先ず自動シャットダウン回路の調整抵抗は10KΩと1.5kΩを直列に繋いだ11.5KΩとなりました。 入力電圧の変化で各部がどうなったかは一覧表を後ほどお見せしますが、これにより入力電圧の下限は5.6Vになりました。 電池1本辺り0.9Vを下限とするなら5.4Vになるのですが、ニッケル水素電池を使用する場合には下限を1Vとするのが標準のようですので6本分の6.0Vに少し接近させてやることにしました。
(以前ニッケル水素電池は使わない!としていましたが、「場合によっては使うこともあり得る!」とアルカリ乾電池を優先としながらも考え方を少し変更しています。)
また基準電圧についてはE101に置き換え2.4Vとしています。 DC-DCコンバーターの出力電圧は調整無しで30.2Vありました。 そして9本のLEDを直列にした時のVfトータルは26.4Vとなりその差3.8Vは定電流動作範囲に入っているため、出力電圧アップの調整抵抗は追加しませんでした。 但し何らかの都合で電圧調整が必要なことが起こりうるので、追加出来るスペースは確保してあります。
調整が完了し新LEDテストの時に使ったLED基板を接続してテストした状態での各部の動作電圧は次の通りです。
|
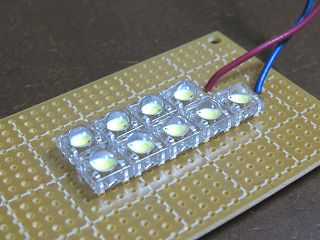 |
|
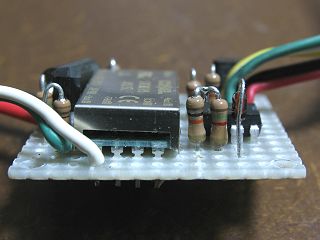 |
|
|
LED基板は過日新型LEDのテストをした時の基板に1個追加した状態で仮に実験しています。
|
|
完成したLED駆動回路基板。 高さは12.5mmほどあり、15mmのスペーサーを介してLED基板と連結します。
|
|
|
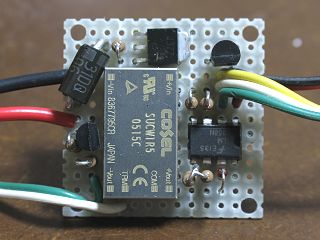 |
|
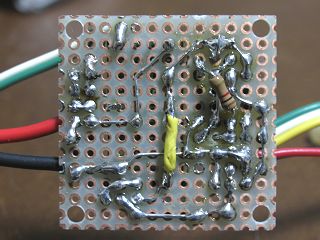 |
|
|
それを真上から見たところ。 一番大きな四角い物がDC-DCコンバーターです。
|
|
裏側の配線の様子。 一部半田付けをやり直した部分もあり大変汚らしい感じになってしまいましたが、電気的には問題無しです。
|
|
|
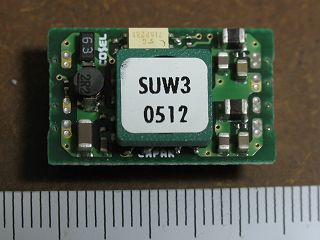 |
|
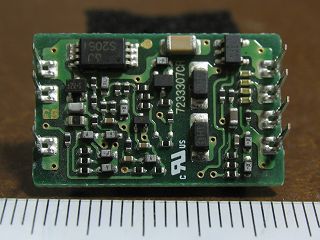 |
|
|
参考までに心臓部のDC-DCコンバーターをお見せします。 これは今回使ったものより1ランク上の容量の物です。
|
|
その裏面ですが実装密度が高く、とても手半田では作れそうに思えません。 自作をあきらめている所以です。
|
|
|
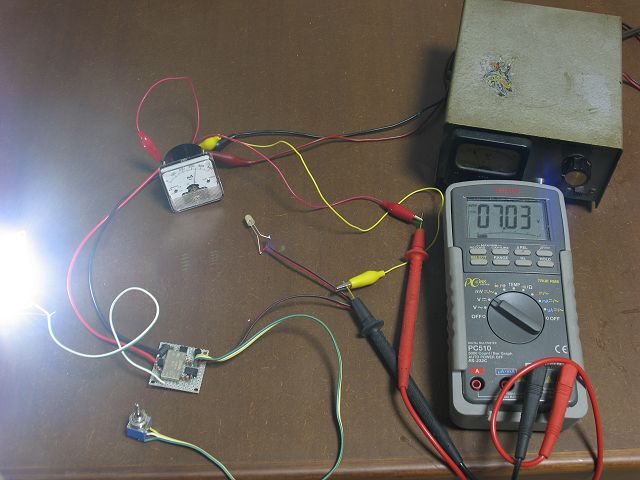 |
|
|
動作テスト風景。 右上が駆動する電池の替わりに使った自作定電圧電源で、1.25Vから32Vまで電圧を可変できます。 現在7.03Vの電源電圧です。 尚LEDの明るさは全電圧域で軸上1m離れて約100ルクスと計算どおりでした。
|
|
|
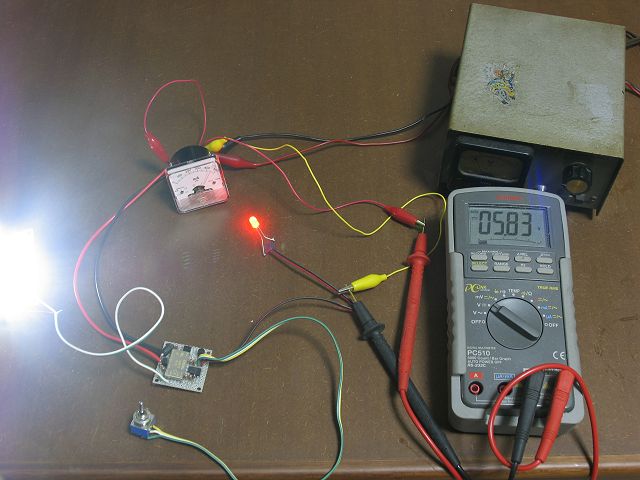 |
|
|
電源電圧が5.83Vまで低下し点滅LEDが点灯しています。 これが更に5.6Vまで下がるとシャットダウンされてLEDは消灯します。 左上の電流計の針は上限の500mAにかなり近く振れているのが判るでしょうか?
|
|
引き続きアルカリ乾電池を使った連続駆動テストをいたしました。 LEDは最終基板に固定した物ではありませんが、ここで何らかの違いが出るとは考えにくいので、このテストでの結果を見て最終的な評価を下すことにします。
|
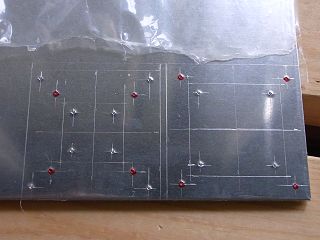 |
|
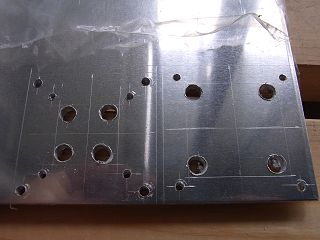 |
|
|
アルミ板にセンターポンチ(mini-Shopで販売しているハンディーポンチ S)で切断線や穴位置をけがき、センターポンチを打ち込みました。 赤くなっているのは2.5mmの穴をあけるというしるしです。
|
|
3種類の穴(2.5、3.2、6.0mm)の穴をあけ終わりました。 2.5mmは雌ネジを切るための下穴、3.2mmはM3ボルト用バカ穴、6.0mmはジグソーで切断するためにブレードを挿しこむ穴です。
|
|
|
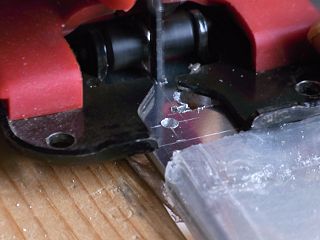 |
|
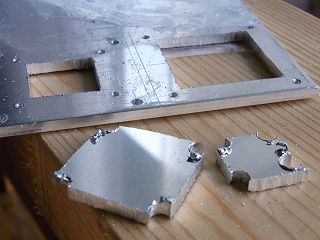 |
|
|
CJ-250にNo.5のブレードを取り付けて切断中。 電動ジグソーにとっては過負荷の状態となるので、オーバーヒートにならないよう連続運転は5分程度に留めて暫し温度が下がるよう休憩しました。
|
|
切断終了後です。 4mm厚アルミの切断は容易とは言えませんが、注意してやれば工具を壊すことなく実現できます。(メーカー保証外の使い方ですが?)
|
|
|
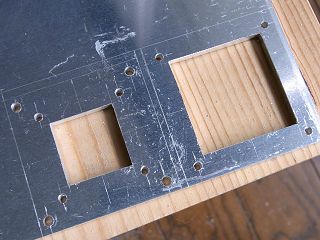 |
|
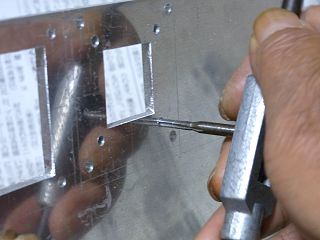 |
|
|
切断面をヤスリで研磨して仕上ました。 電動ジグソーでけびき線の外側0.2mm辺りで切断したため、意外に研磨作業は簡単に終わりました。
|
|
8箇所にM3の雌ネジを切っています。 手に感じる負荷状態次第でタップを少し逆回転してから更に切り込むなど注意しないとタップは簡単に折れます。
|
|
|
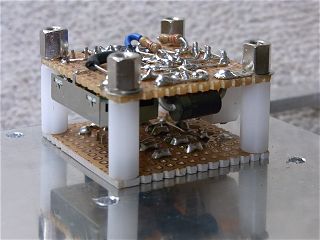 |
|
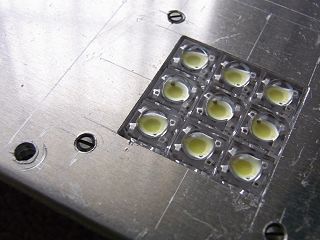 |
|
|
雌ネジを切り終った小さい方のアルミ板に加工精度の確認のためLEDブロックを仮固定してみた。 問題なく取り付けられたので、穴の位置精度は±0.1mm程度にはなっているようです。
|
|
これは表側。 ネジにはM3の俗称芋ネジを使用。 ちょっぴり複雑ですがこうしないと後で分解ができなくなります。 LEDが嵌りこむ穴も大きからず小さからずドンピシャサイズです。
|
|
|
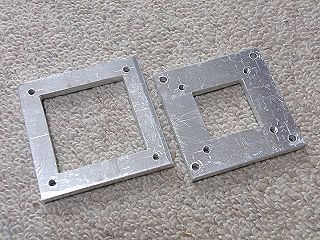 |
|
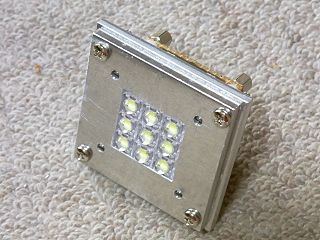 |
|
|
内部の加工が終わりましたので再びジグソーで切断し所要の寸法に研磨して2つのパネルが出来上がりました。
|
|
それらをもう一度確認のために組み上げていますが、最終的にはこの上に木製のスペーサーと3mm厚PET板が更に追加されます。
|
|
|
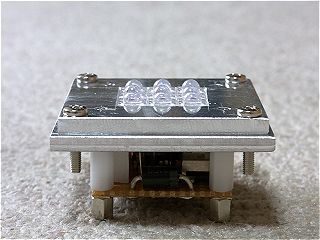 |
|
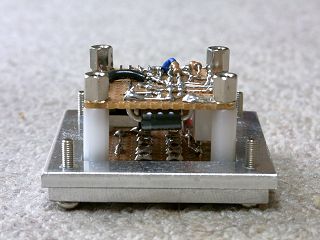 |
|
|
下の大きなアルミ板は実際には本体に埋め込まれます。 そこへ上のアルミパネルに取り付けられたLEDランプユニットがネジ止めされます。
|
|
この上には電池受けの板がネジ止めされますが、それはこのLEDランプユニットを本体に固定した後になります。
|
|
|
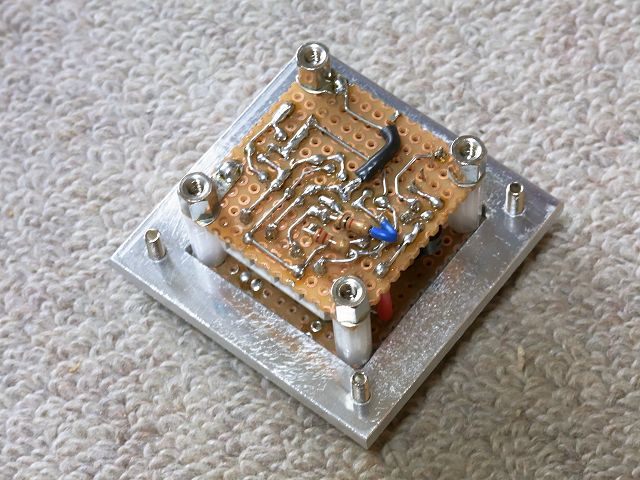 |
|
|
加工寸法精度は±0.1mmで仕上られましたが、穴位置は±0.2mm程のずれが出来てしまい多少の力技が組み立てには必要ですが、何とか使える状態になっています。
|
|
|
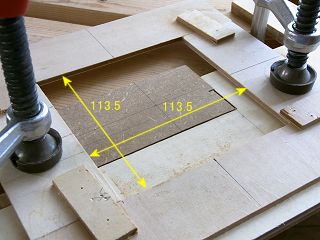 |
|
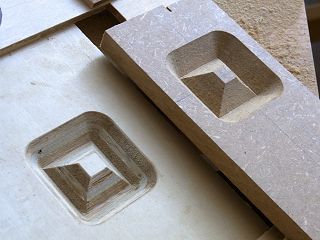 |
|
|
23.5mm四方の窓を切削するには電動トリマーのベースの幅(90mm)を加算した113.5mm四方の枠を作りガイド板とします。 この寸法精度は出来上がる窓の大きさの誤差に直結します。
|
|
後処理の塗装でどちらが良いか判らないので、MDFとシナ合板の両方で作り後ほど良好な物を採用することにしました。 彫り深さを8mmとしましたので、底部分をカッターナイフで切り込みます。
|
|
|
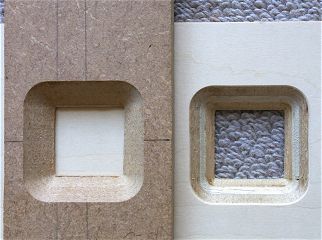 |
|
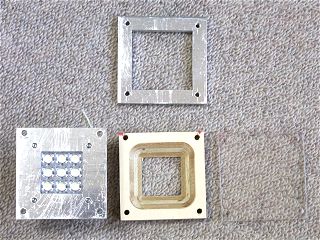 |
|
|
カッターナイフで切り落とした状態です。 成形研磨をする必要がありますが、その前に穴あけと外回りの切断を現物合わせでやります。
|
|
木のスペーサーが出来た後は最前面の板を3mm厚PET板を切断して作りました。 下の3枚を重ねて3mmのネジで上の枠(本体に埋め込まれる。)に共締めします。
|
|
|
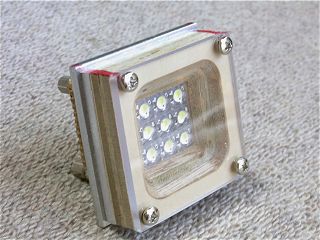 |
|
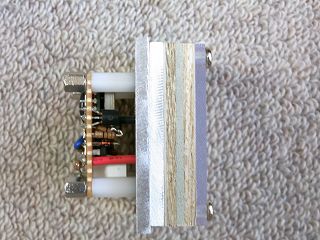 |
|
|
M3のボルトで本体枠に共締めしたところです。 3mm厚PET板はかなりの衝撃に耐えられると思います。
|
|
それを真横から見たところです。 前面から挿入するLEDランプユニットとしてはこれで一応完成です。
|
|
|
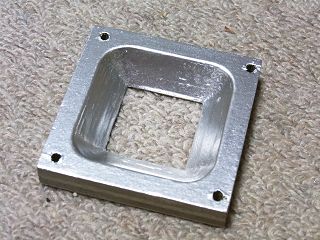 |
|
 |
|
|
再びばらして木製スペーサーの内面をメッキ調スプレー塗料で塗りました。 下地はサンディングシーラー3回塗りですが、塗装面の平坦度は完璧から程遠いです。
|
|
メッキ調の塗装が完全乾燥後に組み上げて確認しました。 面白いものでなんとなくそれらしくなってきたように見えます。
|
|
|
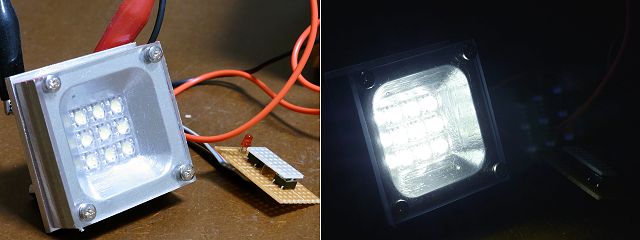 |
|
|
木製スペーサーのメッキ調塗装をした面の反射の具合を確認しました。 LEDの真横に出る光りはかなり光量が落ちるので(メーカー発表のデータでは真横の光量は軸上に対して1.5%程度しかない。)反射光の量はあまりありませんが、それでも光る面積は拡大しますから、外観上の押し出しと言うか見栄えが良くなった様に思われます。
|
|
|
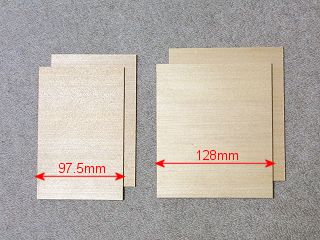 |
|
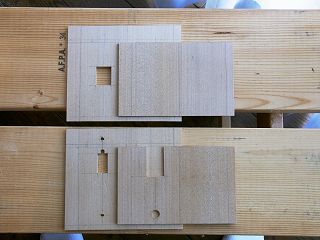 |
|
|
左は3mm厚の内張りの板、右は5mm厚の外側となる板で何れも幅は150mmあり1枚で2面を切り出します。 長さの寸法精度は0.2mm以下に、また正確な直角度が重要です。
|
|
3枚の板の予備加工をしました。 左上は5mm厚の底になる部分に三脚固定ネジ板を嵌め込む穴、左下は5mm厚上板に取っ手固定の穴と電源スイッチ基板が出る部分をあけています。 右下は電源スイッチ基板を落としこむ切り欠きです。
|
|
|
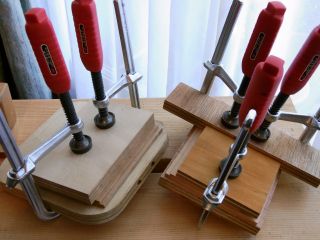 |
|
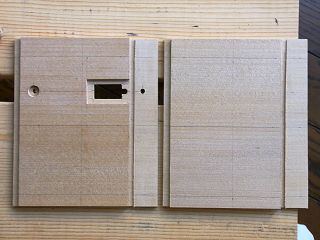 |
|
|
3mmと5mmの板を木工ボンドで貼り合わせ圧着保持をしています。 圧着保持が大袈裟なように思えますが、面積のある接着時には単位面積あたりの圧着力確保のため大きな力を加えないとなりません。
|
|
6時間寝かせて完全硬化させた2枚の板ですが、この後電動トリマーによる切削加工の手始めとして4mm幅、深さ2mmの溝を右手に彫っています。 ここにアルミ板が埋め込まれます。
|
|
|
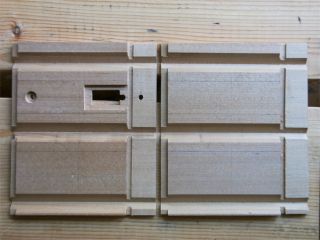 |
|
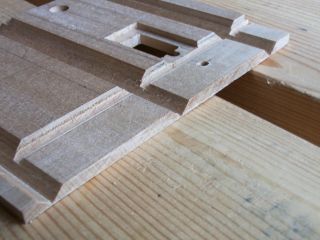 |
|
|
次にV溝ビット(VB-90G)で接着部分を切削しました。 V溝とV溝の間隔は本体の幅になります。 彫りの深さは板厚(8mm)に対して7.7-7.8mmの深さですので、ばらばらにならないよう裏にはマスキングテープを貼っています。
|
|
斜めから見た様子。 両端の幅の狭い部分は組み立て前に取り除きます。
|
|
|
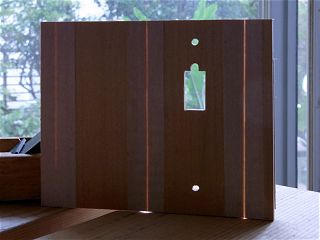 |
|
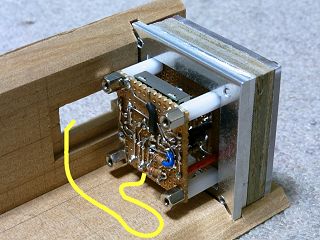 |
|
|
立てて裏から透かしてみると切削した谷の先端部分が判ります。 切り離さないようにぎりぎりの深さに切削するのが肝要です。
|
|
加工が済んだ本体の部材にLEDランプユニットを嵌め込んで電源基板からの配線の収まりを確認したのですが、こんな具合にうまく収まりません。
|
|
|
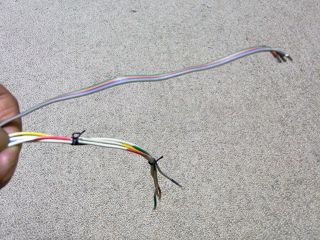 |
|
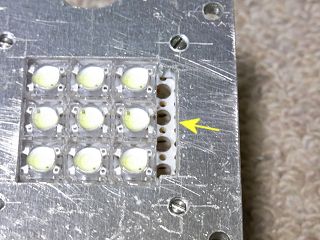 |
|
|
対応策として考えたワイヤーの違い。 同じ長さのワイヤーですがこれまで使ってきた上のビニール線は自重で垂れ下がることなく硬く、替わりに使う特殊なワイヤーはこのように自重で垂れ下がる十分な柔らかさがあります。
|
|
またワイヤーを端子に固定するためにはドライバーが挿入できないとまずいので、アルミ板のこの部分を削り取りました。
|
|
|
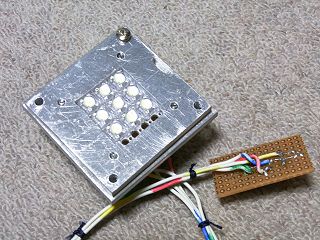 |
|
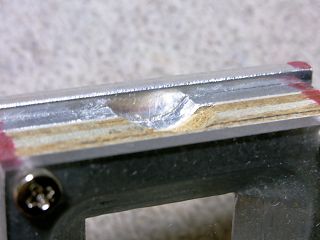 |
|
|
電源スイッチ基板と本体を繋ぐワイヤーも交換し終わりました。 4本のバラのワイヤーですので数センチおきに糸で縛りバラケ防止としています。
|
|
取っ手固定のネジの頭に当たる部分を削り込んでいます。 板のスペーサーは一部の削る込みで済みますので組み上げ後にこれらの削りこみは見えません。
|
|
|
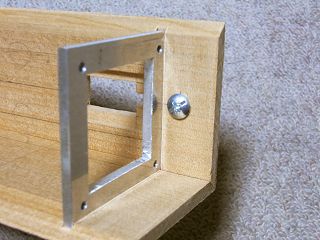 |
|
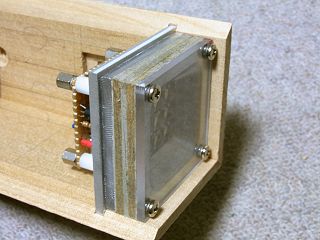 |
|
|
完全に組み上げると判りにくくなるのでお見せしておきます。 LEDランプユニットを挿入する前はこんな具合で、M4のネジの頭が出っぱっています。
|
|
上の写真の欠き取りのためにネジの頭が邪魔することなくLEDランプユニットは挿入できます。 またその欠き取りは挿入後見えません。
|
|
|
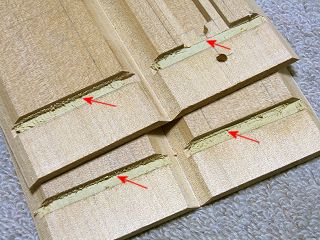 |
|
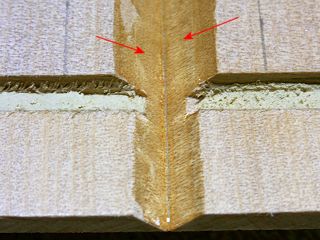 |
|
|
組み上げ作業の1番目はウッドエポキシをアルミ板を嵌め込む溝に塗りつけます。 結果的にはこれでは多すぎて組み立て時にかなり削り取っています。
|
|
2番目はエポキシ接着剤を45度切削面に塗りつけです。 落ち着いて作業が出来るよう60分硬化開始型を使っています。 決して慌てずに進めることが肝要です。
|
|
|
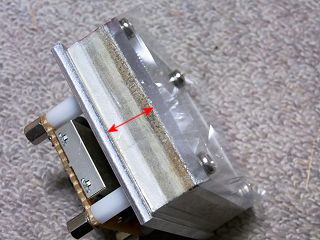 |
|
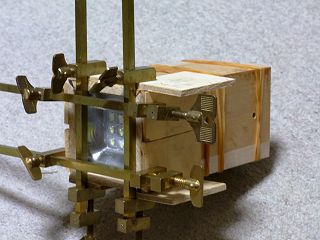 |
|
|
埋め込むアルミ板が正しく収まるようLEDランプユニットを取り付けて埋め込みますが、LEDランプユニットに接着剤が付く恐れがあるので、矢印の部分一周は薄いポリエチレンシートで包みました。
|
|
そして接着して圧着保持です。 前面は溝にアルミ板を埋め込むのにかなりの力がいるためハタ金を使っています。 中ほどから後ろは太いゴム輪を使っています。 これで12時間放置しますが、6時間後にLEDランプユニットは引き抜きました。
|
|
|
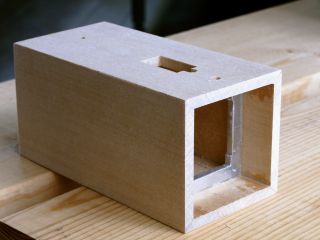 |
|
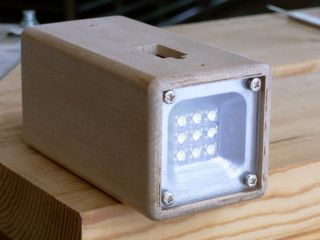 |
|
|
表面にエポキシ接着剤がくっついておりこれは着色が出来ず斑になりますので、寸法出しも兼ねて#60、#120で研磨し完全にそれらを落としました。
|
|
ボーズ面ビットで全ての角を丸く切削しその後#240、#400サンドペーパーで仕上研磨しました。 確認のためにLEDランプユニットを取り付けています。
|
|
|
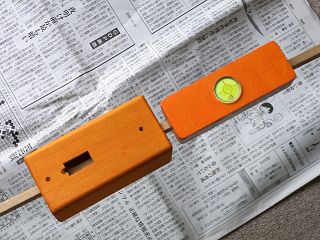 |
|
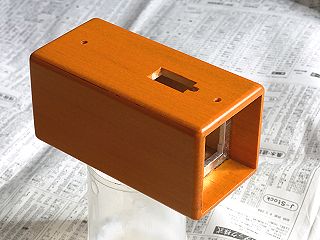 |
|
|
着色はポアステインのオレンジと黄色を等量混合としました。 右側は以前作った水準器で、シナの上にオレンジのみの着色ですが、アガチスは茶色っぽい表面なので右のシナ合板より暗めになります。 但し黄色が強い色味です。
|
|
水性ウレタンニス透明クリヤーを4回塗り肉厚を稼いだ上で艶消しクリヤー1回塗りです。 私の最近の標準仕様で間の研磨には空研ぎペーパー#400-#600を使っています。 但し丸みのある部分は極極細目のスポンジ研磨剤です。
|
|
|
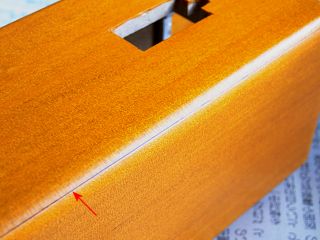 |
|
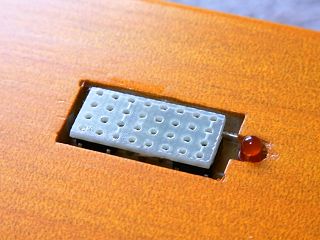 |
|
|
ここに見える黒い線は接合部分です。 これは接着時の圧着保持力が不十分であるために発生するものです。 エポキシ接着剤は充填効果が高いので問題無しとしますが、木工ボンドですと接着力が十分にならないでしょう。
|
|
電源スイッチ基板を本体裏側からエポキシ接着剤で固定しました。 中央のスイッチ板が乗る部分は本体の面と同一の高さにあります。
|
|
|
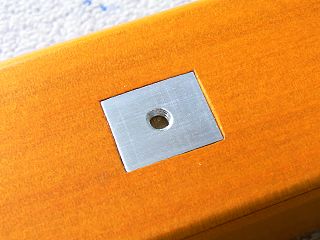 |
|
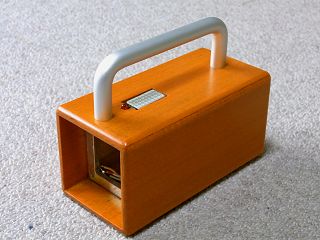 |
|
|
3脚に固定するネジ穴は5mm厚アルミ板を切断し1/4インチタップで切りました。 そして5mm厚板部分の抜き穴に挿入しエポキシ接着剤で固定しています。
|
|
M4のトラスネジを12mmの長さに切断し、アルミハンドル(取っ手)を固定しました。 何かハンドルが大き過ぎるように見えますが、本体が小さ過ぎると言った方が正しいでしょう。
|
|
|
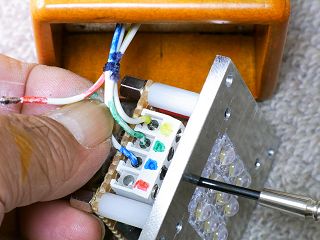 |
|
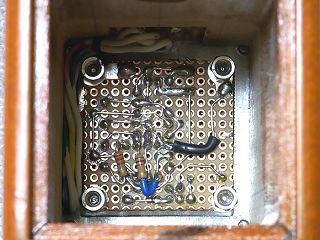 |
|
|
電源スイッチ基板からのワイヤーを接続操作できる範囲で短く切断し、LEDランプユニットに配線しました。 そして本体に取り付けます。
|
|
取り付け後裏側から見るとこんな具合です。 4本のワイヤーの束はふにゃふにゃですから、このようにLEDランプブロックの横にうまく収まります。
|
|
|
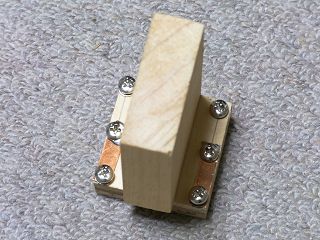 |
|
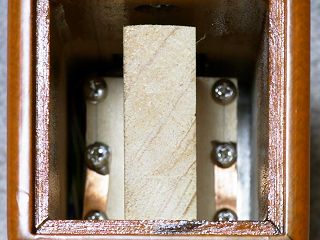 |
|
|
前側の電池受けは15mm厚と12mm厚の板から作ります。 6本の真鍮バインドネジの頭が電池の電極と接触します。 赤く見えるのはネジとネジを電気的に繋ぐ銅板です。
|
|
角にある4本のネジでLEDランプブロックに固定しました。 中央の板の上に3mm強の隙間がありますがその理由は後ほど。
|
|
|
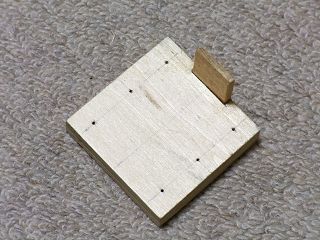 |
|
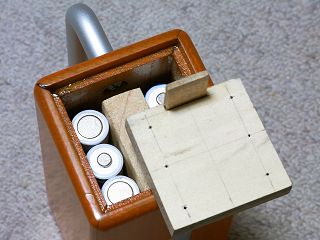 |
|
|
後ろ側の電池押さえの板です。 0.5mmの小さな穴が4箇所あいています。 また上には変な突起をつけています。
|
|
前に触れた隙間と変な突起の関係。 この隙間に変な突起を差し込むようにして蓋をします。 電池受けの電極には方向性があるためです。
|
|
|
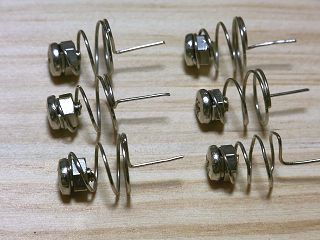 |
|
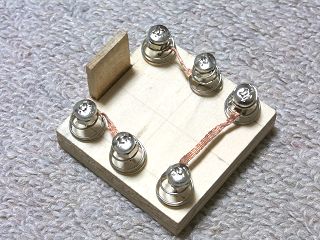 |
|
|
後ろ側の電池に接触する部分もM3バインドネジですが、円錐型のバネの先端にネジ止めしています。 そしてバネの底部分中央には12mm程の突起になっています。
|
|
バネ中央の突起を電池押さえ板の穴に差込みますが、ネジの先端に配線を施しておきます。 線材は柔らかな半田吸い取りワイヤーを使いました。
|
|
|
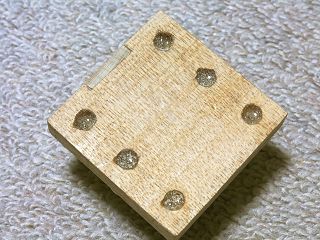 |
|
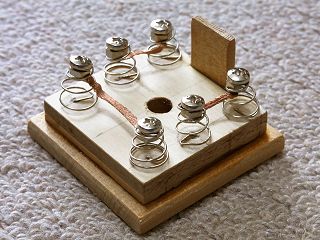 |
|
|
差し込んだ反対側は5mmの穴になっており、スプリングの先端を曲げた上でエポキシ接着剤を流し込み固定しました。
|
|
そして蓋となる5mm厚のアガチスを貼り付けて後ろ側の電池押さえブロックは出来上がりです。
|
|
|
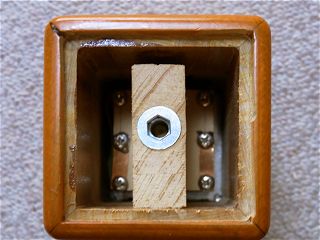 |
|
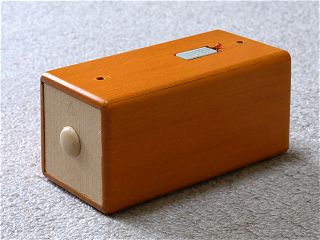 |
|
|
後ろ側の電池押さえブロック(蓋)を固定するためにM6 12mmの鬼目ナットを埋め込みました。
|
|
電池押さえブロック(蓋)の中央に穴を開けてセットキャップボルト(M6 26mm)でネジ止めし更にセットキャップカバーを被せました。 後は蓋の部分の塗装です。
|
|
|
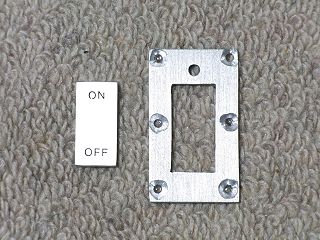 |
|
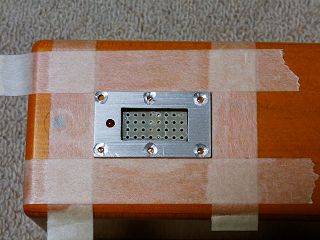 |
|
|
スイッチ押し板とその周りのプレートは1.5mm厚アルミ板から作りました。 スイッチ押し板には文字入れしてあります。
|
|
周りのプレートを固定する位置が定まったらマスキングテープでその周りを覆ってしまいます。
|
|
|
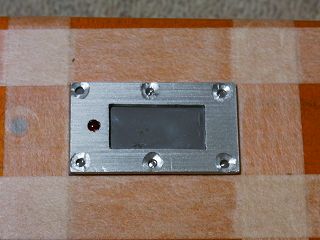 |
|
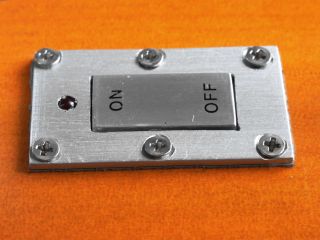 |
|
|
周りのプレートの下に0.5mm厚ゴムシートを置き位置決めをしてネジ止めします。 (中央灰色がゴムシートです。)
|
|
スイッチ押し板の裏面に両面接着テープを貼りつけてゴムシートの上に貼り付けて電源スイッチ部分は完成。 左のLEDの周りには瞬間接着剤を流し込みます。
|
|
|
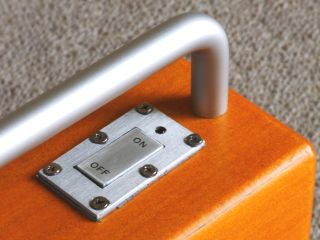 |
|
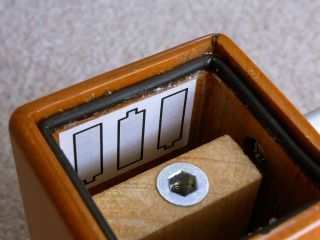 |
|
|
上方斜めから見た様子。 スイッチ押し板のヘアーラインは周りのプレートより目が細かいのでコントラストがあり、まずまずの感じに仕上がったと思います。
|
|
本体背面の内側には電池の極性を示す図を貼り付け、水侵入防止の柔らかなゴム紐を貼り付けました。 これで全ての作業が終了しました。
|
|
|
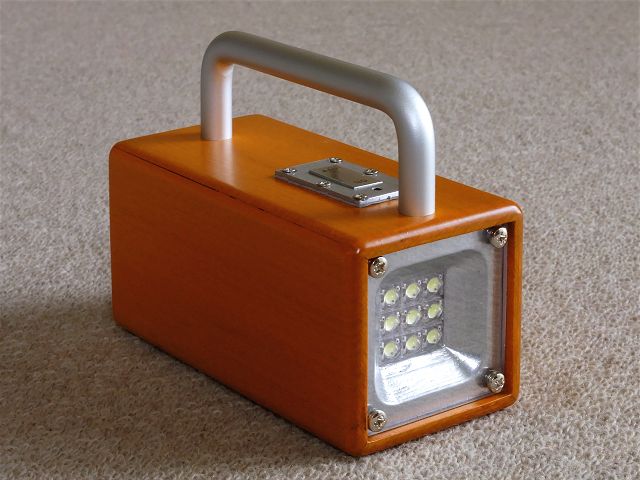 |
|
|
完成したLEDフラッシュライト。 正直言ってけちを付け出したら果てしの無いくらい細かな工作ミスの個所がありますが、実用性、耐久性、信頼性という点で十分耐えられる物に仕上がったと思います。
|
|
|
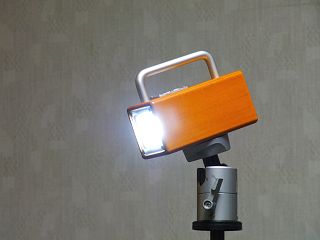 |
|
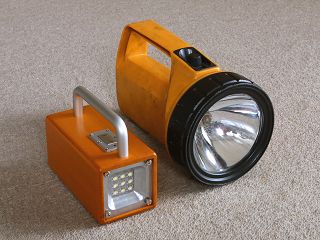 |
|
|
三脚に固定できますからこのように写真撮影の補助光源として有効に使えます。 綺麗な白色ですから変な色付きを起こすこともなく快適です。
|
|
古い大型フラッシュライトとのツーショット。 計算上はこれよりも4-5倍の光量がありながら5.7時間光量低下無しに点灯(エネループ使用時)と、『山椒は小粒でもピリリと辛い!』そのものです。
|
|
最後にこのLEDフラッシュライトの仕様をもう一度紹介しておきましょう。Copyright (C) 2001-2019, Vic Ohashi All rights reserved.