|
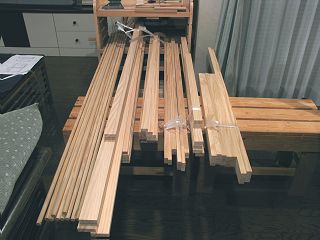 |
|
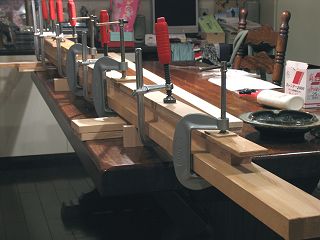 |
|
|
所定の幅に切り出してもらった集成材、そのまま使う18mm厚の物17本、15φ丸棒10本、貼りあわせて10本となる14mm厚の板材が20枚あり、ブロックごとに縛っています。
|
|
30mm厚タモの集成材(長さ3600mm)を台にして貼りあわせた板をクランプで圧着。 2組を合計10本のクランプで固定しておりこれが1回分で12時間放置、同じことを5回繰り返さないとなりません。 (2日掛かりの作業でした。)
|
|
|
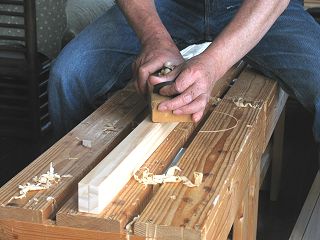 |
|
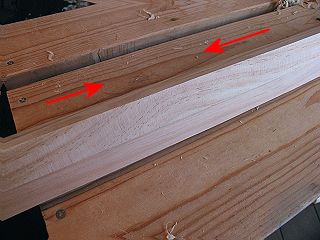 |
|
|
12時間以上圧着保持してはみ出た木工ボンドが完全に固まったらカンナで合わせ目の段差とはみ出た木工ボンドを完全に削り取るのですが?
|
|
木目がうねっていると(ここでは山状に盛り上がっている!)カンナはその部位により矢印の方向に掛けないと逆目になりささくれができてしまいますが、裏の板の木目方向と合わないといずれにしても逆目のささくれが出来てしまいます。
|
|
|
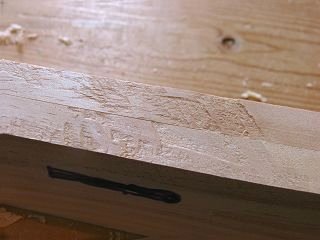 |
|
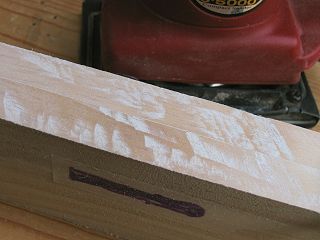 |
|
|
カンナの切れ味がいまいちだったのと逆目のお陰で作ってしまった深いささくれ。 これは最悪の例ですがこれでも修正可能です。 (下に見える横の黒い帯は位置を知るために貼ったテープです。)
|
|
左の写真と同じ位置ですが#120で1分ほど研磨した状態。 かなり深いささくれは#120では短時間には落とせません。 そこで#60ペーパーで研磨すると?
|
|
|
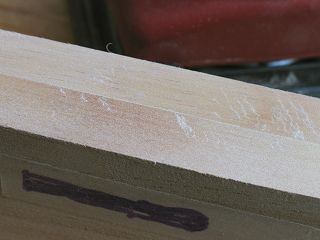 |
|
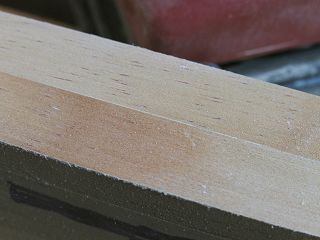 |
|
|
約2分後にはこの程度まで深い傷が削り落とせました。 更に数分#60で研磨を続けた後に#120番で1分そして#240に変えて1分の研磨で?
|
|
このように殆ど傷は見えなくなりました。 #60 → #120 → #240と面倒がらずにペーパーを変更するのが最も効率よく短時間で修正できます。 全部の場所がこのようでしたらとんでもない時間を修正に必要となりますが、私の場合1本の棒の2面の研磨で平均して45分掛かっています。
|
|
|
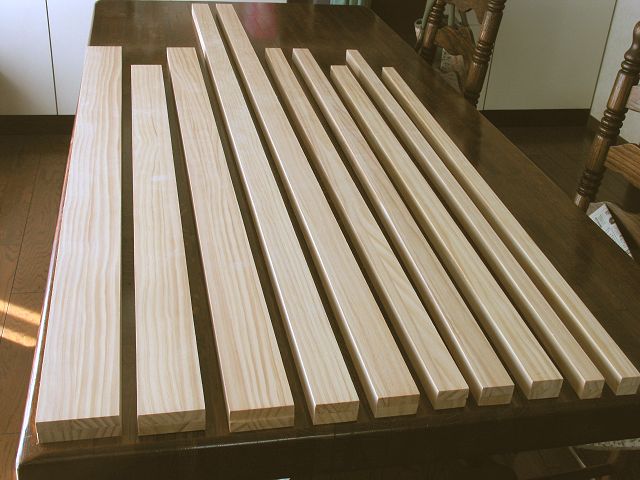 |
|
|
貼り合わせから成形研磨までフルに3日間を費やして出来上がった10本の板材。 このテーマで最も手間の掛かる部分であることは間違いありませんが、無事終了しほっと一息です。
|
|
|
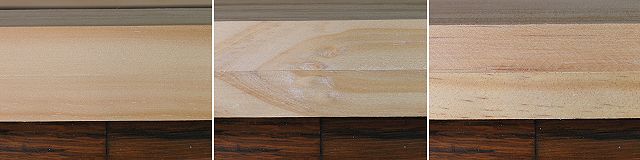 |
|
|
厚さ18mmの貼りあわせ面のクローズアップ。 左は最も綺麗に仕上がった部分で全てがこうは行きません。 真中は最も見苦しくなったかな?という貼りあわせ面で、右は最も多い傾向のものです。 いずれにしても大過ないでしょう。
|
|
|
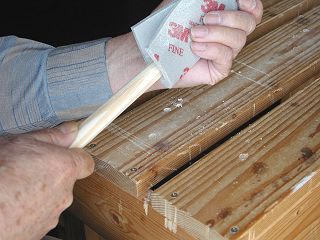 |
|
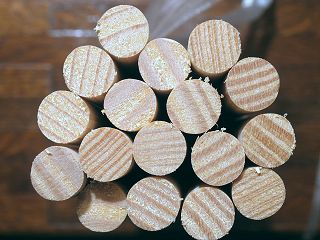 |
|
|
丸棒の研磨にはスポンジ研磨剤(細目 #240-#320の粒度)を使いました。 棒を研磨剤で包むように握って研磨するので曲面には作業性が良く絶好です。
|
|
切断した丸棒の直径をノギスで測った所公称15mmに対し、14.9mm-15.8mmと太め側にばらつき、ご覧のように肉眼でも若干いびつな物があることが判ります。
|
|
|
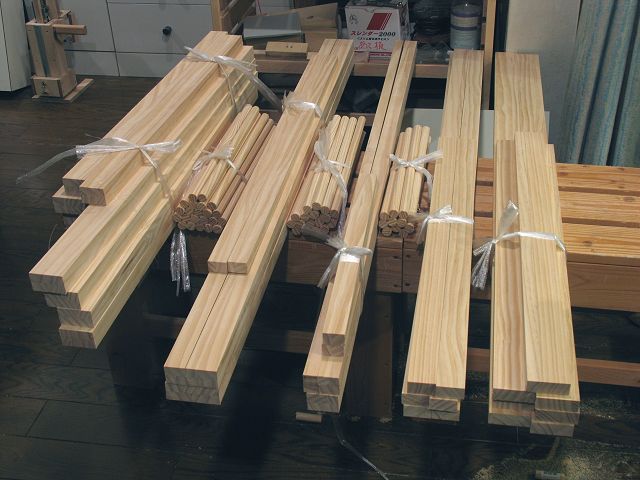 |
|
|
兎にも角にも全部材は最終の長さに切断し終わり、ブロック毎(左から左右の側板ブロック、後の側板ブロック、スライドする柵ブロック、ベッド床ブロック、底板ブロック)に紐でくくりました。 全部で6ブロックで構成されることになります。
|
|
|
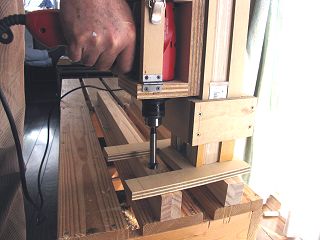 |
|
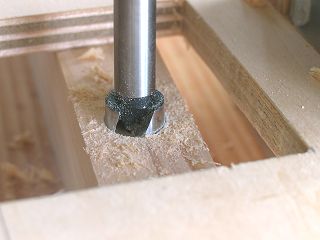 |
|
|
15φの丸棒を挿しこむ穴をフォスナービットで穴あけ開始。 自作電動ドリルアタッチメントが最も活躍する場面です。
|
|
15φフォスナービットの先端。 非力なFDD-1000ですが回転数が540回転/分と遅いことがフォスナービットのためにも良く、安全に楽々と穴あけ可能です。
|
|
|
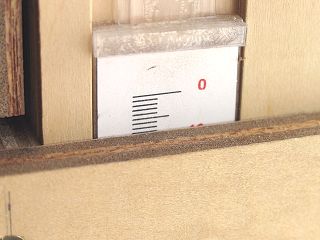 |
|
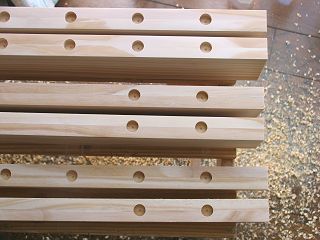 |
|
|
穴の深さは8mm一定にしますが電動ドリルアタッチメントではそれをプリセット出来るので、作業性の良さと加工精度は抜群です。
|
|
穴あけは楽ですが後で丸棒の直径の調整研磨の面倒さが気になります。
|
|
|
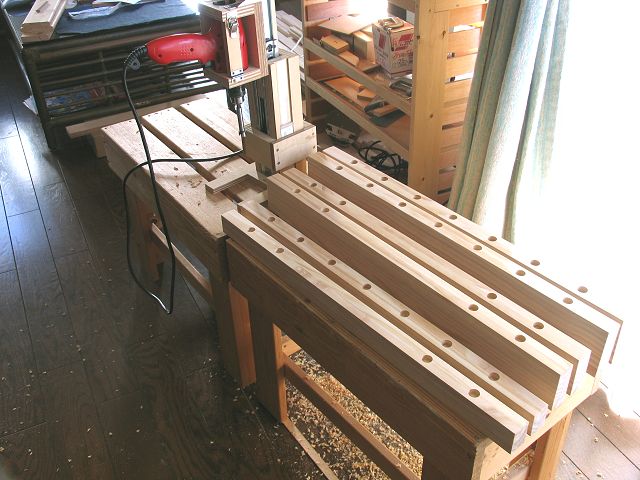 |
|
|
全部で穴あけは100個所ありますのでまだまだ続きます。 今週は左右の側板ブロックの穴あけ(合計44個所)だけ終了しました。
|
|
|
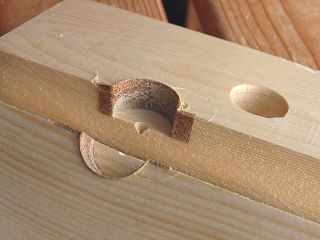 |
|
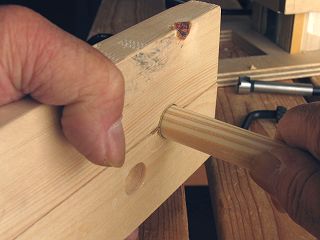 |
|
|
ワンバイフォー材に16φのフォスナービットで深さ8mmの座繰り穴をあけその中心をノコギリで切断し裏側に蝶番を取り付けて連結、穴の側壁に#120サンドペーパーを木工ボンドで貼り付けました。
|
|
棒の先端を挟んで左手はこのジグを握り、右手で棒を捻ることで研磨します。 2分ほど続けるとジグを握り締めても緩くなってきてこの辺りが頃合です。
|
|
|
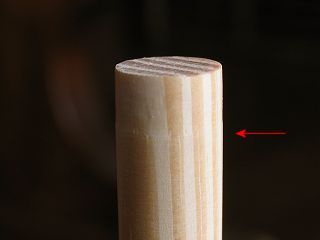 |
|
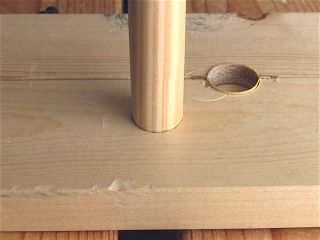 |
|
|
その先端のクローズアップ。 矢印の先より上が削り落とした部分で、良く見ると境目の段差が判るでしょう。
|
|
ジグの横の穴は15φであけてありますので、削り具合を確認できます。 きつからず、緩からずに挿し込めます。
|
|
|
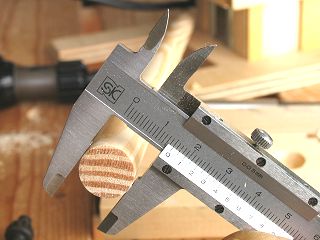 |
|
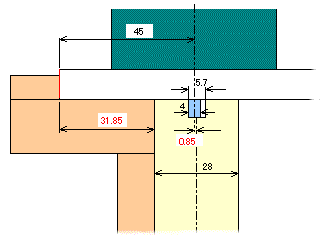 |
|
|
因みにノギスで測ってみるとドンピシャ!15mmになっていますが、さらに0.1mm程削っています。
|
|
4mmのストレートビットを0.85mmオフセットし両面にジグを当てて切削し、幅5.7mmの溝を彫るジグ。 31.85mmはいきなり正確に設定できないので0.5mm程長めにガイドを固定し電動トリマーの縁(赤線部分)に薄いプラスチックを貼ってテスト切削して調整しています。
|
|
|
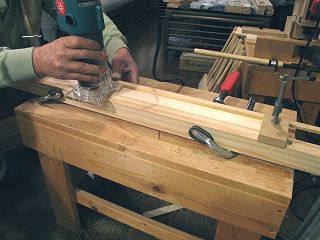 |
|
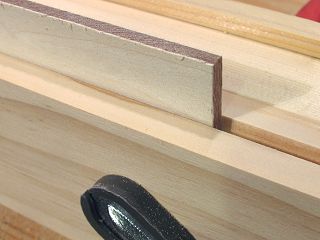 |
|
|
調整後切削開始。 これが済んだら板の反対側にジグを取り付けてもう一度切削すれば5.7mm幅の溝になります。 かなり慎重な作業を要します。
|
|
2回切削後確認のため5.5mm合板の端材を挿入しました。 緩からずきつからずになればOKです。
|
|
|
 |
|
|
こうして彫り終わった溝の端は必ず丸みを帯びています。 そこで3mmのノミで削り落として寸法どおりの四角になるよう調整します。 右端は無事終了し5.5mmの合板がぴったりと納まったところです。
|
|
|
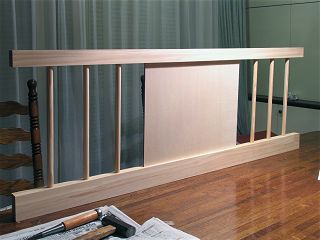 |
|
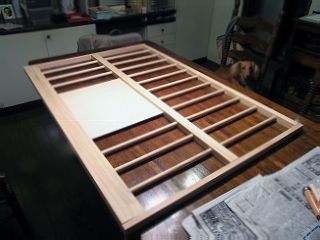 |
|
|
丸穴、各穴の加工に問題がないか確認のため仮組立をしてみました。 これは背面の側板下部です。
|
|
その上に上部の丸棒を追加し上端の横棒を挿し込みテーブルに寝かして左右の棒を添えました。 加工誤差の問題は発生していないようでほっと一安心です。
|
|
|
 |
|
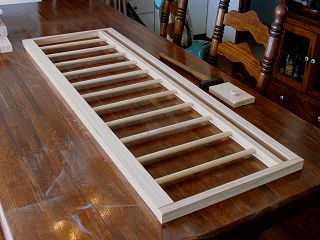 |
|
|
こちらは左右の側板を同様に組み立ててみた所でこちらも問題なし。
|
|
これは手前に付く上下スライド柵ですがこちらもOKでした。
|
|
|
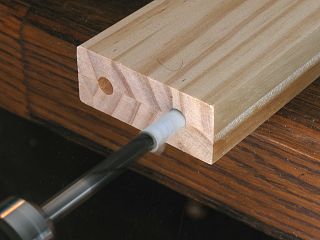 |
|
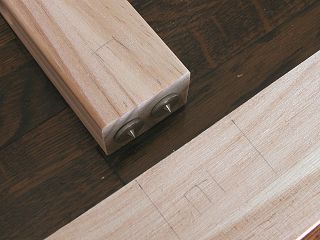 |
|
|
左右の側板枠の組立。 1箇所に8φ木ダボ2本を使いますが最初に木目と平行に穴をあけねばならない部分に8φ深さ16mmの穴をあけます。
|
|
あけた穴にマーキングポンチを挿入し接合する相方をそれに押し付けます。
|
|
|
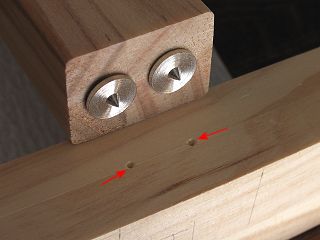 |
|
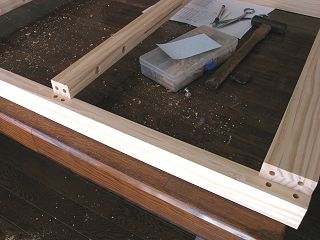 |
|
|
そうするとマーキングポンチの先端による円錐状の窪みが付きますから(矢印の先)その部分に8φ深さ16mmの穴をあけます。
|
|
木ダボ接合の穴があけ終りました。 ここに木ダボを挿し込み木工ボンドを塗って接合します。
|
|
|
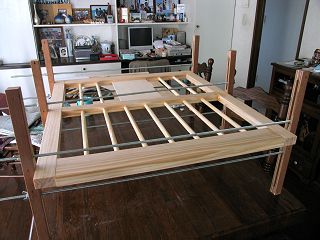 |
|
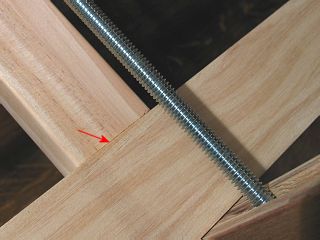 |
|
|
自作中型クランプを3本使い各接合部分の圧着保持をしたところです。 枠の捻れが出ないよう充分調整し、接合部分の直角度も確認した上で4時間寝かせます。
|
|
クランプ充分締め上げていますからご覧のように接合部分に隙間はありません。 接合強度アップの為に大変重要です。
|
|
|
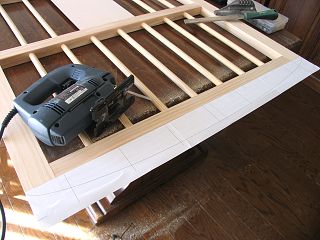 |
|
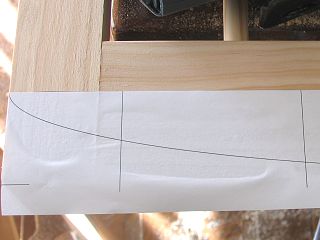 |
|
|
クランプを外した後に上端の曲線切りの為に型紙を作り貼り付けました。 Excelで原寸大の楕円(100 x 762mm)を描いてA4サイズの紙3枚に分けて印刷しています。
|
|
縦線は位置決めの為に入れておいたもので、縦線の間隔は100mmです。(左の縦線と端は62mm)
|
|
|
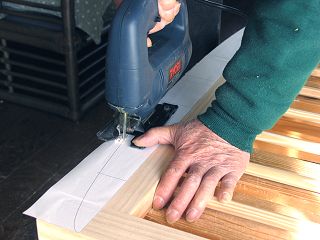 |
|
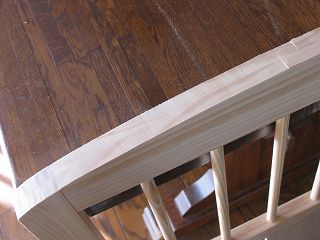 |
|
|
そして電動ジグソーで切断ですが板厚が28mmありますからお馴染みのCJ-250ではちょっと無理で、ここではYJ-50Vに厚板用仕上げ切り替刃(mini-ShopのNo.22)を使いました。
|
|
切断面が傾くことも無く0.5mm程度の誤差で切断できましたが、若干のうねりや段差があります。
|
|
|
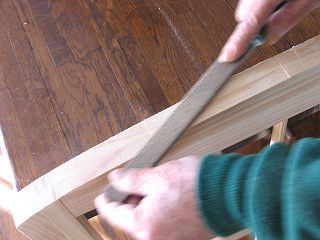 |
|
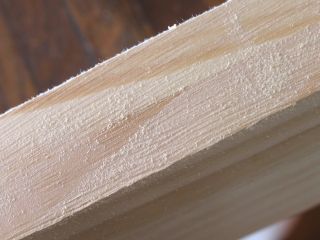 |
|
|
そこで木工粗目ヤスリ(mini-Shopの3本組の平ヤスリ)を使い先ず表面の緩い凸凹や段差を削り落としました。
|
|
荒削りが終わった様子ですが、ご覧のように木目方向に深い研磨痕が残っています。
|
|
|
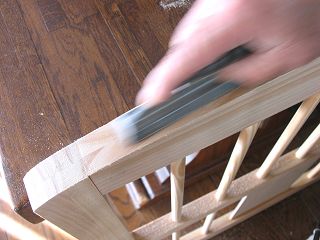 |
|
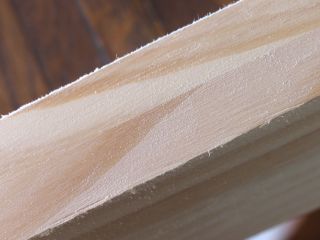 |
|
|
そこで目が大変細かい、強研磨しても問題なし、研磨面はカマボコ状にならない!など替刃式ヤスリ(M20GP)ならではのパワー発揮です。
|
|
1分程度でご覧のようにツルツルに磨きあがりました。 粗目ヤスリは#30-#40程度の目で、M-20GPは#200前後と非常に大きな差がありますが強研磨できるメリットがここにあります。
|
|
|
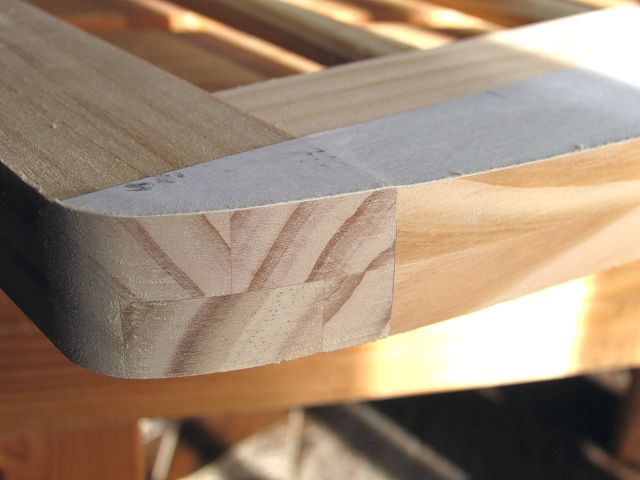 |
|
|
丸め加工が終わった左右側板ブロックの上端角。 この後トリマーで面取りをし#400のペーパーで軽く研磨すれば塗装に入れます。
|
|
|
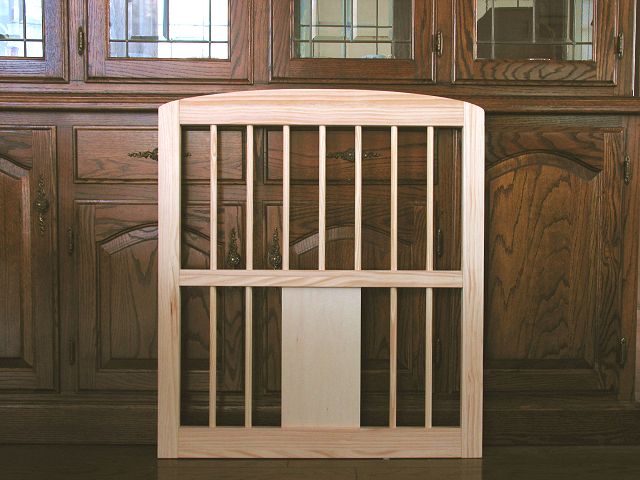 |
|
|
組立と上部の丸め加工が終了した左右側板ブロックの1つ。 背面ブロックと上下スライド柵の組立はもっと簡単に終わるはずです。
|
|
まだまだやらねばならないことは沢山あるのですが、私の気分的な進行状況は既に山を越え第三コーナーに差し掛かったという
|
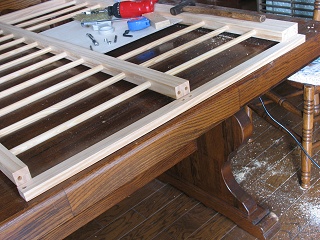 |
|
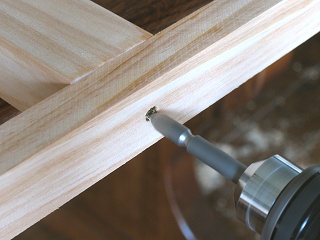 |
|
|
背面ブロックの組立。 木ダボ接合ですが真中と右は木ダボを2本、左端は1本を片側に寄せて打ち込みます。
|
|
接合後真中と右側は中央に3.3φ45mmのネジを1本、左は木ダボの右側に1本打ち込み圧着保持しました。
|
|
|
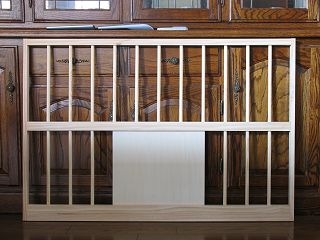 |
|
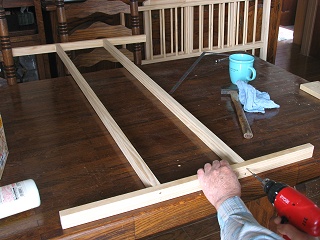 |
|
|
組み上がった背面側板ブロックです。 圧着保持がネジのため作業速度も大変速いですが、直角出しと捻れ発生防止の確認・調整は重要です。
|
|
ベッドの床板の枠を組立、木工ボンドで接合しますが、3.3φ45mmのネジ2本ずつで圧着保持と締結の強化を図ります。
|
|
|
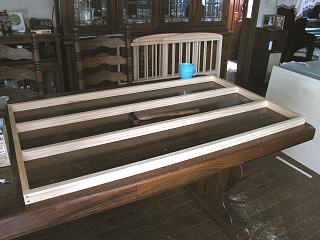 |
|
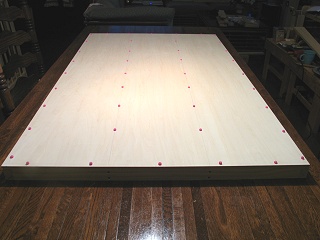 |
|
|
ベッド床板の枠が完成。 組立は簡単ですが切断がいい加減だと直角度が出なかったり捻れたりします。(今更気が付いても遅いのですが?!)
|
|
5.5mm厚シナ合板の床板は木工ボンドで貼り付けますが、22mm隠し釘50本弱で圧着保持しています。
|
|
|
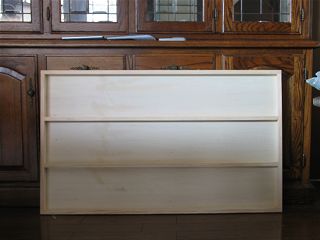 |
|
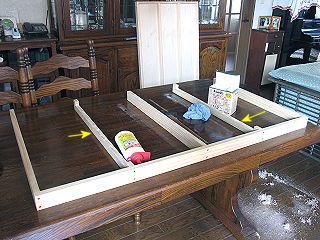 |
|
|
5時間も放置したら隠し釘の頭を落としてベッド床は完成です。 この場合は片面しか薄い合板を貼っていませんが、両面に貼れば軽量の扉などにも応用できます。
|
|
底部の枠の組立です。 矢印の先の棒2本はコの字型にえぐれていますが、寸法図の下のほうとその詳細図を参照ください。
|
|
|
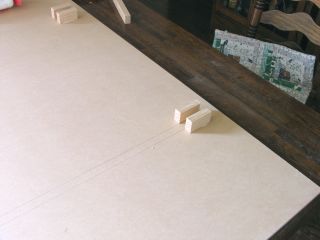 |
|
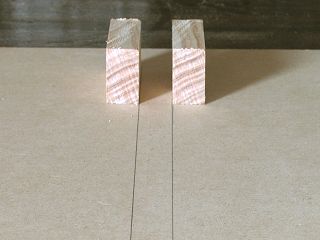 |
|
|
底板跳ね上がり防止のガイドをこのように底板裏側の奥に木工ボンドで貼り付けます。(ボンド硬化後に裏からネジで止めます。)
|
|
2本の線はコの字型にえぐれた枠の棒の位置を表しその両側にガイドは接着されます。
|
|
|
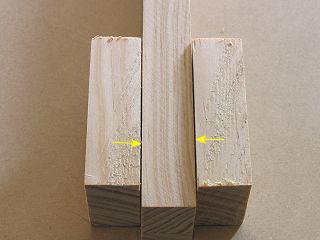 |
|
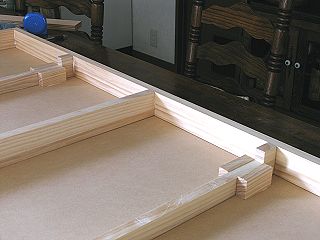 |
|
|
真中の棒はコの字型にえぐれた棒と同じ18mm厚でガイドとの左右の隙間は合計で0.5mm程度にしておきます。
|
|
ガイドを接着した木工ボンドが硬化後に組み上げてあった枠を載せました。 コの字型にえぐれた棒がガイドの間に納まります。
|
|
|
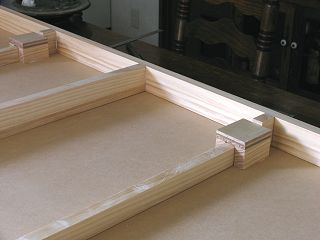 |
|
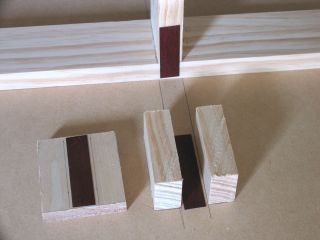 |
|
|
最終的にはガイドをまたぐように押さえの板(12mm厚)がこのように被ります。
|
|
そこまで確認したら一旦枠を外して滑りを良くするためのプラスチック板(敷居滑りなど)をガイド間の底面、押さえ板の裏、そしてコの字型にえぐれた棒の手前上面に貼ります。
|
|
|
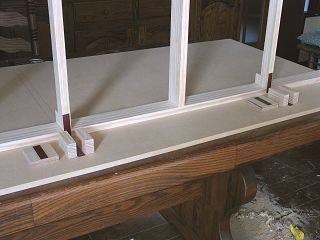 |
|
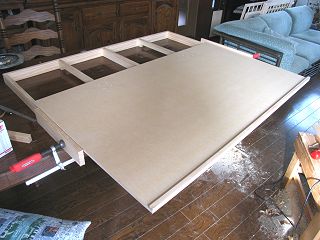 |
|
|
この写真では手前側がベッドの奥のほうになりますが、底板枠をそのまま滑らして再びガイドに嵌め込みガイド押さえ板をネジ止めしてそっとひっくり返します。
|
|
これはベッド手前側からの写真です。 軽い力で前後にスムーズに動きます。 クランプで固定しているのは最終的に取り付けられる側板の替わりです。
|
|
|
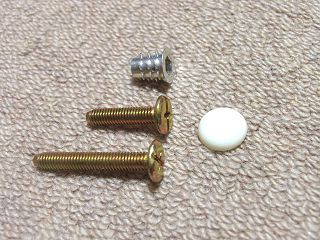 |
|
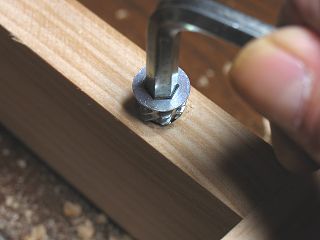 |
|
|
組立てに使う金物。 左上から鬼目ナット M6 13mm Dタイプ(19個使用)、セットキャップボルト M6x26mm(1本使用)、セットキャップボルトM6x40mm(18本使用)、右はセットキャップカバーアイボリー(18個使用)
|
|
M6鬼目ナットは8.5φ深さ15mmの穴をあけて5mmの六角レンチで締めつけます。(後述する底板の跳ね上がり防止部分をお見せしています。)
|
|
|
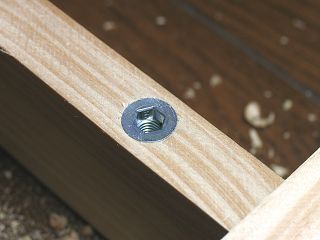 |
|
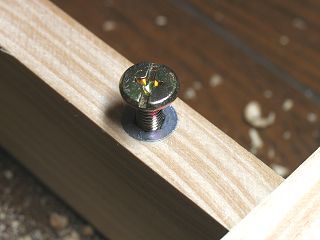 |
|
|
Dタイプの鬼目ナットはフランジが材料表面で止まるようになっていて、締め込み位置が判りやすいのが特徴です。
|
|
やってみると簡単! これだけで丈夫な雌ネジが木材に形成され、何度でも締めたり緩めたりしてもネジバカになることは無くなります。
|
|
|
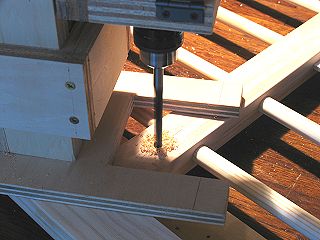 |
|
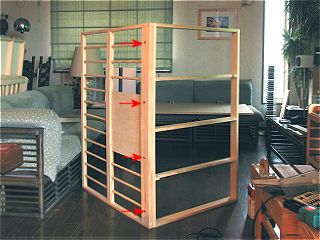 |
|
|
穴あけの垂直度は重要ですので全て電動ドリルアタッチメントを使いました。 また深さ15mmの穴あけもストッパーを使うことにより雑作なくできます。
|
|
最初の組立は底板枠。 40mmセットキャップボルトを4本(矢印の先)使いました。 組立時の重量軽減のために底板は外しています。
|
|
|
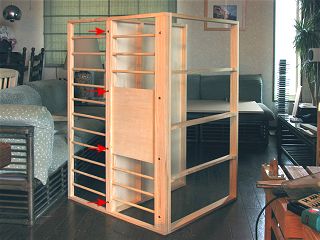 |
|
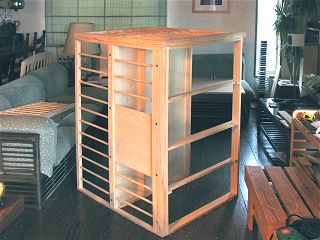 |
|
|
次はベッド床板ブロック。 同じく40mmセットキャップボルトを4本使っています。
|
|
そして左右の側板ですが、ネジ位置は次の写真を参照ください。 片方が終わったらひっくり返してネジ止めします。
|
|
|
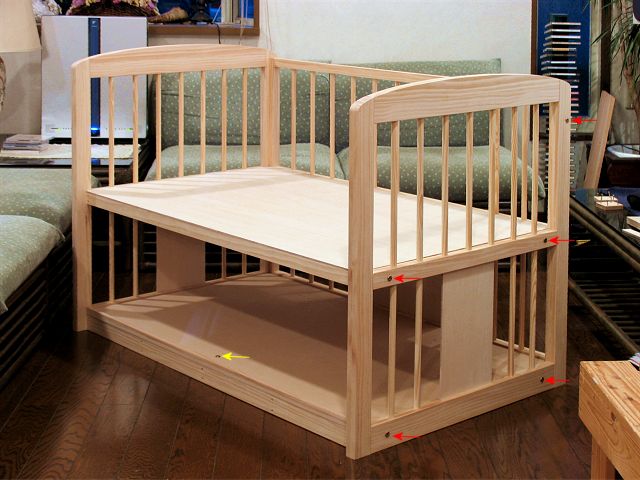 |
|
|
組立が完了したベッド。 赤矢印が側板ブロックのネジ位置です。 尚底板は分解搬入の際にばたつかないよう保管・輸送時には黄色矢印部分に26mmセットキャップボルトネジを差し込んで締めてやるようにしました。
|
|
|
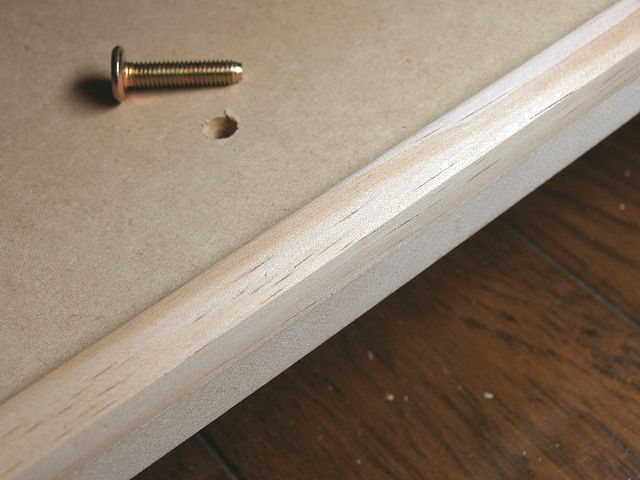 |
|
|
設計図には描いていない追加加工です。 左上は使用しないときに底板が浮き上がらないためのロックネジ(セットキャップボルト 26mm)と捻じ込む穴ですが、板の手前上部に集成材の端材の細い棒を貼り付けて裏から隠し釘で固定しました。 手前下半分はMDFの木口が綺麗ではないので後ほど木口テープを貼ってやります。
|
|
|
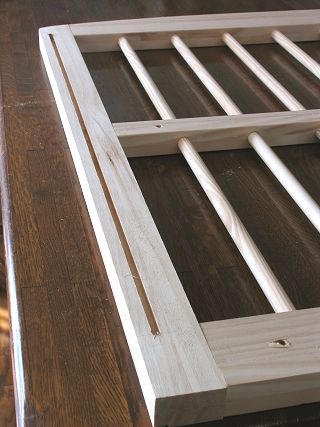 |
|
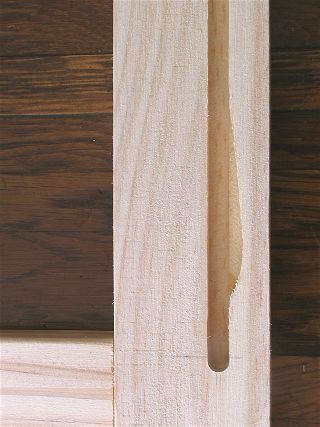 |
|
|
左側の側板ブロック手前内側に彫ったガイド溝。 使ったのは格安なハイストリマービット ストレート1/4インチです。
|
|
同じく右側ですが、下のほうに一瞬の油断で湾曲した余計な彫りこみをしてしまいました。 見栄えをどこまで誤魔化せるかわかりませんが、機能的には完璧な修復をします。
|
|
|
 |
|
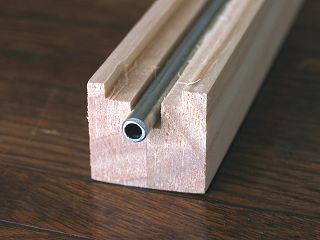 |
|
|
これらの溝には6φのパイプ先端とガイドピンが嵌りこみますが、1/4インチ幅が実に具合の良い溝幅になっています。
|
|
同じく1/4インチ幅の彫りこみをした上下スライド柵の上部の棒。 上側に更にもう一段彫りこみ(幅17mm、深さ4mm)をしていますが、ここにカバーを後で接着します。
|
|
|
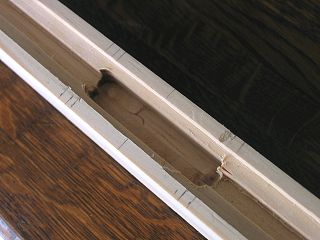 |
|
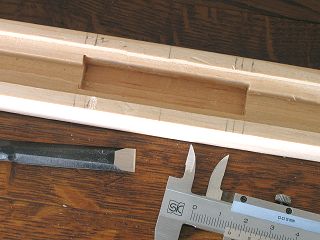 |
|
|
その中央部には更に幅12.5mm、深さ15mm、長さ60mmの彫りこみと少々ややこしい加工していますが、これがカラクリを埋め込む部分になります。
|
|
トリマーでの掘り込みはシャープな長方形にはなりませんので、ノミを使ってノギスで確認しながらドンピシャ寸法になるよう削り込みました。
|
|
|
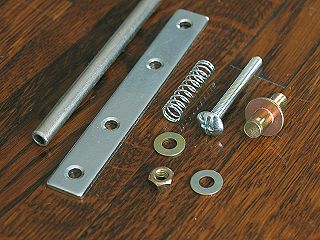 |
|
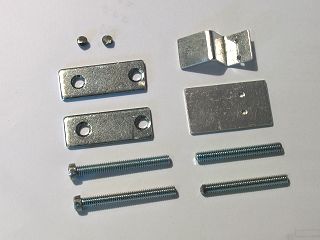 |
|
|
カラクリ機構に使う金物。 特殊な物はなく左から6φ鉄パイプ、2mm厚、幅12mm金折り、押しバネ、M4 35mm トラスボルト、ナット、ワッシャー、6φ鉄製ガイドピン。 写真にはありませんが2mm厚のアルミ板少々。
|
|
ディスクサンダーで切断し金ヤスリで仕上げた左上はスプリング滑り止めのピン(M4ボルトを長さ3mmに切断)、その下は長さ30mmで切断した金折り、その下は頭の直径を6φ以下に落としたM4 35mmトラスボルト、その右が頭を切断したM4 トラスボルト、右上2つは1.5mm厚アルミ板を加工した物。
|
|
|
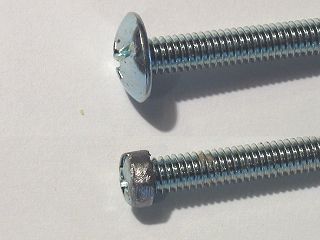 |
|
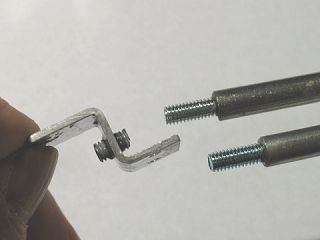 |
|
|
トラスボルトの頭の直径を6φ以下に削った物が下であまり綺麗に削れていませんが、6φを若干下回れば目的を果たせることが後ほど確認できます。
|
|
カラクリ機構の組立開始。 先ず長さ900mmの6φ鉄パイプに頭を切断したM4 ボルトにエポキシ接着剤を塗って差込みボルトの先端が10mm出るようにします。 また3mm長に切断したM4 ボルトをこれまたエポキシ接着剤で加工したアルミ板に貼り付けました。
|
|
|
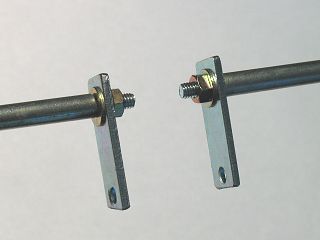 |
|
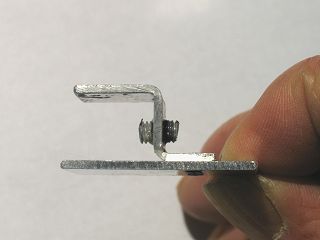 |
|
|
接着剤完全硬化の後にロック解除レバーをこのように取り付けました。 挿入するワッシャーの枚数でスプリングの強さを調節可能です。 尚このままではナットが緩みやすいのでペイントかネジロックで最終的には固定します。
|
|
中央のスプリング支えの蓋をM2皿ネジで固定するとこのようになります。 カラクリ詳細図面の中央部分も参照ください。
|
|
|
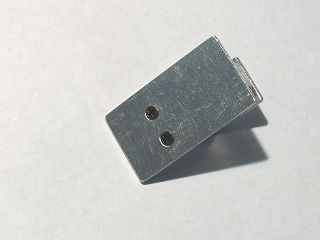 |
|
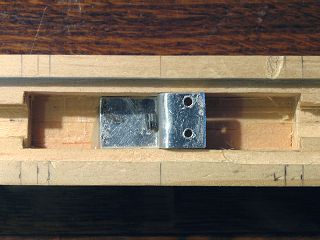 |
|
|
その蓋の面から見たところ。 M2 5mmの皿ネジ2本で固定しています。
|
|
そのスプリング支えを所定の位置に落とし込みエポキシ接着剤で固定しました。 ここでは蓋は外してあります。
|
|
|
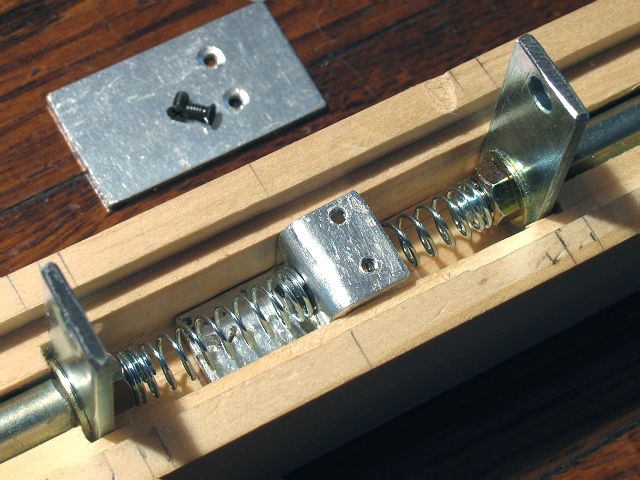 |
|
|
完成したロックピン解除機構です。 解除レバーの最大ストロークはスプリング支えのカバーの長さで決まり左右それぞれ11mmあります。 9mm強のストロークでで解除できるはずなので2mmの余裕があることになります。
後で施す加工をするとこれらの機構は完全に覆われ怪我をする可能性はなくなりますが、まさかのときのために分解して修理・調整が可能な構造になっています。
|
|
|
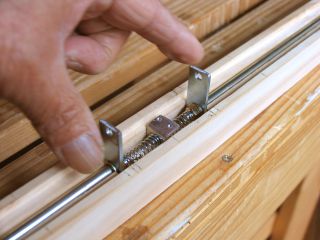 |
|
ロック解除機構の作動を確認しました。
左の写真をクリックするとWindows Media Playerにて動画でその様子をご覧いただけます。
音声も同時に記録していますが、僅かなスプリングのきしみ音が聴こえる程度で動きを阻害するような異常な擦れ音は全くしていません。 実際にはこれらの機構にカバーを被せて上下を反対にして使いますが、問題が生じる部分は恐らくないはずです。 一発必中を狙い事前の検討にはそれこそ相当の時間を掛けましたが、完成度の高い物が出来たようで満足しています。
前作の分別ごみ箱では蓋の跳ね上げ機構が期待通りに作動せず結構手間取りましたが、身近に入手可能な材料に最小限の加工を施しての実現は今回は大変上手く行きました。 |
|
|
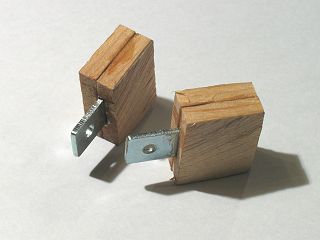 |
|
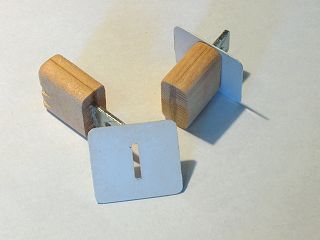 |
|
|
ツマミは14mm厚の板を翔250で半分に切断しその片面に金具を落とし込む溝をノミで削った上でエポキシ接着剤で貼りあわせました。 かなり削り込むので2mm程大きめです。
|
|
粗目ヤスリと替刃式ヤスリで成形を施したのちに機構の穴が若干残る部分を覆うカバーを0.5mm厚塩ビ板で作りツマミに嵌め込みます。
|
|
|
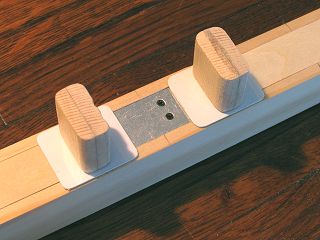 |
|
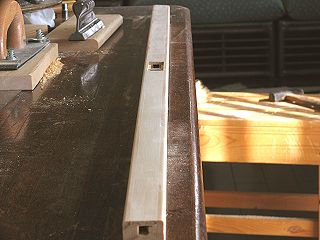 |
|
|
カラクリ部分を再度組み立てましたが目論見どおり完璧に機構は隠れます。 これで安全性はほぼ完璧になると思います。
|
|
4mm厚の板のカバーを接着しそれが硬化したところで面取りと仕上げ研磨を施しました。 手前の端にロックピンとなるパイプが通る穴が見えます。
|
|
|
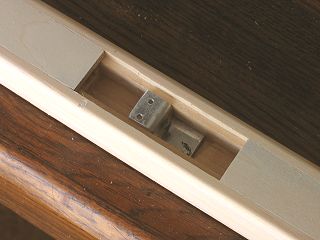 |
|
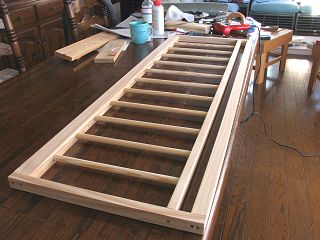 |
|
|
カラクリ中央部分。 作業はやりにくくなりますが、アルミ板のカバーとツマミ、パイプを取り除くとこのような状態に出来ますから、調整・修理は可能です。
|
|
上端の棒が完成したのでスライド柵の組立をしました。 木工ボンド併用ですが、接着部分の面積が小さいため木ダボは使わず片側に45mmのネジ4本で固定しています。
|
|
|
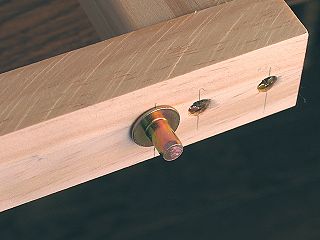 |
|
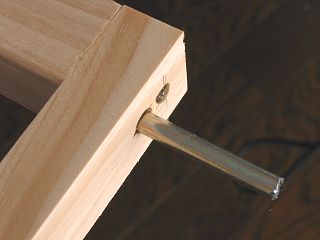 |
|
|
スライド柵の下のほうに固定ガイドピンとなるスチールピンを6φ 13mmの穴をあけて差し込みました。 これは後ほどエポキシ接着剤で固定します。
|
|
切り落としたパイプの端材を使って上端のロックピン穴のあき具合を確認中。 この穴がずれていたら摩擦が多くなって使いものになりません。
|
|
|
 |
|
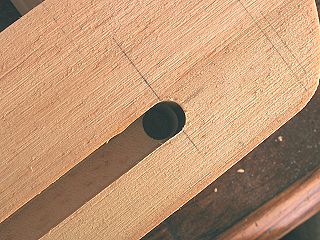 |
|
|
左右の側板ブロックにはロックピンが嵌り込む穴をあけました。 穴の深さは20mmですが、電動ドリルアタッチメントを使っていますから正確な深さ設定が可能で容易に作業できます。
|
|
その穴があいた所。 小判状にあいたように見えますが、それは斜めから撮影したためで実際には正しい円状にあいています。
|
|
|
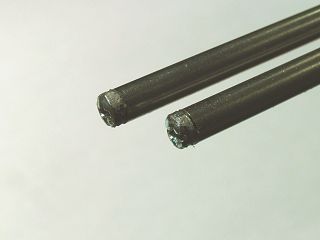 |
|
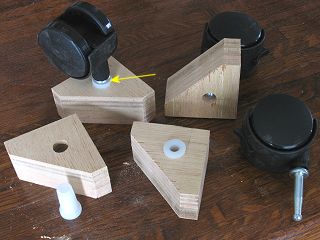 |
|
|
所定の長さに切断したパイプの先端には頭の直径を短く削り落としたM4 トラスボルトを挿し込み接着します。 頭のプラスの溝はそのままですのでプラスドライバーを挿し込むとリンク棒は回転せず、リンク棒にツマミをナットで固定するのが容易になります。
|
|
キャスターはソケットタイプの50mm。 左下はキャスター取り付け板(18mm合板2枚重ね)に12.5mmの穴をあけた所。 その右はソケットを叩き込んだ所。 尚矢印の隙間に大き目のマイナスドライバーを挿し込みこじればキャスターは外せます。
|
|
|
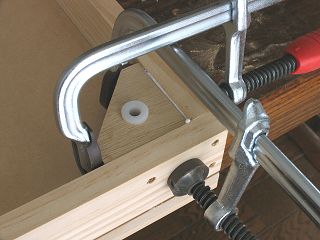 |
|
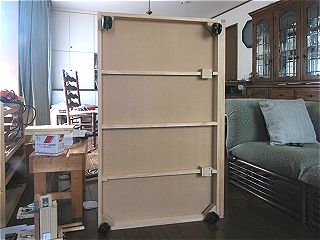 |
|
|
キャスター取り付け台座の固定。 木工ボンドを塗って台座を当てたらクランプで固定した後にネジで締め付ける。 クランプを使わないと間違いなく隙間が生じてしまいます。
|
|
各キャスター台座を4本のネジで木工ボンド併用で固定し全ての加工・組立作業は終了したことになります。
|
|
|
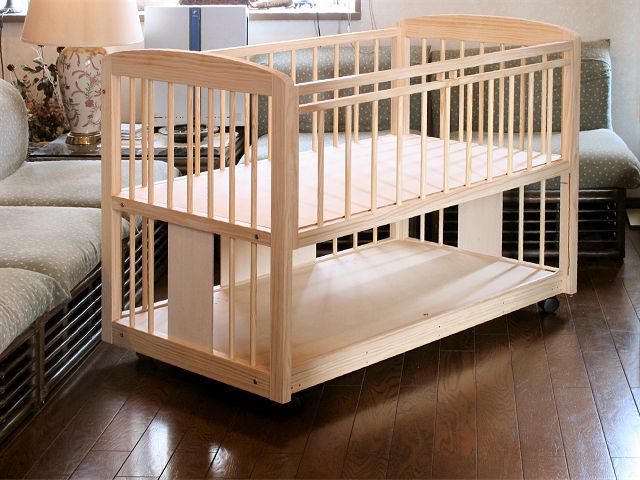 |
|
|
再度組み立ててスライド柵の上下の具合、ロックピンの動作を確認しました。 マイナーな調整はあるが期待していた作動は完璧に出来ており、ロックピンのON/OFFは大人なら片手で楽に操作できます。
|
|
|
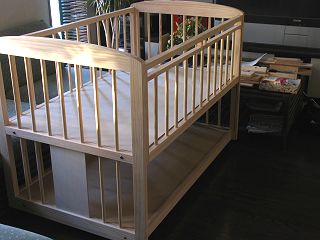 |
|
午後3時過ぎた屋内とあって撮影条件は良くありませんが、左の写真をクリックしてスライド柵の上下ロックピンの作動状況を動画でご覧下さい。
全体を撮影しているのでロックレバーの部分は良く見えませんが、解除する際には2つのレバーを指で挟んでやればピンが外れ、柵は自重で下に降ります。 また上にロックする場合にはレバーに触れずに柵を上端まで引き上げればロックされます。
この動画はAVIファイルで、Windows Media Playerでご覧いただけますが、大きなファイルですので読み込みには時間が掛かります。 |
|
|
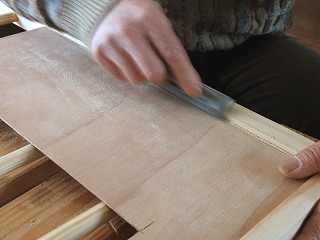 |
|
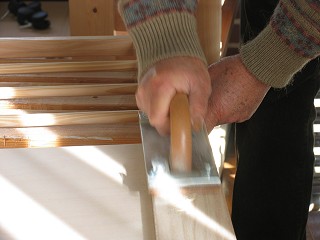 |
|
|
面取りの仕上げ作業。 替刃式ヤスリ(M-20GP)で効率よく進められますが、丸棒部分を傷つけないよう3mm合板で覆いながら作業しています。
|
|
屋外なら電動サンダーをつかえるのですが寒くて我慢できないので、ハンドサンダーに#60を取り付け面の部分の傷や接合部の段差を削り落とし、#120、#240のペーパーに変えてつるつるにしました。
|
|
|
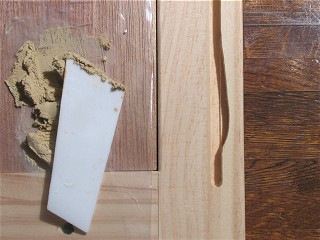 |
|
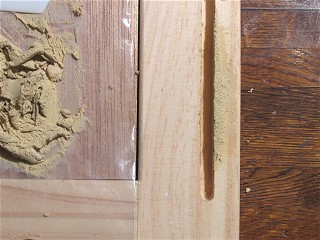 |
|
|
電動トリマーで誤って削ってしまった部分の修復。 ウッドエポキシの2液を等量練り合わせてやりますが、粘土よりも硬めで垂れたり流れたりすることはありません。
|
|
削り落としてしまった部分にこすり付けて埋め込みます。 完全硬化後はそれこそ刃も立たなくなりますが、気温の低い今は24時間以上過ぎた半硬化状態で、ナイフで削り落とす、ペーパーで研磨するなどの仕上げ作業をします。
|
|
|
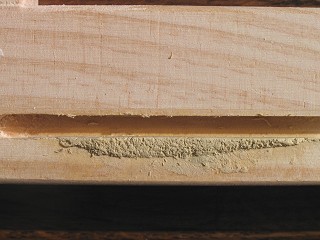 |
|
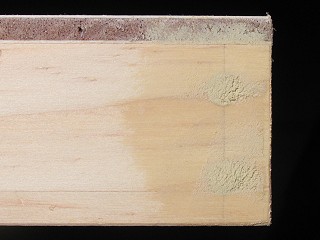 |
|
|
盛り上がった状態を見易くするため回転して撮影。 汚らしく見えますが心配ご無用、1昼夜経ってから仕上げ研削・研磨をします。(後ほどお見せします。)
|
|
これはベッド床板ブロックですが、目に触れる部分にあるネジ穴をウッドエポキシで埋めてしまいます。 ウッドエポキシの最大の利点は収縮が殆ど無いため一回の作業で穴を完全に埋め込める点にあります。
|
|
|
ウッドエポキシの硬化時間は気温により大幅に変化します。 メーカーの説明では充填作業は40分以内(20℃)とありま すが、今のように気温の低いときには1時間経っても充填作業が可能です。 また完全硬化には20℃でも1週間は掛かり ます。 充填後24時間以上経過しかつ完全硬化までの間に、はみ出た部分をナイフで削ったり、ペーパーで研磨したり、
ドリルで穴を開けることが可能ですが、完全に硬化してしまうと研磨は極めて困難になります。 そのような特性を知った
上で使うときれいな仕上がりにすることができます。
|
|
|
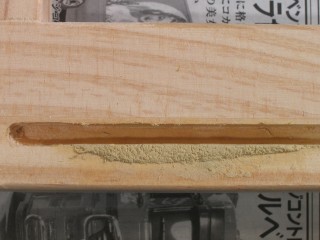 |
|
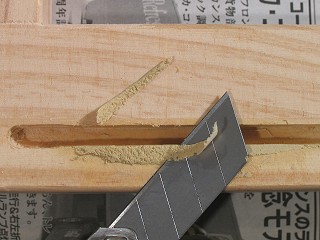 |
|
|
上の写真と同じ部分ですが24時間経過後で光が指す方向が少し違うので変わって見えますが、収縮などの変化はありません。
|
|
まず盛り上がった部分をカッターナイフで削り落とします。 溝内壁の出っ張りも同様にカッターナイフで大まかに削ります。 この作業は半硬化の間は大変容易です。
|
|
|
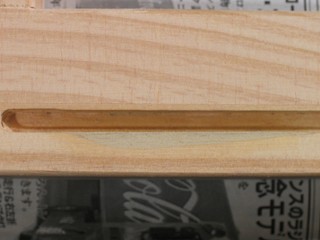 |
|
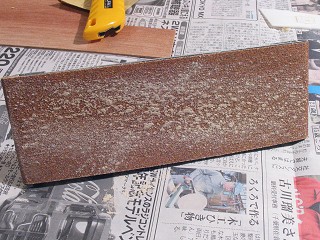 |
|
|
その後#60、#120、#240と3段階で表面が完全に平らになるまで削り落とし修復は終了。 溝内壁もピンがスムーズにとおるよう確認しながら研磨します。 完全硬化すると修復した溝の表面は極めて硬くなり木部より丈夫になります。
|
|
研磨には一番安い洋紙ペーパーがよろしい。 その理由はこれ!半硬化のウッドエポキシがあっという間に目詰まりを起こすからです。 小さな研磨面積なのに目詰まりのため5枚も交換しました。
|
|
|
注意! ここで述べている研磨には安い洋紙サンドペーパーを使う!というのは研磨のみならず切削にも言えます。 削り落とすのに間違ってもカンナやノミを使わないでください。 半硬化とは言え刃物にとってウッドエポキシを切るのは
かなりの負担であり刃を痛め易いからです。 カッターナイフを使っているのはそのためで、研磨にしても全ての金属板ヤ
スリを使ってはなりません。 目詰まりが取れずにお釈迦にしてしまう可能性が大です。
こんなことはウッドエポキシの説明書には全く書いてありませんが、実は私がウッドエポキシを使い始めたときにそのよ
うにして道具を駄目にしてしまった経験があります。
|
|
|
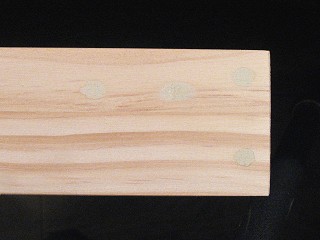 |
|
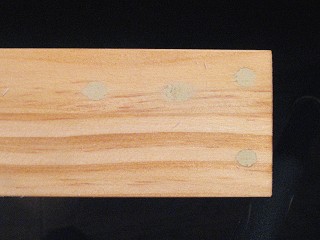 |
|
|
ウッドエポキシ部分は塗料が沁み込みませんから周りと色合いが若干変わってしまいます。 左は研磨終了後の状態ですがニスを塗るとどうなるのか? それに近しい状態は水で濡らすと判ります。 右がそれで水性ニスは黄変が少ないのでこれに近しいですが、油性ニスの場合にはもっと木部の黄味が増します。 このような見え方は嫌だ!という場合にはペイント塗りつぶしとするか或いは組立てに一切ネジを使わずに進めることになります。
|
|
ウッドエポキシは使用後の見栄えそのものは通常のパテ
|
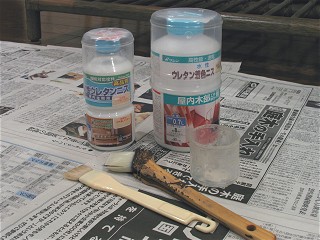 |
|
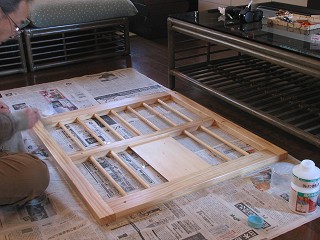 |
|
|
今回使った水性ウレタンニス透明クリヤー(右)と水性ウレタンニス艶無しクリヤー(左)です。 手前は歴戦の30mm水性ニス刷毛と22mmラック刷毛。
|
|
ご覧のように床に新聞紙を3枚重ねてその上で塗装作業をしました。 臭気が殆どないため窓も締め切ったままで外はかなり寒いですが快適?な作業が可能です。
|
|
|
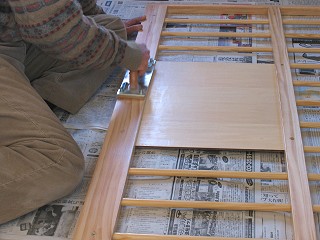 |
|
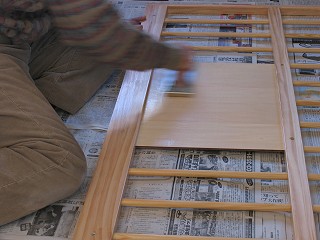 |
|
|
1回目は透明クリヤーを塗りますが、塗装後3時間後に#400ペーパーをハンドサンダーに取り付けて表面を軽く研磨しざらつきを取ります。
|
|
面の部分はハンドサンダーを長手方向と直角方向に移動し研磨しています。 軽い研磨だから出来る芸当ですが、このため作業効率は大変良いです。
|
|
|
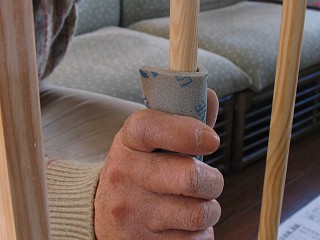 |
|
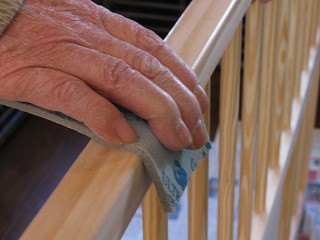 |
|
|
一方丸棒部分はスポンジ研磨剤極細目(#320-#600)で包むようにして研磨しました。 洋紙ペーパーだと曲面になじみにくく一部の削り過ぎが起き易いです。
|
|
同様にボーズ面トリマービットで成形した角の丸い部分もスポンジ研磨剤で磨いています。 研磨の道具には適材適所があり、選択によって作業効率や出来栄えが変わります。
|
|
|
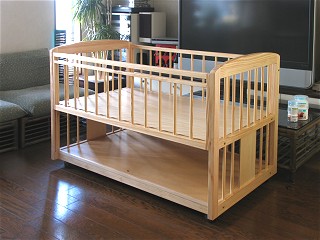 |
|
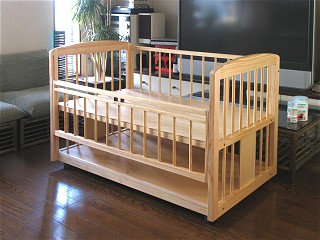 |
|
|
塗装終了後完全乾燥のため1日寝かし、移動柵を途中でロックさせる穴を追加した上で最後の組立てをしました。 これは移動柵が最上段にロックされている状態です。
|
|
ロックレバーを引いて解除しロックレバーを離すと移動柵はこの位置で停止しロックされます。 これで寝ているときにベッドから転げ落ちる心配はなくなります。
|
|
|
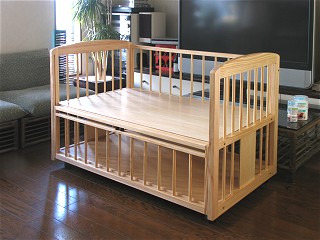 |
|
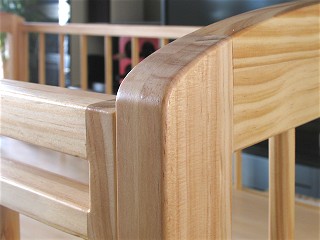 |
|
|
もう一度ロックレバーを引くと移動柵はここまで降りて停止します。 赤ん坊がベッドの外の床などで遊んでいるときに、べっ移動柵がベッド下収納部分をブロックするのでそれらをいたずらできません。
|
|
全ての露出する角はご覧のとおり丸く成形しましたから安全ですし外観上柔らかい雰囲気が出てきています。
|
|
|
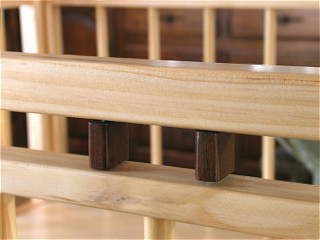 |
|
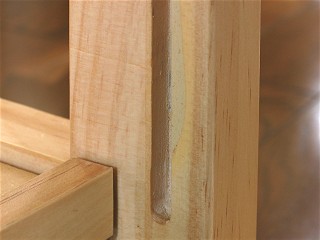 |
|
|
ロック解除レバーのアップ。 このレバーだけはステインでこげ茶色に着色後水性ウレタンニス3回塗りとしています。 完全にニスの皮膜で覆われるので食品衛生法適合となります。
|
|
間違ってトリマーで削り込んだ部分。 ニスを塗った状態は更に見分けがつきにくくなっています。 おそらくここは修復した跡だ!と指摘しない限り気がつくことはないでしょう。
|
|
|
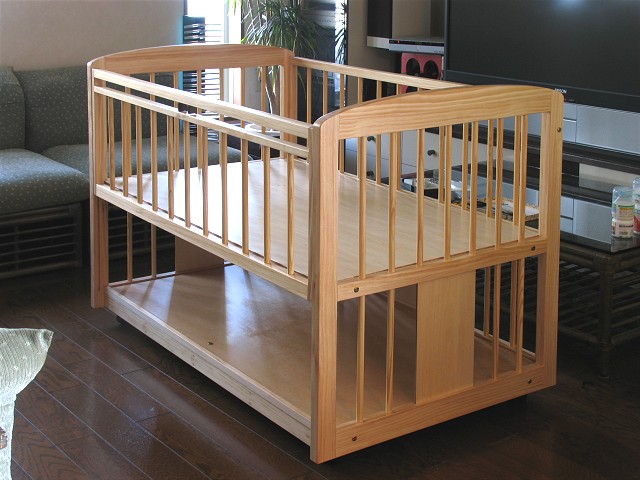 |
|
|
まもなく再びばらして長男宅に運び込まなければなりません。 十分な作業時間があったはずですが実際にはドンピシャタイミングで完成したベビーベッド。 ほっと一安心です。
|
|
Copyright (C) 2001-2019, Vic Ohashi All rights reserved.