2016/01/22
構想
今年早々の完成を見たLEDランタンは災害時に電灯線が遮断された際に明かりを確保する物として製作しています。 発光効率も大変良く出来て、最大光量の50%位で運用すれば1日分はOKと言えそうです。 そしてこれ以外にも単二充電池、単三充電池、単四充電池を使う懐中電灯、ラジオ、石油ストーブ点火機構などかなりの電池が使われますが、インフラの遮断日数が増えればそれらの充電を考えねばなりません。 そしてそれらも電灯線を当てにしない物でなくてはなりません。
そのような充電器を考える時に思い付くのは太陽電池の利用だと思われます。 そこでおぼろげながら左のようなシステムを考えました。
最初にどのような電池を最大で何本充電したいかについて考えました。 大きさとしては単二、単三、単四で、何れもエネループかニッケル水素電池とします。 ひとつの大きさでの充電本数は最大6本が妥当かなと考えています。 と言うのは、大光量のLED懐中電灯とLEDランタンで単三を6本使う場合がある為です。 但し1本から6本まで同時充電本数は任意に選べることとします。 また単三の使用本数は多いので、単二の充電器で単三が充電できるようにします。 こうすると同時充電可能本数は単二、単三、単四各6本か単三12本、単四6本ということになります。
同じサイズ6本までを直列にして0.1C 12時間充電法で充電します。 急速充電は厳密には個々の電池の状況をチェックしてコントロールしますので、ここで考えている多量の同時充電では回路が複雑になりすぎるので、時間が掛かるものの安全性や安定性に優れる0.1C 12時間充電とします。
充電電圧は1本辺り1.5V近くまで上がりますので、6本で9Vが最低必要ですが、若干のゆとりを見て12Vを電源電圧とします。 充電電流は単二で300mA〜400mA、単三は190mA、単四は75mAとなりますので、トータル充電電流は565〜665mA、その他の充電器としての消費電流を50mAとすると、615〜715mAが充電時の消費電流で充電時間12時間を乗ずると、7.4AH〜9.7AHが充電量となります。 上の図ではそれを切り上げて10AHとしています。
また放電時にはリレーを使う予定のためそこで消費される電流が最も大きく、そこで消費される電流は212mAほどでその他での消費電流が合計で100mAあるとすると312mAが放電時の消費電流と見積もられます。 放電時間は一定ではありませんが、仮に平均して2時間掛かるとすると、0.63AHが放電作業に必要な外部電気量となります。
以上を2次充電と考えてその作業はいつでも出来ることとします。
一方その前に一次充電として、シールド鉛蓄電池を太陽電池に繋いだ装置を置かないといけないと考えています。 その一番の理由は太陽電池は曇天、雨天時、夜間には用を成さず、12時間電力を安定的に受け取るのは不可能であるからです。 この時当然ながら一次充電値としてのシールド鉛蓄電池はその物性から電池容量を使い切る使い方をすると著しく寿命が低下します。 今から30年以上前の経験ですが、天体観測の電源としてシールドバッテリーを使っていたときは2晩望遠鏡を駆動するモーターを回したとしても、満充電が半分まで減らない計算で電池の容量を決めていました。
ここでは同じ考え方で2次電池が10AHの容量に対し2.6倍の26AHとしていますが、太陽電池が動かない日のことを考えると更に容量を増やす必要性もあります。 尚この図には表していませんが、一次重電池を外して12V 1AのACアダプターを繋ぐという手が、フレキシブルなシステム運用で考えられます。
二次充電の構想検討
二次充電部分で様々なニッケル水素電池を充・放電するわけですが、その1系統の詳細なブロックダイアグラムを考えてみました。
左の図がそれですが、ここではむやみに図が大きくなるのを避けて最大で3本の電池を処理する場合としていますが、左端の自動放電回路は同じ物が3つ追加されます。 そして充電する電池には単二、単三、単四の三種類がありますから、これと同じ構成の系統が3種類存在することになります。
ブロックダイアグラム内の各セクションについて簡単に説明しておきます。 先ず自動放電回路ですが、図では既に電池が装填された状態になっております。 この時電池装填と連動するスイッチはOFFになっています。 つまり電池が入っていない時はプラスとマイナスの電極はショートされることになります。
手動と書かれた(ON)-OFF-(ON)のスイッチをONに倒すと放電制御回路が動作開始しリレーがONとなり電池を放電回路に接続し、単独で所定の電流にて放電を開始します。 この時オレンジ色の放電動作インジケーターが点灯します。 他の電池はそれぞれの手動スイッチにて放電を開始します。 全部がいっぺんに放電を開始しても良いのですが、放電無しで充電させたい時を考えているのと、充電は最高6本までを一度に充電しますが、放電は個々の電池の残容量はまちまちになることもあり放電時間が異なってくるので、現時点では放電開始は電池毎に手動スイッチにてやる方法としています。
この手動スイッチをON側に倒すと連動している放電モード検出回路がONになり、放電終了検出/充電開始回路がONとなります。 この回路は6本の電池を直列にした状態で1〜7.2Vの電圧を検出すると充電開始のトリガーをONとしますが、全ての電池の放電が終了するとリレーが遮断されて全電池が直列になります。(電池を入れていない部分はプラスとマイナスの電極はスイッチで接続されます。 検出電圧に幅があるのは放電しきった電池の電池電圧は1V、6本の電池を充電する際は6〜7.2Vが直列後の電圧となるためです。)
充電開始回路がトリガーとなって充電回路がONとなります。 この電源ONで充電がスタートしますが、12時間に充電終了の合図により電子スイッチは出力を遮断し充電は終了します。 これらの間充電中を示す緑のインジケーターが点灯しますが、充電終了と同時に青のインジケーターに変り終了を知らせます。
ここでリセットを掛けるか主電源をOFFにしない限り次の放電・充電は開始できませんがその辺りどのような動作にすればよいかまだ検討中です。
2016/01/29
各部の構想その1(放電部)
大きく分けた全体の構成は放電部、充電部、そして放電→充電への切替部の3つの構成になっています。 これらの中で放電部はそれぞれの電池専用の放電回路を持たせます。 放電器の製作例を見ると、複数の電池を直列に繋いで全体を一括放電制御してしまうものがあります。 この方法は使う電池の性能にバラツキが無く、電池に残っている電力も同じであれば使えそうですが、現実はそう都合よく行かないように思います。
例え使う電池が同じメーカーの同一モデルであっても、購入時期が変ったり充放電の回数の違いで諸性能は違ってきます。 また電池を使い終わった時点で残る電力も違いますから、放電電流が同じであっても放電終了までの時間は決して同じにはなりません。 従って充電池を正しく使うために放電する(一般にはリフレッシュすると呼ばれます。)には、電池個々に専用の放電器を用意するべきです。
ということで今週の本題の放電回路ですが、以前エネループを使ったポータブルヘッドフォーンアンプ製作時に試作した放電回路を基本として使います。
この回路は市販されている放電器では先ず採用されることの無い贅沢な回路を使用しており、トランジスターとオペアンプによる高精度なリファレンス電圧との比較で正確な定電流放電制御を致します。 また放電終了電圧の検出・判断にもオペアンプとリファレンス電圧によるもったいない位の高い精度を提供してくれます。
簡単に動作を説明いたしますと、左端のスイッチをONにするとFETのゲートはソース電位より5Vに下がり、ソースとドレイン間がONとなります。 そしてドレイン電圧(5V)は3.9Kと1Kで分圧され左端のトランジスターのベースに掛かるので、トランジスターはONとなりFETのON状態はスイッチが切れても維持されます。
そうするとオペアンプに電源が供給され、TA76432Sを使った1Vと75mVのリファレンス電圧も生成されます。 更にオペアンプの2晩端子は0.5Ωの両端電圧を監視しますが75mVより低いときは正のを出力を75mVより高いときは負の出力を出し2SC2092のコレクター電流を制御します。 具体的には最初は0Vですからプラスの電圧出力が2SC2092のベースに掛かりコレクター電流が流せる状態(スイッチON)になります。 この為電池のプラス→コレクター→エミッター→0.5Ω抵抗→電池のマイナスと電流(放電電流)が流れます。 0.5Ωの両端に75mV以上の電圧が発生するとオペアンプの出力は負になり、これは2SC2092をOFF状態(コレクター電流遮断)となりますので、75mV÷0.5Ω=150mA(極めて正確で安定した定電流)に収まります。 この150mAが放電r電流ですが、単四エネループの容量は750mAhですので電池容量の0.2Cの放電電流と呼ばれます。
左は上の回路を元にして描き上げた今回の放電回路の構想です。 図では同じ放電回路を2つ描いて、左端に1個のスイッチを押すと2つが同時に動作開始するような部分を追加しており、最終的にはこの下にあと4つの放電回路が追加されて1系統となります。
図の右端を見ると「最初の電池+へ」から「最後の電池ーへ」までがリレーの複数の接点を通りながら繋がっている(電池2本が直列になっている。)のが判ります。 この状態が放電時ではない充電時その他のタイミングの時です。
今回作る物では放電時に電池を個々ばらばらにし、放電終了後に全ての電池を直列にする作業をリレーにやらせています。 リレーの使い方で工夫したのは、リレーの消費電流は大きい(使用予定の物で11.7mA)のですが、ONになるのは放電モード時であり、その他のタイミングではOFFとなることです。 というのは放電時間は電池の残存電力によっておりますが、からっぽ寸前まで電池が使われる場合はせいぜい20分程度と見込まれます。 これに対し充電にはきっちり12時間を要しますので、リレーがONとなる時間が放電時の方が遥かに短いため消費電力が大幅に節減できるからです。
回路の動作は以前のものと同じですが、左端のスタートスイッチをちょい押しすると、左端にあるトランジスターのベースに0.7V程度の電圧が掛かり、トランジスタはONとなり、このためFETもONとなり、そして2番目のトランジスターがON状態を保持します。 2番目以降の放電回路の左端のトランジスターのベースにも同じ電圧が掛かりそれぞれの放電回路はON状態になりますが、左端のトランジスターはそれ以降付いていないのと同じとなりますから、複数の放電回路は個々独立して動作します。
さて回路ONとなった状態で左から3番目のトランジスターもONとなり、リレーもONになり電池を繋ぎ込みます。 そして放電動作開始となるのですが、もしも電池が存在していない場合には電池の両端に入れておるスイッチがON状態であるため、オペアンプの6番ピンはゼロ電位になり出力には正出力が出ます。 そうすると一番右の2SC1815GRのベースに電圧が掛かりこのトランジスターはONとなります。 こうすると左から2番目のON保持のトランジスターはONが保持できなくなり、その放電回路は動作を停止します。
この機構により6箇所の電池ホルダーの電池が装填されたところのみ放電回路が動作開始することになります。 ラフな計算上の消費電流は14.9mAですが、それに放電させる電池の本数を乗じた値が放電回路トータルの消費電流となります。
電池が入っていればオペアンプ6番ピンには放電終了電圧の1V以上の電圧が掛かります。 そうすると出力はゼロVが出ますので放電回路は電池電圧が1Vになるまで放電を続けます。 放電電流は以下の考察の上で0.3Cと決定することにしました。
左の図は放電時の状態を検討するために描き上げたものです。 下の方に電池の種類と0.3Cとした時の放電電流と放電電力を計算しました。 単二ニッケル水素電池では放電電流を1200mA、トランジスタでの放電電力は抵抗での消費電力を差し引くと1.05Wになります。
このトランジスタの最大許容コレクタ損失は2Wですから放熱板を使うべきかどうか微妙なところです。 また最大許容コレクタ電流も3Aですからこれ以上は無理しないほうがよさそうです。 当初は放電時間を短縮するために0.5Cを考えていたのですが、こんな事情で0.3Cに減らしました。
現時点では放熱板として30 x 30 x 30の物を使うように考えており、多分これは不必要な大きさだと考えていますがプリント基板を大きくするのは全体に影響するので、最初は大きめの放熱板で基板設計を進め、実験回路で発熱の状況を確認の上調整したいと思います。
トランジスタのエミッタに繋がる抵抗は当初0.5Ωとしていましたが、単二電池の際放電電流により0.6Vの電圧降下が出てしまいトランジスタのVceが小さすぎて制御できなくなる可能性があるため0.27Ωとしています。 また抵抗で389mWの消費電力があります。 抵抗の表面温度を拡散させるため3Wの物を使用予定です。
2016/02/05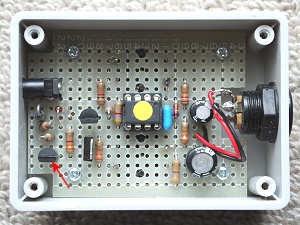
各部の構想その2(充電部)
放電部と異なり充電部は1系統の電池は6本までを直列に繋いで所定の定電流で、まとめて充電させます。 充電部の電源電圧は12Vでこれは放電部と一緒ですが、放電部は1系統で6組もたせて約90mAの小電流に対し、充電部は6本まとめて充電するので、制御回路は1つで良くても充電電流は単二ニッケル水素電池で400mA、単三エネループで190mA、単四エネループでも75mAの消費電流が充電だけで掛かります。 その他に11.6mA程の回路動作電流が流れ、それが12時間も続きますので6本まとめての動作という意味が充分あります。
右は以前に作った単四エネループを3本直列に繋いで使う充電器で、これを元に追加、変更、削除して左のようにまとめました。
この図では電源が右手で左側が充電器としての出力側(電池を繋ぐ側)になります。 この図では電池を2本だけ繋いだように描いていますが、実際には間の電池を省略してあり6本まで繋がります。 そしてこの図には記載してありませんが、電池ホルダーにはスイッチを取り付け、電池が入っていない時はスイッチが閉じ、電池を入れたときにスイッチが開くようにしておきます。
この充電回路で最も大事な部分は定電流回路とタイマー回路ですが、タイマー回路については市販の充電用タイマーICを使って簡単に作れます。 定電流回路については電圧可変レギュレーターによるものとします。 その原理は右の図の通りで、レギュレータのLM317と抵抗1本の簡単な回路ですが、極めて安定度の高い定電流動作を致します。
LM317を図のように結線しますと抵抗の両端には1.25Vの安定した定電圧が発生します。 そこでこの1.25V(定電圧)を抵抗値で除した電流値も定電流になりますので、電池(6本直列に繋がれています。)には定電流(ここでは400mA)が流れる!という訳です。
言うまでも無く、定電流(充電電流)を半分の200mAにしたかったら抵抗値を2倍の6.26Ωに変更するだけで済みます。
この回路で注意すべきは充電する電池の本数が少なくなった時です。
左の図でその問題点を説明いたします。
上段は電池を6本充電する時で電源電圧は12Vとしておきます。 このときに各部の電圧がどうなるかですが、電池の両端電圧は6V(充電初期)から9V(充電末期)、抵抗の両端は変らず1.25V、それらによりLM317の入出力電圧は4.75〜1.75Vとなります。
以上の結果よりLM317で消費される電力は1.9〜0.7Wと求められます。(この試算結果は別な問題を含んでいますが、それについては後述します。)
つぎに下段の電池を1本しか充電しなかった時です。 電池の両端電圧は1〜1.5Vに下がります。 抵抗の両端電圧は変らず1.25Vです。 この時はLM317の入出力間電圧は 9.75〜9.25Vとなり、LM317の消費電力は 3.9〜3.7Wと大幅に増加します。
LM317が発生する損失電力に対しどの程度まで許容し、あるいはどの程度の放熱を施せばよいのかは技術資料ではあいまいな表現になっておりガイドラインは出てきません。 充電時間は12時間も掛かりますから、予備実験で充分なテストを重ねないとなりません。
尚この試算結果が含む別な問題とはDrop Out電圧を指します。 3端子レギュレータが正常に動作するのに必要な入出力間の電圧をDrop Out電圧と言い、温度と出力電流で変化しますが、技術資料で判断すると、0〜40℃で500mAの出力電流ですと1.75〜1.85VのDrop Out電圧になっています。 そしてこれは6本充電の充電終了に近づくと入出力電圧は1.75Vまで下がりますのでDrop Out電圧領域に引っ掛かる可能性があります。 もし引っ掛かると電池電圧供給が充分でなくなりますので、充電不足になります。
これを直すには電源電圧を上げるか、Drop Out電圧の少ないレギュレーターや逆流防止のダイオードの順方向電圧の低い物に変えるかなどの方策を採ることになりますが、別な副作用が発生する可能性がありますから、予備実験で慎重に方向性を探る必要があります。
そんな問題は残っていますがそれらは解決することとして動作説明を続けます。 この回路に電源電圧が印加されると即充電を開始いたします。 これはタイマーICがそのように動作するように使えるわけですが、タイマーが作動するとKD01Pの6番ピンにはタイマーIC電源電圧の4Vが出てきます。 そしてこの電圧で左端のトランジスタがONとなりFETもONとなり充電開始となります。 タイマーが動作開始後12時間経つと6番ピンは0Vになりますので、左端のトランジスタがOFFそしてFETも遮断されます。 この時電源電圧は掛かったままですから2番目のトランジスターのベースは1V近くに上がり青のLEDが点灯し充電終了を知らせます。 この充電回路への電源は全ての電池を外すことで遮断されるようにしておきます。(その時に青のLEDが消灯する。)
2016/02/12
各部の構想その3(充電部再検討)
先週発見したLM317の入出力間Drop Out電圧について更に過去の製作記録を調べて見ました。 そうすると技術資料で判断した値(1.75〜1.85)よりも0.2Vほど高い値が実態であることが判りました。 そこで低損失の定電流回路として最も性能の良いオペアンプを使ったものと比較してみることにしました。 次の図はその比較ですが、今回の充電回路を想定とした回路定数としています。
ピンクの点線で各部材を仕切っていますが、抵抗、電池、ダイオードでの電圧降下を記入して電源電圧の12Vからそれらの電圧降下を差し引いた値を、トランジスタ欄又はLM317の欄に入れました。 トランジスタ、LM317、電池には値が2列に入っていますが、上段が電池1本の最低電圧の時で、下段が電池6本の最高電圧の時です。 尚流れる電流はどちらも400mA(単二ニッケル水素電池の充電電流)です。
右側のレギュレータ(LM317)を使った場合には6本の電池を充電する際レギュレータの入出電力が0.85Vに下がると算出されていますが、上で触れたように実際のDrop Out電圧は2Vほどありますので、電池電圧はその差分だけ低い8.05V(1本辺り1.34V)となります。 これは充電不足になることを意味しています。
一方左のオペアンプを使った方式で同じように眺めてみると、トランジスタで発生する電圧降下(Vce)が1.7Vとなっています。 メーカーの技術資料によればVCE(SAT)はICが400mAの時に-0.8Vとあります。 ということは0.9Vのマージンが残ります。 もしマージンを更に増やしたければ、電流検出抵抗の値を減らせばマージンを増やせます。 例えば現在1Ωになっていますがこれを半分の0.5Ωに減らせばVCEは1.9Vに上昇し、マージンは1.1Vに増加します。
どうようなマージンの改善をレギュレーター法で出来ないかの検討をしました。 先ず電流設定抵抗の両端電圧ですが、これはReference電圧で1.25Vの固定であり調整できません。 また5つの販売店で販売しているReference電圧の最も低いレギュレータを探してみましたが、1.25V以下の物はありませんでした。 次にLow Drop Out電圧(LDOと一般に呼ばれる)の物で今回の使用目的に対応出来そうな物を調べた所、0.45Vという物が出てきました。 但しReference電圧が1.5Vに上昇します。 Drop Outが1.55V改善しますがReference電圧が0.25V上昇するので差し引き1.3Vの改善です。 2Vが0.7Vになります。 0.85Vよりも低いので一見良さそうですが、マージンは0.15Vということで実際に起こりうる変動を考えると、OKとは言いにくいです。
他の方法としてダイオードをショットキーバリヤーダイオードに変更すると順方向電圧が0.7Vから0.4V程度に下げることが可能ですが、ショットキーバリヤーダイオードは逆方向の電流が多い傾向にあり、逆流阻止という目的に合致しません。 残るは電源電圧のアップですが、電池電圧を考えると例えば13Vに微増させることが出来ず、15Vに飛んでしまいます。 そうすると電気的な損失が増大するだけでなく、使えるソーラーセルの大きさ、重さ、そして購入価格にまで負担が掛かってきますので、何としても12Vで食い止めたいと考えています。
オペアンプを使った方式の一番の問題点は使う部品点数です。 レギュレータ方式が回路素子4個(抵抗は2本を直列か並列で接続して使うと考えます。)で済むのに対しオペアンプを使った方式では7個必要で、オペアンプとポテンショメータは場所を喰います。 また使うトランジスタはダーリントンタイプのPNPという品種の少ない物から選べばならないのも不利な点です。 実は品種の多いNPNトランジスタで作ることも可能ですが、電池のマイナス側をGNDに出来なくなり、放電器との接続に問題が起きます。
ここで候補にした2SB880は私のなじみの販売店で見つけたもので、技術資料から抜粋したスペックを上図の左側に紫色の小文字で入れましたが、ダーリントンタイプの為に、Icが400mAの時にhfeが3000もあるのでIbは0.134mA程度で済みオペアンプに負担が少ない、Vceが25℃、Ic=0.4A、25℃で-0.8V程度とダーリントンタイプとしては小さいなど大きな期待を寄せています。
左は気が早いのですが、オペアンプによる定電流回路で充電回路を組める!となった場合の充電回路案です。 ここでは電池を3本直列に繋げられるように描いていますが、同じ物を後3つ追加することになります。 また一番左側で配線などがピンクで表現されているのは、充電モードに入る前の電池検出の方法を説明するもので、次に述べる放電動作から充電動作への受け渡し回路を参照ください。
ということでまだバラ色には程遠い状況ですが、オペアンプを使った方式で予備実験をしてから最終的な判断をしようかと考えています。
放電動作から充電動作への受け渡し回路
冒頭で触れたように放電動作は個々の電池が独立して動作、充電は電池1〜6本を直列に繋いで一括して動作させますので、その接続の切り換え順序が
狂ってなんてことが起きると困ります。 そこでそれらの動作が確実に引き継がれるようなインターフェースを考えています。 左の回路図が現在考えているものですが、初期の全体構想では個々の放電回路にスタートスイッチが設けられていたのが、ここでは1個の電子スイッチで全てのスタートを賄うように変更しています。
動作を追って説明しましょう。 左端の空色の丸は放電回路のスタートスイッチに繋がる空色の丸(各段初段TRベースへ)に繋がります。 放電回路のスタートスイッチを押すと約1Vの電圧が掛かり左端のトランジスタはONとなります。 するとFETが引き続きONになりますので、左から2番目のトランジスタがONとなり、その後左端のトランジスタがOFFになってもFETのON状態を保持します。
この状態が充電前のスタンバイ状態ですが、右にあるFETはその下にあるトランジスタが全ての放電が完了して電池が直列に繋がったことを検知することで、スイッチオンとなります。 右端にあるBattery Chek +へとBattery Chek -へはこの上にある充電回路の左端のBattery Chek +へとBattery Chek -へに繋がります。 ここで二つ上の充電回路の図をご覧ください。
Battery Chek +へとBattery Chek -への間はピンクの線を辿ると明瞭ですが電池が直列に繋がります。(電池が入っていない所はスイッチがONになっておりそれを通過しますので0Vの電池となります。) よって電池が入っている時この間は最低でも1Vの電圧、最高で8〜9Vの電圧が検出されます。
ここでインターフェースの上の回路に戻りますが、この1〜8Vの電圧を検出をした時に右端のトランジスタは検出後ひと呼吸遅れてONになります。 すると右のFETがONになり、充電回路へ電源が供給されて充電がスタートします。
回路中には3連のスイッチがありますが、現在は放電/充電のフルコースまたは充電のみで、スイッチを倒すと放電のみのモードになります。 前者の放電/充電フルコースは説明不要と思いますが、放電のみは電池をホルダーに装填後充電スタートのスイッチを押すとこの回路はスタンバイ状態になり右端のトランジスターは電池の存在を認識してFETをONとしますので、充電がスタートする動作を指します。
後者の放電のみにスイッチが倒れた時は放電スタートスイッチで放電開始しますが、右端のFETには電源が繋がりませんから放電終了後に充電回路は動作しません。 その代わりFETの間にあるLEDが点灯して放電が終わったことを知らせます。
以上3ブロックを組み合わせれば私が志向した自動放電・充電器になるのですが、予備実験にて上記の回路が期待通りの動作をするのかどうか確認後に試作に進みます。
2016/02/19
充電池有無検出回路の実験
充電池有無検出回路動作の基本は、『回路上最も上の電池ホルダーのプラス電極と最も下にある電池ホルダーのマイナス電極間の電圧検出により充電を開始させる。』となっています。
放電動作に入るとリレーにより全ての電池は切り離されて放電回路に取り込まれますので、電極間には電圧が発生しませんが、それ以外の場合は電極間には1.0〜8.0Vの電圧が発生します。
但しその検出回路は放電動作が始まってから検出動作開始となります。 そして放電動作が終り次第電池は随時直列に戻されますので、全ての放電動作が終了して初めて電圧が検出されます。
その検出される電圧値は1.0〜8.0Vとかなりの幅になります。 この電圧をトランジスターのベースに注入してトランジスターをONとして電子スイッチのFETを作動させようというのが魂胆ですが、トランジスタのVbeは0.65V程でONとなるので電池が2〜6本繋がれた時には、検出電圧を抵抗で下げてやろうという考え方が、右の先週提示した回路です。
ところで私は漫然と回路を描き上げていますが、抵抗2本で調整しようといっても1.0〜8.0V全ての領域でバランスの取れた調整が出来ません。 それは当然で8倍の電圧変化は大きすぎますので、もうちょっとしたひねり技を加えてやらないと無理です。 そこで定電流回路を使うことで解決しようというのが、左の図のアイデアです。
右上の回路の抵抗1本を定電流ダイオード(赤丸に横棒がくっついた素子)に置き換えたものです。 こうすると定電流ダイオードを流れる電流は一定値になるので、トランジスタのベースに掛かる電圧も一定となり問題は解決されます。
但しこの定電流ダイオードに掛かる電圧はある値以上にならないと定電流にはなりません。 市販されている定電流ダイオードから数種類の値の物を実際に使ってみるのも手ですが、それでは選ばなかった物は死蔵品になってしまうので、ここではFETと抵抗を組み合わせて実働試験により作ってみることにしました。
というか市販されている定電流ダイオードはFETと抵抗の同じ組合せで出来ているらしいのでそれならやってみるかという塩梅です。
よく使われるジャンクション型FETの2SK30Aのゲートとソース間に抵抗を繋ぎ、ドレイン側をプラス、ゲート側をマイナスとして使います。 取り敢えずその性能を確認すべく実験してみることにしました。 以下の最上段が実験回路で、電流値を電圧値としてDMMで読むために1KΩの抵抗を加えています。
挿入する抵抗の値は、1KΩ、3,3KΩ、10KΩ、33KΩ、100KΩの5種類としました。 FETのバラツキがあることを考えて20本ほど事前に調べて傾向の似た物5本の結果を一覧にしています。 FET2〜FET5では10KΩ以上3種類しか測定していませんが、これはそれらの微弱な電流領域しか使わないだろうという理由によります。 またFET 1の特性をグラフ化したものをその後に示しています。
それらの結果から言えることは定電流といっても使える領域は結構高い電圧領域であり、例えば1KΩを入れた場合0.55mAが定電流値になりますが、その両端電圧は6.3V以上になってしまいます。 但し挿入する抵抗値を上昇すると定電流値は低電圧領域に下がってきます。 今回必要な電流域は0.1mA以下ですから、挿入する抵抗は10KΩ以上になるとみています。
検出電池電圧が1Vの場合定電流ダイオードに掛かる電圧は0.35V程度となります。 そこでそれより低い0.3Vの時の電流値を実測しています。 それらは定電流値よりも低い(0.003〜0.08mA)のですが、トランジスタの必要とするベース電流(hfeを300とすると0.00087mA以上)より遥かに高い10KΩ辺りを使えば低電圧領域でも問題の無い動作を得られそうです。
グラフを見るとFETによる定電流特性が良く判ります。 これでみると大きな電流値の定電流素子としては余り評価できず、微弱電流用と考えた方が良さそうです。 但しトランジスターのベース電流をこの回路で供給するような使い方であれば間接的に大きな電流をコントロール出来ますので、例えばLED駆動回路に応用できそうです。 例えば0.16.7mAをこの方法で作りそれをhfe 300のトランジスターのベース電流とすれば、50mAの定電流になります。
さて実際の回路に近いところでの確認をしてみました。 上の表の空色に染めた部分(FET2で10KΩの抵抗使用。)で実験してみました。
左がその実験回路と測定結果です。 実験に使った2SC1815GRはhfeが丁度300の物を選別して使いました。 12Vが印加される47KΩの抵抗の反対側は2SC1815GRのコレクターに接続されますが、実際にはFETのゲートにも繋がりここの電圧が下がるとFETがONとなります。 ほぼ完璧なONとするにはここの電圧は6V以下(流れる電流が0.13mA以上)になる必要があります。 ここでは流れる電流が0.26mAから0.25mAに下がったポイントをスイッチONとして大変辛い判断をしています。
FETへの入力電圧は上から8.0V、3.58V、1.0V、0.79Vと設定しています。 3.58Vは実用上余り重要ではないのですが、ここまでが完全に定電流となる領域で、この電圧以下では電流値が下がってきます。
4段にて表現していますが、上の青3段が実際に掛かるであろう電圧で、最下段の赤はマージンを確認するための参考値で、実は上で触れた47KΩの抵抗に流れる電流が0.26から0.25mAに下がったポイントで、丁度トランジスタのVbeも下がり始めた(0.64Vから0.61Vへ)ポイントでもあります。
これまで触れていませんでしたが、コンデンサーについて少々説明しておきます。 このコンデンサーは電子スイッチONが若干の遅延動作をするようにとの目的と若干入力がふらついてバタバタとチャッタリングを起こさないようにと考えて入れました。 現在は33μFとしていますが、100μFに上げる予定でいます。
簡単な回路ですが何とかスマートに収まったと思います。 次回も予備実験が続く予定です。
2016/02/26
放電回路の動作確認実験
実働実験放電回路において確認したいことは、0.3Cの定電流放電がきちんと出来るかが最も重要です。 しかし非常に乱暴な言い方をすれば、電池電圧が1.0Vに低下したら放電を停止すれば、『電池を壊さずに最大の充電容量を確保する』という基本的な目標は達成できるので、ショートさせるような高電流で無ければ、放電電流が何であっても構いません。
そうなると一定電流での放電の意味がなくなるのですが、電池の充電容量を正確に知りたかったら、放電電流値を予め判った定電流で放電させ、1.0Vまで電池電圧が下がった時までの時間に放電電流値を掛けると充電容量が算出される!というような意味が生じてきます。
例えば本テーマでは0.3Cの放電電流としますので、充電容量1900mAhの単三エネループを満充電してから放電させて3.3時間で終了したら充電容量は、1900mAh x 0.3C x 3.3時間 = 1,881mAhと算出できます。 そしてほぼ定格どおりの充電容量で問題無し! などの判断が可能になります。
これはいつでも使いたい機能ではありませんが、古くなった2次電池の状態をを正しく評価、あるいはメモリー効果で使えなくなった電池を回復させる処置の経過での状況判断などをするにはこういったことが出来る必要があります。 入手しやすい一般の電池メーカー製純正充電器では放電機能が付いているものが少なく、ましてや放電電流が判る物、定電流放電をする物は見当たりません。 従って本機は自作によってのみ入手出来る物となります。
註): 以下に提示する回路はその後の実働テストにより動作不具合で使い物にならないことが判明致しました。 その詳しい解決策についてこちらをクリックしてお読みください。 (2016/04/15)
|
余談はこの辺にして左が放電回路の実働テスト全回路で、右側に2点鎖線内の『確認第一段階の部分』が最初のテスト回路になります。
2点鎖線内の回路定数について少々触れておきます。 トランジスターのエミッターに繋がる抵抗は0.27Ωから0.28Ωですが、一番近くの部品屋さんでは0.27Ωの在庫が無いので実働テストでは、0.56Ωを2個並列にして0.28Ωで実験することにしました。 放電電流は変えませんのでリファレンス電圧は計算しなおして同じ電流になるようにしています。
この変更でVceの電圧が若干下がりますが、最終的な0.27Ωに対する致命的な違いにはならないと思います。 尚これらの抵抗は高精度の物が必要ですが、1Ω以下の物で抵抗値が多くある酸化金属被膜抵抗で誤差±5%の物を使っています。 但し経験上では誤差は±1%近くに殆どの物が入りますから安心です。 最も温度係数が±350ppm/℃と巻線抵抗の±100ppm/℃に較べると大きいので、消費電力の5倍以上の容量としてなるべく抵抗の温度が上がらないようにしています。(抵抗での消費電力は0.33Wある。)
リレーの青と緑の接点をショートさせるような描き方をしていますが、これは第一段階では電源を入れたら放電開始するようにしたかったからで、最終回路ではリレーで繋ぎ替えをいたしますので、このジャンパーは外してしまいます。
リファレンス電圧の生成には電源電圧の12Vを抵抗、半固定抵抗で分圧する簡易型としています。 これは実験段階では電源が定電圧電源で電圧が非常に安定していることによります。 そのリファレンス電圧を276/131/51.8mVの3種類に変えることで、
単二ニッケル水素、単三エネループ、単四エネループの試験に対応します。
この簡素化した回路で放電電流が最初から最後まで安定した定電流になるかは定電圧電源を電池の代わりに繋ぎ、満充電の時の1.2〜1.3Vから放電終了の1.0Vまで変化させて確認します。 但し実際の電池では放電が進むと内部抵抗が増加しますから、最終確認として満充電とした電池を繋いで放電終了までの電池電圧の変化を記録します。
但し単二についてはまだ充電器がありませんから、購入予定の東芝ニッケル水素電池インパルスの単二を入手していきなり放電試験をすることになります。 電池にどの程度の電力が残ってるかは不明ですが、購入後にすぐ使えるようなことが書いてあるので、満充電に近い量があると期待しています。 6本購入予定ですので6回テスト出来るわけで、一応傾向は掴めるでしょう。
この第一段階の回路は右上のレイアウトで組んでやります。 細長い基板ですが第一段階分は約半分しか組み込みません。
註)以下の基板レイアウトは大幅に変更されました。
詳しくはこちらに移動ください。(2016/04/15)
また最終的なレイアウトも左のように出来上がっており、空いたスペースに残る部品を組み込めば全回路が完成します。
残る部品の中でリレーは手持ちの物を使いますが、本番では消費電流が少なく大きさも小さい最新型の物に変更します。
また1.0Vの放電終了リファレンス電圧も第一段階と同様抵抗で減圧しただけのものですが、最終的な回路ではシャントレギュレータを使った安定度の高いものに変ります。
2016/03/04
放電回路の動作実験 その1
放電動作実験の基板を組立て早速実験に入りました。 ところが組みあがった基板に通電し各部の電圧確認をしていると2つの妙な現象に遭遇しました。
最初に発見したのは、電池の替わりに使おうとした定電圧電源です。 電圧は0Vから連続的に可能なのですが、電池電圧の1.2Vから徐々に電圧を下げて0.6V以下位になった時に、突然電圧ががくんと落ちて慌てて電圧を上げようとツマミを右に回してもうまく上がらなかったり、触ってもいないのに電圧がめまぐるしく変化してしまうなど、何かと何かが干渉しあっているのかぐちゃぐちゃの状態になり、電源スイッチを落として数分待たないと元に戻りません。
よくよく考えてみたら1.0〜1.2Vで1.2Aも流すというのはこの電源にとってはスペックを超える極めて無茶な使い方です。 また2つの定電圧電源を繋ぐ事で互いに干渉を起こしている可能性もあります。 そこで電源を電池の替わりに使うのは中止し電池そのものでテストすることにしました。
もうひとつの問題点は、ある条件で回路の消費電流がかなり大きい30mA前後にもなることでした。 但しダミーの電池として自作の電圧可変定電圧電源を繋いで、1.2V〜1.0Vの電圧を掛けた時には1mA前後の問題の無い消費電流であり、電圧を下げて行くと350mV位になると電流増加が始まり電圧低下でこれが増加して行き、0Vになると30mA前後に到達します。 そしてこの減少は単二の場合350mV以下で、単三の時には300mV以下、単四では110mVと設定電流が高いほど高い電圧で生じます。
無論350mVなんていう低い電池電圧は定電圧電源でのシミュレーションだからこそ設定できるもので、そのような電圧は実際には電池は既に壊れた状態を表しているので考えなくても良いのですが、電池を装填していないあるいは電池が繋がっていない時もオペアンプにとっては0Vと一緒(正確には無電圧なのだが)であり、電池ホルダーに電池はもとより何も繋がない状態でも発生する問題です。
そのような状態は、『メインの電源スイッチを入れてその後スタートボタンを押した後からリレーが作動して電池が繋がるまでの間』とか、『スタートボタンを押して電源が一旦ONとなるものの、電池電圧が1V以下(電池が無いを含む)であるためON保持をしないと電源遮断するまでの間』(何れも1秒未満でしょうが?)に起きます。
暫しの間そうなる原因を考えました。 そして断定ではないのですが、多分以下のような状況が起きているのではなかろうかと考えています。
電池が無いまたは電池電圧がかなり低い状態では、トランジスターのエミッターに繋がっている0.27Ω(ここでは0.28Ωとしている。)の両端電圧は、設計上のリファレンス電圧(336mV/160mV/63mV)よりかなり低い電圧になっています。 オペアンプはこの抵抗の両端電圧がリファレンス電圧と同じになるようトランジスターのベースに電流を送り込みコレクター電流の増加を図りますが、その効果は全く無くコレクター電流は0mA状態が続きます。 そうするとオペアンプはフル運転が続き、出力できる最大の電圧・電流に近いものを出し続けます。(実際11V以上の電圧がオペアンプの出力に出ていることを確認しており、これは12Vの電源電圧では限界の出力電圧です。)
一方出力電流もオペアンプの技術資料では電源電圧が15Vの時に出力出来る最大電流はTypicalで40mA、最小で20mAとあります。 この現象は電源電圧12Vで起きていますので電流は若干下回るかもしれませんがこちらも限界の値になっていると思われますし、これは消費電流増大に直結します。
最終的な充・放電回路では18組の放電回路が組まれますので、全く同時にこのようなことが発生すると瞬間的とはいえ540mAの無駄な電流が流れるわけでちっとも面白くありませんし、オペアンプ、トランジスタなど回路素子の破壊すら起きえます。 そこで善後策を考えることにしました。
思いついたアイデアはトランジスタをパワーMOS FETに置き換える方法です。 これだと不思議なくらい簡単に変更作業が可能です。 使ったFETはNチャンネルの2SK2232ですが、外径はトランジスタと全く同じTO-220で脚の配列が印刷面を見て左からゲート、ドレイン、ソースでそれぞれトランジスタのベース、コレクタ、エミッタに相当するので単に挿しかえればOKです。 尚その後FETのより安定な動作のため抵抗を2本(1KΩと1MΩを基板の裏に固定。)追加しました。 以下の回路図を参照ください。
オペアンプから見たMOS FETとトランジスタの動作上の違いは、MOS FETに対しては電圧駆動であり、トランジスタに対しては電流駆動にあります。 もう少し砕いて言うとMOS FETのゲートとソース間の電圧を変化させるとMOS FETはONとOFFの間を行き来しますので、ドレイン電流を調整できます。 その電圧幅は0Vから4V程です。
トランジスタではコレクター電流はベース電流のhfe倍ですから、ベース電流をコントロールすればコレクター電流をコントロール出来ます。 ここで使った2SD2092はhfeが600程もあるトランジスタで、単二の場合の1200mAの放電電流も2mA程度のベース電流で済みますので、オペアンプの小さな出力電流で充分駆動できると考えていました。 但し特殊条件下ではこの電流駆動が悪さに繋がったと言えます。
よってMOS FETを使った場合電池が無い場合にオペアンプは電流を流させようと最大出力電圧(約11V)を出しますが、FETを駆動するのに電流出力の増加はありませんので、消費電流の増加もありません。 よって問題解決が図れることになります。
その回路にて実験開始しました。 最初に購入した東芝製の単二ニッケル水素電池3本で試しましたがスタート直後の電池電圧は1.0〜1.02Vと充電されていないことが判りました。 従って単二の試験は充電器が出来てからすることにし、そこで1年近くたな晒しとしていた単三エネループをメーカー製専用充・放電器で、完全放電→完全充電を1サイクル終了後実験に供しました。
|
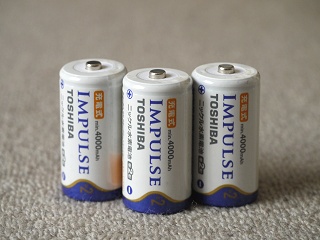 |
|
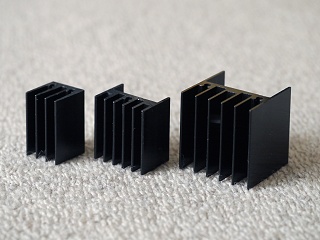 |
|
|
空っぽ状態で販売されてたので単二ニッケル水素の実験は棚上げ。 商品にカラッポなことは記載されてません。
|
|
放熱器は最終的に3種類から選びます。 後程単三以下では一番小さい物で充分であることが判りました。
|
|
|
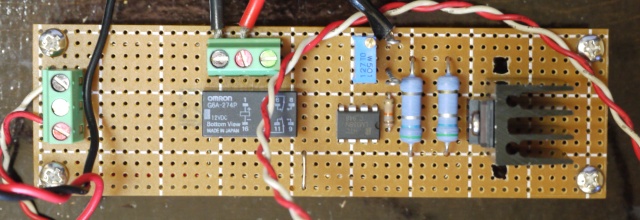 |
|
|
完成したテスト基板。 追加した2本の抵抗は裏付けとしています。 また放熱器は一番小さな16 x 16 x 25mmの物でOKであることが判りました。 ここに見えるものはその一番小さな物で、その上下に見える穴は一番大きな放熱器を固定する穴です。 リレーは単に固定しただけで接続はしてありません。
|
|
|
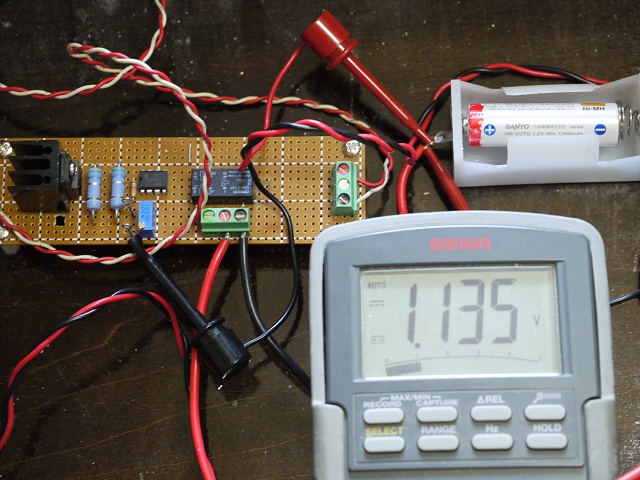 |
|
|
テストそのものは簡単で取り敢えずは電池電圧が1.0Vに低下するまでの時間を記録するだけで用が足ります。 単二電池ホルダーに単三を挿し込んでいますが、これが問題。 単二電池を入れても現象は同じなのですが、接触が極めて不安定でありテスト結果にもかなり影響が出ていると考えられます。 大電流を流すと僅かな接触の不具合が大きな電圧変動となりますので、よく検討された電池ホルダーの使用は絶対条件になります。
|
|
とまあ問題はあるものの、その結果は以下の通りです。
1.放電電流: 570mA(0.3C )
2.放電時間: 2時間58分
3.充電容量: 2.967h x 570mA = 1,691mAh
メーカー発表の充電容量は1900mAhですから11%少ない値です。 電池ホルダーの不完全接触で何らかの影響をしていることと、購入後約5年を経過している古さと最近1年間は使っていなかった電池ですので、このテスト結果は参考値に留めておきます。 数回の充・放電で充分なリフレッシュにより回復すると思われますので、電池ホルダーの改善なども実施した上で後ほど再テスト致します。
尚単二ニッケル水素電池の方は入手した状態で空っぽであることが判り、充電器がありませんからこのままでは試験を続けられないのと、今回のテスト中電池ホルダーでの接触不良がすさまじく、大電流を流すのに市販の電池ホルダーは全く使い物にならないことを確認しました。 従って予定には無かった信頼性の高い電池ホルダーの試作をしてから放電実験に戻ることにします。
2016/03/11
電池ホルダーの試作 その1
市販の電池ホルダーは使い物にならないと切り捨てるのは簡単ですが、まともな物を作るのも決して容易ではありません。 それらのキーとなりそうな項目を列挙してみます。
1.電気が通る部分は伝導率の高い材料とすること。
2.電気的な接触面積が大きくなるよう配慮すること。
3.電池の長手方向の抑え力が充分に高いことこと。
4.電池を受ける部分でのガタが極力無いこと。
などが取り敢えず考えられます。 1.については電気的な抵抗を減らしたいためで、例えば0.1Ωの抵抗があり1.2Aの電流が流れたとすると0.12Vの電圧降下が生じます。 ニッケル水素電池は完全充電状態で1.2〜1.3Vの電圧で放電終了電圧は1.0Vですからその差は0.2V〜0.3Vしかありません。 その環境で0.12Vの損失というのは全く無視できない値です。
2.は接触抵抗が大きくならないようにすることで、3.と抱き合わせて考えないとなりません。 接触面積が大きければ接触抵抗が下がります。 そして同時に電池を長手方向で挟んで力を加えた時に電池を傷付け難いということです。 そこでプラス側は曲率が緩い真鍮 M3のバインドネジ(ニッケルメッキ)を使います。 またマイナス側は真鍮 M4の6角ボルト(ニッケルメッキ)を使う予定です。
電池を挟む力を増すにはスプリングの力を高めれば良いので、単二の物を単三、単四でも使うことにします。
4、は電池の軸に対して直角な放射方向の問題ですが、本番では電池受けは全てトリマーで切削したU溝で受けてやればよいと考えています。 この辺り量産するのであればプラスチックの成型品と簡単に出来、それに較べるとかなり手間が掛かりますが、止むを得ません。
以上に基づき最も大きく影響しそうな1.について、電池ホルダーの導電部分に使われる可能性のある金属材料の功罪を調べて、アマチュア的にベストな材料を決めることにしました。
金属材料名 |
電気抵抗率(at 20℃) |
直径1mm2、 長さ1mの抵抗値 |
銀 |
1.6μΩcm |
0.016Ω |
銅 |
1.7μΩcm |
0.017Ω |
金 |
2.2μΩcm |
0.022Ω |
アルミニウム |
2.6μΩcm |
0.026Ω |
燐青銅 |
3.5μΩcm |
0.035Ω |
真鍮 |
6μΩcm |
0.06Ω |
ニッケル |
7μΩcm |
0.07Ω |
純鉄 |
10.2μΩcm |
0.1Ω |
鋼鉄 |
10〜20μΩcm |
0.1〜0.2Ω |
ステインレス |
72μΩcm |
0.72Ω |
これを見てびっくりはステインレスの抵抗率の高いことです。 殆どの電池バネは錆びないようにステインレス製の物が使われていますが、錆びると抵抗率は大幅アップしますからその意味では鋼鉄のバネよりも良いのですが、抵抗率がこんなに高いと問題が出そうです。
因みに電池ホルダーの抑えバネとして別掲写真の単二電池用のステインレス製電池バネを使う予定でいましたが、これの抵抗値を計算してみると、なんと0.125Ωという値が出ました。 1.2Aの電流が流れるとバネだけで0.16Vもの電圧降下が発生します。 そこでこのバネを使いながら抵抗率が上がらない方法を考えました。
その答えは伝導率の高い材料で作ったボルトを電池バネに通してやります。 ボルトの頭が電池のマイナス側に接触する電極になり、ボルトの先に銅線を繋いでやります。 こうすればより電流は伝導率の悪いバネを通らず、伝導率の良いボルトを通り問題解決できます。
そこでベストなボルトを探しました。 伝導率が最も良い銀で作ったボルトなんて販売されていませんし、あったとしても大変高価で現実味が無いでしょう。 銅は導電率が銀に近く価格も安いですから実現性はあるのですが、アルミニュウムと共に柔らかすぎてネジとしての強度が不十分です。
燐青銅は硬くて良い候補なのですが、これで作られたボルトは聞いたことがありません。 特注したらアマチュアの工作には不適当な価格にしかならないでしょう。
そんなこんなで辿り着いたのが真鍮です。 真鍮製のネジは鉄やステンレスほどではありませんが結構使われています。 ネットで調べたところ秋葉原に行けばM3やM4のニッケルメッキされた真鍮のボルトが入手可能です。 これならば鉄のボルトよりも抵抗値は40%ほど下がります。 ステインレスに較べれば1/10以下です。 秋葉原にボルトの購入だけで行くのは交通費が\1,000以上掛かるので、インターネットで調べまくった結果お眼鏡に適うような物が見付かりましたので、取り寄せました。
電池バネは単二用のものを近くのホームセンターで見つけました。 サイズは図の通りですが大変しっかりしていて横揺れも起こしにくいので、単三、単四用にも使います。 真鍮ネジを電池バネに通したスタイルは右の写真をご覧ください。
左が回路テスト用の電池ホルダーです。 単二用、単三用、単四用と3種類描いておりますが、一番左の単二用にアダプターを取り付けて単三、単四で使えるように考えただけで、本体は1個だけ作ります。
電池の大きさは図に記載してありますが、面白いことに長さは単二よりも単三の方が0.5mm長いです。 そこで長さだけは単三を基準にして単二の場合はM3のバインドネジを0.5mmのスペーサーを通して締め付ける、単四では5mm厚の板と1mm厚の板を重ねてスペーサーとしM3のネジを締め付ける! ということで寸法を出します。
幅方向は単二の電池がすっぽり入る箱として、単三や単四ではそれらの直径に合わせて溝を彫ったブロックを単二用の箱に落とし込む! という構造です。 この間当然ながら電池が変っても軸中心位置は変らないようにして、そこにM3やM4のネジが来るようにします。
M3、M4何れのネジも長めにしてあります。 M3は0.5mmと6mmのスペーサーを入れても対応できる15mmとします。 一方M4のネジについては電池を入れた状態でバネが5mm縮み、出し入れ時はバネが7mmまで縮められる(出し入れ時の隙間が2mm出来る)計算で30mmとしました。
尚何れのネジもダブルナットで固定しますがナットの間にケーブルをかしめた圧着端子を固定します。
木部は5mm厚がアガチス又は朴の工作材で9mm厚と18mm厚は合板です。 また0.5mm、1mm、2mmなどの厚みの物は発泡塩ビ材を使います。
始めに触れたようにアダプターを付け外して3種類の電池に対応しますが、電池が入っている/いない、を判別するマイクロスイッチは組み込めません。 従って最終的には構造を少し変えねばなりません。
その場合この図を見ればはっきり判りますが、電池バネが大きいので単三、単四で幅をそれなりに縮めることが出来ませんが、やむを得ないこととします。
2016/03/18
電池ホルダーの試作 その2
設計がまとまりましたので早速製作に入りました。 とは言っても薄板を切断するのが作業の大半ですから難しいことはありませんが、只ひとつ工作精度については寸法誤差が0.1mm以内になるよう、大きめに切断してカンナで或いはヤスリでドンピシャ寸法に追い込むことに力を注ぎました。 それらの様子は以下の写真と解説をご覧ください。
|
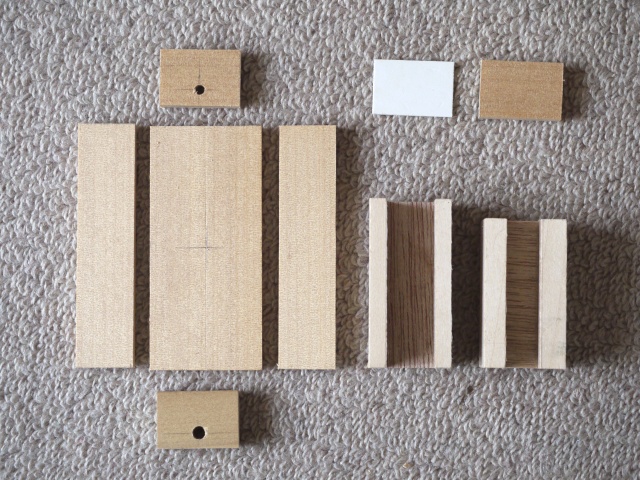 |
|
|
電池ボックス試作のために切り出した全ての部材。 各部材の寸法誤差はノギスを使って確認しながらカンナ、ヤスリで調整し、0.1mm以内に追い込んであります。 右下の2つは18mmシナ合板でトリマーで溝を彫ってあります。 茶色の部材中左下が9mmで残りは5mm厚のアガチスです。 右上に見える白い板は1mm厚発泡塩ビ板で、隣の5mm厚板と貼り合せます。
|
|
|
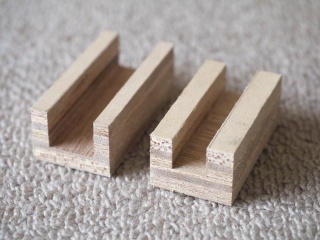 |
|
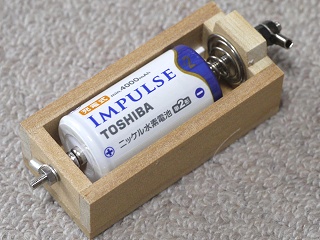 |
|
|
単三と単四用のアダプターです。 18mm合板にストレートビットで15mm、或いは10.5mm幅の溝を彫っています。
|
|
各部材を木工ボンドで接着しハタ金で圧着保持を2時間した上で2次加工を施し完成した単二電池用の外観です。 写真では見えませんが、プラス電極となるM3のネジはスプリングワッシャーを通してからホルダーに差込み、頭が0.5mm飛び出るようにしています。
|
|
|
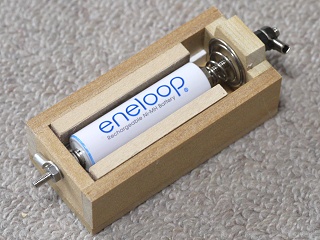 |
|
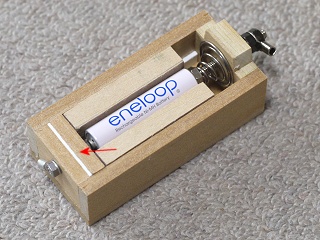 |
|
|
それに単三用のアダプターを嵌め込み、プラス電極のM3ネジに通していたスプリングワッシャーは外してあります。従って長さの内寸は0.5mm長くなっています。
|
|
単四電池の場合はこのように内寸を縮める6mm厚の調整板(矢印先)を嵌め込みます。
|
|
|
重要なことは、以上3種類の状態で電池抑えスプリングの収縮寸法は同じ(電池を抑える力が等しい。) ということで、
電池の大きさが変っても接触抵抗の変化は極小になります。 3種類の電池間で電池ホルダーの電気的な性能が等し くなるよう配慮した結果で、3種類別々に作らなかった最大の理由です。
|
|
|
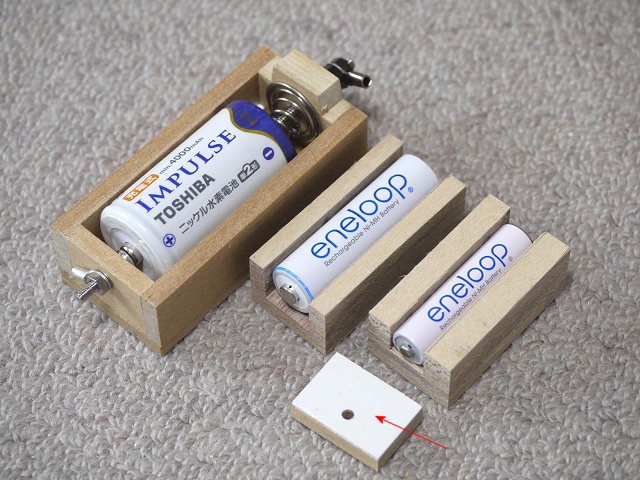 |
|
|
完成した単二、単三、単四兼用の電池ボックス。 自作する電池ボックスではこれ以上の性能は出せないだろう!との、自負があります。
|
|
製作した電池ボックスの性能
さて市販の電池ボックスとの性能比較をしてみました。 ここで予めご注意いただきたいのは、測定系の分別/検出/測定能力の限界、電気的な接触抵抗の変動によるものが原因でテスト結果に対する信頼性は余り良くないと考えられることです。 但し測定の目的は製作した電池ホルダーが充分に高性能かどうかの確認にありますので、理屈に合わない測定結果があっても、それらの結果が指し示す方向は期待していたものであることは間違いありません。 そのような観点から測定結果をご覧ください。
測定回路は非常に簡単で、製作した電池ボックスに充分太目のワイヤー20cmの先に1Ω 3Wの抵抗を繋いだものです。 そして測定場所は抵抗の両端間にて、SANWA製DMM PC-510で測定しています。 尚メーカー発表のPC-510の測定レンジでの測定し度は、直流電圧が0.08% + 2ディジット、抵抗が0.4% + 6ディジットで、直流電圧は兎も角抵抗の測定は値が極めて小さいので上で触れたような測定誤差を発生しやすいです。
この図の見方で気を付けてほしいのは中央上に点線で記載した抵抗で、描きようがないのでこの位置にあるように描いてありますが、実際には電池の外側全体に分散しています。 というのは、この抵抗は電気的な接触抵抗、配線材など電流が通る部分の電気抵抗を総合したものだからです。
テストした電池の開放電圧は1.302Vでした。 この値を単純に電池内部抵抗が無い起電電圧と考えて良いのかどうか私には判りませんが、そうだ!と仮定した上で以下の計算は進めています。
測定に際しては2本の電池を測定し、その測定結果を単純平均して図に表示しています。 最初に測定したのは抵抗両端の電圧でその平均値は1.203Vと出ました。 一方の市販の電池ホルダーでは1.134Vと0.069V低い結果が出ています。 これらから回路電流を計算すると、試作ホルダーでは1.203A、市販ホルダーでは1.134Aとなります。
一方単三エネループの内部抵抗がどのくらいあるのかをネット調べてみたところ、今回とほぼ同じ放電電流の1A時に25〜35mΩになっているようです。 そこで測定に使った電池の内部抵抗を仮に30mΩ(0.03Ω)として、その他の回路内の抵抗を算出しました。
損失電圧の計算結果は、市販のホルダーでは1.302 - 1.134 - 0.034 = 0.134V ありましたが、試作したホルダーでは、1.302 - 1.203 - 0.036 = 0.063V に低下しています。 それぞれの抵抗値を算出すると、市販品は0.118Ωに対し試作品では0.052Ωと半分以下に落ちています。
先週述べたように今回使っているステインレス電池バネは真鍮ネジと併用するため問題ないものの、それ自身で0.125Ωの抵抗があります。 テストに供した市販の電池ボックスに使われている電池バネもステインレスだと思われ、今回のテストではその分に相当する抵抗が削減できているような結果です。 いずれにしても試作電池ボックスは高性能ですので、この延長線上で最終型を設計したいと思います。
只ひとつ問題があるとしたら、何らかの軽いショックを電池に与えた時の接触不良が大幅に低下したものの未だ残っています。 操作感(電池の出し入れ)を損なわないようにするには電極表面に高い伝導性を持つ金属製のスポンジみたいな物を取り付けすっぽりと覆うことで接触抵抗を減らす?なんていうアイデアしか浮かびませんが、そんな材料があるのでしょうか?
2016/03/25
正式な放電テスト
前回の放電テストは電池ボックスの問題が大きすぎるので途中で停止しましたが、改善した電池ボックスを使って放電実験を単二を除いてやりました。 テスト用の放電回路のFETソース側に挿入した抵抗は都合で0.28Ω(0.56Ω2本を並列)としましたので、所定の0.3Cの放電電流を制御するには、リファレンス電圧を以下の値に設定してやります。
電池の種類 |
電池容量 |
放電電流(0.3C) |
リファレンス電圧 |
単二 IMPALSE (東芝) |
4,000mAh |
1,200mA |
336mV |
単三エネループ (三洋) |
1,900mAh |
570mA |
160mV |
単四エネループ (三洋) |
750mAh |
225mA |
63mV |
単三エネループの放電テスト
単二電池は充電器がまだありませんから今回は単三と単四のテストに留めます。 テストは以下の写真に示すように電源は自作定電圧電源を、電池電圧の変化測定はDMMを電池ボックス端子に、経過時間は旅行用目覚まし時計を使い、デジカメ(リコー CX-1)で5分毎にインターバル撮影して、後程放電特性グラフを作ります。 放電時間はDMMの電圧の読みが1.0Vになったら手動で停止しますので、終了間際だけは電圧変化を目視で監視しないとなりません。
放電テストは手持ち16本から無作為に選んだ3本でやっていますが、事前に三洋の放電機能付き充電器(NC-MR58)を使い完全放電・完全充電を3回繰り返して満充電とした物を使っています。
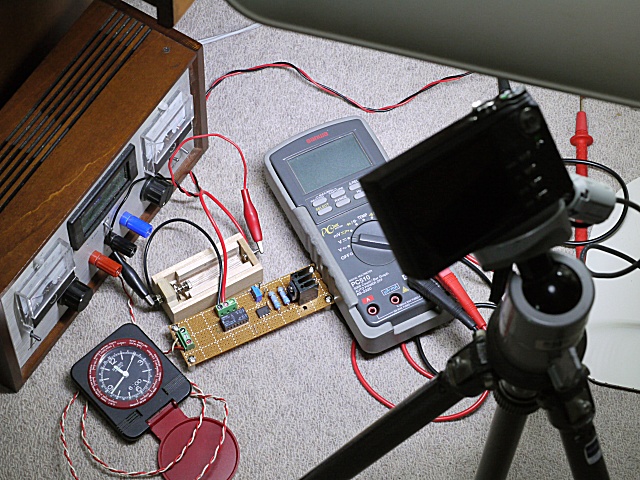 |
左端は自作定電圧電源で12Vに設定します。 その下に試作電池ホルダー、放電回路基板、懐中時計(SEIKO)と続きます。 上部斜めに遮っているのは自作LED電気スタンドの傘で、測定系全体の照明です。 その下の黒い箱は3脚の固定したカメラで5分毎のインターバル撮影をします。 その後MS Excelにてグラフ化したものが以下です。 |
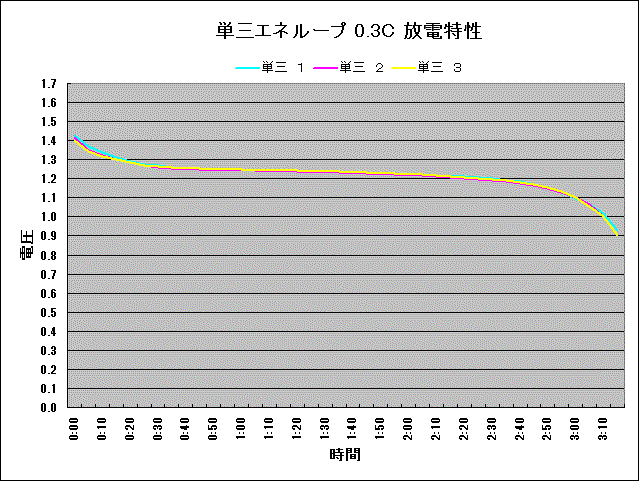 |
このグラフを作った基ネタは撮影した写真から電圧を読み取りExcelに転記しているわけですが、その元ネタを見たいという方はこちらをクリックしてください。
無作為に選んだ3本の放電特性ですが、かなり良く揃っていると思います。 そして放電時間については電池1が3時間11分、電池2と電池3が同じで3時間9分でした。 放電電流は570mAですのでこれから計算すると、電池1は1814mAh、電池2と電池3は1706mAhとなります。
前にやった放電実験では問題があるので参考としてお知らせしたデータは実は電池1のものでした。 そして1691mAhという結果を得ています。 それに対して今回は1814mAhと123mAhも増加しています。 これは電池ホルダーの残存抵抗によるロスや電池が活性化していなかったの2つの原因が改善されたことによるものと考えられます。
残念ながら改善したとは言え充電容量はメーカーのスペック(1900mAh)の95.5%に留まっていますが、現在充電に付いてはメーカー製の充電器を使っているわけで、今後充電器を自作の物に変えたらどうなるかを見たいと思います。
|
2016/04/01
正式な放電テスト2
先週に引き続き単四エネループの放電テストを実行いたしました。 公称充電容量が750mAhですから0.3Cの放電電流は225mA、0.28Ωの両端に発生する電圧=リファレンス電圧は63mVと設定しました。 試験本数は3本です。 以下の写真は測定の様子で、これを5分間隔でインターバル撮影しそこからの電圧の読みをグラフ化しています。
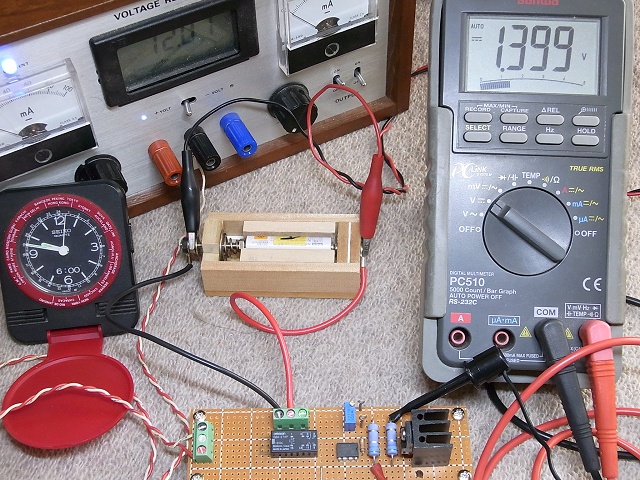 |
単三の時と殆ど同じで中央に見える電池ホルダーには単四用のアダプターが使われており、放電電流が225mAのためリファレンス電圧は63mVに設定してあります。
|
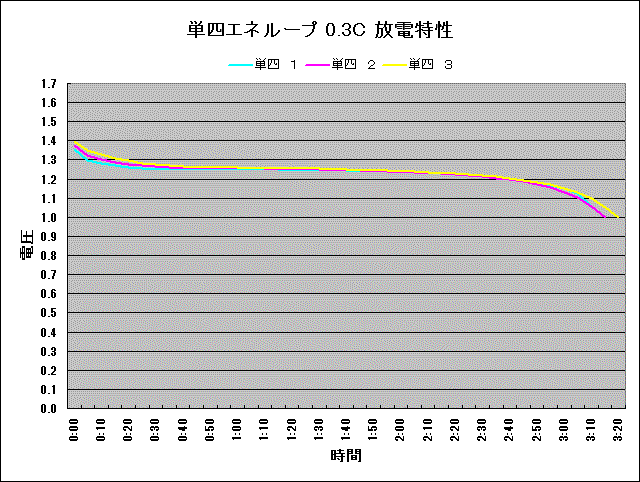 |
放電開始後暫くの間と放電終了間際に不揃いが目立ちますが、中間の安定期は非常に良く揃っています。 そういった中で3番(黄色の線)のエネループは全般に渡って僅かに電圧が高めで放電終了のタイミングも右にずれて充電量が多いようです。 それはどうやら3番は充電終了後1時間で放電に入り、他の2本は充電後数日置いた違いにあるようです。 このグラフを作成した基ネタ(インターバル写真から電圧変化を読み取った。)はこちらです。
充電容量は1番が放電時間3時間14分で728mAh、2番が放電時間3時間12分で720mAh、3番は放電時間3時間20分と最も長く750mAhと3番のみメーカーの定格値となりました。 一番容量の低い電池でも定格の96%ですから大変良い成績と言えます。
|
二つの電池の放電特性が判ったわけですが、それらを観察してある仮説が浮かび上がりました。 それは同じ0.3Cでありながら単四の方が単三より電圧がほんの少し高く推移し充電容量が高めに出ている理由です。 電池の内部抵抗や電池ボックスや配線に含まれる損失となる抵抗分が固定されていても、発生する損失は流れる電流に比例する筈です。 単三の場合は570mA、単四の場合225mAですから、単三における損失電圧は単四のそれよりも2.5倍を越えます。 この差が上で述べた原因だと想像します。 この理屈は単二ニッケル水素電池の場合更に損失電圧の増加となって現れるので、見掛けの充電容量は更に低下するでしょう。 無論メーカーも変ってしまうので、厳密な比較は出来ませんが、後程やる単二の放電テストを注意深く観察したいと思います。
2016/04/15
抜本的な放電回路の変更
先々週、次回には充電回路テスト基板の製作をと触れていましたが、実は放電回路の自動遮断回路部分の組立とテストをまだしておりませんでした。 そこで既に検討していた通り組み立てて、実験に入ったのですが、自動遮断動作は全くうまく動作しません。 そこで回路定数を調べていったところ1Vのリファレンス電圧を作る部分の抵抗の定数が計算ミスであることを発見し修正しました。
しかしそれでもうまく動作しません。 第一に電池の接続を放電モードに切り替えるリレーが動作していません。 リレーを駆動するトランジスターが駆動しきれていないようで暫くチェックしていたのですが、そもそも駆動トランジスタなんて不要なことを発見し、FETの出力側であるドレインにリレーを直結しました。 これで電池の接続はスタートスイッチを押すことでうまく切り替わり放電を開始しました。
ところが電池電圧が1Vに下がっても放電終了の遮断回路が動作しません。 電池電圧が1V以下になるとオペアンプの出力は10V程度まで上昇し、これに繋がるトランジスタがONになりFETのゲートに繋がったトランジスタのベース電位をゼロにすることでこのトランジスタをOFFにすることで、FETの動作が遮断(スイッチオフ)となる筈です。 各トランジスタのバイアスの設定が不十分かと回路定数を色々変更したのですが、FETに繋がったトランジスタのベース電位はゼロにはならず、従ってFETのゲート電圧はソースと同電位の12Vになる筈が、11.7V近辺で宙ぶらりんな遮断状態でFETは半ばOFFにしかなりませんでした。
この間20数箇所の回路定数の変更、回路そのもののマイナーチェンジを5回行っているのですが、満足できる結果に到達しませんでした。 そこでFETに繋がるトランジスタのベースをグラウンドにショートさせたところ即遮断します。 要は電子的なスイッチングのミクロレベルでの曖昧さが原因のようです。
そんなことから純電子的に遮断することをあきらめてリレーを使った物理的な遮断回路に変更することとしました。 左がその回路となります。 回路に記載された青地の電圧値は動作時の実測値です。 また赤字の電流値はそれらの電圧値から計算したものです。
まず追加したリレーの動作は放電中には電流が流れず放電終了のため遮断する時のみ電流が流れる使い方とします。 さもないとリレー自身の電力消費がバカバカしいことになります。 使うリレーはなるべく動作電圧の高い方が動作電流が低くなるので12Vタイプとしました。 手持ちにパナソニックのHYZ1-12がありましたのでこれを使いましたが、動作電流は16.7mAとLM358Nにとっては大きな負荷ですが、ものは試しと直結にしてみました。
リレーの接点はFETに繋がるベースに常時オープンとなるよう接続しています。 この状態にて試しに動かしてみたところ、これまでのぐちゃぐちゃの状態が嘘のように解消され電池電圧が1Vに下がると即遮断するようになりました。 最終的にはここで使ったリレーより消費電流の少ないオムロンのG5V-1(12.5mA)に変更し、ONとなる電圧は定格(12V)の80%(9.6V)であるところから、100Ω程度をオペアンプとリレーの間に入れLM358Nの過剰な負荷を少しでも軽減したほうが良いかもしれません。 右は大幅変更後の基板のレイアウトですが、ジャンパーワイヤーが沢山あり、半田付けし直しなどで大変汚らしいので、参考程度にしてください。 早速動作実験に入りました。 以下の写真をご覧ください。
 |
削除する部品よりも追加する部品の方が多いので、以前より窮屈なレイアウトになりましたが何とかうまく収まっています。 左下のスイッチ右の3点はリファレンス電圧の安定化の為に追加した5Vのレギュレーター回路ですが、本番では更に精度の高いシャントレギュレータを使い、6本の電池を一括して制御させるつもりです。
|
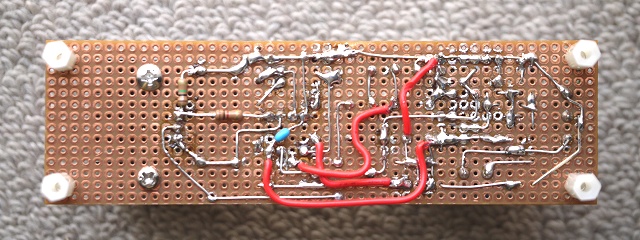 |
その基板の裏側はこのとおり。 ジャンパ線が増えて半田付けをし直ししたところなど、切り貼りが多く作り直したいところですが、再利用出来る部材は減ってしまうので、このまま実験を続けます。
|
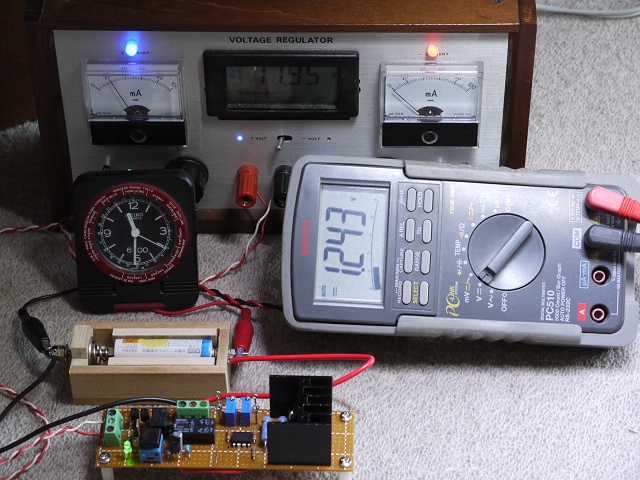 |
自動放電遮断実験を開始したところです。 開始早々の写真ですから終了は2:45前後。 そんな早朝まで起きていたくありませんが、自動遮断であれば記録はカメラにお願いして寝てしまうことが可能です。・・・・・・・
肝心な放電終了切断精度ですが、放電終了の1Vより僅かに高い1.01V辺りで遮断されます。 その原因はどうやら電池電圧を検出するのに電池の電極にDMMのプローブを接続しているので、電池電極とリファレンス電圧との比較をしている場所(ワイヤーで15cm程離れている。)との間に数箇所の接触・接続ポイントがあるので、それらが影響しているのかもしれません。(0.01Vの電圧差ですから0.01÷0.570 = 0.02Ωであり、この程度の残存抵抗?は容易に発生するでしょう。)
この誤差は1%になりますが、これが嫌ならリファレンス電圧をその分下げればドンピシャになります。 でもそこまで気にする必要はまずないでしょう。
|
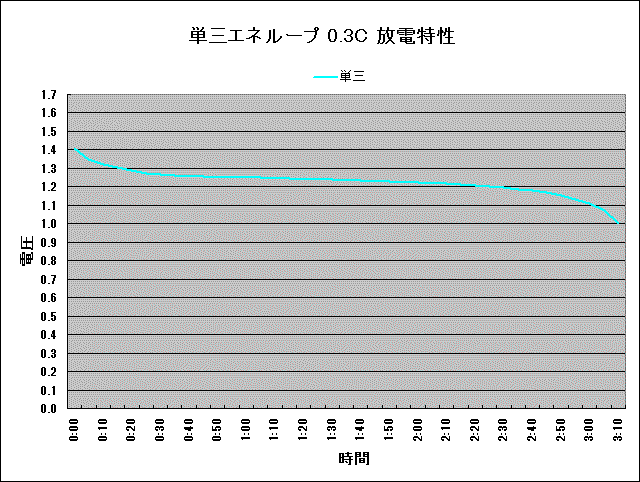 |
単三エネループによる放電特性を完全自動で撮りました。 放電終了は勿論自動ですがその前後を直視しており、遮断時の電池電圧は1.01V、遮断経過時間は3時間10分30秒(3.17時間)でした。 そうすると充電容量は1,807mAhとなります。
|
2016/04/22
充電回路の突っ込んだ検討
充電回路において予め考えておかないといけないのは、充電電流制御のトランジスタに掛かる負荷が充電する充電池の本数により大幅に変化することです。 具体的にどういうことを指すかというと、充電中充電池1本に掛かる電圧は最大で1.53V位ですが、その他に逆流防止のダイオードで0.7V、充電電流検出抵抗で0.4V程度の電圧降下が見込まれます。 充電電圧はこれらの合計で電池6本の時には10.28Vの電圧が必要となり、ここでは1.72V高い12Vの電源電圧としています。
この差の1.72Vは充電電流制御トランジスターに掛かり、充電電流安定化のクッションのような役目をしているのでゼロになっては困りますが、大きすぎても問題がおきます。 1.72Vは最大充電電流(400mA)の時の値ですが、0.688Wの無効電力を消費することになり30PC30L30BAという最外寸30 x 30 x 30の予定の放熱器に付けた時に7℃程度の温度上昇でほんのり暖かくなります。
但し同じ充電回路で1本の電池だけ充電する場合には電池5本分の7.65Vが充電電流制御トランジスタに更に加わわり9.37Vとなります。 そしてここで消費される電力は3.75Wとなり、放熱器に取り付けた状態で温度上昇は43℃見込まれます。 真夏であれば放熱器は75℃以上にもなるわけで、これは少々抑え無効電力を減らしたいところです。
そこで電池の本数により充電電圧を変えてやることを考えました。 但し抵抗やレギュレーターなどで電圧を降下する方法はそこで降下分の熱が出てしまい、電力の有効利用にはなりませんので、DC-DCコンバータで電圧を下げてやることを検討しました。
理想は電池の本数に従い充電電圧を連続的に変えたいところですが、市販のDC-DCコンバータではそれに対応できる物はなく、現実を直視して2段切り換えの方法を3つ頭の中で検討しました。 そのひとつは、私がこれまでに多用しているコーセルのSUCS31205(入力9〜18V、出力5V±5%、0.6A、変換効率77%)という仕様のものを使う方法。 2番目はNJM2360というICを使って、入力12V、出力6〜6.5V、1A、変換効率70%という仕様で自作する方法です。 3番目は2番目のDC-DCコンバーターの出力電圧を11V、8V、5Vの3段切り換えとする方法で、下に行くほど制御トランジスタで発生する無効電力消費が減りますが、自作のDC-DCコンバータはどうしても変換効率がメーカー製に較べると落ちる点が気がかりです。
これらの4つの方法で電池本数で充電電圧を切り換えた時の充電電流制御トランジスタで発生する無効電力の消費がどうなるのかを一覧にしてみました。
上の表で『電源電圧との差』となっている部分が制御トランジスタで発生する無効電力として、その右の(X) W(ワット)になるわけです。 上から見て行くと12Vで1〜6本の電池を駆動した時当然ながら1本の時に最も大きな3.75Wの無効電力が発生し何と全消費電力の78%が無効電力になります。 前述のように夏ですと放熱器は75℃以上になる可能性があります。 これはトランジスタは壊れなくても触ると火傷をしそうな温度です。
2段目の場合は5V出力のDC-DCコンバーターで1〜2本の電池を充電する場合で、この時の最大の無効電力発生は3本の時で2.52Wに下がります。 その時の放熱器の温度上昇は30℃ですから真夏で65℃程度になると考えられまだ熱いですが触り続けない限り火傷はしないでしょう。
3番目は6〜6.5Vの出力電圧を持つDC-DCコンバータを自作した場合で、最大無効電力は1.91Wに下がりこの時の放熱器の温度上昇は24℃程度ですから放熱器の温度は真夏でも60℃以下となる可能性が大です。
4番目は出力電圧が自由に設定できる点を生かして、11V/8V/5Vの3段切り替えとしたもので、最大の無効消費電力は0.95Wとなり放熱器の温度上昇は13℃程度に抑えられ真夏でも放熱器表面温度は50℃程度と熱いけど火傷はしない温度に収まりそうです。
こんな結果から自作のDC-DCコンバータにチャレンジしてみたくなっています。 幸いNJM2360は数個の手持ちがありますので、コイルとショットキーバリヤーダイオードを入手すれば実験できますので、実現の可能性を模索したいと考えます。
2016/04/29
放電終了検出/充電トリガー回路
充電回路の心臓である部分は以前製作した物では定電流回路にLM317Z + 抵抗1本で構成していたのですが、損失を抑えるのと大電流に耐えるようオペアンプと大電流ダーリントントランジスターの組合せに変更しています。 但し放電・充電の自動充電器を考える時、単独で行われる放電終了を正しく検出し充電を開始する部分は未知の部分ですので、充分な事前のテストせねばと考えています。 これは先週触れた電源電圧を電池本数に合わせて変更する点より重要度が高いです。
そこで放電終了検出/充電トリガー回路をブロックごとに分割して実験を進めました。 第一番目のブロックは、放電終了検出/充電トリガー回路の放電終了検出部分をスタンバイさせる部分ですが、FETとTRを組み合わせて放電スタートスイッチを押した時にTRのベースに0.7Vの電圧が掛かります。 これでTRはオンとなりFETもオンになるためドレインに12Vの電圧が出て2番目のTRがオンとなり自己保持するため、放電終了待ちの待機状態になります。
この部分は実回路での実験はしておりませんが、特に問題はないと考えています。
放電動作が終了すると放電中に電池を個々バラバラの接続にしていたリレーがオフなるたびに電池6本の直列接続に随時変更して行きます。 そして最後の電池の放電終了と共に最大6本の直列接続が生成され、最初のプラス電極と最後のマイナス電極の間にはオープン状態から約1V〜8Vの電圧が発生します。(電圧は充電する電池の本数で変動します。)
この部分の実働実験には少なくとも2つの放電回路が必要になるため、確認はまだ先になります。
一方JFETの2SK30Aは定電流回路を形成しており、ドレインは電池ホルダーの最初のプラス極に接続されておりますので、この突然発生した電圧(1〜8V)を完全な定電流ではないものの0.033〜0.092mAと8倍の電圧が2.8倍に圧縮されてTRのベースに流れ込みTRはオンとなります。 そうすると2番目のFETがONとなります。
この部分の動作確認はバラック回路を組み上げ、1〜8Vの電圧をFETのドレインに印加し、トランジスター/FETがオンできることを確認済みです。
次に挿入されたタイマーの目的は、もしも電池が放電動作で加熱した場合にそれを冷やしてから充電動作に入るためのものです。 これは以前に何かの本で読んだ記憶によるもので、電池が加熱したまま充電に入るのはあまり良いことではない! というものでしたので加えた回路です。 但し単三、単四エネループでは加熱するようなことはありませんでした。 単二の場合はまだ確認できていないのですが1.2Aという大きな放電電流ですので過熱するかもしれないと考え25分で設定しています。 もしもこれでは不足の場合は複数のタイマー回路縦列接続にて時間を増加させるつもりです。 そして単二ニッケル水素電池でも発熱が少なく冷却期間は不要ということであればこのタイマー回路とその後の電子スイッチ回路は外してしまいます。
タイマーを外さない場合、この後に繋がる電子スイッチの駆動は25分タイマーによるディレーオンとしたいので、トランジスターで極性を反転させて電子スイッチをオンしています。 そしてこのFETがオンになると充電動作が開始されます。
この部分(タイマー + 電子スイッチ)はバラック配線にて動作の確認をしました。 タイマーは電源回路ONと同時にスタートするためマクロ的にはタイマーの出力は繋いだ瞬間はH(ハイ)で12V 近くある筈で、このため最後のFETは瞬間的にONになりやすいのですが、実験ではそのような兆候は全くありませんでした。
という構成ですが、放電終了検出/充電トリガー回路は12Vの電源回路に2SJ377を使った電子スイッチを3つ縦列接続するわけで、これらのスイッチでのトータル損失電圧(Vds ONによる)が高いと充電電圧不足になる恐れが出てきます。 それが心配されるのは単二ニッケル水素電池の充電時で400mAの充電電流が流れます。 そこでFET(2SJ377)の技術資料からおおよそのVdsを調べてみました。
右が技術資料に載っていたVds-Vgsのグラフですが、この回路ではゲートをGNDに接続した時をONとしVgsは電源電圧の12Vになります。 そこでVgs=12Vの所に赤の縦線を引きました。 そしてIdが1Aとなる線を赤の1点鎖線で引きました。 この時のVdsは約-0.15Vと読めます。 そしてこのグラフを良く見るとVdsはIdにほぼ比例していると思われるので、0.4Aの充電電流の時にVdsは、-0.15V x 0.4 = -0.06Vの値になります。
これが3連続ですから合計の電圧損失は0.18Vとなります。 また計算上の充電電圧は11Vまで下がってもOKであり、使用予定のシールドバッテリー(定格: 12V 12Ah)では0.5Aの消費電流で12時間使っても電池電圧は12V程度に留まるのでFETによる損失が少々増えてもまだゆとりがあるだろうと踏んでいます。
ここで一度に1系統で電池4本を処理できる回路を左のように描いてみました。 実際には電池6本を2系統または3系統ですからかなりのミニ版ですが、これがうまく動作しなければ最終版が実現できるわけがないのです。 そして描いているうちに、ワンステップとして本当に作ってみるか?と目覚めつつあります。
というのは、放電時は6本の電池をバラして処理し、一方充電時はリレーで繋ぎ直して直列で一括処理する! なんていう都合が良さげな動作が思考実験では矛盾無くうまく実現出来るとしているものの、実はそううまくは行かなかった!!
となる可能性が現実ではあるからで、そうならないリスク回避というか損失を最小限とするためのワンステップが必要である気がしています。
そのような想いがあることからこの回路には電源スイッチを入れて放電・充電が終了するまで、LEDでもってどの段階にいるのかが判るような配慮もしてあります。 具体的には、赤のLED(動作中点灯で電源SWオンを表す。) → スタートスイッチを押すと電池が装填された所のみ橙のLED点灯(只今放電中で消灯すると放電終了)、→ 黄色のLED点灯(全ての放電が終了し、電池冷却中) → 緑色のLED点灯(只今充電中) → 青のLED点灯(充電が終了、電池を外して!) → 電源SWオフで赤のLED消灯。 ということです。
2016/05/06
思いがけない良い展開
いよいよ充電回路の動作確認実験に入る所なのですが、とんでもなくこのテーマに好都合な部材を発見してその部材の性能の確認実験を致しました。
とんでもなく好都合な部材とは、DC-DCコンバーターを作るモジュールとなるICで、半導体の専門メーカーであるサンケンの製品です。 DC-DCコンバーターには入力電圧に対し出力電圧を上昇させるアップコンバーターと、出力電圧を下げるダウンコンバーターの2種類がありますが、これは後者です。 おおまかなスペックは入力電圧: 8〜30V、出力電圧: 3〜16V(但し入力電圧より3V以上低いこと。)、最大出力電流: 2A、変換効率: 出力5V/1A時に90%(Typ) といったものです。
先ず驚くべきは高い変換効率で、90%という値は全てのDC-DCコンバーターでトップランクになるでしょう。 そしてこのモジュールにはDC-DCコンバーターには不可欠で通常は外付けされるコイル、ショットキーバリヤーダイオードを含んでいるので、入出力のコンデンサー2本と出力電圧設定用の抵抗2本を追加してやれば簡単に且つコンパクトに作れます。 右がその回路で、ここでは出力電圧を調整しやすいよう半固定抵抗を使っていますが、固定抵抗2本での使用も無論OKです。 この回路定数で後程テストの結果をお知らせします。
モジュールそのもの(IC)は太ったTO-220のような格好ですから、TO-220用の放熱器を使えます。
|
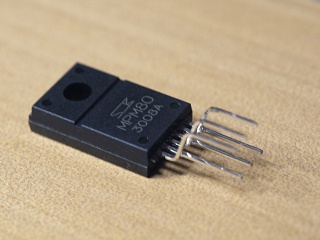 |
|
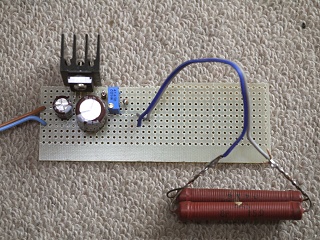 |
|
|
分厚いTO-220といった風情のパッケージですが、脚は6本出ていてそのうち1本は使われていません。 脚は2.54mmピッチで出ていませんが、2.54mmピッチの基板でも実装可能です。
|
|
DC−DCコンバーターではお約束のコイルやショットキーバリヤーダイオードが無いので、なにやらリニヤーレギュレーターを組んでいる雰囲気です。 16 x 16 x 25mmの放熱器を取り付けています。 右下は15Ω8W2本をパラレルとした巻線抵抗による負荷です。
|
|
|
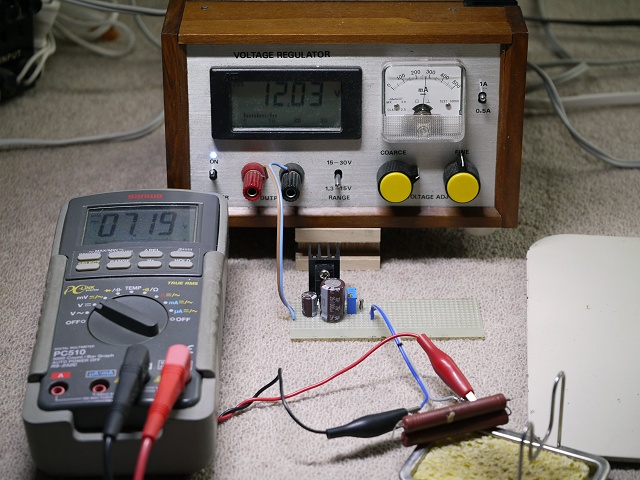 |
|
|
組み立てた基板で実験中ですが、看板どおりの超素晴しい性能でした。 詳しくは次の表をごらんください。
|
|
|
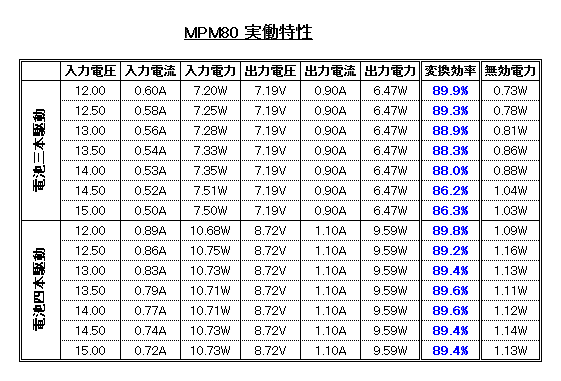 |
|
|
入力電圧は12Vから15Vまで0.5V刻みで可変してみましたが、実際には電池電圧は12〜13Vにあります。 そして出力電圧は設定電圧に張り付きぶれる事が全く無く良好です。 出力電流は実際の値に近い所(2系統で0.8A強)で実験しました。 大変な驚きは高い変換効率で、ほぼ90%という素晴しさです。 これはここで使った、16 x 16 x 25の放熱器で充分であることからも判ります。
|
|
以上の結果だけでも充分に興味が出てきますが、冒頭に『とんでもなく好都合な部材』と記したのは、このDC-DCコンバーターモジュールを使いこれまで進めてきた充電回路の延長線でより省エネの実現を図れることで、以下の図は前回提示したものに若干変更を加え今回出てきた方法(表の最後)とを比較してみたものですが、回路動作の点でややこしさが減少して、省エネという明らかに一段進んだ方法になることが判ります。
どんな変更を加えたかというと、12Vの電源はシールドバッテリーですが、満充電時には13Vまで高くなるため充電回路の無効消費電力は増加しますので、それを計算して一覧に追加しました。 またこの表では以前にあった11/8/5Vの電源は余りに複雑になるため削除しました。 それと充電に必要な電圧の中に制御TRのVceを追加しました。 これは使用するトランジスターはダーリントンタイプのためVceが小さくならないので無視できないため、特性図からゆとりを見ながら一律1Vとして計上しています。
前回の表から構造が余りにも複雑になるので削除した電源電圧3段切り替えを除いた中で最も良かった電源電圧12V/7V切り替えよりも無効消費電力が1.93Wから1.50Wに減少し、ややこしい12V、7Vの自動切り替え回路も不要になります。
そしてもうひとつの方法はDC-DCコンバーターで定電流駆動をさせることにより、更に省エネ度が高く回路も簡素化できる可能性があります。 ここで何故可能性と表現しているかというと、メーカーの技術資料を見た範囲では推奨回路からはみ出るため、問題なく動作するのかどうか(特に安全性や安定性で)確実ではないのです。
そこで左の回路にて充電のシミュレーションをしてみました。 簡単に回路動作を説明しますと、32.9Ωの抵抗は単三エネループ4本を繋いだ状態で、4.7Ωを7本直列で作っています。 この両端電圧は実測6.27Vですので、電池1本辺り1.53Vとなり充電末期の最も電池電圧が上昇した辺りを模していることになります。 またこれに流れる電流は190mAとしていますが、単三エネループ0.1Cの電流値で、これはICの7番ピン(常に0.8V)とGNDの間に入る抵抗(ここでは4.2Ω)で決まります。(0.8 ÷4.2 = 190.5mA ということです。)
前にお見せしている標準回路とどこが違うかというと、電圧設定回路(4.2Ωと32.9Ω)が電圧設定動作と同時に負荷抵抗になっています。 これを流れる電流は4.4Ωで固定され、32.9Ωが変化しても、この抵抗の両端電圧がモジュールの動作範囲内(出力電圧が入力電圧の3V以下で15.2V〜2.8V)であれば、流れる電流は190mAに張り付きます。 このシミュレーション実験結果は以下の表をご覧ください。
実験は7時間連続で実施しましたが、何も不具合は発生せず認められませんでした。 また損失が大変小さく放熱器は16 x 16 x 25の物を使っていますが、指を触れても熱くなるようなことがありません。 当然ながら変換効率も全て90%以上という信じられない結果を得ています。
よって時間が掛かりますが単二ニッケル水素電池を模して同様な動作と安全性の確認実験をすると共にメーカーにも問い合わせるつもりです。
長々と述べて着ましたが以上が、『とんでもなく好都合な部材』の詳細背景でです。 拘りを持って更に確認・検討を進めます。
2016/05/13
そうそう うまい話はなかったの巻!
さてMPM80の動作を確認する中で、先週最後に紹介した定電流出力方式で低電圧(電池の駆動本数が少ない場合)を確認しておかねばと、2.33Vの出力電圧になる抵抗を計算して実験した所、一応動いていて変な発熱も無いのですがやけに入力電流が大きくなっていることに気付きました。 そこで変換効率を測定した所50〜60%とこれまでの話が全て嘘のような信じられない値が出てきます。
そこで出力電圧を上げてみた所70%台まで回復してきました。 そして思い出したのですが、出力電圧の範囲は3V〜16Vになっています。絶対定格ではないため壊れることは無いでしょうが状況はかなり悪いです。
冷静になって頭の中を整理すると、技術資料に記載されている事項で2つの違反をしています。
第一が出力電圧で、メーカーは3V〜16Vと規定している所を、それ以下の電圧で使っています。
第二が7番ピンとGNDの間に繋ぐ抵抗で、680〜1.5KΩとされていますが、190mAの定電流のために4.2Ω、400mAの定電流のために2Ωなどと滅茶苦茶に低い抵抗を繋いでしまっています。 この設定条件を守るとGNDとの間は0.8Vですから、1.2mA〜0.53mAの電流しか許容されないことになります。 よってLEDの定電流駆動にも使えないのです。
こんな状況から私の問い合わせに対するメーカーの返事は未だ届いておりませんが、定電流駆動の目的で使うことはあきらめるべきと結論を出しました。 但しMPM80を使った充電回路として3本直列2系統で6本の充電回路であれば、発熱は低い状態で(最初に考えていたものより効率が良い。)運転できますので、その方法に戻して先に進めます。 その場合の比較は以下の表をごらんください。 赤字の場合が最も発熱が大きく効率の悪い状態を表します。 そしてピンク2重マルの3つが、単二ニッケル水素、単三エネループ、単四エネループの最終的な損失電力計算結果です。
註): その後メーカーから、『定電流負荷のような使い方をした時の問題点』に関した問い合わせに対する大変丁寧
な回答が届いています。 かなり長文ですのでその要旨をお知らせいたしますが、
『定電流負荷方式で単二、単三充電池の充電に使った場合、動作が不安定、或いは異常発振などの不具合が生
じる可能性があり、メーカーとしてはお奨めできない。』
というものでした。 既に実験結果により動作がおかしいとしてこの使い方は止めましたが参考までに!
|
最初に考えた12Vで6本を直列に充電する回路で1本だけを充電すると電源の電池電圧の変化で3.35W〜3.75Wと猛烈な発熱に襲われます。 その当時考えていた30 x 30 x 30mmの放熱器では約40℃以上の温度上昇が考えられます。 真夏であれば80℃近くまでとなる可能性もあるわけで、触ると危険なくらいです採用できません。
2番めと3番目はメーカー製又は自作の低電圧DC-DCコンバーターと12Vのバッテリーを切り換えてやる方法で、1番よりがくんと発熱は下がりますがDC-DCコンバーターと12Vバッテリーの自動切換えという厄介な回路が加わるのが難点で、これも二の脚を踏みました。
4番目は自作の高効率DC-DCコンバーターですが、優秀なモジュールのお陰で出力電圧が可変であり、しかも変換効率が90%に近くなるという優れものです。 これで7Vを作り出し2系統の3本直列を駆動する案を単二、単三、単四何れにおいても踏襲しています。 電源系統を切り替える必要がありませんから回路が複雑になりません。 DC-DCコンバーターの出力電圧を切り替えることも考えましたが、単二と単三で0.1W程度の差しかないので止めました。 但し単四については単独の充・放電装置になるので、仮に6.68Vとして計算しています。
想定される発熱は1.63Wですから、30 x 30 x 30の放熱器で約20.5℃の温度上昇に留まり、最も暑い時期でも表面温度は約60℃くらですから、熱いですが触っていきなり火傷という危険はかなり減ると思います。(発熱対策については強力な放熱器の採用で安全性を高めることを考えていますが後程説明します。)
さて使えない回路のショックでカリカリになった頭が冷えてきた所で、MPM80をもう一度見直して徹底的に使い込む要点を搾り出しました。 要は技術資料を実測データを含め漏らさずに読み直したのですが、面白いことに気が付きました。 それらは、
DC-DCコンバーターとして変換効率が良くなる条件が間接的に読み取れたことでした。 それらとは、
1.入力電圧12Vの時、変換効率は出力電流が0.5A〜0.7A辺りで最大となり90%に到達する。 出力電流が170mA〜1.6A の範囲では85%以上になる。
2.入力電圧12Vの時、出力電流0.75A以下で0.5W以下の内部損失になる。 出力電流が0.4A以下であると内部損失は
0.25W以下になる。
3.MPM80の表面温度は環境温度25℃、0.5Aの負荷電流で13℃の温度上昇が見られる。 0.4Aでは10℃、0.25Aでは7℃
の温度上昇に留まる。
以上の事象は出力電圧5Vの時とされており、2系統の3本直列を駆動する案では約7Vの駆動電圧を考えているのでそれ程かけ離れた結果が出ないだろうと考えています。(出力電圧は3〜16Vとされていることから考えて。)
そう仮定すると上記3点から最も効率の良い出力電流は0.4A辺りで、変換効率は90%、内部損失は0.25W、表面温度上昇は10℃ということになります。 この値(0.4A)は単二ニッケル水素電池の1系統の充電電流そのものです。 また単三エネループでは0.19Aですから変換効率は85%位、内部損失25%以下、表面温度上昇は7℃程度です。 単四エネループの場合は2系統をひとつのDC-DCコンバーターで賄うと0.15Aですから変換効率は85%を少し切るかもしれませんが、内部損失、表面温度上昇は更に下がると思われます。
さて気を取り直して描き上げた充電回路と2次試作の放電回路は左の通りです。 ここでは単二又は単三の電池何れか1本が放電→充電と連続動作するよう描かれています。
左側の放電回路を2つ追加してやれば最終的な1系列の放電・充電器の仕様となります。
回路動作の確認と発熱の処理関係のシミュレーションなど全てがこの実験機で確認できるはずです。
2次試作の放電回路基板の大きさは1次試作より大幅に縮め、96.5mm x 30.5mmと単二ニッケル水素電池のホルダーより小さくなっています。 最終基板は短辺の6倍の183mmとし、その上に6本の単二ニッケル水素電池6本を並べる予定です。(更に充電回路が加わるが?)
右端に見えるのは放熱器の一部で最終的にはこの下に5つの放熱回路基板が追加され、長い放熱器が横断的に取り付けられます。
こちらは充電回路の基板レイアウトで、基板長は放電回路用と同じ96.5mmにしています。 放電用基板の短辺は30.5mmでこちらは36.5mmですが、前述の6つの放電回路に充電回路を追加(36.5 x 2)で、トータル 256mmの幅になりますが、これに250mm x 50mm x 30mmの放熱器が組み合わさては? という実に合理的な構造を志向しています。
何やら最終モデルの仕様に首を突っ込みすぎているきらいがありますが、単純に1電池放電・充電実験機を作るのではなく、常に最終モデルの姿を考えながらその1仮定としてのモデルとして捕らえて検討していることをご理解ください。
ところで単四のことを忘れているように見えますが、単四は単独の別モデルとして考え、放電回路3つと充電回路を1系統とし、これを2系統に充電回路用電源1組を組み合わせるスタイルとする予定です。 この時のDC-DCコンバーターは電流供給値が150mAとなるので、効率の点で有利です。 発熱の点では上の一覧表にあるとおり、単二、単三から大きく変りませんので単二を中心とした確実な設計が慣用と考えています。
さて充電回路と放電回路の放熱について大局的にどう考えているかについて、ここで明確にしておきます。
放熱に関する考え方
以下に述べる部分は次に掲げる放熱器を使用する前提で書かれています。
1.放電時の発熱について
放電時の発熱は充電される電池の残存エネルギー放出によるもので、これを低減しても駆動効率は全く改善されません。 またこれを低減するには放電電流を下げるしかなく、処理時間が長くなりますので現在設定している0.3Cから下げたくありません。
よって単二ニッケル水素電池において1.2V x 4000mAh x 0.3C = 1.44Wの発熱はやむを得ません。 従って6本の単二電池を一度に放電する場合の発熱は8.7Wとなります。
先程触れたように単二電池ホルダー6本分と充電回路2つ分の幅合計に合わせた250mm x 50mm x 30mmの放熱器を共用しようとしていますが、メーカーの資料によると8.7Wの発熱による放熱器の温度上昇は約15℃と求まります。(右の図を参照)
真夏で気温が40℃となっても55℃の表面温度ということですから、火傷などの安全性で問題はないレベルになると思いますし、無論放電本数が減ったり単三であれば更に温度は下がります。
2.充電時の発熱について
一方充電時の放熱は駆動効率に直結しますから、充電本数に応じて充電電圧を変更するのがベストですが、回路が複雑になり過ぎるため1系統3本直列を最大本数と考えています。 充電時の電池1本辺りの電圧は最大で約1.53Vですから、この考え方に添うと3本の時に対して、2本充電では1.53V、2本充電では3.06Vと損失となる駆動電圧の増加が生じます。
単二であれば充電電流が0.4Aですから0.612W(電池2本充電時)、1.22W(電池1本充電時)が増加する損失電力になります。 表で赤字で表示している値はそれらに3本充電時の損失を含み、単二で1.54Wという値が最大ですが、電池が変っても0.1W程度の変化しか生じていません。
さて上で説明した放熱器に取り付けたときにどうなるかというと、1系統で1本だけの充電で1.54Wの熱が加わりますが、2系統ありますから3.08Wが最大です。(実は1系統で2本充電とすればその系統で0.82W発生しもう1系統は休んでいれば0.82Wで済んでしまいますが、意地悪い最大のケースで考えるとそうなります。)
さてその時に同じ放熱器に取り付けると約5℃の温度上昇にしかなりません。 1系列で2本充電とすると1〜2℃程度に留まるでしょう。 よって放熱板を共用することにより充電時の発熱は全く問題が無く、それよりも損失電力が元となるシールドバッテリーのエネルギーを無駄に消費することになるので、そちらの観点から損失の低減に意を払うべきと考えます。
以上で充電回路の検討は終了したように思われるかもしれませんが、どっこいまだ上で取り上げた放熱器にひっかかりを感じています。 何かと言うと購入価格です。 数箇所の販売店をチェックしたのですが在庫を持っている所はありませんでした。 従って特注扱いになりますが、その場合の価格はかなり上がる可能性があります。 若しもべらぼうに高かったら別のソリューションを考えねばなりません。
2016/05/20
只では転ばなかったの巻!
先週最後に触れた放熱器の見積り価格が届きましたが、心配どおりになってしまいました。 何と\5,221.-で納期1ケ月とのことです。 同じシリーズで202mmの物は\1,670.-で販売されています。 材料体積比で1.23倍となりますが、同率で価格がアップするとしたら\2,054.-ですからその2倍以上の値付けとなります。 こんな見積もりを良しと出来ませんので、放電回路基板には202mmの長さを、充電回路基板は58mmの長さの物を使う事を頭に入れて進めたいと思います。 この時の購入価格計は\2,053.-です。
充電回路基板用放熱板は放電回路と共用であれば、充電時には大きな放熱板を独占できますので充電回路の制御トランジスタの発熱など気にしなくてもOKですが、単独の58mm放熱板となると温度上昇を10℃に抑えるためには1.3W程度の発熱に抑えないとなりません。 また発熱は損失電力そのものですから、何とかしないとあかんな! と暫し考えました。
そこで充電用電源電圧を切り替えるアイデアをもう一度蒸し返すことにしました。 無論定電流負荷ではありません。 電源電圧としては7.0V/5.5Vを最大3本直列充電の場合に、また8.2V/5.5Vを最大4本直列充電の場合とします。 こうした時に無効電力(損失電力)がどうなるかを調べたのが次の表で、これは先週紹介したものの延長にあるとお考えください。
これと先週掲載した比較表と較べると、最も大きな発熱は電池1本充電で1Wを若干下回るようで、0.5Wから0.6Wほどの減少になっています。 しかしここでは実際の使い勝手からすると、実際の損失電力はもっと小さいであろうと想定しています。 ずばりそれを申し上げると、『実際に充電する場合は2本か4本の場合が殆どで1本、3本の充電は少ないであろう。』ということです。
と仮定すると、単二の場合0.11W、単三では0.21W、単四では0.27Wが最大の損失電圧です。 同じ見方を先週の表でしてみると、単二の場合0.82W、単三で0.91W、単四で0.82Wと1/3以下になっています。 最大の0.27Wで考えても使う放熱器はこの下の写真に見えるような小型のもので充分になります。
ということで以上のからくりを実現する回路を考えました。
部品が少々多いなーと思いますが、これ以上少なくするのは無理なようです。 さらーつと紹介していますが、最初はトランジスタで5KΩの半固定をショートさせようとしていましたが、ベースとコレクター/エミッター間の漏れが多くて設定電圧が計算どおりにならずうまく動作しませんでした。
そこでゲートとドレイン/ソース間の良好な絶縁状態が特長のMOS FETからON抵抗の値が大変小さい物を選別し置き換えて計算結果に近い動作になつており、そこまでに2日間頭をフル回転させました。 写真に見える緑色の部品はサーミスタでトランジスタのVbeの温度補償に挿入しています。 この実験では1回転の半固定を使いましたが、実際にはデリケートな調整になるので多回転のポテンショメーターを使うべきです。
使用に際してはトランジスターへの入力電圧を0としてMOS FETをONモードにします。 そうすると5KΩのポテンショメータはショートされた状態になりますので、10KΩ(基板中央)を回して出力電圧が7Vまたは8.2Vになるよう調整します。 その後トランジスターへの入力電圧を大きくするとMOS FETはOFFとなり5KΩのポテンショメーターが動作状態になるので、出力電圧が5.5Vになるよう調整します。 最後にトランジスターに繋がったポテンショメーターに3.1Vの電圧を掛けた状態でポテンショメーターを調整し出力電圧が5.5Vから7Vまたは8.2Vに切り替わり出すポイントとなるよう調整します。 この時7Vまたは8.2Vに到達するポイントは3.17V位になりました。
以上の調整を済ませた後で実働試験を致しました。 その結果は以下の表のとおりです。
一番左の欄は充電される電池の電圧で、1本辺り充電開始時には1.0V(放電終了でカラッポ状態)、終了間際には最大で1.53V(0℃の時で気温が高くなると若干低くなる。)まで上昇します。 それが3.1V以下ではMOS FETはオンとなっており5.5Vの低い出力電圧がでています。 それ以上の電池電圧になるとMOS FETはオフとなりますので、出力電圧は7V/8.2Vに上がり、これが次の行になります。
負荷抵抗を3段階で下げて行きましたが、出力電流が大きくなるに従い変換効率は良くなっており、最大効率は0.4〜0.5Aにある!というメーカーの説明どおりです。 また出力電圧は5.5Vよりも高い7Vの方が良くなっており、これはメーカー説明ではなかった点ですが、これも都合の良いポイントとなります。
総じて滅茶苦茶に変換効率が高いですが、電流測定は使った測定器の精度の関係で誤差が多いため、ぬか喜びしないほうが良いですが、相対的な比較或いは評価では問題ないと思います。
結論として充電回路系で必要な放熱器は大袈裟な物は全く不要ですので、\5,000.-を越えるような馬鹿げて高価な放熱器を使う必要が全く無くなります。
という、以上は只では転ばなかったお話です。
2016/05/27
最終的な充電回路の設計
先週に引き続き充電回路の電源電圧は2段階切り換え(3本直列充電時は5.5V/7.0V、4本直列充電時は5.5V/8.2V)方式とすることにしました。 こうした時の切り替えポイントがどこがベストかは図で見た方が簡単ですので、次をご覧ください。
簡単に説明しますと棒グラフで表示した部分はトータル充電電圧の変化を表しています。 下から、赤い部分は電池のトータル電圧で充電が進むと上昇し、放電終了時には1.0Vしかなかったのが最高で1.53V(0℃の時で温度が高くなるとやや下がる。)まで上がります。 その上は電圧として検出する充電電流で、電池の種類で変ります。 その上のピンクは充電池から充電回路への逆流防止のダイオードによる損失電圧でほぼ全ての場合で一定の値です。 そして一番上は制御損失としていますが、電流制御トランジスタのVceです。 オペアンプの微弱な出力電流で制御できるよう電流増幅率が5000と極端に大きいダーリントントランジスタ(2SB880)を使っていますが、その反動でVceが大きくここでは1Vとしています。
さて一番上に引いた赤線は、充電電源の出力電圧で、全てのケースで左の方は5.5Vをそして右端に近い所で7.0Vまたは8.2Vにステップアップしています。 これらの充電電圧が変更になる電池のみの電圧は青の点線でしめした3.10Vにしようとしています。 その場合どのようなことが起きるかを左端のケース(単二ニッケル水素電池)で説明します。
先ず2本の電池が充電終了間際には電池電圧は最高で3.06Vまで上がりますが3.1Vを超えることはないので、充電電圧は5.5Vのままで終了します。 次に3本の充電の場合ですが、初期には電池電圧は3.0Vですから電源電圧は5.5Vでスタートします。 しかし電池電圧は上昇して3.1Vを超えますのでその時に電源電圧は7.0Vに上昇します。
ここで棒グラフの一番上とその上にある赤線の間が大半の損失電圧となりますが、実際には1本だけ充電はかなり少なく、3本の充電もあまり無いだろうと思われます。 そうするとこの図を見ると判るとおりたった2段階の充電電圧の変更ですが、実用上の損失はかなり抑えられるだろうと踏んでいます。
二転三転してころころ変化した充電回路ですが、どうやら省エネ運転のアイデアも出尽くしたようですので、最終的な回路を組みなおしてみました。
検討した回路を紹介する前にブロックダイヤグラムで説明しておきます。
左がその図です。 各ブロックを色付けした太い線で横に繋いでいますが、これは電源からの流れを表します。 そして色が変る度に電子スイッチを通過します。
一番目の電子スイッチ(赤からピンクに変化)は自己保持型で、一度ONとなると主電源がOFFになるまでON状態を保ちます。 2番目の電子スイッチ(ピンクから緑に変化)は充電池ホルダーに電池が入っていればONになり、電池ホルダーから電池を抜き取られたり、放電モードになったり、主電源が切られない限りON状態を維持します。 これは充電終了を明確に知らせるため青のLEDを点灯したいことによります。 2番目の電子スイッチがONになるとタイマーが連動してONになりますがこのタイマーがONの間だけ3番目の電子スイッチ(緑から紫に変化)はONを維持します。 そして3番目の電子スイッチは充電回路のON/OFFを制御します。
2番目の放電終了検出は放電回路に含まれるリレー接点の充電側の接点間の電圧(1.0V〜4.6V)を検出しますが、放電モードでは開放となり電圧を検出できません。 よって放電が終わりリレーがOFFとなった時点で初めて電圧を検出できる(= 充電が開始される!)ということになります。
そうすると12時間タイマーが作動開始し、リファレンス電圧が生成され、充電回路ON/OFF SWがONとなり充電が開始されますが、電池ホルダーに仕掛けられた単三電池用ゲタを検出するスイッチに連動して充電電流が選択されます。 また充電用電源回路では充電する電池本数により充電電圧を選択します。 この回路では最大3本直列充電と考えており、3本であるか否かで7.0V又は5.5Vを選ぶようになっています。
充電時間が12時間に達すると充電回路はOFFとなりますが、先程申し上げているように2番目の電子スイッチは電池電圧を検出していますからON状態を保っています。 このため充電終了のLEDインジケータが点灯し、電池を外すよう知らせます。
放電・充電回路図は左の通りです。 以前提示していたものと電池電圧検出回路、リファレンス電圧生成回路、充電用電源回路が変っています。
最後の充電用電源回路は先週詳細を述べましたので省きますが、電池本数検出部分の抵抗とサーミスタの定数はより小電流で作動するよう変更しました。 というのはここの部分は主電源が遮断状態になっても充電池からの放電電流が流れる(定数変更後は3本最大電圧時に48μAに留まりますが、以前の定数では629μAも流れていました。)ためで、長時間放置すると折角充電したのにそれを放出してしまいます。 一方これに繋がるトランジスタはMOS FETのゲート電圧を変えれればよく出力電流はごく僅かで済みますから、ベース電流もそれに伴い小さくて良いのでここまで絞っても問題ありません。 この程度に絞れば充電が終了後1日間電池を外すのを忘れても計算上は1.2mAh程度の電池の消耗ですから一番容量の小さな単四電池の場合でも満充電の0.16%に留まり問題にならないでしょう。(充電が終わったら速やかに電池を外した方が良いのは変りありませんが。)
ところで放電終了検出は、1.0〜3.0Vを検知することで動作しますが、以前はその電圧の変化幅を圧縮したのち電流に変えてトランジスタを駆動していましたが、充電電流制御に使っているオペアンプは1回路余っているのと、大きな幅の入力電圧(1.0〜3.0V)でもオペアンプが問題なく対応できる点にあります。 但しオペアンプの出力電圧を制限しないと駆動するトランジスタを壊しますので、シリコーンダイオードを挿入して約0,7Vを上限としています。 それとこの回路は若干遅延動作させた方が良いと考え1000μFを挿入しています。
またオペアンプは入力抵抗が高い(1テラΩ=100万MΩ以上)ので、入力に流れる電流は極めて微少であり、充電された電池に直結されていますが電池の消耗には繋がりません。
リファレンス電圧検出回路はシャントレギュレータを使った回路にしています。 これは実装スペースが限られるのでボルテージレギュレータを使った時に必要なコンデンサーが邪魔だったのとより充電電流の精度を高めたかったからです。
取り敢えず基板のレイアウトを右のように検討しましたが、部材がかなり増えるので基板が大きくなるのを抑えるのに大変苦労しています。
まだ厳密なチェックもしていないのでこれで良し!となっていませんが、前回のレイアウトに対し幅は同じながら全長が20mm伸びました。 放電回路基板は基板に厚み30mmの放熱器が密着しますが、充電回路基板に付ける放熱板が厚み10mmであれば、トータルでの収まりは良くなります。
尚MPM80はこれまでの実験では発熱はごく僅かで放熱板は不要となる可能性大と考えていますが、仮に必要となっても小さな物で充分なので基板の端にレイアウトしています。
2016/06/03
私もモウロクしたもんだ!
先週お伝えした基板のレイアウトに添って充電回路の動作確認基板の製作に入りました。 ところが全ての組立を済ませたのち配線を回路図とレイアウト図との比較で確認している際にとんでもない間違いに気が付きました。 そして通電したのですが全ての動作が何かおかしいことに気が付きました。 そしてそれが何なのかを突き止めることが出来ません。 どうしてそうなってしまったかというと、信号の流れに沿ってロジカルに部品が配置されているのではなく、目標としていた基板サイズに収めるべく強引に隙間を埋めて行く手法で進めたため、見通しの悪いレイアウトになってしまったと言って良いでしょう。
もうひとつは私自身、年のせいか長時間緊張度を高めて作業することが出来にくくなっており、正確に論理的な問題の分析と解決策の追求がしにくくなっている事が挙げられるでしょう。 そこで無理をせず抜本的な問題解決を図るため、全面的に回路を見直しした上でレイアウトも組み直すことにしました。
その結果まとまった回路図は左の通りです。
今回発見した大きな問題はシャントレギュレーターを使った充電電流をコントロールするリファレンス電圧生成回路の電源を最終的な充電電圧(7.0V/5.5V)となる前の12Vから取った点です。 当初は判っていながら途中からうっかり見逃していた大事なポイントは、この電圧生成回路の基準点は一般に見受けるGNDではなく+Vにあるということです。(+Vとリファレンスポイント間の電圧がリファレンス電圧となります。)
採用した充電回路では2SB880のエミッターに挿入された1Ωの両端電圧をリファレンス電圧と比較した上で差異があればオペアンプを通して2SB880を制御して所定の充電電流となるように動作いたします。 そして抵抗の一端が基準点となりますが、リファレンス電圧生成回路にも同じ電位の部分を設けないとなりません。 その基準点がV+(7.0Vまたは5.5V)です。 先週までの充電電源検討で2段切り換えにしたわけですから、リファレンス電圧発生回路の電源はその2段切り替え電源回路の後から取らないといけないわけですが、それをうっかり忘れてずーっと前段の12Vから引くという間違いをしていたわけです。
その他にも回路の点検がし難い、ジャンパー線が多い、信号の流れの見通しが悪くチェックしにくい!という問題もありましたので、3段階に組み立てることで、回路点検を容易にしながら動作確認や調整が進められるよう、レイアウトの再検討を致しました。 その3段階の基板レイアウトは右の図の通りです。
大きな変更点は前述の通り充電電流設定のリファレンス電圧生成回路を充電電源回路の出力側に移動したことが大きいですが、その他充電終了インジケーターとなる青のLEDを駆動するトランジスタのベースに1000μFを挿入してこのLEDの点灯を遅らせることにしました。 と言うのは、充電回路がスタートとなる電圧を加えた所数秒間、充電中の緑LEDと充電終了の青LED両方が点灯してしまうことが判ったので、スペースが許す大容量の電解コンデンサーを挿入することにしました。
尚第一段階でかなりの回路がいきなり組み込まれてしまいますが、オペンアプの電源はジャンパーピンでON/OFF出来るようにし、終段の充電回路も最初は電流検出抵抗(1Ω)を外しておき、充電電流設定回路と充電電圧設定回路だけが動作できるようにしています。 更に、充電電圧、充電電流REF電圧、GNDの3箇所のチェックポイントを追加しています。
これらの変更により、第一段階の組立とその後の調整がこの充電回路において最も重要な部分となります。 そしてこれがクリヤーできれば残りの回路は殆ど無調整で済むはずです。
2016/06/10
充電回路試作第一段階
とんでもなく慎重な製作開始となりました。 第一段階とはいってもその1として、充電回路のオペアンプの電源は切断、制御トランジスタ(2SB880)のエミッターに接続する抵抗(1Ω 2W)も一応基板に固定はしましたが配線はせずということで充電回路は動作させずに、リファレンス電圧の調整と電池本数検出そして充電電圧の選択回路が正しく動作するかの確認をしました。
リファレンス電圧は単二と単三の充電電流を設定する為のものですが、その切り替えはリードスイッチを電池ホルダーに、単三用のゲタにマグネットをそれぞれ埋め込んでおき、ゲタを取り付けるとマグネットがリードスイッチに近接してリードスイッチがONになることを志向しています。 従ってリードスイッチがONとなった時に単三用の0.19V(190mA)になるよう調整し、リードスイッチがOFFの時に単二用の0.4V(400mA)になるよう調整します。
ここで使うシャントレギュレーターが発する標準電圧(1.25V)は非常に安定していますから12時間の充電中に全く変動することなく400mV、または190mVのリファレンス電圧を供給してくれます。
組みあがった基板の様子と動作テストの様子は以下の写真をごらんください。
|
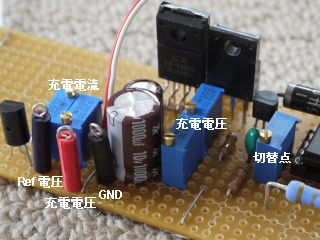 |
|
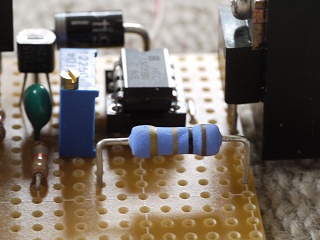 |
|
|
チェックをし易いように3つのT.P.を設けました。 またリファレンス電圧設定には多回転のポテンショメータを使い微妙な調整を容易にしています。
|
|
制御トランジスタのエミッター抵抗は値を1Ωとし、両端電圧を測ることで流れる電流が直読できるようにしています。
|
|
|
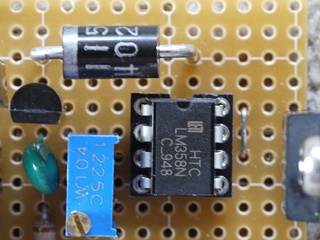 |
|
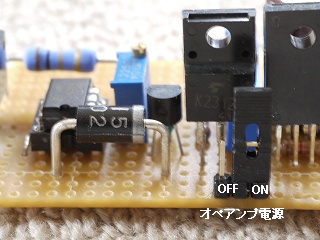 |
|
|
オペアンプはより入力抵抗の高い物が良いかな?とソケットを使い選別を容易にしていましたが、格安のLM358Nで充分に要求を満たしてくれました。
|
|
オペアンプの電源をON/OFF出来るようにして、充電回路の切り離しを可能にしています。
|
|
|
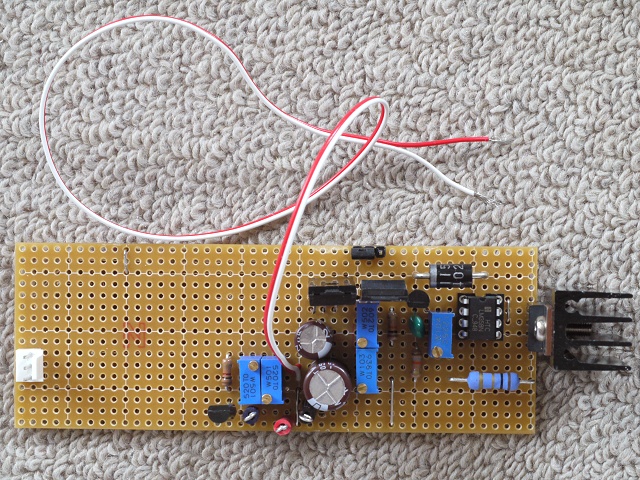 |
|
|
第一段階の組立が完了した電源基板です。 右端に見える放熱器は無いよりはまし!として使っている物で、本番ではもっと大きな物に変更されます。 赤白のワイヤーは電池ボックスに組み込むリードスイッチに繋がり充電電流自動選択として働きます。 現在先端が開いていますが、これは単二モードで、2本をショートすると単三モードになります。
|
|
|
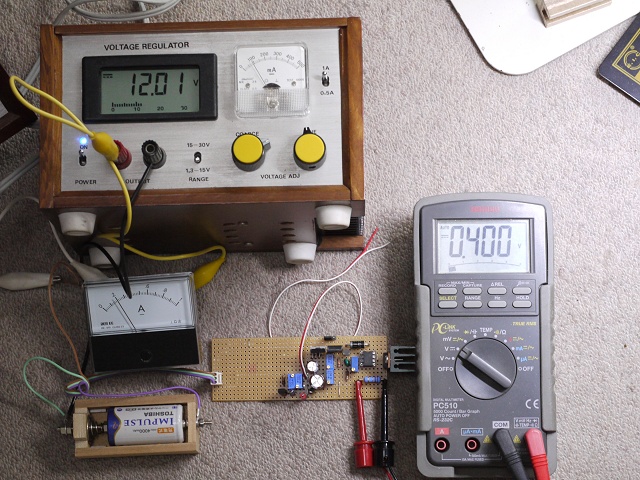 |
|
|
取り敢えずの動作実験の様子です。 充電電流の自動設定、充電電圧の自動切換えの切替点を調整後充電部分が働くよう結線し、試しに充電しています。 赤白ワイヤー先端が開いているため単二モードであり、DMMで0.4Vと読み取っていますが、400mAの充電電流を表します。 左の電流計は、0.21Aを指しておりその殆どは充電電流です。 但しDC-DCコンバーターで12Vが5.5Vに降圧されるため400mAの半分程度になっています。(このこの電流全てが充電電流として計算した場合でも変換効率は87.3%と大変良好です。)
|
|
試運転の際に各部の電圧を調べ回路図に書き込んだものを左に掲載しておきます。 背景が灰色の部分は未製作の部分で、丁度上半分が第一段階で製作した部分になります。 計算で求められる回路電流も記入しておきました。 赤字は電流を、青字は電圧を表します。
被充電池のプラスから電圧を取り出して電池の本数または電池の有り無しを検出する回路が2つありますが、前者の場合回路電流が39μA、後者は27μA流れることが判りました。 合計で66μA流れることになりますが、単四電池の場合充電後11,364時間抜き取らないとカラッポ!、または24時間抜き取らないと0.2%が放電してしまう!ということで、この程度でしたら自然放電よりも小さい値のようなので、充分満足できるとおもわれます。 以上は入力インピーダンスがあまり大きくない廉価なLM358Nで確認できたことで、それまでに検討していたLMC662CNの使用は中止しました。
感覚的な問題ですが無いよりはまし!と2SB880に取り付けた放熱器は21.2℃/Wの物で、400mAの単二用充電電流で1本充電時に20分後にはかなり熱くなるもののやけどをするような温度ではありませんでした。 よって最終仕様では10℃/W以下であれば充分であろうと考えています。 その他のMPM80、2SK2312では発熱は感じませんでしたので、放熱器の取り付けは不要かと思います。
また以上の確認が済んだ後30分近く充電動作を続けましたが、なんら気になる現象は発見されておりません。
2016/06/17
充電回路試作第二段階
充電回路基板組立の第二段階は充電中と充電終了のLEDインジケータに12時間タイマーです。 12時間タイマーはメーカー指定の回路をそのまま使いますから配線を間違えない限り問題は出ないはずですから問題は全く無いだろうと気楽に進めましたが、充電中と充電終了のLEDインジケーターが旨く作動しない、そもそも充電終了がスパーッと終了せず微弱な電流が流れっぱなし! と、コリャナンジャイの問題を発見しました。
色々調べた所電子スイッチに使っている2SJ377のソースとドレイン間が完全には遮断されておらず、絶縁不良のスイッチのようになっていることが判りました。 更に調べるとゲートの電位が完全遮断の場合はソースに一致しないとならないのに、ソースより数ボルト低い電位になっていることが判りました。 そしてそうなるのは、ソース → 47KΩ → ダイオード → GND と電流が流れてしまう為です。
そもそも電子スイッチとLEDインジケータの切替を一緒にして部品点数を減らそう!と考えていたために起きた問題で、これらを分離してしまわないと切れの悪い電子スイッチの状態は治せないと判断しました。
そこで考えたのがNPNトランジスタを2本使いそれぞれの負荷にLEDを繋ぎ、ベース電位が交互に切り変る回路です。 左が充電回路の全図ですが、灰色の部分が今回までに組み上げた部分で、ピンク色の部分が2つのLEDインジケータを駆動する回路です。 充電スタートの電子スイッチは上段右端に独立してあります。 後程お見せしますが、部品点数が増えますのでレイアウト上抵抗1本だけ表側には取り付けられず裏付けしたものの、まあまあ旨く収められたと思います。
新たに組み込んだLEDインジケータ切替回路の動作は右のようなものです。 回路の各分電圧や電流は実測値ですが、緑色は入力のスイッチがOFFの充電中の値で、青色は入力のスイッチがONとなった充電終了後のものです。 緑のLEDのON時の消費電流は0.35mAで、青のLEDのON時の消費電流は0.78mAと2倍以上の開きがありますが、見た目の明るさを揃えた結果です。
LEDがOFFの場合でも緑の場合0.01mA、青のLEDでは0.03mAの電流が流れています。 これらの微弱電流下で青のLEDは完全に消灯してしまいますが、緑のLEDの場合は青の電流の1/3にも拘らず、うっすらと光っているのが見えます。 緑のLED単体で実験した所3μAという微量な電流でも光るのが見えますので、これを消し去ることはあきらめ、青と緑のLEDの光を混合してマスキング効果により緑と青の切替を明瞭にするしかないと考えています。
尚実回路では入力部分の直列に繋いだ47KΩと3,3KΩは、電子スイッチの出力側に、その他は電子スイッチの前に組み込みます。 そうすると充電電圧のON/OFFに従い、0.65Vか0Vの入力が始めのトランジスタに掛かり、LEDの点灯を変更する動作をするというわけです。 既に申し上げたとおり片方のLEDはOFFの状態でもかすかに点灯という問題がありますが、電子スイッチ動作は明確な『遮断・導通』動作をしており、なんの拘わりもないので問題解決は図れています。
以上の変更加味した回路図は今週始めに掲載したとおりですが、基板レイアウトは左の通りです。 抵抗1本を挿入するスペースがありませんでした。 縦方向に抵抗を挿入することで解決できますが、そうすると後で何Ωを入れたのか判りにくくなるとか両端の電圧を測りにくくなるので、裏付けとしました。 その場合の飛び出具合は最小ですので、ひっくり返してもすっきりとしています。
但し新たに別な充電回路基板を起こすのであれば、僅かな部品の移動で抵抗1本の居場所を作り出すのは用意でしょうから、レイアウト変更して裏付けを無くすのがスマートでしょう。
フル充電によるタイマー動作の確認
さて12時間タイマーの動作確認は実際に充電動作をさせて確認するしかありません。 そこで以下の写真に見られるような装置で確認しました。 初めての充電動作実験ですから充電電圧の変化を詳しく分析等を始めとした詳しい調査はせず、単純に12時間経過したらタイマーが作動して充電が終了するかどうかの確認となります。
充電実験は2回(2本)やってみました。 記録に関しては例のデジカメでインターバル撮影した写真から時刻を読み取る方法です。 今回は5分間隔の撮影としましたから最大で5分の誤差が出ることをお断りしておきます。 1回目の開始時刻は6月11日午前11時40分で終了時刻は6月12日午前0時00分でした。 従って充電時間は12時間20分です。
2回目の実験は6月12日午前6時00分スタートで終了は6月12日午後6時20分です。 充電時間は1回目と同じく12時間20分です。 設定した12時間より20分長かったわけですが、ニッケル水素電池の0.1C充電における充電時間はメーカーにより12〜15時間とかなりの幅があります。 これは多分メーカーにより考え方や判断基準が若干異なるためではないかと想像しています。 従って20分の超過(+2.8%の誤差ですが±5%の誤差を有する抵抗で作った誤差の範囲内です。)は即電池を痛めるような問題にはならないだろうと思います。 仮にそれが心配であるなら誤差±0.1%〜1%のより誤差の少ない精密な抵抗に置き換えてやればよいでしょう。(私はこのままで良しとしますが。)
尚実験中に気付いたことですが、充電進行に従い充電されている電池は仄かに温度が上昇します。 温度を測定したわけではありませんが、2〜3℃の上昇というレベルです。 これが所謂急速充電になるとかなりの発熱を伴い、温度管理がかなり重要なファクターになるようですが、01C充電ではこれ以上の発熱は起きないので温度管理は不要です。 そこまでの様子は以下の写真をご覧ください。
|
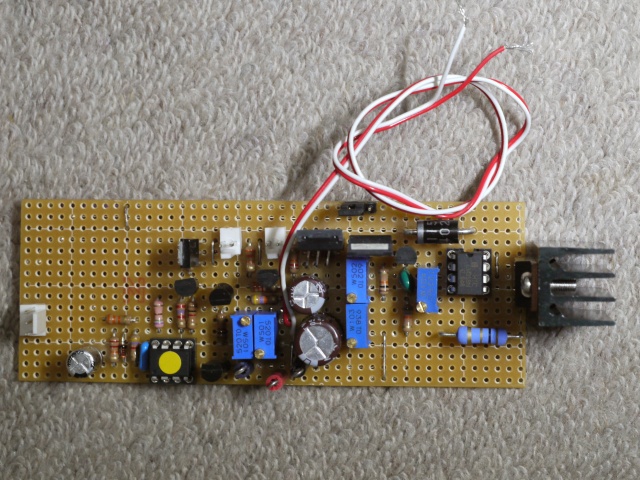 |
|
|
第二段目の組立が完了した基板の上面です。 左下の黄色い丸がタイマーICで、その上と左に12時間タイマー回路周辺部品が配置されています。 中央に二つ見える2ピンの白い物がLED用コネクターでその下にLED切り替え用のトランジスタと抵抗が収まっています。
|
|
|
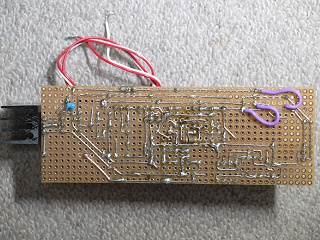 |
|
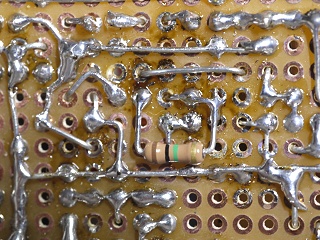 |
|
|
基板の裏側はこんな具合です。 左上に見える青い部品はオペアンプ電源部分に付けたバイパスコンデンサで、回路図には記載されていませんが、お約束の部品です。 右上の2本のワイヤーはジャンパ線で、次のステージで無くなります。
|
|
スペースが無いため裏付けした唯一の抵抗で、LED切替回路の部品です。 カラーコードが茶・黒・緑ですから1MΩである判別や、両端電圧の測定も表面に縦位置で取り付けたのに較べると容易に可能です。
|
|
|
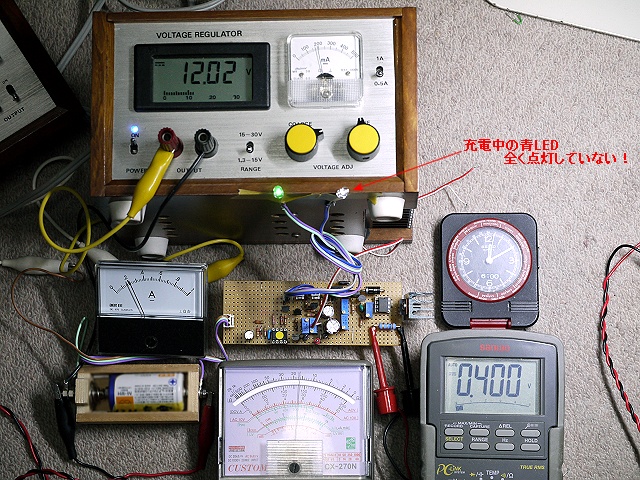 |
|
|
充電開始後の写真です。 電源は12Vで現在0.21Aの消費電流です。 DMMは充電電流を見ており、400mAの電流が流れています。 またこの写真では見難いですがテスターは電池電圧を監視しています。 現在1.35V辺りを指しています。 LEDインジケータは上の電源に貼り付けており、左の緑が点灯し充電中を表していますが、右の青は完全に消灯しています。 尚電池はほーんの少し暖かくなります。 熱いというレベルではありませんので何もする必要はありません。
|
|
|
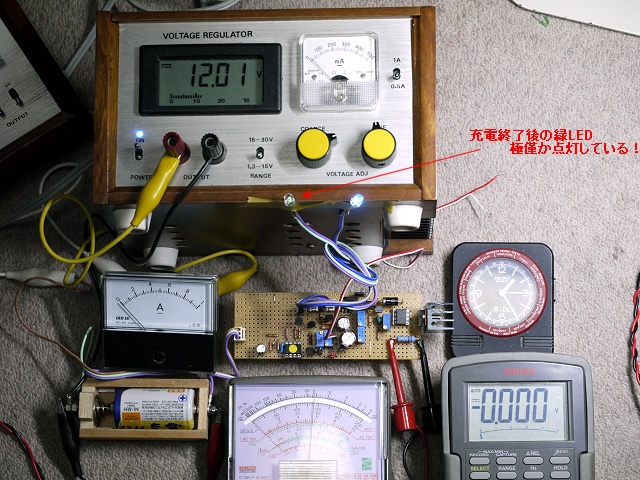 |
|
|
充電が終了後暫く放置した後の写真です。 上のLEDインジケータは青(充電終了)に変りましたが、緑のLEDはほんの僅か点灯しています。(面白くない現象ですが悪影響は全くありません。) 上の安定化電源はONのままですが、回路電流は遮断されていますし、当然ながら充電電流はゼロです。 唯一テスターは電池電圧を検出していますが、電池を抜けばこれもゼロとなります。 一番右のトランジスタの放熱器を指で挟んでみると、これはアチーナー!!と感じますが、長時間挟んではいられない!という熱さではなく、やけどをするような温度ではありません。 この放熱器は21.2℃/Wの熱抵抗ですので、最終的には5〜10℃/Wの放熱器(充電回路2つ分)を使えば十二分なマージンが得られると思われます。
|
|
充電終了後の状態はタイマーICがリセットされるまで続きます。 仮に別な電池を装填しても充電は始まりません。 充電をするには電源を入れなおしてスタートボタンを押さないとなりません。 スタートボタンを押すと放電開始となりますので、充電だけを独立して行うことは出来ず、その前に必ずリフレッシュすることになります。
そのような使い方はメーカー製の充電器にはありませんが、充電時間だけで12時間掛かりますから、リフレッシュを強制されても殆どの場合1時間前後が加算される程度なので、使い勝手の悪さにはならないだろうと思います。 それよりも常にリフレッシュしてから充電するスタイルは充電池に最も優しい使い方で、長期間安定して電池を使うベストな方法です。
2016/06/24
充電回路試作第三段階
充電回路動作確認もやっと完成段階に漕ぎ着けました。 残る取り付ける部品も極僅かですから組み立ては簡単に進みましたが、放電作業が終了したことを検出する回路が一番心配だったので、2段の電子スイッチの後段は出力を切断して今回組み立てた部分だけの動作確認から始めました。 回路図では一番左端のトランジスターのベースに繋がる『IN』に1V程の電圧を加えると最初のFETスイッチがONとなり、これが繋がる放電回路の動作が終了するまでスタンバイ状態となります。 ここの動作は全く問題ありませんでした。
次にオペンアプの3番ピンに電圧が掛かると出力電圧は電源電圧に近い10V程度の電圧が出てこれを3.9KΩで分圧してトランジスターのベースに電圧が掛かり次のFETをONさせるというストーリーでした?! (以前掲載していた充電回路をご覧ください。)
しかし実態は何と3番ピンに何の電圧が掛からなくてもオペンプの出力にはトランジスターをONとし、FETスイッチを作動させるに充分な電圧が出ていることに気が付きました。 オシロスコープを繋いでその信号を見た所、高インピーダンスの端子が発生するバズ信号のようなものが見えています。 考えうるに取り敢えず採用した回路は負帰還が全く無い裸利得で動作する回路でありその増幅度は100dB(100,000倍)もあります。 例えば出力電圧10Vを得るのに0.1mVあれば良いということで、ささやかな雑音電圧がトランジスタを駆動するに充分なレベルに容易に達します。
早い話が設計上完全に抜かっていたわけです。 そこで取り敢えず取った策としてオペンプの増幅回路をボルテージフォロワーに変更しました。 この改造は簡単で、GNDに繋がっている2番ピンを1番ピンに繋ぎます。 こうするとオペアンプの増幅度は100,000倍から1倍に変ります。 となるとオペアンプに入る雑音電圧が0.05mVあったとすると出力に出てくる電圧は0.05mVそのままです。 これなら悪影響を及ぼせません。 但し肝心な電池電圧も増幅無しで入ってくるので、3.9KΩはかなり抵抗値を減らさないとなりません。(回路の変更部分と電池本数により各部がどうなるかは以下の図をご覧ください。)
|
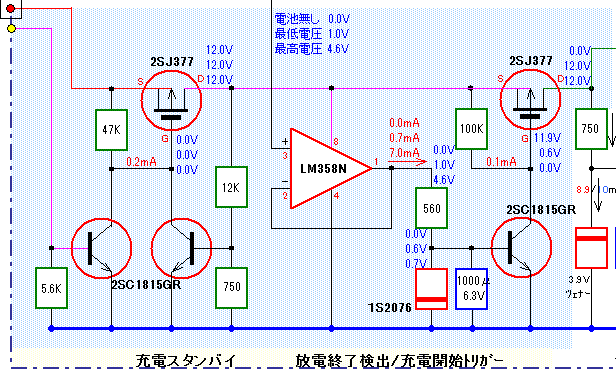 |
|
|
各部の電圧はスタンバイ状態以降を表しています。 3段の電圧表記は上から、電池ホルダーに電池が無い場合、電池1本で最低電圧の場合、電池3本で最高電圧の場合となっています。
|
|
但し電池電圧の最高値は電池三本で充電終了間際に4.59Vまで上昇しますので、それによりトランジスタを破壊しないよう気をつけねばなりません。 そこでカットアンドトライにて最適な抵抗値として560Ωが良かろうということになりました。 回路図にも記載していますが、電池電圧の最小値(1V)の時にトランジスタのベース電圧は0.6V、FETのゲート電圧が0.6V(ゼロが理想だがFETのVdsはゼロなので問題無し。)でした。 また電池電圧の最大値(4.59V)ではトランジスタのベース電圧が0.7V、FETのゲート電圧0.0Vで完璧な電子スイッチ動作をしています。
ところで電池電圧最大値の4.59V時にはオペアンプの出力電流は7.0mAまで増加しますが、吐き出し時の出力電流は40mAまで許容するようなので、過負荷の問題は無かろうと考えます。
以上で問題は片付いた筈なので、電源を繋ぎ入力に1Vの電圧をちょんと与えることで(スタートスイッチを押した時を模している。)、スタンバイに入る事を確認しました。 ついで電池を電池ホルダーに収めます。(放電回路のリレーが電池接続をスタートスイッチを押す前の状態に戻したのを模しています。)
これで充電がスタートする筈ですが、青のインジケーターが2秒弱点灯して完全遮断してしまい(スタンバイモードからも外れてしまう。)充電が開始されません。 そこで配線間違いや壊れた部品が無いかどうかなど多分40箇所以上つぶさにチェックしましたが、異常の原因が突き止められません。 そんなこんなで点検はタイマー回路に及びました。 このタイマー回路は以前にも使っているもので、メーカー推奨どおりの電ONで自動的にスタートするものでしたが、その出力端子を調べた所、何と電池をホルダーに収めた瞬間に出力が出るはずが0Vのままで、2秒弱後に回路全体が遮断してしまう事を発見しました。
なんじゃいこのみょうちきりんな動作は!!と疑心暗鬼になりましたが、気を取り直してメーカーの技術資料のタイマー動作シークエンスの図を見てびっくり仰天!! 『スタートスイッチが押されてもタイマーがスタートするのは約1.7秒後です。』 とあります。 スタートSW無しで電源ONスタートさせる場合も同様で電源ON後1.7秒経過しないと出力はONになりません。 ようするに『チョイ押し』のようなON操作では駄目で、電源スイッチを1.7秒以上押したままの動作が必要なのです。
そこで放電スタートスイッチを模したチョイ押し操作ではなく数秒押しっぱなしにした所、問題無く充電がスタートすることを確認しました。 それと同じ事を実現するために、放電スタートスイッチを押してスタンバイ状態に入った時大容量コンデンサを充電しておき、電池を電池ホルダーに装填して充電スタートのトリガーが掛かった際
にコンデンサからエネルギーが供給され数秒間ONが維持されるようにしました。 その間にタイマー開始のH出力が出て、終段の電子スイッチをONにロックし充電動作が始まるようになりました。
ところで現在大容量コンデンサとして1,000μF 16Vを使っておりますが、これにはスタートスイッチを押した瞬間に大電流(充電電流)が流れます。 どの位の電流が流れるのか0.5Ωの抵抗を直列に繋ぎその両端電圧をオシロスコープで確認しました。
その結果は瞬間的に約4.5Vの電圧が発生しますが、これは9Aの電流が流れたことになります。 2SJ377のパルス ドレイン電流最大定格は20Aですからこのままで問題無さそうですが、容量を更に増加するような場合には、最大ドレイン電流値が更に大きいFETに変えるか、電流制限抵抗を入れた方が良いと思います。(1Ωを入れれば最大電流は12Aになる。)
尚電池電圧検出回路の出力にダイオードのリミッター(1S2076)が入りそれにパラレルに接続されていた1,000μF 6.3Vのコンデンサは上記の大容量コンデンサーを配置するため取払いました。 このコンデンサは電池電圧検出部の出力電圧が微妙にふらつくのを防止する目的で入れたのですが、実働上削除しても問題が起きないことを確認しています。
以上で充電回路は一応所定の動作がするよう完成したわけで、早速3本目の充電実験をしました。 何も問題は無く既に充電を終えた2本と同じ12時間20分の充電時間でした。 それらの様子は以下をご覧ください。
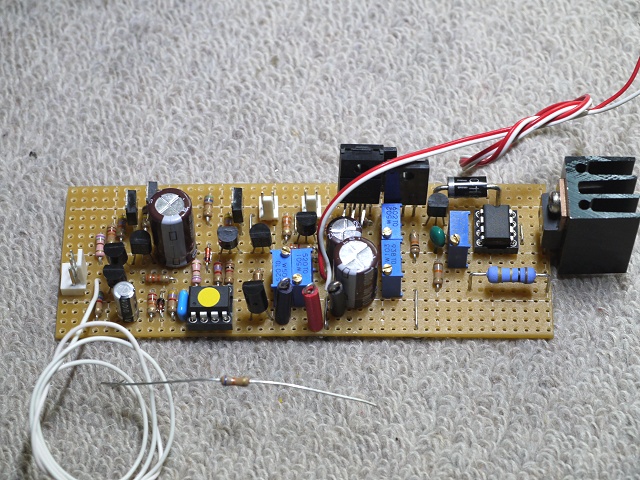 |
完成した充電回路基板。 最初の回路からの変更箇所はかなり多く、3段階で動作を確認しながら進めたに拘わらず順調に済んだとは言えず、いっぺんに組み立てて動作が全く不可解になってしまった初回試作品が余りにも無謀だったことが良く判り、大きな反省点になります。 尚手前に見える68KΩの抵抗が半田付けされた白いワイヤーは、抵抗の先端を電源の12Vにちょんと触ることで、入力に1Vのトリガー信号を模して加えるものです。
|
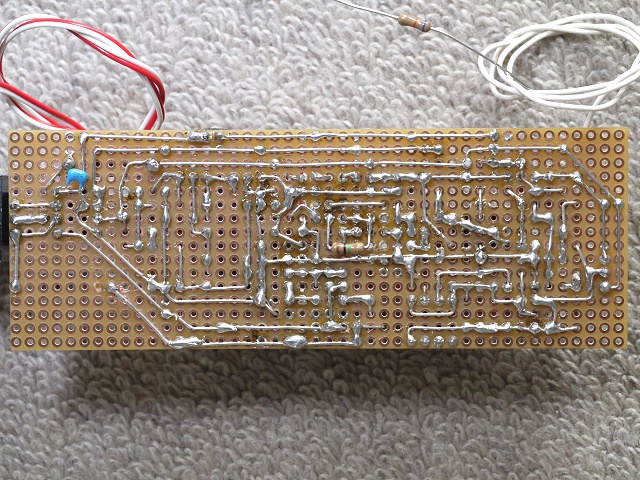 |
完成した基板の裏側です。 ジャンパー線は全て無くなり、2つの裏付け部品が見えるだけですから、高さ4mm位のスペーサーを介して固定できると思われます。 固定穴は4隅に3.2φの丸穴をあけます。
|
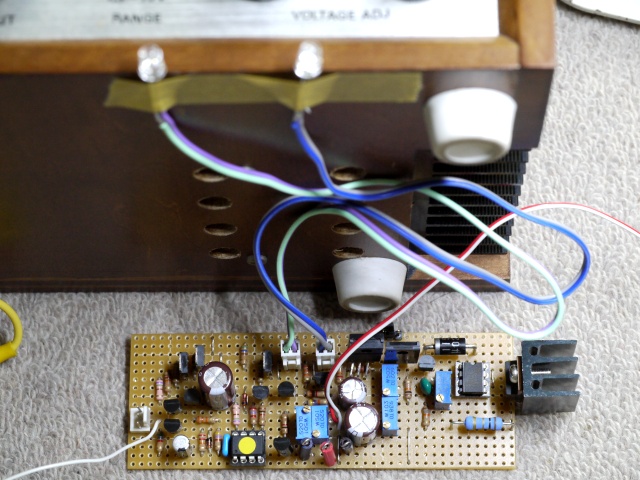 |
動作確認はこのようにLEDインジケータをひっくり返した電源にマスキングテープで止めています。 左が緑(充電中)で右が青(充電終了)を表します。 赤白ワイヤーの先端はオープン状態で充電電流400mAの設定です。
|
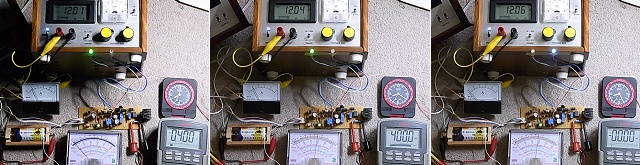 |
5分間隔のインターバル撮影をしていますが、左が充電直後で開始時刻は20:00。 中央は充電終了前の最後の写真で翌朝8:20を指しています。 右が充電終了後の最初の写真で8:25です。 これらから充電時間は12時間20分としています。
|
2016/07/01
放電回路制御部分の見直し
充電回路は旨くまとまったようですが、最後に放電回路からのリンクについて見直しが必要だぞ!?との疑問が湧き、放電回路図を暫しの間見て動作を頭の中で確認した所、難点か見直しが必要だとの結論に達しました。
その基本的な問題提起は、『リレーという機械的な接続/遮断と純電子回路による接続/遮断を組み合わせた時のタイミングの物語!』
から来ています。 なにやらかなりややこしそうですが、きっかけとなった放電回路から充電回路のリンクにおける疑問から触れてみることにします。
充電回路は放電回路が起動する時に受け取るトリガー信号でスタンバイ状態になり、放電回路のリレーが充電池接続を直列接続に切り換え完了時に発する1〜4.59Vを充電池電圧検出回路が確認すると充電開始となります。 つまり放電回路が動作している間は充電池電圧検出回路の入力はオープンの状態で何も検出できないのですが、放電回路動作開始時にはリレーという動作タイミングが遅れる機械的な遮断/接続により、直列状態の電池をばらばらにして個々の放電回路に接続しますので、スタートスイッチを押しても繋ぎ替えるのに短いですが時間が掛かります。
仮にまだ繋ぎ替えが完了する前に放電回路からのトリガー信号が充電回路に到達してしまい充電池電圧検出回路がチョンと何らかの電圧を検出してしまうと充電回路が作動してしまいます。 但し充電池の接続は放電回路側に変っていますから、充電は出来ないまま放電回路ONの状態が12時間続くという変な動作になります。 こうして放電時間終了後に電池の接続が変り充電が始まりますが、フル充電が出来ないまま終了すると想像できます。
放電回路及び充電回路内での動作シークエンスを時系列で分析してみると、
1.電池を挿入後メインスイッチ(機械式トグルスイッチ)を入れる。(赤のLED点灯)
2.スタート スイッチ チョイ押しで放電回路全体制御ブロックがON(電子的自己保持)。
3.テンポラリー動作ブロック内にある各放電回路が電子的チョイ押しスイッチでON。(電子的自己保持)
4.リレーが充電池を放電回路モードに接続変更し、即放電が開始される。(黄色LED点灯)
5.1秒経過後に電池電圧検出回路のリファレンス電圧が0から1Vに増加し電池電圧検出回路動作。
6.電池電圧検出回路が1V以上を検出できなかった時には放電回路電源遮断。(黄色LED消灯)
7.検出できたら放電を継続する。
8.リレー作動の数秒後に充電スタンバイ信号を充電回路に送付。 充電回路は待機状態となる。
9.電池電圧検出回路が1V以下を検出したら個々の放電回路は電子的自己保持を解除。(黄色LED消灯)
10.最後の放電が終わると電池接続は全てを直列にした充電モードに変る。
11.充電回路の電池電圧検出回路が作動し充電を開始。(緑のLED点灯)
12.その数秒後放電回路全体制御ブロックを遮断。
13.充電タイマーは充電開始後12時間経つと充電回路電源を遮断。(緑のLED消灯、青のLED点灯)
14.メインスイッチを切断して電池を抜く。(青のLEDと赤のLED消灯)
となります。 上記中ピンク色で示した部分が何らかのタイマー回路となる部分で上から、0.2〜0.4秒電子スイッチON維持、1秒ディレーON、数秒ディレーON信号送付、数秒ディレーOFFですが、それぞれどのタイミングで作動するかが異なるため、個々に回路設計しないとなりません。
現在までに回路単体での動作検討を終わったものを以下に紹介しておきます。
1.0.2〜0.4秒電子スイッチON維持
これは短時間電子スイッチがON状態になっている間に、そのスイッチを自己保持するための回路です。 機械的なスイッチ
ですとON時間がコンマ何秒の長さになるので不要なのですが、純電子スイッチですとON時間が短いので自己保持出来ない
可能性があります。 そこでトランジスタ1本、抵抗3本、コンデンサ1本で次のような回路を組み実験しました。
回路は2点鎖線の枠内で右のFETとトランジスタは放電回路の頭にある電子スイッチで、ここには描いておりませんが同じ物があと二つ並列に繋がります。 上向きの矢印はそれらの充電回路があることを表しています。
12Vの入力が二つありますが、上はメインスイッチから直接のもので、下はスタートスイッチを通った後のテンポラリー動作ブロック内であることを表しています。
メインスイッチをONとすると上の12VがONとなりますが、右の電子スイッチはOFF状態を保っています。 スタートスイッチを押すと下側にも12Vの電圧が流れ、1μF → 330KΩ → TR ベース及び33KΩ へとコンデンサが充電終了するまで電流が流れます。 この間トランジスタはONとなりますので、コレクタは0Vに低下しこれに繋がるFETのゲートも0Vに下がりFETはONとなります。
そうするとFETのドレイン電圧は12Vになりますが、これが分圧されて右側のトランジスタのベース電圧となり、トランジスタはONとなりコレクタ電圧は0VにロックされFETはON状態は保持されます。 その間に左側のトランジスタはOFFとなりますが、右のトランジスタでFETのON状態は保持されます。 そして右下に見えるリレーの接点がONとなると保持は解除されます。
2.放電開始1秒後にリファレンス電圧が0から1Vに増加し電池電圧検出が動作
ここで言う放電開始とは放電回路がONになり、リレーが充電池の接続を個々バラバラに変更して放電をスタートさせることを意味します。 リレーが行う接続換えは多少の時間を要しますので、その間に電池電圧検出回路が動作すると電池端子はオープンのため、リファレンス電圧よりも低い値として検出します。 これは電池が存在しないか放電は終了したとみなし、放電回路を遮断してしまいます。
そこでリレーが電池接続換えの間は、電池電圧端子にダミーの電圧(1Vより若干高い)を与えて接続が外れていても電池があるように見せかけるか、リファレンス電圧として0Vを与えてやり、電池が無くとも放電回路遮断のリレーが動作しないようにしてやらねばなりません。 前者はそれぞれの放電回路内に組み込むことになりそうなのと、充電池との干渉があるやもしれませんので、後者の方法で行くことにしました。 以下はまだ動作は検証していませんが、多分問題は無いと思います。
右1/3は1Vの電池電圧チェック用リファレンス電圧と、単二、単三の放電電流用リファレンス電圧の調整回路です。 10Vのレギュレータ出力はFETスイッチに入りますが、ゲートに繋がったトランジスタがONになればFETもON、トランジスタがOFFであればFETもOFFです。
これでトランジスタの入力に、充電回路スタンバイのトリガー信号出力(0.7V)を繋げば、放電回路全体制御ブロックがパワーオン後数秒間は1Vのリファレンス電圧は出ません。 従って充電池がリレーの動作で放電用に繋ぎ替えが完了してから電池電圧のチェックが始まるようになる筈です。
3.リレー作動の数秒後に充電スタンバイ信号を充電回路に送付
数秒遅延させて充電回路をスタンバイモードに入れる回路ですが、充電回路の頭の所にあるトランジスタのベースに0.7Vを送り、このトランジスタをオンさせて電子スイッチがONとなり、スタンバイモードに入ります。
左の回路はこれを実現するもので、12Vが印加されると暫くして出力電圧が出てきてカーブを描きながら上昇します。
図の定数で出力が0.5Vに到達するのに約4.5秒、最終電圧の0.71Vに到達するのに8秒掛かりますので、充電回路がスタンバイ状態に入るのはそれらの時間だけ遅れますので、リレーによる充電池を放電回路接続への切替が終了後となります。
そうすると充電回路中の電池電圧検出回路が間違って電圧を検出するようなことが無くなり、ひたすら全放電が終了するのを待つことになります。
このままでも良いはずですが、充電回路のスタンバイモードへはチョイ押し感覚で良いので、1.で述べた0.2〜0.4秒電子スイッチを充電回路の入力部に使う手がありますが、消費電力的にはこの回路を更に変更して数秒間だけ動作する方法がスマートな気がしているので、検討中です。
4.放電回路全体制御ブロックの遅延遮断
放電回路全体制御ブロックは3つある放電回路が放電を終えて遮断した時に動作を停止するのですが、これもリレーのメカニカル動作の遅れが出ても問題ないよう数秒の遅延の後に遮断します。
遮断のトリガーとしては、3つの放電回路それぞれに電源電圧の1/10である1.2Vを抵抗分割で取り出してそれらを混合し遅延回路に送り込みます。 その信号をコンデンサに蓄えますが、放電回路が遮断されて1.2Vの信号が途絶えても数秒間、放電回路全体制御ブロックの遮断は遅らせられます。 この中に含むショットキーバリヤーダイオードは、充電したエネルギーの逆流防止の目的で入れました。(無くても問題なかもしれませんが?)
また放電回路全体制御ブロックは手動のプッシュスイッチでONとなりますので、電子的なスイッチより接続時間が長いので、1.2Vの電圧がこの回路に掛かってFET保持トランジスターをONさせることが出来ると思いますが、それが駄目でON状態が保持出来ないときには、強制ONというか点線で記載したコンデンサーと抵抗を追加してやらないとならない可能性が若干あります。 詳しくは以下の図をごらんください。
以上4点のタイミング調整回路を組み込んだ放電回路全体制御ブロックを以下に掲載します。 完全に満足すべき動作を確認しているわけではないので、更なる確認実験をする予定です。
2016/07/08
単二・単三自動放電・充電回路のまとめ
前回再検討した放電回路に付属する制御・タイミングコントロール回路の追加を反映した、単二・単三自動放電・充電回路をまとめました。 またそれに基づいた基盤レイアウトを検討しました。
左がその回路図ですが、単二または単三電池3本まで用で実際には同じ物をもう1セット製作することになります。
右側45%位は充電回路ブロックで既に製作済みです。 その左側が放電回路ブロックですが横に3列に並んでおり、上3列の右側半分強は同じ回路が上下に3段並んだ放電回路本体です。
そしてその左側の3列目と4列目が先週検討した放電回路全体制御ブロックで、この中にリファレンス電圧生成回路も含まれます。
これを基に基板のレイアウト検討に入りました。 目標としては放電回路部分(回路図左側の点線内)が100 x 100mmの基板に収まることとしました。
その理由はプリント基板作りで露光に使う装置の最大受け入れ寸法が100 x 100mmであるためです。 基板作りはかなり手間が掛かりますが、同じ基板を複数使うのであれば間違い配線を防ぐ、仕上がりを綺麗に出来る!というメリットがありますから、この可能性を残しておきたいのです。
更に横幅については可能であれば96.5mm以内にできればと考えています。 というのは、電池ボックスを5mm厚の板で作ると3本仕切りを含む横幅は、25.5 x 3 + 5 x 4 = 96.5mmとなるからです。 右のレイアウト図は大きさがどうなるかを占うために取り敢えず1日半で描きあげたもので、間違い箇所が幾つか残っている可能性は大きいです。 しかしこの図を左に90度回転した使用状態では、幅94mm、高さ99mmと上で述べた2つのサイズ目標はクリヤーしています。
レイアウトの描きだし前にスペース配分で暫し考え込みました。 というのは放電回路本体はこの横幅の2/3強ですが、3つの放電回路を制御しリファレンス電圧を供給する回路を加算して基板全体になります。 従ってこの全体制御回路とリファレンス電圧発生回路を3つに分けてそれぞれの放電回路本体にくっ付ける方法を取りました。
具体的には上2列の場合電池接続切替リレーとオペアンプの間に2種類のリファレンス電圧生成回路を入れました。 これは3つの放電回路にリファレンス電圧を送る時上下にまっすぐジャンパー線を配するのが最も近いからで、そうするためにはここで分けるのがベストになります。 尚一番上の場合3Pのコネクターが入りスペースが狭いので、部品占有面積の少ない1Vの生成回路とし2段目に放電電流用リファレンス電圧生成回路としています。
よって残りの部品点数が極めて多い放電回路全体の制御回路を押し込めたのですが、最も先頭の電子スイッチを1段目と2段目の間に移動して何とか収めることが出来ています。
尚右端に放電電流制御用のFETが3本基板の端に固定されますが、最終的には電池6本となりますので、同じ基板を2つ上下に並べて長さ202mmの放熱板に固定されます。 その放熱板の厚みは30mmですから放熱板を含むケースへの固定部分の寸法は、幅202mm、奥行き140mmとなります。 ケースの板厚を5mmとするとケース外寸が幅212mm、奥行き150mmとなるでしょうか?
引き続き間違いが無いかどうかの確認・修正に2日程費やしてレイアウトを完成させますが、基板サイズを変更しないとならない可能性はかなり低いと思われますので、サイズ目標についてはほぼ達成できた!と考えて良さそうです。
次回には間違い箇所の修正が終了したレイアウト図を完成させ、そのレイアウト図を基に検証実験用の基板を穴あき基板にて製作します。(本番で使う基板は放電用、充電用各4枚必要ですが、仕上がりの均等化、綺麗さを考えエッチングした基板にて完成させます。)
2016/07/15
放電回路基板の組立その1
その後丸2日を擁して基板レイアウトの間違い探しを4回致しました。 恥ずかしながら出るわ出るわ! 正確には数えていませんが40箇所近くあったと思います。 それらの修正後が左に掲載するレイアウト図ですが、さいわいにも修正のために基板サイズが大きくなることはありませんでした。
この図を描き上げる際に放電の大き目の電流が流れる部分は太い黒で表現することにしましたが、そうするとGNDラインとの区別が付かなくなるので、GND配線部分は太いだけでなく青くして一目で判るようにしました。
これまでに色々な基板のレイアウトを考えてきましたが、今回妥協と言うか最初から少なくすることをあきらめたことがあります。 それはジャンパーワイヤーのことで、裸線を表面に使ってやるものと被覆多芯軟銅線を使って背面でやるものがあります。 数えてみると前者が19本、後者が10本あります。
回路中のあちこちの間でリンクしたり、何らかのリファレンスに従って動作制御をさせるような今回の回路などでは、多層基板を採用しない限りジャンパーワイヤーを減らすのは不可能で、外観上なんとなく間違った配線を修正しているように見えて面白くありませんが、こういった自作の場合は打つ手がありません。
ところで部品点数が大変多く一度に全てを組み立ててしまうと試運転でのチェックが非常にしにくくなりますので、4段階に分割して組み立ててやることにしました。 右の図がそれを表しています。
一番下がスタートの第一段階ですが、放電回路全体制御ブロック、リファレンス電圧発生回路、3系統の放電回路の頭部分だけを組み立てます。 これが出来上がったら、各放電回路のチョイ押し電子スイッチの動作、電池電圧検出のリファレンス電圧生成の遅延スタート、電池接続変更リレー作動後に数秒送れて充電スタンバイとなる動作確認、放電が終了し充電開始後数秒遅れで放電回路全体制御ブロックを遮断、の4動作とリファレンス電圧の調整・確認をします。
下から2段目では放電回路をひとつだけ完成させます。 そして電池1本だけを放電から充電までのフルサイクルで問題なく完全自動動作するかどうかが最重要項目になります。 但し単二、単三の自動選別と電池ホルダーに電池が存在するかどうかの機能は、電池ホルダー自身が3種類の検出スイッチをまだ有していませんから、その確認は後日になります。
上から2番目の第三段階は放電回路をひとつ追加したもので、これで電池の本数が増えた際に妙な誤動作が生じないかどうかの確認の1回目が可能です。(理屈の上では電池電圧検出回路は電池1本の時は1.0〜1.53Vを検出し2本の時は2.0〜3.06Vを検出、そして3本の時には3.0〜4.59Vを検出し、それらにより電池の有り無し、充電電圧の変更をする設計です。)
最上段は残る放電回路を加えた最終回路になります。 ここで動作確認上重要なのは、2本←→3本で充電電圧が正しく切り替わるかですが、設定がおかしいと充電中に電池の両端電圧が上昇して行く中で、充電電圧が変ってしまわないかどうかの確認が必要です。 この確認は私がよくやる簡易型データロガーで検出できないことはありませんが、充電電圧が変ってしまうのは本来の充電条件を外してしまう可能性や、異常発熱などの問題もありますので、12時間の充電の間つきっきりとは言いませんが、張り付いていたほうが良いです。
よって充電をスタートしたら、『お休みなさい!』とは行きませんし外出も出来ませんので、どうやって対応しようかと今から対策に悩ましい部分です。
そんな問題はありますが、第一段階の組立を開始しました。 但し第一段階が最も取り付ける部品点数が多いですから未だ途中の状況であり、組立終了とその後の動作確認の様子は次回になります。 以下組立中の写真です。
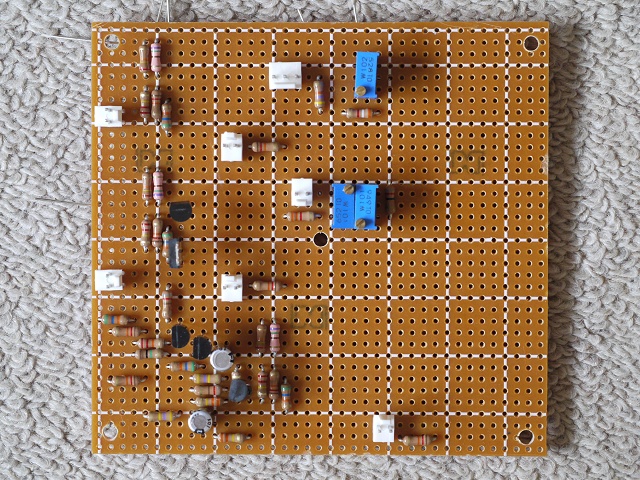 |
まだ部品は1/3程度しか取り付けられておりませんが、第一段階で組みあがる部分は最も重要な回路なので、誤配線がないよう慎重に1点、1点確認しながら進めています。
|
2016/07/22
放電回路基板の組立その1
基板の組み立ては部品点数が多いだけで特に問題も無く終了しました。 そして通電してテストを開始したのですが、三つの異常動作を発見しました。 それらの解決には丸2日間を要しましたが、無事解決策が発見出来ています。
問題1.リファレンス電圧が所定の値に調整できない
リファレンス電圧は速く安定して欲しいので主電源スイッチを押しただけで動作するようにしています。 このため主電源スイッチを押しただけでレギュレーターに電圧が掛かり、アンプであれば無信号電流に相当する約3.5mAの電流が流れます。 そこで早速リファレンス電圧を設定してみました。 単三用の154mVは問題なく終了しましたが、引き続き単二用の324mVの調整に入りましたが、ポテンショメータを0Ωまで絞っても電圧が高すぎて324mVに届きません。 そこでExcelで回路定数を変更した時にどうなるかを自動計算してくれる表を作り原因分析をしました。
回路を横にしたほうがシミュレーションの表が作りやすいので、左側がボルテージレギュレーターからの入力電圧、そして電圧をばっさりと落とす3.9KΩに続き、100Ωのポテンショメータが2つに22Ωと繋がりGNDに落ちます。 電圧出力は1番目のポテンショメーターのスライダーから取り出しますので、スライダーから高電圧側と低電圧側の抵抗値の和がスライダーを動かしても常に100Ωになるようになっています。
4つの抵抗のうち左から2番目の左半分を除き、手入力としています。 そして左から2番目の半分には、「= 100 - 右半分の抵抗値」という式が入れてあります。 その他子の表の上側で言うと154と出ているセル、 2.5mAと出ているセルにも計算式を入れています。
この表の現在の数値は最終的に採用したもので、以前の回路定数と比較すると、22Ωは82Ωになっていました。 思うにスイッチで挟まれた2つの抵抗値は70.8Ωになれば良いわけです。 以前は100Ωのポテンショメータに82Ωを繋いでいましたから、ポテンショメータをゼロにしても82Ωで電圧が高すぎて324mVにならなかったわけです。 この理屈からすると22Ωを取り去ってもポテンショメータだけで70.9Ωの抵抗は作れますが、取り敢えずポテンショメータの中央付近に調整点が来るようにして、何らかの回路乗数の変化で調整点が変ってもはみ出る可能性を少なくしています。
問題2.3つの放電回路間で干渉が起きてしまい、放電回路動作の独立性が怪しくなっている。
スタートボタンを押した時に『放電回路全体制御ブロック』にあるトランジスタが約0.3秒間ONとなりコレクター電位がほぼゼロになります。 そこでコレクターを3つの放電回路の電子スイッチとなるFETのゲートに繋ぐことでONとします。 そしてそこに繋がったトランジスタがONを保持するという仕組みとして設計しました。
ONするまでの動作は目論見どおりですが、各回路のFETをON保持するトランジスタのコレクターはONの時はほぼゼロ電位、OFFの時は12Vとなります。 ところが3つのこのトランジスタのコレクターは接続されているため、3つの放電回路のどれかが放電動作を終了し遮断した時におかしなことになってしまいます。
表現が難しいのですが、まだ放電動作が続いている筈の回路が動作しているのかいないのか判らなくなります。 これは原設計が放電回路同士間の独立性を脅かすようなものであったからで、トランジスタを各回路に1個追加して、3個のトランジスタのベースを接続してONさせることで、独立性を保てるように改造しました。 これら3個のトランジスタはスタートスイッチを押してから0.3秒しかONにならず、その後コレクターは接続されていない解放状態になります。 従って放電回路間での干渉は完全に排除できます。
問題3.全ての放電回路の動作終了後の『放電回路全体制御ブロック』の遮断が正しく行われない。
各放電回路から1.数Vの電圧を取り出してコンデンサに僅かなエネルギーを蓄え、全放電回路の動作が終了後にソノコンデンサーのエネルギーで『放電回路全体制御ブロック』は動作を数秒継続してから遮断する! という動作を目論みましたが、実態は2つの放電回路が遮断すると『放電回路全体制御ブロック』も遮断してしまいます。
これについては、多分あれが原因では?との見当をつけ、図的に状況を表してみました。 左の図は3つの放電回路から僅かな電圧を取り出し、遮断回路に送り込む部分を表しています。 極シンプルな回路で上側の抵抗は全て220KΩ、下側は24KΩです。 こうすると電源電圧が12Vの時には、12 x 24÷(220 + 24)= 1.18Vが遮断回路に送られます。
こうしておいて3つの放電回路がひとつずつOFFとなった時に、この遮断回路へ送られる電圧がどうなるかはこの図をクリックしてご覧ください。 ひとつの放電回路がOFFとなった時に遮断回路への電圧は0.81Vと31%もダウンします。 そして2つの放電回路がOFFとなった時には何と0.42Vで64%ものダウンになります。
トランジスタをOFFにするベース電圧は0.55V近辺ですから放電回路がひとつ止まっただけでヘロヘロになってしまい、ましてや2つも止まったらどうあっても即遮断するしかありません。
以上の図を描いての分析で原因が簡単に特定できたのですが、それじゃ解決策はどうするの? で半日自問自答しましたが意外にもその答えは簡単で、下側の抵抗を定電圧素子に置き換えればいいのではないか? というものでした。
その考え方を図で描き表した上で実験により裏付けを取りましたが、左の図をまずご覧ください。 下側の3本の抵抗は束ねられて1本のLEDに置き換えててあります。 このLEDは5φの赤の物で1本\20の格安品です。 駆動電流が20mAの時のVfは約1.9Vですが、照らすことが目的ではないので、電流は大幅に絞りますので、その時のVfは1.7V前後でしょう。
これで実働実験をした結果はこの図をクリックしてご覧ください。 3つで駆動した時出力電圧は1.72Vです。 そして2つによる駆動時は1.70Vで1.2%のダウンにしかなりません。 ひとつだけの駆動に落としても1.67V維持しており2.9%のダウンで澄んでいますから充分に目標を達成しています。
ここでは手持ちの部品であるLEDを使いましたが、正統的にツェナーダイオードを使えばもっと性能の良い結果が得られるかもしれませんが、流れる電流が微弱なので公称のツェナー電圧は当てにならず、事前の実験が必要になります。 またシリコーンダイオードでも良いでしょうがその場合は2本を直列にすれば1.2〜1.5Vが得られると思います。
5φのLEDは結構嵩張るのでチップLEDを基板の背面に接続するのも手かもしれません。 0.1mAでも意外に発光しますからそれが嫌ならチップLEDがベストチョイスかもしれません。
以上の変更後数時間にわたりテストしましたが、大変うまく動作しております。
当然ながらこれは、7/1にご紹介した4つの遅延ON、遅延OFFなどの項目が、一部の改造後にはシステムの中でもうまく動作しているわけです。
全ての組み立てが完了し動作確認が済むまでに更なる変更があるやもしれませんので、基板レイアウトはそれらをクリヤーしてからお見せすることとして、右に現時点での回路をご紹介しておきます。
第一段階を通過した基板の写真及びテスト中の写真などは、以下をご覧ください。
|
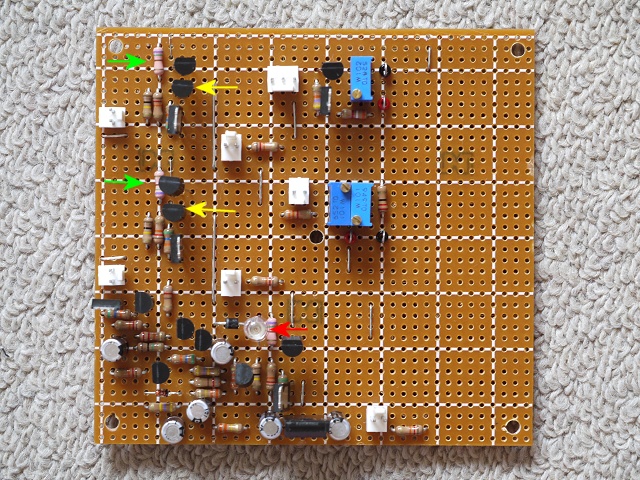 |
|
|
第一段階をパスした基板。 黄色矢印先は追加したトランジスタ。 緑の矢印は削除した抵抗、赤は抵抗を赤のLEDに置き換えた部分です。 結構大きな回路変更なのですが、最少量の部材追加で済み大変ラッキーでした。
|
|
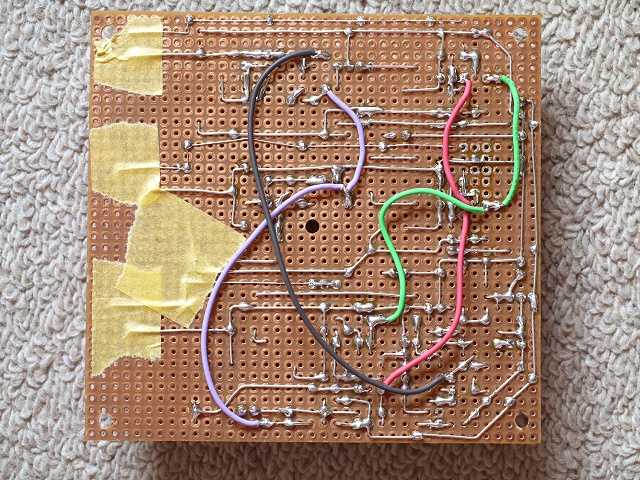 |
|
|
裏面はこんな具合でジャンパー線が4系統あります。 今後更に2系統のジャンパー線が追加され面白くないのですが、回路構成上やむを得ません。 左に見えるマスキングテープがペタペタ貼ってあるのはこの後配線するワイヤーの端末を抑えるためです。
|
|
|
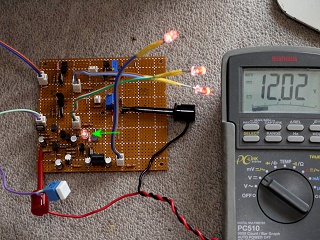 |
|
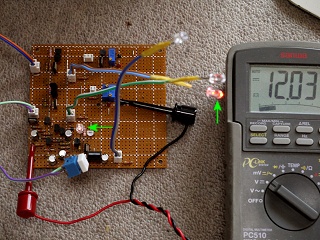 |
|
|
上の『問題3.』で述べた問題解決後の動作確認。 左の写真は3つの放電回路が動作中のため3本のワイヤーの先のLEDが全て点灯。 更に電圧調整用のLED(緑の矢印の先)も点灯している。 DMMは『放電回路全体制御ブロック』の電源がONであることを表している。 これに対し右の写真では2つの放電回路をOFFにしたのでLEDは1本のみの点灯(右の矢印)になっているが、DMMは引き続き『放電回路全体制御ブロック』の電源がONを維持しているのを表す。
尚左のLED(緑矢印先)は右の写真では点灯しているものの明るさは大幅減だが流れる電流が約1/3に減少しているためで、これは理屈に合っており異常ではありません。
|
|
2016/07/29
放電回路基板の組立その2
第一段階に較べると取り付け部品はぐっと少ないので、組立作業は半日で終了しました。 そして動作の確認に入ったのですが、放電電流をコントロールするリファレンス電圧の安定性がかなり悪いことを発見しました。 基板面をこんこんと軽く叩いただけでリファレンス電圧がふらつきます。
これまでの経験からするとテンプラ(半田付け不良)と見当をつけリファレンス生成回路の全部品の半田付けをやり直しました。 その結果不安定だった電圧は充分に安定しました。
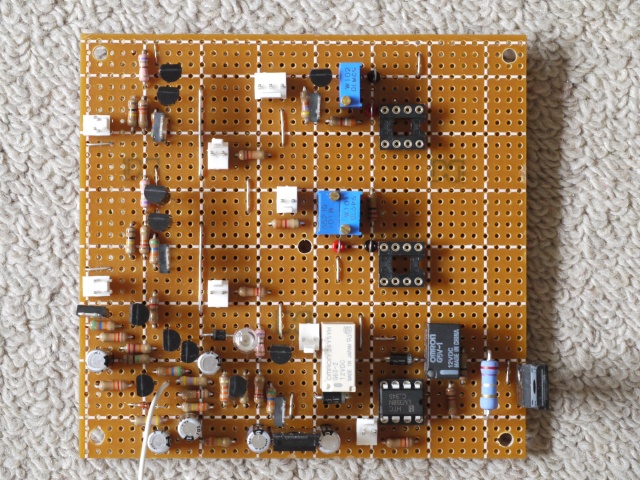 |
第一段階に較べると取り付ける部品点数がぐっと減りますので大きく変ったようには見えませんが、白い縦長の電池接続切り替えリレーと右に同じく縦長で黒の放電回路遮断リレーが目を引きます。 右端に放電電流制御のFETが見えますが、これは最終的に大きな放熱板に固定されます。 |
それ以外に特に問題も無かったので、電池ボックス1個と動作確認が出来ている充電回路基板を接続し、1本の電池のフル放電・充電サイクルの実験を致しました。 1回目のテストでは午後4時頃スタートしましたが、記録は全く取らずに10〜20分毎に電池電圧や放電電流値、充電電流値などをチェックしました。 何事も無く充電に入ったものの充電終了は翌朝5時半頃と推察されるのでそのままにして寝てしまい、翌朝6時に目が覚めた時には既に充電は終了し、電池電圧が1.45Vと満充電になったことを伺わせる状態でした。
2回目のテストでは購入したままの状態の電池を使い、今度は例のインターバル撮影によるデータロガーで、放電スタートから充電終了までを1分間隔で撮影し、電池電圧の変化を記録しました。
|
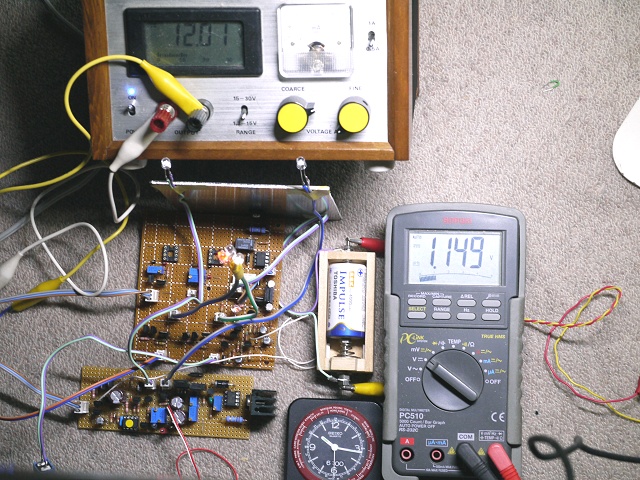 |
|
|
電池1本フルサイクル自動運転テストの様子です。 放電・充電基板2枚と電池ホルダー間を繋ぐワイヤー、外部取り出しのLED5本、スイッチへの接続ワイヤーなど計12本のワイヤーを使いますので、ご覧の通りゴッチャゴチャ! 最終的なインストールの時にはワイヤーを整然としたいです。 8時半にスタートしてまだ放電が継続中です。
|
|
|
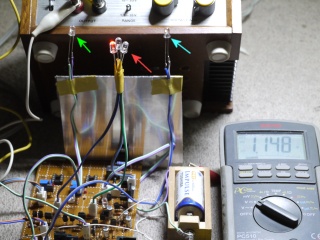 |
|
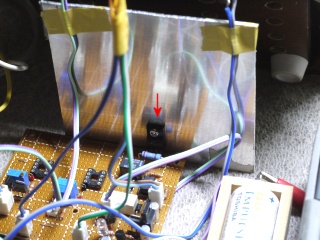 |
|
|
緑矢印は充電中のLED表示、青矢印は充電完了で、その間の3本束ねた赤矢印のLEDは放電中で、1本だけ点灯し電池1本を放電中の表示をしています。
|
|
てかてか光っているのは2mm厚アルミ板で10 x 11cmあります。 矢印先の放電電流制御トランジスタの放熱をしています。 熱抵抗は6℃/Wと能力はたいしたことありませんが、電池1本分であれば充分の能力です。
|
|
|
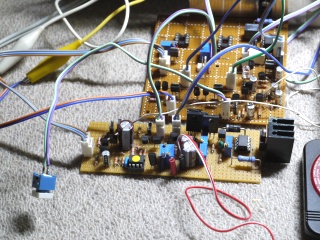 |
|
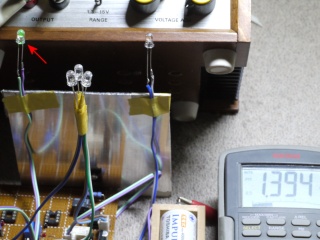 |
|
|
左下はスタートスイッチですが、放電回路は一度だけONとなり、放電が終了し遮断後に再度押してもONになりません。 放電回路を再度ONにするには主電源スイッチを入れ直します。 放電を繰り返すと電池を痛めるので誤操作防止機構となっています。
|
|
回路は放電動作から充電動作に進み電池電圧が徐々に上がって行きます。 現在1.394Vと表示されていますが最高は1.45V位まで上がる筈です。(低温時には充電時に1.54V程度まで上昇します。)
|
|
|
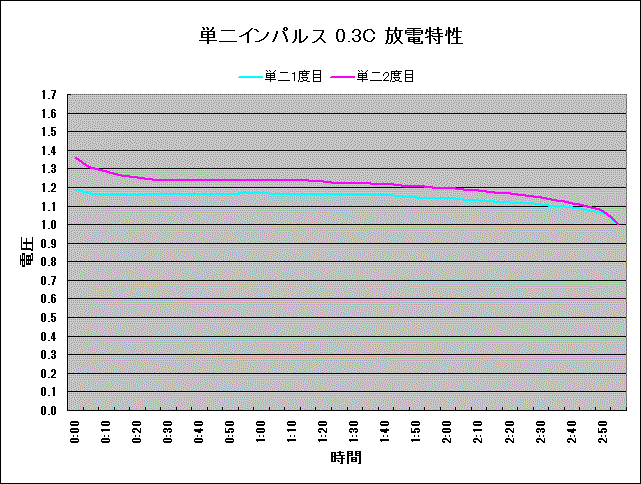 |
|
早速購入したまま全く使っていなかった単二インパルスを電池ホルダーに装填しました。 上記の青線がそれですが、放電終了が2時間55分であるのは計算上の3時間20分に対して12.6%低いのは兎も角出力電圧が殆どのケースで1.2V以下であり、これは異常としか考えられません。
そこでいろいろ調べた所どうも電池ホルダーでの接触抵抗が疑われるので、無水エタノールで電池と電池ホルダーの電極をクリーニングしてからもう一度放電・充電のフルサイクルをやった結果がピンク色の線です。 放電終了までの時間は変りませんが、放電開始後2時間までは1.2V以上あり問題無さそうに思えます。(尚その後色々インパルスを使った方の実験などを伺った結果、色々あるニッケル水素系充電池の中でインパルスは出力電圧が若干低い傾向にあることが判りました。 但し放電時間の長さには粘りがあるようで、決しておかしな電池では無さそうです。)
|
|
|
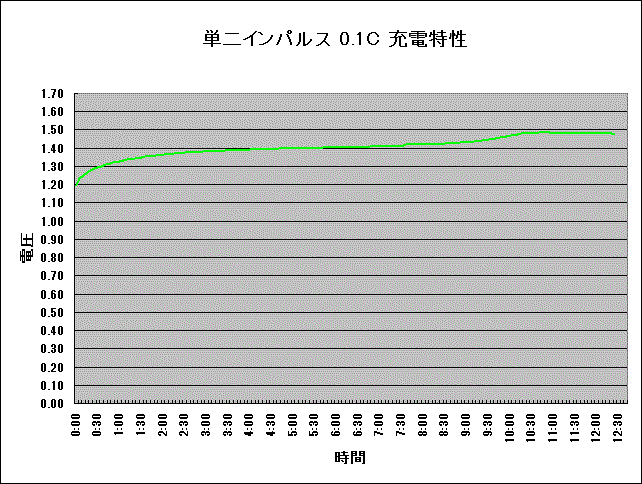 |
|
充電電流は放電電流の1/3の値で、接触不良による影響は低いと思われ、放電時のような妙な挙動はありませんでした。 そして教科書に載っているニッケル水素電池のお手本のような電圧変化が見られます。
一番目は1.4V近辺で発生するゆるーい傾斜です。 そして二番目は8:30〜10:30に掛けて発生する急なのぼり傾斜で、三番目はそれを過ぎると1.48Vで頂点に達し11:30を過ぎると僅かに減少しています。
このピークが充電が完了(満充電)した所だと言われておりますので、全く不足の無い結果と言えます。 | |
ところで少々脱線ですが、上のテストでは放電電流は1,200mAです。 一方先日完成したLEDランタンは電源電圧5.0〜6.0Vの間で平均して約800mAの電流を消費します。 一般に放電電流が減少するとそれの反比例以上に電池が長持ちしますから、LEDランタンに単二インパルスを使うとその動作時間は上の値(2時間55分)から、1200 ÷ 800 = 1.5倍以上伸びると計算されます。
その結果は4時間23分となり、アルカリ乾電池の時の2.8倍以上になります。 これは最大光量の場合で、ツマミ半ばに絞った時と最小光量とした時の点灯時間が同率で伸びるとしたら、それぞれ13時間4分、91時間となります。 これは単二インパルスがLEDランタンには単二アルカリ乾電池よりも相性の良い電池であることを暗示しています。 近々6本の電池を一度に放・充電できるようになってから、その検証実験をしてみたいと考えています。
2016/08/05
この暑いのに何ていうこと!!
第三段階は放電回路を2つに追加するのですが、第二段階とほぼ同じ追加量ですから組み立ては簡単に終了します。 従って早々と動作実験に入れたのですが、何か動作が極めて不安定です。 調べてみた所放電時の電池電圧を測定する回路のリファレンス電圧は1Vなのですが、これが9V以上に跳ね上がることを発見しました。 調査を続けるとほんの少しの間ですが1Vに戻る事もあるようです。 先週はこんな現象は出ていなかったので、今週追加した部分に誤配線かテンプラ(半田付け不良)があるとみて良いです。 一通り調べた所では誤配線があるようには思えませんし、基板レイアウトの設計ミスも無さそうです。 そんなこんなで2つのリファレンス電圧発生回路を調べるとどうやら1Vの回路の出力は9V以上になることが多いですが、324mVの方は大きくぶれるようなことがありません。
但しDMMのプローブをそれら二つに当てている時に妙なことを発見しました。 2つの電圧の片方はGNDであり同電位ですから1Vをチェックして324mVに移る際プローブの黒側(GND)は1V側に付けたまま赤だけを324mVのチェックピンに当てました。 そうしたところとんでない電圧に変ったのです。 おかしなことがあるもんだ!と考えながら黒のプローブを324mVのチェックピンに当てたところ正常な電圧が出るのです。 これは二つの黒のテストピン間に電位差があるためですからDMMで調べました。 そうした所9.何某かの電位があることが判りました。 そしてこれはGNDラインのどこかが断線している為ですからグラウンドラインのあちこちをテスターで当たったところ遂に断線箇所を発見しました。 そしてその断線原因はテンプラでした。
断線箇所の配線をやり直しましたが、この為に1Vのリファレンス電圧発生回路に使っているトランジスタ(2SC1815GR)は高いVbeで破損している可能性が高いので外してテスターで調べた所、案の定ベース・エミッター間は完全にショートしてお釈迦でした。
トランジスターを交換して基板の動作実験を再度開始しましたが、電池を検出できないのか数秒後に遮断してしまいます。 そこでDMMを電池ホルダーに繋いだ所追加した応急的に購入した電池ホルダーはスイッチを入れた瞬間に電池電圧が1.3Vから0.89Vまだ低下してしまいます。 その電池ホルダーを試作した低損失電池ホルダーに換えたところ電池電圧はスイッチON後1.24Vに留まり勿論1Vより高いので放電を開始します。
0.35Vの電圧差があったわけですが、回路電流は1.2Aですから、0.35 ÷1.2 = 0.292Ωものロス抵抗の差が市販のプラスチック電池ホルダーと私の自作電池ホルダーの間にあったわけで、改めて市販品は大電流用には使えないことを実感しました。
電池ホルダーを至急作りたいところですが、電池ホルダーに使うバネをホームセンターに特注せねばなりません。 電話で確認した所早くて7日の入荷ということで実験の継続はあきらめて、基板の全半田付け箇所の再点検を実施することに決めました。
この一番暑い最中になんということか! 最も手間取るトラブルに陥り頭はカリカリしていますが、使っていたチェックピンもどうやらミクロレベルの錆が出ている様でもありましたので、これも金メッキタイプの物に交換し全ての動作実験は次週に致します。
|
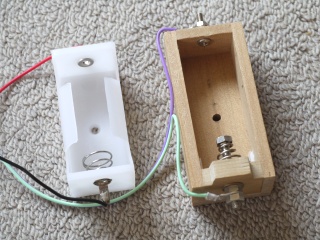 |
|
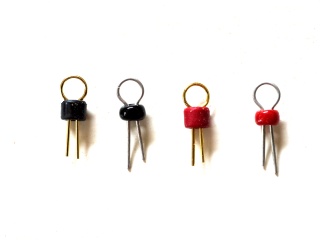 |
|
|
左側の市販の電池ホルダーは、見た感じでは使い物にならないことが全く判りませんが、大電流で使うと恰も電池の寿命が極端に下がったかのように感じるでしょう。
|
|
こちらはチェックピンで丸い部分が約3φです。 それぞれの色の右側はニッケルメッキですが、表面が酸化気味で接触抵抗や半田付けも怪しくなりやすいので、左側の金メッキの物に交換しました。
|
|
2016/08/12
電池ホルダーの製作の前にすること
電池バネの入荷が遅れているため電池ホルダーを製作する前にやっておくべきことに手をつけました。
その一番目はリードスイッチとネオジウムマグネットの入手とそれらを組み合わせた動作の基礎実験です。 リードスイッチは本体部分の長さが10mmで太さは1.8φです。 ネオジウムマグネットの方は長さ9mm、太さ2φ(体積28.3mm3)の円筒形で、吸引力は170gfとあります。 因みに手元にある11 x 6 x 3mm(体積198mm3)のフェライトマグネットとほぼ同等の吸引力です。 従って吸引力はほぼ同等ながら体積は1/7になるということです。 それらの写真及びネオジウムマグネットによるON/OFF試験方法の様子は以下の写真をご覧ください。
|
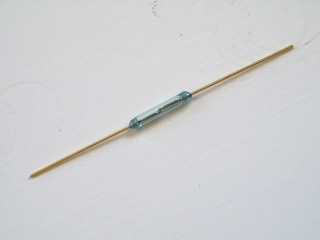 |
|
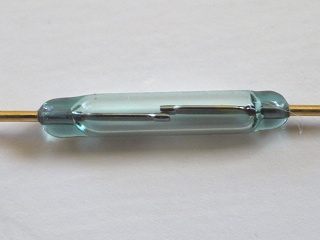 |
|
|
入手したリードスイッチで、本体部分の長さが10mmで太さは1.8mmです。 性能は平均的なものですが1本\40.-と格安なため大量に使う今回の目的では(約25本使用予定)、ありがたいです。
|
|
そのクローズアップですが、正磁性体で作られた2本の電極の突端が僅かな距離をもって固定されています。 これがある強さ以上の磁場に入ると2本の電極がくっついてONとなります。
|
|
|
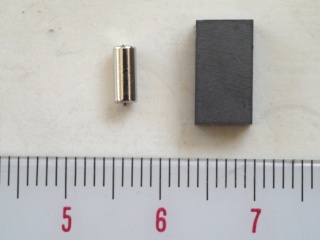 |
|
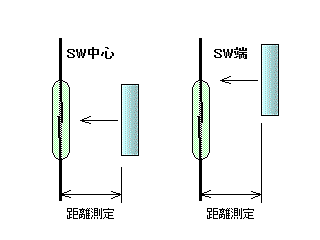 |
|
|
左が今回使うネオジウム磁石で、右が手元にあった吸引力がほぼ同じのフェライト磁石ですが、体積は7倍もあります。
|
|
磁石とリードスイッチは長手方向を平行にしてその距離を縮めて動作磁界をリードスイッチに与えますが、参考値として磁石中心がずれてリードスイッチ本体の端を向いた際の動作距離も調べました。
|
|
リードスイッチの動作実験結果は磁石中心がリードスイッチ中心を向いた時には、8mmの距離まで近づくとONに、そしてそこから10.5mmの距離まで離すとOFFになりました。 また磁石中心がリードスイッチの端に向いた際には感度がやや下がり、7mmの距離まで近づいてON、10mmの距離まで離してOFFでした。
以上はリードスイッチの中心と磁石の面の距離ですから、面と面の距離では0.9mm減じた値になります。 これに基づき電池ホルダーにリードスイッチや磁石を埋め込む設計を進めます。
その2としてはまだ少々先の作業ですが、基板の最終スタイルであるエッチングによる基板作成時の原図を起こさねばなりません。 エッチング基板で最終仕様とする目的は同じような基板を複数作る手間を省けることと出来栄えにありましたが、先週起きた半田付け不良の問題もエッチング基板タイプでは激減します故、絶対に採用したいと考えています。 但し異なった面で問題を生じますので、それに対する対策を充分に考えておかねばなりません。
その大きな問題とは導体抵抗の問題です。 私が試作している基板に使っている錫メッキ線は0.6φの物です。 直径1φの銅線は1cm辺り0.00021Ωの抵抗があると言われていますから、0.6φでは0.00058Ω/cmになります。 さて銅箔で配線するプリント基板の場合は1mm幅で0.0048Ω/cmと固有抵抗値は10倍以上に跳ね上がります。 この抵抗による電圧降下は何らかの信号電流など10数ミリアンペア程度であれば無視できますが、0.005Ω/cmのオーダーとなると例えば1.2Aの放電電流の場合には0.006V/cmの電圧降下となり20cmの長さで0.12Vも電圧降下が発生し、折角損失電圧を抑えてもそれを無にする結果になります。 これを改善するのには銅箔幅を8.3mmにすれば0.6φの銅線で配線したのと同じになりますが、そうすると既に起こしたレイアウトでは箔幅が広すぎて実現できず、基板の大きさも変えねばならなくなります。
いろいろ考えた末にパターン幅を1mmと2mmの2種類、半田付け部分となるランドは直径2mm、パターン間の最小隙間寸法を0.5mmとし、これに基づいて穴あき基板レイアウトをエッチング基板レイアウトに変更する第一段階を致しました。 左がその図です。
多分無いとは思いますが配線ミスなどを2回ほど全面的にチェック後に部材名、何らかの文字表示、ジャンパー線を取り去り全パターンを黒に変更して裏表をひっくり返した後にOHPフィルムに印刷して焼付けフィルムを作ります。
図中で幅広の部分は2mm幅、その他は1mm幅で描いており、更に放電電流が流れる部分は濃い灰色で、GNDラインは濃い青、電源入力は赤、そこから電子スイッチを1回通った部分はピンク色、10Vのリファレンス電圧生成の電源ラインは紫色、と判りやすくしています。
先にも触れたように2mm幅のパターンでは固有抵抗が大きすぎますので、放電電流が流れるラインには1φの錫メッキ線を2mm幅のパターンの上に半田付けして固有抵抗を0.0002Ω/cmに減らすことにしています。 さすれば1.2Aの放電電流が流れても20cmの長さで起きる電圧降下は0.12Vから0.0048Vへと激減し問題解決が図れると考えています。
尚右端に取り付けるFETの間隔が32mmになるようFET位置を微調整していますが、これはFETを放熱板に固定する際放熱板のフィンとフィンの間になるようにすることでネジの先が一番薄い所に来るよう、フィンの間隔(8mm)の4倍としているためです。
2016/08/19
電池ホルダーの製作 1
電池ホルダーは当然ながら放電・充電器本体の一部ですが、装置全体の設置面積を抑えるため、電池ホルダー部分は上段、放電回路基板は下段としたケース構造とします。 放電回路用の放熱板は幅が202mmあります。 一方放電回路基板の左右の幅は94mmでそれを2枚固定しますから188mmとなります。
また電池を入れるスペースの内寸は26mmで、電池間のスペーサーは5mmとしますので、電池ボックス総幅は26 x 6 + 5 x 7 = 191mmとなります。 .基板幅より3mm長いだけですからギリギリと言え電池ボックス幅はこれより狭くするのは不可能ですので、191mmと決定しました。
一方放熱板は202mmですから11mmの差がありますが、電池ボックスと放熱板の間に5mm厚の板を両側に挟み1mmの隙間を残して落とし込み構造にします。 尚前後方向は電池の物理的な長さ、挿入時にスプリングが縮みボルトが突出する量、配線/接続スペースを考慮して109.3mmとしました。
上の図は充・放電器全体を収めるケースの構想図ですが、太い赤の点線で囲った部分が電池ボックスとなります。
この電池ボックスのプラス電極とマイナス電極が取り付けられる横方向の板には、6本の電池を装填した際に電池バネ圧縮による横方向の板を外側に膨らませるような大きな力が加わります。 それによる接着部分の剥がれや破壊防止のために、上部(後ろ側)と前部(前側)には16.3mm幅と24mm幅の1.5mm厚アルミ板を膨らみ防止のために貼り付けます。
また底部は5mm厚の板で全面的に覆いますので、充分な強度を確保できると考えています。
電池ボックス以外の部分はほぼファイナルと言える状態になっていますので、簡単に説明しておきます。 図の下側に薄紫色で表現された部分は放電回路基板とそれに取り付けられた部品の高さ25mmの占有スペースで、実際には取り付けられる部材で最も上背のあるのは20mm程ですから5mm程ゆとりがあることになります。
電池ボックスの下は外部との空気の流通は無い構造ですが、基板に固定された部品で大きな発熱を出すのは放電電流を制御する6本のFETだけで、それらは放熱板に固定されますから、内部に熱がこもるなどの問題はありません。
ケース全体の幅は323mmあり、202mm幅が放電器部分となりますので、右側1/3が充電回路部分となります。 こちらも上下2段構造として下に2枚の充電回路基板を配し、上にはスイッチ類やLEDパイロットランプを手前側29mmに、その先の96mm部分(黒くスリットのような着色を下部分。)は単三電池を収めるための6個のアダプターと接点の接触抵抗を少なくする液剤を納めるスペース、そして一番奥20mmは充電回路の放熱器を納める部分(ここだけ2階建てではない!)と考えています。
さて電池ボックスを構成する部材は合計で11枚ありますが、左の図はそれらの加工図です。 1枚だけは4mm厚でその他は5mm厚です。 材質としては工作用のアガチスか朴としたいと考えていますが、4mm厚は無いのでこれだけはシナ合板となりそうです。 合板を使うと木口が綺麗ではありませんが、最終的にはその上にアルミ板が載りますので、外観上の問題はありません。
前後方向側板の内面と前後方向仕切り板の両面にはリードスイッチを埋め込む溝を彫らないとなりません。 1個の単三電池アダプター左右にはネオジウムマグネットが最も離れるような位置に埋め込まれますからそれに応じて左右でリードスイッチの埋め込み位置を変更しないとなりません。
尚前後方向側板とー側電池押さえ 横板1は単純な長方形ではありませんが、次のような理由があります。
前後方向側板は最前方と最後方に1.5mm厚のアルミ板を載せます。 前方が16.3mmで後方が24mmですが、それらを載せるスペースを切り取る必要があります。
ー側電池押さえ 横板1は頂上を削り取られた丸い山が電池の本数だけ並びますが、これは電池バネのそこ側の直径が19mmあり電池ボックスより飛び出るのを防ぐためです。
クリーム色に着色された部分は幅5mmまたは9mmで深さ1mmの溝で、電動トリマーを使って加工します。 そしてそこにエポキシ接着剤を流し込んでから5mm厚の板、または5mmと4mmの板を重ねて落とし込み正確な接着位置決めが出来るようにします。
----- 以降、公開を停止致します。 -----
Copyright (C) 2001-2019, Vic Ohashi All rights reserved.
|