|
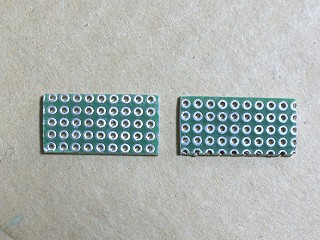 |
|
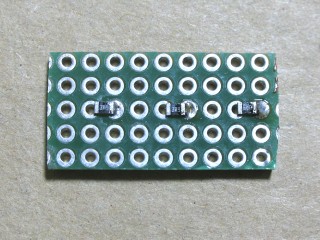 |
|
|
切り出した2枚の穴あき基板。 左はLED用で右がDC-DCコンバーターと電源スイッチ用で、何れもスルーホールメッキ基板ですから両面で半田付け・配線が可能です。
|
|
3.9Ωのチップ抵抗を半田付けしました。 39Ωを半田付けしない方の側を半田付けします。
|
|
|
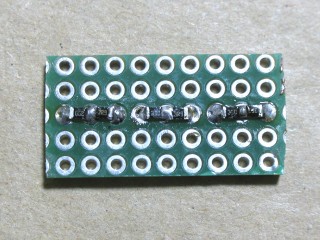 |
|
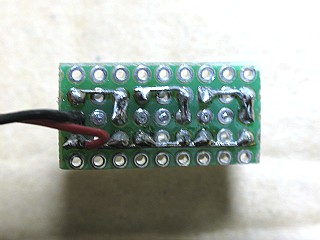 |
|
|
その隣に39Ωを半田付けし、3.9Ωと接続されるところも続いて半田付けします。 そしてこの面にLEDを挿し込みます。
|
|
反対側に飛び出たLEDの脚を半田付けし、結線を済ませて出来上がり。
|
|
|
 |
|
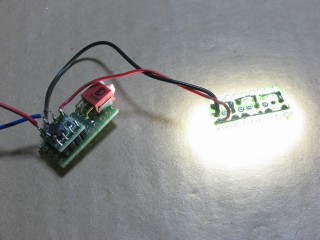 |
|
|
もう一枚の基板にはDC-DCコンバーターと電源スイッチを取り付けて配線します。
|
|
2つの基板はエポキシ接着剤で結合しますが、その前に仮結線して動作確認をしておきます。
|
|
|
 |
|
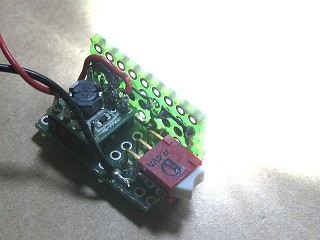 |
|
|
そしてエポキシ接着剤で結合しました。 左の赤黒のワイヤーが電池に接続されます。
|
|
結合後の動作確認。 ご覧のようにLED基板は透け透けになっています。 このモデルの明るさはコンパクトLEDランプ 1と同じで2番目の明るさです。
|
|
|
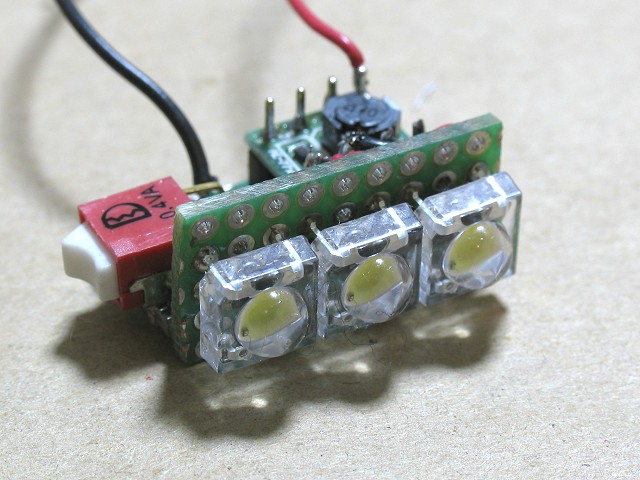 |
|
|
雷神3本を使ったこのモデルは最も小さいこともあり連続点灯時間は短いですが期待の星のひとつです。 LEDの下に駆動電流調整抵抗が6本も入っているのはこの角度ではもう判りませんし、完成時には完全に見えなくなってしまいます。
|
|
|
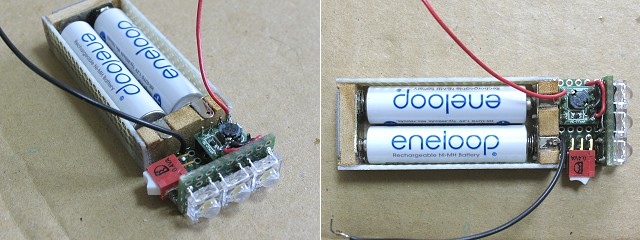 |
|
|
電池ホルダー部分の成形・外寸調整研磨を済ませ、LED、LED駆動部をそれに当てて問題がないことを確認しています。 スイッチの本体の赤い部分半分近くはケースの板に嵌まり込むため出っ張っています。 また赤黒のワイヤーはそれぞれプラス側、マイナス側の電池電極に繋がります。
|
|
|
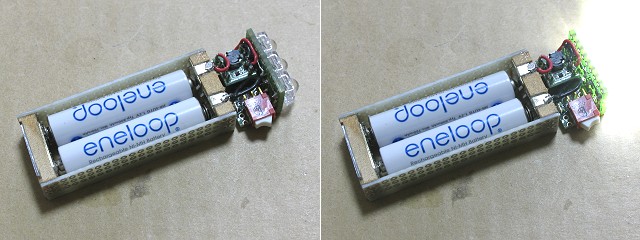 |
|
|
ワイヤーを短く切断して所定の電極に半田付けしました。 これで電気的な接続とスイッチの動作をもう一度確認します。 ケースが被ると完全に遮断されてしまいますから、電気的な調整は全く出来なくなります。
|
|
|
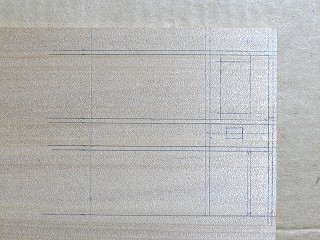 |
|
 |
|
|
ケースの部材は8ピースに切り分けられた板からなりますが、となり通しが繋がった木目になるよう配置します。 尚ある目的があって境には2mm幅の空白が付けられています。
|
|
トリマーによる溝彫りや浅彫り部分を先に済ませてしまいます。 左の写真から消えている墨線がありますが、現物合わせのために不要になった線です。
|
|
|
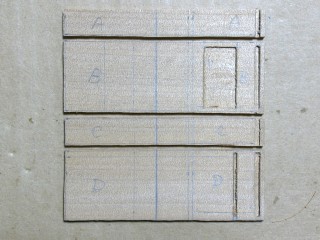 |
|
 |
|
|
4つに切り分けました。 かなり直線性の悪い切断ですが、実墨線に対してかなり大きめになっており、この後ヤスリで調整研磨します。
|
|
その内2枚を切断して頭部部分をL型に接着し、後から塗りにくい部分をスプレー塗料で塗装しました。
|
|
|
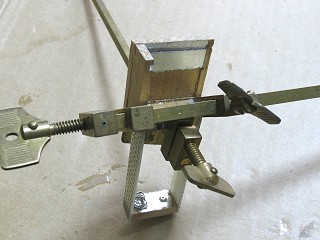 |
|
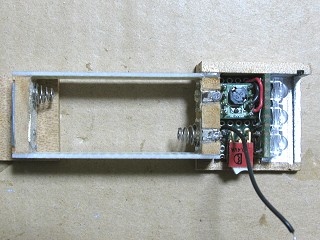 |
|
|
L字に組んだケースにロの字型をした電池ホルダーを接着しました。 直線性がおかしくならないよう念入りに調整し6時間以上寝かし完全硬化させます。
|
|
その後駆動回路+LEDの基板を所定の位置に多量のエポキシで固定します。
|
|
|
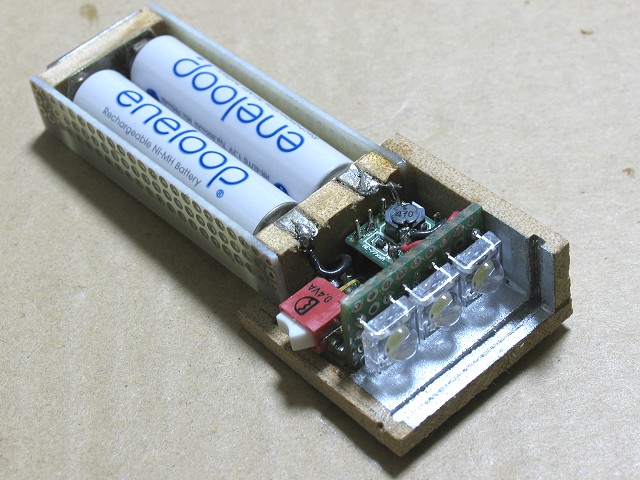 |
|
|
結線を済ましてスケルトンモデル状態まで完成です。 この後側板のスイッチ穴を現物合わせで加工して上部の外周を覆い、電池カバーの組立てに進みます。
|
|
Copyright (C) 2001-2019, Vic Ohashi All rights reserved.