|
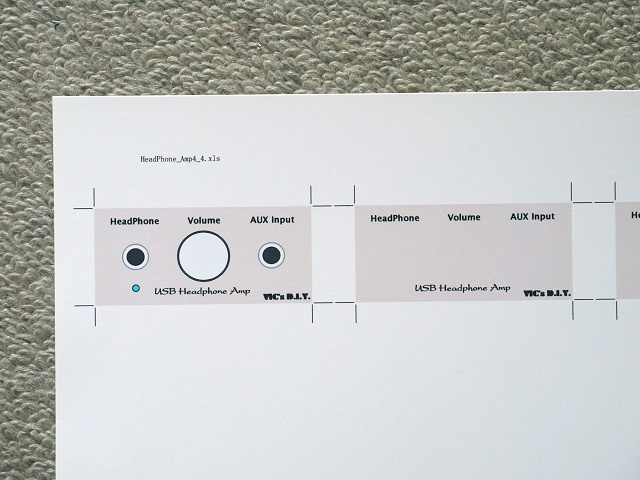 |
|
|
Exceに描画したフロントパネルを薄いマット紙に印刷しました。 写真の左側はミニフォーンジャックやボリュームツマミを取り付けた状態を確認するため描き込んでいますが、フロントパネルに実際に貼り付けるのは右側のそれらを消し去ったものです。
|
|
|
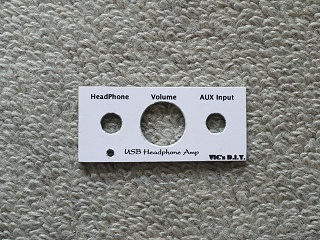 |
|
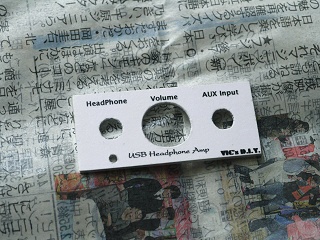 |
|
|
フロントパネルに両面接着テープを使って貼り付けた後、4つの穴を先が細く尖ったカッターナイフによる押し切りで切り抜きました。 押し切りは少しずつ進めます。
| |
そして紙部分の汚れ防止と保護の目的で、透明クリヤー、つや消しクリヤーのスプレー塗料で各1回ずつ塗装します。
| |
|
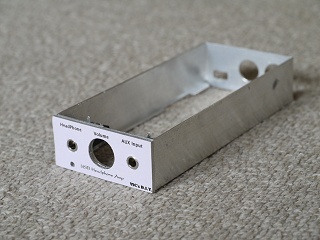 |
|
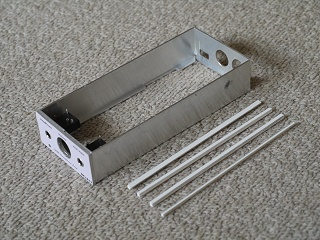 |
|
|
完全乾燥後にミニヘッドフォーンジャック2個で、フレームとフロントパネルを共締めしました。 締め付け位置関係をよく確認・調整しましたら緩み止めのために瞬間接着剤で完全固定しました。
| |
基板固定時のスペーサーを2mm厚発泡塩ビ板から切り出しました。 発泡塩ビ板は柔らかいのでカッターナイフで容易に切断が出来ます。 また良好な絶縁物質です。
| |
|
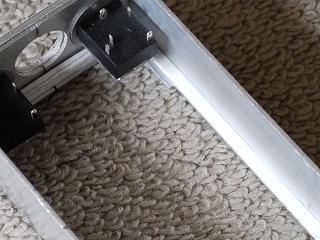 |
|
 |
|
|
フレーム内側の底にスペーサーを瞬間接着剤で貼り付けました。 スペーサーの厚みは2mmなので、2つの基板は2mm浮いて固定されることになります。
|
|
背面板とフレームを締結するネジ穴の加工。 フレームには厚さ1.5mmで15 x 11mmのアルミ板を貼り付け2.5mmの穴をあけてからM3のネジを切り、背面板には3.5φのあなをあけます。
|
|
|
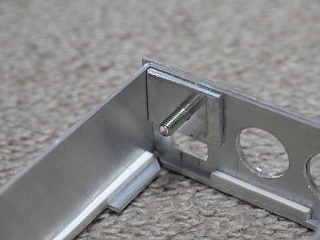 |
|
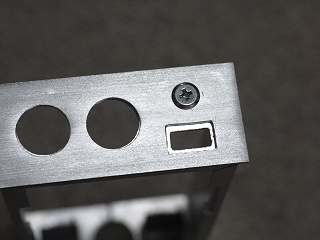 |
|
|
背面板にM3のネジを通しフレームに捻じ込んで固定しました。 このネジは10mmと長すぎるので後程5mm位に切断します。
|
|
USBコネクターが背面板に干渉するのが判りましたので、背面板の穴を6 x 10mmに拡大しました。
|
|
|
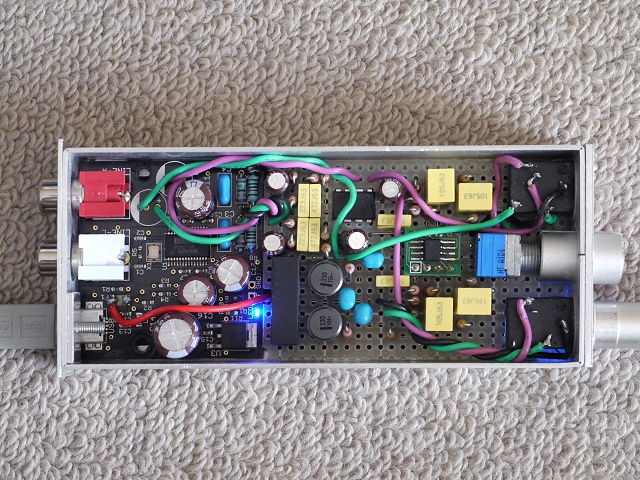 |
|
|
十分に点検を済ませましたので、フレーム内に2つの基板を瞬間接着剤で固定しミニヘッドフォーンジャックへの配線を最終的なものとしてツマミも取り付け本体は完成しました。 早速ノートブックに繋いで動作確認しています。
| |
|
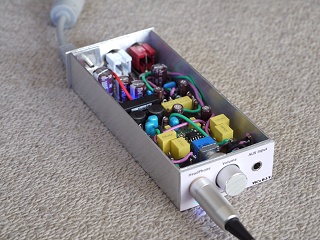 |
|
 |
|
|
前方より見た様子です。 このヘッドフォーンアンプはUSB端子が持つ5V電源を当てにしていますから音楽源もUSBとなることが多く、前面右側のAUX入力ジャックを使うことは稀でしょう。
|
|
背面の様子です。 右側はUSBのケーブルでパソコンに繋がれますが、RCAピンジャックからの出力はこのヘッドフォンアンプがUSBオーディオアダプターとなり大変便利に使えます。
|
|
|
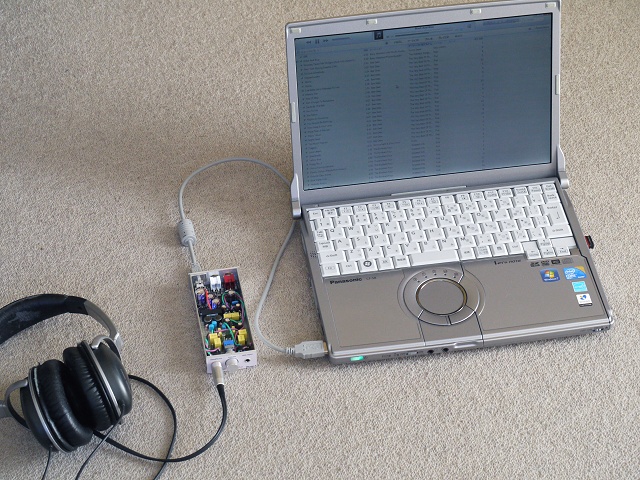 |
|
|
愛用のノートブックに接続し、iTunesで音楽を楽しんでいます。 このヘッドフォーンアンプの主たる使い方になります。
| |
|
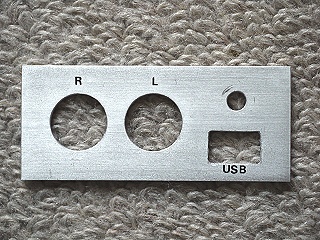 |
|
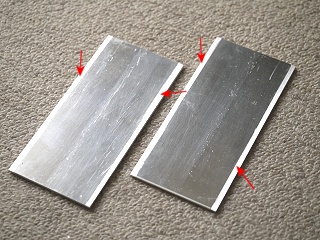 |
|
|
一番小さなFontはインスタントレタリングがまだ残っているので、それを使って背面板に文字入れし、透明クリヤーとつや消しクリヤーのスプレー塗料で仕上げました。
| |
天板と底板の切り出しは±0.05〜0.1mmの寸法誤差となるようヤスリで削りながらノギスで何度も確認しながら仕上げました。 また側板を接着する部分は接着強度を高めるため、#120ペーパーで研摩しています。(矢印の先の部分。)
| |
|
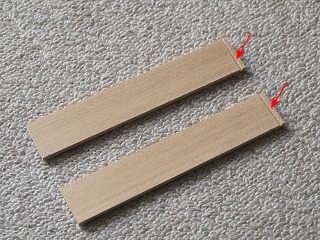 |
|
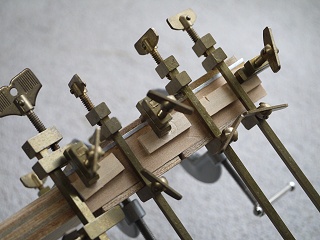 |
|
|
2枚の側板は背面板を落とし込む深さ1mmの溝をトリマーで切削後(赤矢印部分)に少し大きめに切り出し、カンナと替刃式ヤスリで±0.05〜0.1mmの寸法誤差となるよう仕上げています。
| |
底板と左側の側板をエポキシ接着剤で貼り合わせ、クランプとハタ金合計9本で圧着保持しています。 大袈裟なようですが寸法精度を高く保ちながら密着度を高めるために不可欠です。 尚室温が低くなってきていますので完全硬化のために12時間と長めに放置します。
| |
|
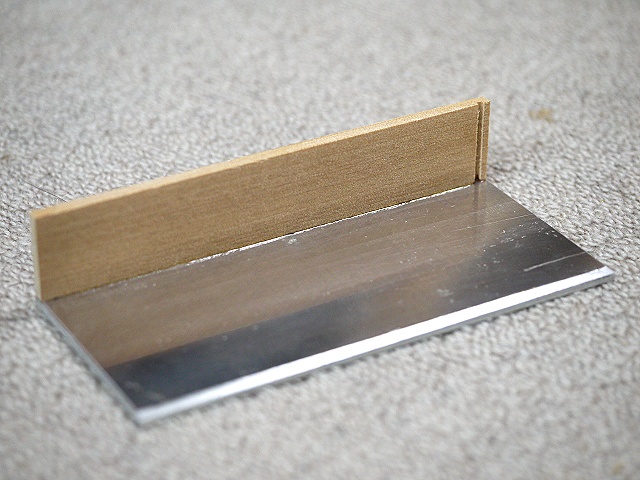 |
|
|
接着後12時間寝かせてからクランプを外しました。 右端に見えるアルミ板に映った側板の反射を見ると接着時の直角度がかなり正確であることが判るのですが、隅に沿って白く光っている部分が若干問題です。
|
|
|
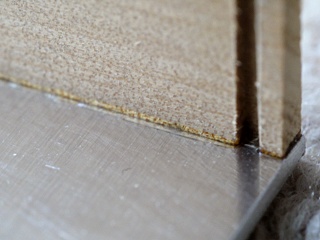 |
|
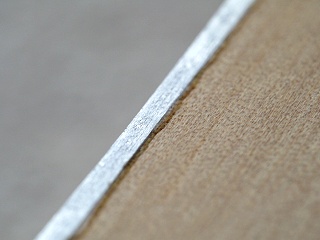 |
|
|
隅に沿って光っていた部分は滲み出た接着剤です。 このままにしておくとヘッドフォーンアンプ本体がスムーズに出し入れできませんのでヤスリで削り落とします。
| |
表面の接着部分にも接着剤が滲み出ていますが、これは最後の仕上げ研摩で落とします。
| |
|
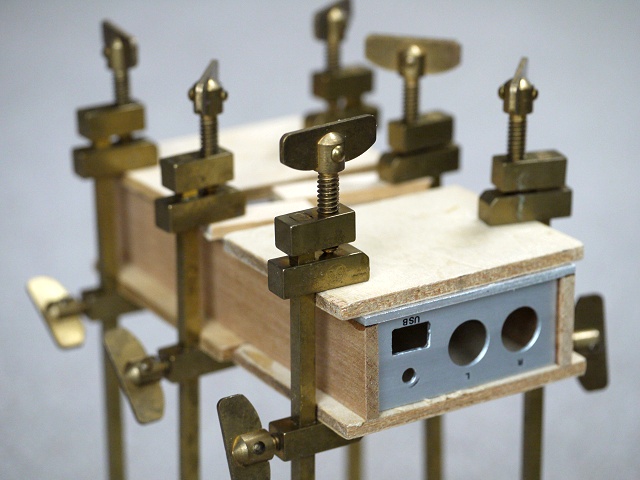 |
|
|
接着工程の第二段はもう一枚の側板と背面板をL型に接着し終わった部分への接着です。 これはハタ金で圧着保持中の写真ですが、アンプ本体を挿し込んで位置関係を確認してハタ金で軽く締め上げ、その後アンプ本体を引き抜いて本締めしています。
|
|
|
 |
|
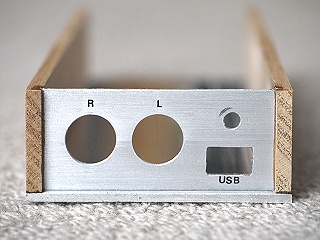 |
|
|
12時間放置後にハタ金を外しました。 コの字型になって後ろ側が塞がった状態です。
| |
その背面はこんな具合です。 仕上げ研摩をするとこんな大雑把な雰囲気ではなくなる筈です。
| |
|
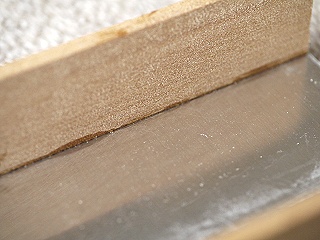 |
|
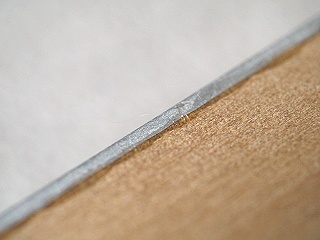 |
|
|
内側の接着剤のはみ出し具合。 強い光の反射がないので暗い部分がはみ出た部分で、無論これは削ります。
| |
外側のはみ出た部分はこんな具合ですが、これも後程仕上げ研摩の時に削り落とします。
| |
|
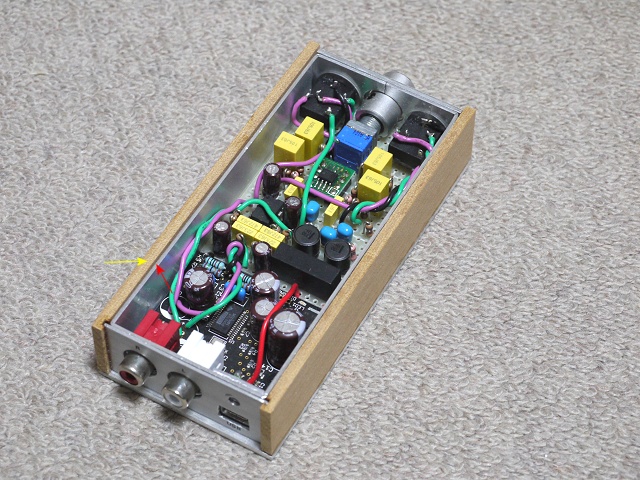 |
|
|
ヘッドフォーンアンプ本体をケースに落とし込んでみました。 側板の黄色矢印面はフレームの赤矢印面より高くないといけません。 そうなっていない時はフレームを削って高さを詰める調整をします。
|
|
|
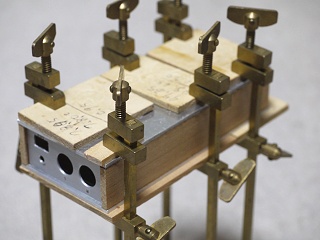 |
|
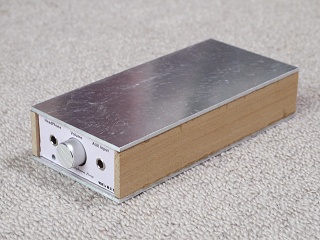 |
|
|
最後の接着ですが、アルミの天板を貼り付け12時間圧着保持しました。 ここでも接着剤の使用量はギリギリまで抑えてはみ出る量を少なくします。
| |
ケースの組み立てはこれで終了ですが、まだ側面の仕上げ研摩と天面、底面のヘヤーライン加工、面取り研摩が残っています。
| |
|
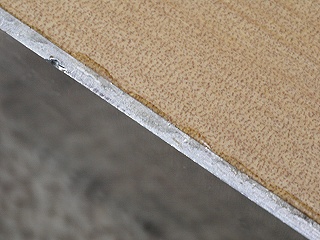 |
|
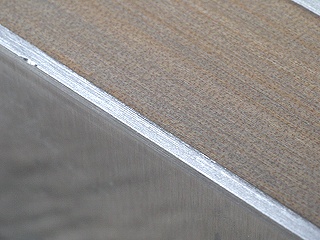 |
|
|
側面研摩の様子。 たまたま天板の角に傷をつけてしまいましたが(左上)、側面研摩と面取りの過程で消すことにします。 これは研磨前で接着剤がはみ出ています。
| |
木部の汚れは削られたアルミの粉によるものです。 左上の傷はかなり小さくなりました。 接着剤もかなり削り取られています。
| |
|
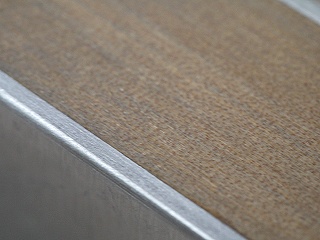 |
|
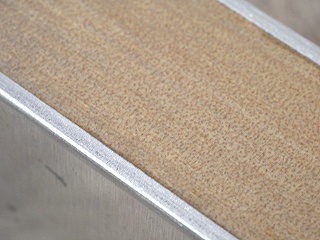 |
|
|
アルミ板の天板の角を削り落とし傷が完全に消えました。 また接着剤のはみ出た部分も完全に無くなっており、仕上げ研磨ほぼ完了の状態です。
| |
研磨面の汚れを落とすべく水洗いしました。 非常に細かなアルミ粉は若干残っていますが、次の着色作業でマスクされます。
| |
|
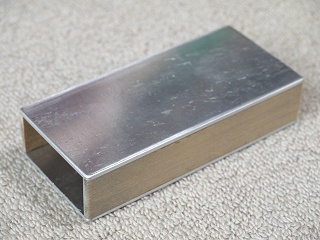 |
|
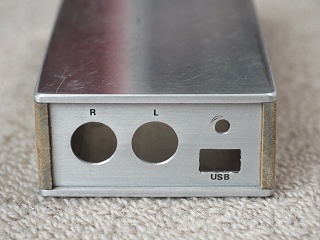 |
|
|
ヘヤーライン加工に入りますが、ヘヤーライン無しだとピリッとした感じが無く間が抜けて見えます。
| |
背面のクローズアップですが、間が抜けている感じが良く判ると思います。
| |
|
 |
|
|
ヘヤーライン加工については何度もお見せしてきているので、いきなり終了後の写真です。 今回は#120のサンドペーパーを使いました。 いうまでもなくキリッとしたシャープなイメージに変貌します。 この後の着色で更に質感が高まります。
|
|
塗装に関しては既に色々なテーマで紹介しているので仕様のみを紹介しておきます。 詳しくは