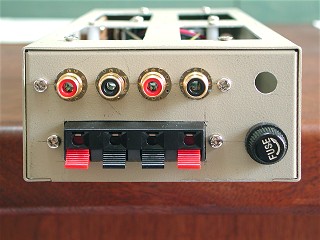 |
|
|
前面の詳細。 電源スイッチはアルミ板を加工した板に固定しそれが左端に見える2個の小さな穴に固定するネジで取り付けられます。
|
|
背面の詳細。 念入りに加工したため特製の入力端子盤のピンとアルミケースにあけた穴は芯ずれもなく綺麗に固定できています。
|
|
|
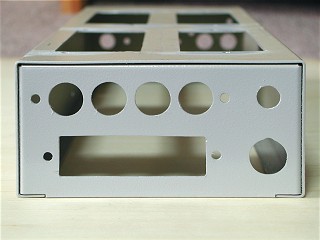 |
|
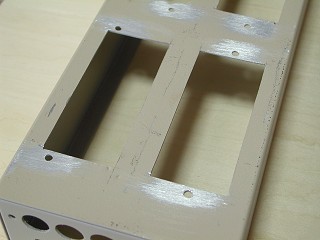 |
|
|
アルミケースの背面部分と底板は明るいグレー色を塗り、細かな擦り傷や下書きの線を消すと共に外観の完成度を上げました。
|
|
アルミケースのトップ部分ネジ穴の周りはこの上に取り付ける真鍮の金網と電気的に接続されるよう#120のペーパーで削ってアルミ面を出します。
|
|
|
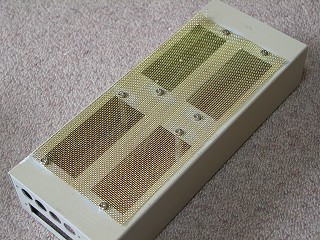 |
|
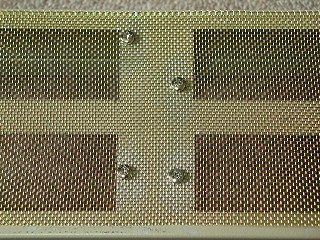 |
|
|
その上から真鍮製の金網を載せてバインドネジでケース内部のスペーサーに固定します。 こうすると電気的には穴があいていないことになります。
|
|
バインドネジで固定した部分のアップ。 バインドネジは真鍮にニッケルメッキ、金網は真鍮、そしてアルミが締結されることで電気的に確実に繋がります。
|
|
|
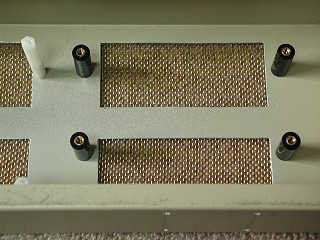 |
|
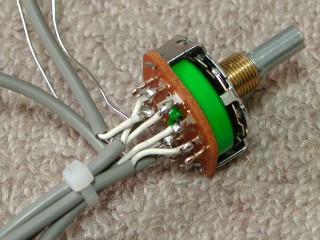 |
|
|
アルミケースの内側。 黒や白の棒がスペーサーで、電源基板やアンプ基板をこれらに固定しますが、それぞれにネジが切ってあるタイプの物を使っています。
|
|
ボリュームとローターリースイッチのシャフトを所定の長さに切断し、ロータリースイッチは固定する前にシールド線を全て接続しました。(取り付けてからの半田付けは困難。)
|
|
|
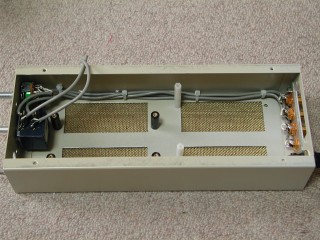 |
|
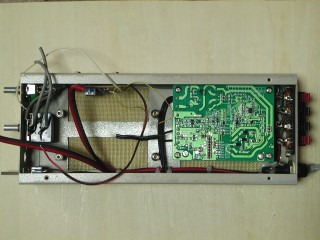 |
|
|
ロータリースイッチを固定しシールド線の反対側を入力ピンジャックに接続。 更にロータリースイッチとボリュームの間を結線しました。 2本飛び出ているワイヤーはアンプの入力に接続されます。
|
|
スピーカー端子からの配線、AC100V周りの配線を済ましてオフセット電圧調整基板を固定し、スイッチング電源基板を載せました。 スイッチング電源への接続はコネクターを使っていますから逆さに固定といっても接続は楽です。
|
|
|
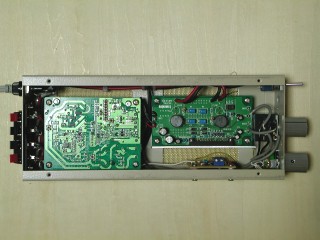 |
|
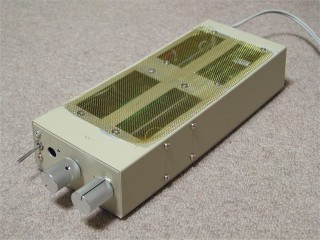 |
|
|
最後にアンプ基板を固定して12V電源の配線、スピーカー出力の配線、入力の配線、オフセット回路の配線を済まして完成。 誤配線がないか念入りにチェックしておきます。
|
|
底板を固定しツマミを付けて裸馬ながらアンプとして動作する状態になりました。 前面に穴があいている部分は木製パネルにLEDを取り付ける際にケーブルを通す穴です。
|
|
|
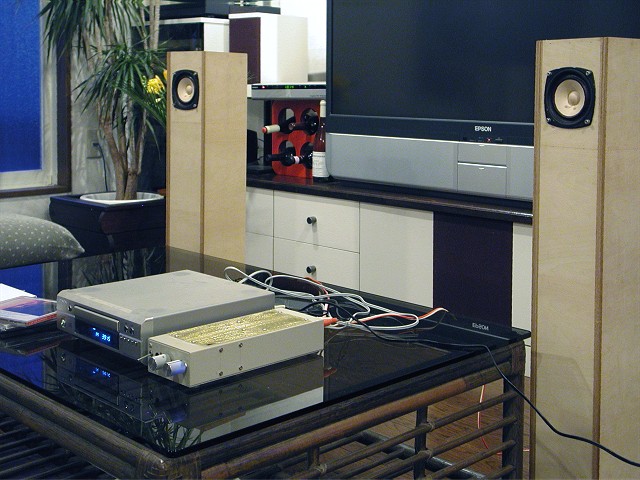 |
|
|
早速DENONのコンパクトCDプレーヤーを直結し、スピーカーには6N FE103を使ったダブルバスレフトールボーイ(息子が自作)で動作テストをしました。 まず音質ですが、極めて分解能が良い鮮明な音色に大変びっくりしました。 低域の馬力もなかなかのもので十分にメインのシステムとして使えるポテンシャルを持っています。 但し入力感度は若干低めですのでボリュームを回しきってもクリップしませんでしたが、そのまま連続して聴いていると家内から「うるさ過ぎるわよ!」とのクレームが出るくらいですので、実用上支障はないでしょう。 尚雑音は大変少なく、スピーカーに耳を近付けてもハム音、サーッというような高域のノイズは聴こえませんでした。 総合的にきわめて優秀と言えるでしょう。
|
|
|
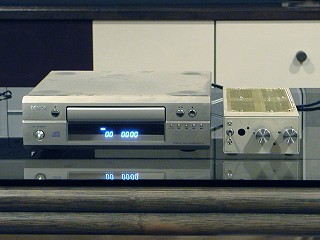 |
|
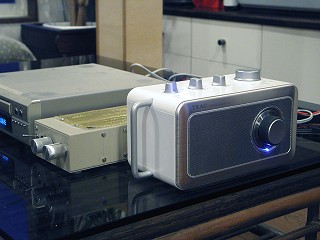 |
|
|
左がDENONのコンパクトなCDプレーヤーですが、今回のアンプが如何に小さいか良く判ると思います。 尚重量は700gしかない超軽量です。
|
|
更に驚きはAMラジオ(右手前の家内のお気に入り)を至近距離に置いてもスイッチングノイズによる影響が殆どありません。 シールド効果がかなりあるようです。
|
|
|
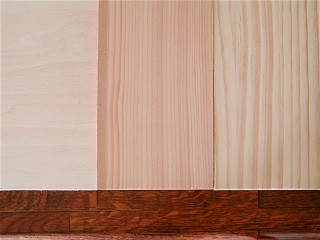 |
|
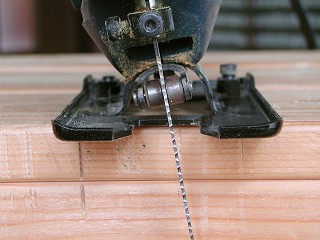 |
|
|
今回使った木目は混成部隊。 左はシナで天板に、真中が杉の柾目で側板に、そして右はラジアタパインで前面パネルに使います。 何故そうなったか? 手持ちの端材の都合とでも言いましょうか?!
|
|
最初が前面パネルの切り出しで上下のテーパー部分カットは電動ジグソー(YJ-50V)の定盤を傾けてやりましたが、切り進むうちに傾きが変化し易く超難易度の高い切断になります。
|
|
|
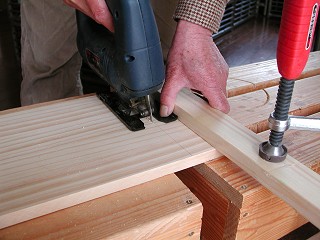 |
|
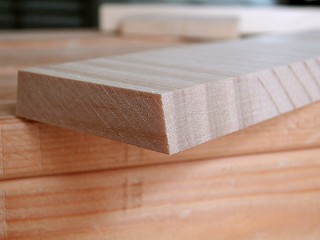 |
|
|
テーパーカットの作業中。 刃の上下速度は最大に、進行速度は刃が焼きつかない程度に出来るだけ遅く、定盤が浮き上がらないように、そしてガイドに定盤全体を密着させる!と4項目を同時に満足させねばなりません。
|
|
テーパー切断が終わった前板の切り口。 木工仕上げ切り刃(mini-Shopの#19)を使ったので切り口は大変綺麗でバリが殆ど出ません。 この後替刃式ヤスリを軽くかけて#240のサンドペーパーで磨けば万全です。
|
|
|
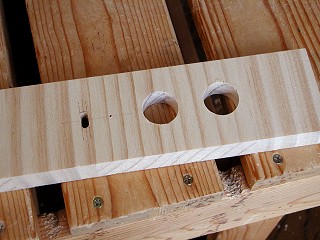 |
|
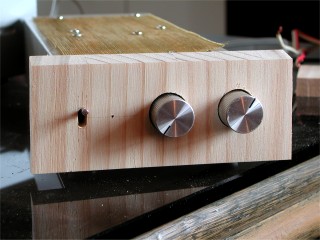 |
|
|
前板両端はまだ切断せず4つの穴をあけました。 ツマミが入る部分は20φフォスナービット、小さなLEDの穴は1.5φドリル、そしてスイッチの穴は4φドリルで2つ穴をあけその間を3mmのノミで小判状に削っています。
|
|
そして被せて見ましたが、ツマミの直径が19.5φですので、とおるにはおとったのですがツマミが擦れて回りません。 21φのフォスナービットがあると丁度良いのですが。
|
|
|
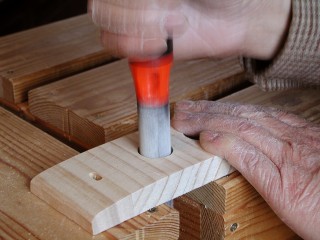 |
|
 |
|
|
そこでツマミが擦れない程度に替刃式ヤスリ(DR-1000P)のグリップに一段細いヤスリを挿し込んだもの(直径18mm)で軽く削りました。 (mini-Shopで販売している替刃BDR-500Pですが、DR-1000Pは直径25mmです。)
|
|
そしてカンナと替刃式ヤスリ(M-20GP)を使って前面のアールを削りだし、前板両端を所定の寸法で切断しました。 上とはぐっと雰囲気が違ってきます。
|
|
|
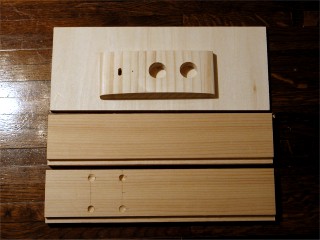 |
|
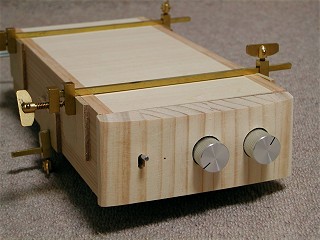 |
|
|
更に天板と側板を切り出し、側板には天板を落とし込む欠き込みをトリマーで彫っています。 側板の1枚に見える座繰り穴2個は右側に飛び出ているバインドネジ4個に当たらないためのものです。
|
|
ここまでの作業で丸一日掛かるという超スローで慎重に進めましたが、夜になってハタ金で仮組立てをしてみたらドンピシャ寸法であることが判りホッとしています。 前板の両端が飛び出ていますが、意識的に大きめにしており後で調整します。
|
|
|
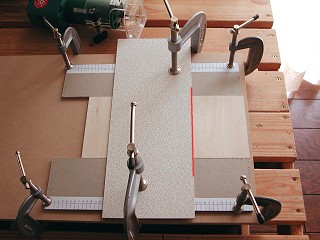 |
|
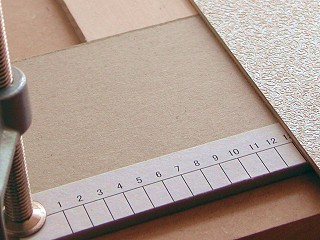 |
|
|
翌朝天板の溝を彫るための一過性のジグを製作しました。 中央横長で一番明るい色の板が天板で、上下を目盛りの付いた天板と同厚の板(最も暗いやつ)で挟み込みその上にトリマーのガイド板を載せて全体が動かないようクランプで固定します。 赤線にトリマーの台座を沿わせます。
|
|
天板を挟む2枚の板(これは下側)には目盛りを刻んだ紙が貼ってあります。 目盛りの間隔は6mmになっていますので、切削するたびにガイド板を1目盛りずつ左にずらしてやれば3mmのビットを使ったときに溝と溝の間も3mmになるという寸法です。
|
|
|
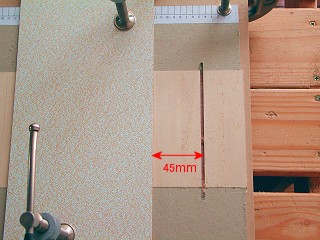 |
|
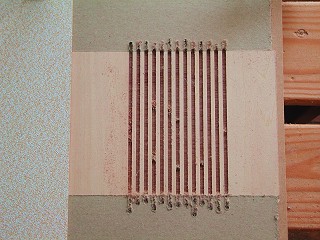 |
|
|
1本目の溝を切削し終えたところ。 上下の押さえ板から切り込むことにより切削開始部分の不安定さや角が掛け易くなるのを防止しています。 当然ながらガイド板と溝中心の距離は台座の幅の半分の値(リョービの場合45mm)となります。
|
|
1本の溝を切削するたびにガイド板を左に1目盛りずつずらして次の溝を切削・・・・を繰り返し、片側の溝列が彫り終わりました。 そうしたら天板の左右を入れ替えてもう1組の溝列を彫ります。
|
|
|
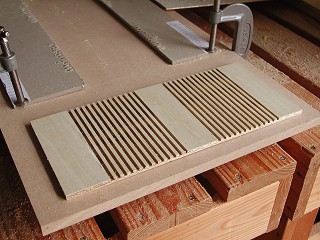 |
|
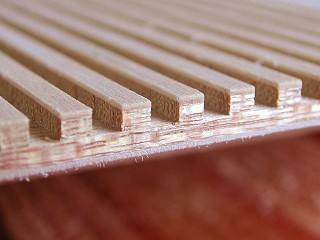 |
|
|
こうして彫り終わった天板上側の溝。 深さが2.75mmですから切削時の反動も少なく作業は容易ですが、切削を急ぐと1枚刃だけにバリが沢山出たり切り口が汚くなりますので、ゆっくりと進めるのが重要です。
|
|
切削断面のアップです。 天板を捨て板で挟んで切削しましたので、端の部分に欠けを生じていません。 切削間隔の誤差も視覚的な観点から許される範疇に入っていると思います。
|
|
|
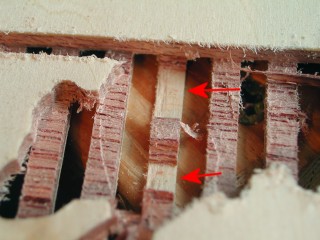 |
|
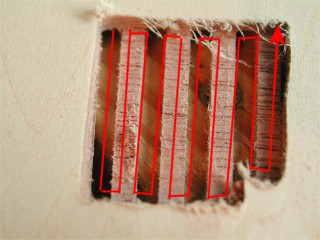 |
|
|
これは天板裏面のテスト切削の結果で、一度に沢山切削すると大きな欠けが生じてしまいます。(矢印の先は3層の中心部分のラワン材が欠けて無くなっており裏の表層のシナ材だけが残っている。)
|
|
そのような欠けを無くすには切削量を抑えて作業することが重要で、このテストでは矢印のようにトリマーを左から右へ少しずつ(右への一度の移動量は約2mm)切削し欠けが出ていないことを確認した例です。
|
|
|
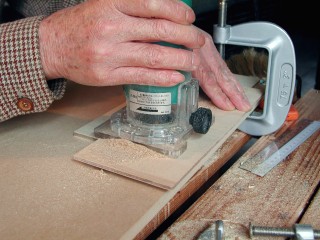 |
|
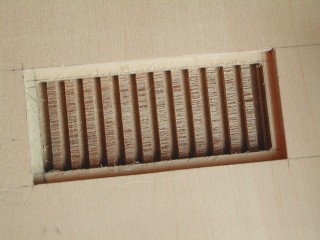 |
|
|
本番では3mmのストレートビットにダブテールガイドを使用し、切削する長方形より7mmずつ大きくしたガイドテンプレートを作って切削しています。 また横方向の移動は一度に0.5-1.0mmという少量に抑え欠けを防止しました。
|
|
1箇所の切削が終わったところですが、一番上にあるのが4mm厚のガイドテンプレートで、実際の切削はその一段下で、ガイドテンプレートより7mmずつ小さな長方形になります。(角は3φの丸みが残る。) 時間が大変掛かりますが途中で作業を止めずに一気に全神経を集中してやる必要があります。
|
|
|
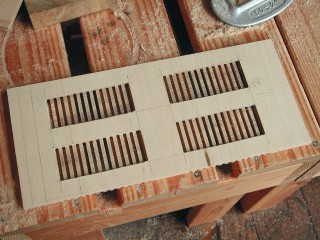 |
|
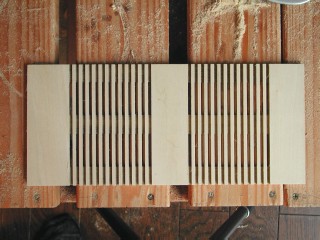 |
|
|
天板裏の4箇所の長方形座繰りが終わりました。 深さは2.75mmですので、表面の溝と重なっている部分は貫通し放熱口となります。
|
|
それを表面から見たところ。 貫通部分が透けて見えるのがお判りになるでしょう。 驚くなかれ念入りなテスト切削にかなり時間を費やしたので、この天板の加工だけで1日使ってしまいました。
|
|
|
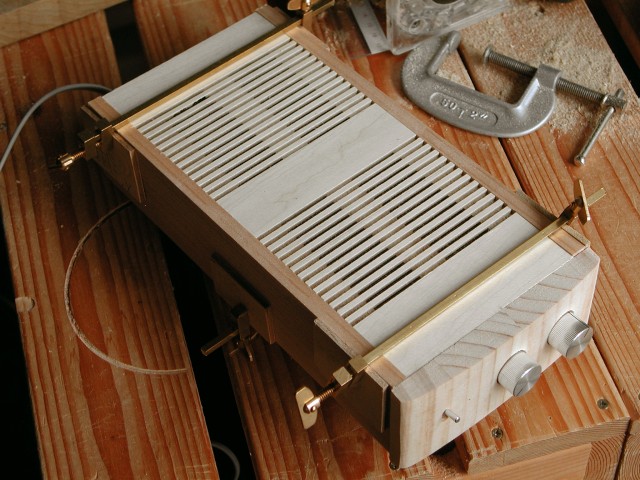 |
|
|
加工が終わった天板を再び側板や前面パネルと共に仮にアンプ本体にあてがってハタ金で軽く抑え放熱口周りを確認したところです。 大変時間が掛かっていますが構想イメージどおりに作業は進んでいます。
|
|
|
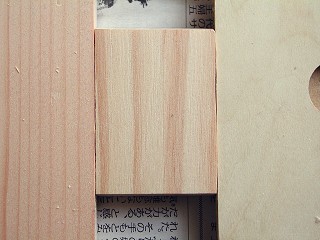 |
|
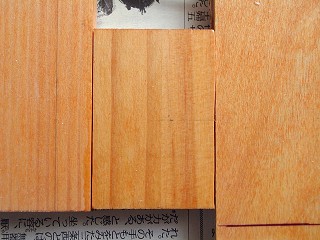 |
|
|
前の方でもお見せした3種類の板の切れ端で、左から側板用、前板用、天板用です。
|
|
同じ場所ではありませんが、それらに油性ウレタン着色ニス チーク色に薄め液を20%強加えた物でテスト塗りしました。 左と真中は2回塗り、右は4回塗りで同じ程度の濃度になりました。 左の赤味はまだ残ってはいますが生地の状態よりは似た色味になっています。
|
|
|
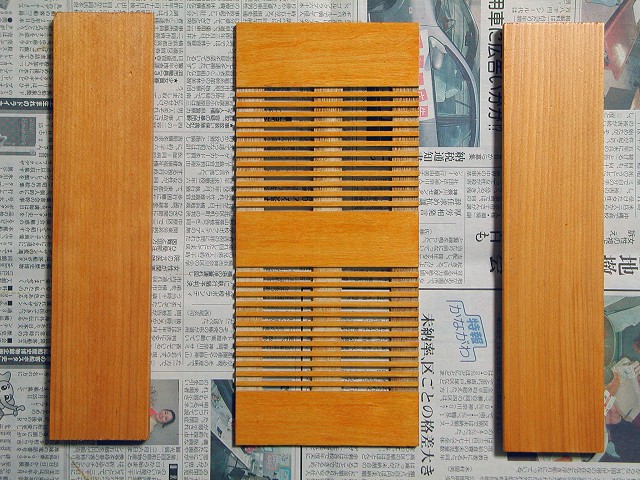 |
|
|
テスト塗装どおりの仕様(油性ウレタンニス チーク色に薄め液20%を加え2回または4回塗り)で本番の塗装を側板と天板に施しました。 色味がテストの時よりも黄味が強くなっているがこれは蛍光灯による影響と思います。 まずまず問題無しです。
|
|
|
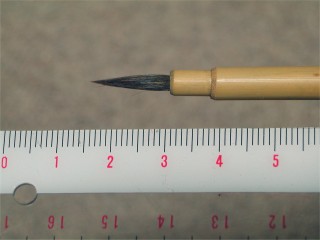 |
|
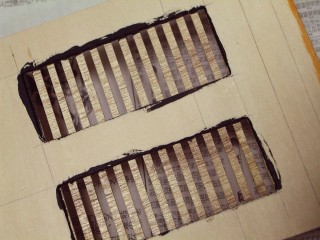 |
|
|
スリット部分の塗装には面相筆を使用。 本来は人形の顔の部分を描くなどデリケートな作業用ですが、狭いところを塗るだけが目的なので使い古しの少し太めのものを使いました。
|
|
天板裏側の座繰りをした壁面を先ず水性つや消し黒で塗りつぶし。 はみ出て汚らしい部分がありますが、これは裏側で見えなくなります。
|
|
|
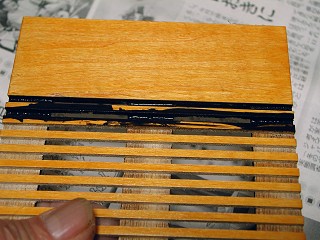 |
|
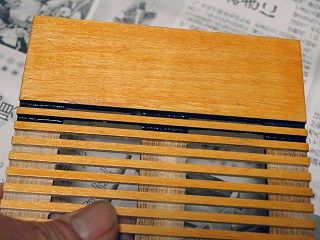 |
|
|
表側のスリットの塗装はどちらかというと荒業に近く、ジャブジャブとスリット内部を筆で塗りつぶします。 ご覧のようにかなりはみ出ていますが?
|
|
濡れ雑巾で表面を拭えばご覧のとおり。 但しもたもたしていると乾燥の速い水性塗料は濡れ雑巾で拭えなくなるので、手際よい作業が必要です。
|
|
|
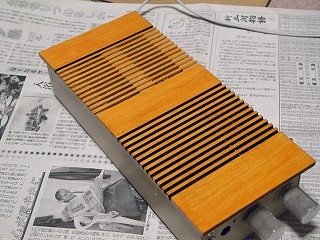 |
|
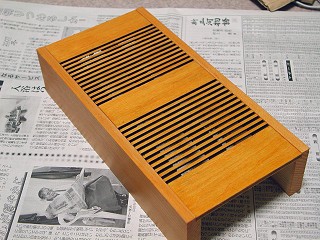 |
|
|
見え方の違いをご覧頂くために半分のスリットを塗りつぶした後アンプケースの所定の位置に載せて見ました。 言うまでもなくその差は歴然としています。
|
|
全てのスリットを塗りつぶした後に側板の上に載せて見ました。 材質の違いによる色合いの差はほぼ無くなったようです。 やれやれ一安心。
|
|
|
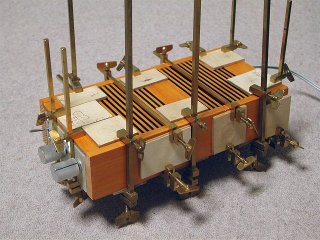 |
|
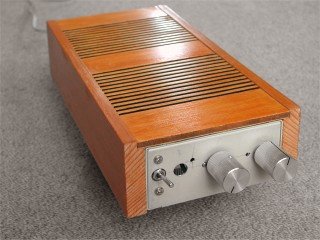 |
|
|
側板と天板をアルミケースに接着、そして側板と天板も接着を同時にやるためこのように15本のハタ金を圧着保持に使いました。 接着にはゆっくり作業が出来るよう60分硬化型のエポキシを使っています。
|
|
エポキシの完全硬化には12時間掛かるので一晩寝かせました。 側板と天板は完全にアルミケースをコの字型に覆い固定されています。
|
|
|
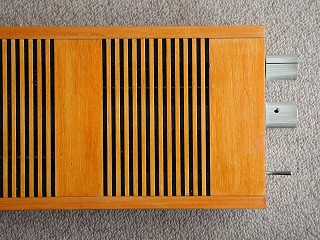 |
|
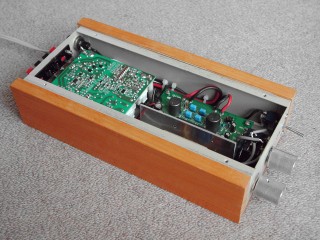 |
|
|
真上から見たところ。 側板と天板の間に隙間もなくぴったりと収まっています。 また側板上面は0.3-0.4mm程度天板面より高くなっていますが、これも予定通り。
|
|
アンプのアルミ底板は相変わらず4本のバインドネジで固定されているだけですから、アンプのメインンテナンスや修理は問題なく出来ます。
|
|
|
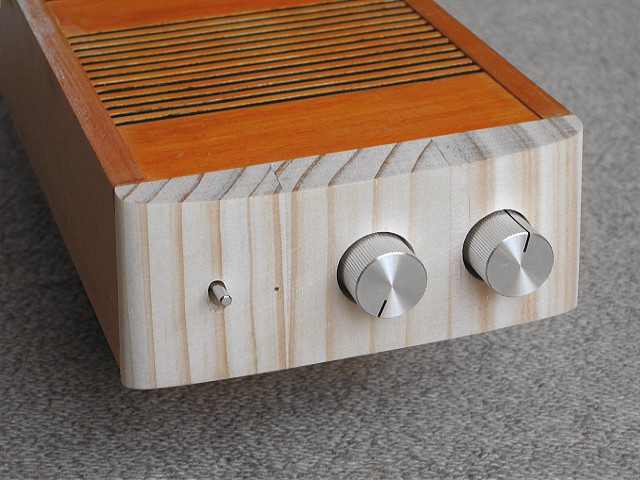 |
|
|
前板はトグルスイッチのストロークを押さえON時にほぼ水平にしたかったのと、ロータリースイッチのツマミの穴位置が0.5mmほどずれていて調整不能であることが判ったので作り直しました。 尚前板はケース内部から2本の木ネジで固定しております。 それとLEDの穴は1.5mmから2.0mmに変更しました。 そしてこの後塗装をしました。
|
|
|
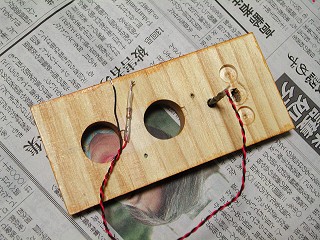 |
|
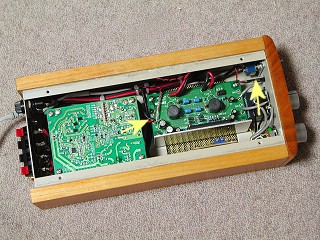 |
|
|
LEDを差し込んで表面から液状瞬間接着剤を穴に楊枝で少しずつ垂らして固定し配線を済ませました。 1.8kΩの抵抗は配線の途中に入れ熱収縮チューブで絶縁しています。
|
|
前面パネルを木ネジ2本で固定し、LEDの配線を済ませました。 右矢印がアルミ板の穴を通したLEDで、左の矢印が接続点です。 これで底板をネジ止めして完成です。
|
|
|
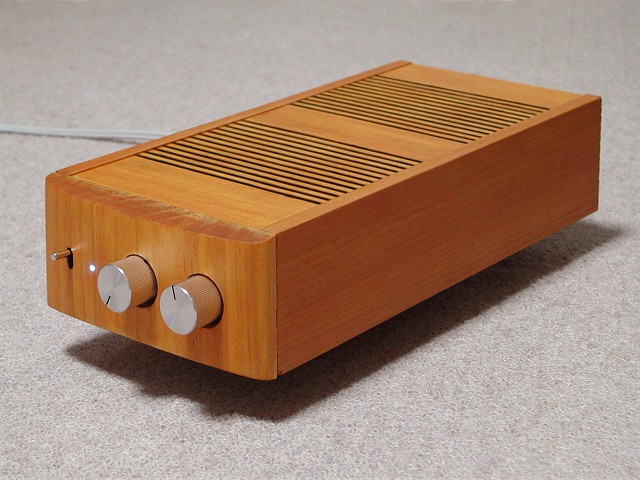 |
|
|
完成した木製ケース入りのアンプ。 塗装の最終仕上げは油性ウレタンつや消しクリヤーとしているため、しっとりした感触で木目が美しく際立ちます。 拘りぬいてとんでもない手間がかかりましたが、ほっと一安心です。
|
|
|
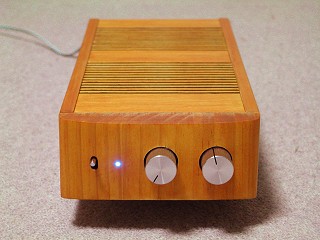 |
|
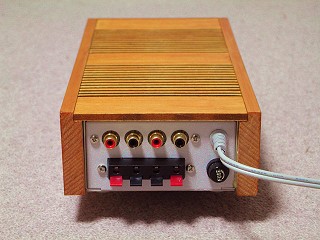 |
|
|
正面から。 LEDの輝いている面積が大きくみえますが、実際には直径2mmの穴にしていますのできりりとした輝きです。
|
|
背面の様子。 狭い面積ながら接続しにくいこともなく、合理的に配置されています。
|
|
電子回路部分と木工部分、それぞれ約半々の時間を割いた感じで仕上がりましたが、これまた自作ならではのかわいい!そして山椒は小粒でもピリリと辛いのような高品質なアンプになったように思います。 電子工作は苦手!とかアンプを作る興味がない!という方でも後半の木工部分は電動トリマーでちょっと変わった加工をして見たいという方には参考になるのではと思います。 どちらかといえば指物の領域に入る工作ですが、これはこれでまた楽しいものです。Copyright (C) 2001-2019, Vic Ohashi All rights reserved.