|
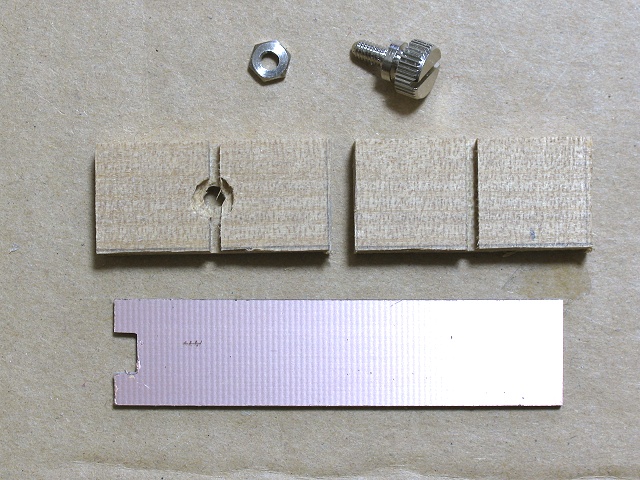 |
|
|
電池ホルダーを構成する部材を切り出しました。 中央は上下の板で1.6mm幅、深さ2.5mmの溝をトリマーで彫っています。また片方には左上に見えるM3のナットを埋め込む穴を削りだしています。 下は仕切り板ですが、穴が全くあいていないプリント基板製作用の板を使いました。 片面に銅箔が貼ったままになっていて余計ですがこれより安いグラスエポキシ板はありません。 左側の切り欠き部分はM3のナットをまたぐ為のものです。
| |
|
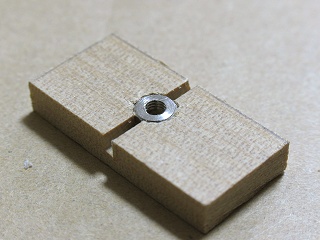 |
|
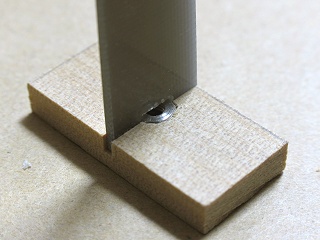 |
|
|
M3のナットはこのように嵌め込まれます。 現在は嵌め込んだだけですが本番ではその前にエポキシ接着剤を薄く塗ってから嵌め込みます。 |
|
仕切り板は切り欠きのある方をこのように溝に落とし込みます。 これも本番ではエポキシ接着剤を溝に塗ってから溝に落とします。
|
|
|
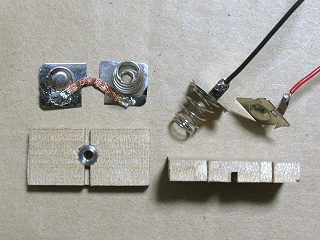 |
|
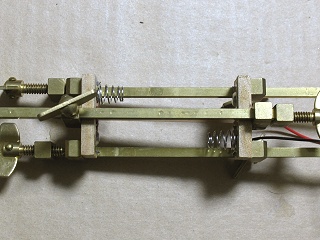 |
|
|
電池受けの電極の前加工をしておきます。 左は仕切り板の厚み(1.6mm)だけ左右に広げるため一度中央を切断後、網状ワイヤーで繋いだ物です。
|
|
電池受け電極をエポキシ接着剤で貼り付けた後に、電池ホルダーの組立てをします。 圧着保持には180mmのハタ金を使っています。
|
|
|
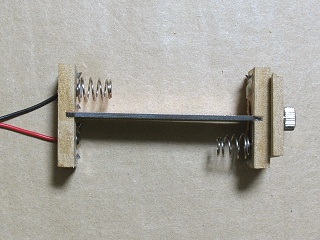 |
|
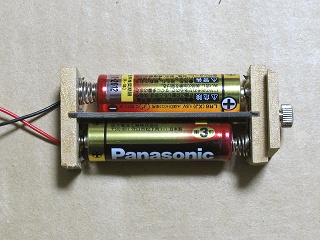 |
|
|
完成したH型電池ホルダー。 右側にはケースが固定できるかどうか確認のため3mm厚の板を飾りネジで固定してあります。
|
|
電池も所定の位置に嵌め込んで見ました。 特に問題はありません。
|
|
|
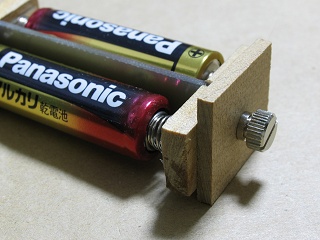 |
|
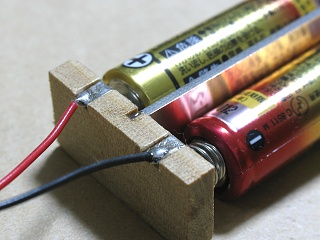 |
|
|
底側のアップ。 どうも無粋なネジで面白くないのですが、入手可能な飾りネジはこんな物しかありません。
|
|
反対側のアップ。 ケースがワイヤーに当たることなく被ります。 この左側にコンバーター基板が入ります。
|
|
|
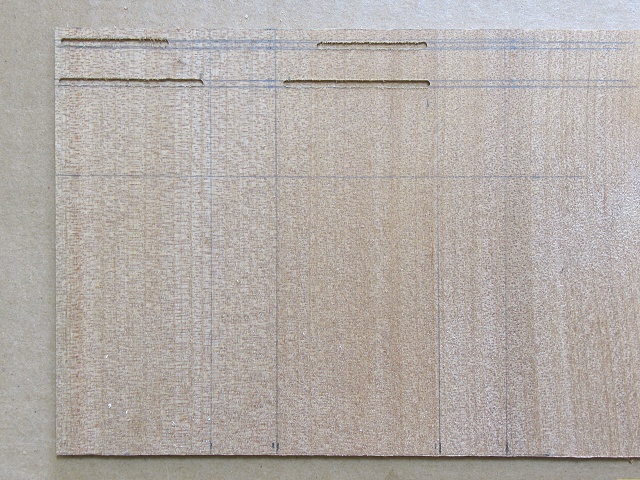 |
|
|
幅の広い側板には溝を2本ずつ彫る必要があります。 直径1.6mmのSS1-1.6G トリマービットで加工しました。 幅の狭い側板にも彫らないとならないのですが、それは切断後になります。
|
|
|
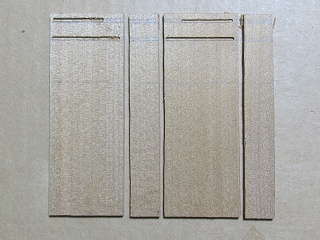 |
|
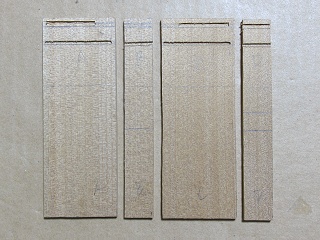 |
|
|
縦方向の切断をして切り離し、幅の細い板は15mmに替刃式ヤスリ(M-20GP)で寸法出しをします。
|
|
幅の狭い板の溝を彫りこんでしまいます。
|
|
|
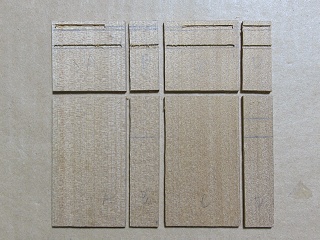 |
|
 |
|
|
LEDヘッド周りと電池カバー部分に切り離します。 これで8ピースになりましたが、切り離す前の隣通しの関係を維持します。
|
|
左写真の左上の2枚をL型にエポキシ接着剤で貼り合わせます。 接合部分の直角度や直線性に十分注意。
|
|
|
 |
|
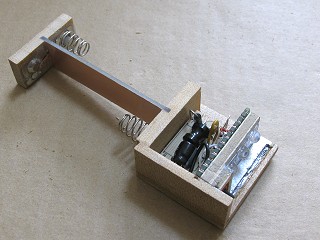 |
|
|
貼り終ったL型のヘッド部分に電池ホルダーを接着します。 はみ出たエポキシは完全硬化する前にナイフで削り取ります。
|
|
DC-DCコンバーター、LEDブロック、電池ホルダーの間の結線を済ませ、LEDブロックを溝に落とし込みました。
|
|
|
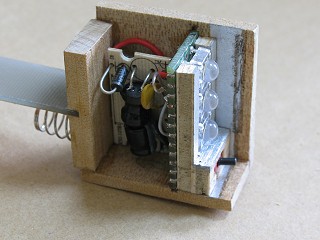 |
|
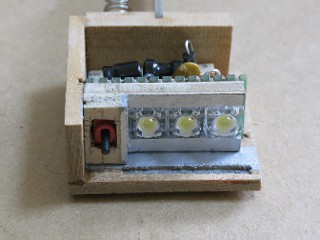 |
|
|
DC-DCコンバーターは現在宙ぶらりんの状態ですが、この上にケース側板を被せるときにはホットメルトまたはエポキシ接着剤で固定します。
|
|
前面から見るとこんなあんばいです。 手前の溝には後ほどPET板が嵌まり込みその左側にはスイッチカバーが貼り付けられる予定です。
|
|
|
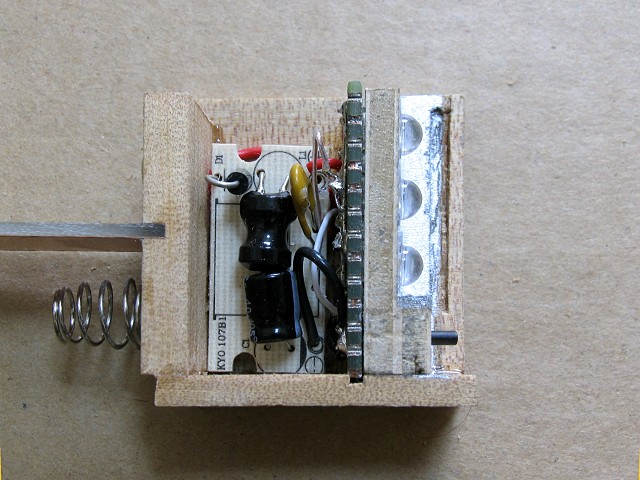 |
|
|
落とし込んだDC-DCコンバーターの周りがワイヤーでぐちゃぐちゃしていますが、右側のLEDブロック基板とショートしないような配慮は十分にされています。
| |
|
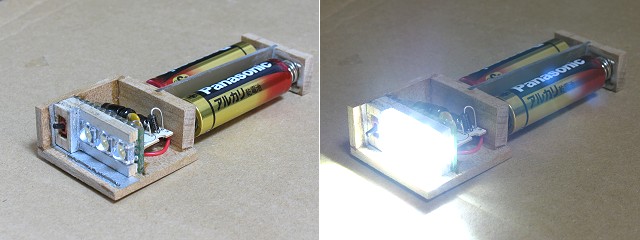 |
|
|
もう電池を入れれば点灯できるので早速試してみました。 さすが「雷神!」です。 3本ですが極めて明るくしかも広角度であるため照射範囲が広く、コンパクトLEDランプ 2とは雲泥の差です。 だからと言ってコンパクトLEDランプ 2は使い物にならないわけではありません。 コンセプトが基本的に違うからです。
| |
|
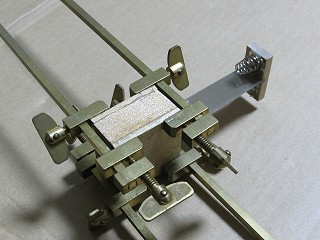 |
|
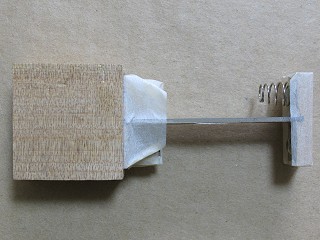 |
|
|
本体組立ての最終段階はLEDブロック周りから。 接着剤は相変わらず30分硬化開始型エポキシ接着剤です。
|
|
電池ホルダー部分で電池カバーと触れる部分はマスキングテープを巻き付けました。 これで電池ホルダーと電池カバーの間に少なくとも0.1mmの隙間が出来ますし、電池ホルダーと電池カバーの接着も防止できます。
|
|
|
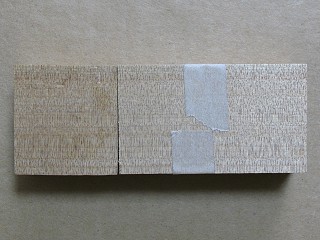 |
|
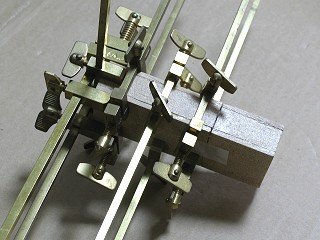 |
|
|
電池カバーの板を当てて見た所ですが、LEDブロック部分との突き合せ調整もしておきます。
|
|
電池カバーの板を貼り付けました。 やり過ぎのように思えるかもしれませんが、圧着保持に10本のハタ金を使っています。
|
|
|
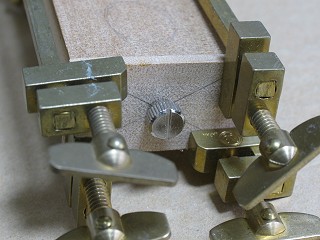 |
|
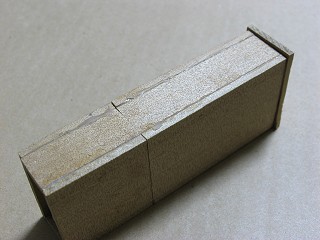 |
|
|
最後に底板を貼り付けました。 電池カバー固定ネジの位置がずれないよう、ネジを締めこんで底板を軽く接着後ハタ金で圧着保持しています。
|
|
本体の組立てが終了しましたが、まだ成形作業が残っています。
|
|
|
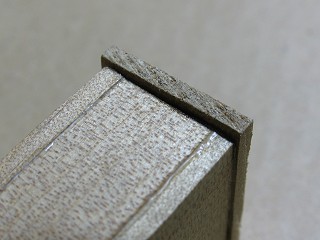 |
|
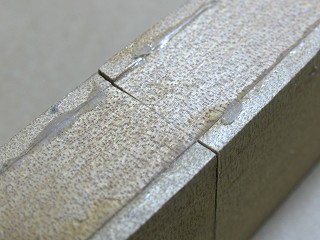 |
|
|
底板は大きめに切断し固定ネジたる飾りネジの穴の位置決めをしながら貼っていますので、この出っ張りを完全に削らねばなりません。
|
|
本体側板の接着部分にも段差や接着剤のはみ出た箇所がありますから、平らに研磨すると同時にそれらを落としてしまわないとなりません。
|
|
|
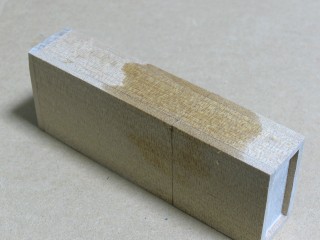 |
|
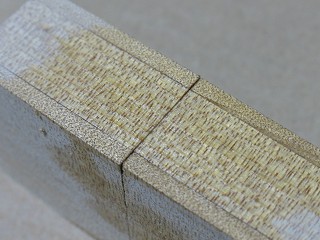 |
|
|
このくらい削れば良いかな?というレベルになったら水で濡らします。
|
|
削り残しで一番問題ははみ出た接着剤ですが、水で濡らしても白っぽいままだとNGで、こんな状態であればOKです。
|
|
|
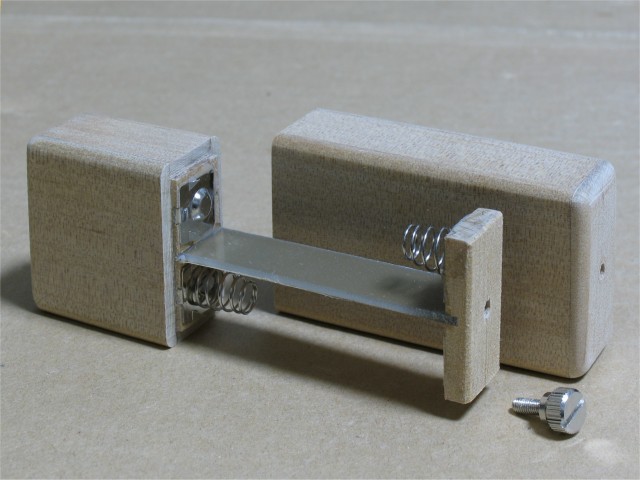 |
|
|
その後全ての角をボズ面ビット(BZ-10G)で削ってスポンジ研磨剤(細目)で仕上げました。 これで塗装に入れます。
| |
|
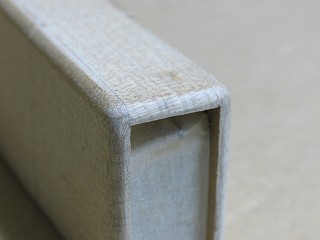 |
|
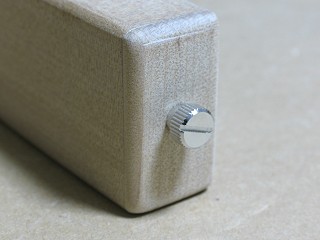 |
|
|
前面内側は保護のためマスキングテープを貼ったままです。
|
|
底面(背面)。 少々無骨ですが機能は十分果たしてくれるネジ止め式です。
|
|
|
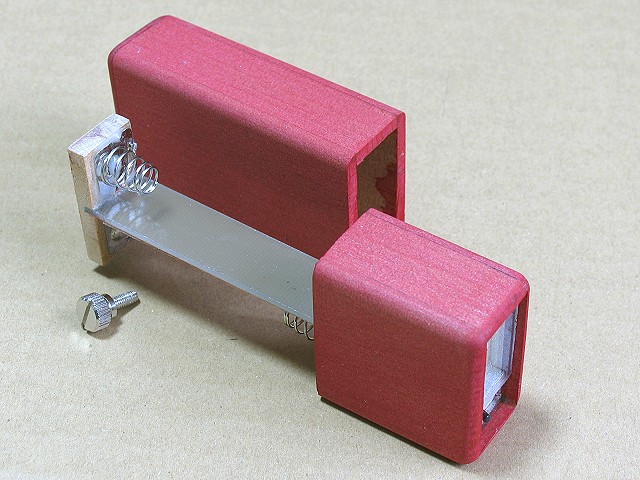 |
|
|
着色はポアステイン(ワインレッド)で、水で2倍に薄めて3回塗りとしました。 かなり派手やかなローズピンクと呼んだ方が良いと思われる色合いです。
| |
|
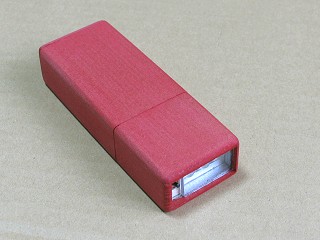 |
|
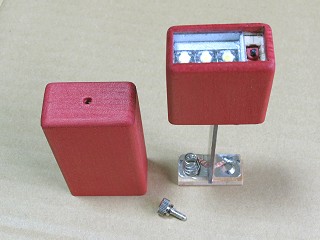 |
|
|
はみ出た接着剤を削り残した部分もなくかなり良好です。
|
|
前面のスイッチ周りには飾りの板(2mm厚)が嵌まり込みますが、それは塗装終了後。
|
|
|
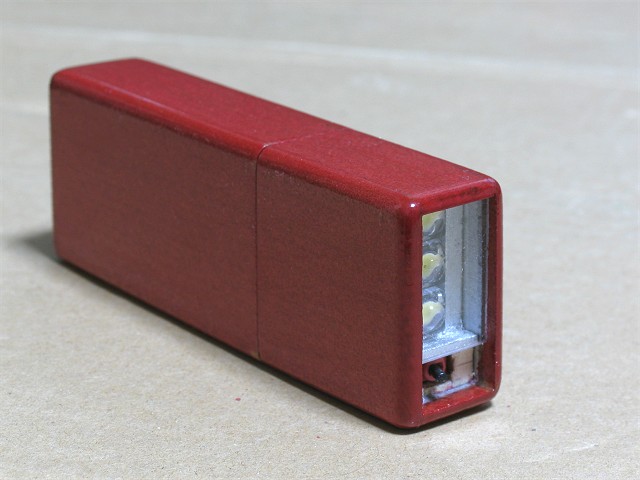 |
|
|
水性ウレタンニス(透明クリヤー)を4回塗りして1次塗装作業は終了です。 この後帯部分の塗装とつや消しニスによる仕上げ塗装があります。
|
|
|
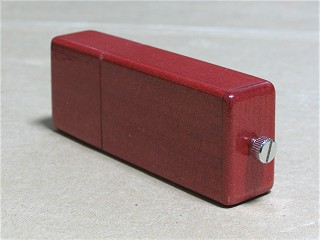 |
|
 |
|
|
後方から見た感じです。 電池カバーロックネジが大げさに見えます。
|
|
コンパクトLEDランプ 2とのツーショットですが、実際に握って感じる大きさの差は見た目より大きいです。
|
|
Copyright (C) 2001-2019, Vic Ohashi All rights reserved.