|
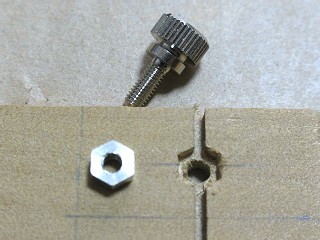 |
|
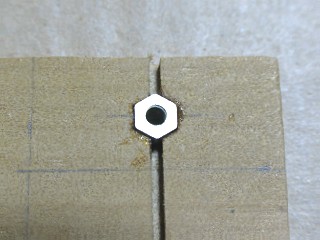 |
|
|
電池ホルダーの部材ですが、深さ2.5mm、幅1.6mmの溝を彫ってから3mmのナットを埋め込む6角形の穴(きつめ!)を3mmのノミで彫ったところ。 上はM3の飾りネジ。
|
|
ナットを埋め込むとこのようになります。 ナットの表面は板の表面とほぼ一致します。 位置の確認をした上でナットの周りに少量のエポキシ接着剤を付けて嵌め込み、固定します。
|
|
|
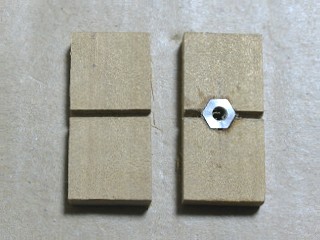 |
|
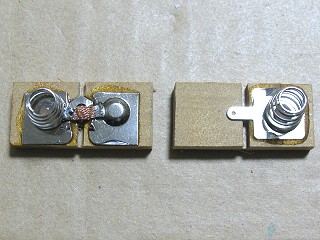 |
|
|
そうしたら部材の最終的な大きさに切り出します。 最初にこの大きさに切り出してしまうと、溝彫りやナットを埋める作業が大変やりにくくなります。
|
|
次に電極を固定しますがこれもエポキシ接着剤によります。
|
|
|
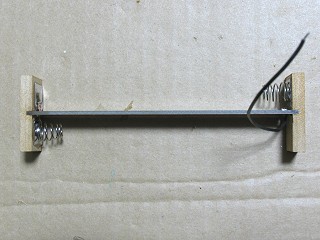 |
|
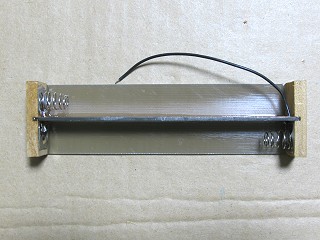 |
|
|
コンパクトLEDランプ 1の電池ホルダーと同じような中央の仕切り板(ガラスエポキシ 1.5mm)を接着します。 仕切り板の両端は板の溝に挿し込まれます。
|
|
更にもう一枚のガラスエポキシ板を貼って断面がT字型になります。
|
|
|
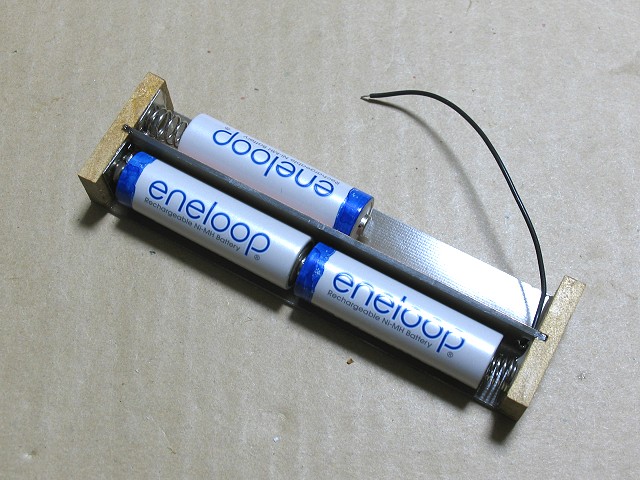 |
|
|
電池はこのように収まります。 上側の電池の右にあいた部分に電気回路が納まります。 撓みや捻れがが想定していたよりもずっと少なく安心しました。 というか過剰品質です!
|
|
|
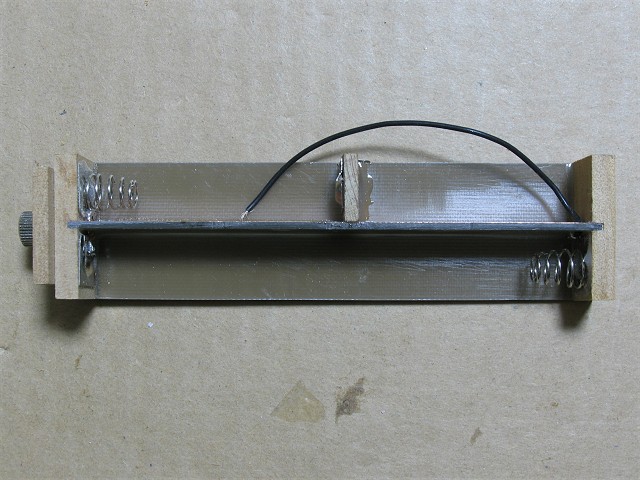 |
|
|
上段に仕切り板を固定しました。 右側の電気回路挿入部分へは多量のエポキシを使って基板を接着します。
|
|
|
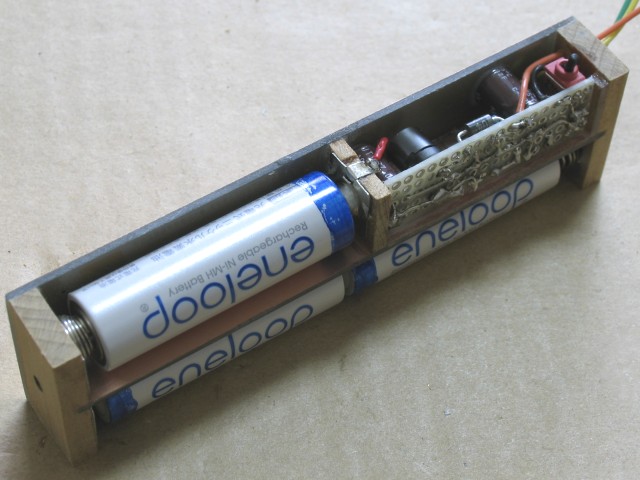 |
|
|
LED基板に接続される3本のワイヤーを前方に引き出した上で、DC-DCコンバーター基板は所定の場所にエポキシ接着剤で固着されました。 エポキシは電気的に極めて安定な不導体なので問題はありませんが、これ以降は電気的な調整は全く出来なくなります。
|
|
|
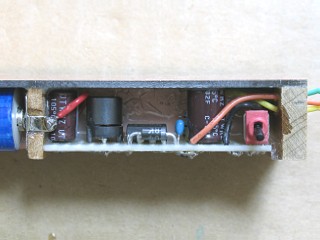 |
|
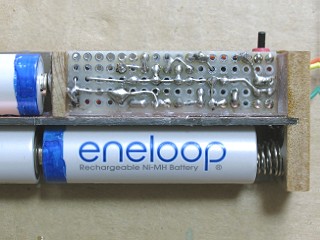 |
|
|
真上から見たところで、当初と基板の向きが変わりました。 これは使うトグルスイッチの形状が変わったためで、トグルスイッチの先端は上部に飛び出します。
|
|
横から見るとこんな具合です。 上に飛び出たトグルスイッチの先端(黒い部分)が判ると思います。
|
|
|
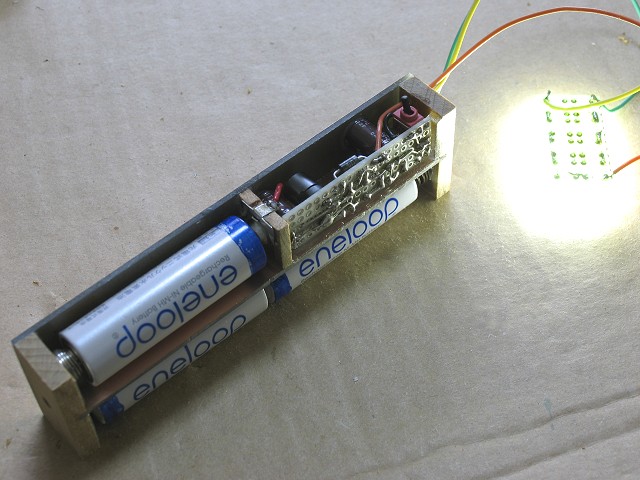 |
|
|
点灯動作実験の様子。 アルカリ乾電池を使うのはもったいないのでエネループを使っていますが、完成後の使用主力電池はアルカリ乾電池になります。(待機時間が長いのでエネループでは逆に不経済になると思われる。)
|
|
|
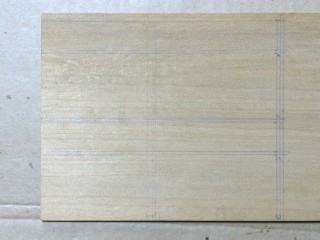 |
|
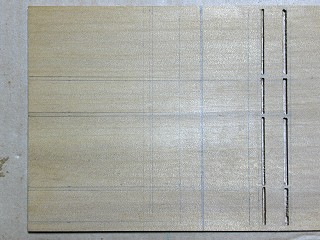 |
|
|
ケースを作る部材に墨線を引きました。 となりとの間は2mmの空間をあけノコギリでの切断にはかなりのゆとりを持たせています。
|
|
前面に2mm厚のアクリルとLED基板を落とし込む溝をトリマーで予め彫ってやります。 位置精度を上げるうまい方法です。
|
|
|
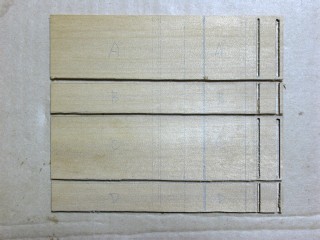 |
|
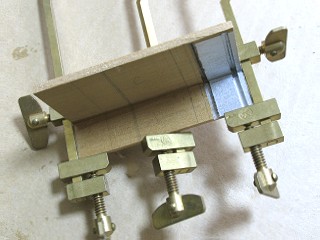 |
|
|
そして4分割しました。 更に切り分けて8つにするのは後ほど。
|
|
前部ですが、組立て後塗装できなくなる部分にメタリック系のスプレー塗料を塗ってやり、L型に接着しました。
|
|
|
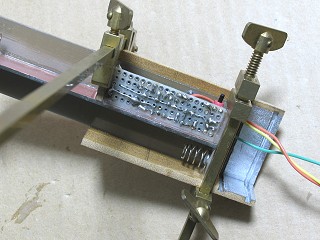 |
|
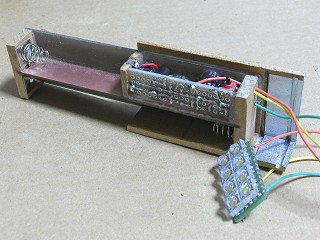 |
|
|
それを前部と後部に切り分けた後で前部を電池ホルダーにエポキシ接着剤で固定しました。
|
|
完全硬化後の様子。 LED基板がぷらぷらの状態ですが、ワイヤーを切り詰めて所定の位置に基板を収めます。
|
|
|
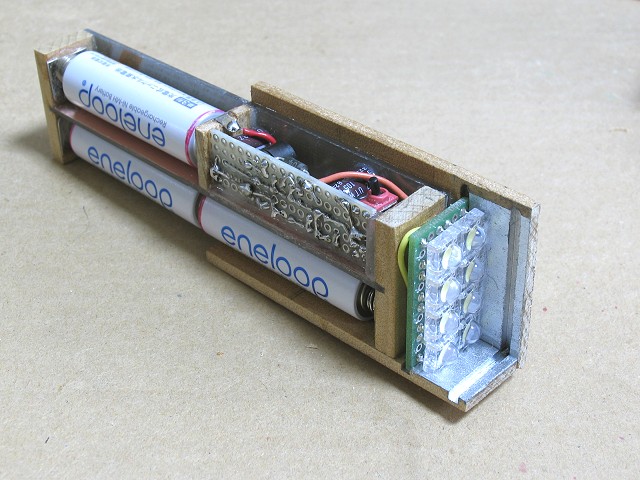 |
|
|
LED基板は所定の溝に収まっています。 この後上部の基板に現物合わせでスイッチのつまみが出る穴の加工、そして前部をケースで覆ってしまいます。 一応このモデルもスケルトンモデルと言えるところまで来ました。
|
|
Copyright (C) 2001-2019, Vic Ohashi All rights reserved.