|
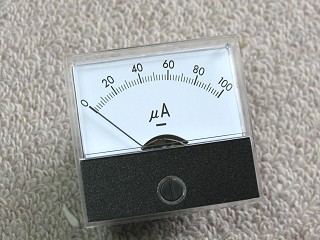 |
|
 |
|
|
目盛り板改造前の100μA電流計。 作業を簡単にするため目盛りはこのまま尊重して使います。
|
|
カバーを外すにはこの部分に細いマイナスドライバーを差込みこじ開けます。
|
|
|
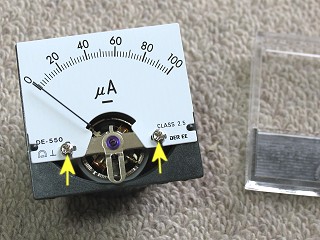 |
|
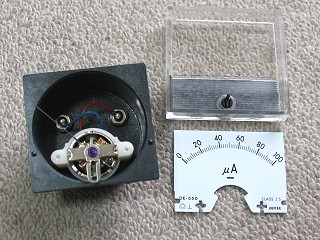 |
|
|
カバーが外れました。 次に2本の目盛り板固定ネジを外して目盛り板を外します。 針を引っ掛けて壊さないよう慎重に。
|
|
分解が終わったメーター。 3つに分かれますが、右下の目盛り板をスキャナーに載せて印刷面をファイル化します。
|
|
|
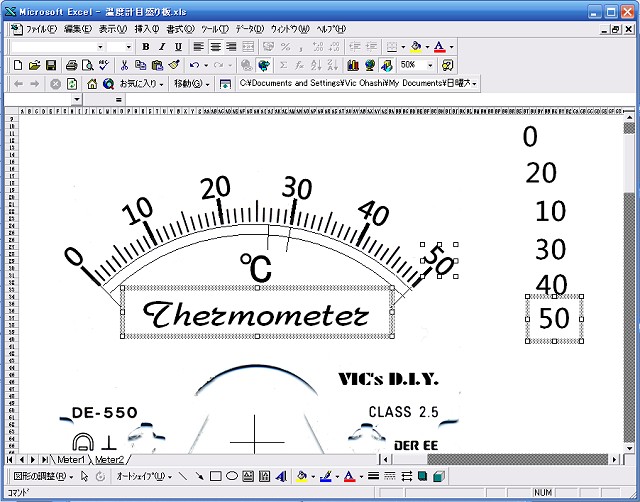 |
|
|
スキャナーでファイル化した目盛りをExcelにて編集中。 これは高機能版の目盛りですが、数字と文字の書き込みをやっています。 数字はExcelで描いた後にPaint Shop Proにて所定の傾きに回転し再びExcelに移動して貼り付けました。 また目盛りの下に色分け帯の境界線を描いてありますが、Paint Shop Proでそれらの中を3色で塗りつぶしています。
|
|
|
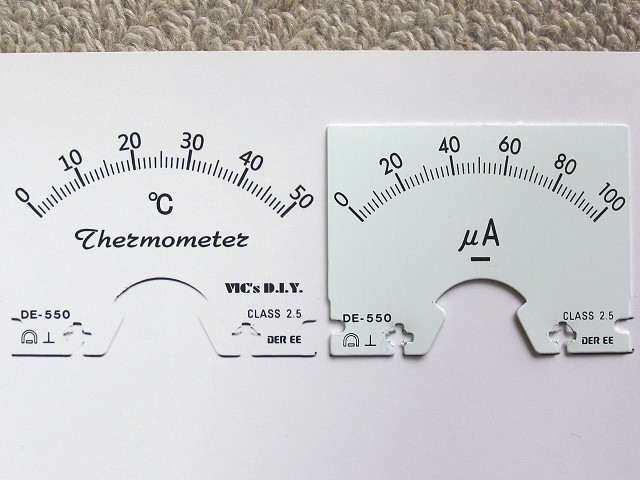 |
|
|
こちらはシンプル版の目盛りで印刷が終わった隣に元々の目盛り板を並べました。 目盛りの幅が若干広くなっていますが、これはあえてそうなるよう調整しています。
|
|
|
 |
|
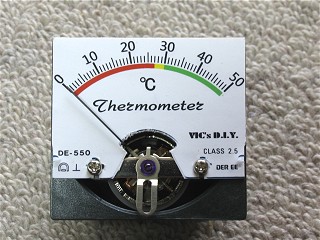 |
|
|
元の目盛り板に両面接着テープを貼り付けます。 ほぼ全面を覆うようにしていますが、下側の一部だけ剥がしておりここから位置を確認しながら貼り付け、その後上のほうの裏紙を剥がし貼り付けてゆきます。
|
|
はみ出た紙を切断してメーター本体にネジ止めしました。 0点がずれている場合にはカバーを被せて固定した後に0点調整します。
|
|
|
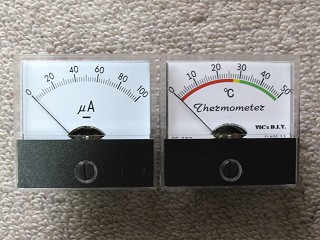 |
|
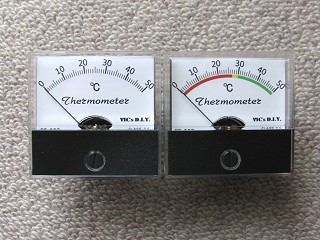 |
|
|
改造前(左)と改造後(右)のツーショット。 うまく化けました。
|
|
改造後の2種類のメーター。 何れもThermometerと温度計であることの表示と、単位が「℃」である事を表しています。 違いは電池電圧表示の3色の帯があるかどうかだけです。
|
|
|
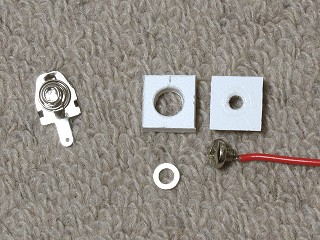 |
|
 |
|
|
電池受けの部分を作る部材。 白くて四角いのは発泡塩ビ板で、当初は3mm厚アガチス板で同じ物を作ろうとしましたが組み立て時にばらばらに割れてしまい割り直した経緯があります。 ネジは3mmの長さで先端にワイヤーを半田付けします。 中央下は0.5mm厚のワッシャーで、左は既製のマイナス側用の電極です。
|
|
2枚の塩ビ板を瞬間接着剤で貼り合わせました。 ネジはワイヤーを先に通した上でこのように嵌め込みます。 ネジの頭は約0.5mm表面より沈みます。
|
|
|
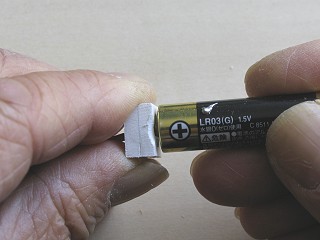 |
|
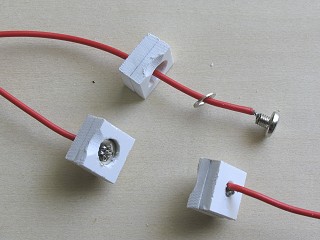 |
|
|
電池の+側の突起を当ててみました。 ごらんのように電池ボディー周辺は塩ビ板から0.5mm浮き上がっており、+の突起はネジに接触しています。 電池を反対にしてマイナス側を当ててもネジの頭には絶対に接触できません。 完璧な電池逆挿入によるトラブル防止になります。
|
|
貼りあわせた塩ビ板の周辺を研磨し11 x 11mmのドンピシャサイズに仕上げ、ケース側板に貼り付ける準備です。 最終的にはご覧のようにワッシャーを1枚入れてネジの沈み具合を調整します。 そして瞬間接着剤を裏側から少し注入して固定します。
|
|
|
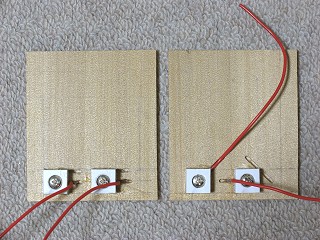 |
|
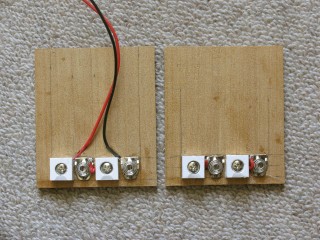 |
|
|
左がB側板で右がA側板です。 +電極ブロックをエポキシ接着剤で貼り付けました。 はっきりとは見えませんが、ワイヤーが出てくる部分には幅・深さ1.5mmの溝を彫ってワイヤを埋め込んであります
|
|
この写真では左がA側板、右がB側板になっていますが、12時間後にマイナス電極にワイーヤーを半田付けした上でやはりエポキシ接着剤で貼り付けています。
|
|
|
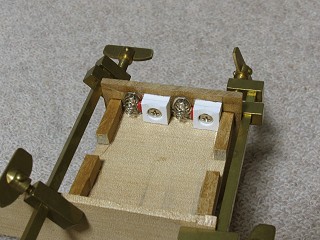 |
|
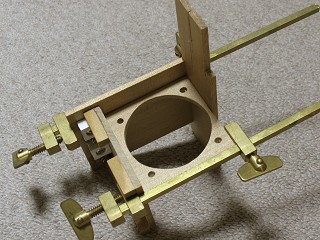 |
|
|
4個の電池蓋固定ブロックを貼り付けた電池室上板にB側板を貼り付けています。
|
|
そして前面パネルを固定しました。 接着位置がずれないよう落ち着いて念入りに作業しないとなりません。
|
|
|
 |
|
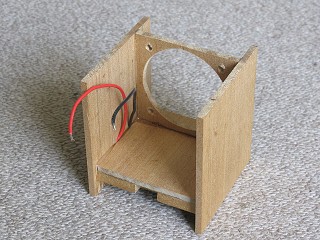 |
|
|
A側板を同様に接着しました。 これは左前方から俯瞰しています。
|
|
右後方から俯瞰した眺めはこんな具合です。 この後天板を貼り付けて前板を挟み込めばケースとしては完成です。
|
|
|
 |
|
|
さて大変苦労した電池ホルダーの部分はこんな具合です。 アルカリ乾電池とエネループが混在していますが、物理的に問題なく装填できるか確認するためで、この状態で使うわけではありません。 既に述べたように損得を無視したような手間は掛かってしまいましたが、市販品ではお目にかかれないコロンブスの卵的な逆接続防止機構は、完璧に動作する拘りのギミックです。
|
|
|
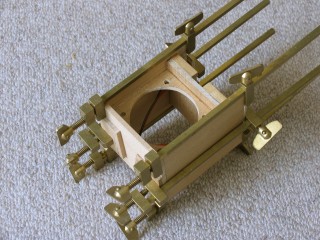 |
|
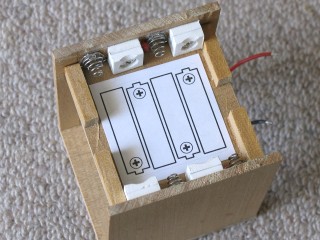 |
|
|
天板を貼り付けました。 ご覧のように180mmのハタ金を6本使い接着位置がずれないよう保持しています。
|
|
挿入する電池の向きを表した図をExcelで描き印刷して貼り付けました。
|
|
|
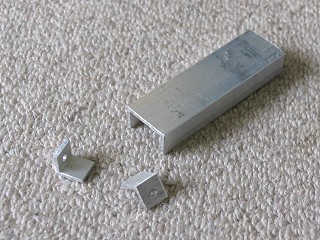 |
|
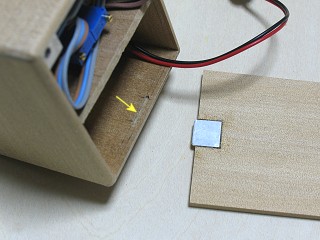 |
|
|
多機能型は背面の板を外して電池交換をするので、アルミ押し出し材を切断して背面固定金具を作り、エポキシ接着剤で背面上部に固定します。
|
|
その背面下部には1mm厚アルミ板を貼り付けて本体内部に加工した溝(矢印)に引っ掛けます。
|
|
|
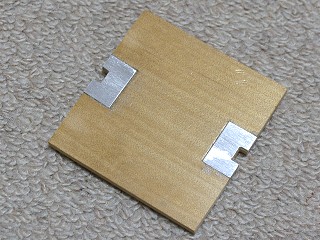 |
|
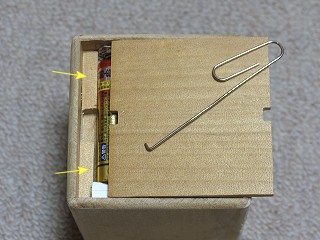 |
|
|
こちらは簡易型の底板で2箇所の切り欠きの周りを保護するため(割れやすい)、凹型に加工した1mm厚アルミ板をエポキシ接着剤で貼っています。
|
|
その底板はこのように収まります。 塗装が終了後矢印の部分にマジックテープを貼り付けて底板をロックします。 底板を外す時には写真に見えるクリップを加工したものを差込み引っ掛けて引っ張ります。
|
|
|
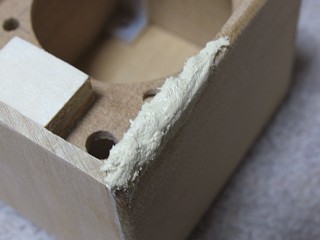 |
|
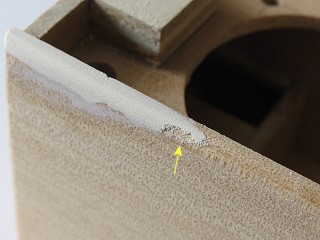 |
|
|
電動トリマー加工ミスで発生した削り過ぎ部分の修復です。 第一工程はこの写真のようにウッドエポキシを修正部分に埋め込み盛り上げます。
|
|
10時間後にカッターナイフで大雑把に削り、24時間後に替刃式ヤスリで削って最終寸法+0.4mm位まで削り#240ペーパーでドンピシャ寸法にします。 矢印先のような段差がある場合には水性パテを擦り込んでやります。
|
|
|
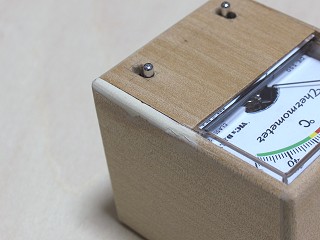 |
|
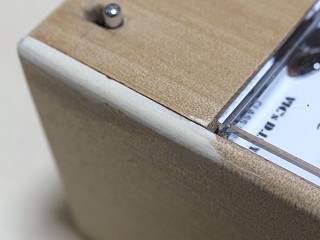 |
|
|
水性パテが乾燥したら#400ペーパーで研摩して表面を均します。 これで削り過ぎの部分の修復は完璧に治りましたがペイント仕上げならではです。
|
|
この上の写真にあった段差は完全に無くなりました。 塗装するとまったく判らなくなります。
|
|
|
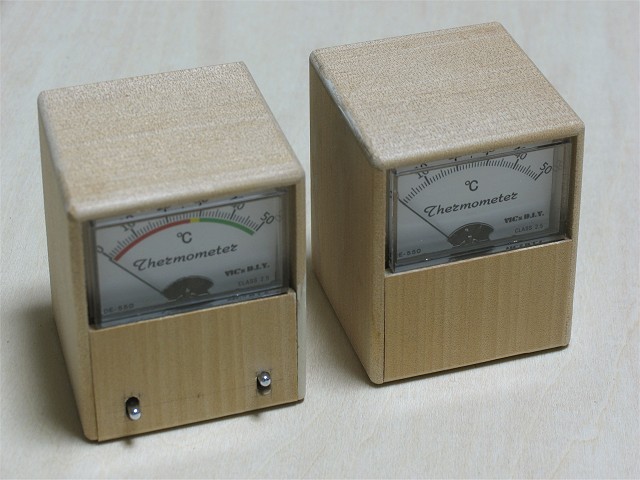 |
|
|
#400ペーパーによる仕上研摩が終了した簡易型(右側)と多機能型(左側)のケースです。 仮にメーターとスイッチを挿入してみました。
|
|
|
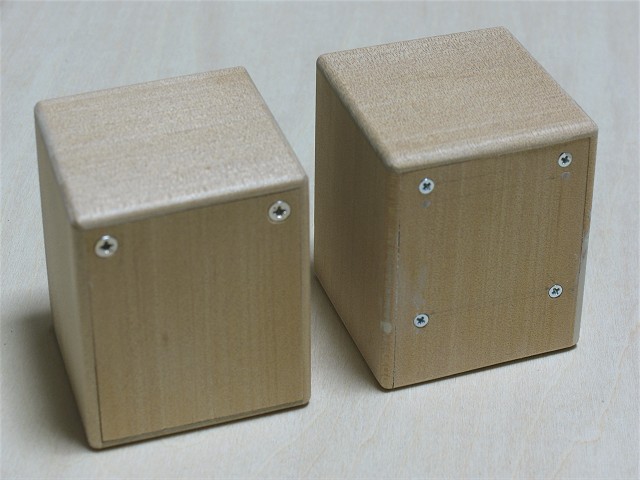 |
|
|
それらの背面はこちらです。 左の多機能型は背面板を外して電池交換するので、M3のネジ止めとし多回数のネジ締めに耐えられるようにしました。 右の簡易型では修理や調整以外では開ける必要がないので木ネジ4本止めです。
|
|
|
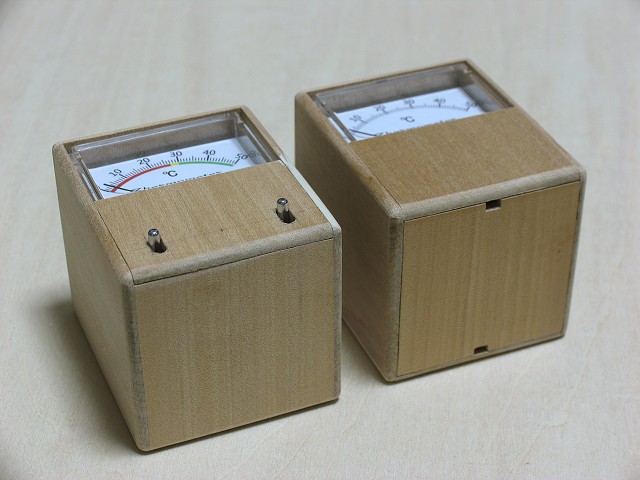 |
|
|
底面の違いです。 左の多機能型では底面は接着固定してありますが、右ではマジックテープで固定し電池交換の時には黒く見える切り欠きに針金を引っ掛けて外します。
|
|
|
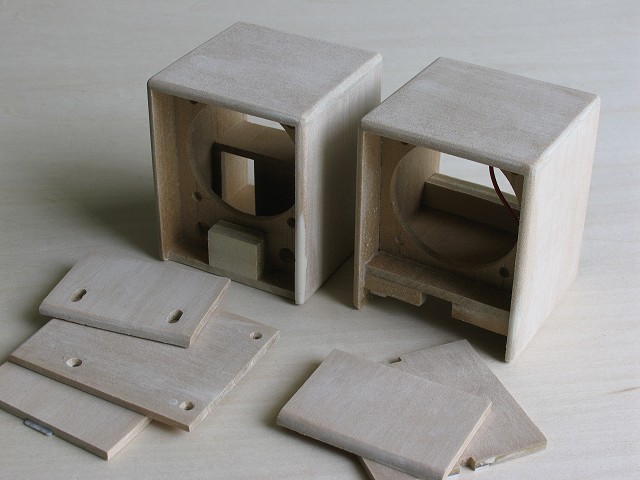 |
|
|
全部材の塗装面に水性パテを擦り込んで乾燥後#400ペーパーを掛けました。 これで木繊維の断面の穴は塞がり目止めがばっちり出来ました。
|
|
|
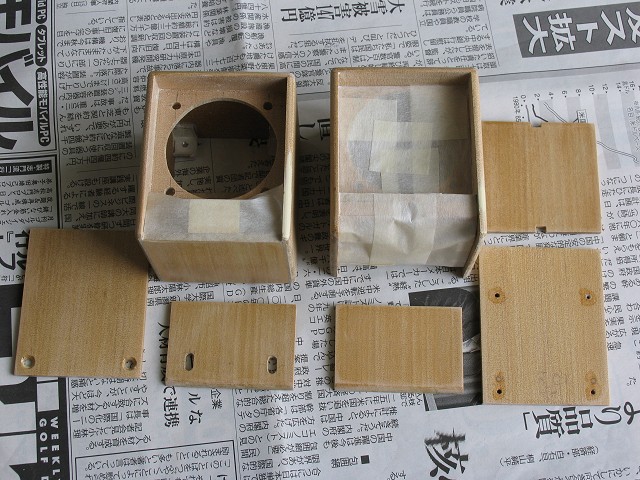 |
|
|
塗装の最初は水性ウレタンニス透明クリヤー2回塗りで乾燥後に#400空研ぎペーパーで研摩します。 その結果表面はつるつるになります。
|
|
|
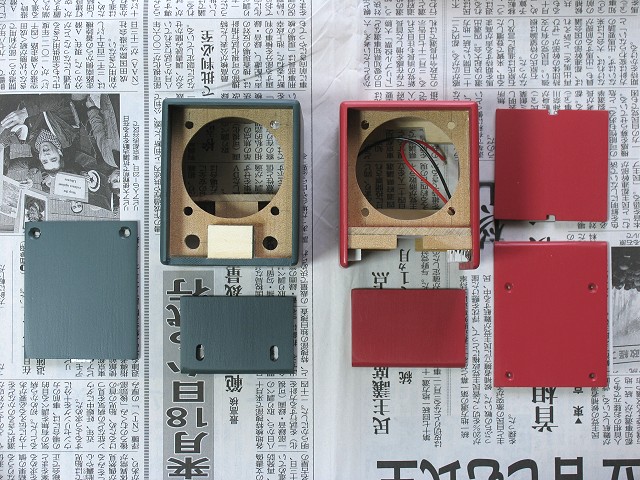 |
|
|
そしてアクリルラッカースプレーを2回塗りました。 水性ウレタンニスで下地が出来ているので塗料の吸い込みもなく大変滑らかな表面です。
|
|
|
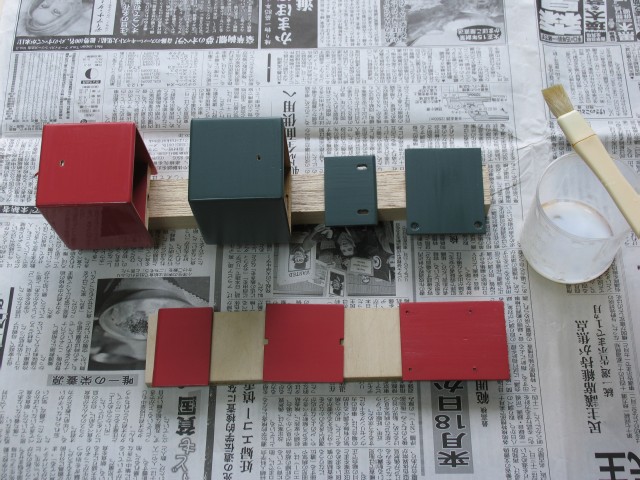 |
|
|
この次に述べる温度センサー取り付け穴をあけてから、水性ウレタンニス艶消しクリヤーを2回塗りました。 これで物理的に弱いラッカーの塗膜は丈夫なウレタンニスの塗膜で覆われました。 小さな作品ですから刷毛には13mmのラック刷毛を使っています。
|
|
|
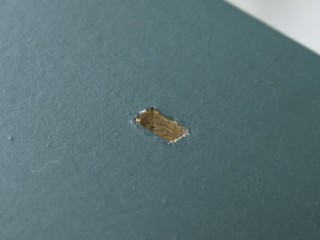 |
|
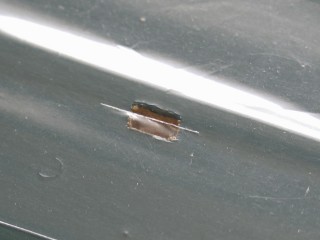 |
|
|
温度センサーの固定方法の説明で、一番目は穴あけですが艶消しウレタンニス塗り前にやりました。 大きさは、1.5 x 3.5mmです。
|
|
その上にポリエチレンシートを被せますが、空けた穴の位置には切り込みが来るようにしてあります。
|
|
|
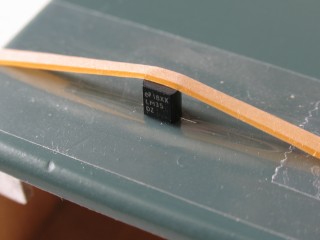 |
|
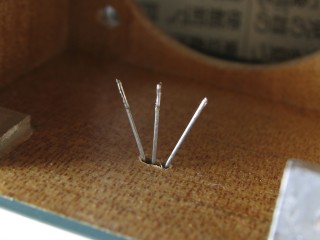 |
|
|
切込みに温度センサーの脚を通してご覧のように輪ゴムで温度センサーを固定します。
|
|
それをひっくり返して内部を見るとこんな具合です。 両側の脚は開いておいた方が、後ほどの配線が楽でしょう。
|
|
|
 |
|
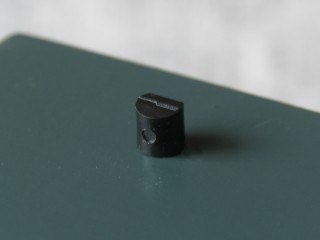 |
|
|
内部のその穴に30分硬化開始型エポキシ接着剤を流し込みました。 大目に垂らしたのでかなり盛り上がっています。
|
|
温度センサーの脚の配線は5時間以上経過してからの方が安全ですが、この写真は温度センサーと天板の間に挟まれたポリエチレンシートを引き抜いた後です。
|
|
|
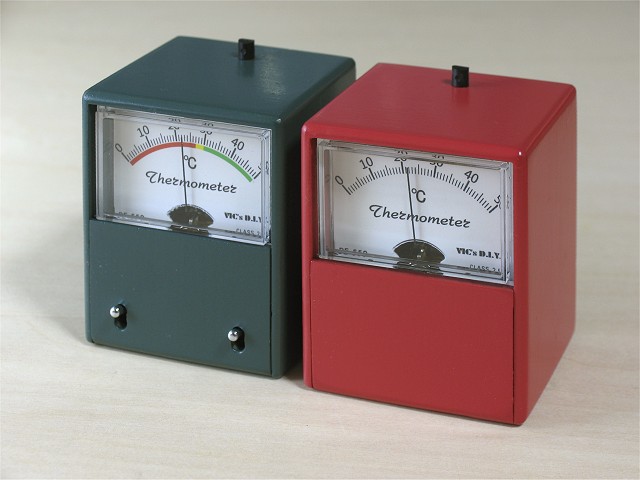 |
|
|
全部材を取り付け配線を済ませました。 前板は後で修理や分解が可能なように両面接着テープで軽く固定しています。
|
|
|
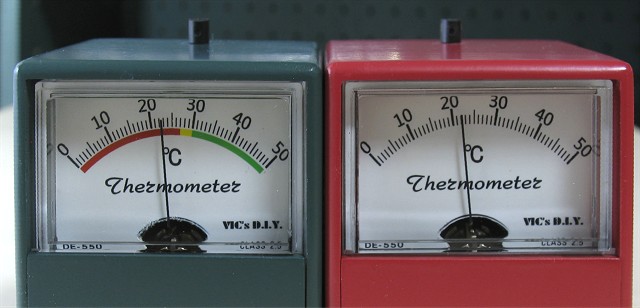 |
|
|
2つの温度計の表示差異をチェックしました。 1目盛りが1℃ですが左の多機能型は0.3℃程高めに表示しています。 無論これだけでは絶対的な誤差がどれだけあるのか判りませんが、選別せずに使ったICですので、小さな差異にいささかびっくりしました。
|
|
|
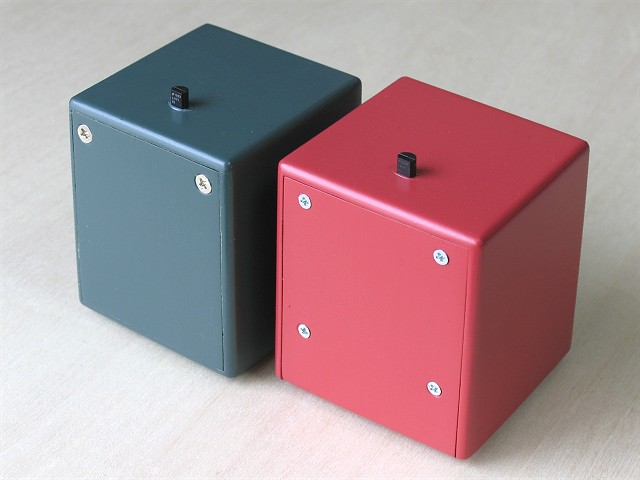 |
|
|
背面の様子。 左の多機能型では電池交換の際に背面の板を外すので、M3のネジ2本で固定しました。 簡易型では調整・修理以外は外しませんので小さな木ネジ4本止めです。
|
|
|
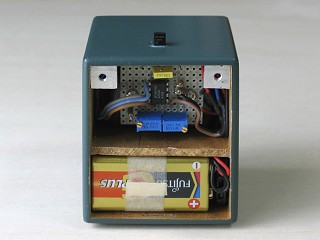 |
|
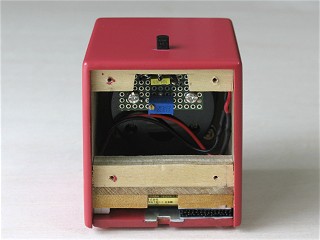 |
|
|
電池は006Pを使用。 このように収まります。 温度センサー出力電圧の10倍がメーター(フルスケール 5V)の読みになるよう左のポテンショメータを調整、その後電池電圧チェックモードでDMMで読んだ電池電圧とメーター(フルスケール 10V)の読みを右のポテンショメータで一致させます。
|
|
簡易型では温度センサーの出力電圧とメーター(フルスケール 0.5V)の読みが一致するよう調整するだけです。
|
|
|
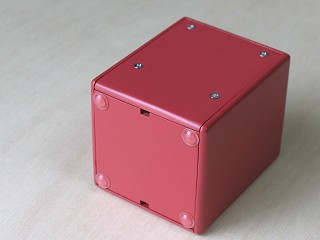 |
|
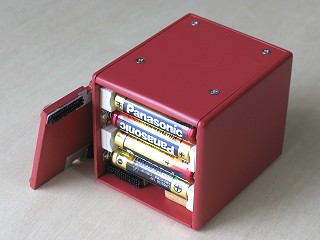 |
|
|
簡易型の底。 底板を外すには、小さな四角の穴にピンを挿し込んで引っ掛けて引っ張ります。
|
|
底板は2枚の小さなマジックテープで固定されています。 電池は単四が4本。
|
|
Copyright (C) 2001-2019, Vic Ohashi All rights reserved.