|
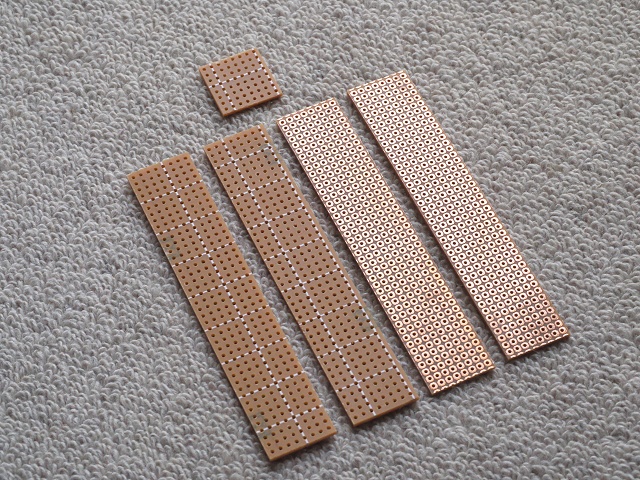 |
|
|
切り出したLEDブロックを構成する基板。 長方形の4枚と正方形1枚ですが、正方形は21.1 x 21.1mm、長方形は幅21.1mm、高さ110mmとなるようノギスを頻繁に使って切断後の研磨で仕上げています。 長方形の右2枚は内面(半田面)を見せています。
|
|
|
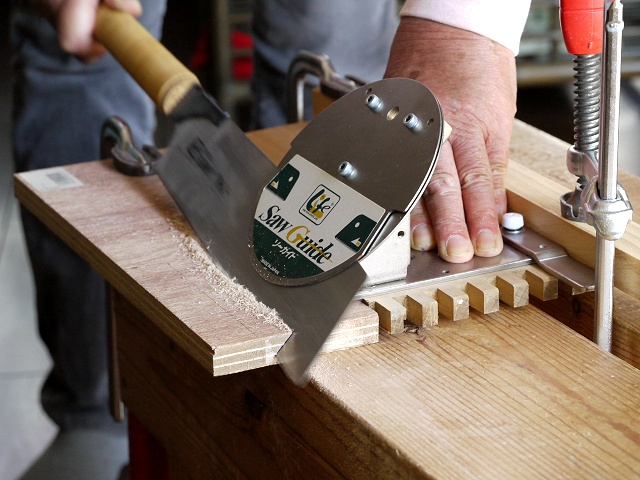 |
|
|
45度研磨ジグ作成開始で、ソーガイドを使って高精度の45度切断をしているところです。 バクマクランプを4本も使う贅沢な材料固定でぐらつき、ずれ、による精度の狂いを抑えています。
|
|
|
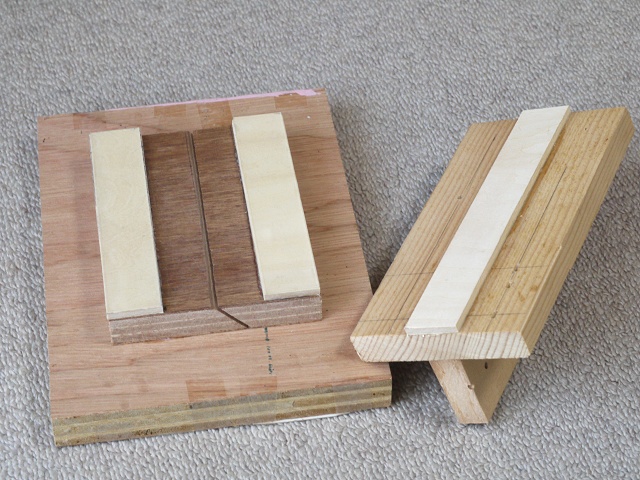 |
|
|
ジグが出来上がったところですが、上の構造図と比較してください。 斜めスリットの両側の白い板の上には、0.5mm厚のプラスチック板が貼ってあります。 また右にあるのはひっくり返した可動部分で、細長い白い板の上に布下地サンドペーパーを貼り付けます。
|
|
|
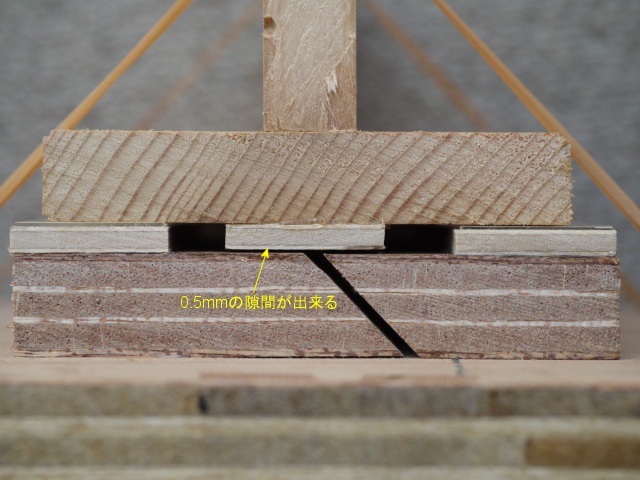 |
|
|
可動部分を所定の位置に置いて輪ゴムで全体を挟み断面を見ています。 前掲の構造図と比較すると良いでしょう。 黄色でコメントしているように0.5mmの隙間が出来ますが、実際にはここを#120の布地サンドペーパーが貼られるので、次の写真に見られる突起だけが削り落とされます。
|
|
|
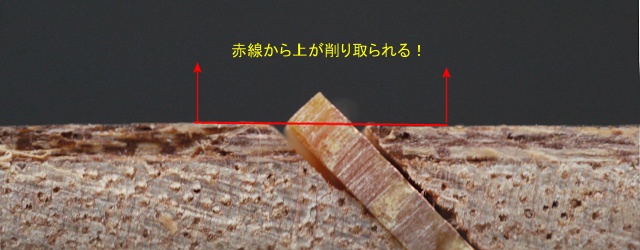 |
|
|
挿し込んだ基板の飛び出た部分のクローズアップですが、この飛び出た部分を削り取れば基板の長辺は45度の角度を為します。(幅は21.1mmのままで変りません)
|
|
|
 |
|
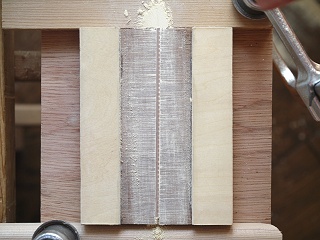 |
|
|
ジグのスリットに基板を差込み、可動部の裏に#120の布下地サンドペーパーを貼り研磨開始です。 左の写真は削られた基板の両側に研磨滓が白っぽく溜まっていますが、これは未だ研磨が不十分であることを表しています。 右は更に研磨が進んだ状態で、研磨滓の溜まりがありません。 これは15mm厚の板に対し基板の飛び出しが無くなった状態であることを表し、ここで研磨は終了です。
|
|
|
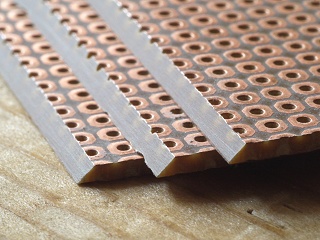 |
|
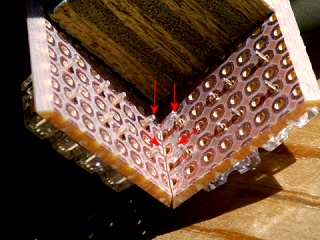 |
|
|
45度研磨が終わった状態です。 4枚の基板の幅は正しく21.1mm(±0.05mm)になっています。
|
|
LEDを挿し込んでピンとピン(赤矢印の先)の距離を確認しました。 約2.5mmありますので、電気的な接触(ショート)は生じないでしょう。)
|
|
|
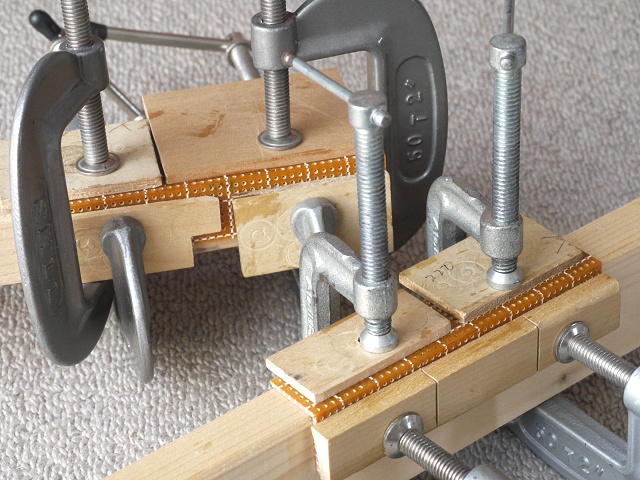 |
|
|
正しい直角が確認済みの角棒に基板を当ててエポキシ接着剤で接着しクランプで圧着保持し24時間放置します。 保持の仕方が大袈裟なようですが、接着強度と密着度を高めるには不可欠なやり方です。
|
|
|
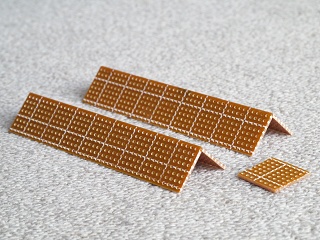 |
|
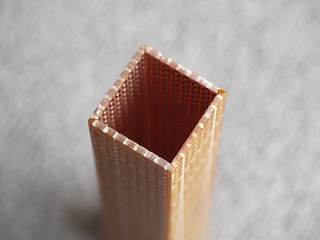 |
|
|
接着が終わった部材。 この後塗装してからLEDの配線に進みます。
|
|
2枚のL字型基板を突き合せました。 非常に正確に加工されているのが判ります。
|
|
|
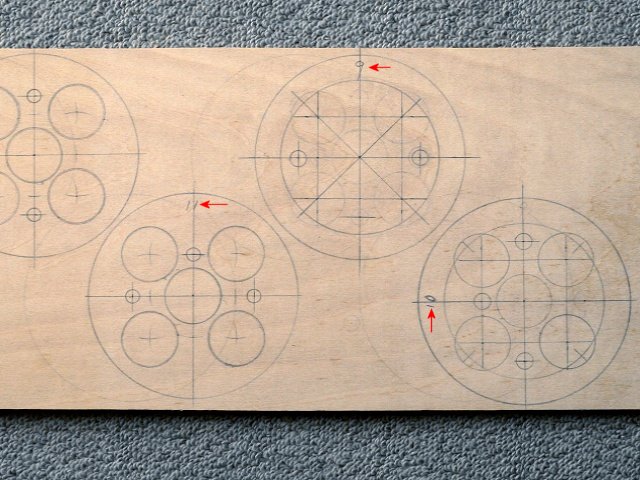 |
|
|
墨線を引いた5.5mm厚合板。 赤矢印の先が層番号で、真ん中が9番で電池ボックスの最上部。 そして右は10番。左は11番です。 この板の表面の木目は横方向で芯材は縦目ですが、各層は90度回転させて貼りあわせるので、偶数の層は90度左に回転させています。 貼りあわせる時には番号の方向を合わせれば木目方向が交差するようになります。
|
|
|
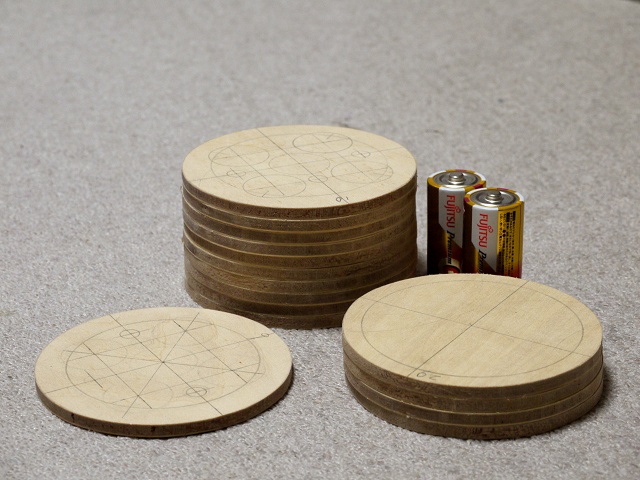 |
|
|
電動ジグソーで丸く切り抜きました。 この時直径は100.5〜101.0mmとほんの少し大きくなっています。 成形研磨でこれを99.5〜100.0mmにして慣らします。 電地の左隣が電池挿入の穴をあける板(10枚)ですが、電池よりも若干高くなっています。
|
|
|
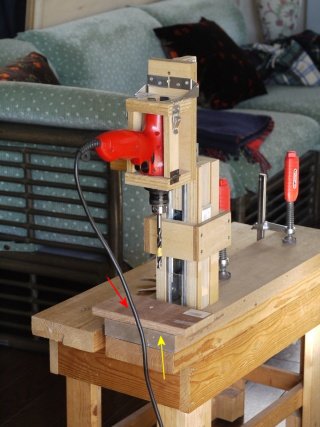 |
|
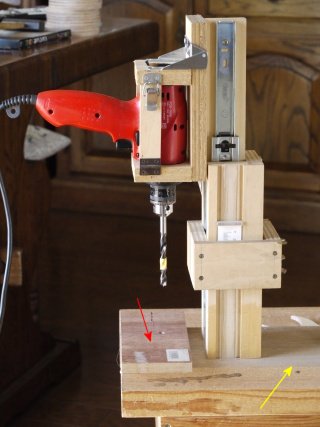 |
|
|
多数の穴の相対位置が全く同じになるような穴あけのカラクリがこれです。 撓みを抑えるため電動ドリルアタッチメントのコの字の座板を外し、幅110mm x 長さ600mm x 厚み30mmのラワンの端材(黄色矢印)に4本のネジでがっちりと固定ししたものを作業台に2つのバクマクランプで固定しました。 赤矢印は130 x 90 x 18mmのラワン合板で、位置決めのテンプレートに使います。
|
|
|
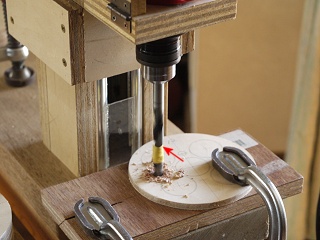 |
|
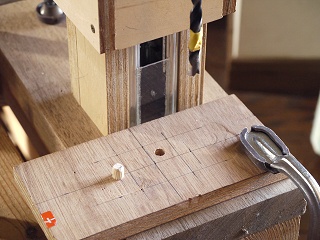 |
|
|
9〜19番の板に穴をあけますが、最初に記入した番号が赤矢印の方向に向けて左端の8φの穴を先ずあけます。 横滑りを抑えるためクランプで固定しています。
|
|
11枚あけ終わったらテンプレートにする材料にも8φの貫通穴をあけ8φの木ダボを埋め込み、背面に瞬間接着剤を沁み込ませ固定します。 中央の穴は無関係です。
|
|
|
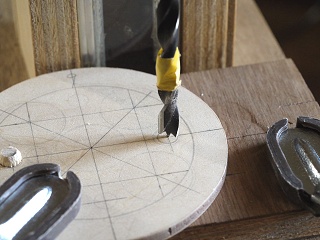 |
|
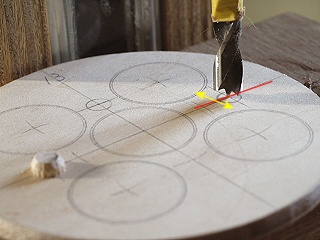 |
|
|
木ダボに既にあけた穴を通して反対側の8φの穴を正しくあけられるよう、テンプレートの板を前後左右に調節して位置が決まったらテンプレートを作業台にクランプ(右)で固定します。 材料の板も回転しないようクランプ(左)で固定し穴をあけます。
|
|
残り10枚の穴あけは木ダボに穴を通した後材料を前後方向に動かし、ドリルの先が赤線の真上に来るよう調節後、材料をクランプで固定して穴をあけます。
|
|
|
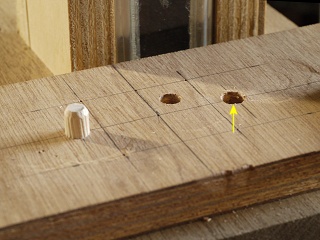 |
|
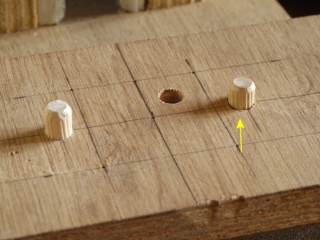 |
|
|
11枚の板の穴があけ終わったら、テンプレート固定のクランプは緩めず、テンプレートの右側の穴を貫通穴にします。
|
|
そして8φの木ダボを差し込み反対側に瞬間接着剤を沁み込ませて固定します。 残りの穴あけはこれら2本の木ダボが基準になります。
|
|
|
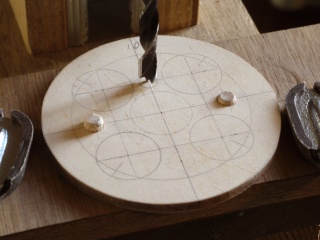 |
|
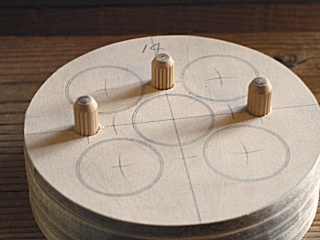 |
|
|
さて中央上の8φの穴あけですが、2本の木ダボに既にあけた穴を通して固定し、テンプレート全体を前後左右に移動して、ドリルの先に中央上の穴の中心が来るよう調節し、テンプレートを2本のクランプで固定して穴をあけます。
|
|
11枚全ての穴があいたので念のために木ダボ3本を5枚重ねの状態で差し込みました。 ご覧の通り無理なく通っており、相対位置誤差は充分満足できる低レベルになっています。
|
|
|
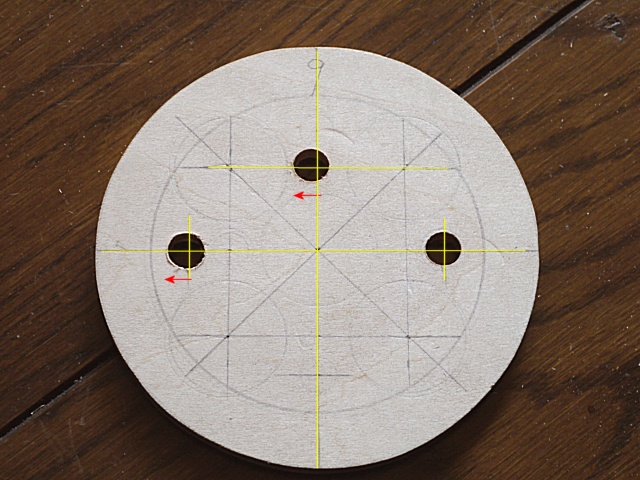 |
|
|
但し一番上の9番は穴の相対位置誤差はOKなのですが、外径の狂いが±1.0mmもあり、成形研磨で修正できそうにも無いので、作り直すことにしました。 その誤差の発生理由は不明ですが、ご覧のように墨線と穴の位置もかなりずれています。
|
|
|
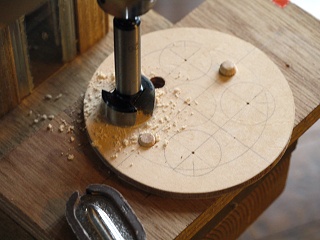 |
|
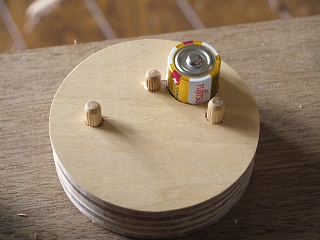 |
|
|
先端工具を26φフォスナービットに替えて電池挿入穴をあけます。 位置決めの要は2本の8φ木ダボで、これに板を嵌め込むことで相対位置精度を確保します。
|
|
5枚あけ終わったのでそれらを重ねて電池を入れてみました。 挿入はスムーズで問題はありません。
|
|
|
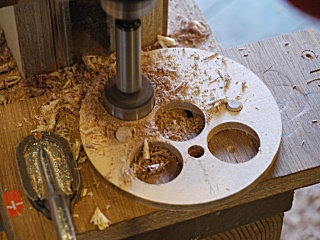 |
|
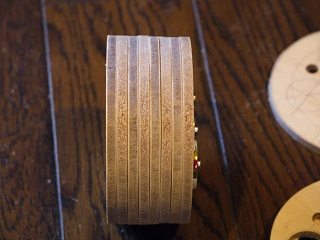 |
|
|
電池穴は5 x 10枚で50個あけないとなりませんから時間が掛かりますが、常に緊張をもって作業に臨まないと、とんでもない失敗をしかねません。
|
|
穴あけが終わったので8枚を重ねて電池を挿入しました。 それを横から見ると外寸のばらつきは0.5mm以内に収まっているようで、これなら外面の成形加工は容易に終わるかもしれません。 但し?
|
|
|
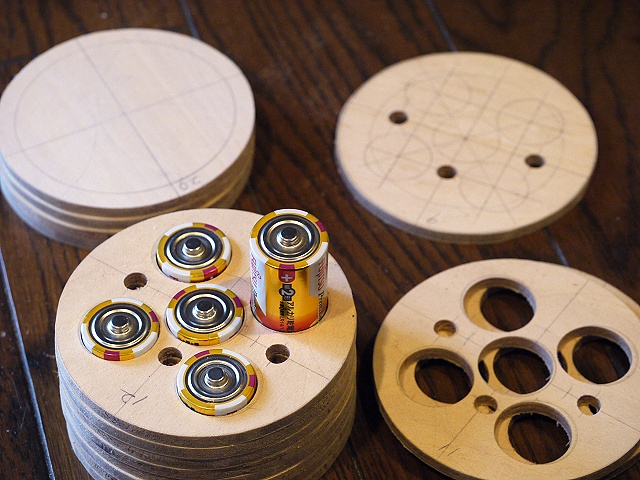 |
|
|
電池がスムーズに入ったのは4本までで、最後の一本は途中で引っ掛かってしまいました。 しかしながら単二電池の太さの規格値はMAX 26.2mmですので、26.5mm程度には削る必要があり新たな作業が発生するわけではありません。
|
|
|
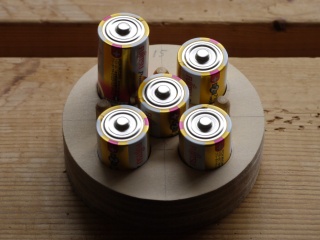 |
|
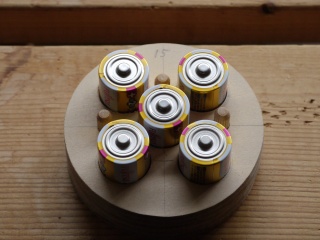 |
|
|
3箇所の8φの穴に木ダボを差込みました。 これは15〜19番で電池がきついながらも通ったのは3本でした。(左側) その穴に26φフォスナービットを通して出っ張りを削ったところ、5箇所とも電池が通るようになりました。(右側)
|
|
|
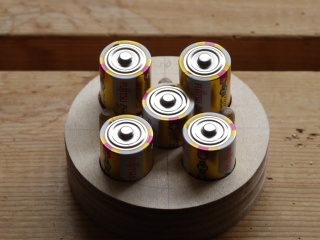 |
|
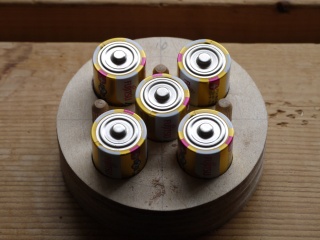 |
|
|
10〜14番のブロックでも2箇所の穴は電池が通りませんでしたが(左側) フォスナービットで同様に出っ張りを削ると全ての穴が電池を通すようになりました。(右側) これで内部の調整は容易に出来る事が判りました。
|
|
|
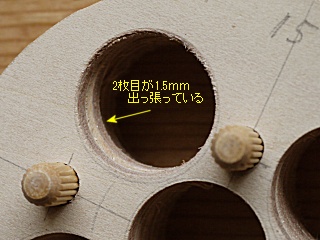 |
|
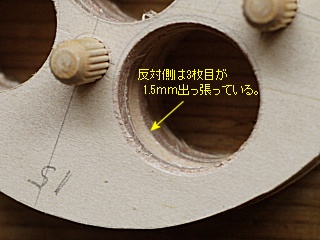 |
|
|
修正切削前の内部の出っ張りの様子の写真です。 5〜19番のブロックの上から2枚目は1枚目より1.5mmも出っ張っています。(左側) その反対側は3枚目が1.5mm出っ張っています。(右側) 他の3箇所はこれほどひどくはありませんが、何か加工作業で致命的なミスをしています。
|
|
|
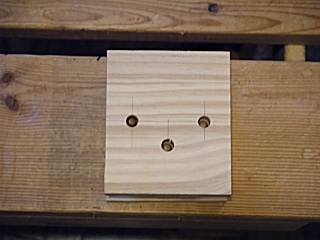 |
|
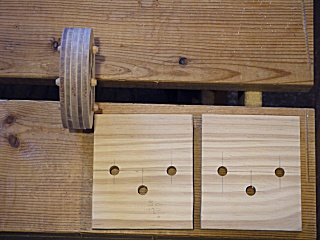 |
|
|
5枚の円盤をこのような15mm厚押さえ板2枚で挟んでやります。 板には8φの穴位置3箇所に10φの穴をあけておきます。
|
|
5枚の円盤に順番どおりに一枚ずつ木工ボンドを薄く伸ばして貼り付けて且つ木ダボに通し木ダボ両端が出るようにします。
|
|
|
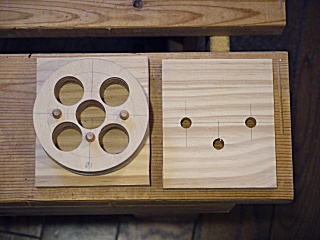 |
|
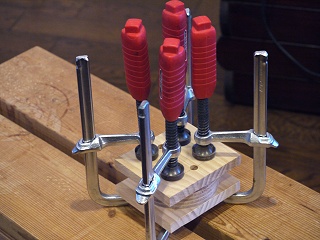 |
|
|
木ダボの先を押さえ板の穴に落としこんで、もう一枚の押さえ板をやはり木ダボが穴に通るよう置きます。
|
|
そしてバクマクランプ4本でクランプし、思いっきり締め上げます。 その後に6φ位の鉄棒を木ダボに当てて玄翁で叩き抜いてしまいます。
|
|
|
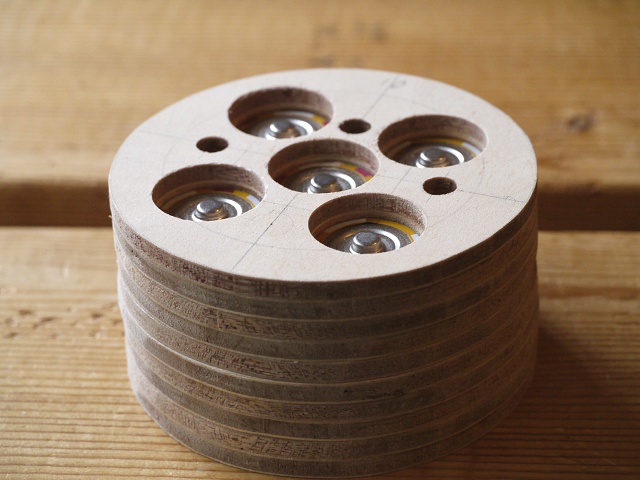 |
|
|
2つのブロックを8φ木ダボで連結し(まだ接着していません。)、替刃式丸棒ヤスリ(直径25mm(お誂え向きの道具)で内部を研磨して段差を落としました。 ご覧の通り全ての穴がひっかかることなく電池を通します。
|
|
|
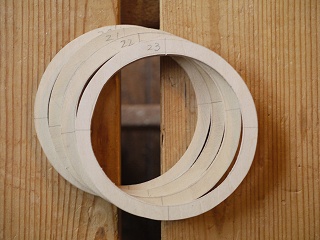 |
|
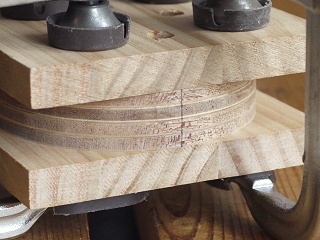 |
|
|
底板の周りのリング板4枚を切り出しました。 リングの幅は7.5mmですから、穴の直径は85mmになります。
|
|
板の直行線の延長4ヶ所でそれぞれひとつにまとまるよう調整しながら木工ボンドで貼り付けて、押さえ板で両側を挟んでからクランプで締め上げました。
|
|
|
 |
|
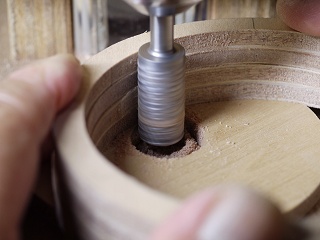 |
|
|
内面はこのような大小の段差が残ります。 いきなりドンピシャ寸法で切断できず、若干大きめに切断しているためです。
|
|
そのような段差は電動ドリルアタッチメントに中目の回転ヤスリを取り付け700回転/分の低速で削り取ります。
|
|
|
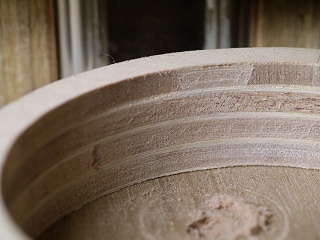 |
|
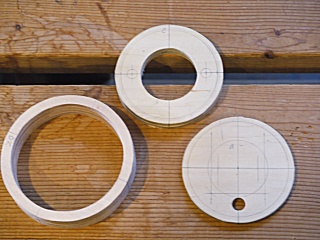 |
|
|
こうして段差を削り取った後はこのように滑らかになります。 電動ドリルアタッチメントの非常に便利な応用例です。
|
|
出来上がった底に貼るリングが左側で、右は底に取り付ける蓋です。 3枚貼りあわせですが、下側2枚はドーナッツ状で左のリングと同じ方法で貼り合わせて加工します。
|
|
|
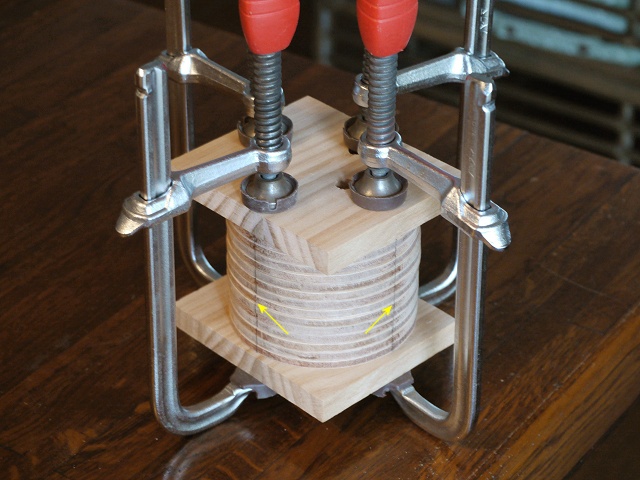 |
|
|
底部のスカートとなるリングを接着しました。 これで電池ブロックの積層数は14枚となります。
|
|
|
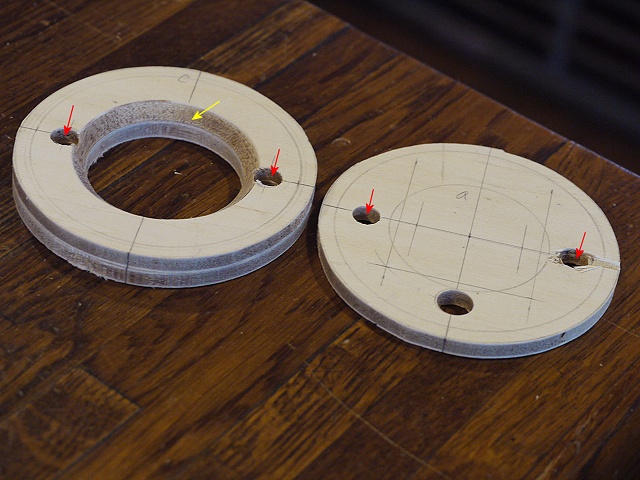 |
|
|
底の蓋の加工に進みます。 先ず2つの8φの穴をあけますが、穴の間隔が19番と同じになるようにします。 また内面をコロ付角面ビットで5mm削り取り、ツマミに指を通しやすくしておきます。
|
|
|
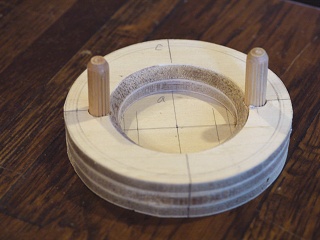 |
|
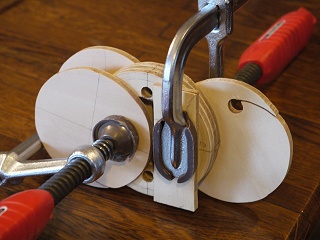 |
|
|
木工ボンドで接着し穴2箇所に木ダボを挿し込んで位置決めします。
|
|
そしてクランプで圧着保持しますが、すぐに木ダボ2本は叩いて抜き取ります。
|
|
|
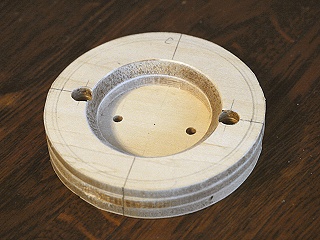 |
|
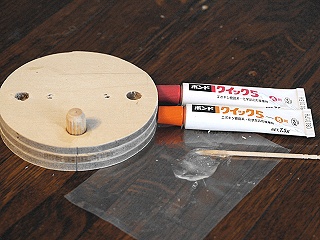 |
|
|
ツマミ固定用の4φの穴(間隔は30mm)をあけます。
|
|
背面の10φの穴には15mmの長さに切断した10φの木ダボを5分硬化開始型のエポキシで埋め込みました。
|
|
|
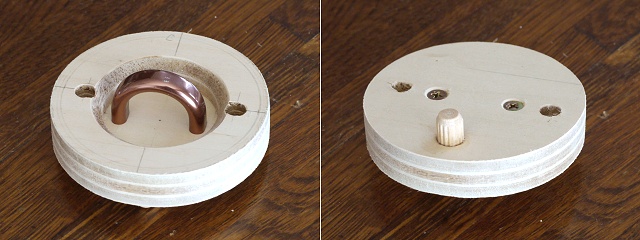 |
|
|
左が蓋の表側になります。 つまみに指を通して引き抜きます。 右が内側で、埋め込んだ木ダボが蓋を閉じる位置決めになります。 このあと外周を上で説明した丸棒ヤスリで現物合わせにて削り込み、その後替刃式ヤスリと#240ペーパーにて仕上げました。
|
|
|
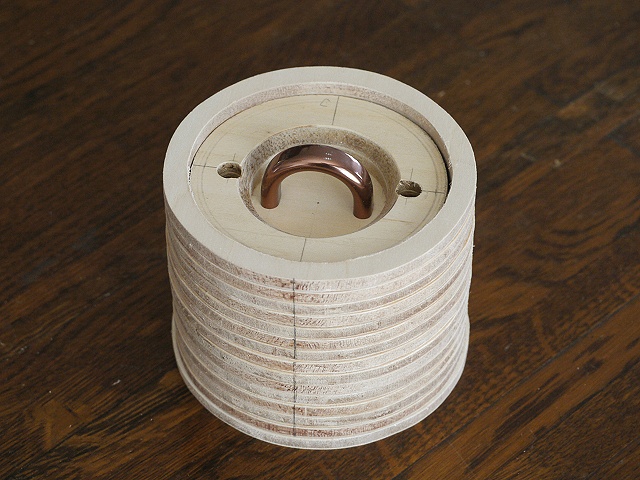 |
|
|
電極を除き完成した電池ブロックです。 これは逆さまになっていますが、この下にあと9層追加されます。
|
|
|
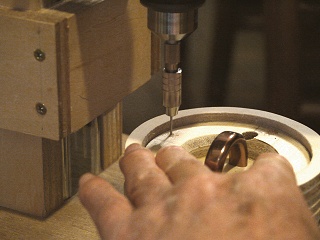 |
|
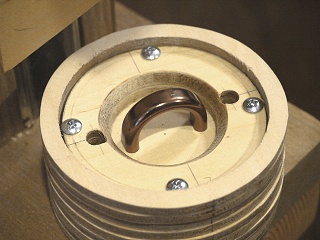 |
|
|
底蓋固定ネジ穴をあけますが、本体に底蓋を所定の位置に挿入した状態で、1mmのドリルで根元まであけマーキングします。 そして本体側は5.5mm 深さ12mmの穴に、底蓋は4.5mmの貫通穴をあけ、M4 25mmのトラスネジを締めこみました。
|
|
|
 |
|
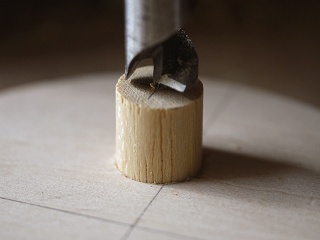 |
|
|
脚は当初ゴム製の物を考えていましたが、適当な寸法のものが無いので12φの木の棒を17mmに切断して作ります。
|
|
切断面に10φ 深さ1.5mmの座ぐり穴をあけます。 芯出しを慎重に!
|
|
|
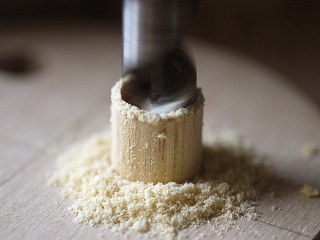 |
|
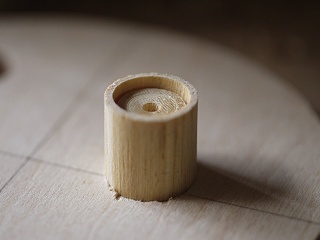 |
|
|
一気にあけると欠けやすいのでゆっくりと慎重に薦めないとなりません。 そのためこんなに細かな切削屑になっています。
|
|
彫り終わった脚です。この窪みに塗装が終了後に9.5φのクリヤーパンポンを貼り付けてやります。
|
|
|
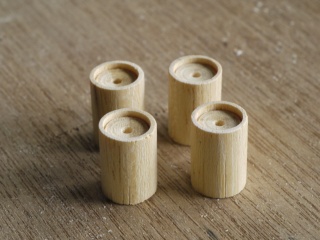 |
|
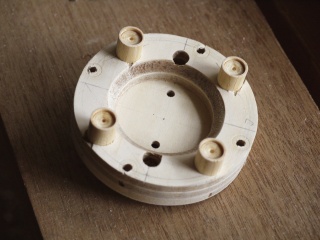 |
|
|
削り終わった4本で穴がうまく中心にあいていますが、実は中心に穴をあけられなくて不良とした物が5本もありました。
|
|
その4本を底蓋に深さ5mmの穴をあけて挿入しました。 玄翁を使うくらいきつかったので接着剤は使いませんでした。
|
|
|
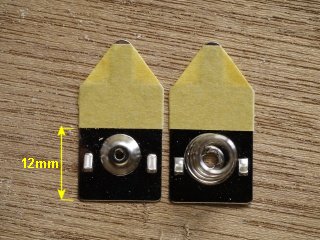 |
|
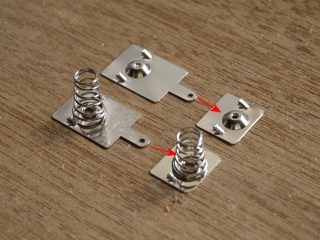 |
|
|
プラス・マイナスの電極は奥行きを12mmに詰めてしまいます。 マスキングテープで切断線としています。
|
|
左側が切断前で接続用のピン部分を切断して右のようになります。
|
|
|
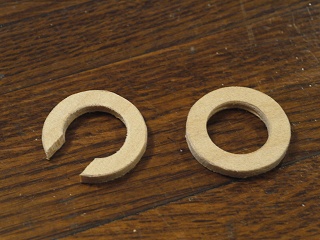 |
|
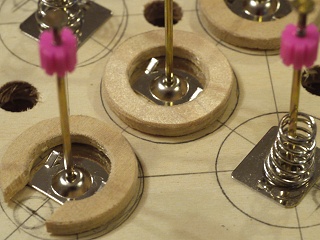 |
|
|
また電池逆接続による事故防止のリングを3mm厚アガチスで作ります。 外径24mm、内径15mmが5個ですが、そのうち2個は左のように幅9mmの切り欠きを入れます。
|
|
これは9番の板の下側に取り付ける電極ですが、切り欠きの入ったリングは左下のような配置となり、駆動回路層に連結するネジの頭との干渉を避けます。
|
|
|
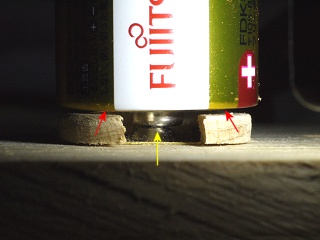 |
|
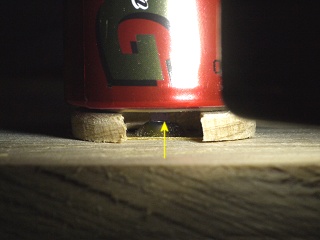 |
|
|
電池逆接続防止の仕組みです。 左は電池のプラス側が接触している正しい接続ですが、黄色矢印部分は電気的に接触しており、電池はドーナッツリングに接触せず浮き上がっています。 右は間違ってマイナス側を当てたところですが、電池をドーナッツリングで受け止めており、電極は電池に全く接触していませんから電気的な接続は為されておりません。
|
|
|
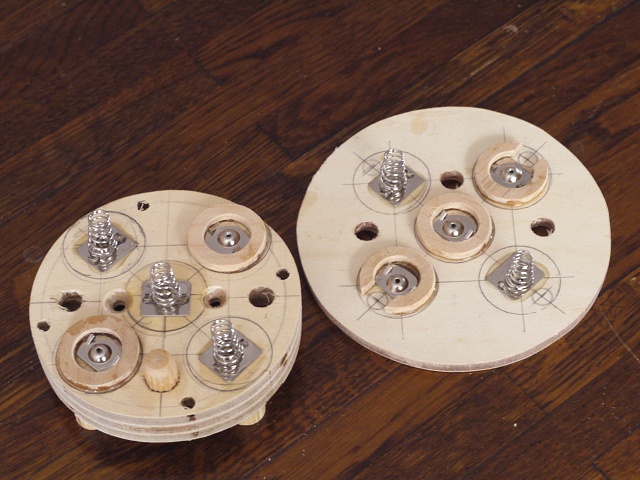 |
|
|
電池用のプラス・マイナス電極と逆接続防止リングをエポキシ接着剤で貼り付けました。 左が底蓋用で右が電池ボックス最上段(9層)ですが、電極の外側に4ヶ所丸く描かれているのは、電池ブロックを上の駆動回路ブロックに締結するネジ位置になります
|
|
|
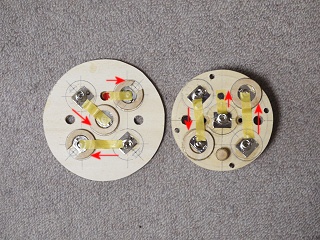 |
|
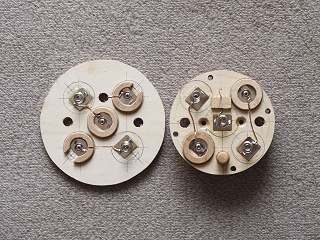 |
|
|
左は配線をする電極を間違えないようにするためのマスキングテープ貼りで、電流の流れは左上部の右向き矢印からスタートし、右中央の矢印で完結します。 そして右はその通りに0.9mmの裸銅線で配線が終わった状態です。
|
|
|
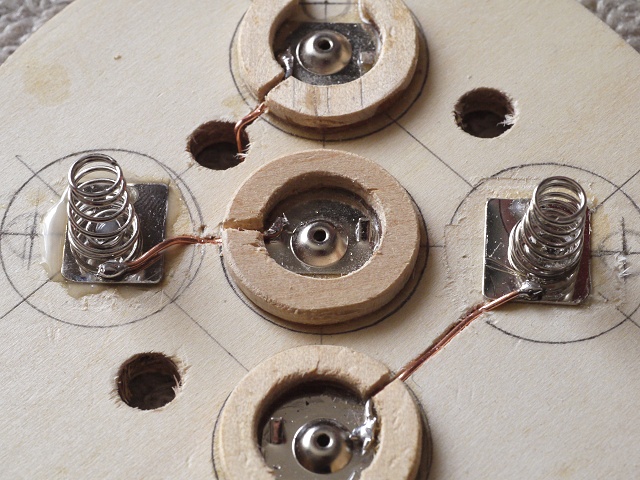 |
|
|
ドーナッツリングの部分は幅1mmの溝を彫りそこに落とし込んでいます。 図に見える電池位置を表す丸の外は板の面以下に銅線が沈むよう溝を彫りました。 尚ドーナッツ上の溝は後程傷や欠けの補修作業の時点で、エポキシパテで埋めてしまいます。
|
|
|
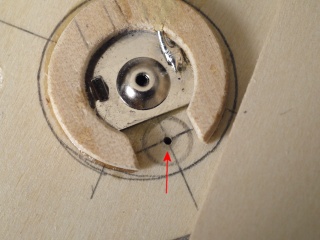 |
|
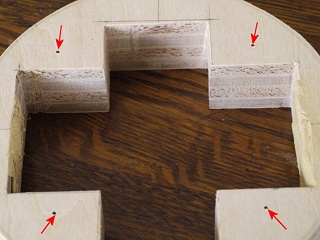 |
|
|
4箇所の電極の外側にネジ位置がありますので、センターポンチでマーキングします。 そしてこの下に貼り合せた5層〜8層を重ねて位置合わせをして1mmのドリルの根元まで穴あけをします。
|
|
5層〜8層にはこのように1mmの穴があきますので、これを5.5φのドリルで深さ12mmの穴をあけます。
|
|
|
 |
|
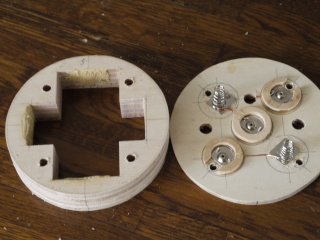 |
|
|
そしてM4の鬼目ナットを埋め込みます。 鬼目ナットはブロックの表面より若干沈むように締めこみます。
|
|
左が鬼目ナットを埋め込んだ駆動回路ブロックで、右は4.5mmの穴をあけた9層です。
|
|
|
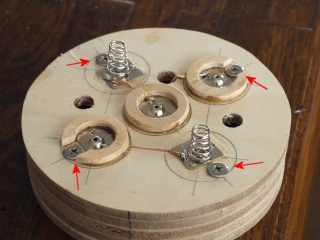 |
|
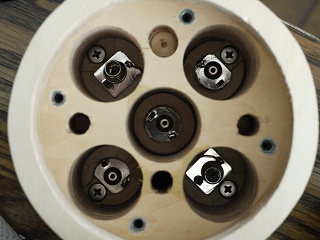 |
|
|
薄頭のM4 30mmボルトで9層を駆動回路ブロックに締結しました。 この9層は電池ブロックの上部に貼り付けられるので、これら4本のボルトが電池ブロックと駆動回路ブロックの連結ボルトになります。
|
|
9層の上に電池ブロックを載せてみました。(未だ接着はしません。) 電池穴の底にネジの頭が見えますから、これを緩めれば電池ブロックと駆動回路ブロックが分離できます。
|
|
|
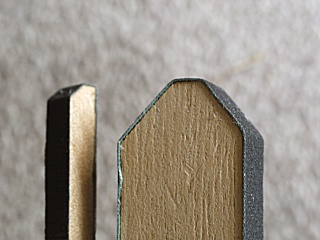 |
|
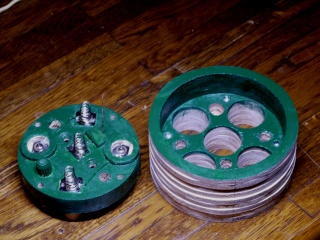 |
|
|
エポキシパテを塗りこんで72時間後に細い木の棒の先を加工して、#240の布ペーパーを切断しパテを削るヤスリを作りました。
|
|
そのヤスリで底の蓋と電池ブロックの底面のエポキシパテを塗りこんだ部分を研磨して平らにした上で、濃い緑色のペイントを塗り込みました。 そして48時間寝かせます。
|
|
|
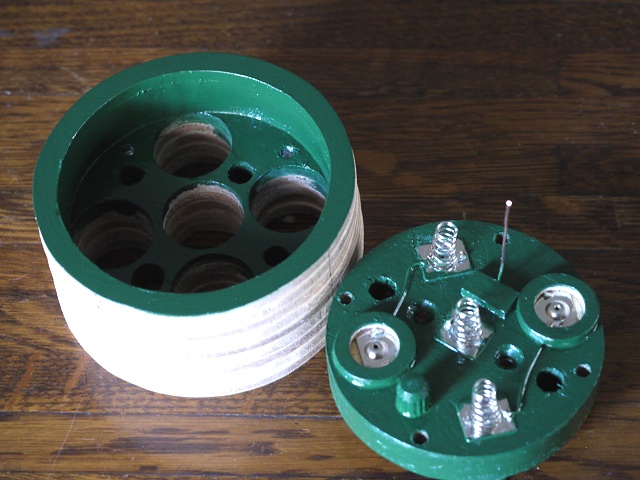 |
|
|
電池ブロック底部と蓋の塗装2回目です。 塗装液は薄め液で若干希釈していますが、2回塗りで塗りつぶせています。 但し表面にブツブツや傷が取れないまま残っており、この写真で順光のお陰でそれらは目立たないものの??
|
|
|
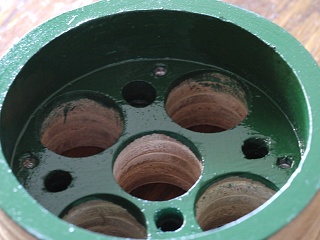 |
|
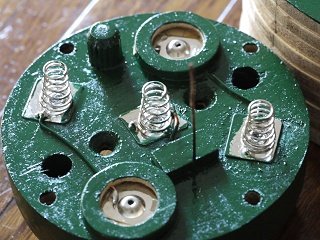 |
|
|
逆光で反射光を見ると、あれれれ・・・・・・ 大変見苦しい見え方になってしまいます。 そこで油性ウレタンつや消しニスの登場でゴマカシのテクニック?
|
|
|
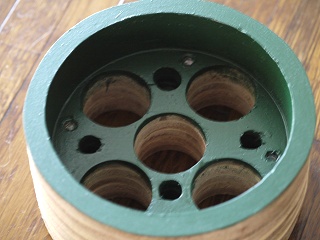 |
|
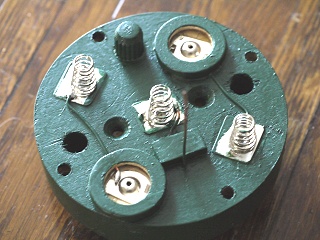 |
|
|
がこちらで、油性ウレタンニスつや消しクリヤーにペイント薄め液を10%入れたもので塗装した結果です。 左の場合は余り複雑でないことと接着剤のはみ出し、汚れが全く無いので余り変りありませんが、右では接着剤による汚れ、はみ出し、傷などが沢山あるため違いがかなり生じます。(艶が無いこと七難隠す!)
|
|
|
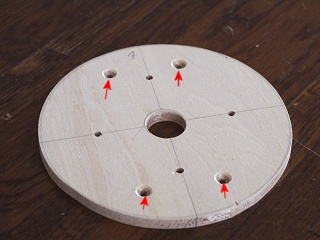 |
|
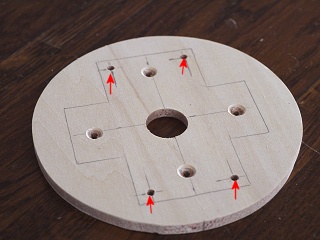 |
|
|
この板は4層の上面側で駆動回路基板の固定部分の加工ですが、この面からM3 7mmの皿ネジを挿しこみますので座ぐってあります。
|
|
同じ板の反対側のネジ穴には長さ5mmの全ネジスペーサーを当てて捻じ込みます。
|
|
|
 |
|
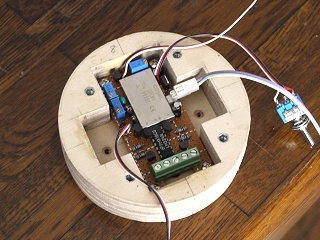 |
|
|
そうするとこのように高さ5mmの固定ポストとなりますが、ポストには深さ3mm程度の雌ネジがありますので?
|
|
4mmのM3 バインドネジで基板を固定できます。 ここでポストとそれを固定した皿ネジは最終固定をする際に瞬間接着剤を沁み込ませ緩み止めをします。
|
|
|
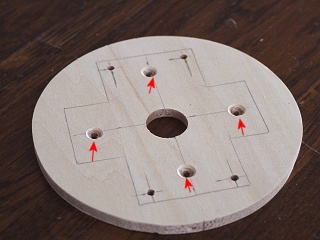 |
|
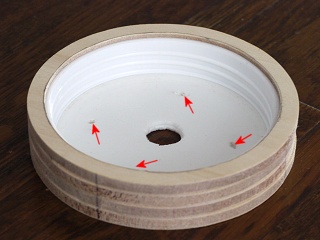 |
|
|
これも4層の下面ですが、矢印部分はLEDブロックの固定ネジ(M3皿ネジ 30mm)の為の座ぐりです。
|
|
これは0〜3層にプラスチック壜の蓋を嵌め込んだもので、左の4層をこれに固定すべく同じ位置にネジ穴をあけてあります。
|
|
|
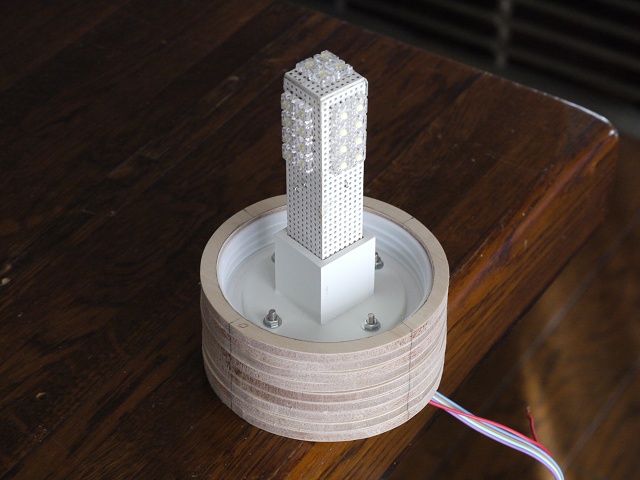 |
|
|
そしてLEDブロック、0〜3層、4層を共締めにした状態がこうなります。 4層の下部には最終工程で駆動回路ブロックが接着されますが、これらの固定ネジを緩めれば、ブロック単位で分解が可能となります。
|
|
|
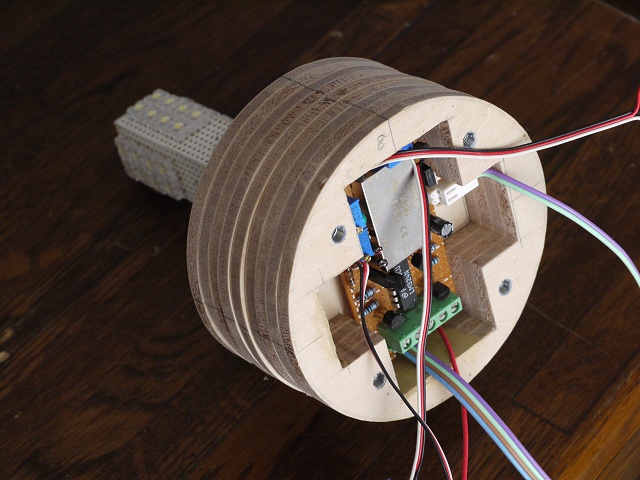 |
|
|
それらの下はこんな具合になります。 この後電源スイッチ、可変抵抗、2色LEDを組み込みます。 そして電池ブロックの最上層(9層)がここに見える鬼目ナットに締結されて一体化します。
|
|
|
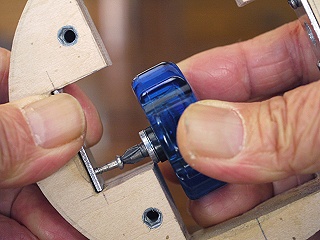 |
|
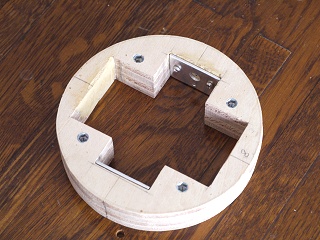 |
|
|
電源スイッチ、LED、可変抵抗を固定するアルミ板を狭いところでネジ止め中ですが、スタビードライバー(mini-Shopで販売しています。)で締め込めます。
|
|
2つのアルミ板が固定できましたので本体の穴あけになりますが、芯がぶれるとまずいので次週、慎重に進めます。
|
|
|
 |
|
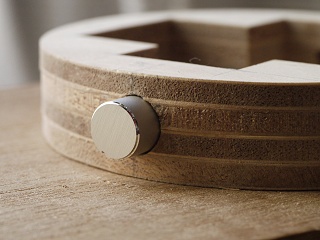 |
|
|
正に3度目の正直ですが、2回失敗後の作業は8φの貫通穴をあけてから丸棒ヤスリで広げて仕上げは替刃式ヤスリ(RS-310P)としています。
|
|
ツマミより1.0mm大きい穴にうまく仕上げられました。 失敗の精神的ダメージはこれにて拭い去れました。
|
|
|
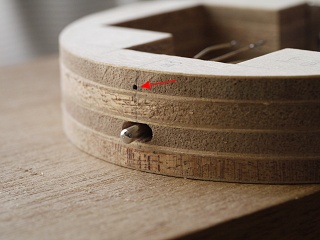 |
|
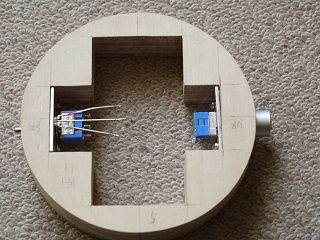 |
|
|
反対側の電源スイッチ取り付け部は 4 x 8mmの小判状の穴にうまく仕上げられています。 通常はレバーが中央で両方向にモメンタリーONの、(ON)-OFF-(ON)の接点構造のスイッチです。 矢印の先は1.2φの穴で塗装後に1.2φのナイロンワイヤーを差込みLEDの光を導きます。
|
|
やり直し作業が一段落した駆動回路ブロック。 やり直しは一番難しい電源スイッチと可変抵抗の取り付けを優先したので、電池ブロックを固定する鬼目ナットはまだ埋め込まれていません。 また駆動回路内部の配線は外面の研磨と塗装が終了後にやります。
|
|
|
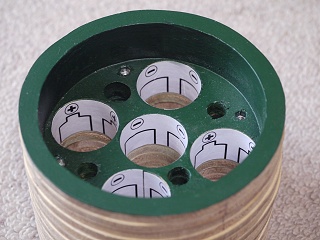 |
|
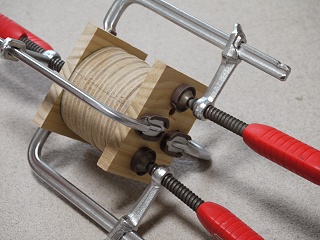 |
|
|
電池挿入方向ガイドの図を内面に貼り付けました。 同じ図が一周で4ヶ所ありますからどの方角から見ても挿入方向が判ります。
|
|
そして3つに分かれていた電池ブロックを一塊に(9〜23の15層)に接着しました。 位置合わせは8φの木ダボ3本を使っています。(圧着保持後すぐに引き抜く)
|
|
|
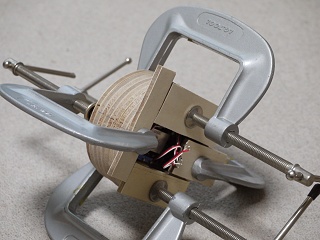 |
|
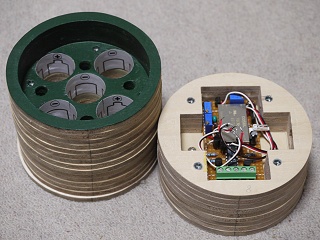 |
|
|
同様に0〜4層のLEDランプホルダーと駆動回路ブロックを接着します。
|
|
接着が終わった電池ブロックとLED駆動回路ブロックでいずれも上下を反対にして撮影しています。 駆動回路内部の配線は外面の研磨・塗装が終了後にします。
|
|
|
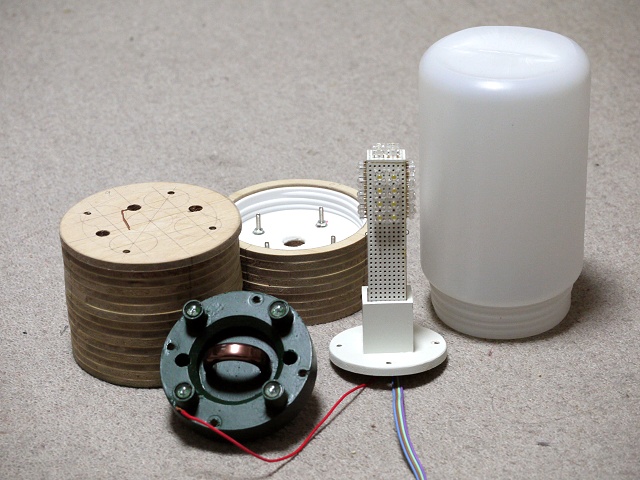 |
|
|
左から電池ブロック、底蓋、駆動回路ブロック、LEDランプブロック、ホヤで、これら5点がボルト12本で締結され、一番右のホヤは逆さに捻じ込み一体化する構造で、通常は底蓋のみ開閉されて電池の出し入れが行われます。
|
|
|
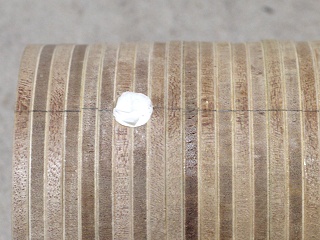 |
|
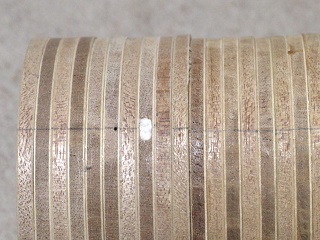 |
|
|
本体外側を研磨する前に二つの穴(電源スイッチのレバー、可変抵抗のツマミ)をティッシュペーパーを詰め込んで埋めました。 こうすることで内部が木粉で汚れるのを防げます。 ご覧の通り存在する段差は相当なものです。
|
|
|
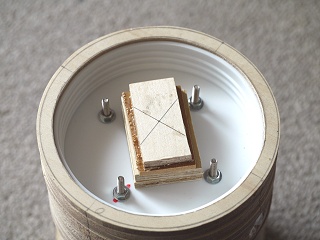 |
|
 |
|
|
上側は薄板を重ねて接着しそれを両面粘着テープで貼り付け、中心を描きました。 底側は既に抜き穴で出来た端材を使い埋め込み同じく中心を描き込んでいます。 こうすることで研磨後の半径の変化を確認できます。
|
|
|
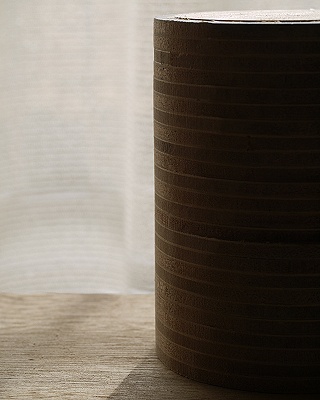 |
|
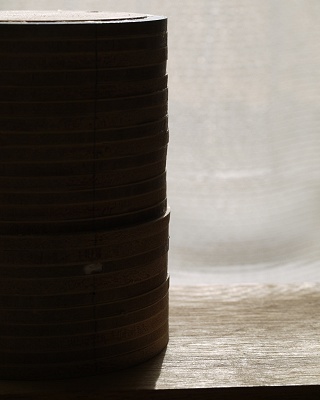 |
|
|
左の写真は1時間ほど研磨した面です。 よく見ると段差は未だ残っていますから更に研磨を続けないとなりません。 右は未研磨部分で、如何に大きな段差があるか良く判ります。
|
|
|
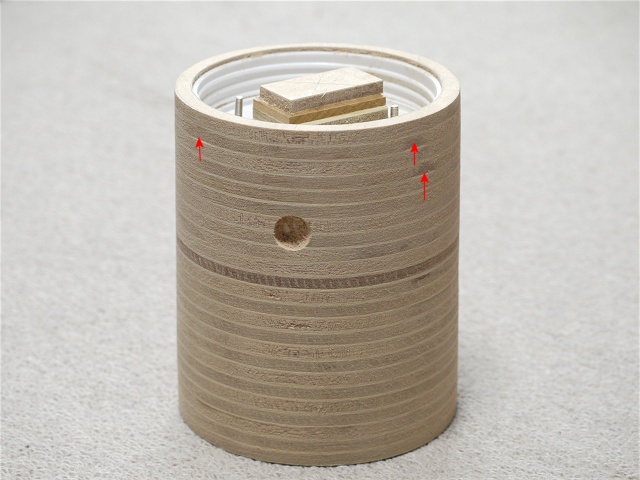 |
|
|
丸一日#60ペーパーでの研磨を続けた結果です。 まだ矢印先に0.2mm前後の浅い段差がありますので後1時間くらい研磨作業が必要です。 その後#120ペーパーに変えてやります。
|
|
|
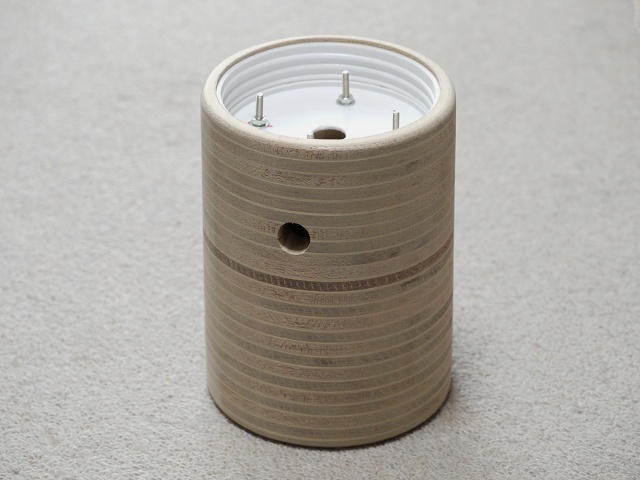 |
|
|
#120ペーパーで全体の曲面を修正しながら削りこみ僅かに残る凹みも取り除きました。 そしてトリマーで上下の角の面取りをした後に#240ペーパーで仕上げ研磨を施しました。 研磨方向ですが#60の際には上下方向に研磨し外面の垂直出しに留意しましたが、#120と#240では外面円周方向に変え滑らかな曲面となるようにしています。
|
|
|
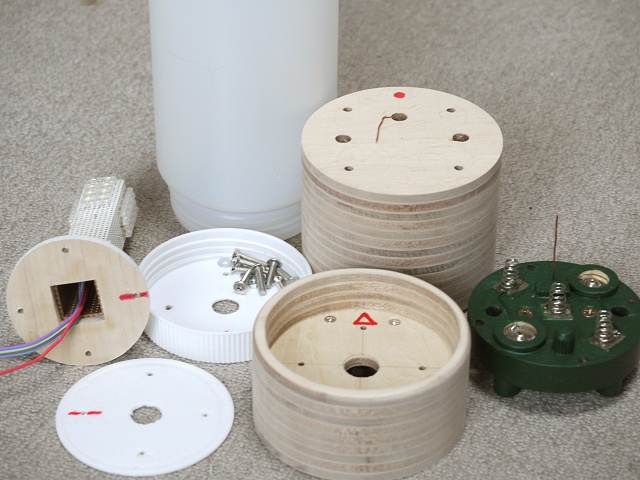 |
|
|
掃除機で木粉を吸い取ってから締結ネジを緩めて分解しましたが、再び組み立てる時の組合せ方向・位置が判るよう、電池ボックスと駆動回路ユニット間は赤丸で、駆動回路ユニットとプラスチック蓋は赤三角、プラスチック蓋の内側と発泡クッション、そしてLEDランプユニットは赤の太い線でマーキングしました。
|
|
|
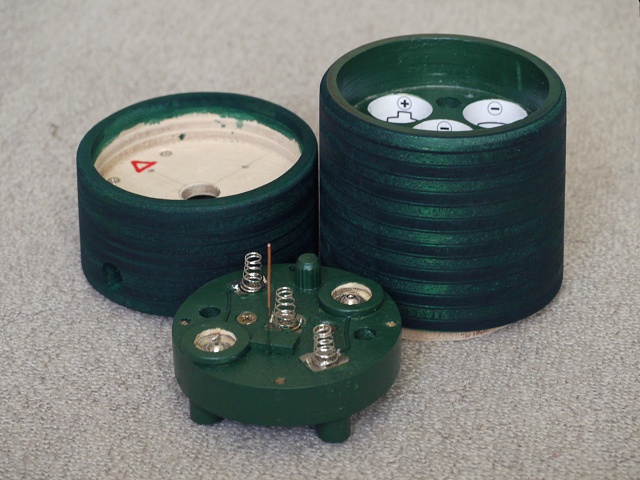 |
|
|
その上で分割した本体を着色しました。 ポアステインは、グラスグリーンに少量の黒とゴールデンイェローを加え青っぽさを押さえながらダークな色調としています。 写真では蓋の色は更に黄色が強いですが、今回使うニスは油性タイプで黄変がかなりでますのでニス塗り後は同じような色調になると思います。
|
|
|
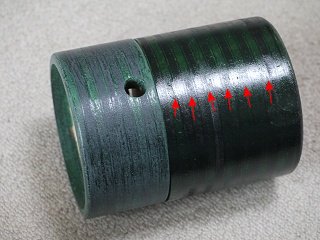 |
|
 |
|
|
左側は本体上部の駆動回路ブロックで右が電池ブロックです。 左側は油性ウレタンニス透明クリヤーを2回塗って乾燥後研磨したものでかなり良好な(平滑度が高い)塗装面です。 右側の矢印の先は反射が鈍いですが、これは木繊維のパイプ断面部でニスの吸い込みがまだ不十分であることを意味しています。
|
|
こちらの写真は4回塗装後の研磨前(左)と研磨後(右)です。 左側の緑色に光って見える部分は塗装面と木目が平行の部分で大変美しく見えます。 左側はもうこれで充分でつや消し塗装に入っても良さそうですが、右側の研磨後の具合もかなり良くなっているものの、後2回の塗装は不可欠だと思われます。
|
|
|
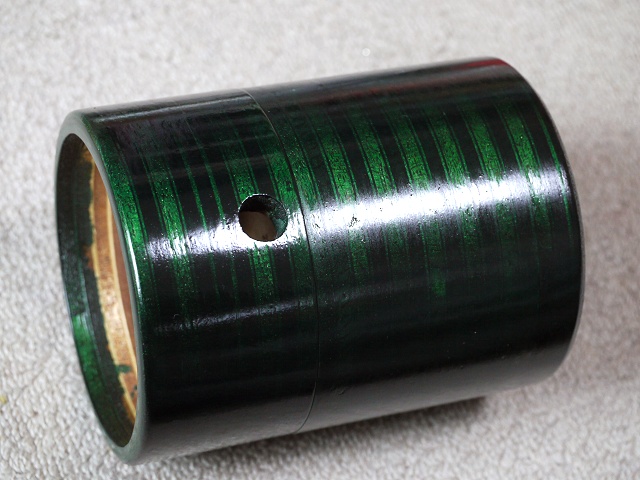 |
|
|
6回目の塗装が済んだところです。 木目が面と直角になる部分の木繊維のパイプもニスで埋まり、ほぼ全体が同じような艶を持ち出しています。 次のつや消し塗装でこのギラギラした艶は薄れてよりしっとりとしたシックで七難隠しの半艶に変貌する筈です。
|
|
|
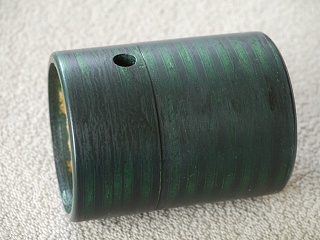 |
|
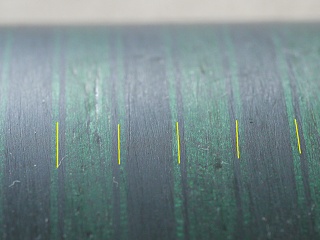 |
|
|
上の写真の状態に油性ウレタンニスつや消しクリヤーを1回塗り塗装作業が終わった状態です。 カメラとランタン本体の間に何かフィルターでも入れたように艶が消えています。
|
|
ちょっぴり脱線ですが黄色い線は5.5mmシナ合板の貼り合わせの位置を表しています。 隙間がまったくなく接着後の圧着保持がうまくいっていることを表しています。
|
|
|
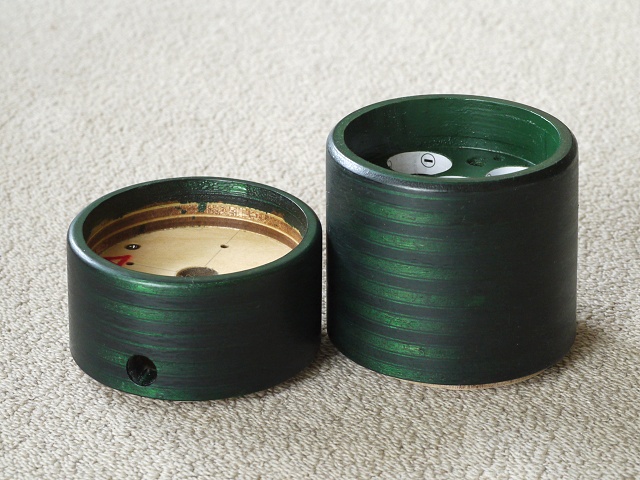 |
|
|
使用位置である縦置きにしました。 右側の上部は実は底部で内側はペイント仕上げになっていますが、ニス塗りの外側と色味が殆ど一致していると思います。 これは前にも話した通り着色後は青みがあったのですが油性ニスの黄変により色が揃いました。
|
|
|
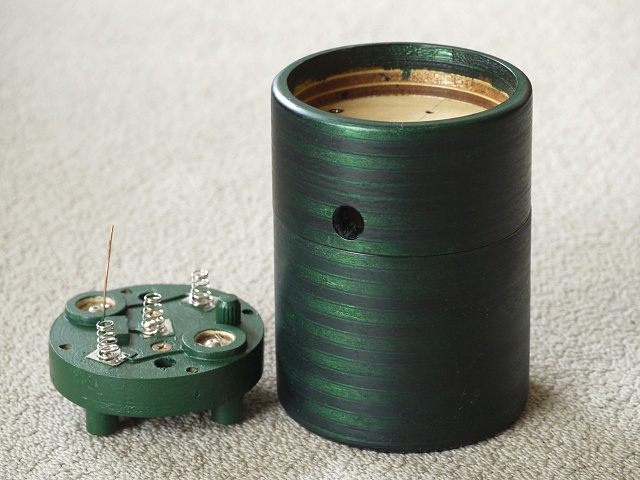 |
|
|
それを更に確認できるのがこの写真でしょう。 但し木繊維を切断している部分ではニス塗りは明度が下がってしまうので、全体的に暗く見えますが、木繊維と平行になっている部分はかなり明るくそして大変美しく見えます。
|
|
|
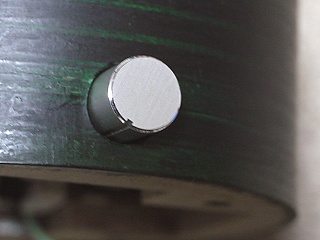 |
|
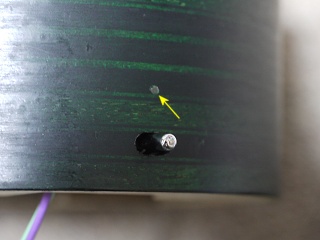 |
|
|
可変抵抗を固定した後の外観で、ツマミの周りの隙間はほぼ均等な0.5mmくらいで、期待していたより良い出来栄えです。 現在左に回しきった最も暗い状態で、右に回すとリニヤーに変化し明るくなります。
|
|
こちらは電源スイッチとLEDを固定した後の外観で、レバーを右へ倒すとON、左へ倒すとOFFとなりますが、通常はセンターに留まります。 矢印の先が1.2φのナイロンワイヤーで、LEDの光を導きます。
|
|
|
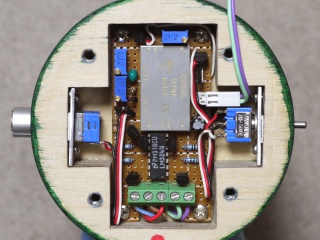 |
|
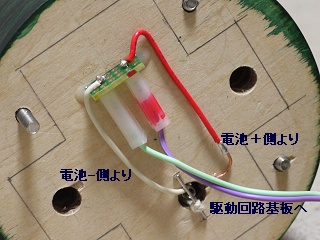 |
|
|
駆動回路ブロックの内部の様子。 結構ぎっしり感がありますが、必要とあらば分解してやるのも容易ですし3つのポテンショメータの調整も容易です。 右手上に伸びる2本のワイヤーが電池ブロックへ導かれます。
|
|
これは電池ブロック最上部の面で、中央の2つのコネクターを外すと駆動回路ブロックと電池ブロックが分離できます。 中央の固まりは最大の高さが7mmで、左写真の中央に見える銀色のDC-DCコンバータの上の空間に納まります。
|
|
|
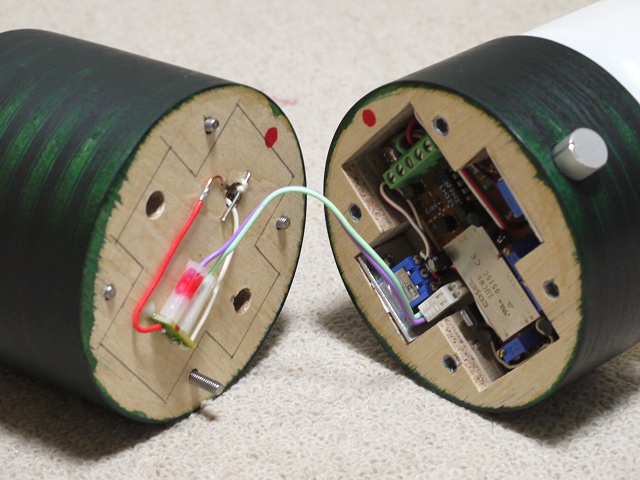 |
|
|
左の電池ブロックと右の駆動回路ブロックを連結する直前です。 電池ブロックから出ている4本のネジを上に見える両ブロックの赤丸の合印を見ながら締めこめば、2つが連結されます。
|
|
|
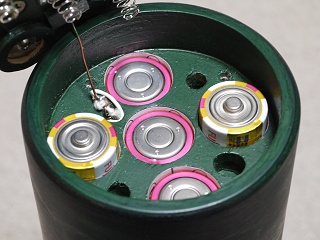 |
|
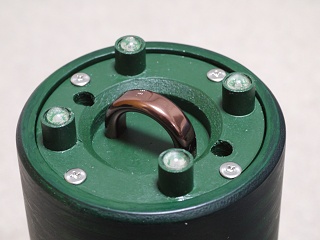 |
|
|
連結が完了したら極性の図を見ながら電池を装填します。 極性を間違えたら絶対に点灯いたしません。 尚電池のマイナスからの引き出し線の処理は前にお見せした図を参照ください。
|
|
蓋を被せて4本のネジを締めこんで点灯準備完了です。 そうそう脚には半球型のクリヤーパンポンを埋め込みました。 またぶら下げて使う時と天井から吊る際には中央のU字金具を使います。
|
|
|
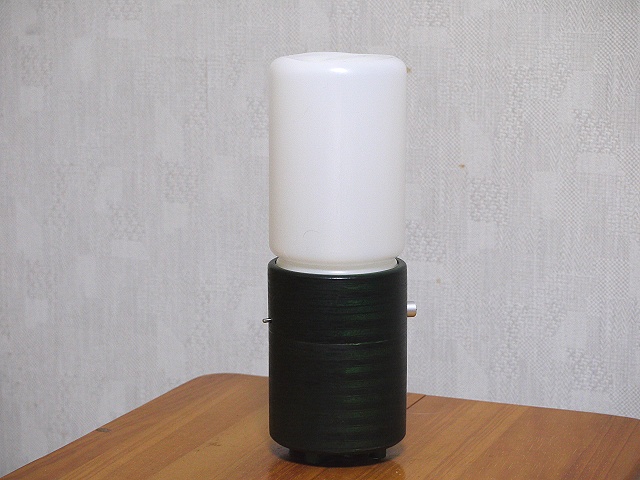 |
|
|
完成したLEDランタンの全景です。 明るさ調整のツマミと電源スイッチの位置が反対側になっているのは、今回の十字レイアウト電気回路では止むを得ないのですが、若干不便と言えば不便です。
|
|
|
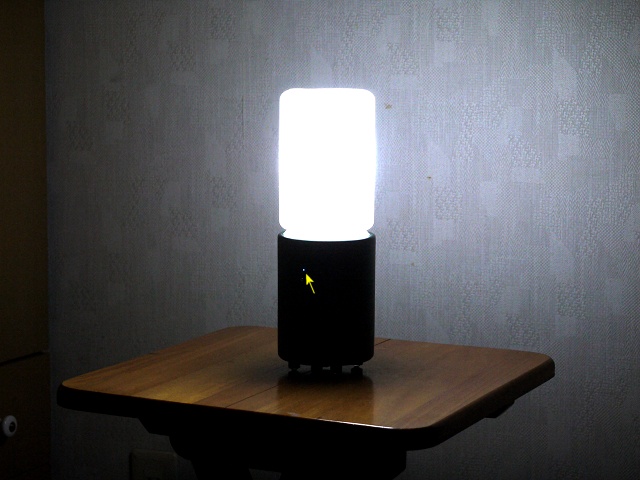 |
|
|
最大光量にて点灯しました。 露出は全く補正せずで撮影しており見た目とは少々異なります。 その辺については基礎実験でのこちらの解説をご覧ください。 尚矢印の先のポチッはLEDによる電圧インジケーターです。 これが赤紫になったらまもなく電池の寿命になり消灯します。
|
|
|
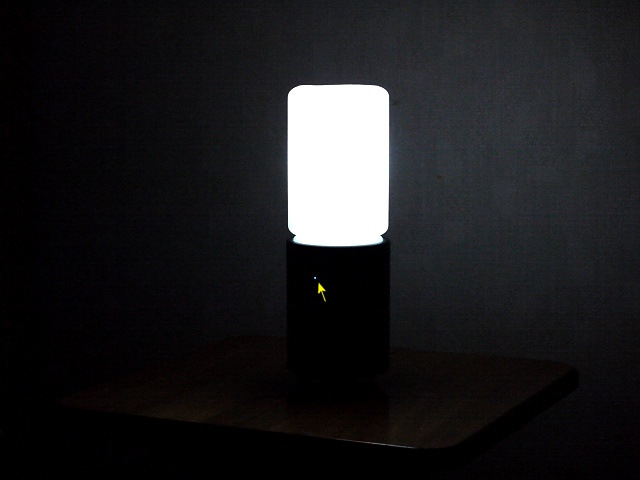 |
|
|
光量を最小に絞ったのがこちらで(勘違いを防ぐため光量ゼロにはなりません。)、こちらも露出の補正は全くしておりませんが、見た目とかなり違っております。 感覚的には非常事態にはこの明るさでも結構使えると思いますので、連続運転テストでどの位の電池寿命になるのかが楽しみです。
|
|
Copyright (C) 2001-2019, Vic Ohashi All rights reserved.