|
 |
|
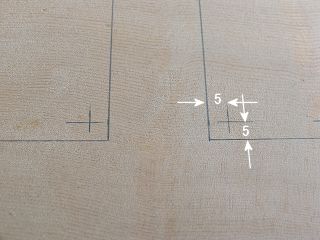 |
|
|
側板の切り出し。 心持ち大きめに(0.5mm以内位)切断しておきます。 中抜き加工後に外寸成形をカンナとヤスリで行います。
|
|
中抜きの角の部分は丸めますが、10φ木工ドリルで穴あけをするので、穴位置を線引きしておきます。
|
|
|
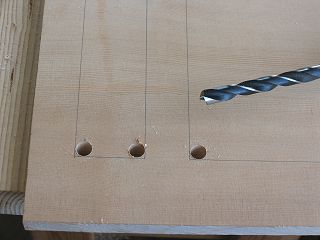 |
|
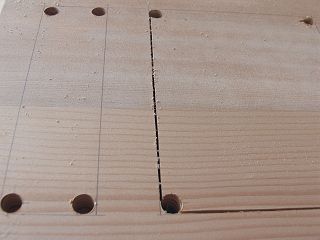 |
|
|
10φ木工ドリルで穴あけが終わったところです。 穴が垂直にあくよう慎重に作業する必要があります。
|
|
そして電動ジグソー(CJ-250)とその専用円仕上切りブレードで穴と穴を切断線に沿って切り抜きます。 このジグソーは切断方向の制御がしやすいので、+0.5mm以内に収める事が比較的容易です。
|
|
|
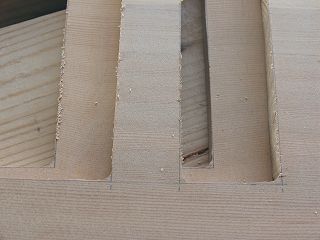 |
|
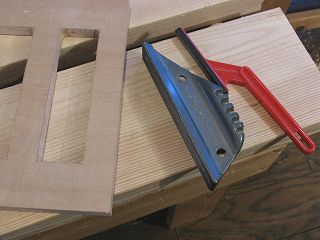 |
|
|
電動ジグソーで切抜きが終わりました。 少々バリが出ていますがこれは気にすることはありません。 切断線にかなり正確に沿っていることが判るでしょうか?
|
|
その切断面を研磨して多少の凸凹を落としますが、2つの替刃式ヤスリ(M-20GPとRS-310P)を使います。 後者は隅の丸い部分の研磨に使用します。
|
|
|
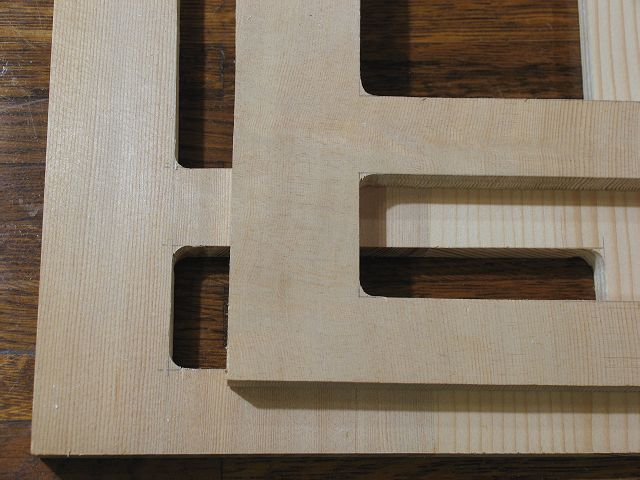 |
|
|
このテーマで最も時間が掛かるのがこの1次研磨です。(2次研磨は後ほど必要!) 私の場合電動ジグソーで+0.3mm以内の精度で切断していますから研磨量は多くはないのですが5時間近く費やしています。 寸法精度は余り問題ありませんから手を抜こうと思えばいくらでも抜けるのですが、きちんとした研磨が出来ていないと塗装するとざらつきや凸凹で馬脚を現します。 この辺りは難易度の問題ではないことをお忘れなく。
|
|
|
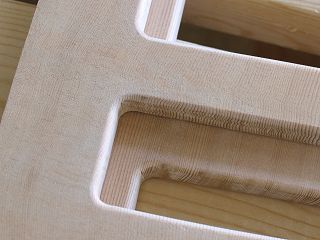 |
|
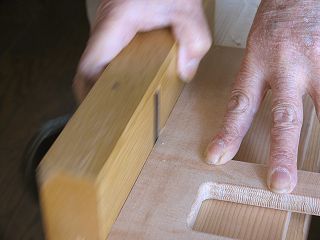 |
|
|
内側の面取りを済ませました。 替刃式ヤスリ(M-20GPtoRS-310P)を使って丸みを出し、その後に#240のサンドペーパーを細い棒に巻きつけた物で仕上ました。
|
|
次が側板外側部分の成形寸法出しです。 カンナを使い木口面を直角に且つ直線性を高めます。
|
|
|
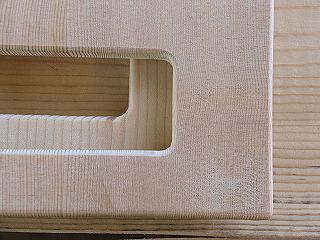 |
|
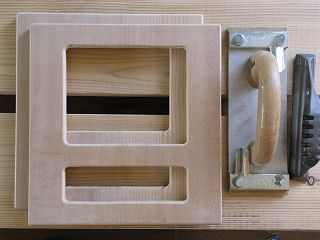 |
|
|
そしてこちらも面取りを済ませます。 M-20GPで丸みを削りだし、#240ペーパーで仕上研摩しました。
|
|
最後が表面と裏面の仕上研摩で、ハンドサンダーに#240ペーパーを付けてつるつるになるまで研摩します。 これで塗装に入れますが、接着部分覆う前作業が必要です。
|
|
|
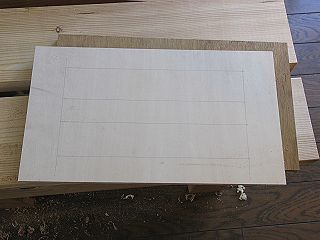 |
|
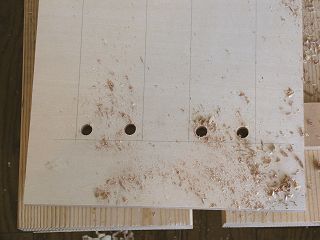 |
|
|
踏み板芯材を切断しました。 私は手持ちは材を使っているので、ラワン合板とシナ合板の混用としていますが、シナ合板は高いだけで芯材としては意味がありません。
|
|
芯材にも抜き穴がありますので、予め抜き穴の長方形の内側に10φの穴を開けて電動ジグソーで切断します。
|
|
|
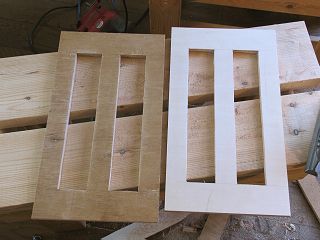 |
|
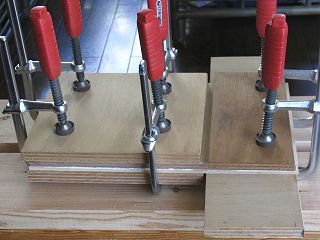 |
|
|
この抜き穴の切断面は研摩や成形は不要でバリを落としておけば十分です。 これに被せる部材は2-3mm大きめにシナ合板から切り出します。
|
|
4-12-4mmと重ねて接着しますが、圧着保持が極めて重要で、ここではバクマクランプを使い思いっきり締め上げています。 上に重い物を載せた程度では全く圧着したことにはなりません。 このまま1晩寝かします。
|
|
|
1晩寝かすという理由についてちょっと触れておきます。 接着が終了後に芯材の両面に貼って飛び出ている板を削り
取りますが、その際に木工ボンドが完全硬化していないとうまく削り取れません。 木工ボンドは数時間で実用強度に
達すると言われていますが、完全硬化までには12時間を要します。 そこで1晩寝かせることで完全硬化を得ようとして
いるわけです。 こんなことを念頭において接着作業が夕方になるように作業を進めれば、作業が出来ない無駄な時
間を排除することができます。
|
|
|
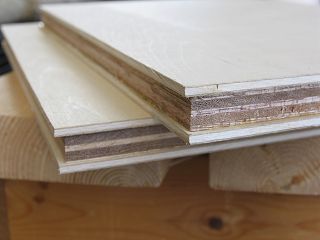 |
|
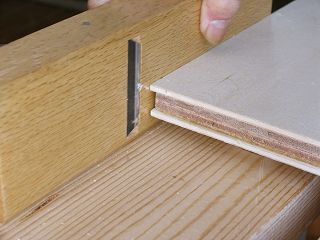 |
|
|
接着が終わった状態で、外側の薄板は芯材よりも飛び出していますので、これらをカンナで削り取りヤスリで仕上ます。
|
|
カンナがこのように当たるようにすれば、材料の切削面は直角を維持したまま削れます。 詳しくはこちらをお読みください。
|
|
|
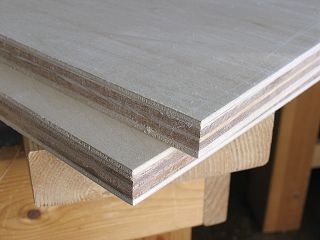 |
|
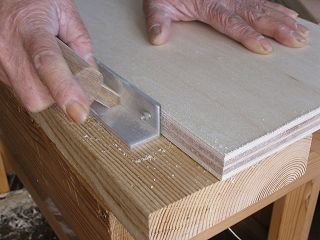 |
|
|
芯材と同一寸法になるよう削ってやればOKです。 切削後はあたかも20mm厚の合板に見えます。
|
|
これらの切削面は塗装をしませんので仕上げ研摩は替刃式ヤスリ(M-20GP)で研摩しただけで十分です。 ここではM-20GPの替刃で作った自作直角研摩ヤスリを使っています。
|
|
|
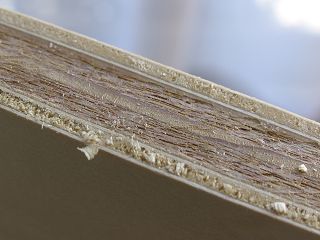 |
|
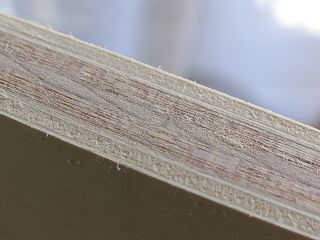 |
|
|
カンナで削った後はこんな感じです。 仕上カンナではありませんから表面はざくざくしておりこのまま接着したり木口テープを貼るには不十分です。
|
|
替刃式ヤスリ(M-20GP)で研摩した後はこのようにかなり面が滑らかになり、接着や木口テープ貼りに十分な面となります。 特製の20mm厚合板? でも中抜きしてあるので軽いです。
|
|
|
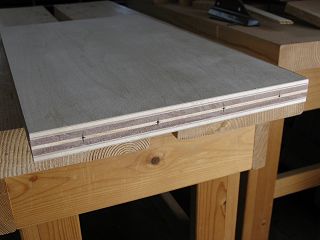 |
|
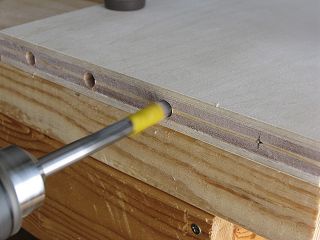 |
|
|
センターポンチで8φ木ダボを埋め込む位置に円錐状の凹みをつけました。 4本使用しますが穴間隔は50mm、両端の穴は端から30mmの所にあります。
|
|
8φ木工ドリルで穴あけ中です。 合板は特に気をつけないといけませんが、木口面はドリルが横滑りしやすいので慎重にあけます。 穴の深さは21-22mmとします。
|
|
|
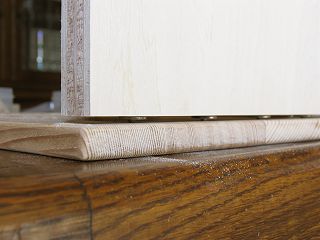 |
|
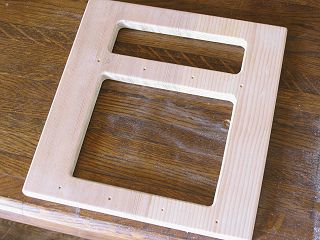 |
|
|
あけた穴にマーキングポンチを挿し込んで、水平に置いた側板の所定の位置に載せ十分に調整後上から押し付けると?
|
|
このように側板側の穴位置に円錐状の窪みが出来ます。 ここに8φ木工ドリルで10mmの深さの穴を開けます。
|
|
|
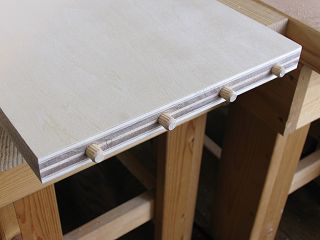 |
|
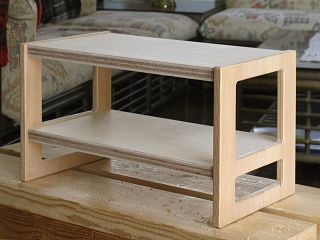 |
|
|
うまくできたか確認のため木ダボを踏み板側に埋め込みました。 接着はしませんので、ペンチを使えば容易に抜けます。
|
|
そして側板を木ダボに嵌め込みました。 これで完成後の姿が登場します。
|
|
|
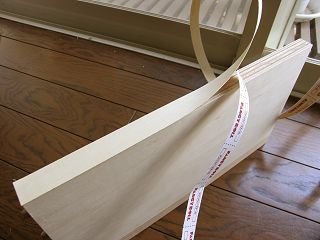 |
|
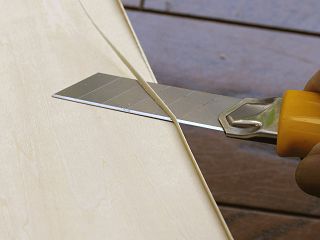 |
|
|
ばらして踏み板の側面に木口テープを貼り付けます。 詳細な作業方法はこちらをご覧ください。
|
|
テープ幅は必ず板厚よりも大きいのではみ出た部分をカッターナイフでこのように切断します。
|
|
|
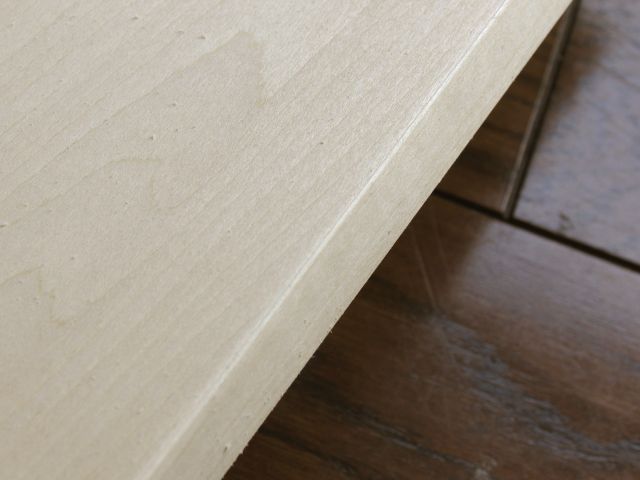 |
|
|
またまた替刃式ヤスリで貼り付けた部分を軽く削り段差を完全に取った上で面取りをします。 削りすぎると合板の地肌が露出してしまうので、面取りの量は余り取れません。 これでぐんと豪華さというかムク材を使ったかのようなイメージに変貌します。 木口テープの使用は初心者でも容易に会得できますが、その効果は大変大きく是非ともお勧めしたいテクニックです。
|
|
|
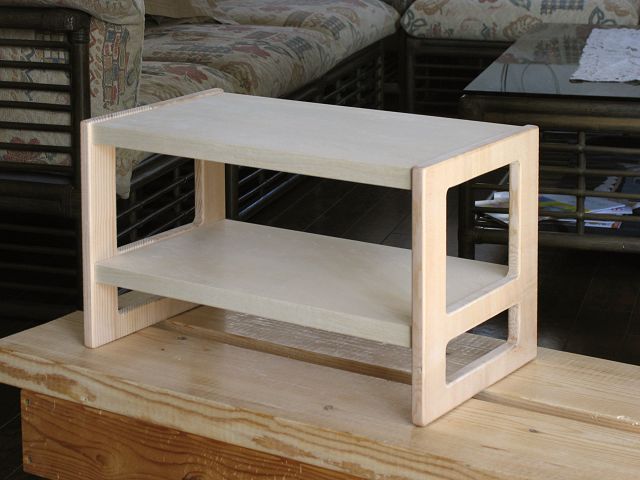 |
|
|
木ダボだけで結合された状態です。 ネジは全く使いませんから見た目は大変すっきりしており、木口テープで切断面を覆っているので合板を使っていることも判らず、ムク材だけで作ったように見えます。
|
|
|
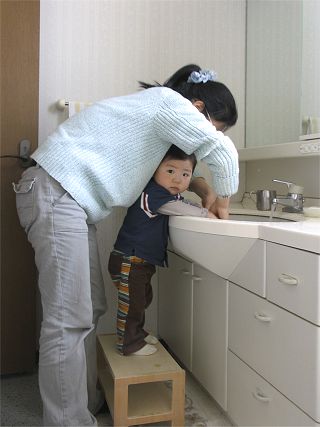 |
|

この脚立を使う優真君が我が家に来ましたのでテストしました。 まだ接着はしていないのですが、優真君程度の体重であればぐらつくこともなく使えます。 無論踏み板の撓みも発生しません。 高さが少し足りませんが、優真君の自宅の洗面台は低いので問題ないとのことです。
また気にしていた重量もご覧の通りなんとか持ち上げられます。 持つ位置を変えればもっと楽に持ち上げて運べるでしょうが、軽量化してなければ持ち上げられなかったように思います。
(因みに最終重量は側板に使ったムク板の比重が計算値より大きく、約1,620gと設計値より90g重くなっています。) |
|
|
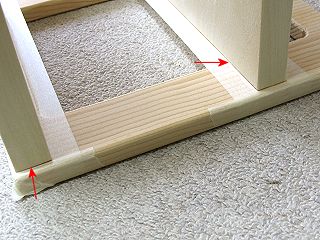 |
|
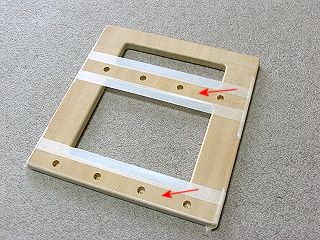 |
|
|
直角に接合した隅に沿ってマスキングテープを貼ります。 これは接着する境目に鉛筆で線を引く代用です。(鉛筆で線を引くと後で消しゴムで消しても線が凹みとして残ります。)
|
|
踏み板を外しました。 矢印の先が踏み板を接着するエリアになります。
|
|
|
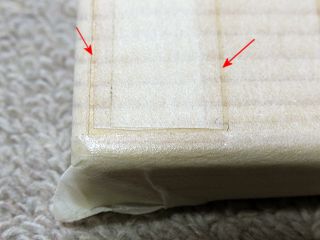 |
|
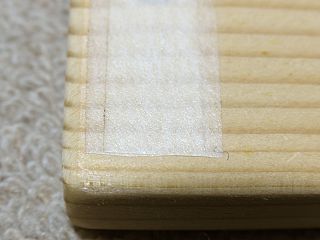 |
|
|
その接着するエリアを新たなマスキングテープで覆いますが、最初に貼ったマスキングテープとの間に0.5mm程度の隙間(矢印の先)が出来るように貼ります。
|
|
そして最初に貼ったマスキングテープを剥がしてしまいますが、こうすることで塗られない部分の境界線はほんの少し内側になり接着すると完全に隠れてしまいます。
|
|
|
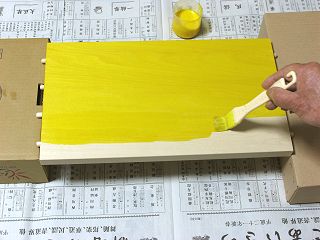 |
|
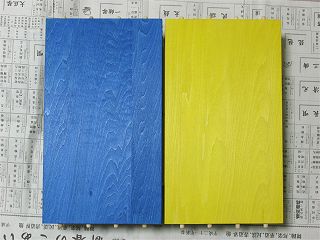 |
|
|
踏み板の着色にはポアステインを使いました。 豊富な色から今回は黄色と青色でカラフルに仕上ますが、私が標準としている水で2倍に薄めて刷毛塗りとしています。
|
|
着色が終わったところですが面白いことに色によって着色濃度が異なり黄色は1回で済んでいますが青色は4回塗っています。 乾燥したら#400ペーパーで軽く研摩します。
|
|
|
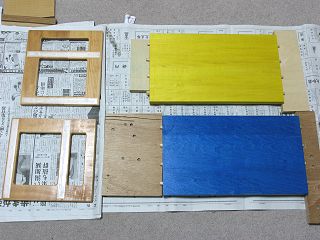 |
|
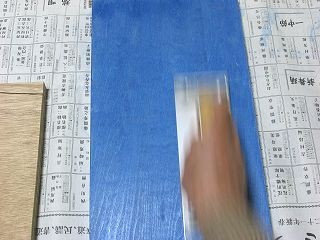 |
|
|
そして油性ニス透明クリヤーの塗装ですが、これもペイント薄め液で若干希釈しています。 左の側板は1度に片面しか塗装できませんから4回塗りの工程数としては8回になります。 右の踏み板は一度に両面の塗装が可能ですので半分の4工程で4回塗りが終了します。
|
|
重ね塗りの前には必ず#400サンドペーパーによる研摩が不可欠でこれにより塗装品質が決まります。 大きな平面にはハンドサンダーに#400空研ぎペーパーがベストです。
|
|
|
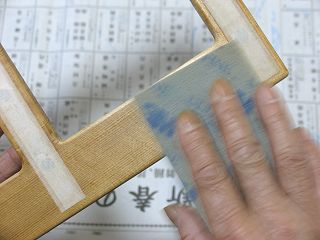 |
|
 |
|
|
小さな面、曲面がある、段差がある、などの場合にはスポンジ研磨剤でないと具合が悪く、ここではウルトラファイン(#800-#1000相当)を使っています。
|
|
最後の4回目はつや消しニスで、しっとりとした感じに仕上がります。 そしてマスキングテープを剥がして塗装作業は終わりです。
|
|
|
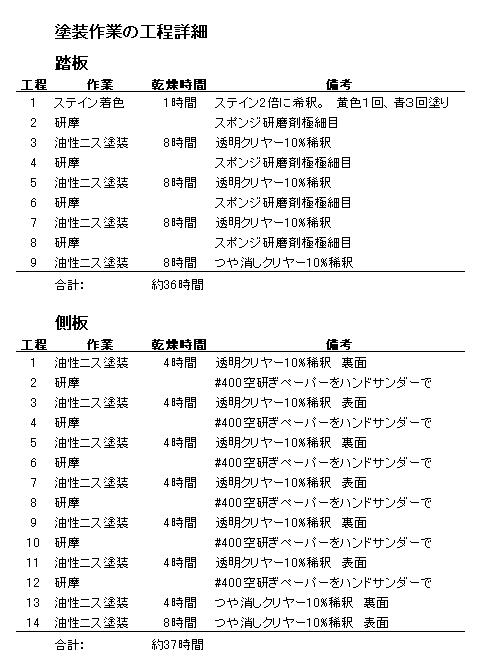 |
|
以上の塗装作業の全工程を一覧にしてみました。
側板と踏板では工程数が異なりますが、これは側板の場合一回の塗装作業で全面塗装は不可能であるため、表面と裏面をそれぞ1工程としていることによります。 但し工程の間隔は最後の塗装を除き乾燥時間の半分の4時間とし作業時間短縮を図っています。 しかし表・裏それぞれ交互に塗装しているため乾燥時間は8時間と変わりありません。
これら乾燥時間はメーカーの推奨値の約2倍としています。 その理由は十分に乾燥させないと乾燥後の研摩作業がうまく研摩できないためです。 またこの際研摩カスがスムーズにはけるよう空研ぎペーパー使用がベストです。
ステインは同じ稀釈度でも色によって着色度合いが変わります。 従って塗り回数は断定的には表現できませんが、1回塗るたびに乾燥時間として1時間以上取ります。
また着色作業が終わったら#400ペーパーで木繊維が立ち上がって粗びてきた表面を慣らしてからニス塗りに入ります。
作業時間を大幅に短縮するには水性ウレタンニスの使用が考えられます。 この場合乾燥時間を8時間から3時間程度に落とせますから、全体では20時間の短縮が可能です。 但し水性ウレタンニスは肉載り性能は油性より低いので、初回の塗装に水性サンディングシーラーを使うことにより、肉載りを稼ぐことが出来ます。
|
|
|
|
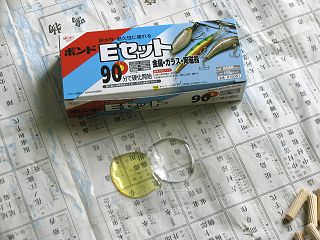 |
|
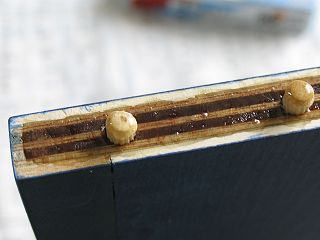 |
|
|
一昼夜寝かせて塗装を完全乾燥した後で、最後の接着組立作業に入ります。 今回は接着強度が高く重点効果もあるエポキシ(90分硬化開始型)を使います。 2つの液を等量搾り出して混合します。
|
|
楊枝で厚み0.5-1.0mm程度に塗り広げます。 また端から2mm前後の部分は塗りません。(圧着時にエポキシがはみ出すのを防止するため。) そして穴の内側にも塗りつけたら木ダボを挿し込みその頭と周囲にエポキシを塗ります。
|
|
|
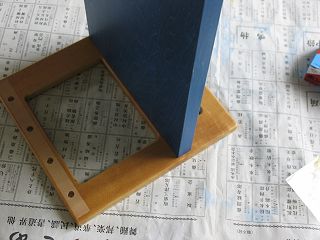 |
|
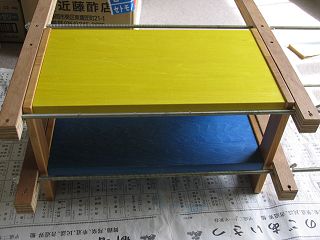 |
|
|
そうしたら側板の所定の穴に挿し込みます。 もう一枚の踏み板も同様にして挿し込み、次に反対側の側板を接着、という手順です。 硬化速度が遅いですから落ち着いてゆっくり作業を進めても大丈夫です。
|
|
そべて接着が終わったら圧着保持をします。 ここでは自作のクランプを使いました。 重しを載せる!程度では圧着保持にはならず接合部分に隙間が出来てしまいます。 これで10時間放置すれば実用強度に達しますが、完全硬化には24時間掛かります。
|
|
|
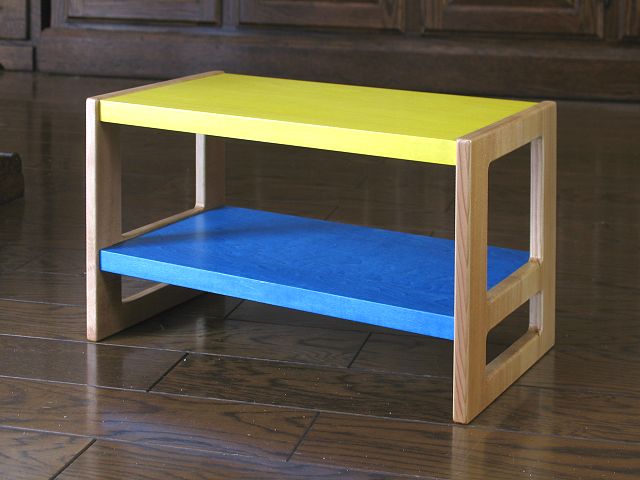 |
|
|
完成した幼児用踏み台。 拘りのある作り方をしたので見掛けよりも遥かに軽く、手がかりがあちこちにあって、幼児でも運びやすい物になりました。 価格が安いプラスチック製で代用できそうですが、木目から来るぬくもり感が全く違います。
|
|
|
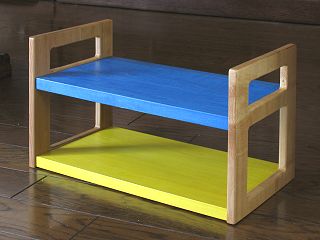 |
|
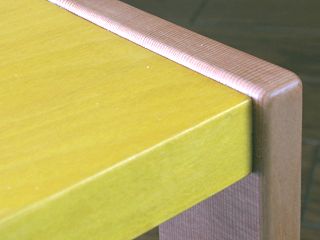 |
|
|
このように逆さに置いて使うことも考えられています。 その場合の高さは16cmになります。
|
|
接合部分は十分な圧着保持をしていますから隙間なく見栄えも良いものになっています。
|
|
|
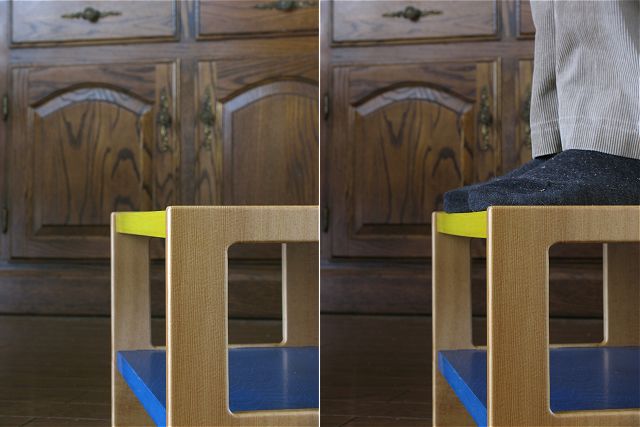 |
|
|
幼児用とは言え大人が乗っても大丈夫。 右は私が上に乗ったところですが、踏み板の撓みはごく僅かで壊れるような心配はなく大変強固です。
|
|
今回のテーマは極めて簡単な構造ですが、丁寧に作れば大変見栄えのする物に仕上られます。 また今回の構造は応用が利き、このまま拡大したり板厚を調整すれば、和室用テーブル、洋室用ティーテーブル、机、飾り棚など様々な物が作れます。 外観的な勘所は木ダボとエポキシ接着剤を使い強度を確保した接合、木口テープの使用で外観の改善にあり、フラッシュ構造や中抜きによる軽量化もテクニックのひとつです。Copyright (C) 2001-2019, Vic Ohashi All rights reserved.