|
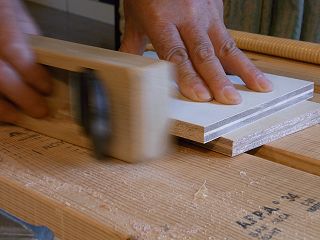 |
|
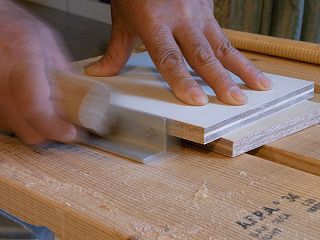 |
|
|
各部材の切断面はこのようにカンナで削って寸法と直角度の調整をしています。
|
|
その後替刃式の自作直角ヤスリで研摩して面精度を高めます。
|
|
|
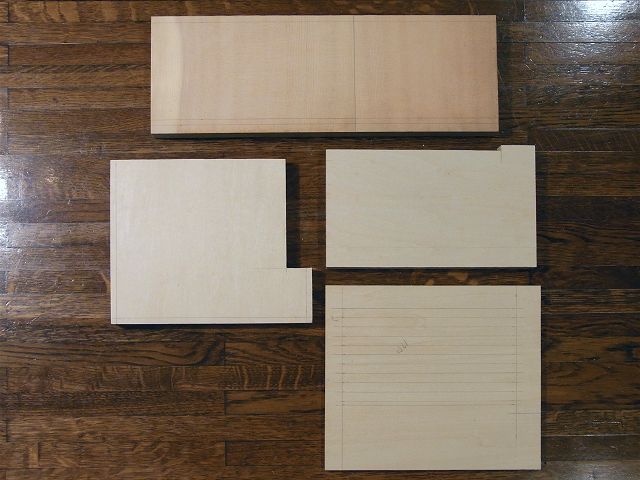 |
|
|
ちっぽけな板4枚の第一次加工(切断)が終わったところですが、ここまでだけで半日を費やしました。
|
|
|
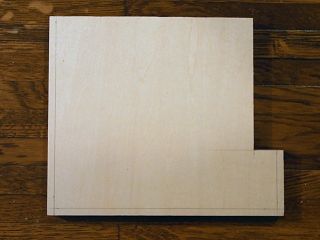 |
|
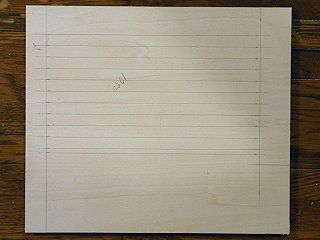 |
|
|
これは底板ですが、左側、下側、右下部には墨線が入っています。 後ほどこの部分を45度切削します。
|
|
こちらは天板で沢山の線が見えるのは3mm幅の溝彫りの位置です。 それが終了後に左右を切断します。
|
|
|
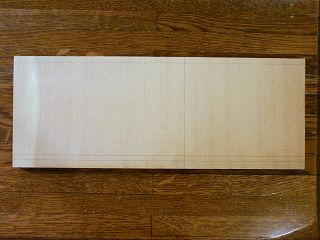 |
|
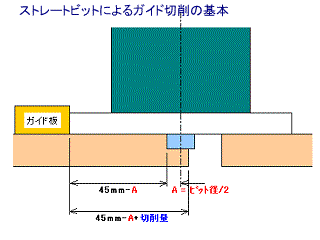 |
|
|
これは側板で左右の側板が横に繋がったまま上下の段差切削加工に進みます。 その後に切り離せば段差加工の左右のバラツキは最少になります。
|
|
ストレートビットで角に段差を付けるには、深さはビットの飛び出し量で決まりますが、切り込み幅は、45mm - (ビット直径の半分) + 切削幅になります。(リョービの場合。)
|
|
|
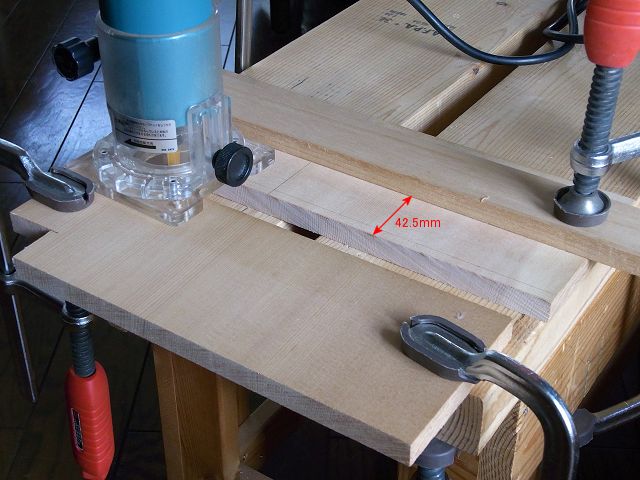 |
|
|
私は15mmのストレートビット(TS2-15G)を使いますが、切削幅を5mmとしたいので上の計算式により、端からガイド板までの長さが42.5mmになるようガイド板をセットしています。
|
|
|
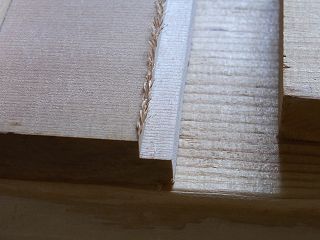 |
|
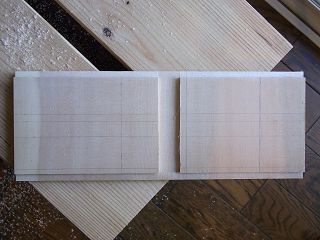 |
|
|
切削し終ったところ。 角にバリがかなり残っていますが、替刃式ヤスリで軽くこすれば綺麗に落ちます。
|
|
繋がったままの側板に段差を施しました。 中央の切削は左側板の背面側の削りこみです。
|
|
|
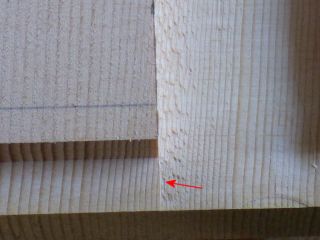 |
|
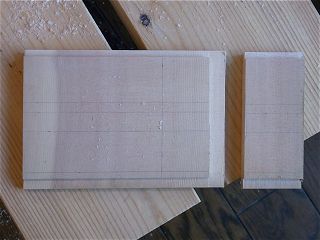 |
|
|
中央切削部分のアップ。 ご覧のようにごく僅かな切削深さの違いがあり、約0.1mm位の段差が出来てしまいました。 これが出ないように切削するのは非常に難しい。
|
|
左側板と右側板に切り離しました。 この後フロントパネル用溝彫り、斜め切削に続きます。
|
|
|
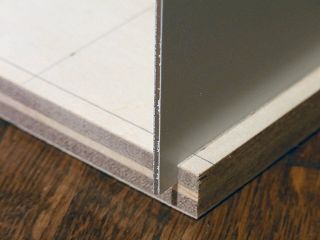 |
|
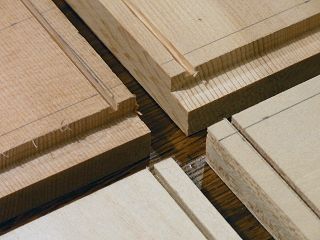 |
|
|
フロントパネル用の溝をストレートビット(SS1-1.6G)で彫ってパネルを挿しこんで見ました。 この場合パネルには保護用の薄い幕が貼ってあり厚みは1.6mmあるため挿しこむ時はきついです。
|
|
全てのパネルが挿しこまれる溝を彫り終わりました。 切削の位置精度は±0.1mm程度になるよう時間を掛けて慎重に進めています。
|
|
|
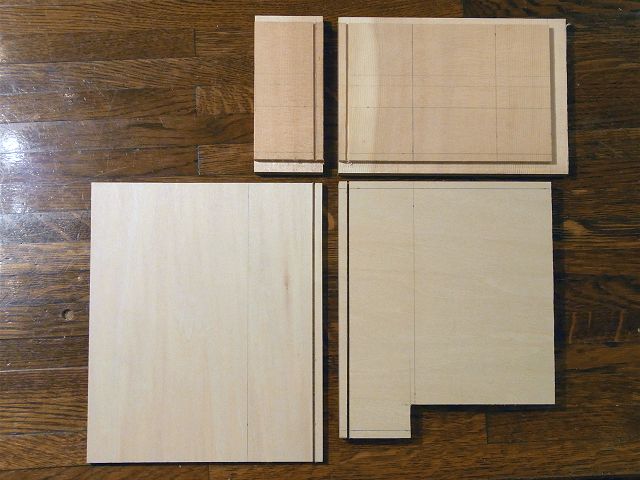 |
|
|
中央縦にパネル用溝の切削後の様子が見えます。 上の左は左側板、右は右側板で、下側は左が天板の裏側で右が底板です。
|
|
|
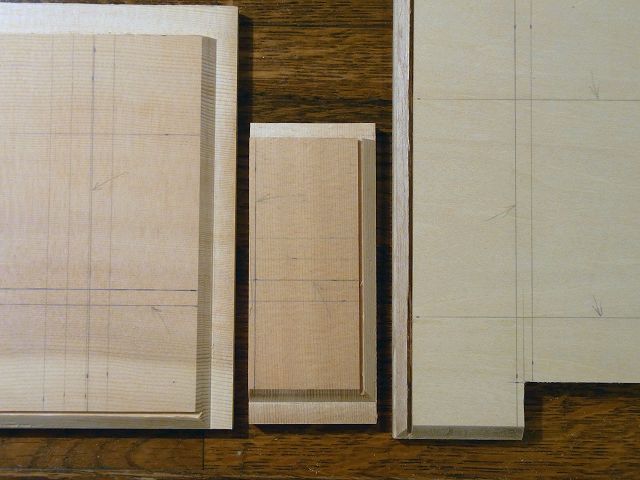 |
|
|
次に45度傾斜切断をV溝ビット(VB-90G)で施しました。 最も神経を使うトリマーが主体となる二次加工がやっと終了しました。 この二次加工だけで1日を使いましたが、実際の加工時間の20倍近くをその前の設定に費やし、加工精度が確保できるようにしています。
|
|
|
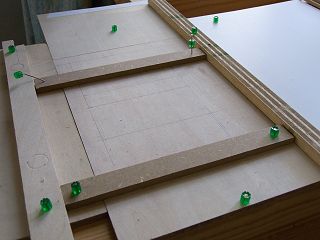 |
|
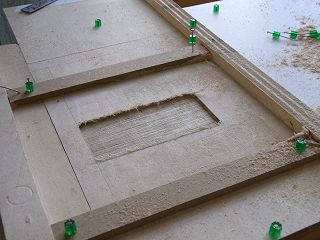 |
|
|
三次加工は天板の放熱口切削です。 方法としては板厚の1/2の深さで裏側に座繰りを彫ることから始めますが、このように切削範囲を制限する枠を打ち付けています。
|
|
10φのストレートビットを使って片側の切削が終わりました。 深さは約2.8mmです。
|
|
|
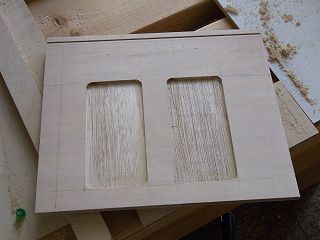 |
|
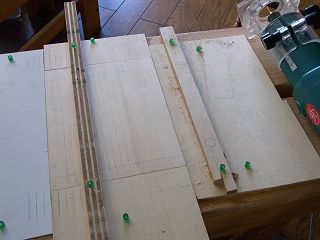 |
|
|
2箇所の座繰り後にバリをヤスリで削り取って裏面の加工は終わりです。
|
|
天板をひっくり返してセットし今度は3φのストレートビットで溝彫りです。 彫る深さは2.8mmで板厚は5.5mmですから、裏面の座繰りと重なる部分は穴があくことになります。
|
|
|
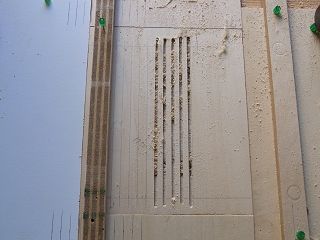 |
|
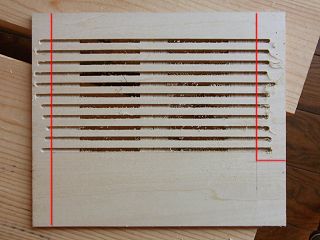 |
|
|
左に見えるガイドの細い棒は1箇所切削するたびに8mmずつ左に移動しますので、溝幅3mm、溝と溝の間が5mmで加工されます。
|
|
彫った溝の長さがまちまちになっていますが大丈夫。 この後赤線で切断して最終的な寸法になります。
|
|
|
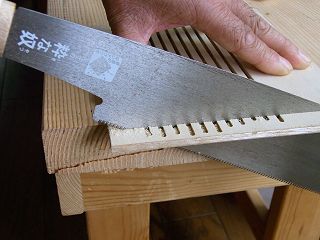 |
|
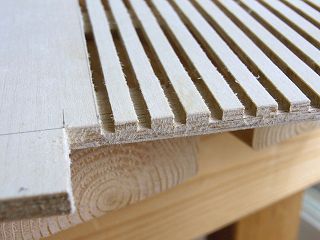 |
|
|
天板横方向を最終的な寸法に切断。 トリマーで切削した溝近辺はデリカシーのあるノコギリでないと欠けたりしますので、『粋な奴』のような精密切断用ノコギリが有効です。
|
|
『粋な奴』で切断後のアップ。 大変綺麗な切り口でバリが殆ど発生しません。
|
|
|
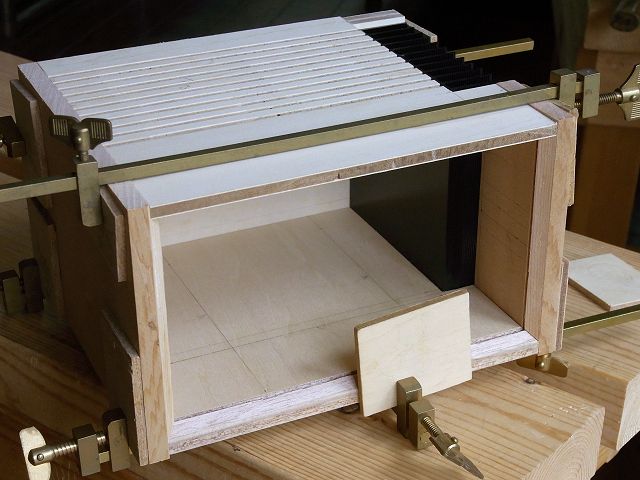 |
|
|
三次加工まで終了しましたので、まさかのミスが無いかどうかの確認のためにハタ金で組み上げて見ました。 寸法調整の研摩はまだ殆どやっていませんが、寸法誤差は±0.2mm位に収まっているようです。
|
|
|
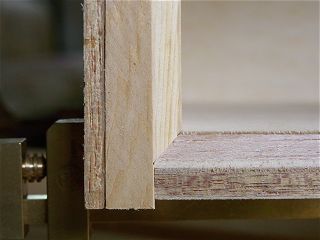 |
|
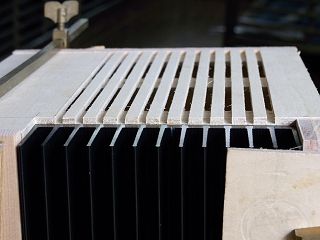 |
|
|
前面左下の角でトリマーによる少々ややこしい切削はうまくできたようで、接合時に変な隙間やゆがみの発生はありません。 側板下部が突出していますが、これは目地払いビットで接合後にカットします。 同様な意識的に突出させている部分は他にも7箇所あります。
|
|
設計時に放熱口の溝と放熱器のフィンが一致するように考えていたのですが、これもドンピシャになったようです。 一次加工から三次加工までおよそ3日間を使い超スローペースで進んできましたが、その甲斐はあったようです。
|
|
|
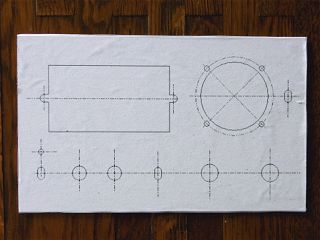 |
|
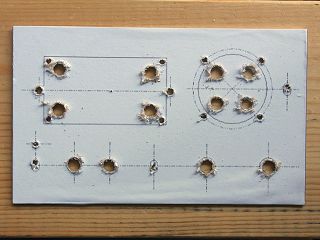 |
|
|
あけるべき穴を描いた原寸大のプリントアウトをアルミ板に貼り付けました。 |
|
センターポンチで穴あけ位置を確実にした上で、3、3.2、3.5、4、8mmのドリルで所定の穴を開け終わりました。 大きな円と長方形の内部の大きな穴(各4個)からジグソーで切り抜いて行きます。
| |
|
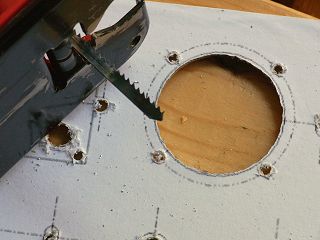 |
|
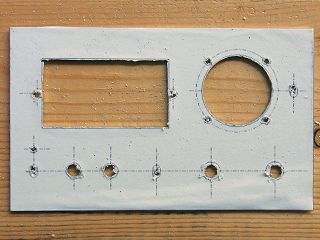 |
|
|
円の部分を切り終わったところですが、使用ブレードはNo.5でCJ-250に取り付けております。 またご覧のように墨線から0.5mm程度離れた所を切り落しています。
| |
ドリルによる穴あけとジグソーによる切断が終わりました。 ここまで1時間程度の所要時間です。 この後寸法出しの研削・研摩に入ります。
|
|
|
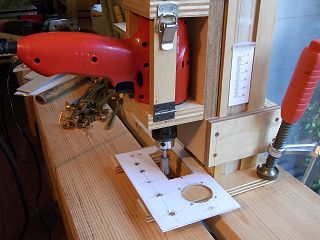 |
|
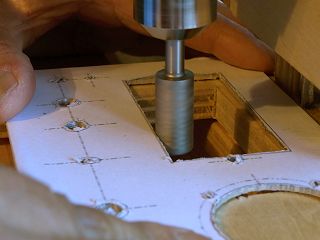 |
|
|
回転ヤスリによる効率的な研削研摩の方法で現在は電動ドリルアタッチメントを使っていますが、近い将来別なアタッチメントを考案する予定です。
|
|
型紙の墨線どおりドンピシャとなるよう研削・研磨中。 これは直線部分ですが、曲線部分(凹凸両方)の研摩も可能です。
|
|
|
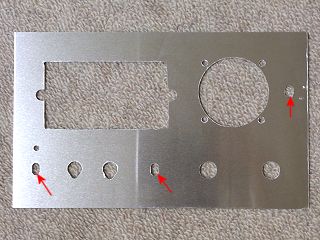 |
|
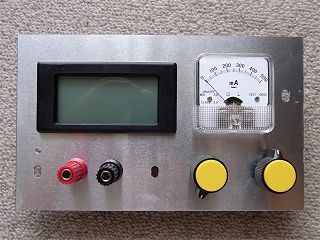 |
|
|
全ての研削・研摩が終わりました。 面倒だったのは矢印の先の小判型の小さな穴くらいなものです。 また私のやるこの方法はアルミ板を曲げてしまうような無理なことが全くありません。
|
|
パネルに直接固定する部材だけを仮固定して確認しました。 この後へヤーライン加工に進みます。
|
|
|
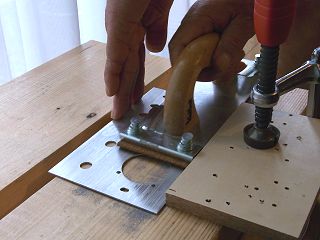 |
|
 |
|
|
アルミパネルの表面を#60サンドペーパーで研摩し一様な平行の筋を付けます。
|
|
何度試しても満足度の高い一様な筋を付けるのが出来ませんが、一応ヘヤーライン加工らしき仕上がりとなりました。
|
|
|
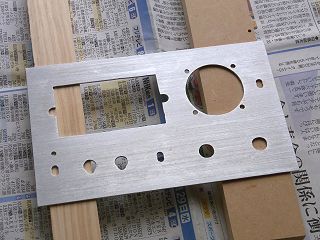 |
|
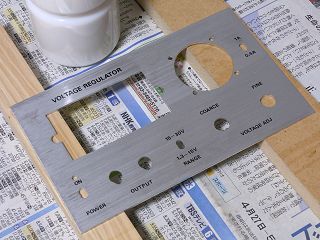 |
|
|
表面を洗って研磨屑を完全に落とし乾燥後に水性ウレタンニスを2回塗りました。 これでインスタントレタリングの付きが良くなります。
|
|
インスタントレタリングで文字入れ後に、剥がれ防止のためもう一度水性ウレタンニスを塗ってフロントパネルは完成です。
|
|
|
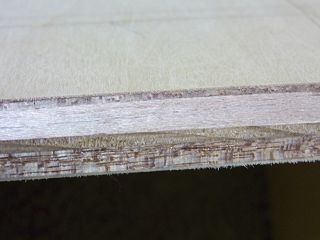 |
|
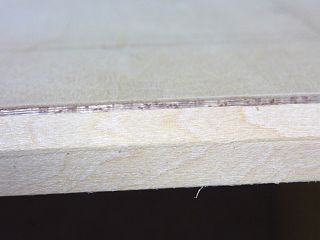 |
|
|
底板は合板ですので前面の見え方は美しくありません。 そこでシナの木口テープでお化粧します。
|
|
傾斜部分と垂直部分を2枚の木口テープで繋いで貼り、表面をサンドペーパーで仕上ました。
| |
|
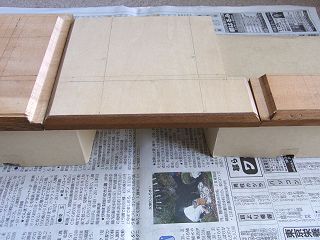 |
|
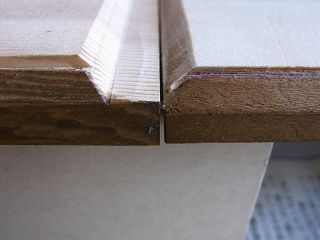 |
|
|
左右の側板と底板の前面はオーク色のポアステインで着色し材木が違うことによる色違いを揃えました。
|
|
濃い目の色であることも手伝い、全く異なる材木であることは先ず判らない状態になっています。
| |
|
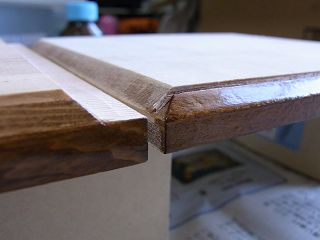 |
|
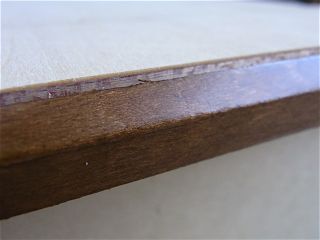 |
|
|
その上に水性ウレタンニス透明クリヤーを3回塗りしています。 油性に比べると肉載りが劣るので塗り回数は増えますが、乾燥時間が短いので作業時間が長くなることはありません。
|
|
そして最後に水性ウレタンニスつや消しクリヤーを塗って完了です。 これは私の標準塗装工程になっていますが、しっとりとした格調高い質感が得られますし、多少の粗を隠せるメリットもあります。
| |
|
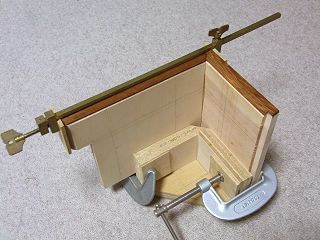 |
|
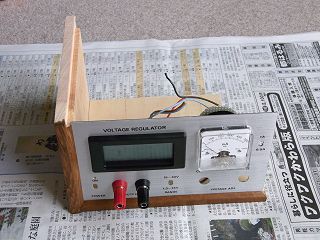 |
|
|
底板と左側板から接着開始。 30分硬化開始型エポキシを使っています。 また直角接合ジグを使い正確な直角が出るよう万全を期しています。
|
|
2時間放置後にフロントパネルを挿入してみました。 全く問題なく装着できます。
| |
|
 |
|
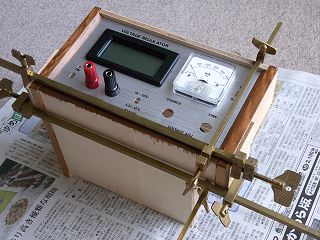 |
|
|
天板を載せて左に90度回転させました。 この面に右側板を接着しますが、天板は位置関係を保持するため残すものの接着はしません。
|
|
ハタ金を使って軽く圧着保持をしています。 エポキシ接着剤の充填効果を期待しているので、強力な圧着保持は歪み防止のため不要で、ハタ金使用がベストです。
| |
|
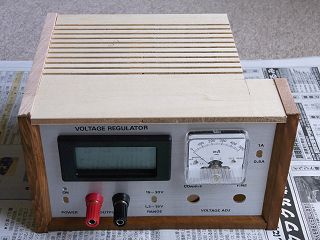 |
|
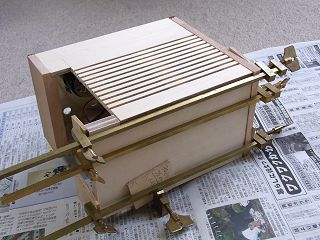 |
|
|
左右側板と底板の接着が終わりました。 この状態で背面の板を接着します。
|
|
背面の板接着時の圧着保持もハタ金です。 勿論天板は接着位置出しのために挟んであるだけで、接着はしません。
| |
|
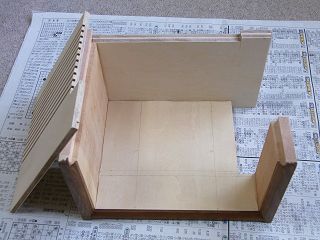 |
|
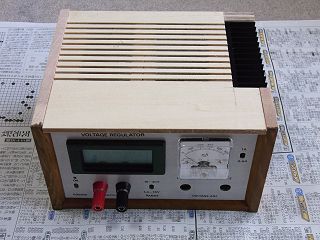 |
|
|
4面の接着が終わったところです。 試しにフロントパネルを抜き差ししてみたところ、無理やりの力技ではなくできました。 これは期待以上で、これまでの切断、切削、研磨などの作業と接着作業が全て高精度であったことの証です。
|
|
再度フロントパネルを挿入し天板を落とし込んで、放熱板を所定の位置にはめ込んで見ました。
| |
|
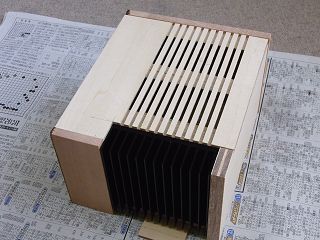 |
|
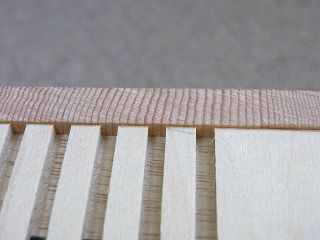 |
|
|
それを右側から見たところです。 まったく不具合はありません。
|
|
落とし込んだ天板と側板の段差は約0.5mmで均等になっており、ここにも正確な作業が表れています。
| |
|
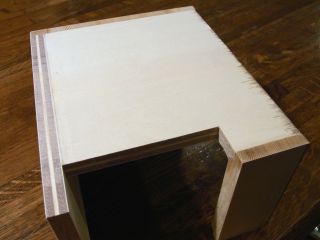 |
|
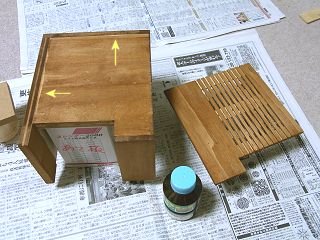 |
|
|
コロ付き傘付き目地払いビット(MB-12.7G)にて接着時に飛び出た部分を削り取りました。 但し底面に付着したエポキシ接着剤は十分に削り取れませんでした。
|
|
ポアステイン(オーク色)を水で3倍に薄め着色中。 これは3回塗装後の様子です。 底面の矢印の先は十分にエポキシ接着剤を削り取らなかったために着色が出来ないため白っぽく斑になっています。
| |
|
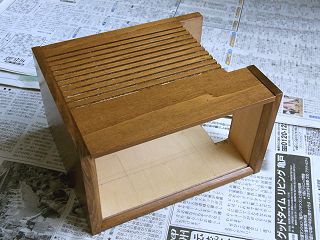 |
|
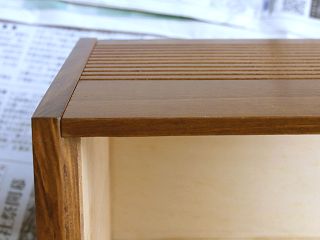 |
|
|
着色終了後水性透明クリヤーニスを3回、つや消しクリヤーを1回塗ってから天板を所定の位置に嵌め込んだ前面側です。
|
|
前面左上のクローズアップ。 天板は5.5mmシナ合板ですが、木口テープを貼ってから着色・塗装しているので、このように合板には見えません。
| |
|
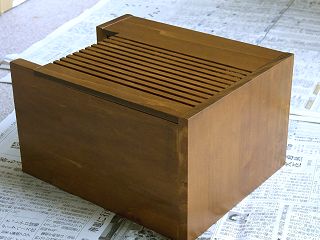 |
|
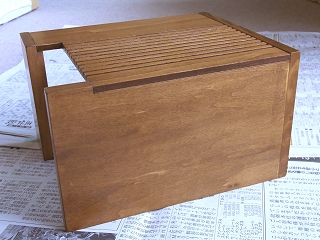 |
|
|
こちらは裏面を右側から見たところです。 右側はムク板を使った左側板面です。 艶は抑えられてしっとりとしています。
|
|
背面を左手の方から見ています。 左側には大きな欠き取りがありますが、ここに放熱板が入ります。
| |
|
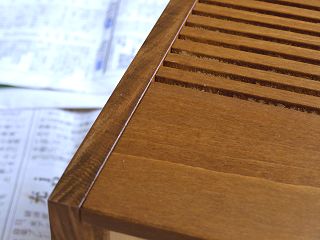 |
|
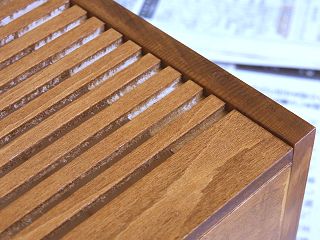 |
|
|
天板が側板に接触している部分。 側板は僅かに突出しています。(約0.5mm)
|
|
その後ろ側の様子。 放熱の為の溝切りも綺麗に並んでいます。
| |
|
 |
|
|
最後にフロントパネルを挿しこんでみた前面からの様子で、最終的な外観にかなり近くなっています。 そして格調高い質感が出てきており、手を掛けただけのことはある!という求めている物になっています。
|
|
|
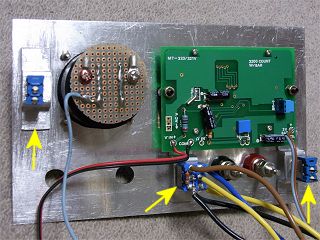 |
|
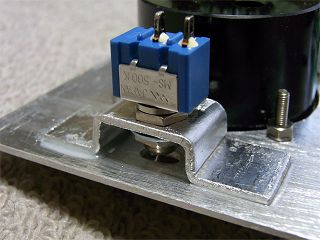 |
|
|
3個のトグルスイッチ固定金具をフロントパネル裏面にエポキシ接着剤で固定しました。
|
|
接着剤による固定状況はこのようです。 接着強度を高めるため接着面は#60のサンドペーパーで表面を粗びています。
|
|
|
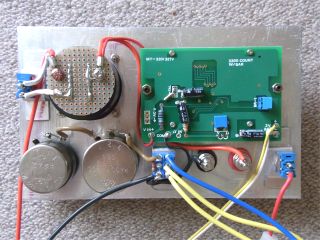 |
|
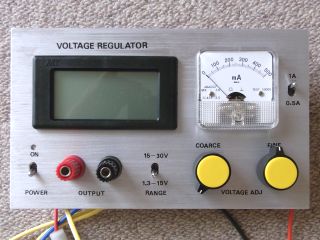 |
|
|
可変抵抗を固定後、フロントパネル面で完結する配線と、電源基板やトランスに接続する線の引き出しを済ませました。
|
|
これでフロントパネルユニットは完成しました。 アセンブリーとしてケース前面の溝にこの状態で抜き差しします。
|
|
|
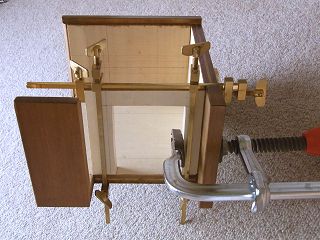 |
|
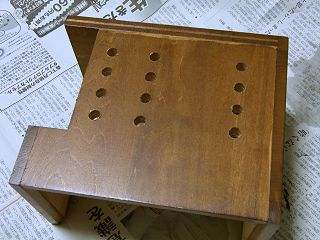 |
|
|
放熱板取り付け枠を切り出しエポキシ接着剤で固定中。 ハタ金、クランプは圧着保持ではなく、接着位置出しのために使っています。
|
|
天板固定の桟もエポキシで固定し、底部には12個の9φの穴をあけました。(右側の8個がトランス冷却用、左の4個は基板と放熱板内面冷却用です。)
|
|
|
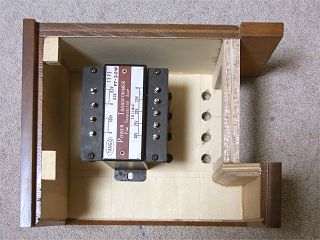 |
|
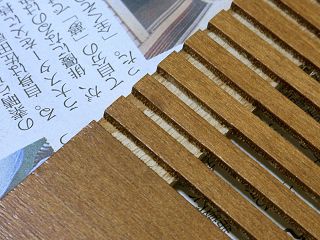 |
|
|
8個の穴はトランスの下になるので最終的には殆ど見えません。 右の4個も電源基板を固定すると見えなくなります。
|
|
天板の溝の中を水性ペイントのつや消し黒で塗装します。(これは塗装前。)
|
|
|
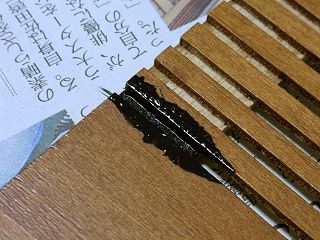 |
|
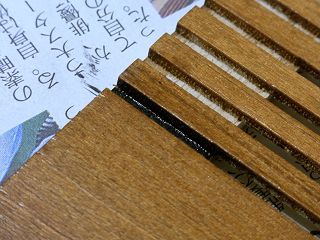 |
|
|
正しい塗装もへったくれもありません。 とにかく手早く完全にペイントで埋める事に専念します。
|
|
表面にはみ出たペイントは水で濡らして絞った布で速やかに拭い去ります。(もたもたしていると乾燥して拭い難くなります。)
|
|
|
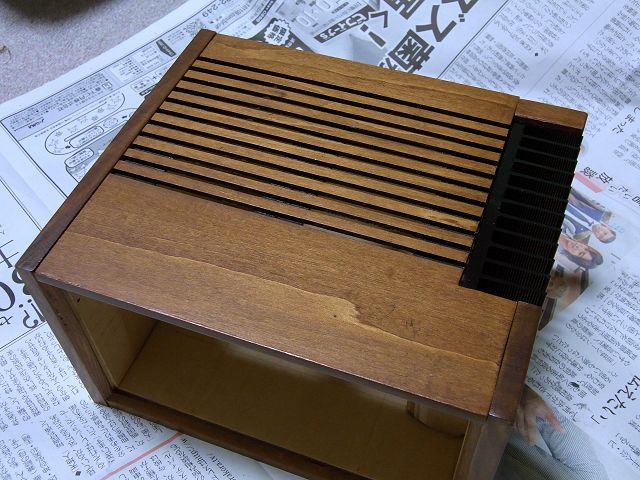 |
|
|
水性塗料の特性を生かした方法で、溝の中は無事真っ黒に塗りつぶしが出来ました。 乾燥後に放熱板をネジ止めしました。
|
|
|
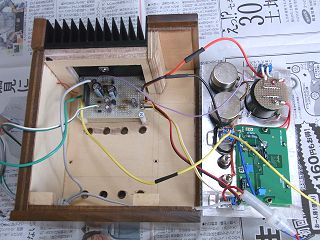 |
|
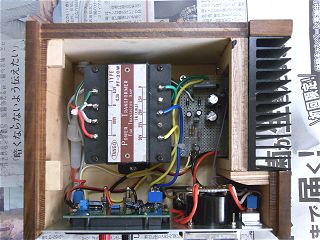 |
|
|
電源基板を所定の位置に固定してから放熱板にレギュレターICをネジ止めし、電源基板とフロントパネル間の接続を済ませます。
|
|
そしてトランスを固定してフロントパネルと電源基板からの配線をトランスに接続して組み上げは終了です。
|
|
|
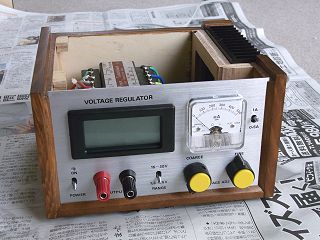 |
|
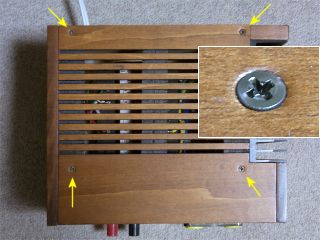 |
|
|
以前のテスト時と同等の性能が得られるか、トグルスイッチの逆接続が無いか、デジタル電圧計の指示誤差は許容範囲か?などを確認します。
|
|
最後の作業で、天板をネジ止めしました。 使ったネジは皿ネジですがステンレス製でブロンズ色に着色してあるものを使い目立たなくしています。
|
|
|
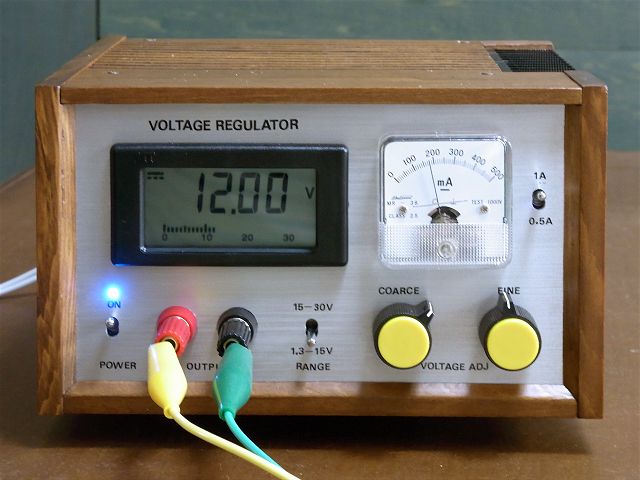 |
|
|
完成後使用状態の様子。 これで電池駆動のアプリケーション製作時により快適に実験が出来るでしょう。
|
|
|
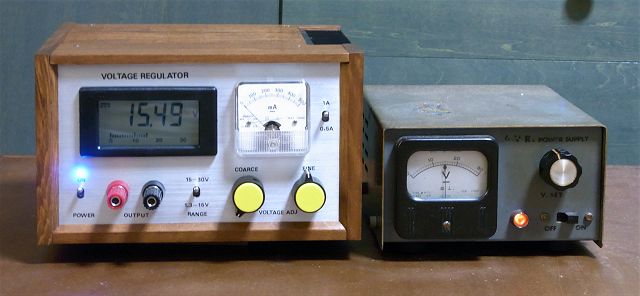 |
|
|
新・旧定電圧電源。 ネオンランプと青LEDのパイロットランプやデジタル、アナログ電圧計に40年近い時間差を感じます。 前面サイズが大きくなりましたが、より多くの部材を取り付けたのが主原因で、これ以上小さくすると使い勝手が悪くなるでしょう。 奥行きは7mm増えただけで内部のレイアウトも考えれば限界に近い大きさかもしれません。
|
|
|
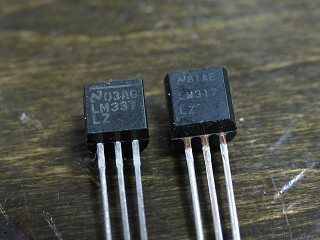 |
|
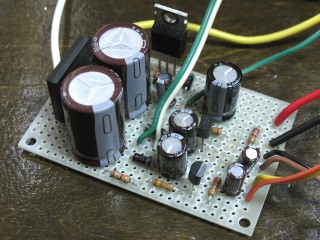 |
|
|
左がここで使ったマイナス電圧用レギュレータ(LM337LZ)。 右はLED駆動用に多く使っている兄弟のプラス電圧用レギュレータ(LM317LZ)です。
|
|
組立が終わった基板。 前の物と同じ定型サイズの基板ですが、実装面積がぐんと増えました。 特に電解コンデンサは容積大にも繋がっています。
|
|
|
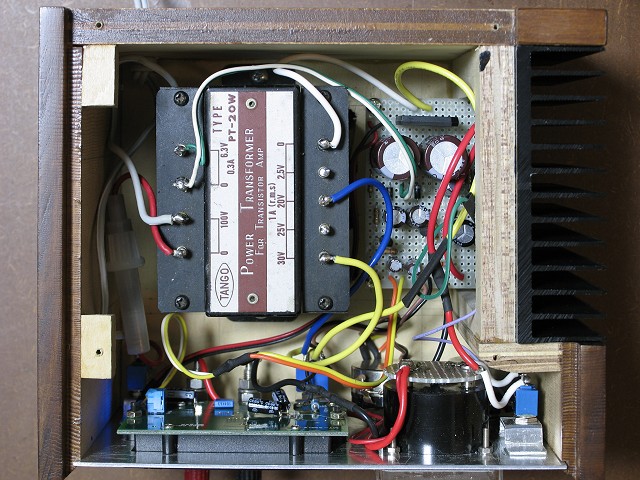 |
|
|
基板サイズは全く同じですから固定は容易です。 フィルターコンデンサが大きくなったのが良く判ります。
|
|
|
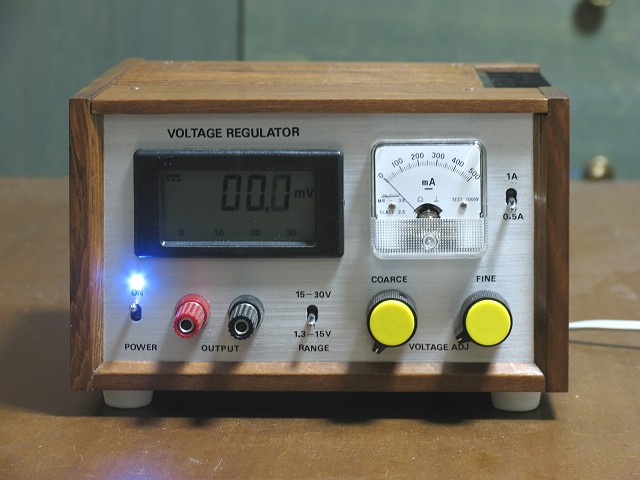 |
|
|
COARCE(粗調)は左に回し切りでFINE(微調)が左に回し切りから少し右へ回した所で0V出力となります。
|
|
|
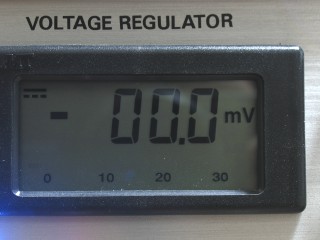 |
|
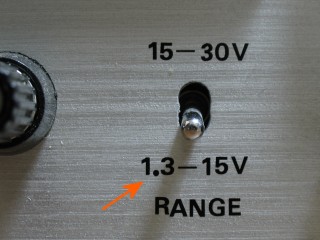 |
|
|
デジタル電圧計は時に"-00.0mV"などと奇妙な表示をします。
|
|
唯一フロントパネルの文字を[1.3-15V]から[0-15V]に修正できないのが残念です
|
|
|
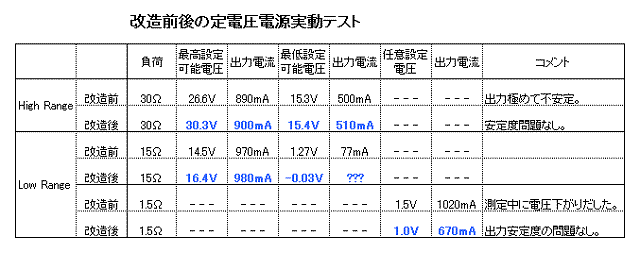 |
|
|
改造後の改善の度合いを見るべく簡単なテストをしました。 High Rangeではフィルターコンデンサ強化(容量アップ)だけが性能に影響する変更ですが、900mAを取り出しながら設定可能な最高出力電圧が30.3Vと3.7Vも増加し名実共に30V出力と言えるようになりました。 スライダックでAC電圧を上昇させて!なんてことが不要になりました。
またLow RangeではReference電圧(+1.25V)をキャンセルすることで0V出力を得たため、設定電圧は全体的に1.25V下がっている筈ですが、設定可能最高電圧は16.4Vと改造前より1.9Vアップしています。 この結果Low Rangeの電圧設定は0V-16.4V、High Rangeでは15.4V-30.3Vとうまくオーバーラップしています。(以前は例えば15Vの設定はHigh、Low何れのレンジでも設定できなかった。)
|
|
Copyright (C) 2001-2019, Vic Ohashi All rights reserved.