|
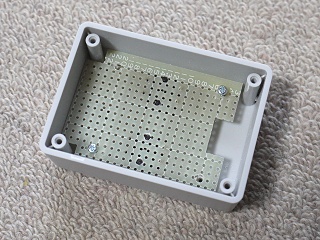 |
|
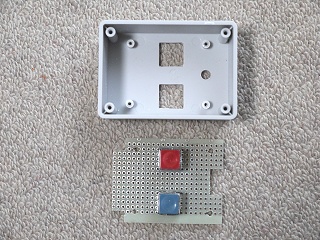 |
|
|
基板を所定のサイズ・形に切断し、タクトスイッチの位置決めピンの通る穴、基盤固定の穴などを慎重に加工しないとなりません。
|
|
次にタクトスイッチを仮止めしてつまみの出る穴、及びLEDの先が出る穴をあけます。
|
|
|
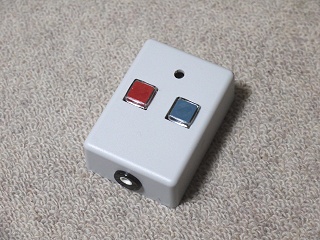 |
|
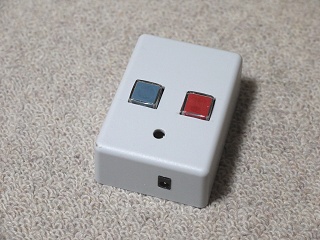 |
|
|
更にACアダプターが接続されるコネクター(12φ)の穴をあけて、
|
|
反対側に充電出力のDCコネクターが出る穴をあけてケースの加工が終了します。
|
|
|
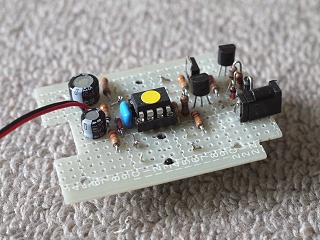 |
|
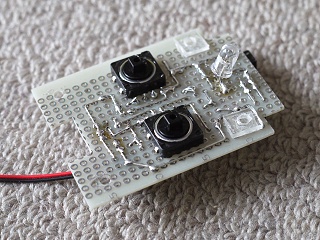 |
|
|
そしてひたすら配線となります。 基板は空いている場所が多そうですが、裏付けのタクトスイッチ、裏側の基板固定の厚み調整板などが結構場所を食っているためで、あまり楽な配線ではありません。
|
|
半田付け面ですが右側の上下に見えるのが基板取り付けの高さ調整のために貼った1.5mm厚のプラスチック板で、タクトスイッチのボタンが出過ぎるのを抑えます。
|
|
|
完成した基板の動作を一通り確認しました。 先に掲載した最後の配線図に記載した電圧はこの段階で測定した値です。
但し電池を接続して実際に充電してみたわけではなく、66Ωのダミー抵抗を繋いでここで充電末期に近い電圧降下を想
定しています。 充電回路の定電流値は74.9mAでほぼ設計値(75mA)です。
タイマー回路の動作電流はタイマー実験回路の場合には0.6mAでしたが、タイマー出力に1mA強の負荷が掛かるように
しましたので、タイマー回路全体の消費電流は1.7mAに上がりました。 更にツェナーダイオードに流れる電流が加算され
10.6mAが電源を含むタイマー回路の消費電流になります。
更に充電回路で75mAの充電電流に発光ダイオードに流れる電流(平均3.6mA)が加算されますので、充電時には89mA
の消費電流となります。(消費電力はACアダプターの効率は抜きにして0.8Wになりますので、ACアダプター込で1W位で
済むでしょう。) こんな結果より繋ぐ9V ACアダプターはゆとりを20%位見込むとしても出力電流が110mA以上あれば良い
ので、最も小型の物で十分です。
|
|
|
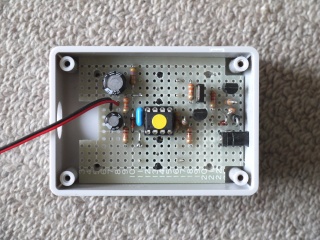 |
|
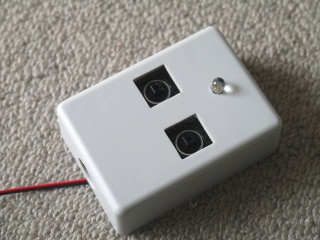 |
|
|
確認のためケースの収めました。 修理・調整のために基板を外すのは簡単にできます。
|
|
基板に固定されたLEDは軽く圧入されているだけです。 最終的には半透明のキャップを被せ視認性を高めます。
|
|
|
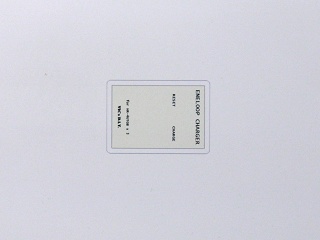 |
|
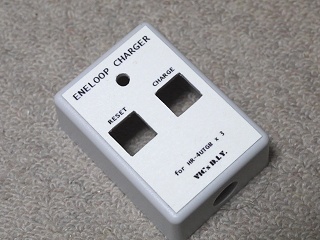 |
|
|
A4サイズ厚手のつや消しの用紙に文字をレイアウトして印刷します。
|
|
それを両面接着テープでケースに貼り付け、タクトスイッチボタン穴とLEDの飛び出る部分をカッターナイフで切り落とします。
|
|
|
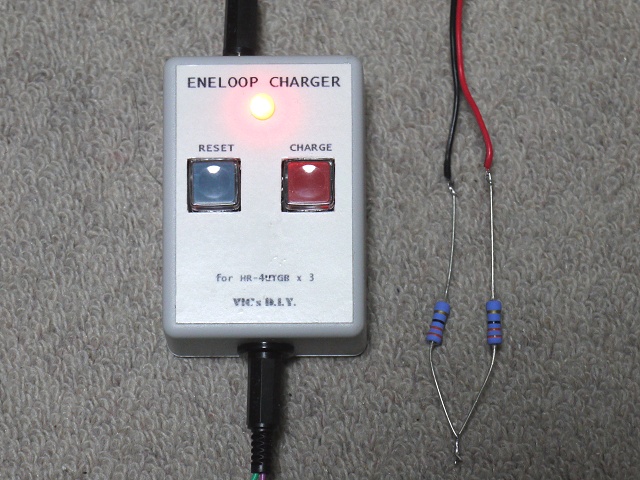 |
|
|
正式にケースに基板を組込み蓋をネジどめしました。 右に見えるのはダミーロードで、33Ωを2本シリーズに繋ぎ、充電終了近辺を模しています。 たまたま撮影時にLEDが点灯しましたが、1mA程度しか流れていない(点滅LED追加により3.6mA消費電流が増加していますが、そのうちツェナーダイオードに2.6mA流れています。)と思えないくらいに、拡散キャップを付けた時の視認性がアップしています。 |
|
|
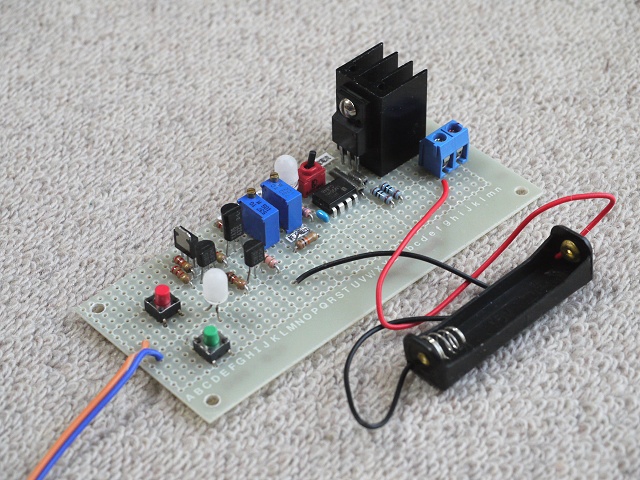 |
|
|
完成した基板の全景です。 次の写真もそうですが、およそ基板の半分は縦方向にがら空きです。 このスペースに単三・単四兼用の電池ホルダーを自作して取り付ける予定です。 また最終的には基板の四隅を木ネジで18mm厚の合板に固定する予定です。
|
|
|
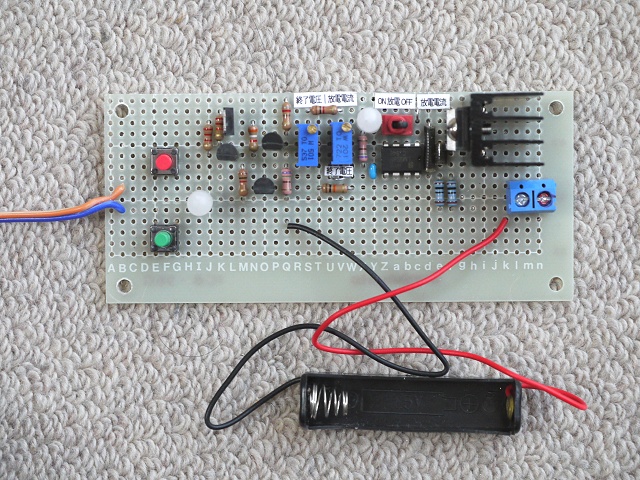 |
|
|
完成した基板を真上から見るとこんな具合で、前に掲載しているレイアウト図と比較すると理解しやすいでしょう。 |
|
|
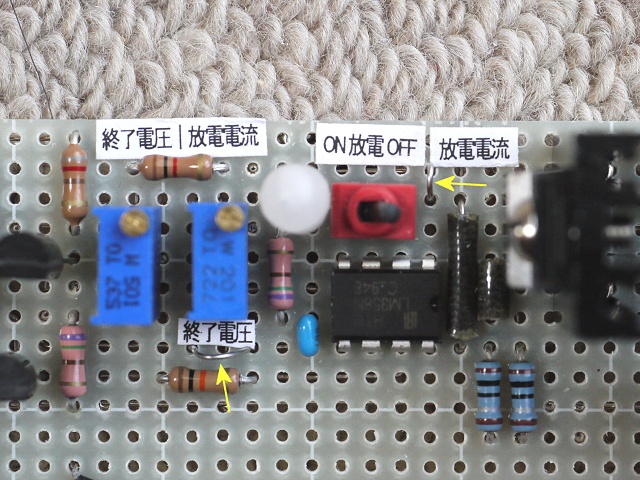 |
|
|
基板には文字を印刷したラベルを貼り付けた所が4箇所あります。 左上からポテンショメータの説明、放電ON/OFFのスイッチのレバー位置説明、電圧チェックのジャンパーピン(黄色矢印)の目的説明です。
|
|
|
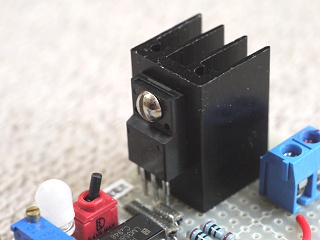 |
|
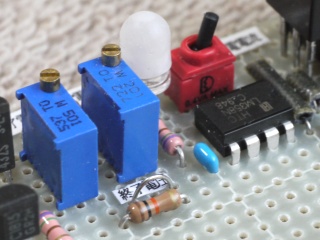 |
|
|
放熱器は今は必要以上の物が付いていますが、単三エネループを放電する時の大電流対策を予めしておきます。
|
|
ポテンショメータとトグルスイッチの間に見える白い部分は点滅LEDの頭です。 トグルスイッチを一時放電停止モードとすると点滅して停止状態であることが判ります。
|
|
|
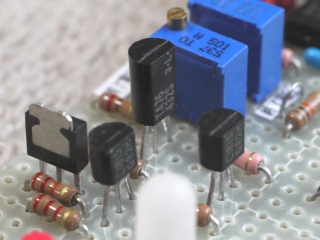 |
|
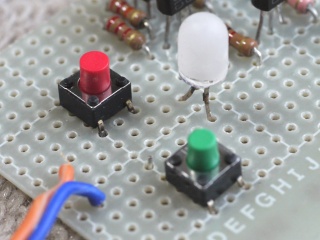 |
|
|
この写真の真ん中にあるのっぽなトランジスターのような物がシャントレギュレーターで、正確なリファレンス電圧を作る重要パーツです。
|
|
赤と緑のタクトスイッチは、放電スタートと放電停止のトリガースイッチです。 そして放電中はそれらの間にあるLEDが点灯して放電中であることを知らせます。
|
|
|
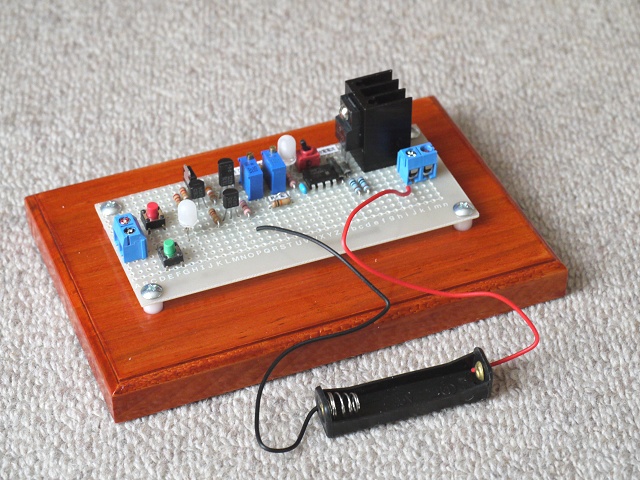 |
|
|
出来上がった基板は端材で作った台に固定しました。 電池ホルダーが最終の物になるともっと格好良くなる筈ですが、一応見られるスタイルになりましたし、基板が安定化して実験中にひっくり返りにくくなります。
|
|
早速放電動作の実働テストを致しました。 手持ちの単四電池3本を無作為に選んで先ず作った放電器で放電電流400mAで電池電圧が1.0Vになるまで放電しその後20分冷やした上で、サンヨーのエネループ用充電器で充電した物を再度放電器に装填して放電時間を測りました。 放電時間は例によってリコーのCX-1で1分間隔のインターバル撮影をして判断しています。 従って測定誤差は1分以内に入る筈です。 結果をグラフにしましたので以下をご覧下さい。
|
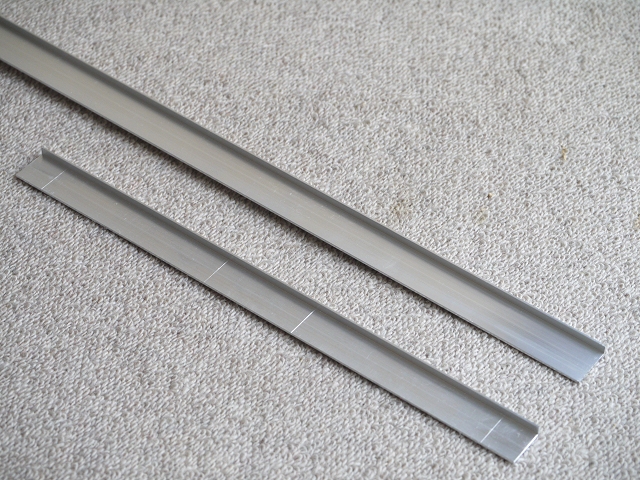 |
|
|
L型押し出し材を所定の長さに切り出し、幅を2mm詰めました。 これらの加工には刃研ぎグラインダーで+0.5mm程度の寸法とした後にヤスリで所定寸法に仕上げています。 上は元のチャンネル材です。 尚加工済みの部材には4箇所ケビキがされていますが、これは折り曲げの場所を示します。
|
|
|
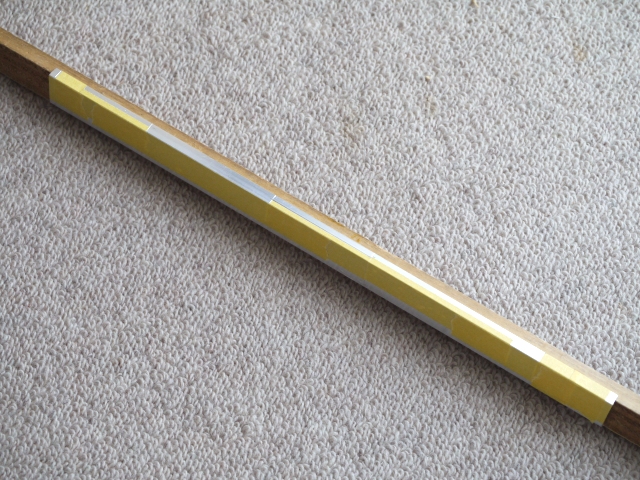 |
|
|
Lチャンネルの折り返し部分は幅が5mmありますが、これを場所によって1.0mm、2.0mm、3.0mm幅に詰めねばなりません。 その境目に沿ってマスキングテープを貼りました。
|
|
|
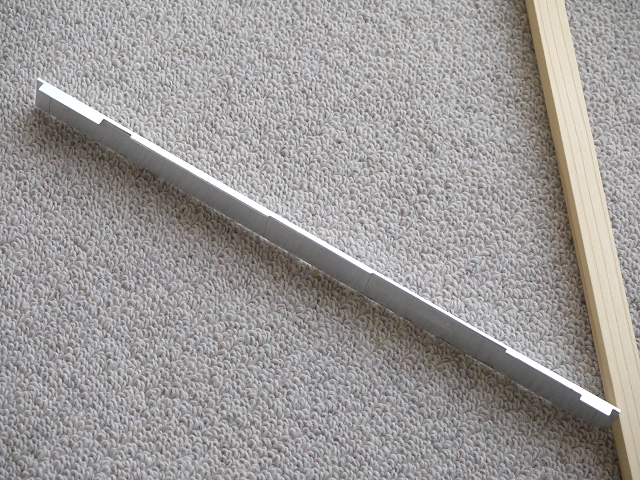 |
|
|
そして平ヤスリにてひたすら削ることにより所定の幅にしましたが、言うまでもなく大変時間がかかる作業であり、こうなるまでに半日以上を費やしました。 もっと効率的な方法があると良いのですが?
|
|
|
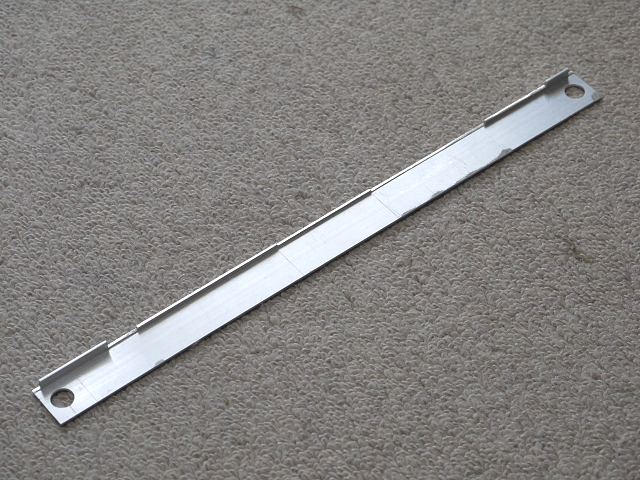 |
|
|
両端に7.5φの穴を開けます。 これはミニヘッドフォーンジャックを固定するための穴ですが、実際にはフロントパネルにあけられた同じサイズの穴を通じて共締めされます。
|
|
|
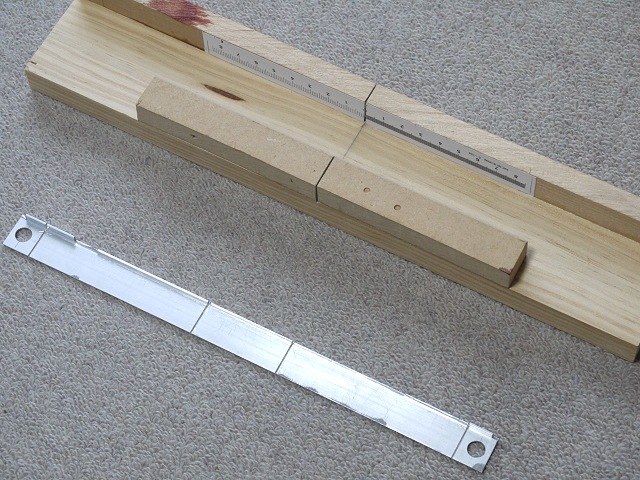 |
|
|
OPA2350使用ヘッドフォーンアンプのアルミフレームを作る際に製作したジグを使って、アルミフレームの折り曲げ部分に深さ0.4mm程度の溝を糸鋸で切ります。 このジグは正確な寸法のアルミフレームを作る上で大きな貢献をしています。
|
|
|
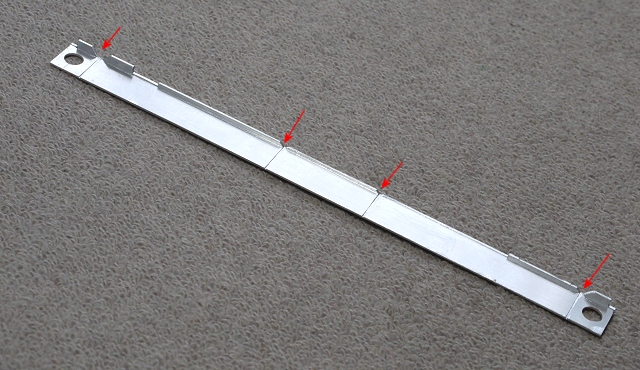 |
|
|
フレームの4箇所を曲げた時に折り返し部分が当たらないよう削り落とします。 少々大きく削り落とす方が良いでしょう。 この後4箇所を折り曲げます。
|
|
|
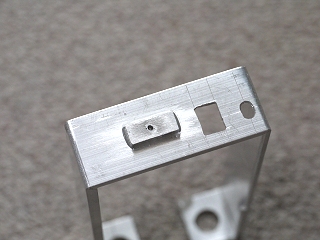 |
|
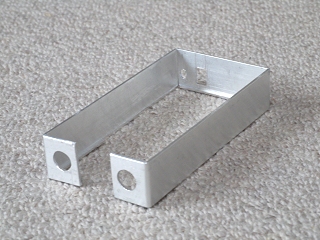 |
|
|
背面に充電器接続のコネクターが飛び出る穴とトグルスイッチの頭が出る穴をあけました。 更に固定ネジ穴を切る1.5mm厚アルミ板をエポキシ接着剤で貼り付けました。
|
|
アルミフレームの加工が全て終わりました。 作り直しをしなかったこともあって1日強で終了しています。 学習効果!まずまずです。
|
|
|
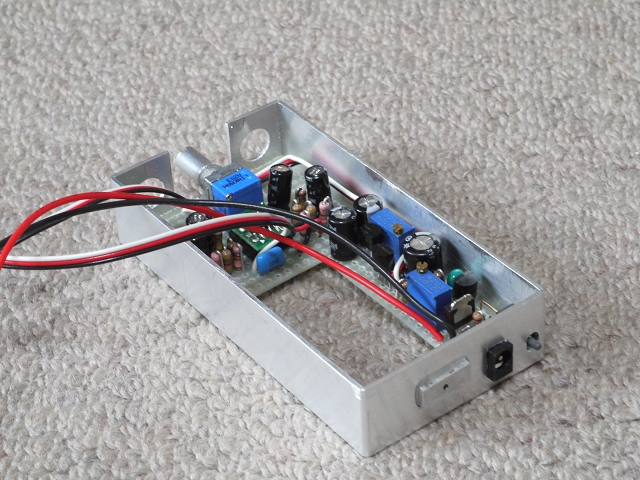 |
|
|
回路基板を所定の位置に挿入してみました。 アルミフレームの寸法誤差は+0.15mm以下に収まっているようです。 無論全く問題ありません。 空間部分に電池ホルダーを構成するプラスチック板で枠を作り嵌め込みます。
|
|
|
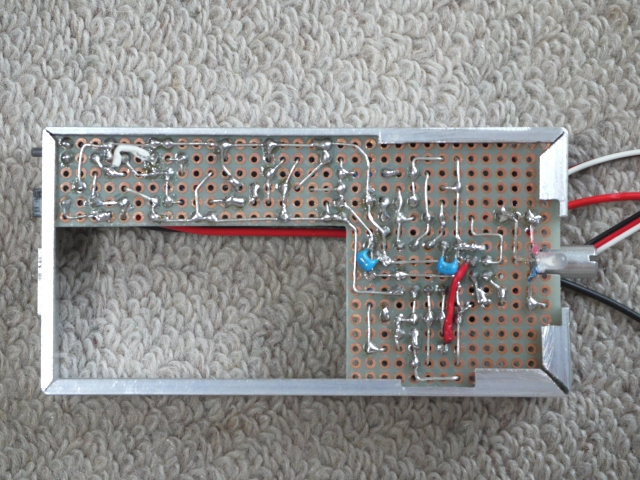 |
|
|
裏はこんな具合ですが設計段階で基板裏の配線がアルミフレームの受け部分に接触しショートしそうな部分を念入りに抽出して加工に繋げたため、ショートの心配はなくこのあとで追加加工することも無さそうです。
|
|
|
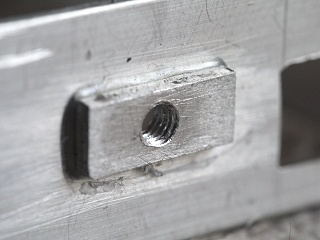 |
|
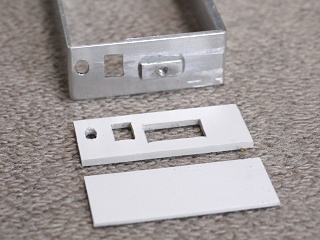 |
|
|
アルミフレームの後面のネジ穴部分は1.5φの穴が貼り付けた1.5mm厚のアルミ板にあいでいるだけですが、2.5φの貫通穴をあけてからM3の雌ネジを切りました。
|
|
2mm厚の発泡塩ビ板に3つの穴を現物合わせであけます。 そして同じ大きさの1mm厚の発泡塩ビ板を切り出します。
|
|
|
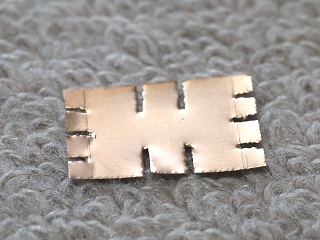 |
|
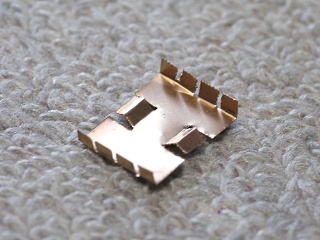 |
|
|
これは0.1mm厚の燐青銅板を切り出したところです。 10箇所の切込がありますが、これらは糸鋸で切り込んでいます。
|
|
燐青銅板はその後このように折り曲げます。
|
|
|
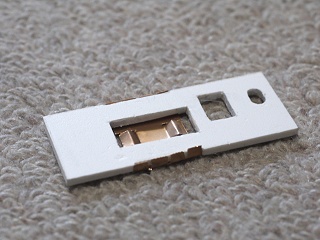 |
|
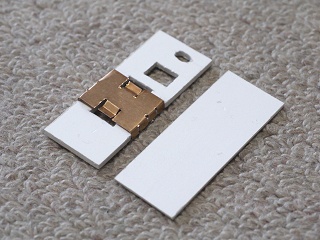 |
|
|
そして2mm厚発泡塩ビ板にこんなふうに当てられます。 燐青銅板のこの写真で見える部分がアルミフレームと電気的に接触します。
|
|
2mm厚塩ビ板をひっくり返すとこんな具合ですが、この面に1mm厚発泡塩ビ板を塩ビ用接着剤で貼り付けます。
|
|
|
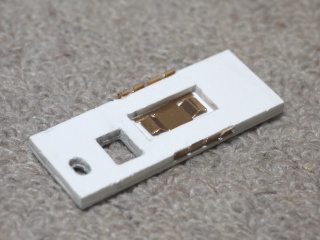 |
|
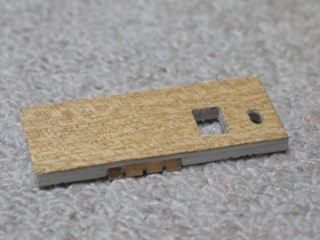 |
|
|
貼り付けが完了しましたので、充電器接続用ジャックとトグルスイッチのレバーが出る穴を1mm塩ビ板にあけました。
|
|
更に木口テープを貼り付けてから充電器接続用ジャックとトグルスイッチのレバーの穴をあけています。 ケース固定のネジ穴は後ほどあけます。
|
|
|
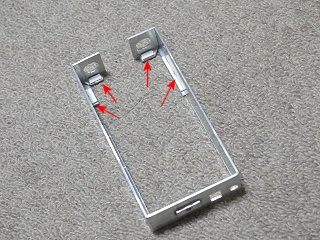 |
|
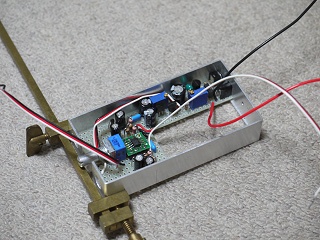 |
|
|
1mm厚発泡塩ビ板を切断してスペーサーとして4箇所に貼り付けました。
|
|
そして基板をアルミフレームに接着します。 この工程とスペーサー接着の接着剤にはゼリー状瞬間接着剤を使っています。
|
|
|
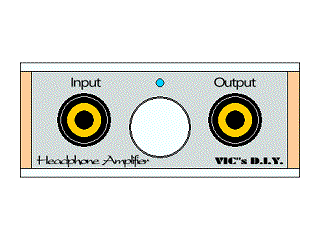 |
|
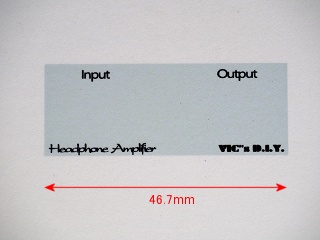 |
|
|
フロントパネルの文字入れはこんな具合にすることにします。 インスタントレタリングでは絶対に得られない3種類の書体を使っています。
|
|
版下の作成はアドビフォトショップを使いました。 小さな文字ですから視認性がイマイチですがこればかりは打つ手がありません。
|
|
|
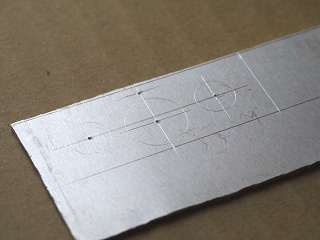 |
|
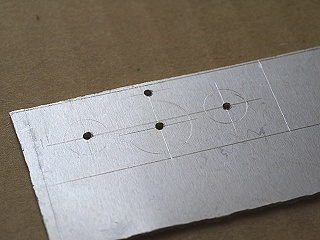 |
|
|
罫書線を入れた上で4つの穴位置にセンターポンチでマーキングをしました。 アルミ板の穴部分が出っ張らないようマーキングは浅目です。
|
|
最初は1.5φのドリルで穴をあけました。 LEDの穴はこれが最終寸法となります。
|
|
|
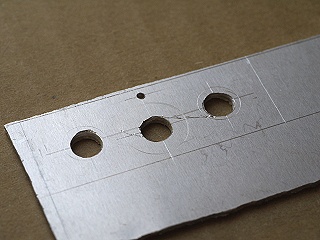 |
|
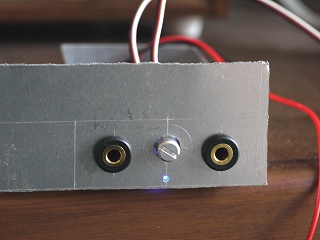 |
|
|
他の3つは、3.0φ、4.5φ、6.0φと少しづつ穴径を大きくしています。(手持ちの電動ドリルでの穴あけはずれやすいので)
|
|
そしてアルミフレームにフォーンジャックで仮止めし、LEDの位置、ツマミ穴の罫書位置の確認をしました。
|
|
|
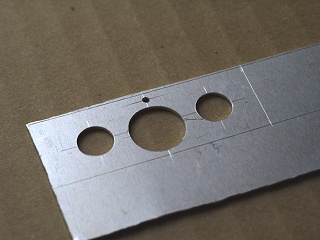 |
|
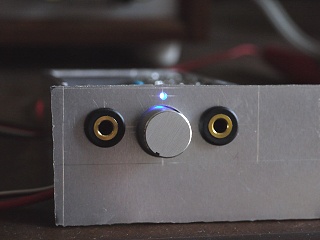 |
|
|
ツマミ穴の罫書はほぼ正確でしたので丸棒ヤスリで広げてドンピシャ寸法にしました。
|
|
再び仮止めしてツマミを差し込みました。 ツマミとパネルの間に均等に隙間が出来ましたが、LEDの光が漏れているのを発見。 これは少しでも抑えたいところです。
|
|
|
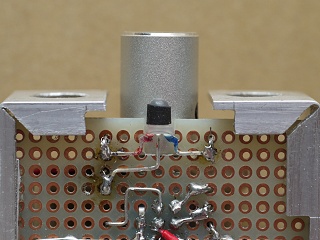 |
|
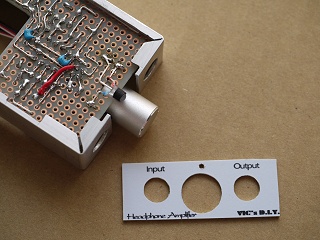 |
|
|
光漏れはLEDの横から出る光によるので、3φの熱収縮チューブをLEDに被せました。 これでかなり収まるはずです。
|
|
アルミフロントパネルに印刷してコーティングした紙を両面接着テープで貼り付けました。 そして穴部分をカッターナイフでくり抜いています。
|
|
|
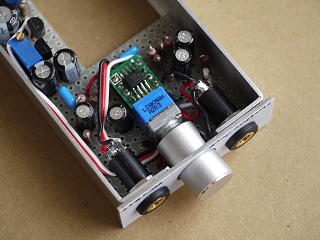 |
|
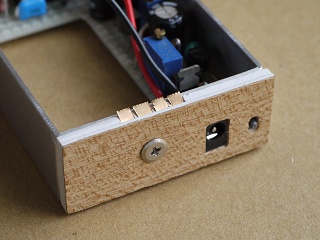 |
|
|
アルミフロントパネルをフォーンジャックでアルミフレームに共締めし、フォーンジャックへの配線をしました。
|
|
現物合わせで背面板に3.2φの穴を開けて例の薄頭ネジで固定できるようにしました。
|
|
|
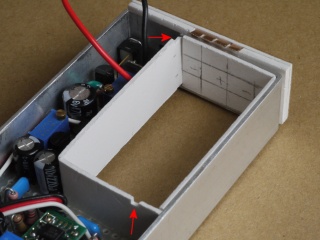 |
|
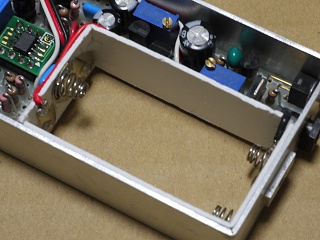 |
|
|
電池ホルダー部分はL字型に切った1mm厚発泡塩ビ板2枚を貼り合わせます。 この写真は所定の位置に挿入したところで、赤矢印先はケーブルが通る欠き込みです。
|
|
電池の電極をエポキシ接着剤で貼り付けL字状の電池ホルダー枠をアルミフレーム内に接着しました。 更に±のワイヤーを配線しました。
|
|
|
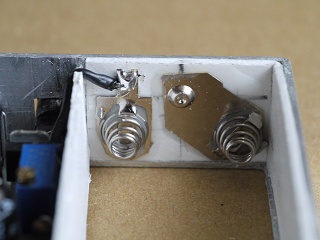 |
|
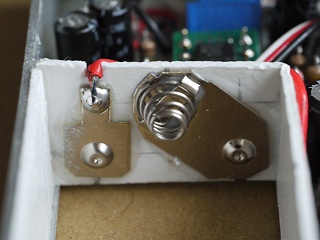 |
|
|
電池ホルダーの後ろ側の様子。 左上にマイナス側のワイヤーが配線されています。
|
|
前側はこんな具合で、左上にはプラス側の赤いワイヤーが接続されています。
|
|
|
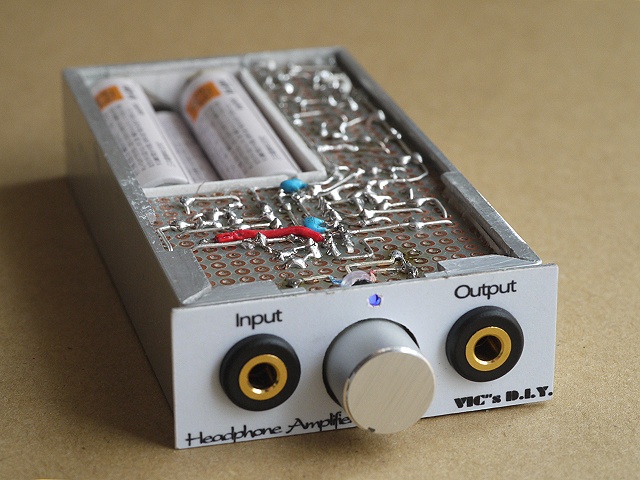 |
|
|
完成したアルミフレームブロックにエネループを装填しました。 ご覧のように実使用時に文字が正常に見える位置はアルミフレーム部は逆さになります。 無論問題はありませんが、これはボリュームのツマミの位置が中心からずれるのでLEDはその反対側にずれて取り付けるしかなく、LED位置を上側になるようにしたいのでこんな具合になってしまいます。
|
|
|
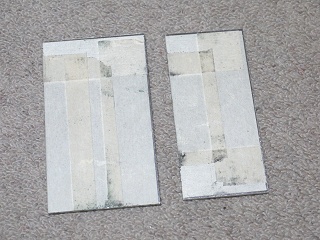 |
|
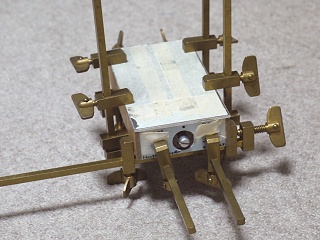 |
|
|
切り出したアルミ側板(左側)です。 無論同じ物がもう一枚必要です。 板の外寸は0.3〜0.5mm大きくなるようにしてあり、後で調整研磨で所定の大きさとします。
|
|
接着して圧着保持をしている状態ですが、15分後に厚み方向以外のハタ金は外してしまいます。
|
|
|
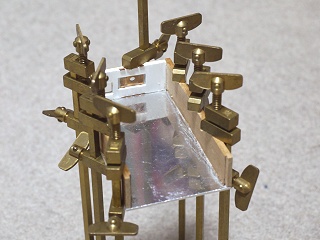 |
|
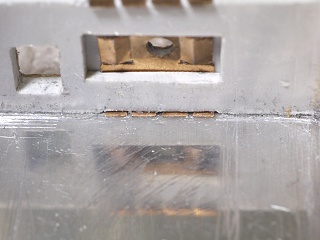 |
|
|
そして厚み方向のハタ金を増やして完全硬化のために6時間放置します。
|
|
内側奥の隅には基盤本体とアルミ側板を電気的に接続する目的の燐青銅板がちらっと見えます。
|
|
|
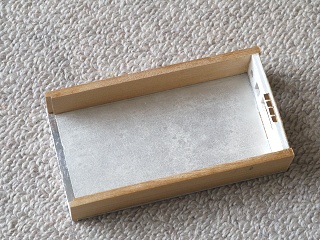 |
|
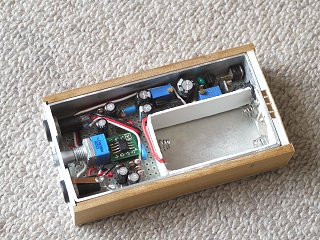 |
|
|
アルミ板の内側には0.2mm厚のポリプロピレーン(P-P)シートを貼り、ショート防止としました。
|
|
アルミフレーム本体のフロントパネルを調整研磨し、ごく僅かの隙間で収まるよう調整しました。
|
|
|
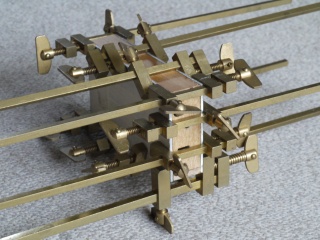 |
|
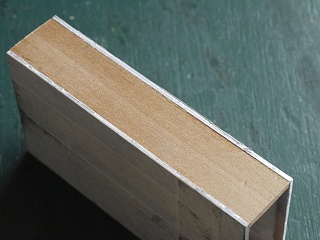 |
|
|
もう1枚のアルミ板を接着しました。 なにか意地になってハタ金を使っているみたいに沢山使用しています。
|
|
貼り終わった直後はアルミ板は僅かに木の枠より出っ張っていますので、
|
|
|
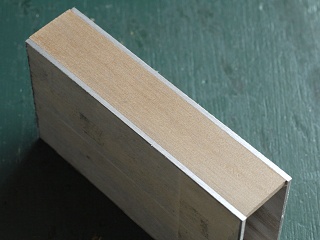 |
|
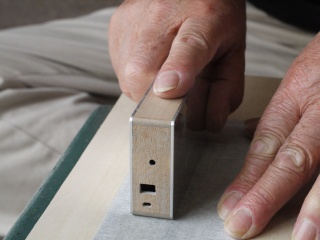 |
|
|
替刃式ヤスリ(M-20GP)で同じ高さになるよう削ります。
|
|
そして板に#240の空研ぎペーパーを貼り付けてケースを握りアルミ板の面を除き全面を研磨し、その後面取りをします。
|
|
|
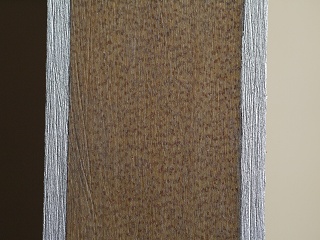 |
|
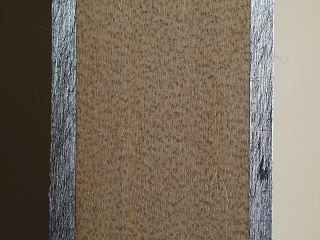 |
|
|
こちらは替刃式ヤスリで削った後。 替刃式ヤスリの粗さは約#150と言われていますが、長手方向の深い溝が沢山見えます。
|
|
そしてこちらは#240の空研ぎペーパーで研磨した後。 長手方向の溝が浅くなっているのが判ります。
|
|
|
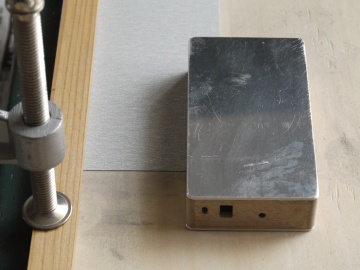 |
|
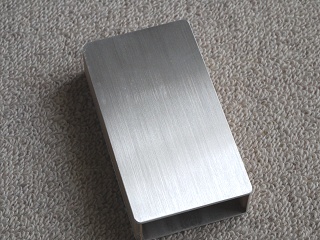 |
|
|
ヘヤーライン加工のジグ。 #400の空研ぎペーパーを板に貼り付け左側にガイド棒を固定してあります。 使い方は簡単で、ガイド棒にケースを沿わせて研磨するだけです。
|
|
ヘヤーラインを掛け終わったケース。 見違えるようにエレガントな外観になりました。
|
|
|
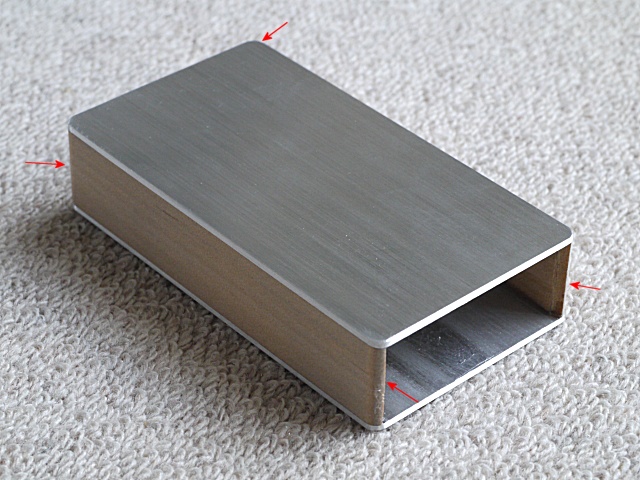 |
|
|
ケースを上から見た4つの角(赤矢印の先)は半径2〜3mmで丸くしましたが、その他の角は痛くないように0.4〜0.6mm削っただけとし、シャープな外観を持たせたつもりでいます。(全てを丸くしてしまうとぼてっとした雰囲気になります。)
|
|
|
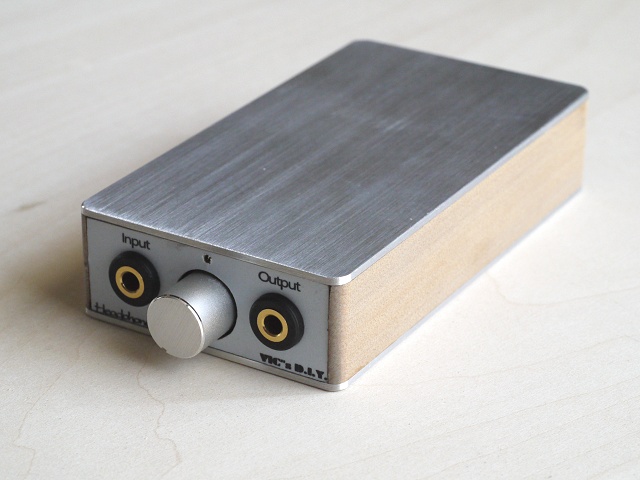 |
|
|
これで外観は木部の色味を除き最終的な形になりました。 シャープさ狙いはこの場合良かったようです。
|
|
|
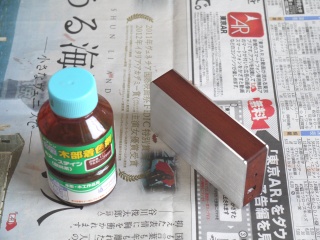 |
|
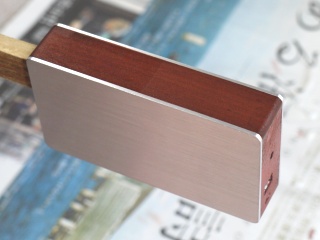 |
|
|
先ずステインで木部を着色しました。 写真には見えませんが、アルミを着色しないようマスキングテープで覆ってやりました。
|
|
木部とアルミの厚み部分を20%の水で薄めた水性ウレタンニス透明クリヤーで塗装しました。(アルミの面部分はまだ塗装しません。)
|
|
|
木部の塗装は透明クリヤー6回塗りとしましたが3回目と5回目の塗装乾燥後には#600空研ぎペーパーで研磨していま
す。 アルミの面塗装はその後アクリルラッカースプレー塗料を2回塗りし、完全乾燥後に表面を#600空研ぎペーパーで
ツブツブの頭を半分削るように研磨します。 そして水性ウレタンニス透明クリヤーを2回塗りし乾燥後に全体をつや消し
クリヤーで塗装します。 その仕上がり具合は以下のクローズアップ写真をご覧下さい。
|
|
|
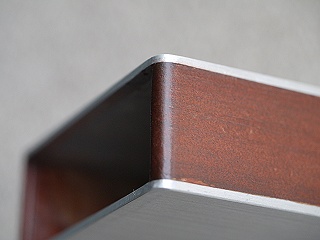 |
|
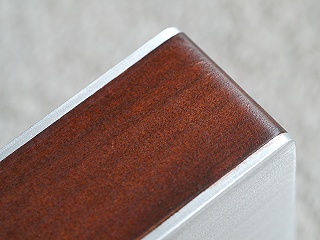 |
|
|
つや消し塗装処理しているためしっとりとした3分艶位になっており品があります。
|
|
木目部分とアルミ板の厚み部分のコントラストが大変美しく仕上がったと思います。
|
|
|
 |
|
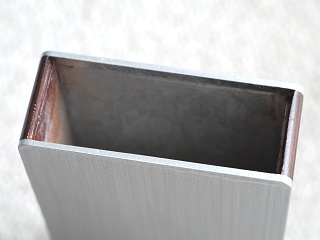 |
|
|
4箇所は半径2mm位に丸めましたが、その他の角は0.3〜0.4mm程角を落とした程度ですから、シャープな感じが残っています。
|
|
全面はこんな具合ですが、フロントパネルを落とし込むように収まります。
|
|
|
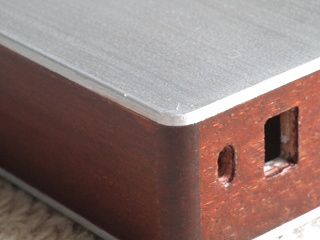 |
|
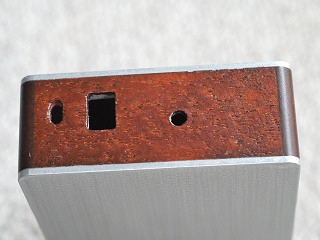 |
|
|
背面の角を見たところ。 実は背面の木目はオクメの木口テープで異なった木目になっています。
|
|
生地の色はアガチスに似ているので着色後雰囲気は似ていますが、木目の違いが判ります。
|
|
|
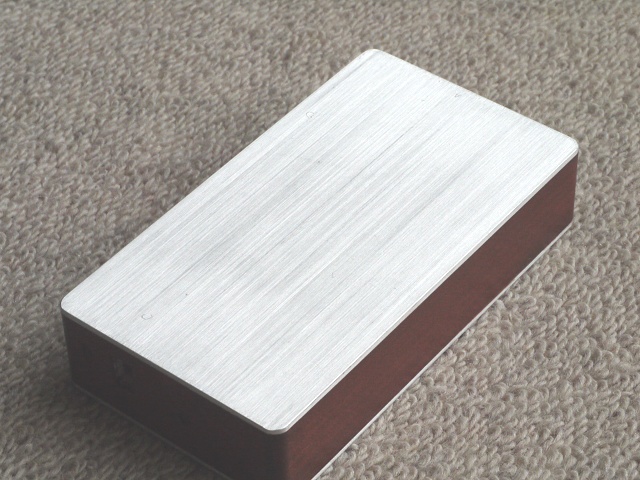 |
|
|
ヘヤーライン加工面は光の当たり具合で見え方が大幅に変化します。 これは最も明るく反射したところを撮影しています。
|
|
|
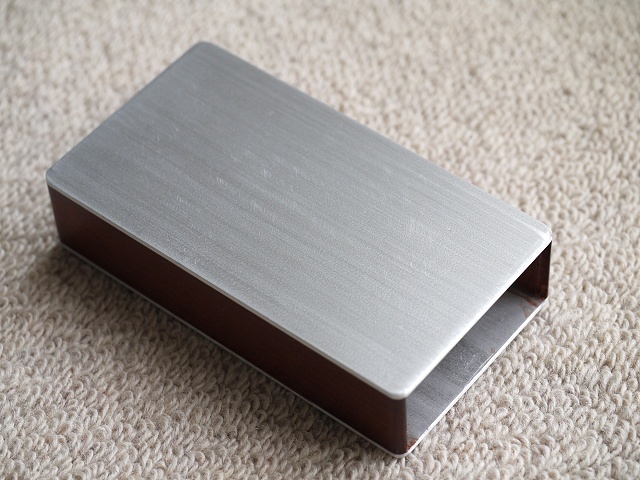 |
|
|
こちらは最も反射光が鈍くなる手間の状態で、前側が強めに反射しています。
|
|
|
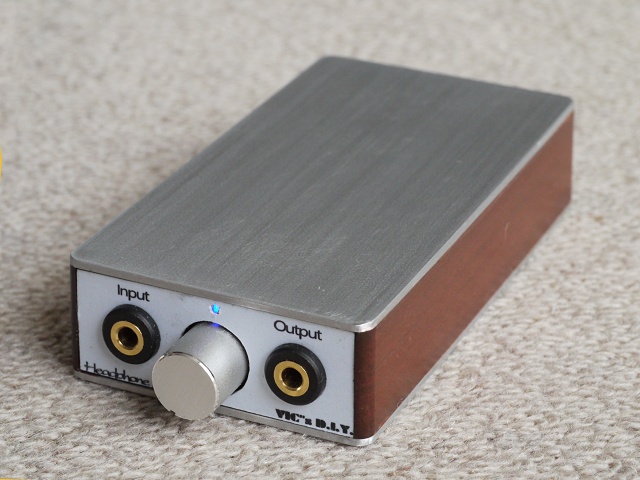 |
|
|
アルミフレームアセンブリーを装填した状態ですが、アルミ板の面は最も反射光が鈍い状態になっています。
|
|
これで2種類のポータブルヘッドフォーンアンプの製作が終了しました。 コダワリに更にコダワリが重なり構想から何と1年も掛かっていますが、何れも省エネ度が高く、満足度の高い物になったと自負しています。 第一世代のポータブルヘッドフォーンアンプそして今回作った2つのモデルの比較は次をご覧下さい。Copyright (C) 2001-2019, Vic Ohashi All rights reserved.