|
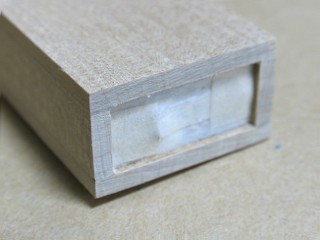 |
|
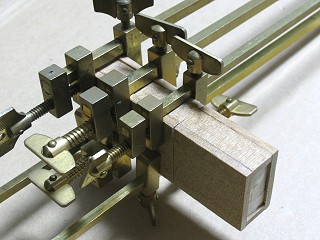 |
|
|
LEDブロック部分を完全に覆いました。 LED部分保護のためマスキングテープを貼ってあります。
|
|
電池カバー部分の組立てです。 電池ホルダーとの間の隙間の作り方は前作と全く同じです。
|
|
|
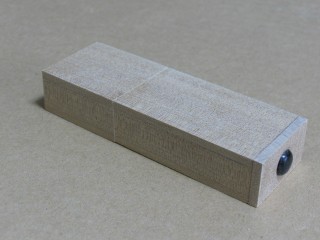 |
|
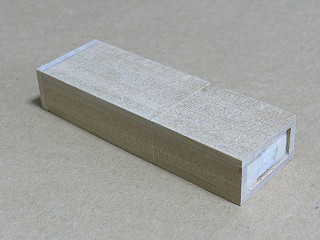 |
|
|
外側の組立てが完了し、接合部分の段差とはみ出た接着剤の削り落としが終わりました。
|
|
前後を反転させた状態です。 電池カバーがLEDブロックに付き合わさる部分の調整研磨も念入りにしてあります。
|
|
|
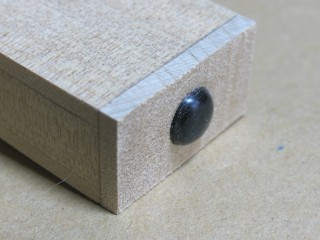 |
|
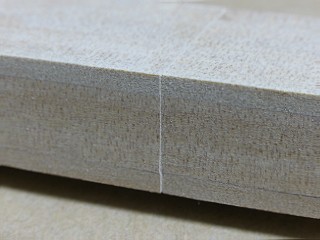 |
|
|
底板を貼った部分の出っ張りもきれいに削り落としてあります。
|
|
前後の突き合せ部分のクローズアップ。 この程度の密着度というか修正状態がベストでしょうか?
|
|
|
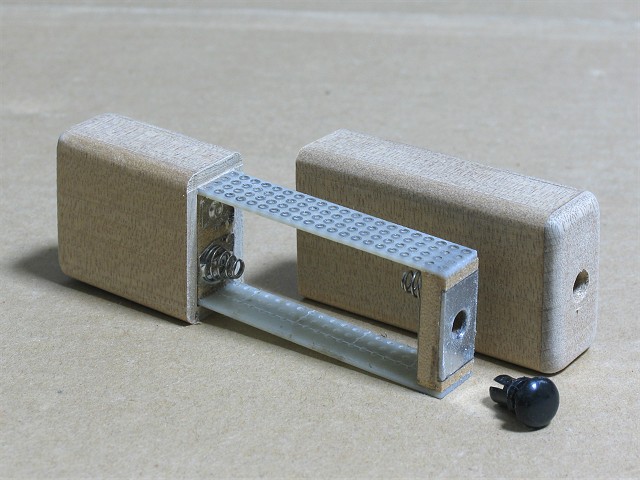 |
|
|
そして全ての角をボーズ面ビットで丸めてスポンジ研磨剤で仕上げ研磨を施しました。
|
|
|
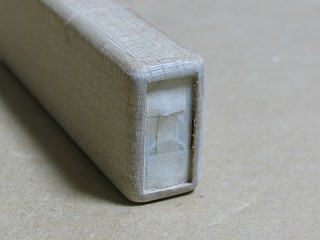 |
|
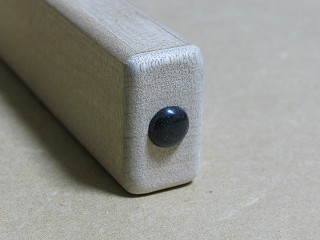 |
|
|
シンプル イズ ベストの好例?みたいな前面の感じです。
|
|
同様に背面です。 真っ黒ではない中間色のプッシュリベットがあると良いのですが?
|
|
|
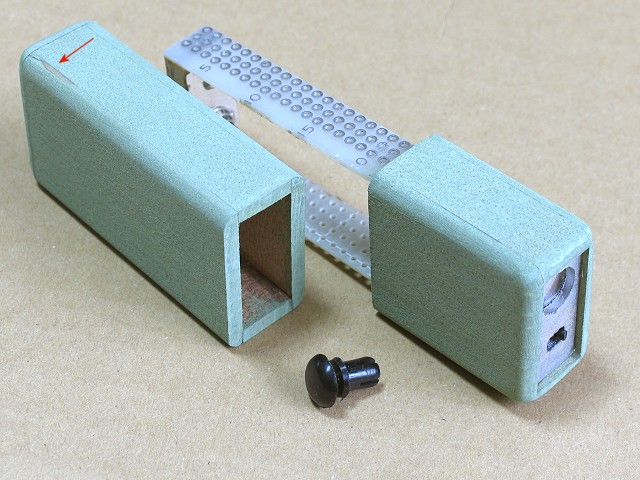 |
|
|
ポアステイン ミストグリーン原液のままによる着色が終わったところですが、木材の欠け部分に埋まったエポキシ接着剤があったのを発見。(矢印の先) 今更削るわけにも行かずそこだけは着色できませんから目立ってしまいます。
|
|
|
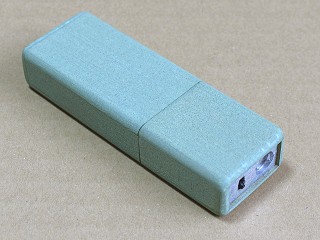 |
|
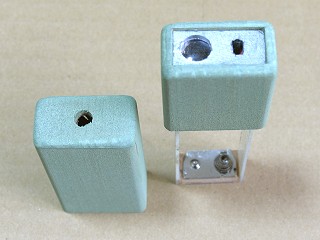 |
|
|
この角度には幸い削り忘れの接着剤はありませんでした。
|
|
24時間寝かせて完全乾燥後ニス塗り作業となります。
|
|
|
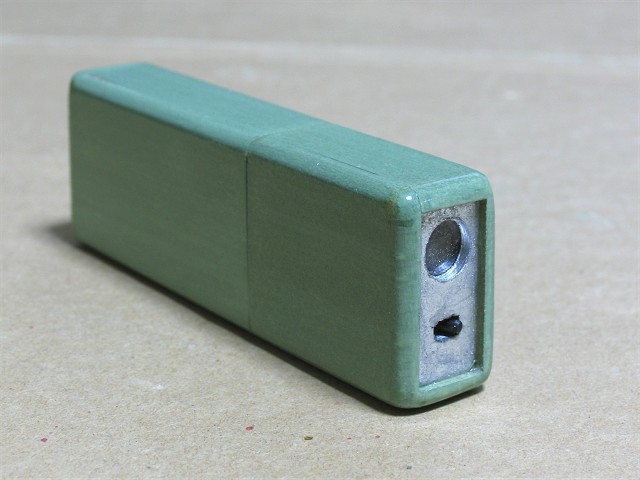 |
|
|
1次塗装が終わりました。 あちこちに色の斑があって完成度はあまり良くありません。 2作目ということで油断した結果かもしれません。
|
|
|
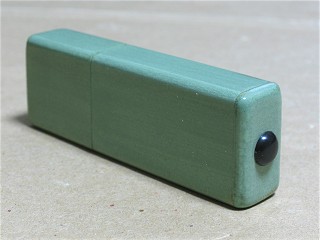 |
|
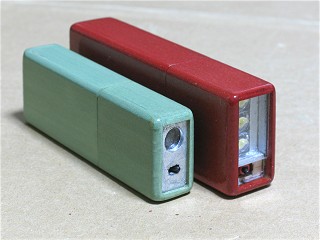 |
|
|
後ろからの眺め。 プッシュリベットによるロックはまあまあですが、リベットの色は何とかして欲しいところです。
|
|
コンパクトLEDランプ 1とのツーショット。 このかわいらしさと電池寿命の長いこと(後でテストしますが、予測は20時間以上。)が身上です。
|
|
Copyright (C) 2001-2019, Vic Ohashi All rights reserved.