|
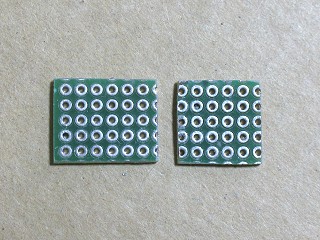 |
|
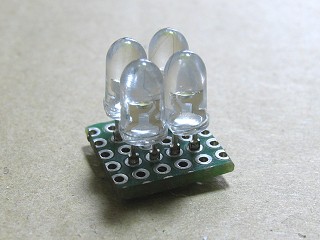 |
|
|
切り出した穴あき基板。 左がDC-DCコンバーターとスイッチ固定用、右がLEDブロック用ですが、何れもスルーホールメッキされているので、両面で配線が可能です。
|
|
干渉しないように鍔部分を削り落としてから4本のLEDを固定しました。 ご覧のように並行に垂直に立っています。
|
|
|
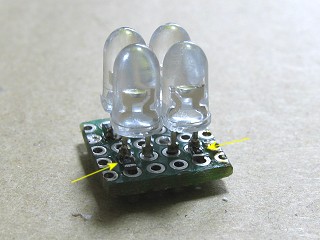 |
|
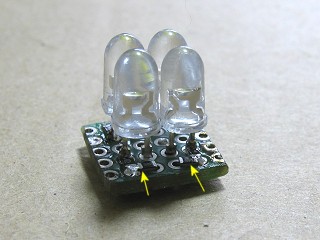 |
|
|
チップ抵抗(10Ω)をLEDの脚(-側)に半田付けします。(合計4箇所)
|
|
付けた10Ωに100Ωの片方を半田付けします。(100Ωの位置は90度曲がる。)
|
|
|
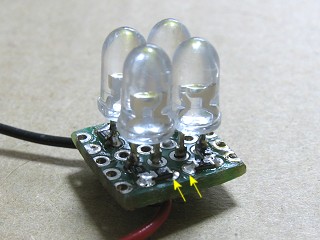 |
|
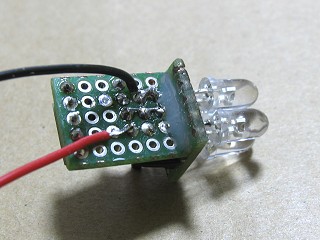 |
|
|
100Ωの反対側を半田付けして終了。 裏面にDC-DCコンバーターへの引き出し線を半田付けします。
|
|
LED基板とDC-DCコンバーター基板間を結線してからとエポキシ接着剤で締結します。
|
|
|
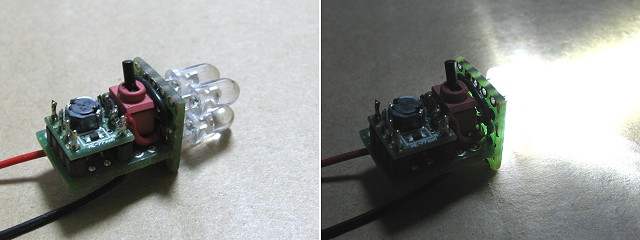 |
|
|
完成した電気回路。 完全に一体化されており、後はケース内部に固定するだけです。 LED本数は4本ながら照射角度が15度と絞り込まれているので、照射面は極めて明るいです。
|
|
|
 |
|
|
外形を細くしながら明るさを保つために半値角15度の5φLEDを4本束ねていますが、その効果は抜群。 細身でありながら明るさ大きくしかも点灯時間を長くしようという矛盾だらけの設定に対する回答になるでしょうか?
|
|
|
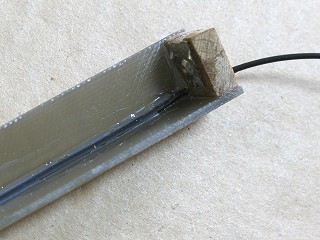 |
|
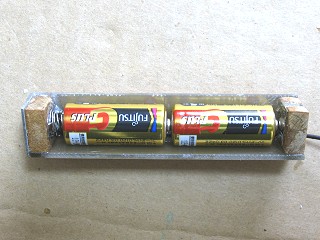 |
|
|
もう一枚の側板を貼りつけ断面はL型になりました。 また底の隅に沿うようにマイナス電極からの線を接着しています。
|
|
確認のために単五電池2本を装填しました。 右側の端にはプラスとマイナスを接続できるようになりました。
|
|
|
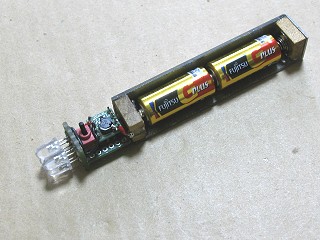 |
|
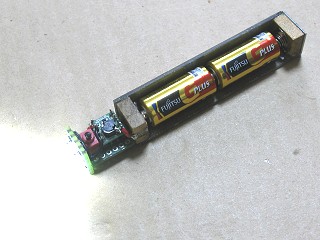 |
|
|
そこでLED、LED駆動ブロックを接続しました。 こんな感じを保ちながらケースが被るようになります。
|
|
そして最後の電気的な動作確認を済ませて、ケースを被せる準備に入ります。
|
|
|
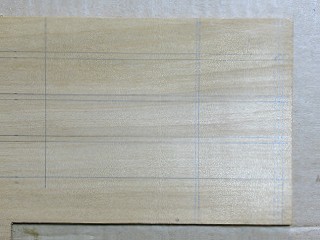 |
|
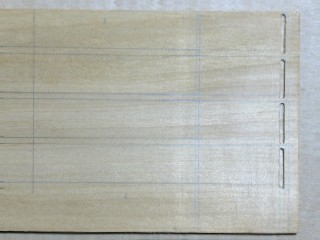 |
|
|
ケースの部材(3mm厚アガチス)に墨線を引きました。 となり通しには2mmの空白を設けています。
|
|
前部のアクリル板がはまる部分に2mm強幅の溝を彫りました。 これは切断後にやると切削位置精度が出ません。
|
|
|
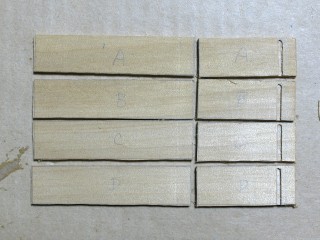 |
|
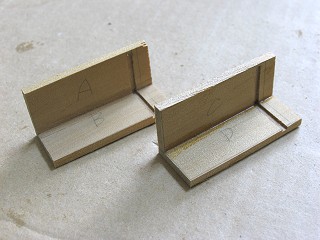 |
|
|
そして8ピースに切断。 実寸法に対しかなりゆとりを見た切断をしているので、ヤスリでこの後寸法出しをします。
|
|
前部の4枚を2枚ずつ接着しました。 位置関係が狂わないようA、B、C、Dとふってあり、その順序どおりに接着しています。
|
|
|
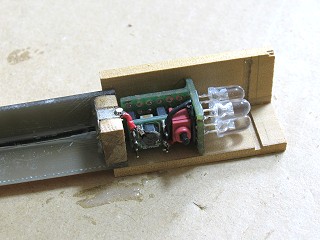 |
|
 |
|
|
前部のL型に電池ホルダー部と電機回路・LEDブロックはこんな状態になるように接着します。
|
|
後から塗装できない部分を塗装しておきます。 メタリック系のスプレー塗料を使い光を少しでも反射するようにしています。
|
|
|
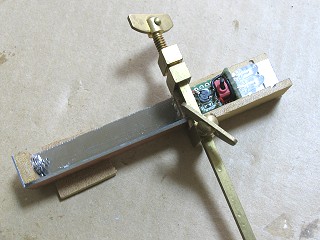 |
|
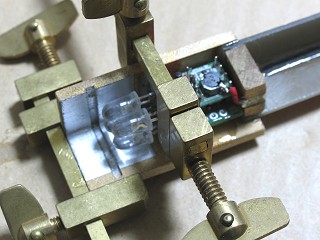 |
|
|
電池ホルダーを前部のL型にエポキシ接着剤で固定。 直線性が狂わないよう十分に調整します。
|
|
電機回路を多量のエポキシで固定。 LEDの照射方向が変な方向にならないよう完全硬化するまでハタ金で抑えています。
|
|
|
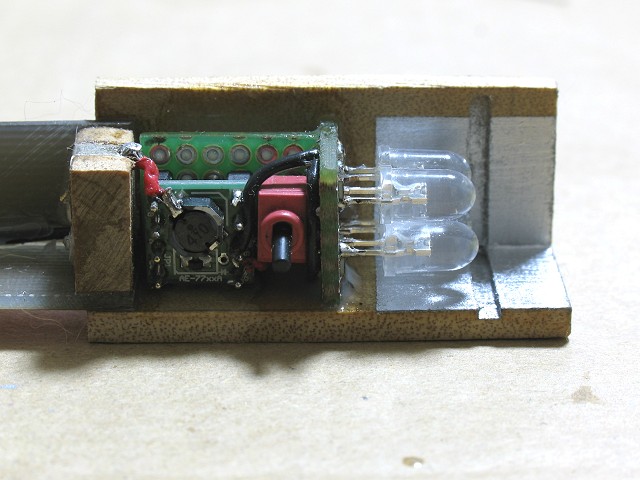 |
|
|
一応スケルトンモデルと言えるでしょうか? ぷらんぷらんした部分はなくなり、勿論点灯も出来る状態になりました。
|
|
Copyright (C) 2001-2019, Vic Ohashi All rights reserved.