|
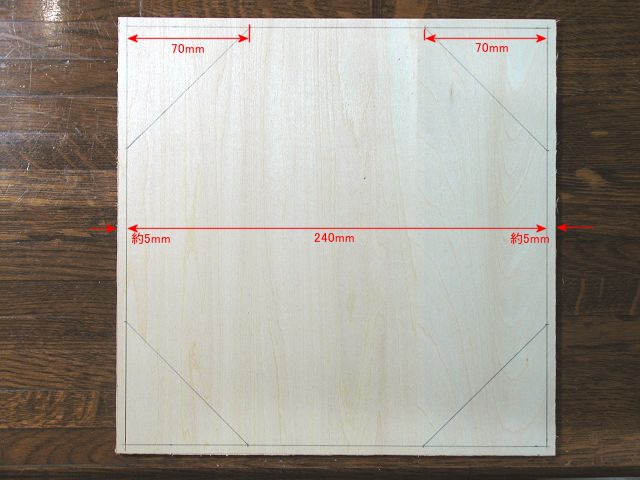 |
|
|
最終寸法より大きめ(ここでは約10mmずつ大きい正方形)に切り出した5.5mmシナ合板の裏面に正方形と八角形の線引きをします。 この線引きの精度はかなり重要です。
|
|
|
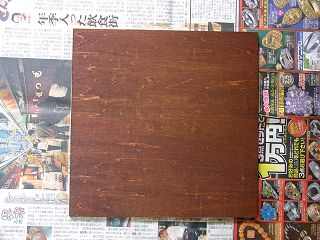 |
|
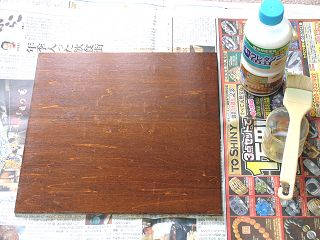 |
|
|
表面に水で2倍に薄めたポアステインを3回塗りとして好みの濃度に仕上げました。 ここで使っている色はオーク色です。 最終塗装後1時間以上乾燥させます。
|
|
その上に水性ウレタンニス透明クリヤーを2回塗りしました。 2回目は1時間後にしその後3時間乾燥させてから次の作業(切断)にに入ります。
|
|
|
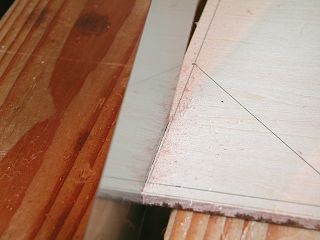 |
|
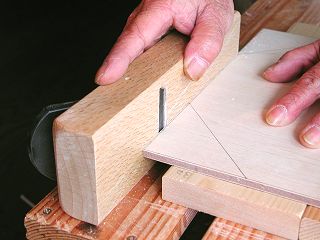 |
|
|
線引きした最外周(正方形)に沿ってご覧のように若干大きめ(0.5-1mm位)に切断します。
|
|
カンナでドンピシャ寸法になるよう削りながら直角出しもします。 このやり方の詳しくはこちらの最後の方で解説しています。
|
|
|
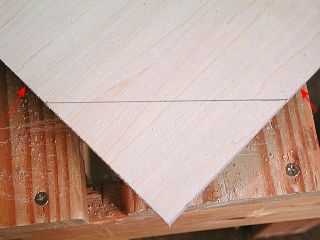 |
|
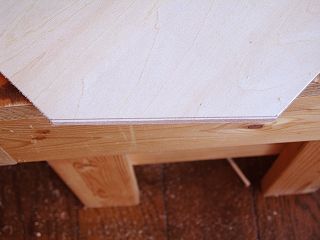 |
|
|
2つの矢印の先の線は線引きどおりのドンピシャになっています。 この後下に見える角の部分を切断します。
|
|
切断方法はやはりこのように線の少し外側としてその後でカンナで削りドンピシャ寸法となるようにします。 その後替刃式ヤスリで軽く切断面のバリを取ります。
|
|
|
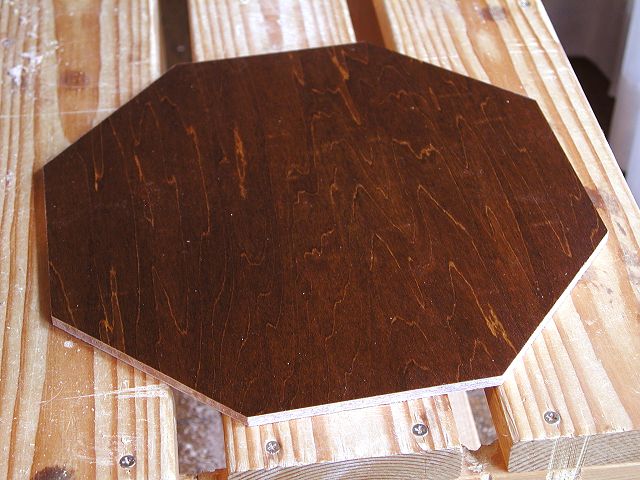 |
|
|
切り出し終えた八角形のお盆の底板。 各辺の長さが99.5-100mmの間に入っていれば極めて正確に加工できたことになります。 ここまでの作業で完成度の70%以上は決まります。 薄い板の加工ですから切断、カンナ掛けともに力技がいるわけでもなく慎重に進めさえすれば精度の高い加工は容易です。
|
|
|
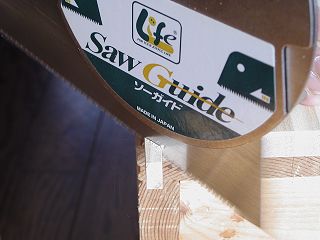 |
|
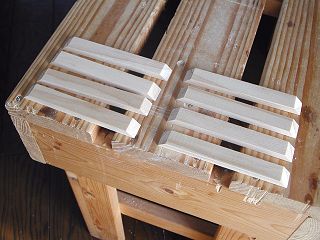 |
|
|
ソーガイドはガイド部分を水平に45度回転した、45度切断モードで切断します。 本番に入る前に正確な45度になるよう微調整が必要です。
|
|
所定の寸法に切断した8本の枠材。 この写真の上面が外側になります。
|
|
|
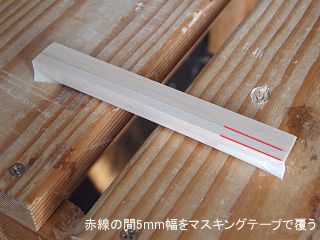 |
|
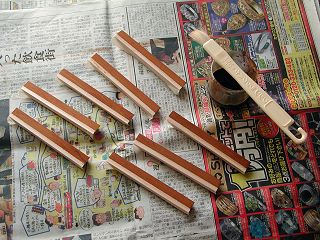 |
|
|
内側になる面(長い方)は#240ペーパーで研磨後接着される部分となる幅5mmをマスキングテープで覆ってやります。
|
|
そしてポアステイン3回塗りで着色しますが、内側になる面だけとします。 マスキングテープを貼って着色していない部分が判ると思います。
|
|
|
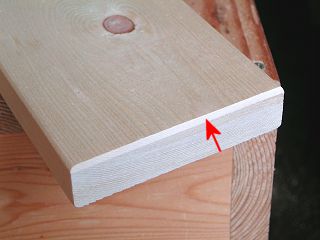 |
|
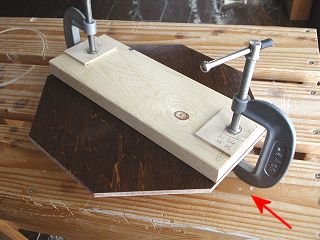 |
|
|
ワンバイフォー材を切断した接着補助のジグは先端の角を少し削っておきます。 これは接着材の付着防止です。
|
|
接着補助ジグをこのようにクランプ2個で底板に固定します。 矢印方向から見た具合は次の写真のようにします。
|
|
|
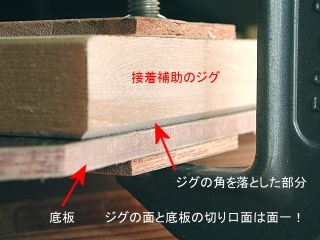 |
|
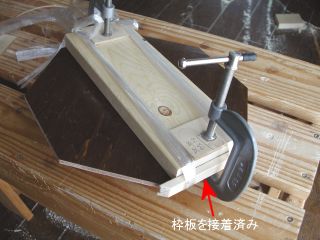 |
|
|
接着補助のジグと底板の切り口は面一になるようにします。 尚ジグの角を削った部分はこのような位置になるようにします。
|
|
木工ボンドを塗って枠を貼ったら紐をこのように巻きつけて圧着保持します。(ハタ金を使えれば作業性良く完璧な圧着保持が可能。)
|
|
|
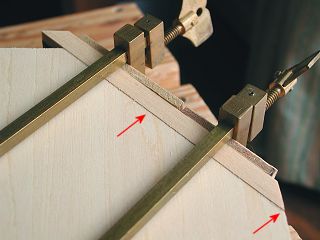 |
|
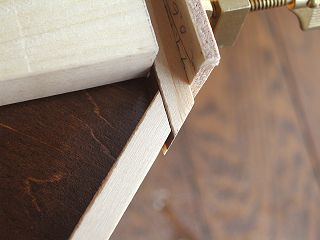 |
|
|
こちらはハタ金式の接着ですが、枠板の接着位置(枠板は底板よりほんの僅か突出。 枠板の片方の斜めの線は底板の隣の辺の線と一致。)に充分注意します。
|
|
左の写真の枠板の左側(突出部分)に別な枠板を当てるとこのように僅かに突出するはずでこれが正常です。
|
|
|
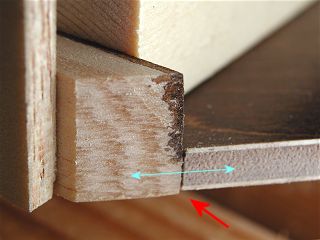 |
|
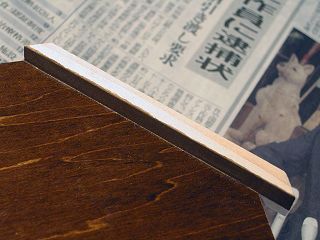 |
|
|
上の写真の右下矢印部分を横からクローズアップした写真で、空色の両矢印の繋ぎ目に段差があってはfなりません。 また底板より枠板が僅か突出しているのが(赤矢印)判ります。
|
|
2時間経って実用強度に達したので圧着保持を解いて撮影しました。 底板と枠の隅の部分にはごく僅かな木工ボンドの滲みが認められますが、予め着色してありますので問題ありません。 同様に次の枠材を貼り付けてゆきます。
|
|
|
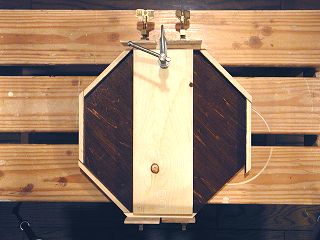 |
|
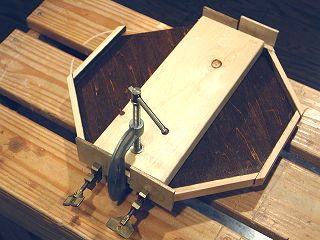 |
|
|
これは圧着保持を紐ではなくハタ金を使った時の様子です。 (今週撮影に使っているカメラはカラーバランスが悪くこの写真と次の写真は特に奇妙な発色になっています。)
|
|
位置を変えて撮影しました。 この圧着方法を使えればより完璧で確実な圧着保持が可能です。
|
|
|
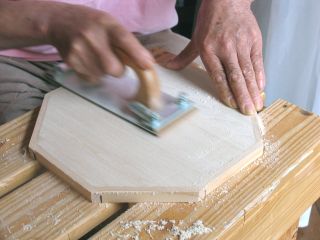 |
|
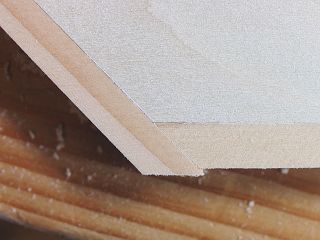 |
|
|
ここからカメラを変えました。 ハンドサンダーに#120ペーパーを付けて底板と枠の接合面の段差を取り、#240、#400とペーパーを替えて仕上げ研磨しました。
|
|
接合面のクローズアップ。 指先で触っても段差は全く無くなっています。 またはみ出た木工ボンドを完全に削り取れていることも重要です。
|
|
|
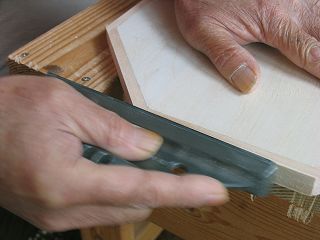 |
|
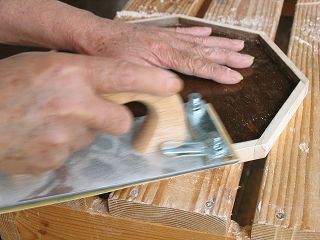 |
|
|
枠の接合部分の突出はまず替刃式ヤスリで突出を完全に削り取った後にハンドサンダーで#240、#400ペーパーによる仕上げ研磨をします。
|
|
枠の上面は#120ペーパーで接合部分の段差を取った後に#240、#400とペーパーを替えて仕上げ研磨します。 このあと好みにより面取りをして研磨は終了です。
|
|
|
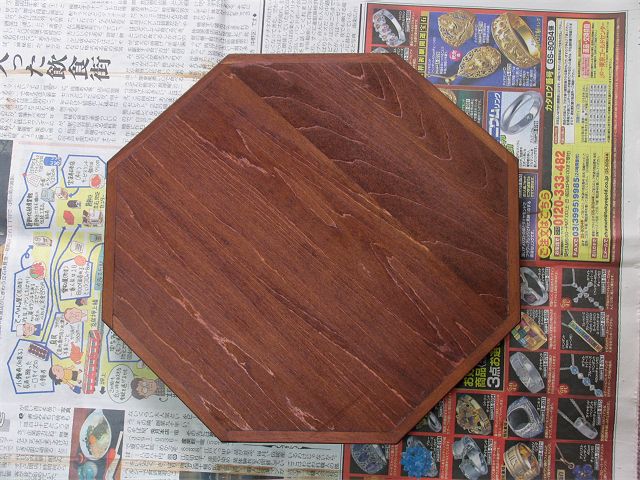 |
|
|
濡れ雑巾で仕上げ研磨屑を完全に拭きとって乾燥させた後にポアステインで着色しました。 前と同様水で2倍に薄めた物を3回塗りしています。
|
|
|
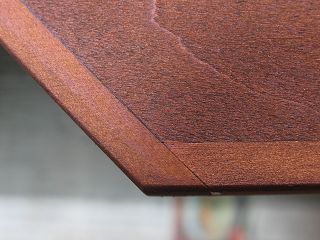 |
|
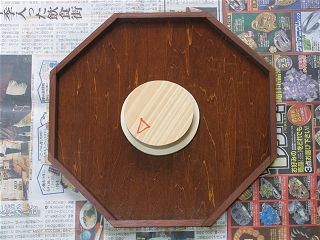 |
|
|
裏面の角のクローズアップ。 接合面に白っぽい着色できない部分があったとしたらそれは木工ボンドが残っています。 これは無論完璧にボンドは削り取られている例です。
|
|
実は着色とこの後のニス塗りの作業性を良くするためこんな即席のハンドルを作り両面接着テープで表側の底に貼り付けています。 お盆の底部分だけ先に2回塗りした理由のひとつです。
|
|
|
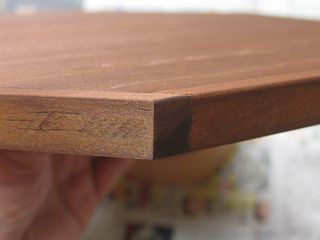 |
|
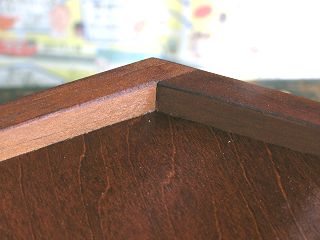 |
|
|
角の部分外側のクローズアップ。 こちらもはみ出た木工ボンドは完全に削り取られて残っていません。
|
|
角の部分の内側のクローズアップです。 枠の内側は着色済みだったのですが底板の切り口が白い線になって見えていたので、1回だけステインを塗り消しこんでいます。
|
|
|
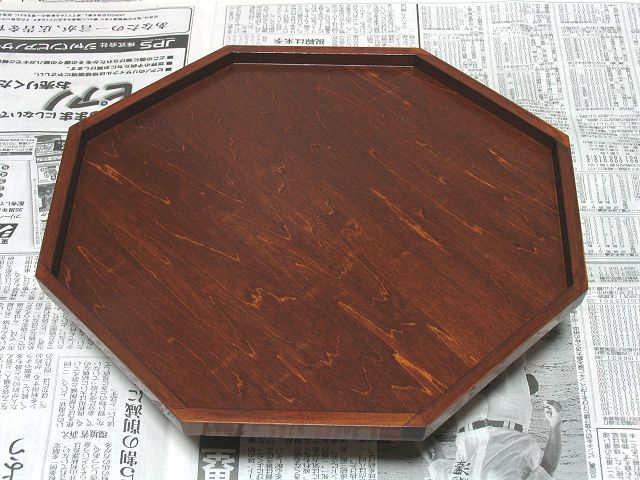 |
|
|
水性ウレタンニス透明クリヤーを4回塗り最後に内面は艶消しクリヤーを1回塗って完成した八角形のお盆。 重ね塗りの前には#400-#600の空研ぎペーパーで塗面をならしています。 色味と模様が何となく桜の皮を貼ったようでなかなか重厚な感じがするように思います。
|
|
|
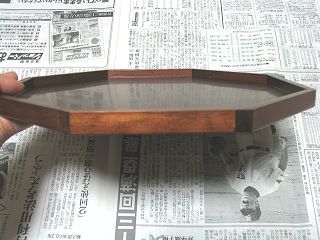 |
|
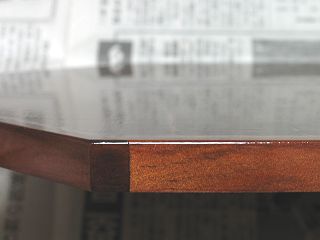 |
|
|
艶消しニスを塗った内面は反射もニブーイ感じになっています。 内面のみ艶消しとしたのは傷が付いても目立たないようにとの配慮?です。
|
|
側面と裏面は艶が充分にあります。 ピントが外れているので良く判りませんが、文字などが反射でよく読めます。
|
|
|
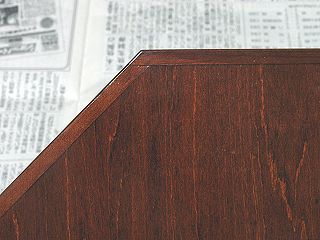 |
|
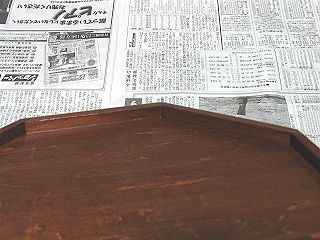 |
|
|
木目が良く見えるよう反射を抑えて撮影した底面。 枠板の貼り合わせがきちっと出来ているのが判るでしょう。
|
|
接着が隙間無くやられていることとウレタンニス5回塗りで木部は完全に保護され、汚れたら水洗いもOKです。
|
|
Copyright (C) 2001-2019, Vic Ohashi All rights reserved.