|
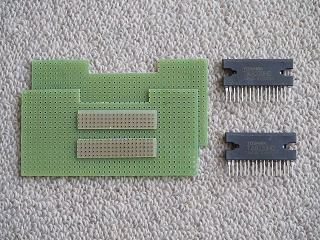 |
|
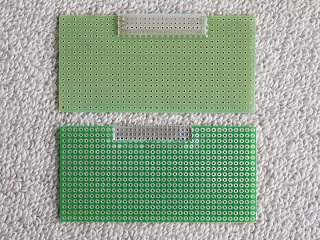 |
|
|
電動ジグソーに鉄工用ブレードを付け少し大きめに切断後ヤスリで所定の大きさに削り出した2.54mmピッチと2.0mmピッチの基板とパワーアンプIC。
|
|
2mmピッチ基板を2.54mmピッチ基板に瞬間接着剤で接着しました。 上が表面で下が裏面です。
|
|
|
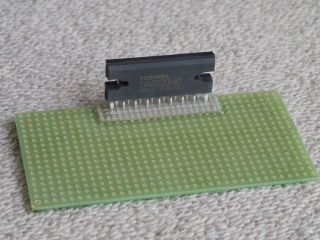 |
|
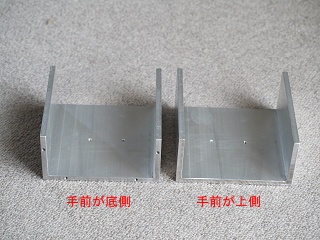 |
|
|
基板の2mmピッチ部分にパワーアンプICを挿しこむとこんな感じになります。
|
|
到着した50 x 100で5mm厚アルミチャンネル材を95mmの長さに切断し、ネジ穴6箇所をあけた放熱板です。
|
|
|
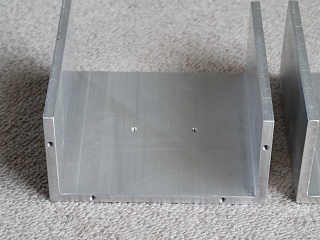 |
|
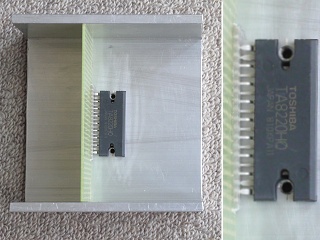 |
|
|
底側を拡大するとネジ穴が6箇所というのが良く判ります。 底側4箇所はケースの底板に固定する為のもので、内側2箇所はパワーICを固定する為のものです。
|
|
パワーICを基板に挿したまま放熱板の内側に入れてみました。 パワーICの止めネジの加工位置がバッチリ正確になっていることが判ります。(右端の拡大写真)
|
|
|
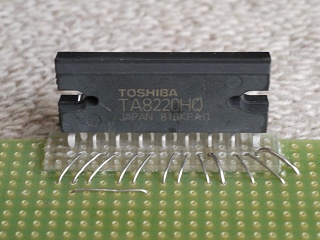 |
|
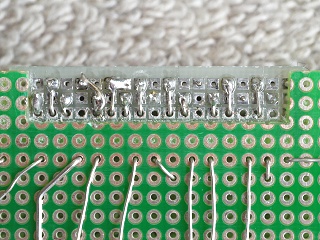 |
|
|
製作の第一歩はパワーICの固定とそこから2.54mmピッチ基板へのジャンパー線の接続ですが、これが最も神経を使う配線になります。
|
|
基板裏側のジャンパー線の様子です。 太い線は電源からの配線とGND周りです。 下の方への配線・半田付けは後ほどやるので、長めに切っています。
|
|
|
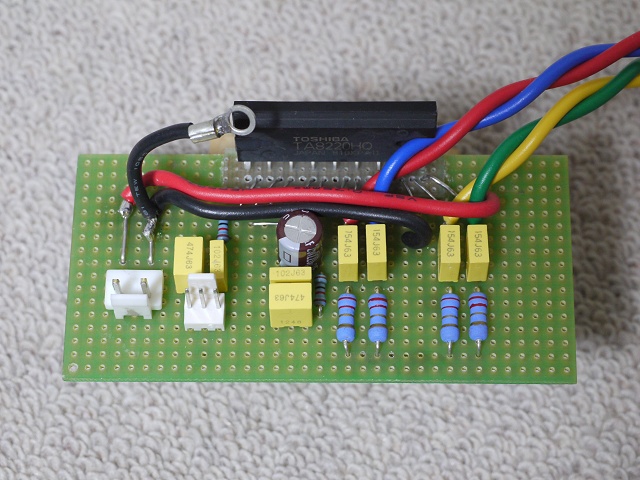 |
|
|
全部材の半田付けとと配線が済みました。 上側に太いジャンパー線が7本もありますが、撚ってある4本はスピーカーへの配線で、残りは電解コンデンサーを裏づけした為に表面側で接続しないとならなくなった電源周りのジャンパー線です。
|
|
|
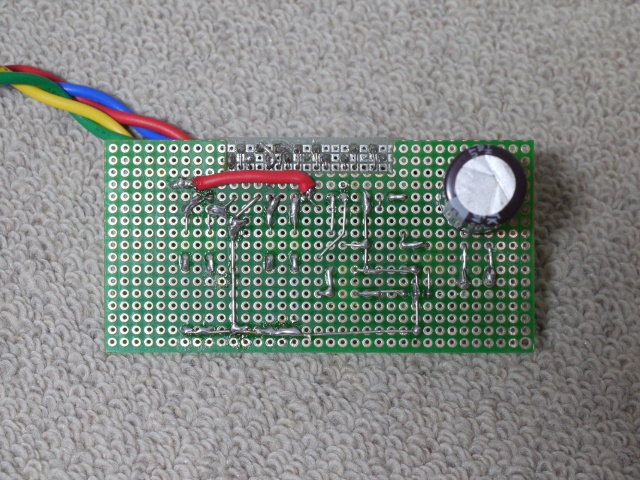 |
|
|
裏側は電源のジャンパー線1本と高さ30mmの電解コンデンサーが目立つ程度です。 この電解コンデンサーは環境温度が基板の上側よりも低くなると予測される下側に敢えて取り付けました。 またそうする事によりスピーカーターミナルとの干渉も避けられます。
|
|
|
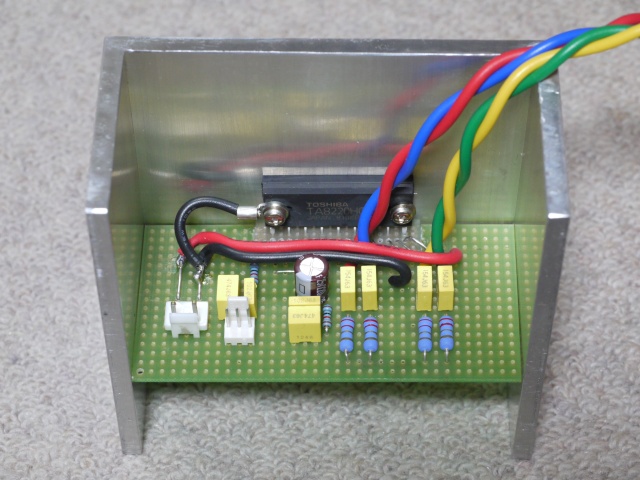 |
|
|
放熱板にパワーIC固定用のネジで仮固定しました。 左側のネジはラグ端子を共締めしていますが、放熱板と基板のGNDを接続する仕掛けです。
|
|
出来上がった試作基板を動作確認の試験をしました。
|
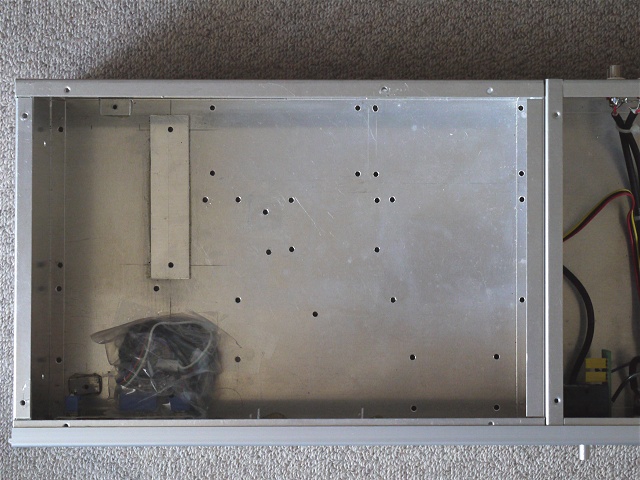 |
|
|
電源トランス、デジタルパワーアンプ基板2枚、電源回路基板2枚、交流電流検出回路基板、ネットワーク回路基板、トーンコントロール回路基板を外し、トグルスイッチへ繋がるワイヤーを束ねてポリエチレンの袋で包んで、加工作業の準備が出来ました。 右側の小さなシャーシ内はそのままにしています。 ただ無作為に解体するのではないので、半日掛かっています。
|
|
|
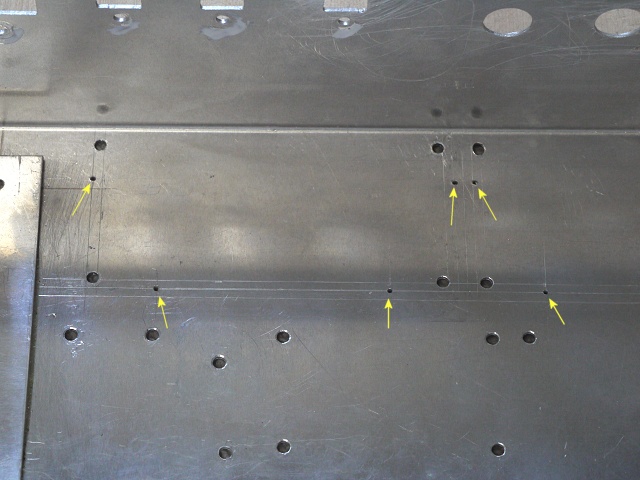 |
|
|
矢印の先は放熱板をシャーシに固定するネジ穴ですが、まず1.5mmの穴をあけてやります。
|
|
|
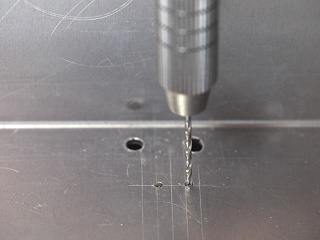 |
|
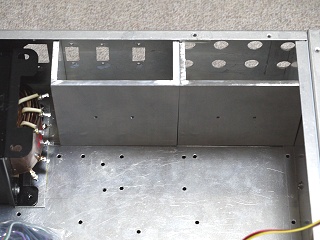 |
|
|
次に底板を取り付け1.5mmドリルをピンバイスに取り付けて底板にそれらの位置をマーキングしておきます。(後ほどネジの頭の当たり防止の座繰り穴をそこにあけます。)
|
|
そしてアルミ板の穴を3.2mmに拡大して放熱板固定の確認をしておきます。
|
|
|
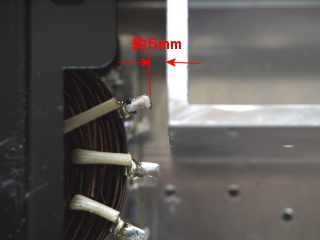 |
|
 |
|
|
問題はありませんが、左の放熱板の端はトランスの端子と5mmしか離れていないギリギリの配置です。
|
|
放熱口の位置を表すテンプレートを作りました。 上は内側に貼り下は外側に貼るため左右が反転しています。
|
|
|
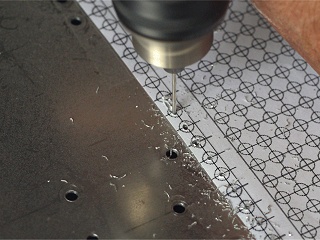 |
|
 |
|
|
センターポンチで軽くマーキングを入れたら1.5mmのドリルで最初の穴をあけます。 続いて2.5mmのドリルで穴を拡大してから4mmのドリルで拡大します。 穴周辺のハリは6.5mmのドリルで落としました。
|
|
放熱口をあけ終わったシャーシです。 穴数が多いのと、1.5mm → 2.5mm → 4mmの3段階であけるため大変時間が掛かり1日を使いました。
|
|
|
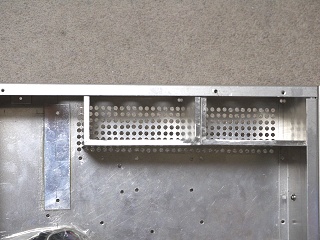 |
|
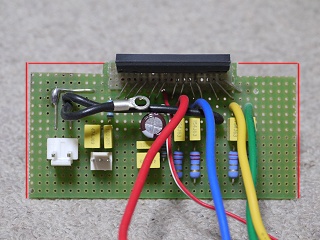 |
|
|
再びヒートシンクを仮止めしてみました。 ヒートシンクの外も中も放熱口で囲まれるようになったのが判ります。
|
|
ヒートシンク内の空気の流れを改善する為プリント基板を削りました。 赤線が元の端になります。
|
|
|
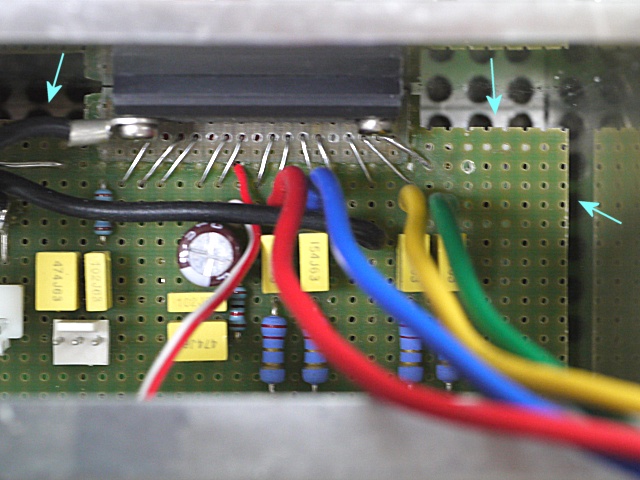 |
|
|
加工したパワーアンプ基板を放熱板に固定し、その放熱板を所定の位置に仮止めしました。 十分とも言える隙間がパワーIC横と基板の端に出来ています。
|
|
|
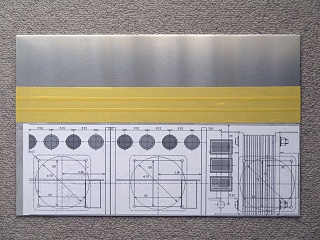 |
|
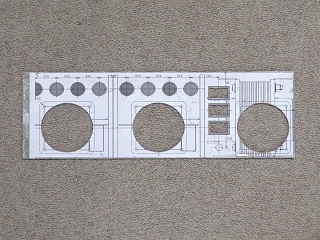 |
|
|
300 x 200mmの厚さ1mmのアルミ板にテンプレートを糊で貼り付けました。 黄色い部分はマスキングテープで切断線のガイドであるのと同時に切断時に不要な傷が付かない為の防護です。
|
|
NO.5ジグソーブレード(木工円切り用)でアルミ板を切断後DCファンの空気流通口3つとACアウトレット(小さい四角の穴)3個を切断しました。
|
|
|
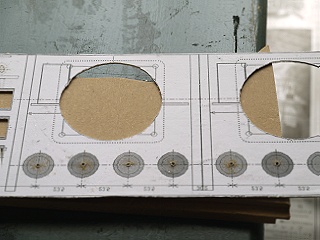 |
|
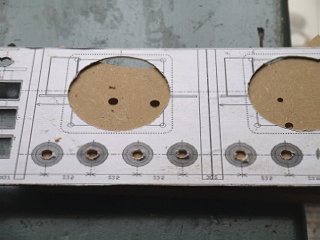 |
|
|
スピーカー端子固定の丸穴8個とACコードブッシュが固定される穴の中心にセンターポンチで軽くマーキングし最初に1.5φの穴をあけます。
|
|
次に3.5φ、5.0φ、6.0φ、7.0φとドリルを変えて穴を広げてゆきます。
|
|
|
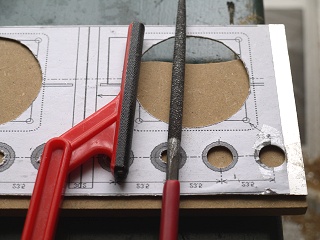 |
|
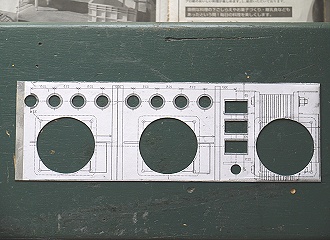 |
|
|
そこからは丸棒ヤスリで11.5φ程度まで削って広げ、最後に替刃式ヤスリ(RS-310P)で12.0〜12.2φになるよう仕上研摩します。
|
|
これで追加パネルの加工はDCファン止めネジ穴を除いて完了しました。
|
|
|
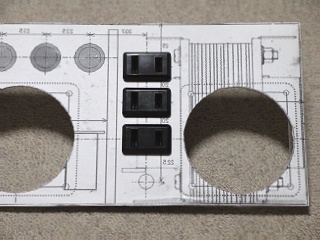 |
|
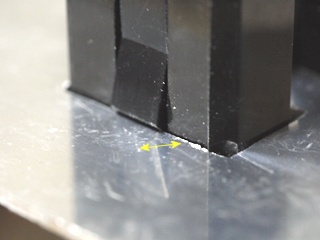 |
|
|
ACアウトレットの固定具合の確認をしました。 がたも無く良好です。
|
|
内側から見たACアウトレットです。 止めネジ無しで固定しますが、この写真に見えるヒレ(斜めに見える部分)が矢印方向に動きACアウトレットを完全に挿入するとアルミ板に突っ張って抜けなくなります。
|
|
|
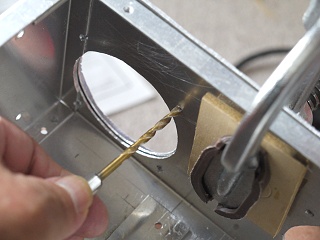 |
|
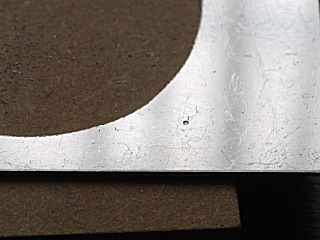 |
|
|
加工がほぼ終わったアルミ板をシャーシ背面の所定の位置にあててクランプで動かないように固定してからDCファン固定ネジ穴に内側から3.2φのドリルを差込み10回ほど回転して中心をマーキングします。
|
|
ここに見えるポチッとした部分がマーキングの後ですがそこにマーキングポンチで軽く追加マーキングをします。
|
|
|
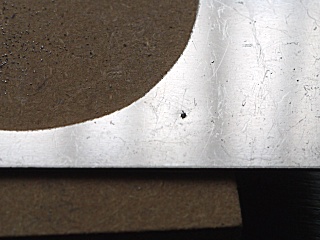 |
|
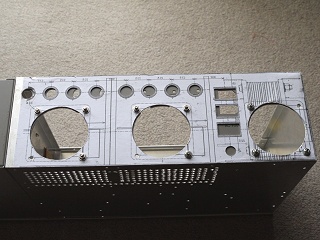 |
|
|
マーキングが若干深くなりますが、ここに1.5φのドリルで穴をあけた後に3.2φのドリルで拡大し両面のバリを取っておきます。
|
|
そしてシャーシ背面にDCファンネジ穴を使って仮固定します。
|
|
|
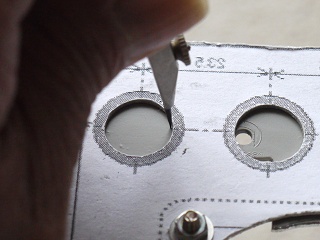 |
|
追加パネルが仮固定されたら、スピーカー端子の穴(8個)、ACアウトレットの穴(3個)、ACコードブッシュ穴位置をケガキ針でシャーシ面にケガキます。
またDCファンの空気流通口の穴がシャーシと追加パネルで食い違っている部分もケガいておきます。
今週はここまでですが、次回にはケガいた線を参考にしてシャーシを削る作業をいたします。 その後スピーカー端子の共締め部分の不安定解消の加工をすれば、背面パネル追加に拘わる加工作業は終了となります。
|
|
|
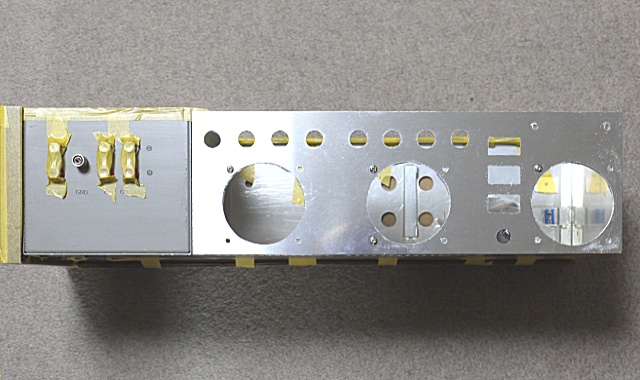 |
|
|
背面パネルの全ての加工が終わりましたのでテンプレートを剥がしました。 テンプレートが加工時に傷を付けない保護として役立ち、ご覧のように綺麗な面になっています。
|
|
|
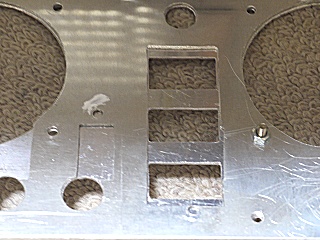 |
|
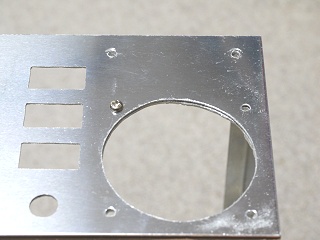 |
|
|
ACアウトレットは上下方向はヒレの引っ掛かりをよくするためシャーシ側の穴が大きくなっています。 またACコードブッシュの穴はシャーシ、追加パネル共同じ大きさの穴としました。
|
|
右端のDCファン上部にはパネル浮き上がり防止の固定ネジ穴2個を追加しました。
|
|
|
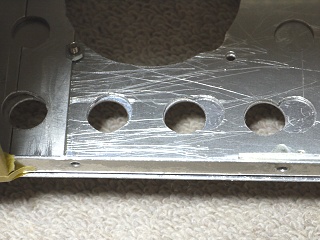 |
|
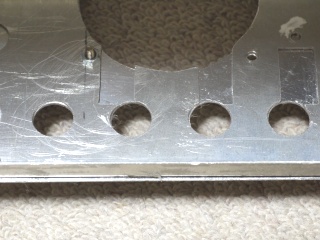 |
|
|
問題のスピーカー端子穴。 左側の4個中、右側2個は古い穴がかなり端子が引っ掛からない部分を作るのでダミーの小片を挟まないと不安定になります。
|
|
右側の4個中3個は以前のACアウトレット穴と重なっていますが、重なる面積が小さいのでこのままで大丈夫だと思われます。
|
|
|
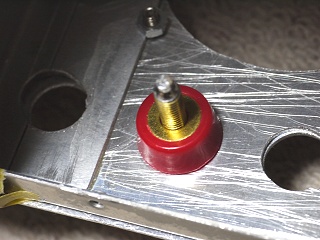 |
|
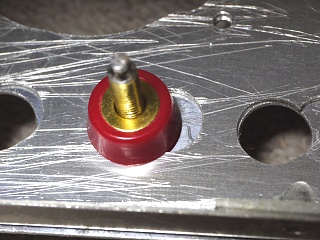 |
|
|
左側4個のスピーカ端子の左から2番目で、古い穴は2mm弱ずれている程度ですので、端子のカラーが完全に被さり問題ありません。 この左の端子も同様です。
|
|
左から3番目の端子。 カラーが浮いた状態の部分がかなりあります。 これは対策する必要有りと判断しました。
|
|
|
 |
|
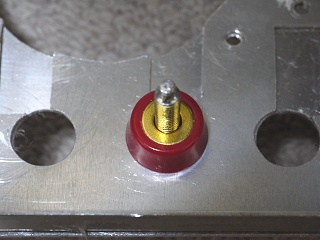 |
|
|
4番目の端子のカラーは更に浮いている部分が大きくなります。 無論これも対策しないとなりません。
|
|
右側の4個においては、左端は古い穴と全く干渉しませんので問題なし。 その右側3個の部分がこの写真ですが、以前のACアウトレットと少し重なり合っています。 この程度ですと不安定さは発生しないだろうと判断しました。
|
|
|
この後追加する背面パネルを塗装しました。 そして文字入れなのですがインスタントレタリングはもうないので、紙に文
字を印刷し貼り付ける方法を取りましたが、前面に紙を貼り付けると放熱効果が落ちますので部分的に2箇所に分けて貼
りました。 そして紙の背面が白だと面白くないので真っ黒にし文字を白としています。 これに合わせてパネルの色は濃
いめの黄土色(暗めのカーキ)としています。
塗料は濃い目の黄土色の油性スプレー塗料を2回塗りとし、乾燥後に文字入れの紙(マット紙)を両面接着テープで貼り
付け、その後水性ウレタンニス透明クリヤー、水性ウレタンニス艶消しクリヤーを1回ずつ塗っています。 こうすると塗装
面は大変丈夫になります。
|
|
|
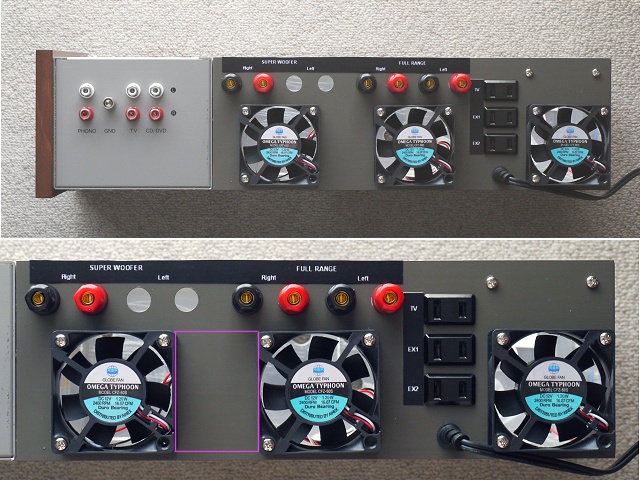 |
|
|
不安定さ解消の加工を残した2箇所のスピーカー端子を除き全ての背面に固定される部材を取り付けました。 上は背面全体ですが下は追加パネル部分のみです。 真っ黒な細い紙に文字入れし2箇所に貼りましたが、みっともない感じにはなっていないと思います。 ピンクで囲った部分は幅42mm、高さ60mm、高さ25mmありますが、DCファン制御回路を組み込む場合の設置場所と考えています。 DCファンは3本のネジで固定し残る穴はケーブルパスとしています。
|
|
|
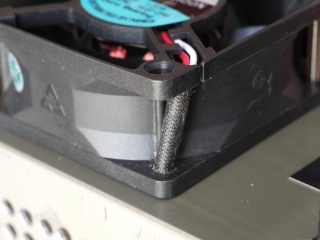 |
|
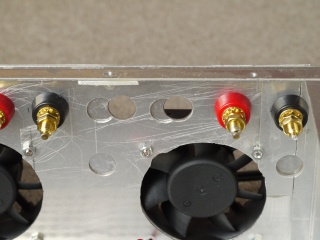 |
|
|
DCファンのケーブルはDCファン固定ネジ穴を通して体裁よくシャーシ内部に導きます。 余計な剥き出し部分がないのですっきりとしています。
|
|
スピーカー端子のカラーが浮くので更なる加工が必要な2箇所の部分です。(大袈裟な作業ではないのですが?)
|
|
|
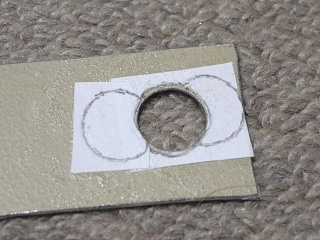 |
|
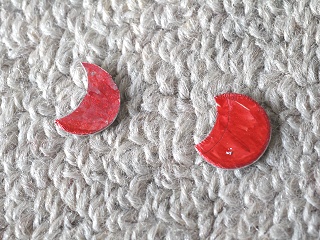 |
|
|
シャーシから写し取ったスペーサー(三日月型の部分)の型紙を1mm厚アルミ板に貼りました。 真ん中の穴は直径12mmで予めあけておきます。
|
|
ジグソーで大まかに切り出してからヤスリで削りだしています。(赤く染めているのはスペーサー部分が判るようにしているだけで、後ほど落とします。)
|
|
|
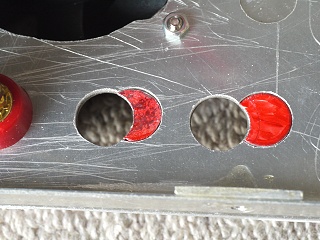 |
|
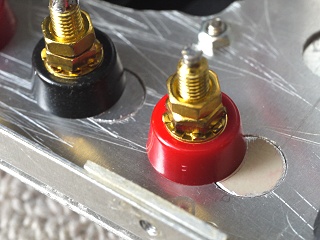 |
|
|
所定の場所にスペーサーを嵌め込むとこんな具合で、スピーカー端子が通るところには12φの穴ですがそれ以外は埋まってしまいます。
|
|
そしてスピーカー端子を固定しました。 これでスピーカー端子は妙なぐらつきも無く安定して固定されます。
|
|
|
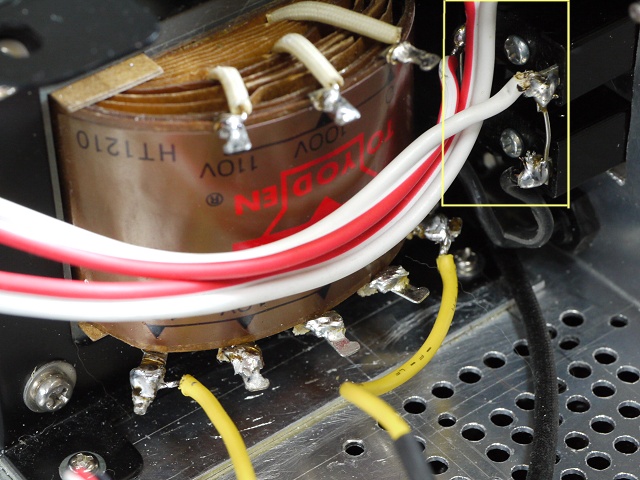 |
|
|
黄色い枠内にはACアウトレットが3個、そしてその下にはACケーブルインレットがありますが、トランスを固定する前に配線しないとなりません。 トランスの下側に接続された黄色い2本はAC12Vですが、これもトランスを固定する前に配線すべきです。
|
|
|
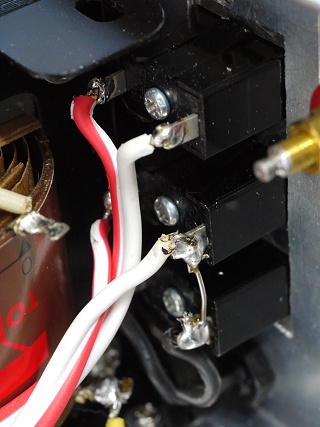 |
|
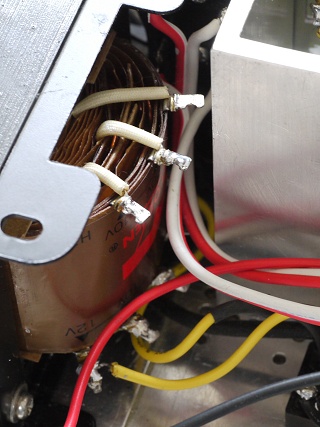 |
|
|
3個のACアウトレット部分。 一番上はTV用でこれを通過する電流が1Aを超えるとこのアンプの電源はONとなります。 下の2個のアウトレットはAC入力に並列で補助用です。
|
|
この後パワーアンプブロックを固定するとこんな具合でACアウトレット周りは配線をいじることが不可能になります。
|
|
|
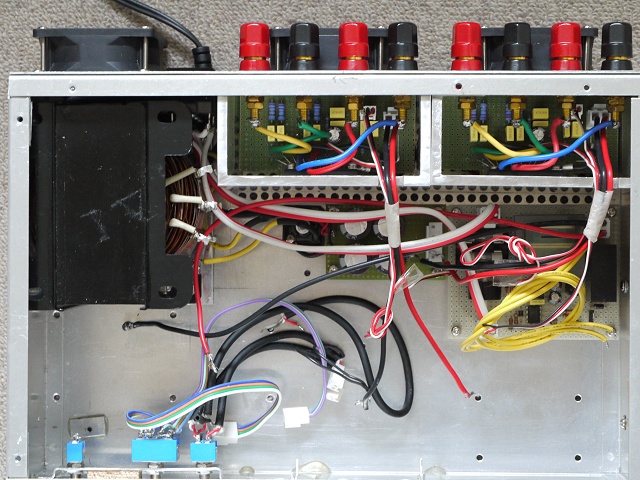 |
|
|
電源のフィルター回路基板とTV ON/OFF検出回路基板を固定したところです。 中心横に走る赤白のケーブルはAC100Vですが、他のAC100V回線と共に後ほど束ねてやります。
|
|
Copyright (C) 2001-2019, Vic Ohashi All rights reserved.