|
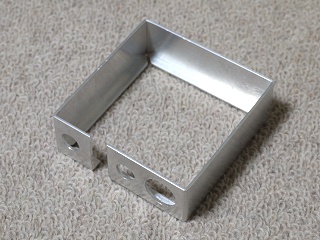 |
|
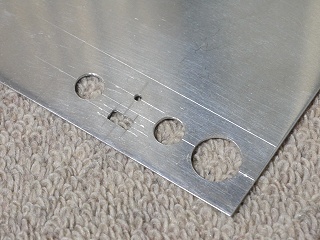 |
|
|
フレームの前面にボリュームツマミが通る穴(13φ)、2個のフォーンジャックが通る穴(8φ)をあけます。 加工位置と大きさはかなりシビアに保たないと、組み上げてゆくうちにとんでもないいびつな物になりかねませんので、±0.2mm位の精度を目指しました。
|
|
こちらはフロントパネルの穴加工でフレームと同じ穴以外にシーソースイッチの頭が出る穴(3.5 x 6.5mm)とLEDの窓穴(2φ)をあけます。 こちらは±0.2mm以下の加工精度を目指しました。
|
|
|
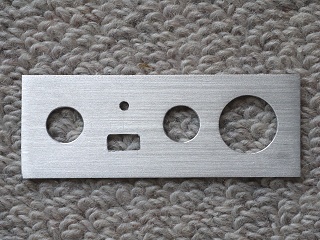 |
|
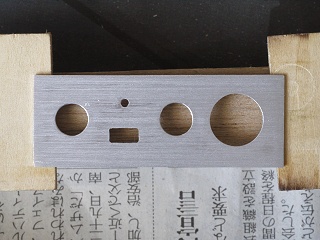 |
|
|
穴あけが終わったら所定の寸法に切断し、#120ペーパーでヘヤーライン加工しました。
|
|
そして水性ウレタンニス透明クリヤーを2回塗ってやります。 この後の文字入れは完全乾燥後としますので、12時間放置しました。
|
|
|
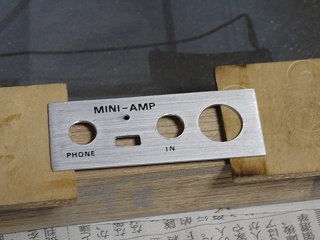 |
|
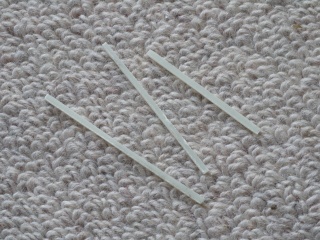 |
|
|
文字入れはインスタントレタリングですが、小さい文字なので、省略した表現(Headphone → PHONE、Input → IN、電源スイッチとボリュームは無表現)としました。
|
|
プリント基板の端を約1.5mm幅で切断しスペーサーとします。
|
|
|
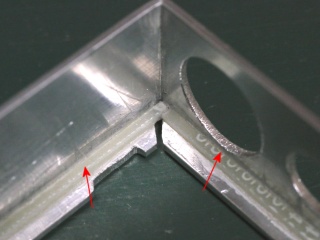 |
|
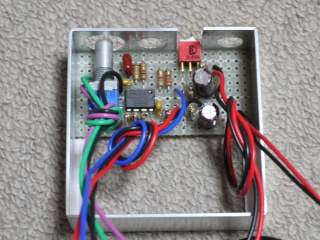 |
|
|
瞬間接着剤を使ってスペーサーを隅に接着します。 矢印の先がスペーサーです。
|
|
そしてプリント基板を挿入しスペーサーに密着するよう抑えて瞬間接着剤を数箇所の隅に沁み込ませて固定します。
|
|
|
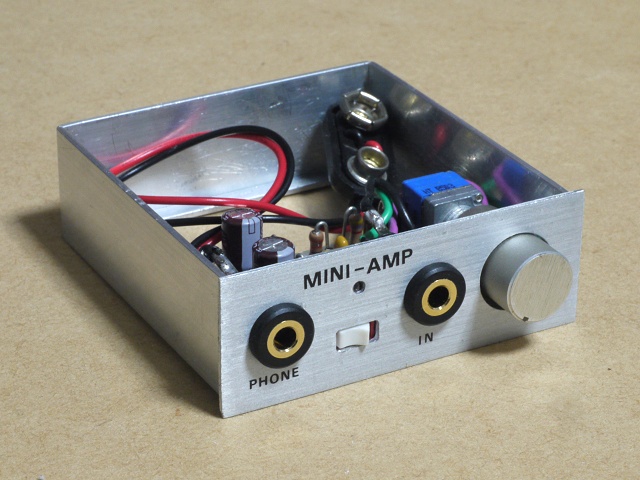 |
|
|
そしてフロントパネルをフレームの上に載せてフォーンジャック2個で共締めします。 そしてフォーンジャックへの結線、LEDの固定と配線が済んで、フレーム内の電機回路部分は完成しました。 これ全体が木製のケースに収まるわけです。
|
|
|
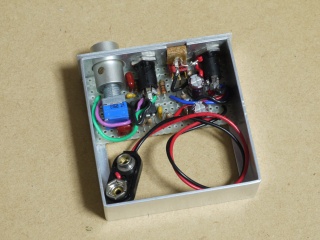 |
|
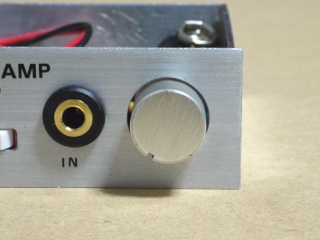 |
|
|
電池を挿入する部分が筒抜けですが、ここを埋めることとケース固定の雌ネジを切る作業がまだ残っています。
|
|
ボリュームツマミは穴を貫通させる構造にしたため、穴の加工精度と位置関係など難易度はきわめて高いのですが、まずまず見られるレベルに仕上がったと思います。
|
|
|
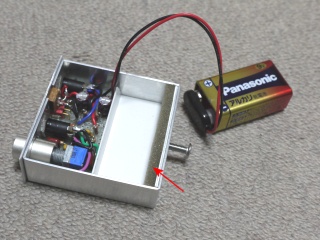 |
|
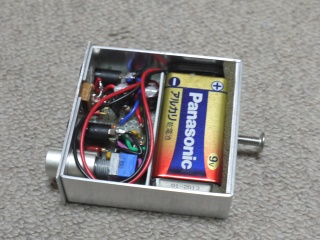 |
|
|
1.5mm厚のアルミ板を底に貼り付けて中央にM4のネジを切り、1mm厚発泡塩ビ板をL型に曲げ、電池受けとして瞬間接着剤で貼り付けました。 そして軽く電池を押さえるためにポリエチレンフォームを貼り付けています。(矢印の先)
|
|
電池を収めるとこんな感じになります。 ネジは例の頭の薄い奴ですが、木製ケースが出来た時に現物合わせで長さを調節します。
|
|
|
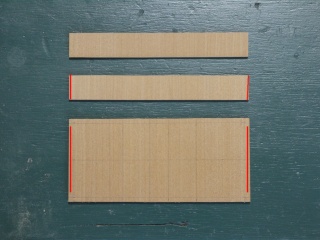 |
|
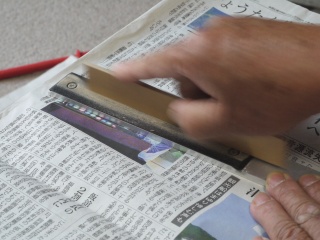 |
|
|
まずノコギリでの切断。 私は翔220(7寸目)を使いました。 上2枚は天板/底板/背面板用で、下は左右の側板ですが、赤線の部分のトリマーによる溝彫が終わったら切り離します。
|
|
細い板2枚の幅出し(20.5mm)は自作の替刃式平ヤスリで行いました。 削られる側が動かされるわけですが、ヤスリは台に容易に抑えられぐらぐら動きませんから好都合です。
|
|
|
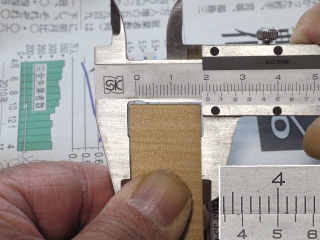 |
|
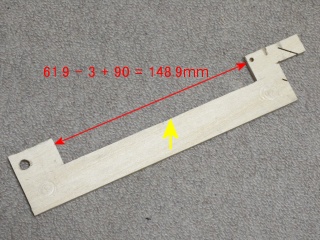 |
|
|
所定の20.5mmドンピシャに成形研摩出来ました。 寸法確認は3箇所で行い確実さを期しています。
|
|
側板に61.9mm幅の溝を切削するためのジグ。 溝幅からビットの直径(3mm)を差し引き、電動トリマー台座の幅を加算すればジグの内寸となります。 また黄色矢印先が板の端から44.5mmとなるようセットすると彫られる溝幅は1mmとなります。 溝の深さは1.1mmとなるよう調節しました。
|
|
|
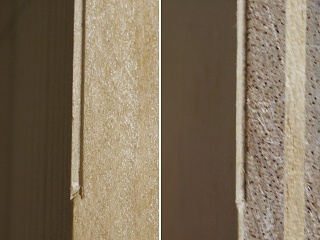 |
|
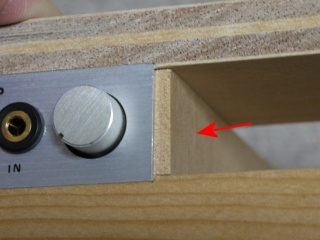 |
|
|
シナ合板(右)とムク板(左)の端材に試しに溝を彫ってみました。 この試し打ちでは溝の端の成形がいまいちうまく出来ていませんが溝幅、深さ共に良好なようです。
|
|
削った溝にフレームのフロントパネルを落とし込んで間に20.5mm幅の板(赤矢印)を挟みました。 ご覧のとおりフロントパネルの嵌り具合や天板、底板との間の隙間の出具合など、ほぼドンピシャで満足すできる状態です。
|
|
|
上の溝切削の調整と確認は、トリマービットの出具合の調整や、ジグの取り付け位置調整などを数回やり直したうえに、
20回近くの試し切削をやってバラツキの出具合の確認をするというかなり慎重なやりかたをしています。
と言うのも削る量は僅かですが、切削許容誤差を限りなく0に近づけたい(目標は±0.05mmでノギスの測定限界値)とい
うかなり無茶な目標設定のためです。
|
|
|
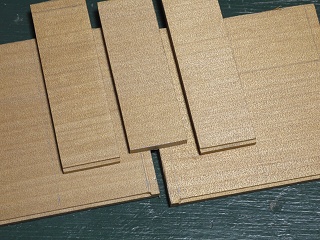 |
|
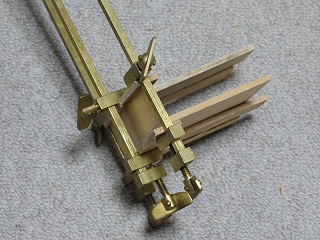 |
|
|
板に予め彫っておくべき溝を電動トリマーで加工したのち、板を切り離しました。 全部で5枚になります。
|
|
底板を側板に貼り付けました。溝と溝がきちんと一致する事と接合角が直角になっている事が肝要で、180mmのハタ金を使って圧着保持しています。
|
|
|
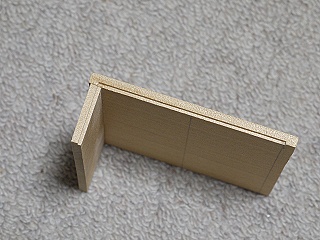 |
|
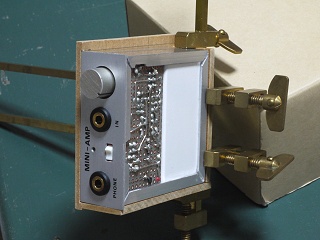 |
|
|
接着剤の硬化を待って2時間後にハタ金を外し、2枚の接着が完了しました。
|
|
次に背面板を貼りつけますが、貼り付け位置はアンプフレームを当ててやると簡単に判ります。 そしてハタ金で圧着保持します。
|
|
|
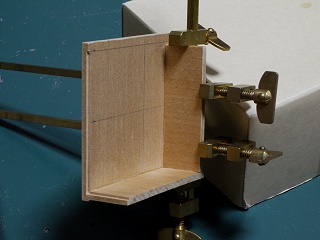 |
|
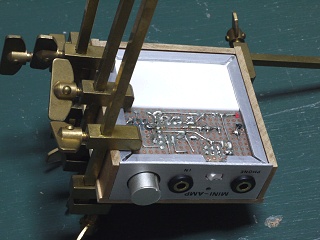 |
|
|
アンプは接着位置関係を確認するために当てていただけであることがお分かりでしょうか?
|
|
その後天板を接着しますが、ここでもアンプフレームは接着位置を確認しやすくするため当てています。
|
|
|
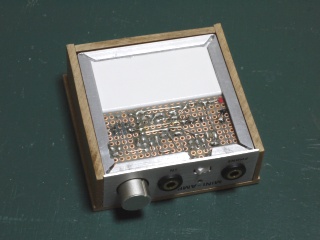 |
|
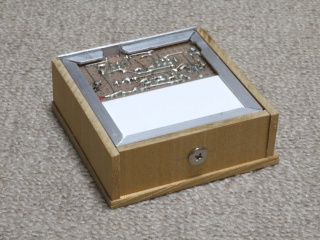 |
|
|
ご覧のようにごく僅かな隙間を残してフレーム本体はケースに収まります。 ここで現物合わせで背面の止めネジが通る穴をあけ、ネジも長さを5.5mm(アルミ板厚が2.5mm + ケース厚3mm)に詰めてやります。
|
|
背面の止めネジ部分の加工も無事終わりました。 頭の薄いネジ(M4)は大変好都合でした。
|
|
|
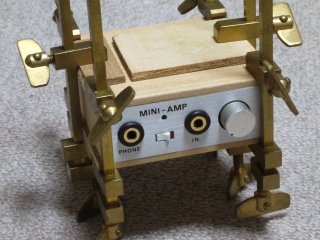 |
|
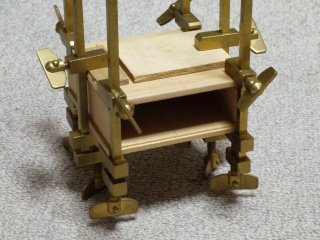 |
|
|
そして残りの側板を接着します。 こんな物に対して!と思うかもしれませんが、6本のハタ金で圧着保持をしています。 また接着位置関係確認のためアンプフレームを装填したまま組み立てましたが?
|
|
手前の2本のハタ金を緩めて抜き出しました。 さもないと万が一内部で接着剤がはみ出たらフレームは接着されてしまい電池交換も出来なくなります。
|
|
|
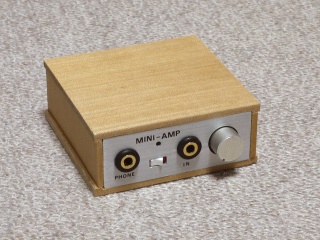 |
|
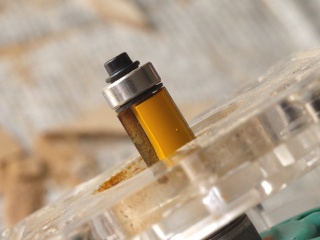 |
|
|
箱の組立は終わりました。 アンプフレームの挿入具合をもう一度確かめます。
|
|
箱の出っ張った部分は傘付き目地払いビット(MB-12.7G)で一気に削り落とします。 この写真に見える銀色のローラー(コロ)の当る面が基準面になります。
|
|
|
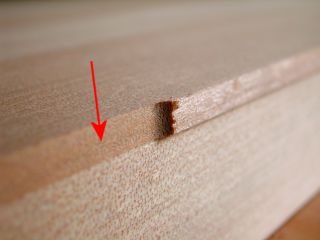 |
|
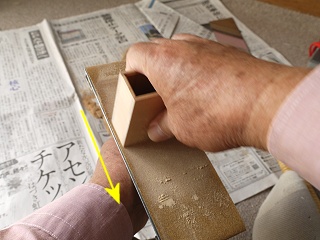 |
|
|
MB-12.7Gで切削した例。 矢印の部分がその下とツライチになりました。 右側はまだ切削されていない部分です。
|
|
切削した面を#120、#240でならしました。 ハンドサンダーを左手で握りヤスリ面が上を向くようにして、研摩する物を右手で掴み向こうから手前に引く時に研摩しています。 研摩の効率は悪いですが、一部だけ削り込んでしまうことがないように思います。
|
|
|
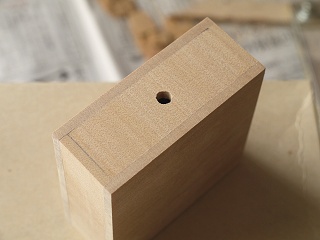 |
|
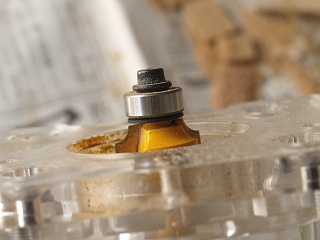 |
|
|
仕上げ研摩が終わったかのような綺麗な面になっていますが、まだまだ。 この後面取り作業に入ります。
|
|
フロントの角を除き、このボーズ面ビット(BZ-10G)で面取りをします。 このボーズ面ビットは半径3.2mmのRとなるように切削します。
|
|
|
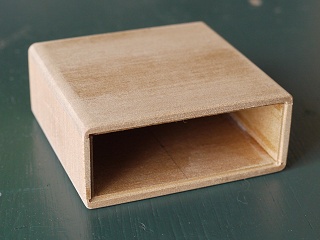 |
|
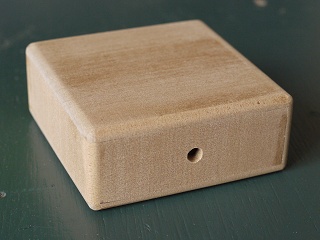 |
|
|
ボーズ面ビットで角を丸く成形後に#240、#400、#600とサンドペーパーを換えて仕上げ研摩としました。 フロントの縁だけは45度の角度で1mm弱削るだけにしました。
|
|
背面はこのような感じです。 木目を生かそうと考えていますからシンプルそのもの。
|
|
|
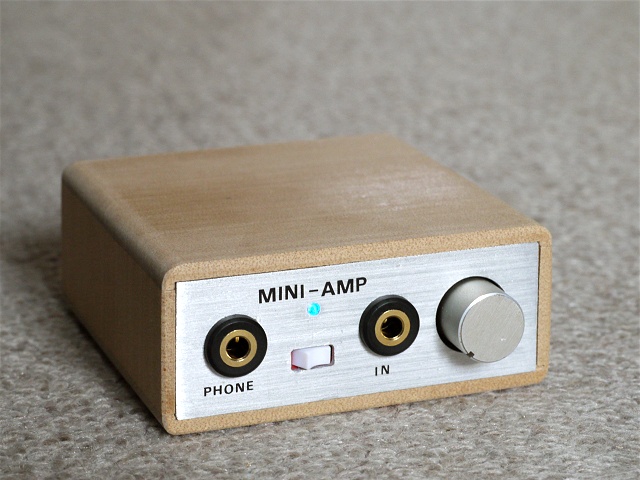 |
|
|
アンプフレームを挿入するとこんな感じでケースだけだと丸みの塊で全体がぼやーっとしていたのが直線と金属面が入るのできりりと引き締まってきます。
|
|
|
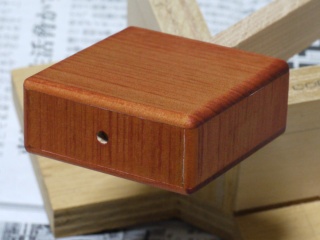 |
|
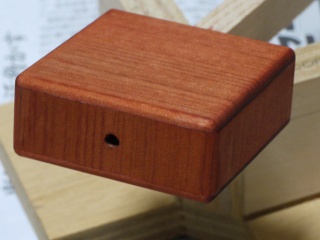 |
|
|
水で3倍に薄めたマホガニーブラウンで着色の一度目です。 3倍にも薄めているにも拘らず随分色が付きます。
|
|
4回着色した状態。 一回目の時よりも濃度が高くなると同時に赤みが増してきます。
|
|
|
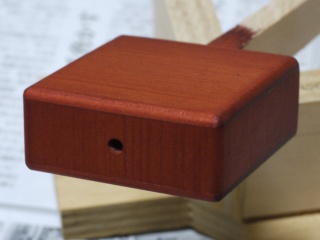 |
|
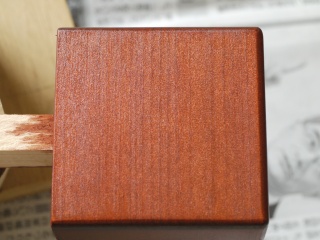 |
|
|
6回目の着色後。 着色濃度が更に高まり赤みも増し、木目が若干目立たなくなってきています。 これで良しとしました。 かなり水を吸い込ましたので一晩寝かせて乾燥させます。
|
|
1回目の塗装後。 目で見てはっきり判るようにざらついています。 木部にニスの大半が吸い込まれて表面の幕を形成する部分が少ないからです。
|
|
|
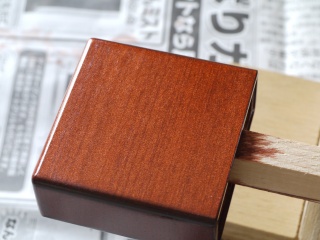 |
|
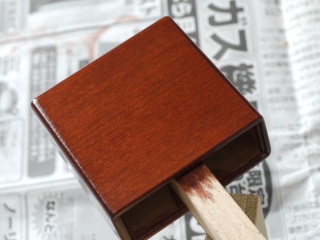 |
|
|
塗膜が出来ないうちに研摩すると着色無しの地肌が出てしまう可能性があるので、研摩せずに2回目のニスを塗りました。
|
|
2回目が乾燥後#400ペーパーで研摩し3回目を塗装。 そして乾燥後に研摩して4回目のニス塗りです。
|
|
|
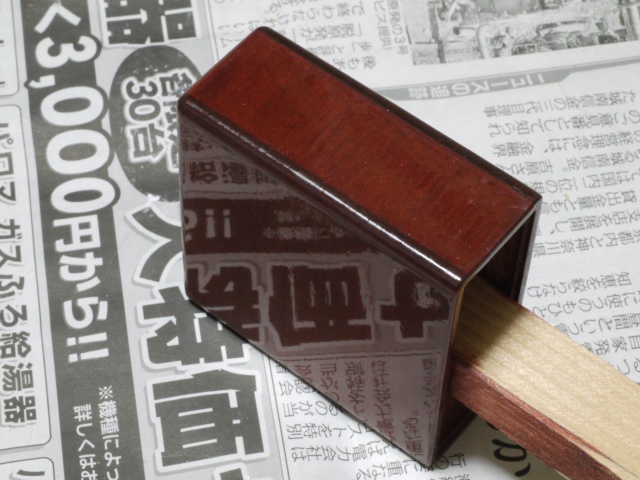 |
|
|
5回目のニス塗りが終わったところですが、不思議なことに塗装前に較べて着色濃度が上がってきています。 無論ご覧のように表面はぴかぴかになり光を良く反射します。 これで最後の艶消しニスの塗装をします。
|
|
|
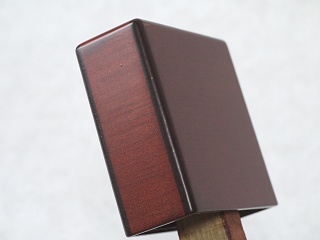 |
|
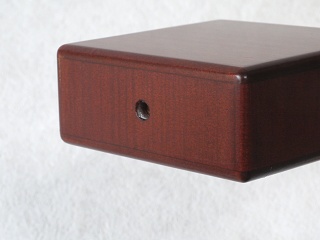 |
|
|
水性ウレタンニス艶消しクリヤーを塗って乾燥中ですが、艶消しクリヤー塗装による見え方を数カットお見せします。 左は側面で右は背面になります。 右の写真では貼り合せた部分が細い黒い線状になって見えますが、接着剤がはみ出てほったらかしにすると白っぽい斑になって出てきます。
|
|
|
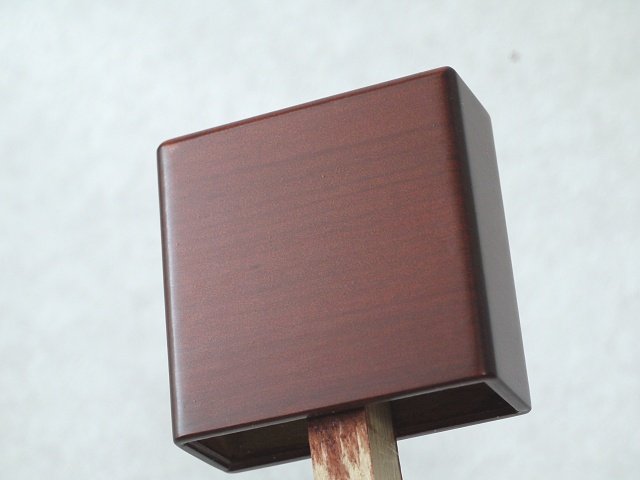 |
|
|
艶消し処理した結果を最も理解しやすいのはこんな見え方でしょう。 この上にある艶ありのピカピカの写真とは雲泥の差で、しっとりとした落ち着き、独特の高級感があります。
|
|
|
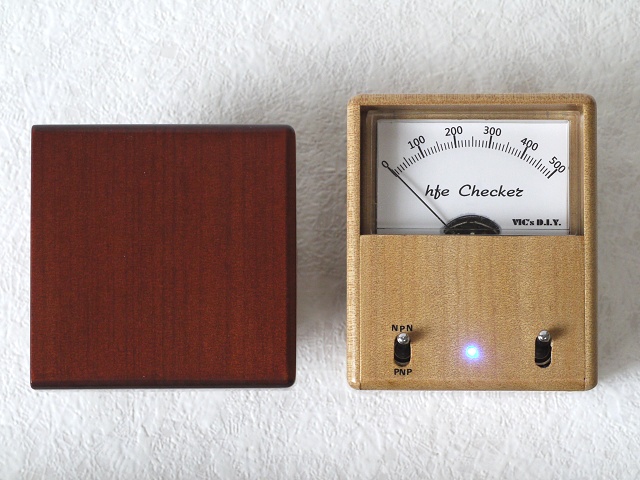 |
|
|
右は同じタイミングで完成したhfe チェッカーですが、同じ材料(アガチス)を使っているにも拘らず、着色のありなしでこんなに見え方が変わります。 従って着色は極めて面白みのある作業でやみつきになります。
|
|
|
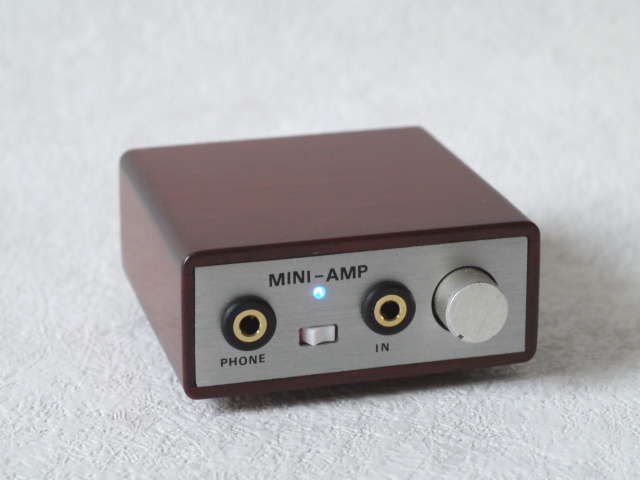 |
|
|
塗装が完了したケースにアンプを装填しました。 これで完成ですが私が頭の中でイメージした格調高い重厚な質感を持つケースが出来上がったと思います。 これで聴く音楽はアンプの実力以上の音色になりこれまた格別ですが、主観の世界の面白みです。
|
|
Copyright (C) 2001-2019, Vic Ohashi All rights reserved.