|
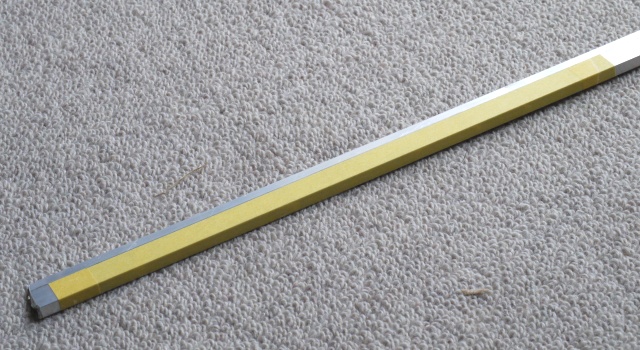 |
|
|
購入したL字型のアルミ押出材は幅が15mmありますので、10.5mmに、長さを235mmに切断します。 写真の黄色いのがマスキングテープでマスキングテープで覆った部分を使います。 切断には電動刃研ぎグラインダーを使います。
|
|
|
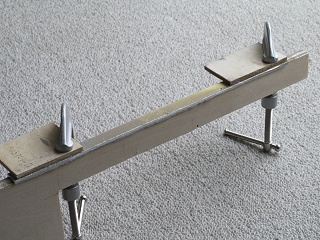 |
|
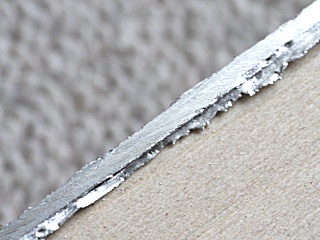 |
|
|
折曲り防止のため端材にクランプで固定して刃研ぎグラインダーで少し大きめに(0.3mm前後)切断しました。
|
|
切断面はこんな具合です。 バリも沢山ついていますので、ヤスリで削りながらドンピシャ寸法に追い込みます。
|
|
|
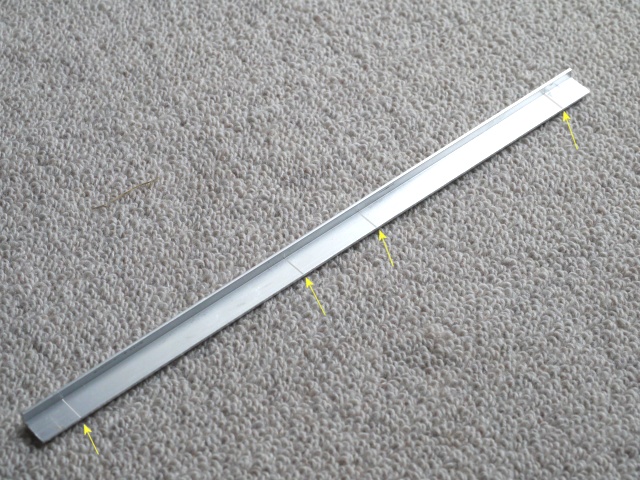 |
|
|
合計4箇所の(矢印先)谷折り部分となる部分のケガキをします。 これは曲げた後の出来具合に非常に影響しますので十分な注意が必要で、シャープペンでは太すぎて適切ではありません。
|
|
|
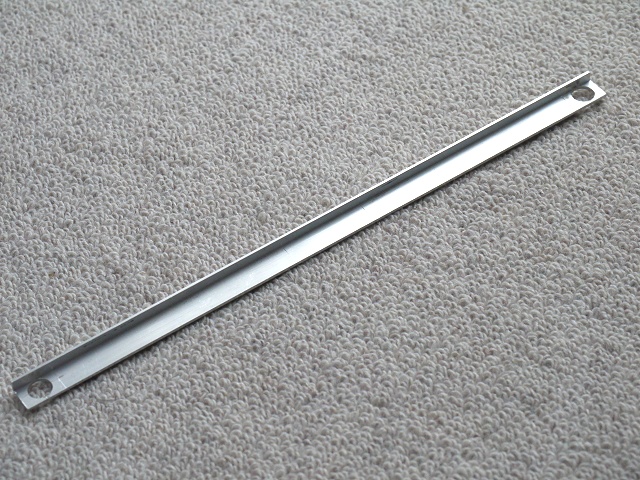 |
|
|
それと両端にミニヘッドフォーンジャックを固定する8φの穴を開けておきます。 これはパネルにもあく穴と重ねてナットで共締めします。
|
|
|
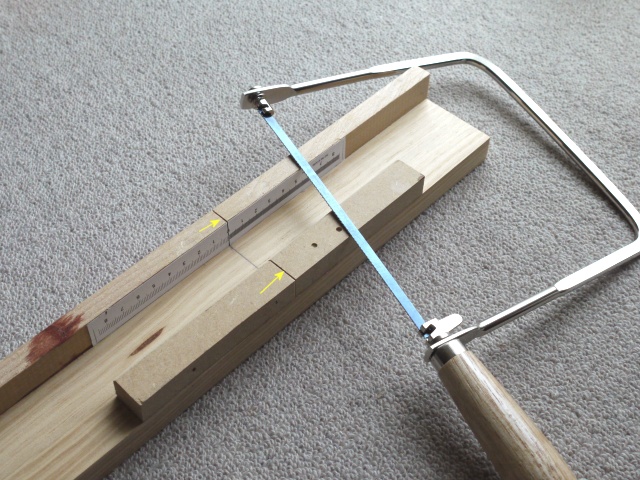 |
|
|
2回加工に失敗した後に加工精度を上げるために考えたジグで、アルミ板切断用糸ノコ刃と共に使います。 糸ノコ刃の厚みは実測で0.6mm、アサリも殆んどないので0.65mm程度の細い切り幅になります。 深さを0.3〜0.5mmになるようにすれば、その溝部分が強制的に折り曲がります。 矢印先は0.6mm幅の溝になっていて、横ブレを抑えます。
|
|
|
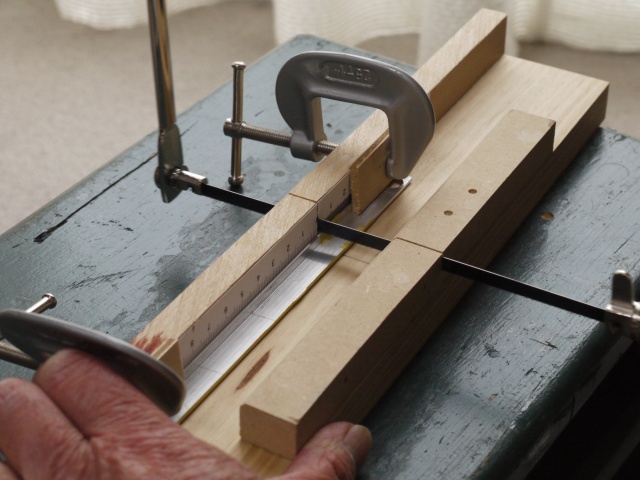 |
|
|
実際に溝を切っていますが、真ん中の126mmの間は2mm幅を狭くするために先ず2mm長の切り込みを入れています。
|
|
|
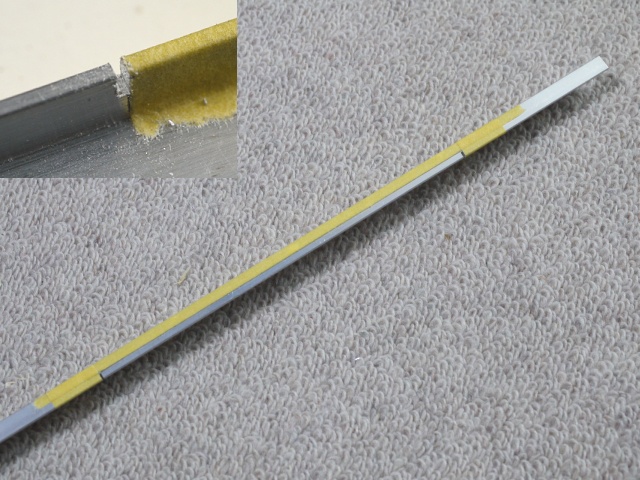 |
|
|
大きな写真では判りにくいですが2箇所の2mm長の切り込みを入れたところで、マスキングテープで囲まれた細い部分を削ります。 左上の写真はその部分のクローズアップです。
|
|
|
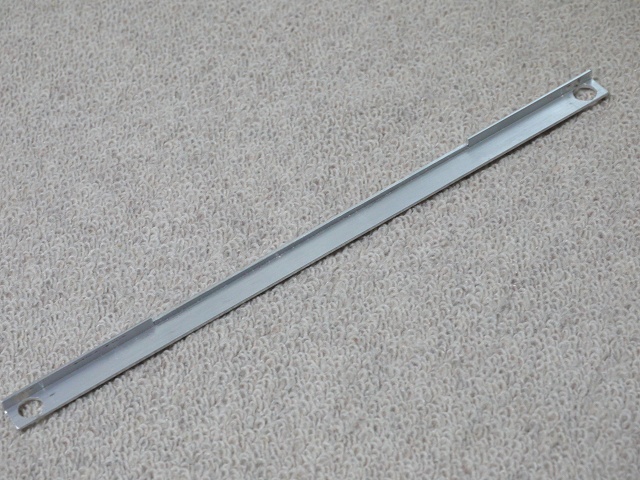 |
|
|
2mm幅の削り込が終わりました。 本来は刃研ぎグラインダーで手際良くしたかったのですが、雨が降りだして外では作業できないのでヤスリで削りました。
|
|
|
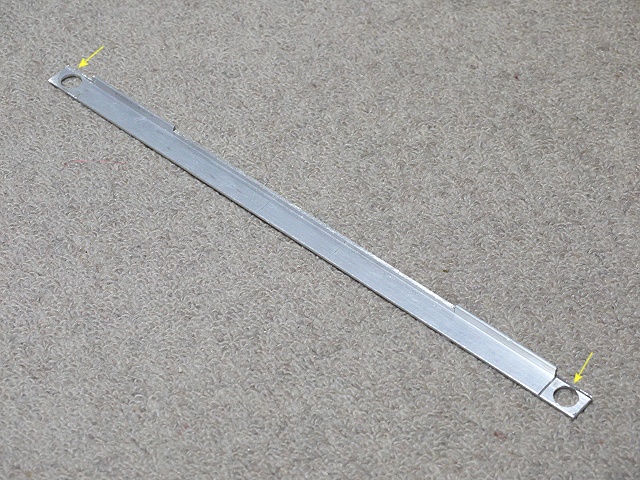 |
|
|
両端の折り返し部分はそのままではミニヘッドフォーンジャックのナットが干渉して締められないので、削り落としました。 これもヤスリで削り落としています。
|
|
|
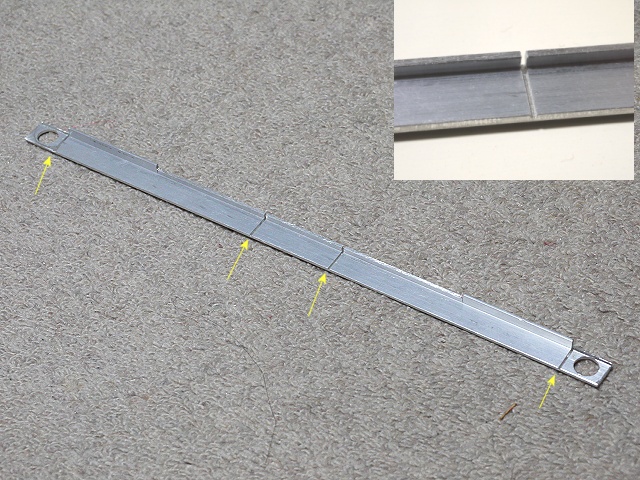 |
|
|
4箇所の折り曲げ部分の溝切りです。 溝の深さは目分量で判断しますが、0.3〜0.5mmになるようにします。 ジグに貼ってあるスケールで溝の位置を十分に確認してから切り込みます。 右上は切り込み後のクローズアップです。
|
|
|
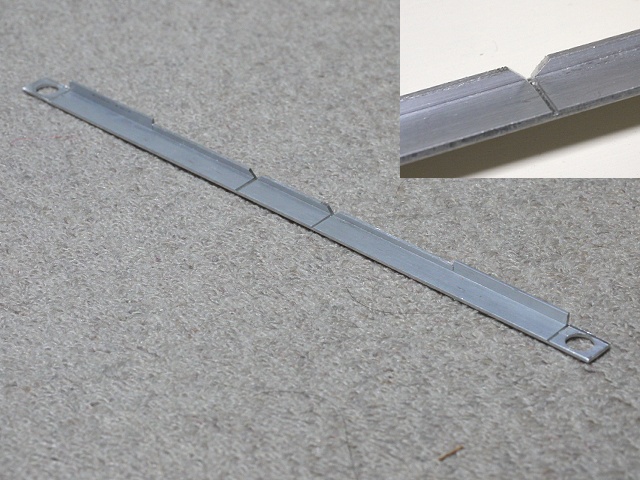 |
|
|
真ん中の2箇所は45度+αの傾斜になるようヤスリで削り込みます。 右上の写真は加工後の写真で、若干削り過ぎの方がよろしい。 これで加工は終了で後は曲げるだけです。
|
|
|
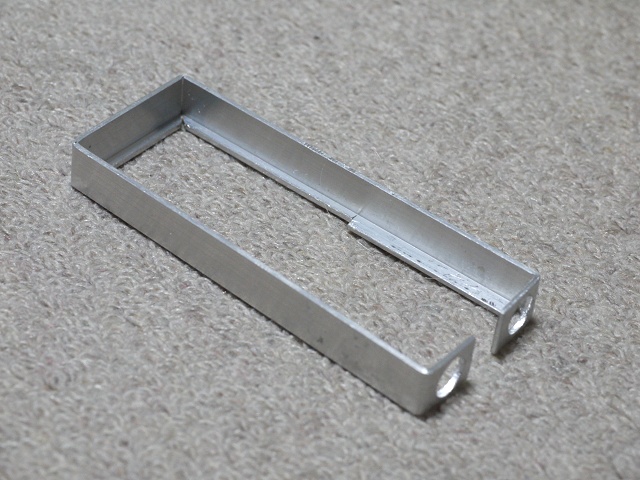 |
|
|
完成したアルミフレーム。 内寸をノギスで測ったところ設計値に対し-0.2mmの結果で満足すべき値でした。 無論基板や電池の組み込みに問題になるような寸法誤差ではありません。 失敗した2回の時には0.5-0.8mmもずれていたことを考えると夢のようです。 まだまだ油断できない加工が続きますが、大きな山は超えた気がします。
|
|
|
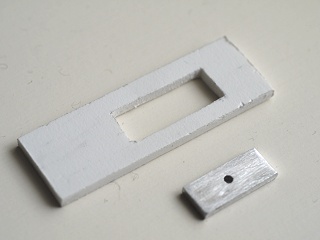 |
|
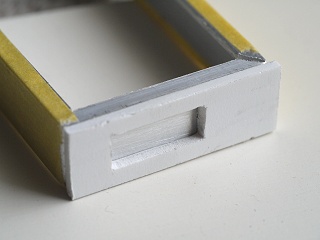 |
|
|
2mm厚発泡塩ビ板と1.5mm厚アルミ板を加工して作りました。 塩ビ板の外寸は0.1mm以下の誤差で加工されています。 アルミ板の中央にはケース固定の穴部分に1.5mmの穴をあけました。
|
|
2mm厚塩ビ板を小さく切った両面接着テープでアルミフレームに仮固定しました。
|
|
|
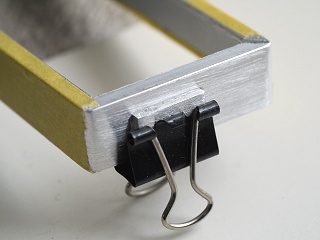 |
|
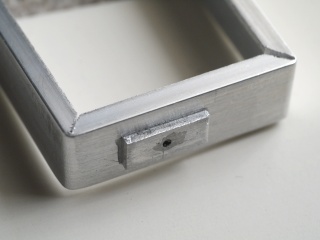 |
|
|
塩ビ板の穴の中央にアルミ板をエポキシ接着剤で固定し、接着剤が硬化開始後に塩ビ板は外します。
|
|
接着が終わったケース固定ネジのアルミ板。 この部分の厚み合計は2.5mmになりますので、十分安定した雌ネジになります。
|
|
|
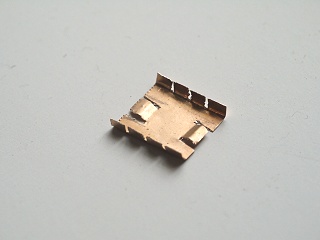 |
|
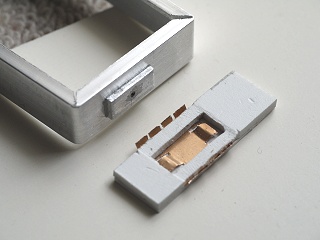 |
|
|
0.1mm燐青銅板をこんなふうに切断して加工します。 4つの爪が並んだ2列はアルミ板に確実に接触し、中のくの字に曲げた部分は確実にアルミフレームに接触します。
|
|
燐青銅板はこのように2mm厚発泡塩ビ板にまたがるように取り付け、この裏に1mm厚塩ビ板を貼り付けます。 これがアルミフレームの突起部分に被さります。
|
|
|
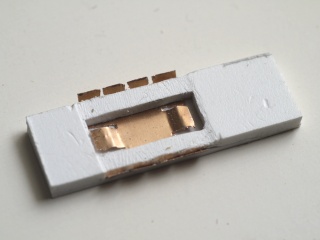 |
|
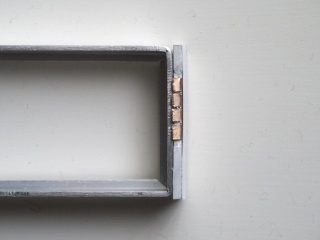 |
|
|
断面がくの字状に曲げた部分がアルミフレームをケースにネジどめした時に当たり電気的に接続されます。
|
|
4枚のフィンが並んだ部分は後ほどアルミ側板を裏板に接着すると電気的に接触してくれます。
|
|
|
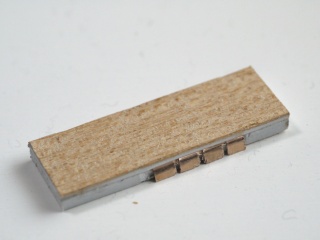 |
|
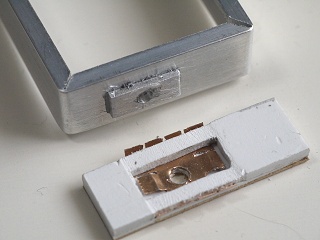 |
|
|
1mm厚発泡塩ビ板を貼った面には木口テープを貼ってやります。 木製側板はアガチスですので違う木材ですが、色みや木目が似ている物を使いました。
|
|
止めネジ穴は直径1.5mmでしたが、アルミフレーム側は2.5mmに拡大し、裏板には3.2mmの穴をあけました。 そしてアルミフレーム側はM3の雌ネジを切ります。
|
|
|
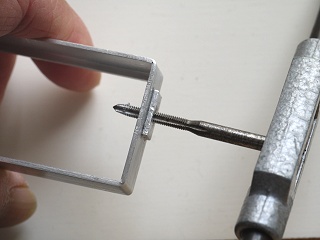 |
|
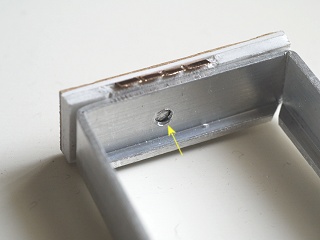 |
|
|
アルミフレーム側の2.5φの穴はM3の雌ネジにすべくタップでネジ切りをします。
|
|
その雌ネジに超薄のネジを締め込みますが、ネジの先がフレームの内側に飛び出さないよう切断しておきます。
|
|
|
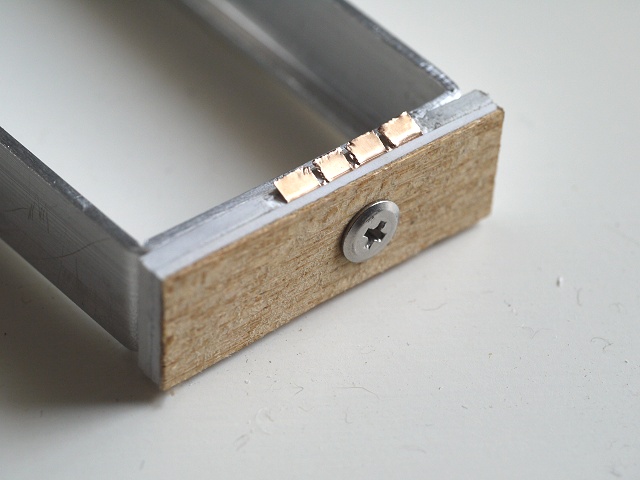 |
|
|
アルミフレームに裏板をネジどめしたところです。 これでケースの固定部分とアルミ側板をGNDに確実に接続する部分の細工が終了しました。
|
|
|
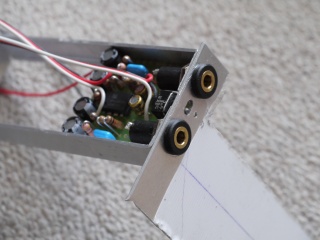 |
|
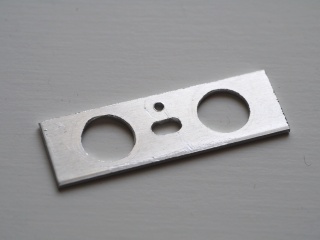 |
|
|
アルミフロントパネルの加工はその中にある4つの穴を加工してから周りを切断して作りました。 その方が中の穴あけがやり易いためです。 この写真は穴あけが終わったので、基板を当ててみて確認しているところです。
|
|
そして周りを切断してフロントパネルの加工が終わりましたが、小判状の穴(2.5 x 5.0mm)の成形だけで2時間近く掛かっています。(焦って作業すると削りすぎる傾向があり穴が大きくなりやすいので、ほんの少し削ってはノギスで確認しながら進めるため。)
|
|
|
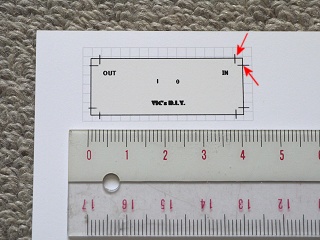 |
|
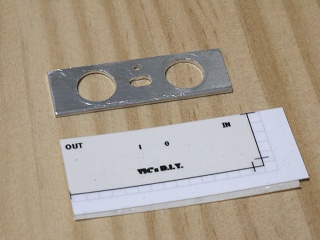 |
|
|
穴に貼り付ける紙はマット紙を使いましたが、作画は例によってExcelで、その後Paint Shop Proに取り込んで画像調整、大きさの微調整をして印刷し、乾燥後にアクリルラッカースプレイ塗料で3回塗りしています。 これは切断前ですが、矢印先の短い線を結んだ線が実際の大きさになります。
|
|
紙の裏に両面接着テープを貼り付け上と左だけ線に沿って切断し、貼り付けの準備が完了したところです。 接着剤で貼るのは伸び縮みが出やすいので両面接着テープとしています。 貼り付けた後に先の細いカッターナイフで、穴の部分を切り抜きました。
|
|
|
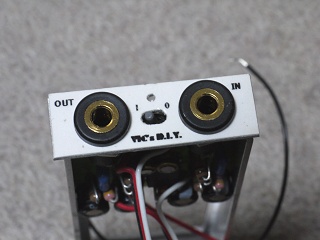 |
|
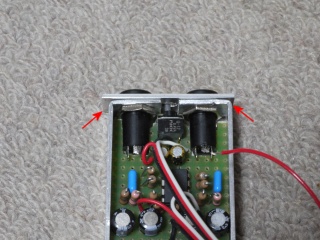 |
|
|
出来上がったフロントパネルをアルミフレームとミニヘッドフォーンジャックで共締めしました。 この方向から見ると一見問題が無さそうに見えますが、VIC's D.I.Y.の文字が滲んで一部繋がってしまいました。
|
|
この方向から見るとフロントパネルの横方向が0.5mmほどずれています。 これは修正しないとなりません。 またトグルスイッチのレバーの出が少なすぎて爪で操作するのが困難ですのでこれも追加加工が必要です。
|
|
|
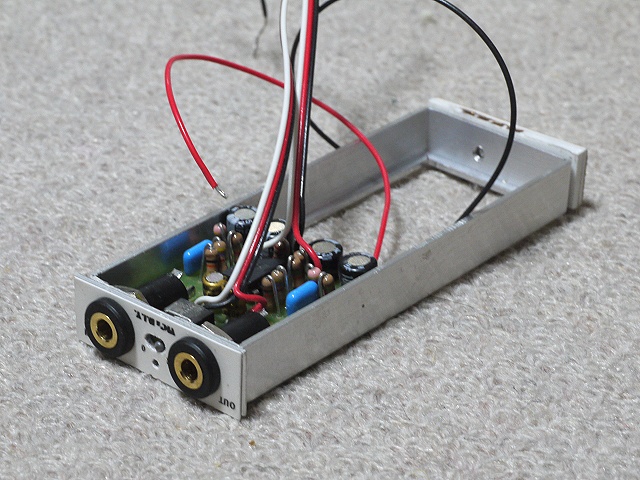 |
|
|
2箇所の修正・追加加工がありますが修正は簡単に出来る範囲ですので、目論見通りに作業は進んでいると言って良いと思います。
|
|
|
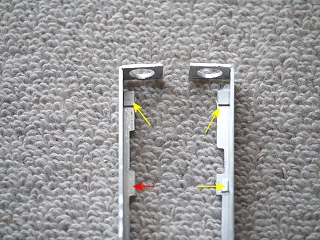 |
|
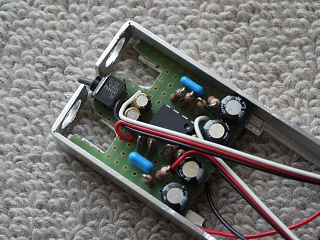 |
|
|
黄色矢印先に1mm厚の発泡塩ビ板を切って貼り付けました。 赤矢印部分は電池のプラス側に繋ぐワイヤーが通り太さが1mmですので、ワイヤーがスペーサーとなります。
|
|
それら4箇所にゼリー状瞬間接着剤を塗って基板を貼り付けました。
|
|
|
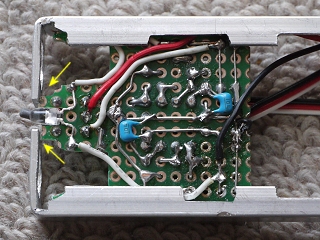 |
|
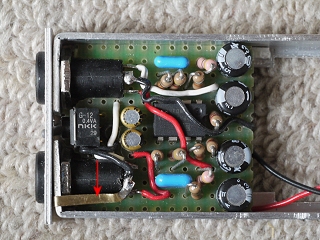 |
|
|
裏側から見ていますが、矢印の先の基板部分は1mm削りましたのでトグルスイッチのレバー先端は表面に1mmほど出るようになり、スイッチの操作が楽になっています。
|
|
ミニヘッドフォーンジャックを固定し配線を済ませました。 またアルミフレームとケースのアルミ側板をGNDに繋ぎ静電シールド効果を持たせるため、赤矢印先の幅の狭い真鍮板がフレームとヘッドフォーンジャックのGND端子を接続しています。
|
|
|
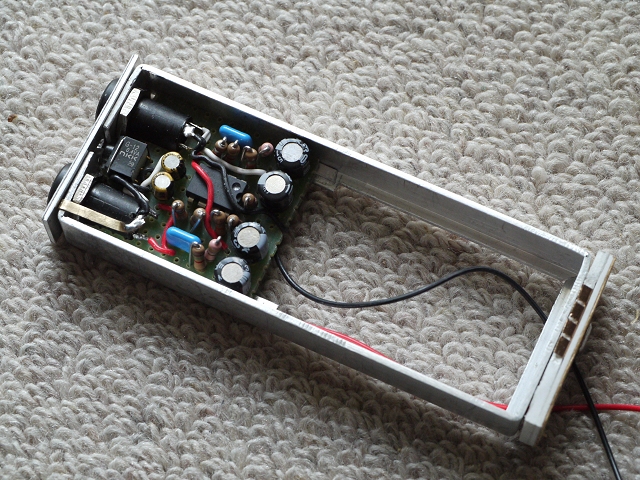 |
|
|
アルミフレームには大きな空間が残りました。 ここに単四電池3本が収められます。 ケースをギリギリまで薄くするために底板もありませんので、電池はプラス/マイナスの電極で保持しないとなりません。
|
|
|
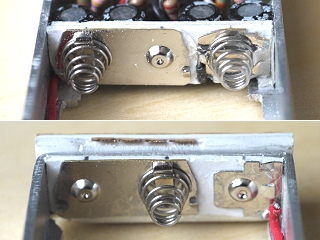 |
|
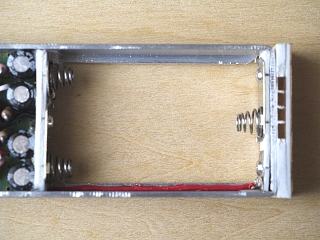 |
|
|
電池ホルダーの電極はゼリー状瞬間接着剤で1mm厚発泡塩ビ板に貼り付けました。 上側が前側、下が後ろ側の写真です。
|
|
完成した電池ホルダー。 ご覧のとおり素通しのままですが、電極だけによる電池の保持は意外に安定しており、強く振らない限り電池が脱落することはありません。
|
|
|
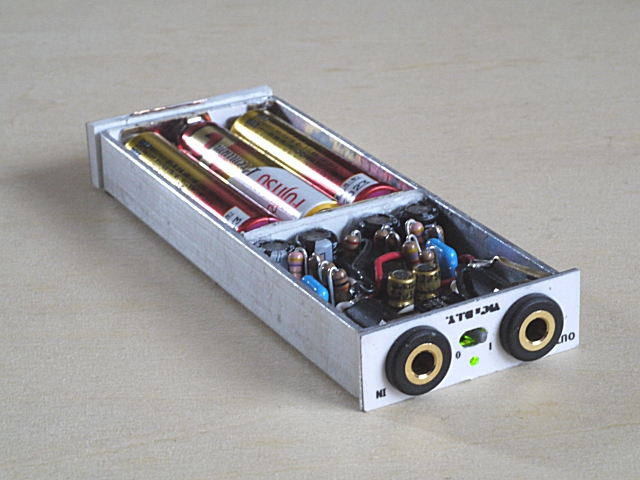 |
|
|
完成した本体に電池を装填し通電しました。 無論動作は完璧ですので、これにiPod Nanoと16Ωのイヤーフォーンを繋いで連続動作テストに入ります。 この面の配線とアルミ側板間のショート防止のため、アルミ側板の内面に0.2mm厚のポリプロピレーンの板を貼り付けます。
|
|
|
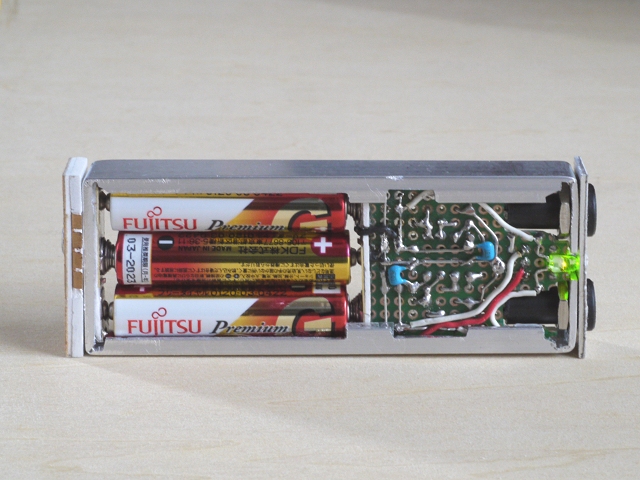 |
|
|
背面はこんな具合です。 基板から出ているワイヤーは表面に飛び出ることもなくうまく収まりました。 そしてこの面には0.2mm厚のポリプロピレーンの板を全面に貼り付け、ショート防止とします。
|
|
|
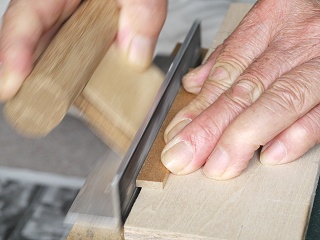 |
|
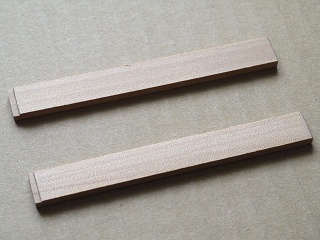 |
|
|
3mm厚アガチスの板を所定の幅より0.5mm大きく切断後、カンナ、ヤスリで寸法を出します。 これは自作直角研磨器で最後の寸法差し研磨をしているところです。
|
|
切断、寸法出しの研削・研磨が終わった2枚の側板。 フロントパネルを受ける欠き込みもしてあります。 この後接着剤の選択でつまづき2日間費やしました。
|
|
|
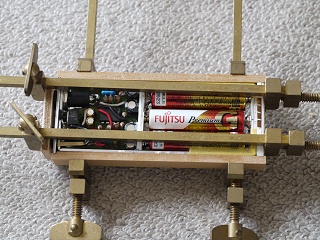 |
|
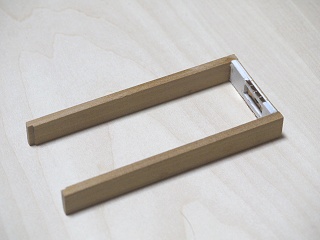 |
|
|
背面板をネジ止めしたアンプ本体を板2枚で挟み接着します。 接着剤はゼリータイプの瞬間接着剤ですが、ゼリー全体が完全に固まるのに時間が掛かりますので、ご覧のようにハタ金4本を使って圧着保持しています。
|
|
接着が終わったケースのコの字部分。 これの両面にアルミ板を貼るまでは接着部分は剥がれやすいので要注意です。
|
|
|
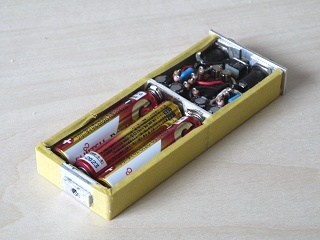 |
|
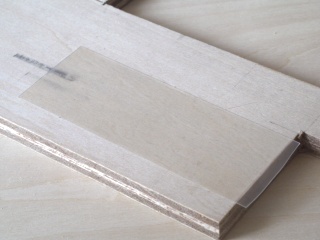 |
|
|
アルミ板を貼り付けるときにもアンプ本体を挟み込みますが、接着剤でアルミフレーム部分が」くっついてしまわないようマスキングテープでフレーム全体を覆いました。
|
|
ケース内寸とアルミフレーム外寸の差は極く僅かなので、問題がないかどうかの確認を一応しておきます。 先ずショート防止の0.2mm厚ポリプロピレンシートを貼り付けました。 |
|
|
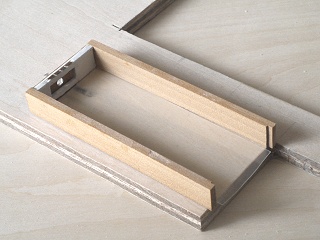 |
|
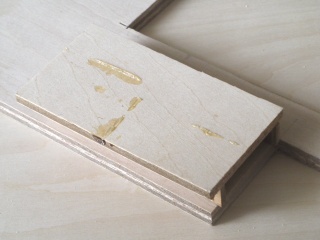 |
|
|
貼り付けたPPシートを覆うように(載せては駄目)コの字のフレームを置きます。
|
|
そしてその上に板を載せてやります。 これでテストの準備が整いました。
|
|
|
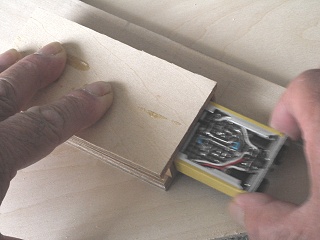 |
|
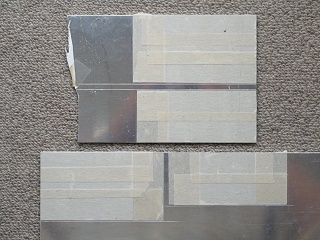 |
|
|
アンプ本体をこのように奥まで挿入してみます。 全く引っかからなければOKで、その後出し入れを数回して念を押しておきます。 感覚では0.2mm程度の僅かな隙間が残っていますが、実際にはマスキングテープの厚み分(0.1mm)増えます。
|
|
1.5mm厚アルミ板に側板を罫書き傷防止のマスキングテープを貼ったところで今週はおしまい。 大きな2枚はAD8397仕様の側板です。
|
|
|
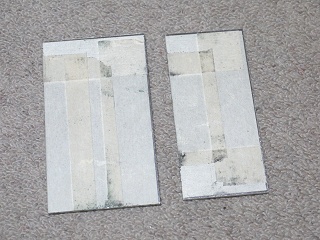 |
|
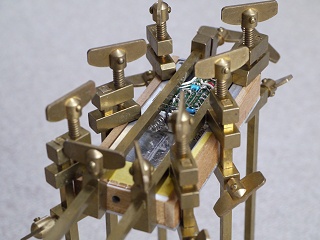 |
|
|
切りだして寸法出しをしたアルミ側板ですが、このモデルで使うのは右側です。
|
|
接着直後の圧着保持状態で、まるでハタ金のジャングルです。
|
|
|
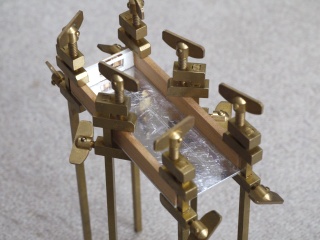 |
|
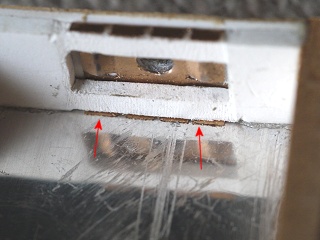 |
|
|
15分後に厚み方向のハタ金だけ残して完全硬化のために6時間寝かせます。
|
|
電気回路本体のGNDとアルミ側板を電気的に繋ぐ燐青銅板の爪の部分がチラリと見えます。
|
|
|
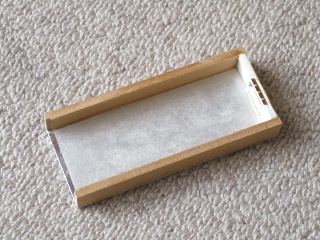 |
|
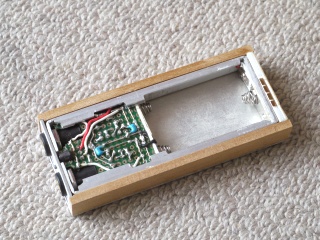 |
|
|
ショート防止のP-Pシートを内側に貼り付けました。
|
|
そしてフロントパネルがごく僅かの隙間をもって収まるよう調整研磨をしました。
|
|
|
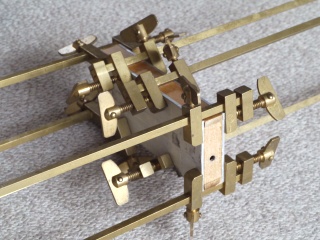 |
|
 |
|
|
そしてもう1枚のアルミ側板を接着します。 今回は内寸を調整するスペーサーは不要です。
|
|
箱状に組みあがったケース。 中に飛び出ているかもしれない接着剤を削り取りたいのですが?
|
|
|
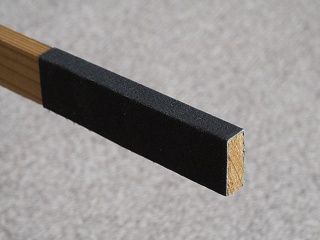 |
|
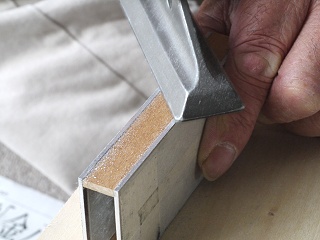 |
|
|
細い棒に#240のサンドペーパーをコの字状に貼り付けたもので削り落としました。
|
|
アルミ板は木の板より0.2〜0.3mm出っ張っていますからアルミ板と木の板が同じ高さになるよう替刃式ヤスリで削ります。
|
|
|
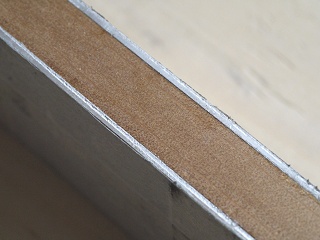 |
|
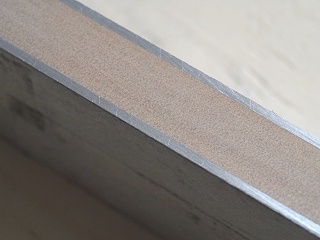 |
|
|
これは替刃式ヤスリで削る前です。
|
|
削った後はこうなります。 木の部分が妙な色ですが細かなアルミの削りくずが木目に入ってしまうためで、後程洗って落とします。
|
|
|
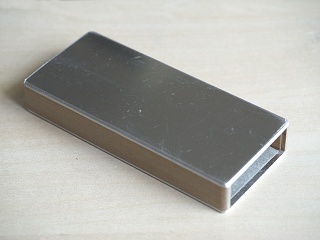 |
|
 |
|
|
その後#240、#400のサンドペーパーで研磨し面取りをしました。 このモデルは胸のポケットに入れて使うことが多いと考えられるので、全ての角を丸くしました。
|
|
そしてアルミ板の面の部分を#400サンドペーパーでヘヤーライン加工しました。(加工法詳細はAD8397
仕様をご覧下さい。)
|
|
|
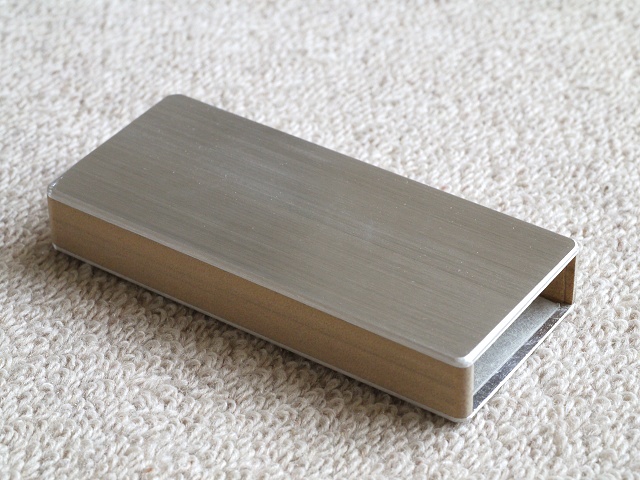 |
|
|
木目にアルミの細かい研摩カスが詰まって汚らしい色になっているので、水洗いして乾燥しました。 ヘヤーラインが入ってエレガントな感じになったと思います。 これでケースの加工・組立が終了しました。
|
|
|
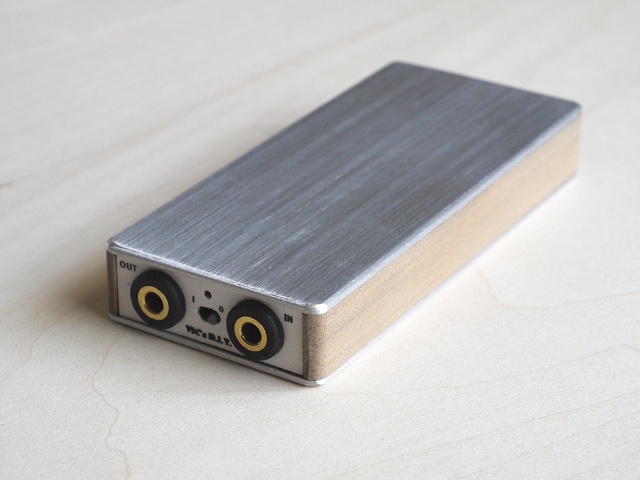 |
|
|
アルミフレームアセンブリーを挿入して後部をネジ止めしました。 この姿は木部の色味以外は最終の状態です。
|
|
|
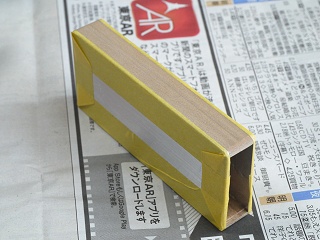 |
|
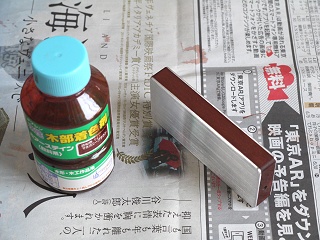 |
|
|
マスキングテープでアルミ板の厚み部分を覆った所。 アルミだけを覆うのが重要ですので、落ち着いての作業が肝要です。
|
|
ポアステイン マホガニーブラウン色で着色しました。
|
|
|
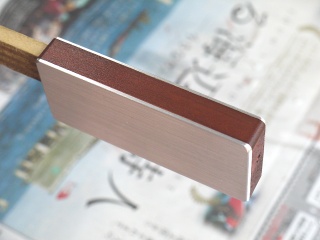 |
|
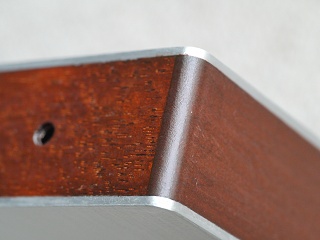 |
|
|
アルミ板の面を除いて水性ウレタンニス透明クリヤー6回塗りです。 その後つや消しクリヤー1回塗りとしました。
|
|
コーナーはこんな具合ですが、私の大好きなニブーイ光り方をしています。
|
|
|
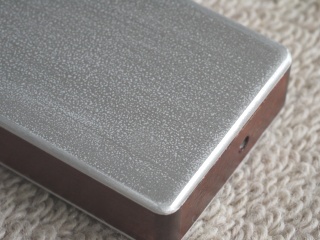 |
|
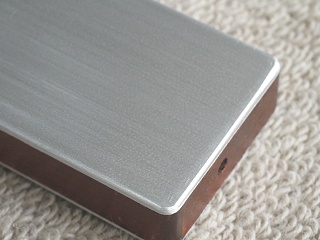 |
|
|
アルミの面部分はアクリルラッカースプレー2回塗りとし完全乾燥後につぶつぶを#600空研ぎペーパーで半分削り落としました。 まだつぶつぶが見えますが?
|
|
その上に希釈した水性ウレタンニス透明クリヤーを2回塗り、最後につや消しクリヤーを1回塗ってやるとつぶつぶも殆ど消えてヘヤーラインが映えます。
|
|
|
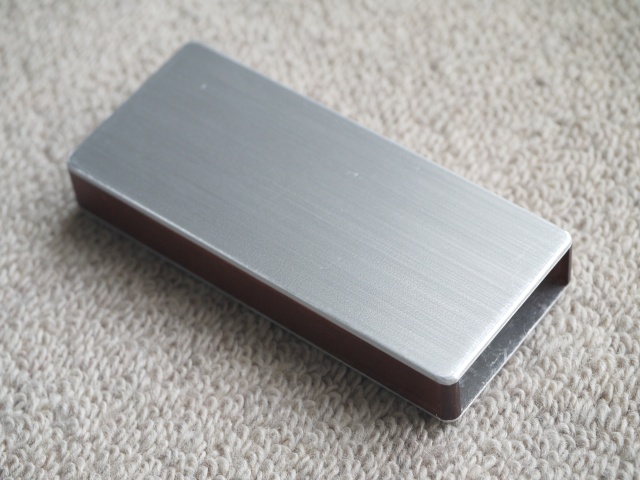 |
|
|
難物だったアルミ板の面の塗装がうまく行きほっとしました。(塗装しないとこの美しさは短時間のうちに腐食で失われますので。)
|
|
|
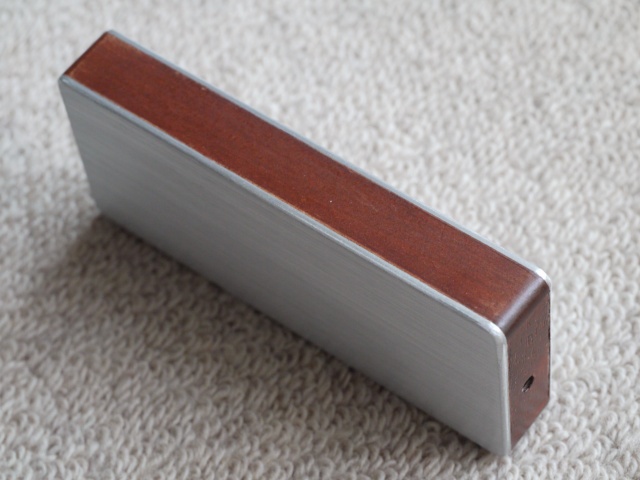 |
|
|
マホガニー色と銀色のアルミ板の厚みによる線とのコントラストが大変綺麗です。
|
|
|
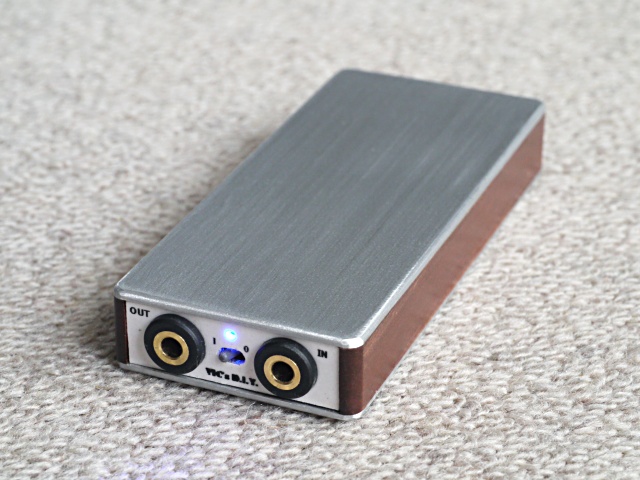 |
|
|
そしてヘッドフォーンアンプユニットを収めました。 今後胸のポケットにiPod Nanoと一緒に収まり心地よい音楽を提供してくれるでしょう。
|
|
これで2種類のポータブルヘッドフォーンアンプの製作が終了しました。 コダワリに更にコダワリが重なり構想から何と1年も掛かっていますが、何れも省エネ度が高く、満足度の高い物になったと自負しています。 第一世代のポータブルヘッドフォーンアンプそして今回作った2つのモデルの比較は次をご覧下さい。Copyright (C) 2001-2019, Vic Ohashi All rights reserved.